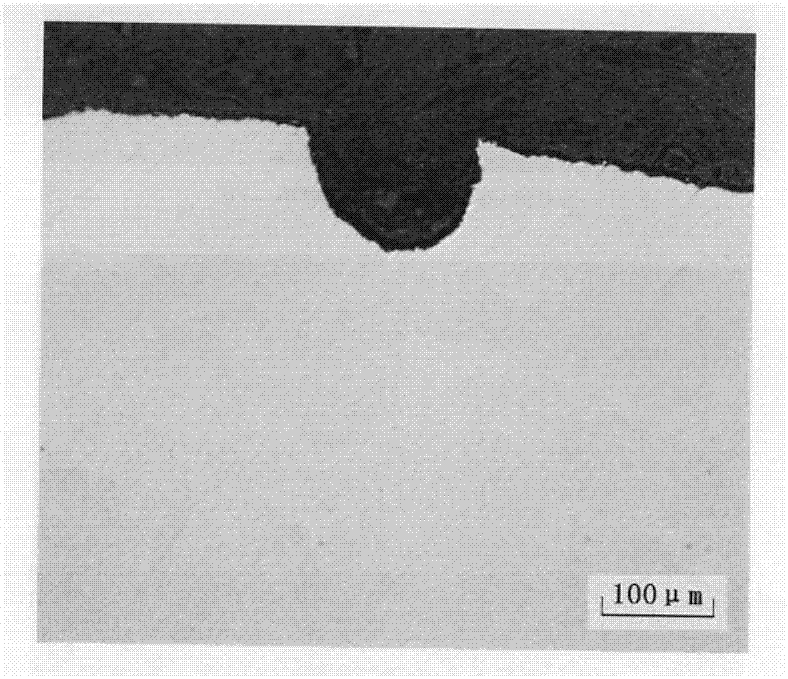
本发明涉及钢铁冶炼技术领域,具体涉及一种高线精轧机组出口到吐丝机盘条恒微张控制装置和方法。
背景技术:
高线精轧出口辊道一般都是滑动或滚动的,如附图1所示,最后一架精轧机出口到吐丝机之间有6段滑动辊道,由于轧件的高速运动,滑动辊道很容易把轧件划伤,划伤的原因主要是滑动辊道的老化,还有就是吐丝机前的夹送辊速度比精轧机速度慢,或者说吐丝速度比轧制速度慢,造成轧件下垂或上弓,或左弓或右弓,与滑动辊道强力相擦,从而划伤轧件,盘条的划伤主要发生在轧件出最后一架精轧机到吐丝机。若改用滚动辊道,很易被轧件冲坏,或被轧件拱坏。盘条热划伤见图1所示。
技术实现要素:
本发明的目的在于提供一种高线精轧机组出口到吐丝机盘条恒微张控制装置和方法,本发明能有效减少盘条划伤和多头缺陷,增加滑动辊道寿命。
为解决上述技术问题,本发明所设计的高线精轧机组出口到吐丝机盘条恒微张控制装置,它包括精轧机、第一轧件输送喇叭口、多个滑动辊道、第二轧件输送喇叭口、夹送辊和吐丝机,所述精轧机的输出端对应第一轧件输送喇叭口的大端口,多个滑动辊道沿轧件输送方向依次布置,其中第一个滑动辊道与第一轧件输送喇叭口的小端口对应,最后一个滑动辊道与第二轧件输送喇叭口的大端口对应,第二轧件输送喇叭口的小端口与夹送辊的输入端对应,夹送辊的输出端与吐丝机的输入端对应,其特征在于:它还包括多个伸缩式支撑辊机构,相邻两个滑动辊道之间设置一个伸缩式支撑辊机构;
轧制前,各个伸缩式支撑辊机构的上辊面低于滑动辊道下内面,轧件头部到达夹送辊时,各个伸缩式支撑辊机构的上辊面上升到滑动辊道内孔的中间高度位置,如此,万一轧件在轧制过程中出现上弓、左弓、右弓,也会减轻轧件与滑动辊道内孔的摩擦。当轧件尾部进入第一架精轧机,即开始抛尾,此时各个伸缩式支撑辊机构下降,轧件尾部到达第一喇叭口各个伸缩式支撑辊机构上辊面已下降到低于滑动辊道下内面,其目的是为了保护伸缩式支撑辊机构。
一种利用上述装置的高线精轧机组出口到吐丝机盘条恒微张控制方法,其特征在于,它包括如下步骤:
步骤1:由精轧机输出的轧件进入第一轧件输送喇叭口;
步骤2:轧件的头端由第一轧件输送喇叭口输出并到达夹送辊时,各个伸缩式支撑辊机构的支撑辊的上辊面上升到滑动辊道内孔的中间高度位置;
步骤3:轧件由滑动辊道进行输送,各个伸缩式支撑辊机构的支撑辊托起相邻两个滑动辊道之间的轧件使其悬空;
步骤4:当轧件尾部进入精轧机,即开始抛尾,此时各个伸缩式支撑辊机构下降,轧件尾部到达第一轧件输送喇叭口2时各个伸缩式支撑辊机构上辊面已下降到低于滑动辊道下内面,其目的是为了保护伸缩式支撑辊机构。
本发明通过以上设计能有效减少盘条划伤和多头缺陷,增加滑动辊道寿命,适用于高级盘条的生产。
附图说明
图1为盘条热划伤图;
图2为本发明的结构示意图;
图3为没有伸缩式支撑辊机构时的受力简图;
图4为有伸缩式支撑辊机构时的受力简图;
