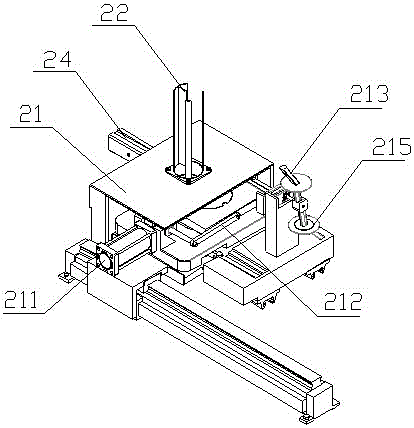
本发明涉及一种机加工设备,尤其涉及一种活塞环斜端面全自动磨床。
背景技术:活塞环是汽车、摩托车发动机里的重要部件,与活塞一起密封汽缸,防止高压的燃气从活塞上部向下泄露,并将活塞的热量传给缸壁,使之具有良好的散热效果;同时,活塞环控制缸壁上润滑油膜的厚度,将多余的润滑油刮回油箱,防止润滑油进入燃烧室。活塞环在随着活塞往返上下运动时与汽缸壁产生摩擦,自身被磨损而保护活塞不与汽缸壁接触而磨损。活塞环的斜端面可将环槽中的积碳排出,有效防止环结胶卡死,向上运动能有效布油,向下运动能有效刮油。活塞环斜端面是一种应用于高速、大功率、高负荷发动机上的优秀结构。活塞环整体呈圆形,其一侧具有一缺口,且一端的内侧面为斜面;在加工过程中,活塞环中的斜端面的加工是比较复杂的,精度要求较高,如果活塞环在加工中存在尺寸不当或者瑕疵,将会严重影响其工作甚至损坏发动机。同时,随着汽车业的发展,对发动机活塞环的质量和产量的要求也是越来越高,以往的活塞环加工设备己不能满足现代加工的要求,因此研发新的、高速、高效的活塞环加工设备已势在必行。
技术实现要素:针对现有技术存在的上述不足,本发明的目的在于怎样解决现有活塞环斜端面加工复杂,加工精度低,并且加工效率低的问题,提供一种活塞环斜端面全自动磨床。为了解决上述技术问题,本发明采用的技术方案是这样的:一种活塞环斜端面全自动磨床,包括床身、自动上下料架、复合加工台、动力头架以及集料架,其特征在于:在床身上设有两相互平行的导轨,所述自动上下料架和复合加工台分别位于两导轨的两端,动力头架和集料架分别位于两导轨的两侧;所述自动上下料架包括存料架、送料滑台以及送料气缸,所述存料架包括支架和存料管,所述支架包括一水平设于导轨上方的支板,所述存料管竖直设于支板上,在支板上设有一与存料管相连通的通孔;在支板的下方设有一推料板,其开口端呈V形并朝向复合加工台,封闭端与一推料气缸相连,该推料气缸与支架固定连接,通过推料气缸推动推料板能将从存料管落下的活塞环推动;所述送料滑台包括上料板和送料滑板,所述上料板的上表面具有一定位槽,所述定位槽呈V形,其开口端朝向支架,其封闭端能够将活塞环卡紧;在定位槽底部靠近封闭端处开有一贯穿上料板的穿孔,所述穿孔的内径大于活塞环的内径小于活塞环的外径,当活塞环由定位槽卡紧时,活塞环的轴心线与穿孔的轴心线重合;在上料板下侧设有一上料推环气缸,所述上料推环气缸通过气缸固定架与上料板固定连接,其气缸杆与一上料推爪相连,通过上料推环气缸推动上料推爪能够将活塞环从定位槽中推出;所述送料滑板与两导轨滑动连接,在送料滑板上设有一支撑板,所述送料滑板和支撑板对应上料推环气缸和气缸固定架的位置均设有过孔;在送料滑板的中部设有一凸起的定位环,该定位环与过孔轴心线重合;在支撑板下侧的中部对应定位环设有一外齿轮环,所述外齿轮环可转动套设于定位环上;在送料滑板的一侧设有一推拉气缸,所述推拉气缸的气缸杆连有一齿条,且该齿条与外齿轮环啮合,通过推拉气缸能够带动支撑板转动和定位;所述上料板靠近动力头架的一侧与支撑板铰连,在支撑板远离动力头架的一侧设有一上料翻转气缸,该上料翻转气缸通过翻转架与上料板相连,通过该上料翻转气缸能够推动上料板朝动力头架方向向上翻转;在送料滑板靠近复合加工台的一端设有一下料架,所述下料