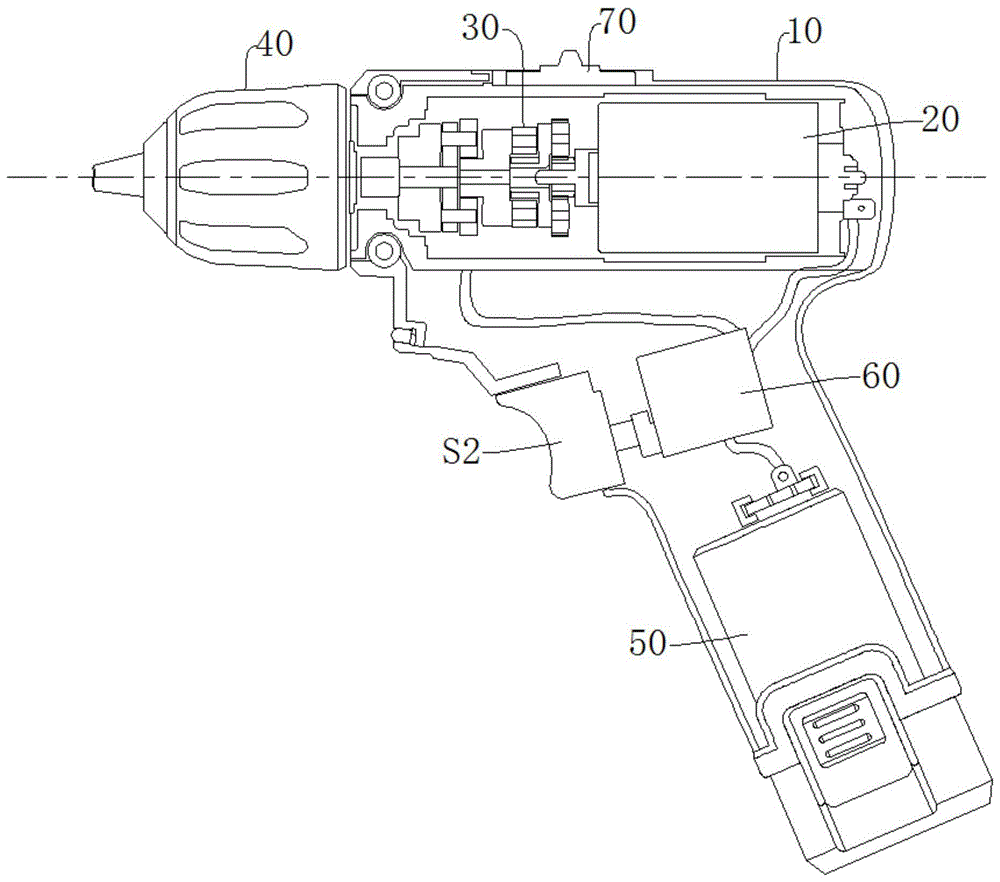
本发明涉及电动工具控制领域,具体涉及一种电动工具及其控制方法。
背景技术:
:本部分的描述仅提供与本发明公开相关的背景信息,而不构成现有技术。随着操作工况的多样性,诸如电钻或螺丝批等电动工具配置两挡或多挡调速的功能。实现多挡调速的技术方案大多为通过齿圈的移动来实现齿轮系输出不同的传动比。即,通过移动速度切换件在不同位置间移动,来实现齿轮系以不同传动比啮合,从而输出不同的转速。使用时,当工作场合对扭力要求不高时,可以使用高速挡,以获得高速低扭力。而当扭力要求较高时,可以使用低速挡,以获得低速高扭力。现有技术中,上述电动工具在进行扭力调节时,通过预先设定一个电流阈值。当电动工具在不同速度状态下达到该电流阈值时,控制电动工具停机。这样会出现不同速度挡位下,同一电流阈值所对应的实际输出扭力会不同,进而出现扭力控制不精确的情况。应该注意,上面对技术背景的介绍只是为了方便对本发明的技术方案进行清楚、完整的说明,并方便本领域技术人员的理解而阐述的。不能仅仅因为这些方案在本发明的
背景技术:
部分进行了阐述而认为上述技术方案为本领域技术人员所公知。技术实现要素:基于前述的现有技术缺陷,本发明实施例提供了一种电动工具及其控制方法,其可以在不同挡位下,在马达停机时输出的扭力一致,从而提高扭力的控制精度。为了实现上述目的,本发明提供了如下的技术方案。一种电动工具,包括:工作头;马达;变速机构,其基于所述马达的转动,驱动所述工作头工作以输出扭力;所述变速机构能被执行操作而具有不同的传动比;控制所述马达工作的控制模块,所述控制模块包括能够获取预设扭力的控制单元;所述控制单元为所述马达匹配与传动比相对应的第一电流阈值;当所述马达的实际工作电流达到所述第一电流阈值时,所述工作头的实际输出扭力与所述预设扭力趋于一致,所述控制单元控制所述马达停机。一种电动工具的控制方法,所述电动工具包括:工作头;马达;变速机构,其基于所述马达的转动,驱动所述工作头工作以输出扭力;所述变速机构能被执行操作而具有不同的传动比;所述控制方法包括:获取预设扭力以及所述变速机构的当前传动比;为所述马达匹配与所述当前传动比相对应的第一电流阈值;当所述马达的实际工作电流达到所述第一电流阈值时,所述工作头的实际输出扭力与所述预设扭力趋于一致,所述马达停机。本发明实施例的电动工具及其控制方法,通过获知或识别变速机构的传动比,并基于变速机构的传动比,为马达匹配对应的第一电流阈值。从而在工作头处于不同转速情况下,控制其在马达停机时的实际输出扭力相一致,实现对具有不同速度挡位的电动工具更为精确的扭力控制。参照后文的说明和附图,详细公开了本发明的特定实施例,指明了本发明的原理可以被采用的方式。应该理解,本发明的实施例在范围上并不因而受到限制。在所附权利要求的精神和条款的范围内,本发明的实施例包括许多改变、修改和等同。针对一种实施例描述和/或示出的特征可以以相同或类似的方式在一个或更多个其它实施例中使用,与其它实施例中的特征相组合,或替代其它实施例中的特征。应该强调,术语“包括/包含”在本文使用时指特征、整件、步骤或组件的存在,但并不排除一个或更多个其它特征、整件、步骤或组件的存在或附加。附图说明在此描述的附图仅用于解释目的,而不意图以任何方式来限制本发明公开的范围。另外,图中的各部件的形状和比例尺寸等仅为示意性的,用于帮助对本发明的理解,并不是具体限定本发明各部件的形状和比例尺寸。本领域的技术人员在本发明的教导下,可以根据具体情况选择各种可能的形状和比例尺寸来实施本发明。在附图中:图1为本发明实施例的电动工具的结构示意图;图2为本发明实施例的电动工具中移动件处于不同位置的结构示意图;图3为本发明实施例的电动工具在不同的传动比下马达电流与输出扭力的关系图;图4本根据发明第一较佳实施例的电动工具的电路示意图;图5本根据发明第一较佳实施例的电动工具的控制流程图;图6本根据发明第二较佳实施例的电动工具的控制流程图;图7本根据发明第二较佳实施例的电动工具的电路示意图;图8本根据发明第三较佳实施例的电动工具的控制流程图。具体实施例为了使本
技术领域:
