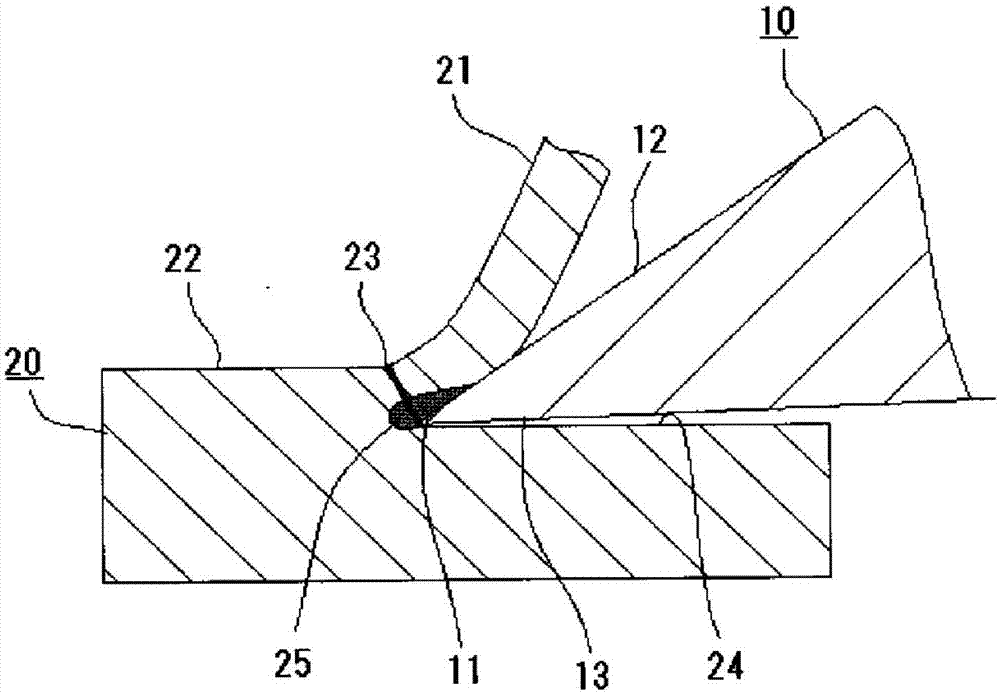
本发明涉及机械加工刀具的刀刃部结构及其表面处理方法,更详细地说,涉及钻头、立铣刀、滚刀、拉刀、铰刀等切削刀具和冲头等冲裁刀具之类的具备用于切削或切断的刀刃(刃)的机械加工刀具的所述刀刃部结构及其表面处理方法。
背景技术:
以所述机械加工刀具中的切削刀具为例进行说明。在切削加工中,如图1所示,由切削刀具10的刀刃11物理性地切入被加工物20的表面并割裂,从而切掉被加工物20的一部分。并且,一边排出由该切削产生的切削碎片(切屑)21,一边连续地推进刀刃11进行切削。理想的切削是切削刀具10的刀刃11以不会勉强地切削被加工物20的深度进入被加工物20的表面。在进行该理想的切削时,作为切屑21而排出的被加工物的断片从切削刀具10的刀刃11延伸到被加工物20的表面22,因剪切面23而受到连续的滑动破坏从而被削掉。并且,形成在切削刀具10的前刀面上滑动并连续排出的所谓“流动型”的切屑21。在这样的切削状态下,切削阻力大致一定,振动也小,能够形成表面不粗糙的良好的成品面24。在所述切削加工中,由于在切屑21与切削刀具10的前刀面12之间产生的高的压力、大的摩擦阻力以及切削热,从而切屑21的一部分由于物理性、化学性变化而粘合到刀刃11的前方部分。由于该粘合的切屑,从而在切削刀具10的刀刃11形成与原本的刀刃不同的被称为“积屑瘤”的新的刀刃。并且,该积屑瘤25作为切削刀具10的刀刃11的一部分,对被加工物20进行切削。所述积屑瘤25由于加工硬化而变为高硬度,所以也可以认为积屑瘤25具有保护切削刀具10的原本的刀刃11的功能。但是,当生成所述积屑瘤25时,由于刀刃11钝化而有损锋利性,所以成品面24变粗糙,另外,积屑瘤25的顶端比切削刀具10原本的刀刃11更靠下方,所以切入量变大,加工精度也会降低。并且,如此由于积屑瘤25的顶端位于原本的刀刃11的下方,所以摩擦阻力的增大和过切削会导致切削阻力增大。由此,产生切削温度的上升和切削刀具的早期磨损,并且积屑瘤25由于切屑的粘合而成长,当成长到某种程度就会剥离。由于该动作周期性地反复,所以积屑瘤25的生成导致针对被加工物20的加工状态不稳定,成为导致被加工物20的成品面24变粗糙的原因。另外,如上所述,积屑瘤成为切削阻力增大的原因之一,在切削阻力大的状态下,积屑瘤陷入被加工物中并剥离时,积屑瘤的脱落强度变大,刀刃承受非常强的负荷。强负荷集中到刀刃,成为产生崩缺(chipping)、缺口的原因。如此,作为应对与形成在切削刀具10的刀刃11上的积屑瘤25相关的问题的以往技术,提出了如下方案:(a)保持粘合、成长的积屑瘤25使其不从切削刀具10的刀刃11脱落,(b)在粘合的积屑瘤25成长之前将其去除,(c)防止积屑瘤25粘合于切削刀具10的刀刃11。其中,作为(a)保持粘合、成长的积屑瘤25使其不从切削刀具10的刀刃11脱落的方案,提出了通过在切削刀具10的前刀面12设置一端与刀刃11连通而能够向刀刃11引导切削油的导油槽,从而生成的积屑瘤25进入导油槽,利用“锚固效应”增加积屑瘤25与切削刀具基体材料的结合力,防止积屑瘤25脱落,使积屑瘤25作为对切削刀具10的刀刃11进行保护的保护膜发挥功能(专利文献1)。