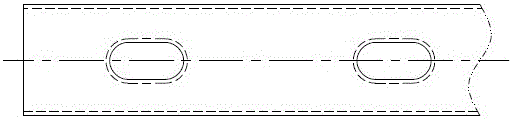
本实用新型涉及一种金属型材,尤其是一种冷弯金属龙骨,同时还涉及其成型工艺方法,属于金属结构件技术领域。
背景技术:
据申请人了解钢结构工程中,檩条及墙梁等结构件(工程中通常称为冷弯金属龙骨)常采用截面呈半包围结构(例如C形)的冷弯薄壁型钢。此类型钢一般由冷弯薄壁钢板通过檩条机冷弯辊压成型,并沿长度方向间隔分布有穿孔。为了解决开孔后截面强度削弱的问题,檩条上间隔分布的穿孔常采用冲孔工艺制成翻边孔(参见图1、图2)。
上述现有技术在冲孔时不仅有可能产生型钢变形,而且虽然理论上翻边高度越高、强度和刚性就越好,但实际上冲孔翻边高度越高就越容易开裂和变形,从而降低檩条强度。随着建筑业的不断发展,对具有间隔穿孔型钢的强度、材料损耗率以及标准化等要求越来越高,上述现有技术存在的缺点已难以满足这些要求。
技术实现要素:
本实用新型的目的在于:针对上述现有技术存在的缺点,提出一种可以显著提高强度和刚性的冷弯金属龙骨,同时给出相应的成型工艺方法,从而切实满足建筑等行业迅猛发展的要求。
为了达到以上目的,本实用新型的冷弯金属龙骨包括截面呈半包围结构的檩条主体,所述檩条主体上具有沿长度方向间隔分布的卷边孔,其特征在于:所述卷边孔的翻边外围箍有围圈,所述翻边的边缘外卷围住围圈。
上述截面的半包围结构可以是C形结构、U形结构或m形结构。
本实用新型进一步的完善是,所述围圈的截面为矩形,所述翻边朝向卷边孔内的一侧呈圆弧状。或,所述围圈截面的内侧呈凸弧形,所述翻边对应处的截面呈围住围圈的凹弧形。
本实用新型冷弯金属龙骨的成型工艺方法至少包括以下步骤:
步骤E、套圈——把沿长度方向间隔分布有垂直翻边孔的檩条主体放置在输送辊道上送进,将内廓与垂直翻边孔的垂直翻边外廓相配的围圈逐一套在垂直翻边孔外;
步骤F、压边——完成套圈的檩条主体继续在输送辊道上送进,经过上压边辊和具有圆周间隔分布对应垂直翻边孔压边凸模的下压边辊之间,使垂直翻边的边缘外卷围住围圈。
由于本实用新型在卷边孔外包箍围圈,因此解决了开孔截面强度削弱后为获得高强度增高卷边与开孔及卷边过高容易开裂反而降低强度和刚度的矛盾。采用本实用新型的方法则不仅可以实现高强檩条的连续高效生产,而且滚压工艺具有逐步压延的工效,因此可以避免冲压工艺卷边的开裂问题。
附图说明
下面结合附图对本实用新型作进一步的说明。
图1为现有檩条的结构示意图。
图2为图1的截面结构示意图。
图3为本实用新型一个实施例的檩条截面结构示意图。
图4为条状金属板材冲孔步骤结构示意图。
图5为冲孔后的折边步骤结构示意图。
图6为折边后的卷边步骤结构示意图。
图7为卷边后的翻边步骤结构示意图。
图8为翻边后的套圈步骤结构示意图。
图9为套圈后的压边步骤结构示意图。
图10为串联成生产线的各工艺设备结构示意图。
图11为截面呈U形的檩条主体结构示意图。
图12为截面呈m形的檩条主体结构示意图。
具体实施方式
实施例一
本实施例的冷弯金属龙骨基本结构如图3所示,截面呈C形的檩条主体1上具有沿长度方向间隔分布的翻边孔2,翻边孔2的翻边4外围箍有截面为矩形的围圈3,翻边4的边缘外卷围住围圈3,其朝向翻边孔的一侧呈圆弧状。