的人员更好地理解本发明中的技术方案,下面将结合本发明实施例中的附图,对本发明实施例中的技术方案进行清楚、完整地描述,显然,所描述的实施例仅仅是本发明一部分实施例,而不是全部的实施例。基于本发明中的实施例,本领域普通技术人员在没有做出创造性劳动的前提下所获得的所有其他实施例,都应当属于本发明保护的范围。需要说明的是,当元件被称为“设置于”另一个元件,它可以直接在另一个元件上或者也可以存在居中的元件。当一个元件被认为是“连接”另一个元件,它可以是直接连接到另一个元件或者可能同时存在居中元件。本文所使用的术语“垂直的”、“水平的”、“左”、“右”以及类似的表述只是为了说明的目的,并不表示是唯一的实施例。除非另有定义,本文所使用的所有的技术和科学术语与属于本发明的
技术领域:
的技术人员通常理解的含义相同。本文中在本发明的说明书中所使用的术语只是为了描述具体的实施例的目的,不是旨在于限制本发明。本文所使用的术语“和/或”包括一个或多个相关的所列项目的任意的和所有的组合。承接上文描述,电钻或螺丝批等配置两挡或多挡调速功能的电动工具,其在不同速度挡位下,同一电流阈值限定工作头输出的扭力不同,将可能导致工具损坏或工作效率低下的问题。例如,在一个可设想的场景中,需要在质地较硬的工件中旋入螺钉。电动工具开始为低挡位,工作头的转速较慢。此时,工作头输出的扭力刚好满足螺钉的旋入要求。而为加快工作效率,将电动工具调至高挡位,工作头的转速变快。但电动工具的电流阈值不变,导致工作头获得的扭力反而下降。那么,当马达的实际工作电流上升至电流阈值时,马达停机,但螺钉尚为被旋入指定的深度位置。或者,在另一个可设想的场景中,需要在质地较软的工件中旋入螺钉。当电动工具为高挡位时,马达驱动工作头工作输出的扭力仍可以满足螺钉的旋入要求。这样,当螺钉被旋入达到指定的深度位置后,马达的实际工作电流仍未达到电流阈值。此时,马达将驱动工作头继续旋转。这样,需人为操作断开电动工具与螺钉的接触。否则,可能出现未能及时停机而导致螺钉旋入深度过大,进而造成工件损坏的情况。有鉴于此,本发明实施例提供了一种电动工具及其控制方法,其可以在不同速度挡位下,在马达停机时使工作头输出的扭力大致相同或相一致,实现对不同速度挡位的电动工具更为精确的扭力控制,以适应不同工况需求,提升工作效率。具体的,如图1所示,本发明实施例的电动工具包括:壳体10、设置于壳体10中的马达20、与马达20传动连接的变速机构30、被变速机构30驱动的工作头40、为马达20提供电能的供电模块50、用于控制马达20工作的控制模块60。工作头40用于夹持刀具,变速机构30基于马达20的转动驱动工作头40工作输出扭力。结合图4所示,在一个实施例中,控制模块60可以包括电子开关s1、马达开关s2、电阻r1、控制单元61、存储单元63、位置检测单元64、扭力检测单元65、电流侦测单元67及电压侦测单元68。马达20的正极通过马达开关s2与供电模块50的正极连接,负极与电子开关s1的第一端连接。电子开关s1的第二端与控制单元61的第一端连接,第三端通过电阻r1与供电模块50的负极连接。控制单元61具体可以为mcu,其第二端连接于马达开关s2与马达20之间的节点,第三端通过电压侦测单元68与马达20的正极连接,第四端与电子开关s1的第二端连接,第五端通过电流侦测单元67与电子开关s1的第三端连接,第六端与位置检测单元64连接,第七端与扭力检测单元65连接,第八端与存储单元63连接。马达开关s2为扳机,使用者按下电动工具100的扳机以启动马达20。进一步地,扳机不仅可以用于马达20的启停控制,而可以为对马达20的转速进行调节。具体的,扳机连接有电位器(电阻调节元件,例如滑动变阻器),电位器设置在控制单元61与马达20之间。扳机能被执行按压操作而使其进程深度发生变化,扳机带动电位器的电刷移动,进而改变电位器的电阻值。籍此,在供电模块50的电压不变的情况下,通过电位器的电阻值的改变,使电位器与马达20的电压得以分配,进而实现调节马达20的输入电压,以调节工作头40的转速。具体的,电位器与马达20串联。在串联回路中,电气元器件或电子设备分配的电压与其电阻值呈正相关关系。