另外,作为(b)在粘合的积屑瘤25成长之前使其脱落的方案,提出了在由切削刀具10切削被加工物20时,通过多次反复地使切削刀具10或者被加工物20瞬间地略微反向旋转,从而在该反向旋转时一边去除粘合在切削刀具10的刀刃11上的积屑瘤25一边进行切削的方法(专利文献2),以及一边对切削刀具10和被加工物20的任意一方赋予与其切削行进方向大致相同方向的超声波振动,一边进行被切削面的加工的拉刀加工方法(专利文献3)。此外,作为(c)防止积屑瘤25粘合到切削刀具10的刀刃11上的方案,提出了用原子%比为n:40~60%、ti:40~60%、剩余部分为实质不可避免的杂质构成的硬质覆盖膜,来覆盖切削刀具10的与被加工物20接触的面的一部分或者全部的表层(专利文献4),以及使刀刃11部分的表面粗糙度为ra:0.3μm以下,且至少对该刀刃11部分形成厚度为2μm以下的ticn系涂覆层等(专利文献5)。专利文献1:日本专利公开公报特开2013-146819号专利文献2:日本专利公开公报特开2004-268176号专利文献3:日本专利公开公报特开平9-108936号专利文献4:日本专利公开公报特开2006-255848号专利文献5:日本专利公开公报特开2001-277004号在上述的作为以往技术介绍的现有技术中,专利文献1记载的发明提出了通过在切削刀具10的前刀面12形成导油槽,使刀刃11上产生的积屑瘤25难以脱落,积极地使该积屑瘤25粘合,用作保护切削刀具10的原本的刀刃11的保护膜。在此,如上所述,由于在切削刀具10的刀刃11上生成的积屑瘤25的硬度高,所以如果能够维持附着有积屑瘤25的状态,也可以视为能够期待积屑瘤25作为保护膜发挥功能。但是,在该方法中,由于形成积屑瘤25而导致刀刃11钝化,并且相对于原本的切削位置,被加工物20的表面被较深地削除。因此,由于切削阻力增大而导致发热温度上升,所以可以预测到不能由积屑瘤25保护的后刀面13的磨损会加速,其结果,切削刀具10会早期磨损。并且,在该结构下,伴随积屑瘤25的成长,刀刃的角度变化而使切削深度变化,如果不进行根据积屑瘤25的成长而改变切削刀具10相对于被加工物20的表面的接触角度等措施,就不能以稳定的加工状态进行加工,成品面24变得粗糙。另外,在专利文献1记载的方法中,由于形成导油槽而使粘合于前刀面12的积屑瘤25难以脱落。因此,即使能够保护前刀面12,最大成长的积屑瘤25最终也会脱落。因此,不能防止由于积屑瘤25的粘合、成长、脱落周期性地重复而产生的成品面24的粗糙。可以认为特别是由于形成导油槽而难以脱落的积屑瘤25长得更大才脱落,其结果,可以预料到会更进一步加剧成品面的粗糙(凹凸)。在专利文献2、3记载的方法中,通过使切削刀具10或者被加工物20相对于切削方向反向旋转(专利文献2),或者沿着与切削方向相同的方向赋予超声波振动,能够将粘合到切削刀具10的刀刃11上的积屑瘤25在成长之前去除。但是,在该方法中,切削加工时的切削刀具10和被加工物20的动作变复杂,装置构成和装置的动作控制也变复杂。