其完整的具体成型工艺方法包括如下步骤:
步骤A、冲孔——将条状金属板材放置在输送辊道上送进,经过具有圆周分别分布对应腰形凸模AT和凹模AQ的成对上冲压辊AH和下冲压辊AL之间,冲压出间隔分布的待翻边腰形底孔2-A,参见图4。
步骤B、折边——将具有间隔分布腰形底孔2-A的条状金属板材在输送辊道上继续送进,通过一组具有两外侧压面BW的上侧压辊BH和一组具有两内侧压面BN的下侧压辊BL之间,相对侧压面的间距沿送进方向渐缩,从而将条状金属板材两侧逐渐收折,形成折边4-B,上侧压辊BH和下侧压辊BL即可上下成对分布,也可以错位分布,参见图5。
步骤C、卷边——将折边后的条状金属板材在输送辊道上继续送进,通过一组具有两外侧挡面CW及外滚压圈CG的上侧压辊CH和一组具有两内侧挡面CN的下侧压辊CL之间,上侧压辊CH和下侧压辊CL成对分布,成对上侧压辊CH的外滚压圈CG外圆和下侧压辊CL的外圆滚切,上侧压辊CH的外滚压圈CG外圆直径沿送进方向渐扩而下侧压辊CL的外圆直径沿送进方向渐缩,从而将折边后的条状金属板材两侧折边A-B边缘逐渐收卷,形成具有卷边4-C的截面整体呈C形的檩条主体,参见图6。
步骤D、翻边——将檩条主体在输送辊道上继续送进,经过具有圆周分别分布对应腰形凹陷模DQ和台阶凸模DT的成对上翻边辊DH和下翻边辊DL之间,台阶凸模DT的台阶头与凹陷模DQ之间留有翻边间隙,从而挤压出间隔分布的垂直翻边腰形孔2-D,参见图7。
步骤E、套圈——把沿长度方向间隔分布有垂直翻边腰形孔2-D的C形截面檩条主体1在输送辊道上继续送进,将内廓与垂直翻边腰形孔2-D的垂直翻边外廓相配的矩形截面围圈3逐一套在垂直翻边腰形孔外,参见图8。
步骤F、压边——将完成套圈的檩条主体1继续在输送辊道上送进,经过成对的上压边辊FH和具有圆周间隔分布对应垂直翻边腰形孔2-D压边凸模FT的下压边辊FL之间,使垂直翻边的边缘外卷围住围圈3,成形卷边孔2,并且由于压边凸模FT的端头具有圆弧倒角,因此翻边朝向卷边孔内的一侧呈圆弧状,参见图9。
由于以上工艺步骤分别通过辊道上送进的相应辊压设备实现,因此可以如图10所示串联为生产线,各工艺步骤在串联成生产线的设备上完成,从而大大提高生产效率。
下表为试验得出的本实施例的冷弯金属龙骨物理力学性能指标,比原有技术均提高了30%以上。
本实施例的结构由于在翻边孔外包箍有围圈,因此无需增高翻边即可显著提高檩条强度和刚性——试验表明,强度和刚性分别比现有技术提高30%和50%,妥善解决了为获得高强度增高翻边与翻边高容易开裂反而降低强度的矛盾。采用本实施例的方法则不仅可以实现高强檩条的连续高效生产,而且滚压工艺具有逐步压延的工效,因此有利于避免开裂。尤其是针对围圈截面的内侧呈凸弧形、翻边对应处的截面呈围住围圈的凹弧形结构,压边时的对应压边凸模具有相应的弧形过渡角,因此更有利于垂直翻边的边缘顺畅压延外卷围住围圈,避免开裂。
图11、图12所示截面分别呈U形和m形的檩条主体结构及成型工艺方法根据上述实施例不难推知,故不另详述。
除上述实施例外,本实用新型还可以有其他实施方式。凡采用等同替换或等效变换形成的技术方案,均落在本实用新型要求的保护范围。