具体到本实施例中,扳机的按压进程深度增大,电位器的电阻值减小,则马达20侧的电压增大,从而工作头40的转速提升。反之,扳机的按压进程深度减小,电位器的电阻值增大,则马达20侧的电压减小,从而工作头40的转速下降。通过设置与扳机连接的电位器,则使用者可以操作扳机来对电动工具的转速进行调节,电动工具对各种工况的适应性较强。变速机构30能被执行操作而具有不同的传动比。变速机构30的传动比不同时,相当于电动工具在不同的速度挡位下运行。如上文描述,变速机构30可以包括行星轮系。行星轮系以不同的方式啮合,即可获得相对应的传动比。变速机构30在不同的传动比之间切换,可以是电动工具100在运行过程中自动调节实现的。例如,变速机构30可以设置有与控制单元61信号连接的操作件。该操作件可基于控制单元61发来的控制信号,操作行星轮系的啮合方式发生变化,从而使变速机构30获得不同的传动比。或者,变速机构30在不同的传动比之间切换,也可以通过人为操作来实现。如图1和图2所示,变速机构30设有移动件70,移动件70能被使用者执行操作,以在不同的位置之间切换。从而行星轮系以不同的方式啮合,使变速机构30获得不同的传动比。在本实施例中,控制单元61可以感知或识别变速机构30的传动比及传动比变化。具体的,位置检测单元64可以用于检测变速机构30当前所处工作状态。由于变速机构30所处不同的工作状态对应不同的传动比。由此,控制单元61即可通过位置检测单元64获知变速机构30的传动比。如图2所示,位置检测单元64可以包括设置在移动件70上的触发元件641,以及与控制单元61相连接的检测元件642。移动件70可以以拨纽或移动纽的形式外露于壳体10,以方便使用者操作。移动件70相当于电动工具的换挡操作件。使用者通过对其执行拨动操作,实现电动工具的换挡,输出不同的转速。触发元件641可以设置在移动件70的下表面,从而移动件70可以带动触发元件641移动。检测元件642设置在触发元件641的下方,且两者之间间隔。检测元件642可以感应触发元件641发出的信号,并将信号发送给控制单元61。控制单元61可以根据检测触发元件641发来的信号,识别变速机构30的当前传动比。触发元件641可以为任意能够产生光/电/磁等信号的器件。相应的,检测元件642为能够接收或感应上述信号的结构。例如,触发元件641为光源(例如,包括但不限于led、oled、红外光源等在内的发光器件),检测元件642对应为光传感器。或者,触发元件641为能够产生磁场的磁性元件(例如,磁铁),检测元件642对应为磁场传感器(例如,霍尔传感器)。控制单元61能够获取预设扭力,该预设扭力为期望输出扭力。控制单元61可以为马达20匹配与传动比相对应的第一电流阈值。当马达20的实际工作电流达到第一电流阈值时,工作头40的实际输出扭力与预设扭力趋于一致,控制单元61控制马达20停机。在本实施例中,工作头40的实际输出扭力与预设扭力趋于一致可以为,实际输出扭力与预设扭力的差值在[0,t']的预定范围内。其中,预定范围的上限值t'可以根据不同的工作场景而变化,本发明实施例对此不作限定。例如,在某一场景下,预设扭力为10kgf.cm,工作头40的实际输出扭力与预设扭力的上限差值为1kgf.cm。则当工作头40的实际输出扭力在[9,11]kgf.cm的范围内,均可以认为工作头40的实际输出扭力与预设扭力趋于一致。由于变速机构30的传动比不同,工作头40的转速也不同。因此,欲使工作头40在不同转速情况下,在马达20停机时具有相一致的输出扭力,则第一电流阈值也不同。如图3所示,当变速机构30在换挡或变速之前,其传动比为c1(c1较大,相当于慢挡),第一电流阈值为i1。当马达20的实际工作电流达到第一电流阈值i1时,停机,工作头40的实际输出扭力为n1。随后,变速机构30被执行换挡或变速操作后,其传动比变为c2(c2小于c1,相当于快挡),工作头40的转速变快。此时,如果欲使马达20停机时,工作头40所获得的实际输出扭力仍与变速前一致(趋近于n1),则此时的第一电流阈值应升高至i1’。这样,工作头40才有可能在传动比为c2即转速加快的情况下,仍能在马达20停机时输出与增速前相一致的扭力。