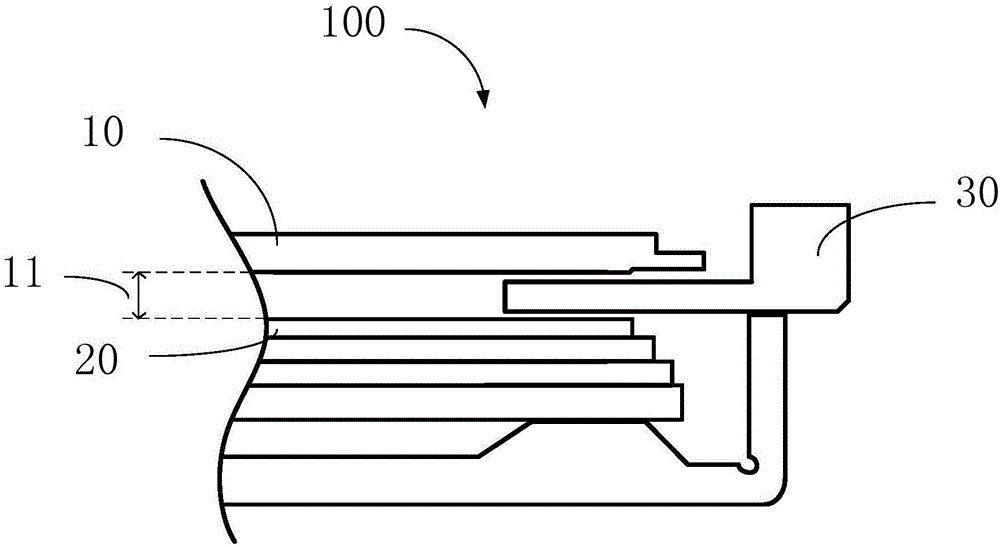
本发明涉及液晶显示技术领域,具体而言,涉及一种显示装置及液晶面板。
背景技术:
在液晶显示器的装配过程中,为了保证更好的显示效果,需要在液晶面板一侧设置多层光学膜片,如增光膜或扩散膜等,这些光学膜片上分布有微小的光学结构。但在液晶显示器的装配过程中,为了避免由于液晶面板与光学膜片之间的相对运动造成的液晶面板擦伤的情况,现有技术中必须在液晶面板与光学膜片之间保留一物理间隙。
发明人发现,预留的这一物理间隙虽然可以避免液晶面板与光学膜片之间的擦伤,但这一物理间隙会影响液晶显示器的整体厚度,不利于液晶显示器的薄型化设计。并且,本领域技术人员在进行显示装置的薄型化设计时,普遍且长期采用的技术手段是从显示装置的外围固定结构上进行改进。
技术实现要素:
有鉴于此,本发明提供了一种显示装置及液晶面板,可以解决上述问题。
本发明提供的技术方案如下:
一种显示装置,包括液晶面板,所述液晶面板包括入光面、出光面以及贴合在所述入光面一侧的第一光学膜片,所述第一光学膜片包括第一基层和设置在所述第一基层一侧的第一微结构层,所述第一光学膜片通过所述第一微结构层与所述液晶面板的入光面一侧贴合。
进一步的,所述显示装置还包括设置在所述液晶面板贴合所述第一光学膜片一侧的光学模组;
所述光学模组包括第二光学膜片,所述第二光学膜片包括第二基层和设置在所述第二基层靠近所述液晶面板一侧的第二微结构层。
进一步的,所述显示装置还包括:
用于承载所述液晶面板的中框,所述中框包括设置在所述液晶面板和所述光学模组之间的承载部。
进一步的,所述显示装置还包括:
光源;
设置在所述光学模组远离所述液晶面板一侧,用于承载所述光源的背板,所述光源设置在所述背板靠近所述光学模组的一侧,或者所述光源设置在所述背板的侧面。
进一步的,所述光学模组还包括:
设置在所述第二光学膜片远离所述液晶面板一侧的第三光学膜片;及
设置在所述第三光学膜片远离所述第二光学膜片一侧,用于将所述光源发出的光线引导至所述第三光学膜片的入光面的光学板,所述第三光学膜片包括第三基层和设置在所述第三基层一侧的第三微结构层。
进一步的,所述第一光学膜片、第二光学膜片、第三光学膜片为增光膜或扩散膜,所述第一微结构层、第二微结构层、第三微结构层包括若干条棱镜单元或若干个微透镜单元。
进一步的,所述光学板为扩散板或导光板。
进一步的,所述第一光学膜片、第二光学膜片为增光膜,所述第三光学膜片为扩散膜。
本发明还提供了一种液晶面板,所述液晶面板包括入光面、出光面以及贴合在所述入光面一侧的第一光学膜片,所述第一光学膜片包括第一基层和设置在所述第一基层一侧的第一微结构层,所述第一光学膜片通过所述第一微结构层与所述液晶面板的入光面一侧贴合。
优选地,所述第一光学膜片为增光膜或扩散膜。
综上所述,通过在液晶面板的入光面上贴合固定第一光学膜片,使得第一光学膜片和液晶面板处于相对静止的状态,在受到外力影响时,第一光学膜片和液晶面板的入光面之间也不会发生相对运动,不会出现擦伤等损坏情况,增强了对液晶面板的保护,减少了由于擦伤问题带来的高额维修成本。这样的结构使得现有技术中光学膜片和液晶面板之间的间隙可以被消除,有利于减小液晶显示装置的整体厚度,促进液晶显示装置的超薄化。同时,由于消除了第一光学膜片和液晶面板之间的间隙,使得组装过程中,环境中的颗粒不会进入到液晶面板和第一光学膜片之间,对组装环境的洁净要求降低,减少组装环境洁净度的投入,降低整体成本。此外,由于液晶面板已经贴合了第一光学膜片,在显示装置的组装过程中,省略了一张光学膜片的组装工艺,提高了组装效率。