并且,通过定期地反向旋转或者赋予振动,不会得到在理想的切削状态下由连续的滑动破坏所产生的切削,切削阻力经常变动,利用一定周期各自的剪切滑动切削被加工物的表面,排出所谓的“剪切型”或者“撕裂型”的切屑,其结果,成品面24形成凹凸或撕裂痕迹,变得粗糙。因此,如果想要得到美观的成品面24,则希望能够防止积屑瘤25粘合于切削刀具10的刀刃11这一现象本身。作为这样的构成,在前述的专利文献4、5中提出了在切削刀具10的刀刃11部分形成tin或ticn等陶瓷系涂覆层。如此,在设置了陶瓷系涂覆层的构成中,由于存在涂覆层,不仅难以产生积屑瘤25的粘合,而且陶瓷系涂覆层的硬度高,也能够期待作为抑制刀刃11磨损的保护膜发挥功能。但是,即使在设置了这样的涂覆层的构成中,也不能完全防止积屑瘤25的粘合,另外,如果涂覆层剥离,则作为积屑瘤25的粘合防止膜的效果和作为刀刃11的保护膜的效果都会消失,所以由该方法进行表面处理也并不完美。并且,这样的涂覆层的形成通常是利用以溅射或离子镀为代表的“物理蒸镀(pvd)”来进行的(专利文献1的[0047]段、专利文献5的[0006]段),由于对切削刀具10形成涂覆层或修复剥离的涂覆层都需要昂贵的pvd装置,并且需要在高真空下的真空腔内精确地管理温度、反应气体的导入速度、处理时间等来形成涂覆层,所以涂覆层的形成需要很大的成本。因此,对如下的表面处理方法的期望较高:该表面处理方法能够更简单且低成本地得到与形成涂覆层相同的防止积屑瘤25粘合和实现刀刃11部分的表面硬化的效果。在此,前述的专利文献1中,为了促进积屑瘤25的粘合和防止粘合的积屑瘤25剥离,采用了在切削刀具10的前刀面12设置了导油槽的构成。另外,在专利文献5中,为了防止积屑瘤25粘合,提出了形成切削刀具10的刀刃11部分的表面粗糙度ra为0.3μm以下的平滑的面之后,形成涂覆层,由此使涂覆层的表面平滑。从这些以往技术的存在可知,积屑瘤25对切削刀具10的刀刃11部分的粘合,在切削刀具10的刀刃11部分的表面形成有凹凸时容易产生。(除了专利文献1之外,参照专利文献4的[0006]段。在此,作为产生积屑瘤的原因,列举了磨损而导致的表面粗糙度恶化)。并且,生成的积屑瘤由于“锚固效应”而牢固地附着(专利文献1)。相反,可以认为在将切削刀具10的刀刃11部分平坦加工时,能够抑制积屑瘤25的粘合,这属于本领域技术人员的技术常识。但是,本发明的发明人进行了深入研究,其结果开发了一种方法,通过对切削刀具10的刀刃11部分实施由预定的方法形成凹凸的表面处理,能够降低切削刀具等机械加工刀具的刀刃11部分的摩擦阻力,防止发生积屑瘤25之类的被切削物的粘合,并且能够提高进行了表面处理的部分的表面硬度。即使在无润滑或者低润滑的状态下,通过降低伴随切削而产生的切屑21与刃面及前刀面之间的摩擦,提高了切屑21的排出性。由于降低摩擦能够抑制切屑21和刃面变为高温,所以也能够通过防止粘合来提高耐久性。并且,这样的表面处理能够使用比进行物理蒸镀(pvd)的装置廉价的喷丸加工装置,只要进行喷射大致球状的喷射颗粒这样的比较简单的处理就能够实施,与形成陶瓷系涂覆层的处理等相比,能够用极其低的成本且简单地进行表面处理。此外,在以上的说明中,作为具备刀刃的机械加工刀具,以切削刀具为例进行了说明,在此说明的课题不仅存在于切削刀具,而且也是例如用于冲裁加工的冲头之类的具备切削或切断时成为剪切的起点的刀刃(刃)的机械加工刀具全体(以下将它们仅统称为“加工刀具”)共同存在的课题。