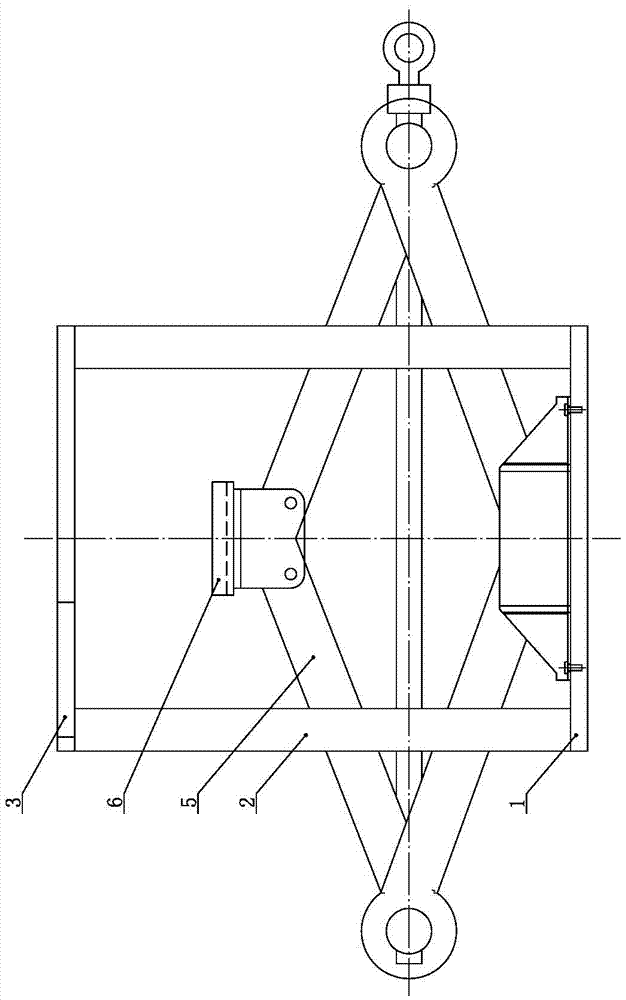
本实用新型涉及一种拆装工具,尤其涉及一种花键传动轴的便携式拆装工装,属于采油厂辅助工具技术领域。
背景技术:
采油厂经常使用特种车辆运输工具及人员,或者举升定位进行辅助作业,车辆传动轴的端头设有多个台阶,其中最外侧的轴端加工有花键齿,花键齿上安装有花键套,花键套与万向节连为一体,花键齿向内的轴肩处安装有轴承,轴承外周带有橡胶套。
在维修过程中,分解该传动轴时,花键套与花键齿的分离相对比较容易,而拆卸轴承则比较困难,由于轴承内圈与传动轴的轴颈配合比较紧,需要借助于工具才能进行拆卸。传统上采用小型机械拉马进行拆卸,将机械拉马的中心螺杆顶在花键齿的轴端,钩爪勾住轴承的外圈,逐渐旋进中心螺杆,钩爪将轴承拉出。由于传动轴上靠近轴承内端面的轴肩与轴承外圈之间距离比较近,供钩爪卡入的空间比较小,导致钩爪难以钩牢。此外,采用扳手转动中心螺杆的外端头时,不仅施加了旋转的力,还使中心螺杆承受向下的压力,在钩爪难以钩牢的情况下,容易导致拉马脱落,不但无法将轴承取下,操作人员还容易受伤。
在实际工作中,为了赶时间,现场施工人员通常采用硬棒顶住轴承内圈,采用铁锤击打硬棒的外端头,逐步将轴承冲出。由于轴承外周带有橡胶套,锤击拆卸一方面会造成橡胶的损伤,另一方面由于橡胶的弹性使得轴承的取出过程耗时较长。如此操作工的操作不熟练还容易将传动轴的表面敲出毛刺,将花键齿碰坏,甚至将扶棒的人员击伤。造成经济损失的同时,还容易带来人身伤害。
技术实现要素:
本实用新型的目的在于,克服现有技术中存在的问题,提供一种花键传动轴的便携式拆装工装,制作简单,成本低,便于运输,可以大大提高花键传动轴的拆卸速度,且不会造成工件损坏或人身伤害。
为解决以上技术问题,本实用新型的一种花键传动轴的便携式拆装工装,包括底板,所述底板的四个角部焊接有向上延伸的立柱,所述立柱的顶部焊接有与底板相平行的顶板,所述顶板上设有U形凹槽,所述U形凹槽的中心为半圆形通孔,所述半圆形通孔的圆心位于所述顶板的中心,所述U形凹槽的两平行边与所述半圆形通孔光滑过渡连接;所述底板上放置有千斤顶,所述千斤顶的顶升端与所述半圆形通孔的圆心共轴线,所述半圆形通孔的半径大于花键传动轴上待拆轴承处轴颈的直径且小于待拆轴承内侧轴肩的外径,所述顶板的厚度小于待拆轴承的内端面与相邻轴肩之间的距离;所述千斤顶的顶升端固定连接有U形槽钢,所述U形槽钢的开口宽度与花键传动轴的花键齿的齿顶圆直径相适配。