为使本发明的上述目的、特征和优点能更明显易懂,下文特举较佳实施例,并配合所附附图,作详细说明如下。
附图说明
为了更清楚地说明本发明实施例的技术方案,下面将对实施例中所需要使用的附图作简单地介绍,应当理解,以下附图仅示出了本发明的某些实施例,因此不应被看作是对范围的限定,对于本领域普通技术人员来讲,在不付出创造性劳动的前提下,还可以根据这些附图获得其他相关的附图。
图1为现有技术中显示装置的剖面示意图。
图2为本发明实施例提供的一种显示装置的剖面示意图。
图3为本发明实施例提供的增光膜的剖面示意图。
图4为本发明实施例提供的扩散膜的剖面示意图。
图5为本发明实施例提供的一种液晶面板的剖面示意图。
图标:100-显示装置;20-光学膜片;10,101,201-液晶面板;102,202-第一光学膜片;1021-第一基层;1022-第一微结构层;103-光学模组;1031-第二光学膜片;1032-第三光学膜片;10321-第三基层;10322-第三微结构层;1033-光学板;30,104-中框;1041-承载部;105-背板,11,1011-间隙。
具体实施方式
下面将结合本发明实施例中附图,对本发明实施例中的技术方案进行清楚、完整地描述,显然,所描述的实施例仅仅是本发明一部分实施例,而不是全部的实施例。通常在此处附图中描述和示出的本发明实施例的组件可以以各种不同的配置来布置和设计。因此,以下对在附图中提供的本发明的实施例的详细描述并非旨在限制要求保护的本发明的范围,而是仅仅表示本发明的选定实施例。基于本发明的实施例,本领域技术人员在没有做出创造性劳动的前提下所获得的所有其他实施例,都属于本发明保护的范围。
应注意到:相似的标号和字母在下面的附图中表示类似项,因此,一旦某一项在一个附图中被定义,则在随后的附图中不需要对其进行进一步定义和解释。同时,在本发明的描述中,术语“第一”、“第二”等仅用于区分描述,而不能理解为指示或暗示相对重要性。
液晶显示器由于其易用性佳、功耗较低,被广泛应用于液晶电视、电脑显示器等领域作为液晶显示装置。在这些液晶显示装置的制造过程中,液晶面板作为液晶显示装置中的一个重要部件,是液晶显示装置组装制造过程中的关键。液晶显示装置的正常显示也不仅需要液晶面板还需要其他结构,由于液晶面板其本身并不能发光,需要提供光源使液晶面板显示。光源发出的光也并不会直接投射到液晶面板上,需要经过一系列的光学处理。现有技术中,一般会在光源和液晶面板之间设置引导光线的导光板以及其他类型的多层光学膜片,以提高液晶面板的显示效果。
图1为现有技术中显示装置100的剖面示意图。由于光学膜片20的特殊光学结构,最靠近液晶面板10的光学膜片20靠近液晶面板10的一侧的微观结构并不是光滑的,例如增光膜上的微观结构即是多条棱镜单元。这样的具有微观结构的光学膜片20如果与液晶面板10发生了碰撞,就会对液晶面板10或光学膜片20中的一者或两者造成擦伤损坏。损坏的液晶面板10在显示过程中会出现黑色不良,而损坏的光学膜片20由于微观光学结构被破坏也会影响液晶面板10的显示效果。因此,在液晶显示器或液晶电视的组装过程中,液晶面板10与最靠近液晶面板的光学膜片20之间会通过使用一中框30的方式预留一间隙11。通过该间隙11使光学膜片20和液晶面板10之间实现物理上的隔离,避免由于碰撞产生液晶面板10或光学膜片20的损坏。现有技术中,该间隙11一般都需要大于2mm以尽量避免碰撞擦伤的可能性。