其中,1—精轧机、2—第一轧件输送喇叭口、3—滑动辊道、3.1—下内面、4—第二轧件输送喇叭口、5—夹送辊、6—吐丝机、7—伸缩式支撑辊机构、7.1—液压缸、7.2—支撑辊、7.3—活塞杆、8—轧件
具体实施方式
以下结合具体实施例对本发明作进一步的详细说明:
一种高线精轧机组出口到吐丝机盘条恒微张控制装置,如图2所示,它包括精轧机1、第一轧件输送喇叭口2、多个滑动辊道3、第二轧件输送喇叭口4、夹送辊5和吐丝机6,所述精轧机1的输出端对应第一轧件输送喇叭口2的大端口,多个滑动辊道3沿轧件输送方向依次布置,其中第一个滑动辊道3与第一轧件输送喇叭口2的小端口对应,最后一个滑动辊道3与第二轧件输送喇叭口4的大端口对应,第二轧件输送喇叭口4的小端口与夹送辊5的输入端对应,夹送辊5的输出端与吐丝机6的输入端对应,其特征在于:它还包括多个伸缩式支撑辊机构7,相邻两个滑动辊道3之间设置一个伸缩式支撑辊机构7;
轧制前,各个伸缩式支撑辊机构7的上辊面低于滑动辊道3下内面3.1,轧件8头部到达夹送辊5时,各个伸缩式支撑辊机构7的上辊面上升到滑动辊道3内孔的中间高度位置托起相邻两个滑动辊道3之间的轧件8使其悬空。
上述技术方案中,所述每个伸缩式支撑辊机构7均包括液压缸7.1和支撑辊7.2,所述液压缸7.1的活塞杆7.3顶端安装有支撑辊7.2,液压缸7.1控制对应支撑辊7.2的伸缩;
轧制前,各个伸缩式支撑辊机构7的支撑辊7.2的上辊面低于滑动辊道3下内面3.1,轧件8头部到达夹送辊5时,各个伸缩式支撑辊机构7的支撑辊7.2的上辊面上升到滑动辊道3内孔的中间高度位置。
上述技术方案中,每个伸缩式支撑辊机构7的支撑辊7.2同步伸缩。
上述技术方案中,所述伸缩式支撑辊机构7的支撑辊7.2随轧件运动而转动。
一种利用上述装置的高线精轧机组出口到吐丝机盘条恒微张控制方法,其特征在于,它包括如下步骤:
步骤1:由精轧机1输出的轧件8进入第一轧件输送喇叭口2;
步骤2:轧件8的头端由第一轧件输送喇叭口2输出并到达夹送辊5时,各个伸缩式支撑辊机构7的支撑辊7.2的上辊面上升到滑动辊道3内孔的中间高度位置;
步骤3:轧件8由滑动辊道3进行输送,各个伸缩式支撑辊机构7的支撑辊7.2托起相邻两个滑动辊道3之间的轧件8使其悬空;
步骤4:滑动辊道3将轧件8送至夹送辊5,并由夹送辊5送至吐丝机6。
步骤5:当轧件8尾部进入精轧机1,即开始抛尾,此时各个伸缩式支撑辊机构7下降,轧件8尾部到达第一轧件输送喇叭口2时各个伸缩式支撑辊机构7上辊面下降到低于滑动辊道3下内面3.1,其目的是为了保护伸缩式支撑辊机构7,等待下一支轧件轧制,如此反复。
