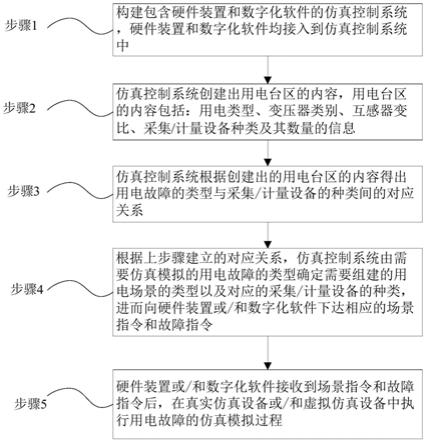
1.本发明属于电力设备领域,具体涉及一种软硬件协同的多场景用电故障的模拟仿真方法。
背景技术:2.随着能源互联网、营配融合和智慧物联体系在电力系统中的快速推进,低压配变台区中的用电信息采集终端、智能电能表、低压居民智能计量箱等设备正在被广泛投入使用。现有的电力系统中,数据采集和运维的节点多覆盖面广,这使得采集故障的分析与处理的复杂程度也相应提高。在这种状况下,用电故障的分析和处理对个人的专业能力依赖性增强。因此,如何通过创建故障仿真场景开展采集运维培训,提高一线采集运维人员的业务水平成为各基层供电单位需要面对的急迫问题。
3.现有的采集运维培训主要依赖真实的用电场景,相关的用电故障仿真场景少有建设。偶有少量的供电所单位进行简单的故障场景模拟建设,也通常只用于某些简单的故障模拟,仿真度不高,与真实的现场场景和电力系统的拓扑结构差异较大。这非常不利于开展采集运维人员的技能专业培训,不利于加强运维服务团队的队伍建设。
技术实现要素:4.为解决现有技术中难以开展用电故障的模拟仿真,或模拟仿真的用电场景单一、场景元素互联互通性不强,场景模拟范围小,台区设备数量容量小等问题;本发明提供一种软硬件协同的多场景用电故障的模拟仿真方法。
5.本发明采用以下技术方案实现:
6.一种软硬件协同的多场景用电故障的模拟仿真方法,该模拟仿真方法包括如下步骤:
7.步骤1:构建包含硬件装置和数字化软件的仿真控制系统,硬件装置和数字化软件均接入到仿真控制系统中。
8.其中,硬件装置中的包括真实仿真设备;数字化软件中包括虚拟仿真设备,真实仿真设备和虚拟仿真设备分别用于在各自启用状态下执行故障的仿真模拟过程。
9.步骤2:仿真控制系统创建出用电台区的内容,用电台区的内容包括:用电类型、变压器类别、互感器变比、采集/计量设备种类及其数量的信息。
10.步骤3:仿真控制系统根据创建出的用电台区的内容得出用电故障的类型与采集/计量设备的种类间的对应关系。
11.步骤4:根据上步骤建立的对应关系,仿真控制系统由需要仿真模拟的用电故障的类型确定需要组建的用电场景的类型以及对应的采集/计量设备的种类,进而向硬件装置或/和数字化软件下达相应的场景指令和故障指令。
12.步骤5:硬件装置或/和数字化软件接收到场景指令和故障指令后,在真实仿真设备或/和虚拟仿真设备中执行用电故障的仿真模拟过程。
13.进一步地,步骤1中,硬件装置用于接收由仿真控制系统下发的场景指令和故障指令,进而组建相应的用电场景,并在真实仿真设备中实时反馈用电场景中硬件装置的故障状态和运行状态;数字化软件用于接收由仿真控制系统下发的场景指令和故障指令,进而完成数据建模,虚拟化出仿真设备模型的电气状态和结构形态,组建相应的用电场景,并在虚拟仿真设备中实时反馈用电场景中仿真设备模型的故障状态和运行状态。
14.进一步地,步骤3中,用电故障的类型包括一类故障、二类故障、三类故障、四类故障、五类故障、六类故障和七类故障;一类故障具体包括:时间错误、时钟电池故障、rs485端口故障、esam损坏、esam密钥未下发、设备电源损坏、软件运行故障、系统死机、交采芯片损坏、采集数据存储错误、本地通信模块损坏、可恢复hplc模块串口异常、不可恢复hplc模块串口异常;二类故障具体包括:数据未采集、户表档案错误、设备档案错误、终端任务错误、远程通信模块端口故障、远程通信模块设备损坏;三类故障为供电电池/电容故障;四类故障为本地载波通信端口故障;五类故障为电能表计量异常;六类故障为控制模块损坏;七类故障为控制模块继电器故障。