技术实现要素:本发明是根据本发明的发明人的上述研究结果得到的认识而提出的,目的在于提供一种机械加工刀具的刀刃部结构及其表面处理方法,能够防止积屑瘤粘合到切削刀具等加工刀具的刀刃部,并且能够提高刀刃部的表面硬度,由此能够形成不粗糙的成品面,并且也能够提高加工刀具自身的耐久性。以下,将具体实施方式中使用的附图标记与用于解决课题的手段一同记载。该附图标记用于明确权利要求的记载和具体实施方式的记载的对应关系,当然并不是用于限制本发明的技术范围的解释。用于实现上述目的的本发明的机械加工刀具的刀刃部的表面处理方法的特征在于,将机械加工刀具10的刀刃(刃)11和所述刀刃11附近的优选距刀刃11至少为1mm、更优选至少为5mm的范围的区域15作为处理区域15,以0.01mpa~0.7mpa的喷射压力对所述处理区域15喷射中位直径为1~20μm的大致球状的喷射颗粒,形成当量直径为1~18μm、优选为1~12μm,深度为0.02~1.0μm以下的凹坑16,使所述凹坑16的投影面积为所述处理区域15的表面积的30%以上(权利要求1)。在此,“中位直径”是指从某一粒子直径将粒子群分为两份时,大的一侧的粒子群的累计粒子量和小的一侧的粒子群的累计粒子量等量的直径(累积分布50vol%的直径)。另外,“当量直径”是指将形成于处理区域15的一个凹坑16的投影面积(在本说明书中,“投影面积”是指所述凹坑16的外轮廓的面积)换算为圆形的面积进行测定时的所述圆形的直径。在所述机械加工刀具的刀刃部的表面处理方法中,优选在喷射所述喷射颗粒之前,将所述处理区域15预备研磨到ra为3.2μm以下的表面粗糙度(权利要求2)。此时,也可以通过对磨粒分散于弹性件或磨粒承载于弹性件表面而形成的弹性研磨材料进行喷射,并使所述弹性研磨材料在所述处理区域15上滑动,来进行所述预备研磨(权利要求3)。此外,也可以对进行了tialn、dlc(类金钢石:diamond-likecarbon)等陶瓷涂覆的所述处理区域15进行所述喷射颗粒的喷射(权利要求4)。在进行陶瓷系涂覆的处理时,可以认为只有涂覆层发生细化,因此,可以推测对母材几乎不产生影响。此外,也可以在喷射所述喷射颗粒之后,对所述处理区域15涂覆tialn、dlc(类金钢石)等陶瓷(权利要求5)。另外,也可以在形成所述凹坑之后,对所述处理区域15进行事后研磨,所述事后研磨用于去除形成所述凹坑16时产生的微小的突起17(权利要求6),此时,也可以对磨粒分散于弹性件或者磨粒承载于弹性件表面而形成的弹性研磨材料进行喷射,并使所述弹性研磨材料在所述处理区域15上滑动,来进行所述事后研磨(权利要求7)。另外,本发明的机械加工刀具的刀刃部结构的特征在于,对机械加工刀具10的刀刃(刃)11和所述刀刃11附近的优选距刀刃11至少为1mm、更优选至少为5mm的区域15,形成当量直径为1~18μm、优选为1~12μm,深度为0.02~1.0μm以下的凹坑16,并且所述凹坑16的投影面积为所述处理区域15的表面积的30%以上(权利要求8)。通过使用由以上说明的本发明的表面处理方法进行了刀刃部分的表面处理的加工刀具,能够得到以下的显著效果。