架包括下料杆和旋转下料气缸,所述旋转下料气缸安装于送料滑板上,其气缸杆与下料杆相连;所述送料气缸安装于床身上,其气缸杆与送料滑板相连,通过该送料气缸能够带动送料滑台沿导轨移动;所述复合加工台包括加工滑台和滑台位移伺服电机,所述加工滑台与两导轨滑动连接;所述滑台位移伺服电机安装于床身上,该滑台位移伺服电机通过滚珠丝杆副与加工滑台相连,通过该滑台位移伺服电机能够带动加工滑台沿导轨移动;在加工滑台远离自动上下料架的一端设有一磨削电机,该磨削电机经传动带和传动箱后与一砂轮相连,该砂轮的轴心线方向与导轨的长度方向一致;在加工滑台靠近自动上下料架的一端设有一直线电机,在直线电机上设有一车削刀架,通过该直线电机能够带动车削刀架沿垂直于导轨长度方向的方向移动,在车削刀架上设有一车刀,该车刀的刀头朝向动力头架;所述动力头架包括壳体,在壳体内设有中空轴管,该轴管内径大于活塞环的内径,小于活塞环的外径,其长度方向与导轨的长度方向垂直;在轴管靠近导轨的一端套设有一电磁吸盘和定位盘,所述电磁吸盘位于定位盘背离导轨的一侧,并与定位盘紧贴在一起;在定位盘中部开有一活塞环定位孔,该活塞环定位孔的轴心线与轴管的轴心线重合;在轴管的另一端设有一下料推环气缸,所述下料推环气缸的气缸杆伸入轴管内,并通过一下料推杆与下料推爪相连,通过下料推环气缸推动下料推杆,能够使下料推爪将活塞环从活塞环定位孔中推出;在轴管的一侧设有一驱动电机,该驱动电机通过传动带与轴管相连,并能够带动轴管旋转;所述壳体通过动力头架滑台安装于床身上,在床身上设有一动力头架位移伺服电机,该动力头架位移伺服电机通过滚珠丝杆副与动力头架滑台相连,通过该动力头架位移伺服电机能够带动动力头架滑台朝复合加工台方向移动;在动力头架滑台上设有一转盘,所述壳体固定于该转盘上,所述转盘通过转轴与动力头架滑台可转动连接,在转轴上套设有一蜗轮,与该蜗轮配合设有一蜗杆,该蜗杆可转动安装于动力头架滑台上,通过该蜗轮蜗杆机构能够带动转盘转动;在壳体与动力头架滑台之间设有一托板,所述托板与动力头架滑台固定连接,该托板中部具有一与转盘同轴心线的通孔,所述转盘位于该通孔内,并与托板之间形成一环形槽,所述壳体通过四根贯穿壳体和环形槽的连接螺杆与托板及转盘相连,从而实现动力头架的转动及定位;所述集料架包括集料杆、导向杆以及两倒L型连接架,所述导向杆一端通过一水平设置的连接板与倒L型连接架相连,另一端向下料杆方向倾斜,且导向杆与下料杆的弯折段能部分重叠;在导向杆靠近下料杆的一端设有一通槽,当下料杆转动时,其与导向杆重叠的部分能够从该通槽穿过;在连接板上方水平设有一理料杆,所述理料杆的直径小于活塞环缺口的开度,该理料杆与一理料电机相连,该理料电机安装于倒L型连接架上;所述集料杆与两倒L型连接架相连,其靠近导向杆的一端向上倾斜,并与连接板上下重叠;当活塞环沿导向杆落下后,能同时套入理料杆、连接板及集料杆上,在理料杆的带动下,能使活塞环的缺口与理料杆正对;当活塞环的缺口与理料杆正对时,活塞环能够从理料杆和连接板上落下,仅套在集料杆上,并移动至集料杆的另一端。进一步地,所述上料翻转气缸与支撑板固定连接,所述翻转架为一矩形框架,该翻转架与上料板下侧固定连接,所述上料翻转气缸的气缸杆通过一U型架与翻转架相连,其中,U型架的开放端与翻转架相对的两侧转动连接,其封闭端与上料翻转气缸的活塞杆转动连接,当上料翻转气缸推动U型架时,能够迫使翻转架向上转动。