15.进一步地,与一类故障建立对应关系的采集/计量设备的种类为单相电能表、三相四线电能表、集中器或专变终端;与二类故障建立对应关系的采集设备的种类为集中器或专变终端;与三类故障建立对应关系的采集/计量设备的种类为三相四线电能表、集中器或专变终端;与四类故障建立对应关系的采集/计量设备的种类为单相电能表、三相四线电能表或集中器;与五类故障建立对应关系的计量设备的种类为单相电能表或三相四线电能表;与六类故障建立对应关系的采集设备的种类为专变终端;与七类故障建立对应关系的采集/计量设备的种类为单相电能表、三相四线电能表或专变终端。
16.进一步地,步骤4中,用电场景的类型包括场景1、场景2、场景3、场景4、场景5和场景6。
17.其中,场景1、场景2、场景3、场景4分别定义为:“低压
‑
杆变/箱变
‑
全载波抄表”、“低压
‑
杆变/箱变
‑
半载波抄表”、“低压
‑
杆变/箱变
‑
混合抄表”、“低压
‑
杆变/箱变
‑
ii型集中器抄表”;场景1、场景2、场景3中包含的设备种类均包括电流互感器、集中器、采集器、三相电能表和单相电能表;场景4中包含的设备种类包括:电流互感器、集中器、三相电能表和单相电能表。
18.场景5定义为“专变
‑
杆变/箱变
‑
高供低计”,场景5包含的设备种类包括:电流互感器、集中器、采集器、三相电能表和单相电能表;场景6定义为“专变
‑
杆变/箱变
‑
高供高计”,场景6包含的设备种类包括:电流互感器、电压互感器、集中器和三相电能表。
19.进一步地,场景1、场景2、场景3、场景4对应的用户类别为公变用户;场景5和场景6对应的用户类别为专变用户。
20.进一步地,步骤5中,用电故障的仿真模拟包括三种方式;第一种方式是由硬件装置单独模拟出用电故障;第二种方式是由数字化软件单独仿真出用电故障;第三种方式是由硬件装置和数字化软件综合仿真模拟出用电故障;仿真控制系统根据用电故障类型优先采用第一种方式进行模拟仿真;在硬件装置无法满足模拟仿真所需的资源要求时,采用第三种方式;在硬件装置完全无法实现时模拟仿真过程时,采用第二种方式。
21.进一步地,硬件装置单独模拟出用电故障的过程如下:
22.(1)仿真控制系统选择对应的硬件装置。
23.(2)硬件装置中的真实仿真设备准备好设备位置、类型、数量、资产、地址、故障状态的信息,并上报给硬件装置;硬件装置获取真实仿真设备的设备位置、类型、数量、资产、地址、故障状态的信息,以及自身的地址、资产的信息,并上报给仿真控制系统。
24.(3)仿真控制系统获取硬件装置和真实仿真设备的故障状态、位置、地址、资产号的信息。
25.(4)仿真控制系统准备台区数据信息。
26.(5)采集终端将上线状态上报至仿真控制系统。
27.(6)仿真控制系统将用电台区信息、故障设备关联信息与硬件装置状态信息进行比对,匹配后将台区信息和故障信息下发给硬件装置,硬件装置接收台区信息后组建用电台区,并转发故障信息至真实仿真设备。
28.(7)硬件装置实时监控真实仿真设备的故障状态,用于支撑用电台区教学、培训、竞赛。
29.(8)用电台区结束时,硬件装置上报结束指令至仿真控制系统,仿真控制系统配置台区重置信息、故障重置信息,并下发给硬件装置。
30.(9)硬件装置接收台区重置指令,解除台区,并转发设备故障重置指令至真实仿真设备,真实仿真设备重置故障。
31.(10)仿真控制系统接收硬件装置的台区重置状态及真实仿真设备的故障重置状态,故障仿真场景模拟流程结束。
32.进一步地,数字化软件单独仿真出用电故障的过程如下:
33.(1)仿真控制系统选择对应的数字化软件。