另一方面,液晶面板10和光学膜片20之间保留间隙11,在组装过程中,由于组装环境中空气内可能有一定数量的尘埃颗粒,这些颗粒就会进入到液晶面板10和光学膜片20之间的间隙11中,这些颗粒同样也会由于液晶面板10和光学膜片20之间的相对运动而对液晶面板10或光学膜片20造成擦伤。因此,组装环境对洁净度的要求就要更高,以避免颗粒进入到上述间隙11中,提高了环境成本投入。
在现有技术中,液晶显示装置行业由于行业分工的不同,处于行业上游的厂商只进行单一元件的生产制造,例如液晶面板企业只进行液晶面板10的生产制造,而光学膜片厂商只进行光学膜片20的生产,而下游的显示器厂商或电视厂商需要根据自身需要采购液晶面板10、光学膜片20以及其他周边元件,进行液晶电视或液晶显示器的组装。处于产业下游的厂商由于只能根据其他上游厂商已经生产好的液晶面板10和其他组件进行组装。因此,显示装置的生产厂商需要在液晶面板10和光学膜片20之间的间隙11预留至少大约2mm的距离来避免上述提到的缺陷。
在液晶显示装置日益向超薄化的趋势发展,现有技术中液晶显示装置的减薄都是在固定结构上进行改进,本领域技术人员对于液晶显示装置的减薄都是认为需要改变显示装置整体的固定结构。本领域技术人员在薄型化设计普遍且长期采用的技术手段就是改变固定结构,例如对外框、中框等固定组件进行结构调整以实现减薄,并没有发现液晶面板10和光学膜片20之间保留的间隙11对液晶显示装置的超薄化也造成了阻碍。由于显示装置的组装厂商并不具备液晶面板10和光学膜片20的生产能力,其只能从组装结构上进行改进以实现显示装置的减薄。对于目前显示装置的减薄以毫米来计算的情况下,显示装置的组装行业也面临通过改变固定结构也无法进一步减薄的问题。
有鉴于此,如图2所示,本申请实施例提供了一种显示装置100,包括液晶面板101,所述液晶面板101包括入光面、出光面以及贴合在所述入光面一侧的第一光学膜片102,所述第一光学膜片102包括第一基层和设置在所述第一基层一侧的第一微结构层,所述第一光学膜片102通过所述第一微结构层与所述液晶面板101的入光面一侧贴合。
在本申请实施例中,在液晶面板101的入光面贴合上一层第一光学膜片102,该第一光学膜片102可以是增光膜或扩散膜等膜片,膜片的种类可以根据实际需要进行贴合,贴合工艺也可以采用现有的涂布粘结物等方式进行贴合。只需要保证第一光学膜片102具有微观光学结构的第一微结构层与液晶面板101的入光面贴合即可。
本申请实施例中,在液晶面板101的入光面贴合一第一光学膜片102,使得第一光学膜片102和液晶面板101处于相对静止的状态,无论外界如何干扰,液晶面板101和第一光学膜片102的贴合固定也不会被破坏,也就不会出现第一光学膜片102和液晶面板101之间相对运动而带来的擦伤问题。
进一步的,由于显示装置100中使用的光学膜片一般都是采用有机材料,例如增光膜一般是在一层涤纶树脂PET作为基层的基础上,涂布一层丙烯酸树脂形成光学微结构,这些有机材料的硬度相对液晶面板101使用的玻璃材料的硬度要小。使得采用本申请实施例提供的贴合了第一光学膜片102的液晶面板101进行显示装置100的组装时,该液晶面板101和其他光学膜片之间由于第一光学膜片102的保护,不会对液晶面板101造成损伤。由于光学膜片的硬度较低,即使该液晶面板101和其他光学膜片的间隙很小,硬度较小的其他光学膜片和第一光学膜片102由于碰撞产生损伤的几率也更小。
