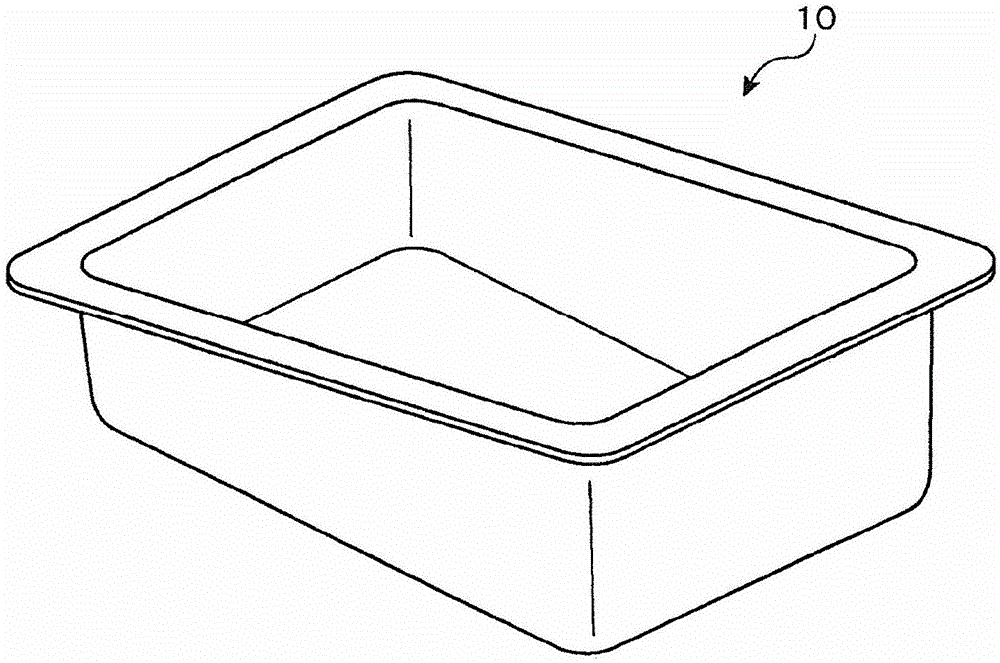
本发明涉及防音材料以及防音罩的制造方法,特别是涉及适用于减少从汽车的发动机周边发生的噪声的防音材料,以及使用了这样的防音材料的防音罩的制造方法。
背景技术:
:目前,为了减少以汽车的发动机等为发生源的噪声,各种防音材料被提出。例如,本申请人提出了具备与声源相对配置的吸音材料、与吸音材料层叠的非通气性的软质隔音层和在与软质隔音层之间形成空气层的软质罩,并将空气层密封而成的防音罩(参照专利文献1)。现有技术文献专利文献专利文献1:日本专利特开平2011-64167号公报技术实现要素:发明所要解决的课题然而,在联合国的欧洲经济委员会(ECE)的汽车标准协调世界论坛上,对于涉及汽车噪声的标准协调进行了探讨。在该论坛上,进行涉及车辆结构的规则的制定、改订,对于汽车的噪声在该规则51(ECER51)规定有车外噪声的限制值,该限制值随着规则的改订日益严格。本申请人在专利文献1中提出的防音罩虽然也是受到该规则改订而进行的,但为了应对日益严格的对于降低车外噪声的要求,对于以往未寻求防音对策的例如机油盘(oilpan)等发动机周边的声源,成为必须寻求防音对策的状况。然而,对于例如机油盘这样配置在发动机室下方的声源寻求防音对策时,用于此的防音材料被要求对于在发动机室内使用的冷却水(LLC)、电池液、玻璃水液等的耐久性,有必要在即使这些液体漏出附着也不会劣化。另外,在发动机室内,由于不仅暴露于来自发动机的热,还会暴露于发动机机油、自动传动液(ATFluid)、助力转向油(powersteeringoil)等油脂类的雾中,因此对此的耐热性、耐油性也是必要的。进而,发动机室的下部安装有底罩,但通常机油盘多数情况下不用底罩覆盖,而是以裸露在外部的状态设置。因此,对于风雨或飞石等外部环境的耐久性也被要求。这样,用于发动机室内设置的发动机周边的声源的防音对策的防音材料,期望提高其在严酷的使用环境下的耐久性,抑制其经年劣化以耐受长期使用。而且,还有必要在符合机油盘等声源的形状而成型为规定形状时的成型性不受损害。本发明鉴于上述情况而完成,其目的在于提供例如,作为适合用于汽车的发动机室内设置的发动机周边声源等的防音对策的防音材料,能够不损害成型性,即使在严酷的使用环境下也能够抑制经年劣化并且耐受长期使用的防音材料,以及使用这样的防音材料的防音罩的制造方法。用于解决课题的方法本发明所涉及的防音材料,作为其结构在于,具备:与声源相对地配置的吸音材料层;和层叠于所述吸音材料层的外装材料层,所述外装材料层包含由织布构成的保持材料和由热塑性树脂膜构成的表皮材料,并以所述表皮材料位于表面侧的方式而层叠于所述吸音材料层。另外,本发明所涉及的防音罩的制造方法,作为其方法在于,将上述这样的防音材料热压成型为规定形状。发明效果根据本发明,能够提供不损害成型性,即使在严酷的使用环境下也能够抑制经年劣化,并且耐受长期使用的防音材料,以及使用这样的防音材料的防音罩的制造方法。附图说明图1是示出将本发明的实施方式所涉及的防音材料热压成型而成的防音罩的概要的立体图。图2是本发明的实施方式所涉及的防音材料的主要部分放大剖面图。