进一步地,所述下料杆的中部与旋转下料气缸的旋转轴相连,其靠近动力头架的一端向上弯折,另一端向下弯折;在下料杆的两弯折处分别套设有一挡板,所述挡板的直径大于活塞环的内径。进一步地,所述集料杆包括前段、中段和后段,其中,前段和后段分别与倒L型连接架固定连接,中段分别与前段和后段卡接。进一步地,在复合加工台的车削刀架上还设有车削传感器,用于检测车刀与活塞环的相对位置,从而调整动力头架的进给位置,保证活塞环斜端面的精确加工。与现有技术相比,本发明具有如下优点:1、通过V型槽与V型推料杆将料筒落下的活塞环收圆于工装夹具中并由上料滑台送至上料工位进行上料作业,其各旋转运动都是通过可调死挡定位,方便可靠;加工完成后送至下料工位,由旋转下料杆将推爪推出的活塞环下料转移至理料机构进行整理,以便更便捷的进行下一步工序。2、采用先车后磨的加工工艺,不但减小了磨削量避免磨削烧伤,而且车削之后磨削切入面的形状更好延长了砂轮寿命;采用直线电机驱动车刀,利用传感器测量车削距离来调整头架位置,从而减少因为上料引起的定位误差,进一步提高加工精度。3、由于活塞环型号种类很多,梯形活塞环端面的角度也各不相同。考虑到活塞环生产为同型号批量大规模生产,所以头架的角度调整设计为手动调节,在满足需求的前提下最大的降低成本。附图说明图1为活塞环斜端面全自动磨床的装配结构示意图。图2为活塞环斜端面全自动磨床的上下料架的结构示意图。图3为活塞环斜端面全自动磨床的上下料架的局部结构示意图。图4为活塞环斜端面全自动磨床的上下料架的底面结构示意图。图5为活塞环斜端面全自动磨床的复合加工台的结构示意图。图6为活塞环斜端面全自动磨床的动力头架的结构示意图。图7为活塞环斜端面全自动磨床的集料架的结构示意图。图中:1—床身,2—自动上下料架,21—支架,22—存料管,23—推料板,24—推料气缸,25—上料板,26—送料滑板,27—定位槽,28—穿孔,29—上料推环气缸,210—支撑板,211—上料翻转气缸,212—翻转架,213—下料杆,214—旋转下料气缸,215—挡板,3—复合加工台,31—加工滑台,32—滑台位移伺服电机,33—磨削电机,34—砂轮,35—直线电机,36—车削刀架,37—车刀,4—动力头架,41—中空轴管,42—电磁吸盘,43—定位盘,44—下料推环气缸,45—气缸连接架,46—驱动电机,47—动力头架滑台,48—动力头架位移伺服电机,49—转盘,410—托板,411—连接螺杆,5—集料架,51—集料杆,52—导向杆,53—倒L型连接架,54—通槽,55—理料杆,56—理料电机。具体实施方式下面将结合附图及实施例对本发明作进一步说明。实施例:参见图1,一种活塞环斜端面全自动磨床,包括床身1、自动上下料架2、复合加工台3、动力头架4以及集料架5。在床身1上设有两相互平行的导轨,所述自动上下料架2和复合加工台3分别位于两导轨的两端,动力头架4和集料架5分别位于两导轨的两侧。参见图2至图4,所述自动上下料架2包括存料架、送料滑台以及送料气缸。所述存料架包括支架21和存料管22,在存料管22内竖直设有一定位板,在装填活塞环时,使活塞环的缺口从定位板的上端套入,从而实现活塞环的定位,使后续加工精确度更高。所述支架21包括一水平设于导轨上方的支板,所述存料管22竖直设于支板上,在支板上设有一与存料管22相连通的通孔。