也就是说,为了在不同挡位情况下,当马达20停机时使工作头40的实际输出扭力保持一致,第一电流阈值与传动比呈反相关关系。具体解释为,传动比增大(即工作头40的转速减小),第一电流阈值降低。而传动比降低(即工作头40的转速增大),第一电流阈值升高。籍此,通过控制单元61获知或识别变速机构30的传动比,并基于变速机构30的传动比,为马达20匹配对应的第一电流阈值。从而在工作头40处于不同转速情况下,控制其在马达20停机时的实际输出扭力相一致,实现对具有不同速度挡位的电动工具更为精确的扭力控制。并且,当马达20的实际工作电流达到第一电流阈值时停机,由于工作头40的实际输出扭力相一致,从而在不同传动比情况下,工件达到一致的深度,以方便经验较少的使用者操作本发明实施例的电动工具。在一个实施例中,预设扭力的获取,可以是从存储单元63预存的数据中调取的方式实现。预设扭力可事先预置于存储单元63中,与存储单元63连接的控制单元61调取存储于存储单元63中的预设扭力,实现预设扭力的获得。或者,在上述方式的基础上,预设扭力的获取,也可以为存储单元63主动提供给控制单元61的方式。进一步地,预置于存储单元63中的预设扭力的数量可以是一个,也可以是多个。当预置的预设扭力的数量为一个时,控制单元61通过主动或被动的方式从存储单元63中获得该预设扭力。则电动工具的挡位不同时,工作头40的实际输出扭力趋于一致。当预置的预设扭力的数量为多个时,控制单元61通过主动或被动的方式从存储单元63中获得一个预设扭力。则可实现工作头40实际输出扭力可调。控制单元61从预置于存储单元63中的多个预设扭力获取一个的方式,可以是人为操作来实现。具体的,举例为,电动工具的壳体10上可设置有旋钮或拨块,旋钮或拨块可允许使用者对其执行相应的旋转或拨动操作,以改变其位置。旋钮或拨块处于不同位置,对应不同的预设扭力输入值。当旋钮或拨块被执行操作而位于某一位置时,该位置可指向对应的预设扭力,实现该位置对应的预设扭力的选择和调取。在一种可行的实现方式中,控制单元61可基于旋钮或拨块的操作,主动的从存储单元63中获取预设扭力值。具体的,旋钮或拨块上可设置有类似于上文所述的可发出光/电/磁等信号的触发元件,控制单元61连接可感应光/电/磁等信号的检测元件。旋钮或拨块被执行操作时带动触发元件与之一起运动,检测元件感应触发元件发出的信号,并将该信号提供给控制单元61。控制单元61基于该信号,从存储单元63中请求调取相应的预设扭力值。在另一种可行的实现方式中,存储单元63可基于旋钮或拨块的操作而将预设扭力值提供给控制单元61。具体为,在上述实现方式的基础上,可感应光/电/磁等信号的检测元件与存储单元63连接。旋钮或拨块被执行操作带动触发元件与之一起运动,检测元件感应触发元件发出的信号,存储单元63基于该信号,将相应的预设扭力值提供给控制单元61。上述两种可行的方式,分别对应于控制单元61以主动的方式获取预设扭力(具体为向存储单元63请求调取),及以被动的方式接收预设扭力(具体为存储单元63向其提供)。在另一个实施例中,预设扭力的获取,可以是控制单元61接收扭力检测单元65输入的方式。具体的,电动工具还可以包括与扭力检测单元65连接的扭力调节装置(未示出),其用于可操作的设定预设扭力。扭力检测单元65可以获得到扭力调节装置由于被操作而输入的预设扭力。扭力调节装置可允许使用者对其执行旋转操作,实现对电动工具100的期望输出扭力的设定。同样的,扭力调节装置可包括接收使用者的操作的旋钮或拨块,旋钮上可设置类似于上文所述的可发出光/电/磁等信号的触发元件,触发元件对应设置可感应光/电/磁等信号且与扭力检测单元65连接的检测元件。旋钮或拨块处于不同位置,对应不同的预设扭力输入值。旋钮或拨块被执行操作时,带动触发元件与之一起运动,从而检测元件可以感应触发元件发出的信号,进而识别与当前位置相对应的预设扭力。检测元件将识别的预设扭力输入至控制单元61。扭力调节装置不仅可以用作预设扭力的设定,还可以用于电动工具的工作模式的选择。电动工具的工作模式包括输出扭力可调的螺丝批模式,以及输出扭力不可调的枪钻模式。扭力调节装置的旋钮可在预定角度的范围内旋转,该旋转范围内的某一个特定的位置(例如,旋转范围的两个死点中的一个或者两个)对应为枪钻模式,在该位置(简称枪钻模式位置)下,电动工具的预设扭力锁定,工作头40实际输出的扭力不可调。