图3是示出实施例以及比较例中测定的声透射损失的结果的图表。符号说明1防音材料2表皮材料3保持材料4粘接层5(5a、5b)吸音材料6软质隔音材料7内衬材料8外装材料层9吸音材料层具体实施方式以下,对于本发明所涉及的防音材料的实施方式,参照附图进行说明。需要说明的是,图1是示出将本实施方式所涉及的防音材料热压成型而成的防音罩的概要的立体图,图2是本实施方式所涉及的防音材料的主要部分放大剖面图。本实施方式中的防音材料1是敷设在汽车的发动机室内设置的发动机周边的声源处,能够适合用于其的防音对策,例如,如图1所示,被热压成型为规定形状以覆盖机油盘等声源,作为防音罩10安装在敷设部位。如图2所示,防音材料1具备与声源相对地配置的吸音材料层9和层叠于吸音材料层的外装材料层8,外装材料层8包含由织布构成的保持材料3和由热塑性树脂膜构成的表皮材料2,并以表皮材料2位于表面侧的方式而层叠于吸音材料层9。需要说明的是,在图2中,以声源位于图中下方示出防音材料1的剖面。作为形成表皮材料2的热塑性树脂膜,能够使用例如,聚酰胺系树脂膜、聚酯系树脂膜、聚烯烃系树脂膜、软质氯乙烯系树脂膜、聚乙烯醇系树脂膜、聚碳酸酯系树脂膜、聚苯乙烯系树脂膜、聚丙烯腈系树脂膜、乙烯-乙酸乙烯酯共聚物系树脂膜等,这些之中,优选使用强韧性、抗冲击性、柔软性优异的聚酰胺系树脂膜。这些热塑性树脂膜可以是拉伸膜、未拉伸膜中的任意种,考虑到将防音材料1热压成型为规定形状时的成型性,优选未拉伸膜。作为形成表皮材料2的热塑性树脂膜,使用未拉伸膜来提高防音材料1的成型性时,该未拉伸膜优选能以伸长率5~500%进行拉伸的膜,更优选为10~500%,进一步优选为20~200%。需要说明的是,未拉伸膜的伸长率是指,依照JISK7161进行拉伸试验,将宽度25mm×长度150mm的长条状的试验片以100mm/分钟的速度进行拉伸时,载荷达到10N时的该膜的伸长率。作为形成保持材料3的织布,能够使用例如将聚丙烯系树脂纤维等的聚烯烃系树脂纤维、聚酯系树脂纤维、聚酰胺系树脂纤维、软质氯乙烯系树脂、聚碳酸酯系树脂纤维、聚丙烯腈系树脂纤维等热塑性树脂纤维进行编织而成的织布,这些之中,考虑到将防音材料1热压成型为规定形状时的成型性或成型后的形状保持性,优选使用将聚丙烯系树脂纤维、聚酯系树脂纤维、聚酰胺系树脂纤维中的任意一种或者二种以上进行编织而成的织布。这些织布可以是通过平纹、斜纹等编织的织布,考虑到将防音材料1热压成型为规定形状时的成型性,优选通过双向经编(2-waytricot)编织的具有伸缩性的织布。外装材料层8是通过将这样的表皮材料2与保持材料3层叠形成,在将表皮材料2与保持材料3层叠时,依照需要可以介由粘接剂等。进一步,外装材料层8是,为了使外装材料层8粘接于吸音材料层9而层叠,在与吸音材料层9相对的保持材料3的背面侧可以是含有例如,聚氨酯弹性体膜、聚烯烃共混物系弹性体膜、聚烯烃共聚物系弹性体膜、聚苯乙烯共聚物系弹性体膜、聚酯共聚物系弹性体膜等作为粘接层4的层叠结构。制成这样的层叠结构的外装材料层8是在对防音材料1进行热压成型时,形成保持材料3的织布的纤维熔融并成型后,在成型为规定形状的状态下冷却固化,该纤维之间发生粘着而使刚性提高,成型后的形状保持良好。