在本申请实施例中,显示装置100可以采用中框104来固定液晶面板101,也可以采用其他形式的无中框104的结构。
进一步的,在采用中框104固定液晶面板101的固定方式时,所述中框104可以包括设置在所述液晶面板101和所述光学模组103之间的承载部1041。
再如图1所示,在现有技术中,没有贴合光学膜片20的液晶面板10和光学膜片20之间可以通过中框30来维系两者之间的间隙。光学膜片20设置在中框30的一侧,液晶面板10固定在中框30的另一侧,利用中框30的物理厚度和其他固定组件的组合实现液晶面板10和光学膜片20之间预留间隙的方案。现有技术中的中框30不仅具有固定液晶面板10的作用,还具有维系液晶面板10和光学膜片20之间间隙的作用。
在本申请中,再如图2所示,所述显示装置100还包括设置在所述液晶面板101入光面一侧的光学模组103,所述光学模组103包括第二光学膜片1031,所述第二光学膜片1031包括第二基层和设置在所述第二基层靠近所述液晶面板101一侧的第二微结构层。
在本申请中,如前所述,由于液晶面板101的入光面贴合了第一光学膜片102,该液晶面板101的入光面由于第一光学膜片102的保护作用,其抗擦伤的能力也得到了增强。
进一步的,本发明实施例中,由于在液晶面板101入光面上贴合第一光学膜片102,无需考虑该液晶面板101和光学膜片被擦伤的可能,液晶面板101和光学模组103之间的间隙1011就可以进一步减小,甚至取消掉该间隙1011。另外,将中框104设置在光学模组103和液晶面板101之间,使得承载部1041的厚度也就可以进一步减小,从而使得整体显示装置100的厚度也较现有技术中的厚度更小,有利于显示装置100的超薄化设计。
发明人发现,通过在液晶面板101上贴合第一光学膜片102不仅消除了液晶面板101和第一光学膜片102之间的物理间隙,也使得第一光学膜片102和光学模组103之间的间隙1011可以减小。由于间隙1011的减小,组装过程中,环境中的尘埃颗粒等进入到该间隙1011的可能性也就更低。组装环境的洁净度要求也较现有技术中组装环境的洁净度要求更低。如此,使得显示装置100的生产企业在生产洁净度上的投入也更小,生产成本得以减小。
此外,由于本申请实施例提供的液晶面板101的入光面贴合了第一光学膜片102,在显示装置100的组装过程中,可以减少一张光学膜片的组装流程,组装工艺得到了简化,提升了组装效率。
进一步的,所述显示装置100还可以包括光源(图未示)和背板105。背板105设置在所述光学模组103远离所述液晶面板101一侧,用于承载所述光源。所述光源设置在所述背板105靠近所述光学模组的一侧,或者所述光源设置在所述背板105的侧面。
光源的设置位置可以根据实际需求确定,在侧入式背光模组中,可将光源设置在背板105的侧面,在直下式背光模组中,可以将光源设置在背板105靠近光学模组103的一侧。
所述光学模组103还包括设置在所述第二光学膜片1031远离所述液晶面板101一侧的第三光学膜片1032,及设置在所述第三光学膜片1032远离所述第二光学膜片1031一侧的光学板1033,光学板1033用于将所述光源发出的光线引导至所述第三光学膜片1032的入光面。如图3所示,所述第三光学膜片1032可以包括第三基层10321和设置在所述第三基层一侧的第三微结构层10322。