34.(2)仿真控制系统准备台区信息,并向数字化软件发出台区数据建模请求;台区信息的内容包括台区类型以及台区设备种类和数量。
35.(3)数字化软件生成台区信息创建成功的结果,并反馈至仿真控制系统。
36.(4)台区信息创建成功后,仿真控制系统准备虚拟仿真设备的参数信息,并向数字化软件发出虚拟仿真设备的参数信息数据建模的创建请求;虚拟仿真设备的参数信息包括设备类型、资产号和地址。
37.(5)数字化软件生成虚拟仿真设备的参数信息创建成功的结果,并反馈至仿真控制系统。
38.(6)虚拟仿真设备的参数信息创建成功后,仿真控制系统准备仿真故障信息,向数字化软件发出故障参数信息数据建模请求。
39.(7)数字化软件生成故障参数信息数据建模成功的结果,并反馈至仿真控制系统;仿真控制系统对数字化软件中的虚拟仿真设备的故障状态进行监控,并基于虚拟仿真设备开展用电信息采集运维教学、培训与竞赛。
40.(8)当需要结束用电台区场景时,仿真控制系统准备虚拟仿真设备的故障重置参数和台区清除参数,向数字化软件发出仿真故障参数重置和台区清除请求。
41.(9)数字化软件启动虚拟仿真设备的故障数据重置过程并释放台区信息,结束软件模拟场景流程。
42.进一步地,硬件装置和数字化软件综合仿真模拟出用电故障的过程如下:
43.(1)仿真控制系统选择对应的硬件装置和数字化软件。
44.(2)真实仿真设备准备好设备位置、类型、数量、资产、地址、故障状态的信息,并上报给硬件装置;硬件装置获取真实仿真设备的位置、类型、数量、资产、地址、故障状态的信息,及自身的地址、资产的信息,并上报给等待仿真控制系统。
45.(3)采集终端将上线状态上报给仿真控制系统。
46.(4)仿真控制系统准备好台区信息,台区信息包括台区类型、设备种类和数量。
47.(5)仿真控制系统根据台区信息,优先选择硬件装置中设备进行匹配和关联,对于硬件装置中的设备资源不能满足的,再创建软件台区,并分配剩余的设备种类和数量。
48.(6)硬件装置组建硬件台区,接收故障指令,并转发至真实仿真设备,真实仿真设备执行由该部分负责的故障模拟内容。
49.(7)数字化软件接收台区信息和故障信息,组建虚拟的软件台区;生成虚拟仿真设备的参数信息,虚拟仿真设备执行由该部分负责的故障模拟内容;软件台区与硬件台区在拓扑结构上从属于同一个台区。
50.(8)基于硬件台区和软件台区组合,构建在同一个台区拓扑结构下的大容量用电台区的仿真场景。
51.(9)结束台区场景时,仿真控制系统接收结束指令,配置台区清除信息和故障重置信息,并同时下发给数字化软件和硬件装置,数字化软件和硬件装置接收该指令后,数字化软件重置虚拟仿真设备的参数,释放用电台区;硬件装置解除用电台区,并下发故障重置指令至真实仿真设备,真实仿真设备进行故障重置,并恢复正常状态;综合模拟场景流程结束。
52.本发明提供的技术方案,具有如下有益效果:
53.本发明采用一种软硬件协同的方式,实现了对多场景、不同故障类型的模拟和仿真。从而为电力系统开展人员培训,创建大台区、多设备场景,以及在电力系统客户侧开展用电采集运维竞赛等活动奠定软硬件基础。该方法相对现有的简单模拟设备而言,可以模拟仿真出范围更大的复杂用电场景,场景元素互联互通性强,台区设备数量更多,也更接近于实际用电台区内的场景状态。
54.本发明提供的方法优先采用硬件装置进行用电故障的模拟仿真,并将数字化软件做为硬件装置的补充,因此该仿真控制系统模拟出的场景可以更加直观地展现真实的用电故障场景,具有更好的场景沉浸感,可以使得使用该方法进行培训的人员具有更好学习效果。同时数字化软件也可以独立实现硬件装置无法完成的用电故障模拟仿真场景。