而当旋钮处于该旋转范围内除去枪钻模式位置外的其他任意位置时,电动工具处于螺丝批模式。且旋钮在该旋转范围内除去枪钻模式位置外的其他位置发生变化时,预设扭力随之改变,实现工作头40实际输出扭力的调节。为了基于传动比获取第一电流阈值,存储单元63中预置有第一电流阈值与传动比对应之间的对应关系。在一个实施例中,电流阈值与传动比的对应,可以为一一对应的关系,即一个传动比唯一对应一个电流阈值。存储单元63中预先存储有电流阈值集{i1,i2…in},该电流阈值集包含有多个不同的第一电流阈值,或者,包含有多个不同的第一电流阈值组成该电流阈值集。如表1所示,存储单元63可以预先存储传动比与第一电流阈值的对应关系。基于这种对应关系,根据传动比,可以唯一关联或映射到一个第一电流阈值。表1传动比与第一电流阈值的对应关系表传动比第一电流阈值c1i1c2i2……cnin传动比与第一电流阈值之间一一对应关系,可依照上述表1所示的数据表的形式存储于存储单元63中。数据表的一列存储传动比,另一列存储第一电流阈值。相对应的传动比与第一电流阈值处于同一行。或者,也可以为第一电流阈值和传动比的索引对应存储。具体的,为传动比制定编号,例如,传动比c1、c2…cn的编号依次为1、2…n,寓意为1挡、2挡…n挡。该编号即为对应的传动比的索引,通过该索引可以唯一确定对应的传动比。将传动比的索引与第一电流阈值对应存储。由此,当控制单元61通过位置检测单元64获取变速机构30的当前传动比,根据存储单元63中预先存储的第一电流阈值与传动比之间的对应关系,即可获取与当前传动比相对应的第一电流阈值。在本实施例中,与所有传动比相关联的电流阈值所对应的工作头40的实际输出扭力是相一致的。即当变速机构30的传动比不同时,为马达20匹配的第一电流阈值也不同,但当马达20的实际工作电流达到第一电流阈值时,工作头40的实际输出扭力与预设扭力是一致的。亦即,工作头40实际输出的扭力不可调。举例为,参照表1所示,当变速机构30的传动比为c1时,为马达20匹配的第一电流阈值为i1。而当变速机构30的传动比为c2时,为马达20匹配的第一电流阈值为i2。在这两种情况下,当马达20的实际工作电流分别达到i1和i2时,工作头40的实际输出扭力均与预设扭力相一致。在该实施例下,控制模块60控制电动工具100的流程如下:获取预设扭力以及变速机构30的当前传动比;其中,变速机构30的当前传动比通过位置检测单元64获取,预设扭力按照上述所述方式获取;在此不作赘述;基于存储模块63中预置的第一电流阈值与传动比之间的对应关系,获取与当前传动比相对应的第一电流阈值;当马达20的实际工作电流达到第一电流阈值时,控制马达20停机,工作头40的实际输出扭力与预设扭力趋于一致。籍此,当使用者操作移动件70而使变速机构30的传动比发生变化时,位置检测单元64可以感知变速机构30变化后的传动比(即当前传动比),并将该变化后的传动比提供给控制单元61。控制单元61基于该变化后的传动比,在预置的传动比与第一电流阈值的对应关系或映射表中,匹配得到与该变化后的传动比相对应的第一电流阈值。这样,当马达20的实际工作电流达到第一电流阈值时停机,工作头40的实际输出扭力,与变速机构30的传动比变化之前相一致。从而,实现精确控制扭力,使得工件达到一致的深度。在另一个实施例中,第一电流阈值与传动比的对应,还可以为一对多的对应关系。即一个传动比对应多个第一电流阈值。而与一个传动比对应的多个第一电流阈值,则与预设扭力一一对应。具体的,获取的预设扭力与第一电流阈值一一对应。预设扭力包括上文所述的通过扭力检测单元65来检测扭力调节装置输入的,以及从预先存储的数据中调取的。从上文描述可知,工作头40实际输出的扭力,不一定与预设扭力完全相同。而在这里预先设置预设扭力的目的,是为了获取在某一个传动比下的第一电流阈值。那么,后续当马达20的实际工作电流达到该第一电流阈值时,工作头40的实际输出扭力,才能够趋近于该预设扭力。如表2所示,电流阈值集中多包涵的多个第一电流阈值被划分为多个电流阈值组[i11,i12…i1m]、[i21,i22…i2m]…[in1,in2…inm]。