在由本发明的方法对包含刀刃11的预定范围(处理区域15)进行了处理的加工刀具10中,违背了上述的技术常识,尽管由于形成凹坑16而导致表面形成有凹凸,但是能够抑制积屑瘤25的生成。即,由本发明的刀刃处理方法处理的处理区域15形成有所述的凹坑16,该凹坑16作为油槽发挥功能。因此,在刀刃11和距该刀刃11处于一定范围的前刀面12和/或后刀面13上形成润滑油(切削油)的油膜。由此,大幅度地降低了加工刀具10的刀刃11和刀刃附近的前刀面12与切屑21之间的摩擦阻力、以及后刀面13与成品面24之间的摩擦阻力,抑制了导致切屑21硬化并粘合于前刀面12的原因,即抑制了大的摩擦阻力和切削热的产生。可以认为其结果可以防止积屑瘤25的生成。如此,由本发明的表面处理方法对刀刃11部分进行了处理的加工刀具10由于抑制了积屑瘤25的生成,其结果能够消除伴随积屑瘤25的生成而产生的问题:诸如刀刃11的钝化、切入量的增大、随之而来的加工精度降低、由摩擦阻力或过切削导致的切削阻力增大、切削温度上升和切削刀具的早期磨损、由积屑瘤的脱落导致的崩缺或缺口、由于切削阻力变化导致的成品面24产生表面粗糙。另外,利用所述喷射颗粒的碰撞而形成凹坑16,由此伴随处理区域与喷射颗粒的碰撞而产生的变形,能够使处理区域的距表面约为3μm的范围的晶粒细化,利用该细化,能够抑制由于切削加工时产生的热量引起的膨胀和收缩而产生的热龟裂(热裂纹)的发生等,能够利用比较简单的处理提高表面硬度。另外,由于喷射颗粒的碰撞产生的变形能够对处理区域赋予压缩残留应力,所以能够进一步提高由本发明的方法处理的刀具的耐久性。其结果,本发明的刀刃处理方法通过喷射颗粒的喷射这样的比较简单的处理,能够得到为了提高表面硬度而进行的渗碳和氮化等热处理或者涂覆以tialn为代表的陶瓷涂层而得到的表面强化的效果,能够作为替代所述热处理或陶瓷涂覆的处理而被采用。例如能够对残留有刀具痕迹等的状态下的处理区域进行本发明的刀刃处理,也能够对残留有某种程度的凹凸的处理区域进行本发明的刀刃处理,但是通过对预备研磨到ra为3.2μm以下的表面粗糙度的处理区域进行本发明的刀刃处理,能够将刀刃部分的表面加工为更好的表面状态。在利用弹性研磨材料的喷射进行这样的研磨时,利用使用喷丸加工装置的喷丸加工,能够比较简单地进行预备研磨以便加工到镜面或者接近镜面的状态,与进行手工作业的精磨或抛光研磨的情况相比,能够高效率地进行研磨。此外,也能够对形成有tialn等陶瓷涂层的所述处理区域进行本发明的表面处理方法,此时不仅能够得到形成凹坑带来的效果,还能够细化涂覆层的组织,提高涂覆层的耐久性。并且,在喷射所述喷射颗粒之后,进行去除形成凹坑16时产生的微小的突起17的事后研磨的构成中,使用进行了这样的表面处理的加工刀具10对被加工物20进行切削等,不仅能够将被加工物20的成品面24加工成不粗糙的更美观的表面,还能够进一步提高加工刀具10的耐久性,特别是通过喷射弹性研磨材料来进行这种事后研磨,能够比较容易且简单地进行研磨。附图说明图1是切削状态下的切削刀具和被加工物的说明图。图2是实施了本发明的表面处理的处理区域的说明图,(a)表示处理前的状态,(b)表示处理后的状态。