附图说明
55.附图用来提供对本发明的进一步理解,并且构成说明书的一部分,与本发明的实施例一起用于解释本发明,并不构成对本发明的限制。在附图中:
56.图1为本发明实施例1中一种软硬件协同的多场景用电故障的模拟仿真方法的流程图;
57.图2为本发明实施例1中仿真控制系统的与硬件装置、数字化软件之间的拓扑关系示意图;
58.图3为本发明实施例1中,基于硬件装置的用电故障模拟过程的流程图;图4为本发明实施例1中,基于数字化软件的用电故障模拟过程的流程图;
59.图5为本发明实施例1中,基于硬件装置和数字化软件综合的用电故障模拟过程的流程图;
60.图6为本发明实施例1中硬件装置的结构示意图;
61.图中标记为:1、一号面板;2、二号面板;3、三号面板;4、四号面板;5、五号面板;6、六号面板。
具体实施方式
62.为了使本发明的目的、技术方案及优点更加清楚明白,以下结合附图及实施例,对本发明进行进一步详细说明。应当理解,此处所描述的具体实施例仅用以解释本发明,并不用于限定本发明。
63.对实施例内容中的名词解释如下:“台区”是指(一台)变压器的供电范围或区域;本实施例中,用电台区、硬件台区和软件台区是台区概念在不同场景下的命名。“杆变/箱变”指杆式变压器或箱式变压器,二者根据用电场景下用电容量和用电负荷的分散情况进行选择。“全载波抄表”、“半载波抄表”、“混合抄表”、“ii型集中器抄表”分别代表不同的电表集抄方案,全载波的模式是将载波模块嵌入到电表里,本地信道采用载波通信技术;半载波为本地信道中加入采集器,集中器到采集器采用电力线载波通信技术,而采集器到电能表一般采用rs485通信技术;混合抄表指使用载波通信、rs485、微无线等通信中的至少使用两种方式进行抄表的模式。ii型集中器抄表是采用ii型集中器作为数据集采终端工具实现抄表。“高供高计”是指高压供电同时在高压装置pt,ct进行计量的方式。“高供低计”是指高压供电,在低压侧装置ct进行计量;二者主要根据不同的用电场景进行选择,其中,高供高计的计量方式中,电力变压器的损耗在计量装置的后面,已包含在计量数据内。高供低计的计量方式中,电力变压器的损耗在计量装置的前面,未包含在计量数据内。
64.实施例1
65.如图1所示,本实施例提供一种软硬件协同的多场景用电故障的模拟仿真方法,该模拟仿真方法包括如下步骤:
66.步骤1:构建包含硬件装置和数字化软件的仿真控制系统,硬件装置和数字化软件均接入到仿真控制系统中。
67.其中,如图2所示,硬件装置中的包括真实仿真设备;数字化软件中包括虚拟仿真设备;真实仿真设备和虚拟仿真设备分别用于在各自启用状态下执行故障的仿真模拟过程。
68.步骤2:仿真控制系统创建出用电台区的内容,用电台区的内容包括:用电类型、变压器类别、互感器变比、采集/计量设备种类及其数量的信息。
69.步骤3:仿真控制系统根据创建出的用电台区的内容得出用电故障的类型与采集/计量设备的种类间的对应关系。
70.步骤4:根据上步骤建立的对应关系,仿真控制系统由需要仿真模拟的用电故障的类型确定需要组建的用电场景的类型以及对应的采集/计量设备的种类,进而向硬件装置或/和数字化软件下达相应的场景指令和故障指令。
71.步骤5:硬件装置或/和数字化软件接收到场景指令和故障指令后,在真实仿真设备或/和虚拟仿真设备中执行用电故障的仿真模拟过程。