电流阈值组的数量与传动比的数量相等,每个电流阈值组对应一个传动比。而每个电流阈值组中所包含的第一电流阈值的数量与预设扭力相等,则每个电流阈值组中所包含的第一电流阈值与预设扭力一一对应。也就是说,在该实施例中,由传动比和预设扭力共同确定一个第一电流阈值。同样的,第一电流阈值与传动比、预设扭力之间的对应关系,可依照表2所示的数据表的形式存储于存储单元63中。数据表的一列存储传动比,另一列存储预设扭力,再另外一列存储第一电流阈值。相对应的传动比、预设扭力与第一电流阈值处于同一行。表2传动比、预设扭力与第一电流阈值的对应关系表或者,也可以为第一电流阈值和传动比的索引、预设扭力对应存储。具体的,为传动比制定编号,例如,传动比c1、c2…cn的编号依次为1、2…n,寓意为1挡、2挡…n挡。该编号即为对应的传动比的索引,通过该索引可以唯一确定对应的传动比。将传动比的索引、预设扭力与第一电流阈值对应存储。亦或者,也可以为第一电流阈值和传动比、预设扭力的索引对应存储。具体的,为预设扭力制定编号,例如,预设扭力n1、n2…nm的编号依次为1’、2’…m’。该编号即为对应的预设扭力的索引,通过该索引可以唯一确定对应的预设扭力。将传动比、预设扭力的索引与第一电流阈值对应存储。又或者,也可以为第一电流阈值和传动比的索引、预设扭力的索引对应存储。具体可参照上文描述,在此不作赘述。由此,当控制单元61通过位置检测单元64获取变速机构30的当前传动比,以及通过扭力检测单元65检测电动工具100的当前预设扭力之后,根据第一电流阈值与传动比、预设扭力之间的对应关系,即可获取与当前传动比和当前预设扭力相对应的第一电流阈值。在该实施例中,当预设扭力相同时,与所有传动比相关联的电流阈值所对应的工作头40的实际输出扭力是相一致的。即当预设扭力相同、而变速机构30的传动比不同时,为马达20匹配的第一电流阈值也不同,但当马达20的实际工作电流达到第一电流阈值时,工作头40的实际输出扭力是一致的。举例为,当变速机构30的预设扭力为n1、传动比为c1时,为马达20匹配的第一电流阈值为i11。而当变速机构30的预设扭力为n1、传动比为c2时,为马达20匹配的第一电流阈值为i21。在这两种情况下,当马达20的实际工作电流分别达到i11和i21时,工作头40的实际输出扭力均与n1相一致。在该实施例下,控制模块60控制电动工具100的流程如下:通过位置检测单元64,获取变速机构30的当前传动比;通过扭力检测单元65检测当前预设扭力的值;基于第一电流阈值与传动比、预设扭力之间的对应关系,获取与当前传动比以及当前预设扭力相对应的第一电流阈值;当马达20的实际工作电流达到第一电流阈值时,控制马达20停机,工作头40的实际输出扭力与预设扭力趋于一致。本实施例通过在设置与扭力检测单元65来检测电动工具的预设扭力,并基于该预设扭力与当前传动比一起确定第一电流阈值,从而在电动工具于同一个传动比下具有多个不同的输出扭力的前提下,扩展工作头40的实际输出扭力的数量,即输出扭力可调,进而提高电动工具100的适用范围。例如,在一种场景中,电动工具100先在质地较软的工件中打入螺钉,其传动比为c1(较小,相当于快挡),设定的扭力为满足该工况条件下的值(较小),对应匹配的第一电流阈值为也较小。随后,电动工具100切换至另一个工作模式:在质地较硬的工件中打入螺钉。而为了提高工作效率,想沿用原来的传动比c1。此时,如果预设扭力也依然采用原来的值,第一电流阈值将不变。那么,在质地较硬的工件打入螺钉,马达20的负载增大,其实际工作电流可能很快达到第一电流阈值。那么,在马达20停机时,螺钉可能并未达到指定的深度。而采用本发明实施例的方案,当电动工具100切换至另一个工作模式时,可以根据该工作模块的情况,选择一个较大的预设扭力值。那么,控制单元61将为马达20匹配一个较大的第一电流阈值。如此,即便由于该工况会导致马达20在操作过程中的实际工作电流升高的较快,但由于匹配的第一电流阈值也相应的增大了。从而,依然可以满足在马达20停机时,螺钉能被顺利的旋入指定的深度。