在支板的下方水平设有一推料板23,其开口端呈V形并朝向复合加工台3,封闭端与一推料气缸24相连,该推料气缸24与支架21固定连接,通过推料气缸24推动推料板23能将从存料管22落下的活塞环推动。所述送料滑台包括上料板25和送料滑板26,所述上料板25的上表面具有一定位槽27,所述定位槽27呈V形,其开口端朝向支架21,其封闭端能够将活塞环卡紧。在定位槽27底部靠近封闭端处开有一贯穿上料板25的穿孔28,所述穿孔28的内径大于活塞环的内径小于活塞环的外径,当活塞环由定位槽27卡紧时,活塞环的轴心线与穿孔28的轴心线重合。在上料板25下侧设有一上料推环气缸29,所述上料推环气缸29通过气缸固定架与上料板25固定连接,其气缸杆与一上料推爪相连,通过上料推环气缸29推动上料推爪能够将活塞环从定位槽27中推出。所述送料滑板26与两导轨滑动连接,在送料滑板26上设有一支撑板210,所述送料滑板26和支撑板210对应上料推环气缸29和气缸固定架的位置均设有过孔。在送料滑板26的中部设有一凸起的定位环,该定位环与过孔轴心线重合;在支撑板210下侧的中部对应定位环设有一外齿轮环,所述外齿轮环可转动套设于定位环上;在送料滑板26的一侧设有一推拉气缸,所述推拉气缸的气缸杆连有一齿条,且该齿条与外齿轮环啮合,通过推拉气缸能够带动支撑板210转动和定位。所述上料板25靠近动力头架4的一侧与支撑板210转动连接,在支撑板210远离动力头架4的一侧设有一上料翻转气缸211,该上料翻转气缸211通过翻转架212与上料板25相连,通过该上料翻转气缸211能够推动上料板25朝动力头架4方向向上翻转。具体实施时,所述上料翻转气缸211与支撑板210固定连接,并通过滑块与滑轨的配合与床身1相连,从而使上料翻转气缸211的移动过程中稳定性更好。所述翻转架212为一矩形框架,该翻转架212与上料板25下侧固定连接,所述上料翻转气缸211的气缸杆通过一U型架与翻转架212相连,其中,U型架的开放端与翻转架212相对的两侧转动连接,其封闭端与上料翻转气缸211的活塞杆转动连接,当上料翻转气缸211推动U型架时,能够迫使翻转架212向上转动。在送料滑板26靠近复合加工台3的一端设有一下料架,所述下料架包括下料杆213和旋转下料气缸214,所述旋转下料气缸214安装于送料滑板26上,其气缸杆与下料杆213相连;所述下料杆213的中部与旋转下料气缸214的旋转轴相连,其靠近动力头架4的一端向上弯折,另一端向下弯折;在下料杆213的两弯折处分别套设有一挡板215,所述挡板215的直径大于活塞环的内径。所述送料气缸安装于床身1上,其气缸杆与送料滑板26相连,通过该送料气缸能够带动送料滑台沿导轨移动。参见图5,所述复合加工台3包括加工滑台31和滑台位移伺服电机32,所述加工滑台31与两导轨滑动连接;所述滑台位移伺服电机32安装于床身1上,该滑台位移伺服电机32通过滚珠丝杆副与加工滑台31相连,所述滚珠丝杆副包括丝杆和丝杆螺母,所述丝杆与滑台位移伺服电机32的电机轴相连,丝杆螺母与加工滑动的下侧相连,通过该滑台位移伺服电机32能够带动加工滑台31沿导轨移动。