72.其中,步骤1中的硬件装置用于接收由仿真控制系统下发的场景指令和故障指令,进而组建相应的用电场景,并在真实仿真设备中实时反馈用电场景中硬件装置的故障状态和运维状态;数字化软件用于接收由仿真控制系统下发的场景指令和故障指令,进而完成数据建模,虚拟化出仿真设备模型的电气状态和结构形态,组建相应的用电场景,并在虚拟仿真设备中实时反馈用电场景中仿真设备模型的故障状态和运维状态。
73.步骤3中,用电故障的类型包括一类故障、二类故障、三类故障、四类故障、五类故障、六类故障和七类故障;一类故障具体包括:时间错误、时钟电池故障、rs485端口故障、esam损坏、esam密钥未下发、设备电源损坏、软件运行故障、系统死机、交采芯片损坏、采集数据存储错误、本地通信模块损坏、可恢复hplc模块串口异常、不可恢复hplc模块串口异常;二类故障具体包括:数据未采集、户表档案错误、设备档案错误、终端任务错误、远程通信模块端口故障、远程通信模块设备损坏;三类故障为供电电池/电容故障;四类故障为本地载波通信端口故障;五类故障为电能表计量异常;六类故障为控制模块损坏;七类故障为控制模块继电器故障。
74.其中,与一类故障建立对应关系的采集/计量设备的种类为单相电能表、三相四线电能表、集中器或专变终端;与二类故障建立对应关系的采集设备的种类为集中器或专变终端;与三类故障建立对应关系的采集/计量设备的种类为三相四线电能表、集中器或专变终端;与四类故障建立对应关系的采集/计量设备的种类为单相电能表、三相四线电能表或集中器;与五类故障建立对应关系的计量设备的种类为单相电能表或三相四线电能表;与六类故障建立对应关系的采集设备的种类为专变终端;与七类故障建立对应关系的采集/计量设备的种类为单相电能表、三相四线电能表或专变终端。
75.本实施例中的各故障类型与其对应的采集/计量设备的匹配关系如表1所示:
76.表1:故障类型与设备种类的匹配关系对照表
77.78.79.80.[0081][0082]
步骤4中,用电场景的类型包括场景1、场景2、场景3、场景4、场景5和场景6。
[0083]
其中,场景1、场景2、场景3、场景4分别定义为:“低压
‑
杆变/箱变
‑
全载波抄表”、“低压
‑
杆变/箱变
‑
半载波抄表”、“低压
‑
杆变/箱变
‑
混合抄表”、“低压
‑
杆变/箱变
‑
ii型集中器抄表”;场景1、场景2、场景3中包含的设备种类均包括电流互感器、集中器、采集器、三相电能表和单相电能表;场景4中包含的设备种类包括:电流互感器、集中器、三相电能表和单相电能表。
[0084]
场景5定义为“专变
‑
杆变/箱变
‑
高供低计”,场景5包含的设备种类包括:电流互感器、集中器、采集器、三相电能表和单相电能表;场景6定义为“专变
‑
杆变/箱变
‑
高供高计”,场景6包含的设备种类包括:电流互感器、电压互感器、集中器和三相电能表。
[0085]
在本实施例中,场景1、场景2、场景3、场景4对应的用户类别为公变用户;场景5和场景6对应的用户类别为专变用户。
[0086]
具体地,本实施例中,仿真控制系统创建的各仿真用电台区场景的描述如表2所示:
[0087]
表2:用电场景的类型及其描述
[0088]
[0089][0090]
步骤5中,用电故障的仿真模拟包括三种方式;第一种方式是由硬件装置单独模拟出用电故障;第二种方式是由数字化软件单独仿真出用电故障;第三种方式是由硬件装置和数字化软件综合仿真模拟出用电故障;仿真控制系统根据用电故障类型优先采用第一种方式进行模拟仿真;在硬件装置无法满足模拟仿真所需的资源要求时,采用第三种方式;在硬件装置完全无法实现时模拟仿真过程时,采用第二种方式。
[0091]
其中,如图3所示,硬件装置单独模拟出用电故障的过程如下:
[0092]