由此,本实施方式中的防音材料1是在热压成型前具有柔软性且成型性良好,并且在热压成型后刚性提高,形状保持变得良好。为了使防音材料1的成型性与成型后的形状保持成为良好,外装材料层8在热压成型前的杨氏模量优选为0.005~0.5GPa,更优选为0.05~0.3GPa,热压成型后的杨氏模量优选为0.6~5.0GPa,更优选为1.0~3.0GPa。需要说明的是,杨氏模量是指依照JISK7127进行测定的值。另外,层叠有这样的外装材料层8的吸音材料层9含有吸音材料5,作为吸音材料5,优选使用玻璃棉、岩棉等人造矿物纤维,其基重优选为100~5000g/m2。除此以外,也可以使用例如将聚对苯二甲酸乙二醇酯等的聚酯纤维毡、尼龙纤维毡、聚乙烯纤维毡、聚丙烯纤维毡、丙烯酸纤维毡、二氧化硅-氧化铝陶瓷纤维毡、二氧化硅纤维毡或者将绵、羊毛、刨花、碎纤维等用热固性树脂加工成毡状的树脂毡等的毡类,将聚氨酯泡沫、聚乙烯泡沫、聚丙烯泡沫、酚醛泡沫、三聚氰胺泡沫、或者腈丁二烯橡胶、氯丁烯橡胶、苯乙烯橡胶、硅酮橡胶、聚氨酯橡胶、乙烯·丙烯·二烯橡胶等发泡为连续气泡状或在发泡后进行破碎加工等连续气泡化而制成的连续气泡体等多孔质材料作为吸音材料5。本实施方式中,为了提高防音材料1的防音性能,介由软质隔音材料6将相同种或者不同种的二个吸音材料5a、5b层叠。进一步,在对应于吸音材料层9的声源的一侧,从防止形成吸音材料5b的纤维类的飞散或从制品外观的观点出发,层叠有由无纺布或者热塑性树脂膜等构成的内衬材料7。即,吸音材料层9是,从层叠有外装材料层8的一侧依次制成第一吸音材料5a/软质隔音材料6/第二吸音材料5b/内衬材料7而成的层叠结构。在此,如果雨水等浸入安装在敷设部位的防音罩10的内部,则有吸了水分的吸音材料5a、5b等发生老化、吸音性能降低的情况或者霉菌等繁殖的担忧,但通过在内衬材料7使用热塑性树脂膜,还能够防止这样的问题。作为内衬材料7使用热塑性树脂膜的情况下,作为所述热塑性树脂膜,能够使用与表皮材料2相同的热塑性树脂膜。在这样制成层叠结构的吸音材料层9中,层叠软质隔音材料6是为了通过其自身变形使透过第二吸音材料5b的声音的振动衰减。为此,软质隔音材料6是由取决于声音的振动而变形的程度的柔软素材而形成,杨氏模量优选为0.001~0.5GPa,更优选为0.02~0.1GPa。进一步,软质隔音材料6的杨氏模量优选为热压成型后的外装材料层8的杨氏模量的1/5以下,更优选为1/10以下。通过这样,将把防音材料1热压成型而成的防音罩10敷设在声源时,透过第二吸音材料5b的声波选择性地使软质隔音材料6发生振动变形而被消耗,使隔音性提高,因软质隔音材料6衰减的声波被第一吸音材料5a吸音,进一步通过外装材料层8进行隔音,由此能够进一步提高防音罩10的防音性能。另外,软质隔音材料6为了提高其隔音性,透过率优选为10cc/cm2·sec以下,更优选为0.001~10cc/cm2·sec,特别优选为0.01~1cc/cm2·sec。需要说明的是,透过率是指依照JISL1018测定的值。作为这样的软质隔音材料6,能够使用例如树脂膜等,但只要是具有规定的杨氏模量、透过率的材料,就没有特别限定。