相对于现有技术,本实用新型取得了以下有益效果:传动轴的花键齿所在的一端为外端头,轴承安装在花键齿内侧,拆卸时,将传动轴的外端头朝下,使轴承卡在顶板的下方,与轴承相邻的轴肩卡在顶板的上方,U形凹槽的根部即半圆形通孔卡在轴承与轴肩之间的轴颈处。沿U形槽钢的开口方向将千斤顶推入,将千斤顶调整居中后,U形槽钢的两侧卡在花键齿的两侧,确保顶升时,轴承的外周均匀受力,平稳顶升。逐渐将千斤顶向上顶出,传动轴逐渐向上移动,轴承被卡在顶板下方保持不动,顶升一段后轴承即从所在轴颈处脱落,如此拆卸,不会造成轴承外周橡胶的损坏,避免敲击带来的设备损坏或人身伤害的风险,且操作十分便捷。
作为本实用新型的改进,所述千斤顶为剪式千斤顶。剪式千斤顶的顶升力足以将轴承取下,且剪式千斤顶的高度比较低,可以降低该工装的高度,使其重量更轻,外形尺寸更小。
作为本实用新型的进一步改进,所述U形槽钢的中心垫有圆形顶块,所述圆形顶块的直径与花键传动轴的花键齿的齿根圆直径相适配。在U形槽钢距离花键齿比较远的情况下,在U形槽钢上垫圆形顶块,可以减少千斤顶的顶升高度,圆形顶块顶在花键齿的齿根圆下方,然后随千斤顶向上顶升,可以避免花键齿受力,造成意外损坏。
作为本实用新型的进一步改进,所述底板上焊接有对千斤顶底座进行定位的千斤顶定位靠山。千斤顶底座抵靠在千斤顶定位靠山上即获得定位,此时千斤顶的顶升端与传动轴及顶板中心的半圆形通孔共轴线。
作为本实用新型的进一步改进,所述底板上设有可以嵌入千斤顶底座的千斤顶定位凹坑。千斤顶底座嵌入千斤顶定位凹坑中,千斤顶即获得定位,此时千斤顶的顶升端与传动轴及顶板中心的半圆形通孔共轴线。
作为本实用新型的进一步改进,所述千斤顶的底座通过螺钉固定在所述底板上。在工作地点相对固定的情况下,不会每次搬运千斤顶及校正,直接在工装上进行拆装。
附图说明
下面结合附图和具体实施方式对本实用新型作进一步详细的说明,附图仅提供参考与说明用,非用以限制本实用新型。
图1为本实用新型花键传动轴的便携式拆装工装实施例一的主视图。
图2为图1的左视图。
图3为图2的俯视图。
图4为图1的立体图。
图5为本实用新型工作状态的主视图。
图6为图5的左视图。
图7为图5的俯视图。
图8为图5的立体图。
图9为本实用新型实施例二的主视图。
图10为本实用新型实施例三的主视图。
图11为本实用新型实施例四的主视图。
图中:1.底板;2.立柱;3.顶板;4.U形凹槽;4a.半圆形通孔;5.千斤顶;6.U形槽钢;7.圆形顶块;8.千斤顶定位靠山;9.千斤顶定位凹坑;10.传动轴;10a.花键齿;11.轴承。
具体实施方式