(1)仿真控制系统选择对应的硬件装置。
[0093]
(2)硬件装置中的真实仿真设备准备好设备位置、类型、数量、资产、地址、故障状态的信息,并上报给硬件装置;硬件装置获取真实仿真设备的设备位置、类型、数量、资产、地址、故障状态的信息,以及自身的地址、资产的信息,并上报给仿真控制系统。
[0094]
(3)仿真控制系统获取硬件装置和真实仿真设备的故障状态、位置、地址、资产号的信息。
[0095]
(4)仿真控制系统准备台区数据信息。
[0096]
(5)采集终端将上线状态上报至仿真控制系统。
[0097]
(6)仿真控制系统将用电台区信息、故障设备关联信息与硬件装置状态信息进行比对,匹配后将台区信息和故障信息下发给硬件装置,硬件装置接收台区信息后组建用电台区,并转发故障信息至真实仿真设备。
[0098]
(7)硬件装置实时监控真实仿真设备的故障状态,用于支撑用电台区教学、培训、竞赛。
[0099]
(8)用电台区结束时,硬件装置上报结束指令至仿真控制系统,仿真控制系统配置台区重置信息、故障重置信息,并下发给硬件装置。
[0100]
(9)硬件装置接收台区重置指令,解除台区,并转发设备故障重置指令至真实仿真设备,真实仿真设备重置故障。
[0101]
(10)仿真控制系统接收硬件装置的台区重置状态及真实仿真设备的故障重置状态,故障仿真场景模拟流程结束。
[0102]
如图4所示,数字化软件单独仿真出用电故障的过程如下:
[0103]
(1)仿真控制系统选择对应的数字化软件。
[0104]
(2)仿真控制系统准备台区信息,并向数字化软件发出台区数据建模请求;台区信息的内容包括台区类型以及台区设备种类和数量。
[0105]
(3)数字化软件生成台区信息创建成功的结果,并反馈至仿真控制系统。
[0106]
(4)台区信息创建成功后,仿真控制系统准备虚拟仿真设备的参数信息,并向数字化软件发出虚拟仿真设备的参数信息数据建模的创建请求;虚拟仿真设备的参数信息包括设备类型、资产号和地址。
[0107]
(5)数字化软件生成虚拟仿真设备的参数信息创建成功的结果,并反馈至仿真控制系统。
[0108]
(6)虚拟仿真设备的参数信息创建成功后,仿真控制系统准备仿真故障信息,向数字化软件发出故障参数信息数据建模请求。
[0109]
(7)数字化软件生成故障参数信息数据建模成功的结果,并反馈至仿真控制系统;仿真控制系统对数字化软件中的虚拟仿真设备的故障状态进行监控,并基于虚拟仿真设备开展用电信息采集运维教学、培训与竞赛。
[0110]
(8)当需要结束用电台区场景时,仿真控制系统准备虚拟仿真设备的故障重置参数和台区清除参数,向数字化软件发出仿真故障参数重置和台区清除请求。
[0111]
(9)数字化软件启动虚拟仿真设备的故障数据重置过程并释放台区信息,结束软件模拟场景流程。
[0112]
如图5所示,硬件装置和数字化软件综合仿真模拟出用电故障的过程如下:
[0113]
(1)仿真控制系统选择对应的硬件装置和数字化软件。
[0114]
(2)真实仿真设备准备好设备位置、类型、数量、资产、地址、故障状态的信息,并上报给硬件装置;硬件装置获取真实仿真设备的位置、类型、数量、资产、地址、故障状态的信息,及自身的地址、资产的信息,并上报给等待仿真控制系统。
[0115]
(3)采集终端将上线状态上报给仿真控制系统。
[0116]
(4)仿真控制系统准备好台区信息,台区信息包括台区类型、设备种类和数量。
[0117]
(5)仿真控制系统根据台区信息,优先选择硬件装置中设备进行匹配和关联,对于硬件装置中的设备资源不能满足的,再创建软件台区,并分配剩余的设备种类和数量。