如以上所述,本实施方式中的防音材料1具备:与声源相对地配置的吸音材料层;和层叠于吸音材料层的外装材料层,外装材料层包含由织布构成的保持材料和由热塑性树脂膜构成的表皮材料,并以表皮材料位于表面侧的方式而层叠于吸音材料层,如前所述,在热压成型前具有柔软性且成型性良好,并且在热压成型后刚性提高,形状保持变得良好。而且,通过这样将外装材料层以表皮材料位于表面侧的方式层叠于吸音材料层,能够提高对于在发动机室内使用的冷却水(LLC)、电池液、玻璃水液等的耐久性,对于来自发动机的热的耐热性,对于油脂类的耐油性,对于风雨或飞石等外部环境的耐久性。由此,能够提供即使是在严酷的使用环境下也能够抑制经年劣化并且耐受长期使用的防音材料1。实施例以下,举出具体的实施例,对本发明进行详细的说明。[实施例1]将聚丙烯系树脂纤维以平纹编织而成的基重为200g/m2的织布(UBEEXSYMOCO.,LTD.制造:SIMTEX布)作为保持材料,将厚度为55μm的未拉伸聚酰胺系树脂/聚烯烃系树脂共挤出层叠膜(UBEFILMCO.,LTD.制造:35N-L)作为表皮材料,将厚度为30μm的聚氨酯弹性体膜(SHEEDOMCO.,LTD.制造:DUS-235)作为粘接层,将这些以未拉伸共挤出层叠膜(表面侧为聚酰胺系树脂/里面侧为聚烯烃系树脂)/织布/粘接层的层叠结构进行层叠,形成外装材料层。对这样形成的外装材料层的杨氏模量进行测定,结果为0.2GPa。另一方面,将基重500g/m2的聚对苯二甲酸乙二醇酯短纤维毡(TAKAYASUCO.,LTD.制造:S500-HSGYN)作为第一吸音材料,将厚度为70μm的聚烯烃系树脂/聚酰胺系树脂/聚烯烃系树脂共挤出层叠膜(UBEFILMCO.,LTD.制造:35N-LL)作为软质隔音层,将基重为500g/m2的聚对苯二甲酸乙二醇酯短纤维毡(TAKAYASUCO.,LTD.制造:S500-HSGYN)作为第二吸音材料,将基重为125g/m2的无纺布(MAEDAKOSENCO.,LTD.制造:125H/PUR)作为内衬材料,将这些以第一吸音材料/共挤出层叠膜(聚烯烃系树脂/聚酰胺系树脂/聚烯烃系树脂)/第二吸音材料/无纺布的层叠结构进行层叠,形成吸音材料层。之后,以表皮材料位于表面侧的方式,将外装材料层层叠于吸音材料层,制作防音材料,将由此制作的防音材料在175℃下热压成型得到试验成型品。从试验成型品切出外装材料层,测定杨氏模量,结果为3.0GPa。另外,对于试验成型品,评价耐水性、耐热性、结冰剥离性、平滑性、成型性、隔音性能。评价基准如下,其结果示于表1。[耐水性]以泵压7MPa从喷嘴喷射水,使试验成型品的表面受到3N的冲击时,以从表皮材料向内部有无水的浸透进行评价,对于未认定水的浸透的标记为“○”,认定水的浸透的标记为“×”。[耐热性]将试验成型品放入吉尔炉(Geeroven)(热老化性试验机)中,在100℃的设定温度下放置144小时(1周)后,对于未认定试验成型品上的显著变形或者外观上的破裂、褶皱、剥离、龟裂等有害的损伤的标记为“○”,认定这样的变形、损伤的标记为“×”。[结冰剥离性]在试验成型品的表面载置圆筒状的树脂杯,将水注入内部,使其冻结后,去除树脂杯,形成冻结并粘着在试验成型品表面的冰柱。