在加工滑台31远离自动上下料架2的一端设有一磨削电机33,该磨削电机33经传动带和传动箱后与一砂轮34相连,该砂轮34的轴心线方向与导轨的长度方向一致;在加工滑台31靠近自动上下料架2的一端设有一直线电机35,在直线电机35上设有一车削刀架36,通过该直线电机35能够带动车削刀架36沿垂直于导轨长度方向的方向移动,在车削刀架36上设有一车刀37,该车刀37的刀头朝向动力头架4。实际制作过程中,在复合加工台3的车削刀架36上还设有车削传感器,用于检测车刀37与活塞环的相对位置,从而调整动力头架4的进给位置,保证活塞环斜端面的精确加工。参见图6,所述动力头架4包括壳体,在壳体内设有中空轴管41,该轴管内径大于活塞环的内径,小于活塞环的外径,其长度方向与导轨的长度方向垂直;在轴管靠近导轨的一端套设有一电磁吸盘42和定位盘43,所述电磁吸盘42位于定位盘43背离导轨的一侧,并与定位盘43紧贴在一起;在定位盘43中部开有一活塞环定位孔,该活塞环定位孔的轴心线与轴管的轴心线重合。在轴管的另一端设有一下料推环气缸44,所述下料推环气缸44通过一气缸连接架45与壳体相连,其气缸杆伸入轴管内,并通过一下料推杆与下料推爪相连,通过下料推环气缸44能够推动下料推杆,使下料推爪将活塞环从活塞环定位孔中推出。在轴管的一侧设有一驱动电机46,该驱动电机46通过传动带与轴管相连,并能够带动轴管旋转。所述壳体通过动力头架滑台47安装于床身1上,在床身1上设有一动力头架位移伺服电机48,该动力头架位移伺服电机48通过滚珠丝杆副与动力头架滑台47相连,通过该动力头架位移伺服电机48能够带动动力头架滑台47朝复合加工台3方向移动。在动力头架滑台47上设有一转盘49,所述壳体固定于该转盘49上,所述转盘49通过转轴与动力头架滑台47可转动连接,在转轴上套设有一蜗轮,与该蜗轮配合设有一蜗杆,该蜗杆可转动安装于动力头架滑台47上,通过该蜗轮蜗杆机构能够带动转盘49转动,使用时,该蜗杆由手驱动。在壳体与动力头架滑台47之间设有一托板410,所述托板410与动力头架滑台47固定连接,该托板410中部具有一与转盘49同轴心线的通孔,所述转盘49位于该通孔内,并与托板410之间形成一环形槽,所述壳体通过四根贯穿壳体和环形槽的连接螺杆411与托板410及转盘49相连,从而实现动力头架4的转动及定位。参见图7,所述集料架5位于床身1靠近复合加工台3的一端,其包括集料杆51、导向杆52以及两倒L型连接架53,两倒L型连接架53沿床身1的长度方向分布;所述导向杆52一端通过一水平设置的连接板与靠近自动上下料架2的倒L型连接架53相连,另一端向下料杆213方向倾斜,且导向杆52与下料杆213的弯折段能部分重叠;在导向杆52靠近下料杆213的一端设有一通槽54,当下料杆213转动时,其与导向杆52重叠的部分能够从该通槽54穿过。在连接板上方水平设有一理料杆55,该理料杆55与连接板位于同一竖直平面上;所述理料杆55的直径小于活塞环缺口的开度,该理料杆55与一理料电机56相连,所述理料电机56安装于倒L型连接架53上;所述集料杆51的上侧通过连接支板与两倒L型连接架53相连,该集料杆51靠近导向杆52的一端向上倾斜,并与连接板上下重叠。当活塞环沿导向杆52落下后,能同时套入理料杆55、连接板及集料杆51上,在理料杆55的带动下,能使活塞环的缺口与理料杆55正对;当活塞环的缺口与理料杆55正对时,活塞环能够从理料杆55和连接板上落下,仅套在集料杆51上,并沿集料杆51的倾斜段移动后,在惯性作用下移动至集料杆51的另一端。