[0118]
(6)硬件装置组建硬件台区,接收故障指令,并转发至真实仿真设备,真实仿真设备执行由该部分负责的故障模拟内容。
[0119]
(7)数字化软件接收台区信息和故障信息,组建虚拟的软件台区;生成虚拟仿真设备的参数信息,虚拟仿真设备执行由该部分负责的故障模拟内容;软件台区与硬件台区在拓扑结构上从属于同一个台区。
[0120]
(8)基于硬件台区和软件台区组合,构建在同一个台区拓扑结构下的大容量用电台区场景仿真,用于电力系统中用电台区的采集运维学习、培训和教学。
[0121]
(9)结束台区场景时,仿真控制系统接收结束指令,配置台区清除信息和故障重置信息,并同时下发给数字化软件和硬件装置,数字化软件和硬件装置接收该指令后,数字化软件重置虚拟仿真设备的参数,释放用电台区;硬件装置解除用电台区,并下发故障重置指令至真实仿真设备,真实仿真设备进行故障重置,并恢复正常状态;综合模拟场景流程结束。
[0122]
本实施例提供的一种基于软硬件协同的用电故障仿真场景模拟方法既可以可以作为电力系统培训人员创建大台区、多设备场景的方法;也可以作为电力系统硬件故障场景培训的方法;还可以作为电力系统客户侧用电采集运维竞赛的方法。
[0123]
本实施例中,图6展示了硬件装置的结构示意图,其中一号面板1中包括1个集中器
和1个载波三相表;二号面板2中包括2个载波三相表;三号面板3中包括6个载波单相电能表;四号面板4为工控显示器;五号面板5中包括2个载波三相表;六号面板6中包括6个载波单相电能表。各个面板中智能电能表及采集终端的编号顺序为从左到右,从下至下。
[0124]
结合图6,进一步举例该方法在硬件装置模拟出用电故障场景的详细过程。
[0125]
其中,以建立“公变用户
‑
低压
‑
全载波抄表”场景为例,硬件装置模拟用电故障场景的方法包括以下这些步骤。
[0126]
(1)根据本发明公开的用电台区场景列表,本实施例选取其中一种场景进行陈述。仿真控制系统中选择用户类别为公变,场景类型为低压全载波台区,集中器数量为1,载波单相电能表数量为6,载波三相表数量为2。
[0127]
(2)故障
‑
设备匹配绑定可进行自定义选择,本实施例选择以下情况,以三号面板3中位置编号为1的单相电能表绑定故障为“控制模块继电器故障”,六号面板6中编号为2的单相电能表绑定故障为“设备电源损坏”。
[0128]
(3)以本实施例中硬件装置中仿真设备配置情况为例,硬件装置接入仿真控制系统,仿真控制系统获取硬件装置状态,并读取到硬件装置上1块集中器,有12块载波单相电能表,5块载波三相表,并且仿真设备各位置状态、地址、资产等信息已同步至仿真控制系统。
[0129]
(4)按照图3所示的流程规则,硬件装置组建台区,根据台区选择的设备种类和数量,台区组成为一号面板1、三号面板3,六号面板6中所选的仿真设备,其中,绑定故障的仿真设备并接收故障指令,并执行故障模拟,三号面板3中位置编号为1的单相电能表“继电器故障”故障创建成功,此时通过仿真控制系统下发拉/合闸命令,此电能表继电器无动作;六号面板6中编号为2的单相电能表绑定故障为“设备电源损坏”创建成功,此时观察该单相电能表,发现设备屏幕无显示,按键无反应,并且集中器无法抄读该设备电量数据。
[0130]
(5)此时创建的故障仿真场景,用于支撑用电台区用电信息采集运维教学、培训、竞赛。
[0131]
(6)仿真控制系统实时监控故障状态,当需要结束场景,接收到故障恢复命令后,清除一号面板1、三号面板3、六号面板6之间的台区拓扑关系,并重置三号面板3中位置编号为1的单相电能表、六号面板6中编号为2的单相电能表的故障内容,故障仿真场景模拟流程结束。