马达20在其实际工作电流达到第一电流阈值时停机的实现方式为,控制单元61通过电流侦测单元67侦测马达20的实际工作电流,并将侦测到的马达20的实际工作电流与第一电流阈值比较。当马达20的实际工作电流达到第一电流阈值i1时,控制单元61停止输出驱动信号,以控制马达20停机。在本实施例中,电动工具的具体控制流程如图5所示:步骤s101:通过检测元件642和触发元件641检测移动件70的位置,进而识别变速机构30的当前传动比;步骤s102:通过扭力检测单元65检测当前预设扭力的值;步骤s103:基于当前传动比和当前预设扭力的值,为马达20匹配第一电流阈值;步骤s104:使用者按下电动工具100的扳机以启动马达20;步骤s105:通过电流侦测单元67实时侦测马达20的实际工作电流;步骤s106:判断马达20的实际工作电流是否达到第一电流阈值,是则进入步骤s107,否则返回步骤s105;步骤s107:当马达20的实际工作电流达到第一电流阈值时,控制马达20停机。在另一个实施例中,控制单元61设定低于第一电流阈值的第二电流阈值。当电流检测单元67检测到马达的实际工作电流达到第二电流阈值时,控制单元61控制马达20维持在转速预定值。由于马达20的转速与电压及电流有关,且在负载增大时,马达20的实际工作电流也相应的增大。若需维持马达20的转速,则需要增大的马达20的电压。因此,可以根据侦测的马达20的实际工作电流计算维持转速预定值所需的电压值,再将马达20的实际电压调节到计算得到的电压值以维持马达转速为转速预定值。存储单元63中存储有转速预定值,电流侦测单元67侦测马达20的实际工作电流,控制单元61根据转速预定值及侦测到的马达20的实际工作电流计算维持转速预定值所需的电压值,控制单元61以计算得到的电压值为基准电压。电压侦测单元68实时侦测马达20的实际电压,控制单元61根据侦测的实际电压与基准电压之差调节控制单元61输出的驱动信号,从而维持马达20的转速。驱动信号为脉宽调制信号。若马达20的实际电压超过基准电压时,控制单元61减小驱动信号的占空比。若马达20的实际电压小于基准电压时,控制单元61增大驱动信号的占空比。在本实施例中,存储单元63中存储有若干预定的常数,每一预定的常数与不同的第一电流阈值对应,第一电流阈值减去预定的常数,得到第二电流阈值。第二电流阈值也可通过软件的方式计算得到。存储单元63存储第一电流阈值及第二电流阈值。当马达20的实际工作电流达到第二电流阈值时,控制单元61控制马达20的转速保持在转速预定值,此时马达20的电流随之升高。在维持马达20转速的同时,控制单元61通过电流侦测单元67继续侦测马达20的实际工作电流,并将侦测的马达20的实际工作电流与第一电流阈值比较。当侦测的马达20的实际工作电流达到第一电流阈值时,控制单元61停止输出驱动信号,以控制马达20停机。在该实施例中,电动工具的具体控制流程如图6所示:步骤s201:通过检测元件642和触发元件641检测移动件70的位置,进而识别变速机构30的当前传动比;步骤s202:通过扭力检测单元65检测当前预设扭力的值;步骤s203:基于当前传动比和当前预设扭力的值,为马达20匹配第一电流阈值;步骤s204:基于匹配得到的第一电流阈值,自动计算第二电流阈值,且第二电流阈值低于第一电流阈值,第一电流阈值等于第二电流阈值与预定的常数之和。本实施例中,第二电流阈值由手持电动工具100中的控制单元61计算得到;步骤s205:使用者按下电动工具100的扳机以启动马达20;步骤s206:通过电流侦测单元67实时侦测马达20的实际工作电流;步骤s207:判断马达20的实际工作电流是否达到第二电流阈值,是则进入步骤s208,否则返回步骤s206;步骤s208:当马达20的实际工作电流达到第二电流阈值i2时,控制马达20的转速保持在转速预定值;步骤s209:判断马达20的实际工作电流是否达到第一电流阈值i1,是则进入步骤s210,否则返回步骤s208;步骤s210:当马达20的实际工作电流达到第一电流阈值i1时,控制马达20停机。如图7所示,在另一个实施例中,控制模块60进一步可以包括限流单元66。限流单元66连接在电子开关s1和控制单元61之间,且限流单元66与电流侦测单元67连接。