具体实施时,该集料杆51包括前段、中段和后段,其中,前段和后段分别与倒L型连接架53固定连接,中段分别与前段和后段卡接;从而方便将加工完成后的活塞环取下。该全自动磨床由与之相配合的控制系统进行控制。工作过程中,根据需要(活塞环斜面加工要求),先手动转动动力头架4(通过转动蜗杆实现动力头架4的转动),使动力头架4靠近导轨的一端朝复合加工台3(或自动上下料架2方向)倾斜;该(转动动力头架4)动作只在活塞环更换规格时根据斜面角度才做的调整,平时动力头是由连接螺杆411锁死不动的。初始状态送料滑台位于支板正下方,控制系统控制全自动磨床启动后,砂轮34开始并一直保持转动:首先,启动推料气缸24带动V形推料板23朝推料气缸24方向移动,直至活塞环落下并落入上料板25的V形定位槽27内,然后,推料气缸24推动V形推料板23,通过V形推料板23推动活塞环,使活塞环移动至V形定位的封闭端,由定位槽27将活塞环卡紧。其次,启动送料气缸,通过送料气缸推动送料滑台,同时,动力头架位移伺服电机48带动动力头架滑台47朝导轨方向移动,当送料滑台的上料板25上的活塞环移动至与动力头架4上的活塞环定位装置相对应时,通过推拉气缸带动支撑板210转动,使上料板25翻转后活塞环能够与定位盘43上的定位孔正对。然后,上料翻转气缸211推动上料板25翻转,当活塞环与定位盘43上的定位孔正对后,上料推环气缸29启动,将活塞环推入定位盘43上的定位孔内;同时,电磁吸盘42通电,将活塞环紧紧吸附在定位盘43上,从而实现将活塞环安装到动力头架4上并定位;之后,上料板25复位,送料气缸带动送料滑台回到初始位置。再次,位移伺服电机带动滚珠丝杆副推动加工滑台31移动,直至加工滑台31上的刀头与活塞环的内侧面位置相对应,这时,直线电机35推动刀头,直至刀头与活塞环内侧面接触,通过动力头架4带动活塞环转动,实现车削加工,车削过程中,驱动电机46带动轴管转动,通过轴管带动定位盘43及活塞环转动,同时,动力头架位移伺服电机48带动动力头架滑台47微量移动,从而完成活塞环斜端面的车削加工;车削加工完成后,位移伺服电机通过滚珠丝杠副继续推动加工滑动移动,直至砂轮34与活塞环端面接触后,通过磨削电机33带动砂轮34转动,同时由于动力头架4带动活塞环转动,从而实现活塞环端面加工,加工完成后,复合加工台3回位。最后,送料滑台重新上料后朝复合加工台3方向移动,当下料杆213与活塞环正对时,下料推环气缸44通过下料推爪将活塞环推出,套入下料杆213上;然后,通过旋转气缸带动下料杆213转动,当下料杆213套有活塞环的一端进入导向杆52上的通槽54时,活塞环滑入导向杆52,并通过导向杆52的导向移动至同时套设在理料杆55和存料杆上;此时,理料杆55在理料电机56的带动下转动,使活塞环的缺口与理料杆55正对,进而使活塞环从理料杆55上落下,仅套在存料杆上,并沿存料杆移动至存料杆的另一端。而同时,上料板25上的活塞环在送料滑台的带动下,其位置与动力头架4的活塞环定位装置相对应。重复上述过程,实现活塞环端面连续自动加工。最后需要说明的是,以上实施例仅用以说明本发明的技术方案而非限制技术方案,本领域的普通技术人员应当理解,那些对本发明的技术方案进行修改或者等同替换,而不脱离本技术方案的宗旨和范围,均应涵盖在本发明的权利要求范围当中。