从试验成型品的表面将冰柱拉脱,对于未认定试验成型品的表面上的破裂、剥离等有害的损伤的标记为“○”,认定这样损伤的标记为“×”。[平滑性]对于试验成型品的尽量平的部分实施JISK7125(1999)的摩擦试验,将动摩擦系数为0.3以下的标记为“○”,将动摩擦系数超过0.3的标记为“×”。[成型性]对于试验成型品的表面未认定破裂、褶皱、剥离、龟裂等有害的损伤,并且用于成型的金属模具的内径尺寸与试验成型品的外形尺寸之差在2.5mm以内的标记为“○”,同样的尺寸差超过2.5mm的标记为“×”。[隔音性能]利用小型混响箱(扩散声场)·消声室(自由声场)·声强法,测定了试验成型品的声透射损失。将其结果示于图3。对于在5kHz的声透射损失为36dB以上的标记为“◎”,少于36dB且在33dB以上的标记为“○”,少于33dB且在30dB以上的标记为“△”,少于30dB的标记为“×”。需要说明的是,图3(a)是对于实施例的测定结果,图3(b)是对于比较例的测定结果。[表1]实施例1实施例2实施例3实施例4实施例5耐水性○○○○○耐热性○○○○○结冰剥离性○○○○○平滑性○○○○○成型性○○○○○隔音性◎◎○○◎[实施例2]除了将聚酯系树脂纤维以双向经编编织的基重为140g/m2的织布(ASAHIKASEIINTERTEXTILESCORPORATION制造:KARI140)作为保持材料以外,都与实施例1同样地形成外装材料层。对该外装材料层的杨氏模量进行测定,结果为0.15GPa。之后,将外装材料层层叠于与实施例1同样地形成的吸音材料层以制作防音材料,将这样制作的防音材料在175℃下进行热压成型得到试验成型品。从试验成型品切出外装材料层,测定杨氏模量,结果为2.0GPa。另外,对于试验成型品进行与实施例1相同的评价,结果示于表1。[实施例3]除了将聚酰胺系树脂纤维以双向经编编织的基重为40g/m2的织布(ASAHIKASEIINTERTEXTILESCORPORATION制造:AG1529)作为保持材料以外,都与实施例1同样地形成外装材料层。对该外装材料层的杨氏模量进行测定,结果为0.1GPa。之后,将外装材料层层叠于与实施例1同样地形成的吸音材料层以制作防音材料,将这样制作的防音材料在175℃下进行热压成型得到试验成型品。从试验成型品切出外装材料层,测定杨氏模量,结果为1.5GPa。另外,对于试验成型品进行与实施例1相同的评价,结果示于表1。[实施例4]除了将聚酯系树脂纤维以双向经编编织的基重为70g/m2的织布(ASAHIKASEIINTERTEXTILESCORPORATION制造:1430)作为保持材料以外,都与实施例1同样地形成外装材料层。对该外装材料层的杨氏模量进行测定,结果为0.1GPa。之后,将外装材料层层叠于与实施例1同样地形成的吸音材料层以制作防音材料,将这样制作的防音材料在175℃下进行热压成型得到试验成型品。从试验成型品切出外装材料层,测定杨氏模量,结果为1.0GPa。另外,对于试验成型品进行与实施例1相同的评价,结果示于表1。