为了说明本发明的效果,对精轧机1、吐丝机6和处在它们之间的轧件8进行力的分析,首先对其进行简化,如附图3所示,进一步简化为一端固定(轧机端相当对轧件固定),一端施加拉力(夹送辊对轧件不变形,相当于只施加拉力)的悬索结构,本实施例以均布的3个伸缩式支撑辊机构7支撑轧件8,三个伸缩式支撑辊机构7作用在轧件上,为3次超静定问题,如附图4所示,虽说是超静定问题,但它是悬索结构,其只会承受支承力,悬索也承受拉力f和精轧机1、夹送辊5、三个伸缩式支撑辊机构7共5个支承力,5个支承力分别为ql/8、ql/4、ql/4、ql/4、ql/8。在没有3个伸缩式支撑辊机构7作用时,悬索的中间最大下垂为p,附图3所示。此下垂度与拉力f有关,下垂度p和拉力f及单位载荷q之间关系见下式:
f=ql2/(8p)
式中:f为悬索内的拉力,kg;
q为悬索单位重量,kg/m;
p为悬索中间最大下垂度,m;
l为两个支柱之间悬索的长度,m。
从上式看出p=ql2/(8f),从不划伤盘条的角度看,悬索中间最大下垂度p应越小越好,在悬索单位重量q和两个支柱之间悬索的长度l一定情况下,要想悬索中间最大下垂度p小,必须加大拉力f,但拉力f的加大是有限度的,当加大到足以是盘条产生塑性变形,就会拉断盘条,形成多头,悬索中间最大下垂度p的加大也会使盘条直接与滑动辊道接触,使滑动辊道加速磨损。当f和l一定情况下,粗规格盘条下垂更多些。
当f和悬索单位重量q一定情况下,本发明采取减小支柱与支柱之间距离的办法,即增加3个伸缩式支撑辊机构7,减小p值。从而使轧制时轧件悬空。
当轧制一定规格的轧件,为了使轧制稳定,f应恒定,在增加了支承辊后f可以减小。从而达到恒微张力轧制,保证产品质量。q就是轧件单位重量。各规格单位重量见下表:
下面计算如果没有支承辊的情况下f的最小值,若l为10m,轧制盘条直径为10mm,若滑动辊道高度为20mm,则p最大为10mm,此时对应的f最小为:
f=ql2/(8p)=0.612×102/(8×0.01)=765(kg)
盘条横截面的应力为:95.5mpa。但若在700-1000℃终轧,盘条此时的变形抗力只有50-80mpa左右,所以要想轧件在此10m内完全悬空,不与滑动辊道接触是不可能的,否则的话就会被拉断。
下面看在增加3个伸缩式支撑辊机构7的情况下f的最小值,此时l=10/4mm,p仍取0.01m,此时对应的f最小为:
f=ql2/(8p)=0.612×2.52/(8×0.01)=47.81(kg)
盘条横截面的应力为:5.97mpa。在700-1000℃终轧,盘条此时的变形抗力为50-80mpa左右,5.97mpa比50mpa小很多,所以轧件不与滑动辊道接触是完全可以的。为了更保险,把盘条横截面内的应力增加到10mpa,此时对应的拉力f增加到80.1kg,对应的p为6mm。从上面分析看出每2.5m长滑动辊道增加1个支承辊,就可使轧件在轧制时不与滑动辊道接触,且使轧件内的张力大大小于盘条变形抗力,从而使轧件划伤和多头基本消除。
伸缩式支撑辊机构7是可随轧件运动而转动的,不会使轧件划伤,且支承辊是可上下移动的,轧制前,支承辊辊面低于滑动辊道下内面,当轧件头部到达夹送辊时支承辊上辊面上升到滑动辊道内孔高度中间,托起轧件使其悬空。
本说明书未作详细描述的内容属于本领域专业技术人员公知的现有技术。