电流侦测单元67侦测马达20的实际工作电流,限流单元66将侦测的马达20的实际工作电流与第二电流阈值比较。当马达20的实际工作电流达到第二电流阈值时,限流单元66控制马达20的电流保持在第二电流阈值,此时马达20的转速随之下降。具体地,限流单元66具有比较器。比较器在侦测到的马达20的实际工作电流小于第二电流阈值时输出导通信号,在侦测到的马达20的实际工作电流大于等于第二电流阈值时输出关断信号。导通/关断信号被反馈到控制单元61输出的驱动信号中,从而将马达20的电流值维持在第二电流阈值。在维持马达20的实际工作电流的同时,控制单元61判断马达20的转速并在马达20转速下降到转速预定值时,控制单元61控制马达20的转速保持在转速预定值。转速预定值低于一般工作状态时的马达20转速,如此在后续的控制中马达20能够快速地做出反应。由上文可知,当马达20的实际工作电流恒定时,马达20电压越小,马达20的转速越低。控制单元61通过电压侦测单元68侦测马达20的实际电压,从而判断马达20的转速。存储单元63中存储有转速预定值,控制单元61计算马达20的转速为转速预定值、马达20的实际工作电流为第二电流阈值时的马达电压,电压侦测单元68侦测马达20的实际电压。当马达20的实际电压下降到控制单元61计算的马达电压值时,控制单元61控制马达20的转速保持在转速预定值。控制单元61根据转速预定值及侦测的马达20的电流计算维持转速预定值所需的电压值,并以维持转速预定值所需的电压值为基准电压。控制单元61通过电压侦测单元68侦测马达20的实际电压,根据侦测的实际电压与基准电压之差调节控制单元61输出的驱动信号,从而维持马达20的转速。在维持马达20转速的同时,控制单元61通过电流侦测单元67继续侦测马达20的实际工作电流,并将侦测的马达20的实际工作电流与第一电流阈值比较。当侦测的马达20的实际工作电流达到第一电流阈值时,控制单元61停止输出驱动信号,以控制马达20停机。在该实施例中,电动工具的具体控制流程如图8所示:步骤s301:通过检测元件642和触发元件641检测移动件70的位置,进而识别变速机构30的当前传动比;步骤s302:通过扭力检测单元65检测当前预设扭力的值;步骤s303:基于当前传动比和当前预设扭力的值,为马达20匹配第一电流阈值;步骤s304:基于匹配得到的第一电流阈值,自动计算第二电流阈值,且第二电流阈值低于第一电流阈值,第一电流阈值等于第二电流阈值与预定的常数之和。本实施例中,第二电流阈值由手持电动工具100中的控制单元61计算得到;步骤s305:使用者按下电动工具100的扳机以启动马达20;步骤s306:通过电流侦测单元67实时侦测马达20的实际工作电流;步骤s307:判断马达20的实际工作电流是否达到第二电流阈值,是则进入步骤s308,否则返回步骤s306;步骤s308:当马达20的实际工作电流达到第二电流阈值时,维持马达20的电流为第二电流阈值;步骤s309:判断马达20的转速是否下降到转速预定值,是则进入步骤s310,否则返回步骤s308;步骤s310:控制马达20的转速维持在转速预定值;步骤s311:判断马达20的实际工作电流是否达到第一电流阈值,是则进入步骤s312,否则返回步骤s310;步骤s311:当马达20的实际工作电流达到第一电流阈值时,控制马达20停机。需要说明的是,在本发明的描述中,术语“第一”、“第二”等仅用于描述目的和区别类似的对象,两者之间并不存在先后顺序,也不能理解为指示或暗示相对重要性。此外,在本发明的描述中,除非另有说明,“多个”的含义是两个或两个以上。应该理解,以上描述是为了进行图示说明而不是为了进行限制。通过阅读上述描述,在所提供的示例之外的许多实施例和许多应用对本领域技术人员来说都将是显而易见的。因此,本教导的范围不应该参照上述描述来确定,而是应该参照前述权利要求以及这些权利要求所拥有的等价物的全部范围来确定。出于全面之目的,所有文章和参考包括专利申请和公告的公开都通过参考结合在本文中。在前述权利要求中省略这里公开的主题的任何方面并不是为了放弃该主体内容,也不应该认为申请人没有将该主题考虑为所公开的发明主题的一部分。当前第1页12