[实施例5]除了作为内衬材料,使用未拉伸聚酰胺系树脂/聚烯烃系树脂共挤出层叠膜(UBEFILMCO.,LTD.制造:35N-L),以第一吸音材料/共挤出层叠膜(聚烯烃系树脂/聚酰胺系树脂/聚烯烃系树脂)/第二吸音材料/未拉伸共挤出层叠膜(聚烯烃系树脂/聚酰胺系树脂)的层叠结构进行层叠以形成吸音材料层以外,都与实施例1同样地制作防音材料,将这样制作的防音材料在175℃下进行热压成型得到试验成型品。从试验成型品切出外装材料层,测定杨氏模量,结果为3.00GPa。另外,对于试验成型品进行与实施例1相同的评价,结果示于表1。[比较例1]除了将基重为125g/m2的疏水疏油处理无纺布(MAEDAKOSENCO.,LTD.制造:125H)作为保持材料以外,都与实施例1同样地形成外装材料层。对该外装材料层的杨氏模量进行测定,结果为0.25GPa。之后,将外装材料层层叠于与实施例1同样地形成的吸音材料层以制作防音材料,将这样制作的防音材料在175℃下进行热压成型得到试验成型品。从试验成型品切出外装材料层,测定杨氏模量,结果为0.5GPa。另外,对于试验成型品进行与实施例1相同的评价,结果示于表2。[比较例2]在基重为125g/m2的疏水疏油处理无纺布(MAEDAKOSENCO.,LTD.制造:125H)的背面,层叠厚度为30μm的聚氨酯弹性体膜(SHEEDOMCO.,LTD.制造:DUS-235)作为粘接层,形成外装材料层。对该外装材料层的杨氏模量进行测定,结果为0.25GPa。之后,将外装材料层层叠于与实施例1同样地形成的吸音材料层以制作防音材料,将这样制作的防音材料在175℃下进行热压成型得到试验成型品。从试验成型品切出外装材料层,测定杨氏模量,结果为0.5GPa。另外,对于试验成型品进行与实施例1相同的评价,结果示于表2。[比较例3]在厚度为55μm的未拉伸聚酰胺系树脂/聚烯烃系树脂共挤出层叠膜(UBEFILMCO.,LTD.制造:35N-L)的背面,层叠厚度为30μm的聚氨酯弹性体膜(SHEEDOMCO.,LTD.制造:DUS-235)作为粘接层,形成外装材料层。对该外装材料层的杨氏模量进行测定,结果为0.1GPa。之后,将外装材料层层叠于与实施例1同样地形成的吸音材料层以制作防音材料,将这样制作的防音材料在175℃下进行热压成型得到试验成型品。从试验成型品切出外装材料层,测定杨氏模量,结果为0.25GPa。另外,对于试验成型品进行与实施例1相同的评价,结果示于表2。[比较例4]对于在实施例1中制作的防音材料,不进行热压成型,对其耐水性、耐热性、结冰剥离性、平滑性、成型性、隔音性能进行评价。其结果示于表2。[表2]比较例1比较例2比较例3比较例4耐水性○×○○耐热性○○○○结冰剥离性○×○○平滑性○×○○成型性-○○-隔音性△××△虽然以上对本发明示出优选实施方式进行说明,但本发明不限于上述实施方式,显然能够在本发明的范围内进行各种变更实施。例如,在上述实施方式中,虽然示出敷设在汽车的发动机室内设置的机油盘等发动机周边的声源处而适用于其的防音对策的例子,但不限定于此。能够适用于各种领域的防音对策。本说明书中所记载的文献以及成为本申请的巴黎优先权基础的日本申请说明书的内容,在此全部援引。当前第1页1 2 3