[0132]
接下来,结合图6本实施例进一步以使用硬件装置及数字化软件联合模拟用电故障场景为例,对本实施例的方法进行举例说明。
[0133]
其中,以建立“公变用户
‑
低压
‑
混合抄表”场景为例,硬件装置、数字化软件联合模拟用电故障场景的方法包括以下这些步骤。
[0134]
(1)根据本实施例公开的用电台区场景列表,本实施例选取其中一种场景进行陈述。仿真控制系统中选择用户类别为公变,场景类型为低压混合台区,集中器数量为1,采集器数量1,载波单相电能表数量为100,485单相电能表数量为20,载波三相表数量为6。
[0135]
(2)故障
‑
设备匹配绑定可进行自定义选择,本实施例选择以下情况,以硬件装置二号面板2中位置编号为1的载波三相表绑定故障为“交采(计量)芯片损坏”,六号面板6中编号为1的载波单相电能表绑定故障为“本地通信端口故障(载波)”,设置数字化软件中2块载波单相电能表“软件运行故障”故障,3块485单相电能表“继电器故障”。
[0136]
(3)硬件装置接入仿真控制系统,仿真控制系统获取硬件装置状态,并读取到硬件装置上1块集中器,有12块载波单相电能表,5块载波三相表,并且仿真设备各位置状态、地址、资产等信息已同步至仿真控制系统。
[0137]
(4)硬件装置组建台区,硬件台区组成为一号面板1、二号面板1,六号面板6中所有仿真设备(1块集中器、3块载波三相表、6块载波单相电能表),其中,绑定故障的仿真设备并接收故障指令,并执行故障模拟,二号面板2中位置编号为1的载波三相表“交采(计量)芯片损坏”故障执行,六号面板6中编号为1的载波单相电能表“本地通信端口故障(载波)”故障执行;此时,仿真控制系统所创建的台区设备剩余的94块载波单相电能表,20块485单相电能表,3块载波三相表,1块采集器在数字化软件中创建软件台区。
[0138]
(5)数字化软件接收剩余仿真设备参数,通过数据建模,生成虚拟化仿真设备,建立与现实化硬件装置处于同一拓扑的软件台区,并完成数字化软件中2块载波单相电能表“软件运行故障”故障,3块485单相电能表“时间错误”。
[0139]
(6)通过现场运维排查,硬件装置的2号面板中位置编号为1的载波三相表,a相电流在表计屏幕中显示为20v,实际用万用表测量端子电压为220v,由此确认“交采(计量)芯片损坏”故障执行成功;硬件装置中六号面板6中编号为1的载波单相电能表,集中器无法抄读其计量数据,通过更换新的载波模块,可以重新抄读,确认该设备“本地通信端口故障(载波)”故障执行成功。
[0140]
(7)通过web页面虚拟化场景进行排查,发现软件场景中有2块载波单相电能表屏幕界面卡死,按键功能无法使用,硬件台区中集中器抄读该表实时有功电量,无回复,确认该设备“软件运行故障”故障执行成功;通过集中器实时抄读软件场景中所有电能表,发现数块电能表无法回复数据,经过筛查排除上述2块载波表故障后,剩下3块485单相电能表故障,从虚拟化场景内,按键查看单相电能表时间,发现时间错误,确认该设备“时间错误”故障执行成功。
[0141]
(8)仿真控制系统实时监控故障状态,当需要结束场景,接收到故障恢复命令后,清除硬件装置一号面板1、二号面板2、六号面板6之间的台区拓扑关系,并重置故障设备故障内容,清除数字化软件中场景内容,重置虚拟仿真设备的故障内容。
[0142]
以上所述仅为本发明的较佳实施例而已,并不用以限制本发明,凡在本发明的精神和原则之内所作的任何修改、等同替换和改进等,均应包含在本发明的保护范围之内。