如图1至图8所示,本实用新型花键传动轴的便携式拆装工装,包括底板1,底板1的四个角部焊接有向上延伸的立柱2,立柱2的顶部焊接有与底板1相平行的顶板3,顶板3上设有U形凹槽4,U形凹槽4的中心为半圆形通孔4a,半圆形通孔4a的圆心位于顶板3的中心,U形凹槽4的两平行边与半圆形通孔4a光滑过渡连接;底板1上放置有千斤顶5,千斤顶5的顶升端与半圆形通孔4a的圆心共轴线,半圆形通孔4a的半径大于花键传动轴上待拆轴承处轴颈的直径且小于待拆轴承内侧轴肩的外径,顶板3的厚度小于待拆轴承的内端面与相邻轴肩之间的距离。
传动轴10的花键齿10a所在的一端为外端头,轴承11安装在花键齿10a内侧,拆卸时,将传动轴10的外端头朝下,使轴承11卡在顶板3的下方,与轴承11相邻的轴肩卡在顶板3的上方,U形凹槽4的根部即半圆形通孔4a卡在轴承11与轴肩之间的轴颈处。将千斤顶5调整居中后,千斤顶5的顶升端顶在花键齿10a的端头上,逐渐将千斤顶5向上顶出,传动轴10逐渐向上移动,轴承11被卡在顶板3下方保持不动,顶升一段后轴承11即从所在轴颈处脱落,如此拆卸,不会造成轴承外周橡胶的损坏,避免敲击带来的设备损坏或人身伤害的风险,且操作十分便捷。
千斤顶5为剪式千斤顶。剪式千斤顶的顶升力足以将轴承11取下,且剪式千斤顶的高度比较低,可以降低该工装的高度,使其重量更轻,外形尺寸更小。
千斤顶5的顶升端固定连接有U形槽钢6,U形槽钢6的开口宽度与花键传动轴的花键齿10a的齿顶圆直径相适配。沿U形槽钢6的开口方向将千斤顶5推入,千斤顶5与半圆形通孔4a共轴线后,U形槽钢6的两侧卡在花键齿10a的两侧,确保顶升时,轴承11的外周均匀受力,平稳顶升。
如图9所示,U形槽钢6的中心垫有圆形顶块7,圆形顶块7的直径与花键传动轴的花键齿10a的齿根圆直径相适配。在U形槽钢6距离花键齿10a比较远的情况下,在U形槽钢6上垫圆形顶块7,可以减少千斤顶5的顶升高度,圆形顶块7顶在花键齿10a的齿根圆下方,然后随千斤顶5向上顶升,可以避免花键齿10a受力,造成意外损坏。
千斤顶5的底座通过螺钉固定在底板1上。在工作地点相对固定的情况下,不会每次搬运千斤顶5及校正,直接在工装上进行拆装。
如图10所示,底板1上焊接有对千斤顶底座进行定位的千斤顶定位靠山8。千斤顶底座抵靠在千斤顶定位靠山8上即获得定位,此时千斤顶5的顶升端与传动轴及顶板3中心的半圆形通孔4a共轴线。
如图11所示,底板1上设有可以嵌入千斤顶底座的千斤顶定位凹坑9。千斤顶底座嵌入千斤顶定位凹坑9中,千斤顶5即获得定位,此时千斤顶5的顶升端与传动轴及顶板3中心的半圆形通孔4a共轴线。
以上所述仅为本实用新型之较佳可行实施例而已,非因此局限本实用新型的专利保护范围。除上述实施例外,本实用新型还可以有其他实施方式。凡采用等同替换或等效变换形成的技术方案,均落在本实用新型要求的保护范围内。本实用新型未经描述的技术特征可以通过或采用现有技术实现,在此不再赘述。