光学板1033可以是扩散板或导光板,光源发出的光线可以经过扩散板或导光板的引导向第三光学膜片1032的入光面入射。第三光学膜片1032可以采用如图3所示的扩散膜,第三光学膜片1032上的第三微结构层10322可以具有一层微透镜单元,光线经过第三光学膜片1032的扩散被混合的更加均匀。第二光学膜片1031可以采用增光膜,利用第二微结构层上的棱镜单元,将光线导入到靠近第二光学膜片1031法线的方向上,提升亮度。贴合在液晶面板101上的第一光学膜片102也可以采用如图4所示的增光膜,进一步提升亮度。第一光学膜片102的第一基层1021上设置一层第一微结构层1022,第一微结构层1022可以包含多条棱镜单元。第一光学膜片102和第二光学膜片1031都采用增光膜时,两个膜片上条状的棱镜单元可以处于正交的位置,即上下两张膜片的棱镜单元所在直线垂直,使得亮度可以提升110%以上。可以理解的是,第一光学膜片102、第二光学膜片1031、第三光学膜片1032都可以为增光膜或扩散膜。
此外,可以理解的是,液晶面板101上贴合光学膜片的数量不仅限于一张,还可以贴合多张。
如图5所示,本申请实施例还提供了一种液晶面板201,所述液晶面板201包括入光面、出光面以及贴合在所述入光面一侧的第一光学膜片202,所述第一光学膜片202包括第一基层和设置在所述第一基层一侧的第一微结构层,所述第一光学膜片202通过所述第一微结构层与所述液晶面板201的入光面一侧贴合。该贴合了第一光学膜片202的液晶面板201的结构和前述的液晶面板101的结构和效果相同,这里不再赘述。
对于本领域人员针对显示装置的薄型化设计主要采用改变固定结构的问题,采用本申请实施例提供的显示装置的结构,对于本领域技术人员长期存在的无法进一步减薄的工艺痛点有极强的解决效果。
综上所述,通过在液晶面板101的入光面上贴合固定第一光学膜片102,使得第一光学膜片102和液晶面板101处于相对静止的状态,在受到外力影响时,第一光学膜片102和液晶面板101的入光面之间也不会发生相对运动,不会出现擦伤等损坏情况,增强了对液晶面板101的保护,减少了由于擦伤问题带来的高额的维修成本。这样的结构使得现有技术中光学膜片和液晶面板101之间的间隙可以被减小或消除,有利于减小液晶显示装置的整体厚度,促进液晶显示装置的超薄化。同时,由于消除了第一光学膜片102和液晶面板101之间的间隙,使得组装过程中,环境中的颗粒不会进入到液晶面板101和第一光学膜片102之间,对组装环境的洁净要求降低,减少组装环境洁净度的投入,降低整体成本。此外,由于液晶面板101已经贴合了第一光学膜片102,在显示装置的组装过程中,省略了一张光学膜片的组装工艺,提高了组装效率。
另外,在本发明各个实施例中的各功能模块可以集成在一起形成一个独立的部分,也可以是各个模块单独存在,也可以两个或两个以上模块集成形成一个独立的部分。
以上所述仅为本发明的优选实施例而已,并不用于限制本发明,对于本领域的技术人员来说,本发明可以有各种更改和变化。凡在本发明的精神和原则之内,所作的任何修改、等同替换、改进等,均应包含在本发明的保护范围之内。应注意到:相似的标号和字母在下面的附图中表示类似项,因此,一旦某一项在一个附图中被定义,则在随后的附图中不需要对其进行进一步定义和解释。