图3是随着形成凹坑而在机械加工刀具表面产生的突起的说明图。图4是由本发明的表面处理方法处理的机械加工刀具的刀刃部的表面电子显微镜照片(sem图像)。图5是切削刀具的刀刃部的状态照片,(a)是未处理的切削刀具的刀刃部的状态照片,(b)和(d)是由本发明的表面处理方法处理的切削刀具的刀刃部的状态照片,(c)和(e)是由比较例的方法处理的切削刀具的刀刃部的状态照片。图6表示切削刀具的刀刃部的状态,(a)是由实施例处理的切削刀具的刀刃部的状态,(b)是由比较例处理的切削刀具的刀刃部的状态。图7是表示利用实施例和比较例的加工而排出的切屑的状态的照片。附图标记说明10切削刀具(机械加工刀具)11刀刃12前刀面13后刀面15处理区域(或者区域)16凹坑17突起20被加工物21切屑(切削碎片)22表面23剪切面24成品面25积屑瘤具体实施方式下面参照附图对本发明的实施方式进行说明。(处理对象)本发明的刀刃处理方法用于加工刀具10中的刀刃11部分的处理,所述加工刀具10是切削刀具或冲裁刀具等,具备用于切削或切断的成为剪切的起点的刀刃11,作为一个例子,冲头、钻头、立铣刀、滚刀、拉刀、铰刀等都包含在作为本发明的处理对象的加工刀具10中。这样的加工刀具10的材质也没有特别限定,除了skd(模具用工具钢)、sk(炭素工具钢)、skh(高速工具钢)等钢材之外,也可以是超硬合金、陶瓷(氧化铝、氧化锆、碳化硅、金属陶瓷)等。另外,这些加工刀具也可以在由所述的材质形成的加工刀具中的刀刃及其附近部分(后述的区域或处理区域15)的表面形成厚度为1~10μm的tialn、tic等陶瓷系的涂覆层。本发明的刀刃处理方法适用于这样的加工刀具10的刀刃部,如图2的(a)所示,成为切削或切断时的剪切的起点的刀刃(刃)11的部分以及相对于该刀刃11至少为1mm的范围、优选至少为5mm的范围的区域15,作为被喷射后述的喷射颗粒并被碰撞的处理区域15,进行后述的喷射颗粒的喷射,如图2的(b)所示,在该处理区域15形成凹坑16。在本实施方式中,将以刀刃11为中心的两侧的倾斜面都作为处理区域15,但是也可以仅在切削时受到更大的摩擦阻力的一侧的面(图1的例子中为前刀面12侧)设置处理区域15。另外,虽然加工刀具10的处理区域15也可以将刀刃附着有毛刺的状态或者保持形成有刀痕等加工痕迹的状态的部分作为处理对象,但是优选进行预备研磨,该预备研磨用于预先研磨到算术平均粗糙度(ra)为3.2μm以下的表面粗糙度。这样的预备研磨的方法没有特别限定,可以采用由手工作业进行的精研或由抛光进行的研磨,也可以通过使用了弹性研磨材料的喷丸加工进行这样的预备研磨。在此,弹性研磨材料是磨粒分散于橡胶或弹性体(elastomer)等弹性件或者磨粒承载于弹性件表面的研磨材料,能够通过倾斜地喷射这样的弹性研磨材料等方式,使弹性研磨材料在处理区域15上滑动,由此比较简单地将处理区域15的表面研磨成镜面或者接近镜面的状态。此外,分散或承载于弹性研磨材料的弹性件的磨粒可以根据作为处理对象的加工刀具的材质等来适当选择,作为一个例子,能够使用#1000~#10000的碳化硅、氧化铝或金钢石磨粒。(表面处理)通过喷射大致球状的喷射颗粒来碰撞所述处理区域,从而对距所述加工刀具10的刀刃11处于预定范围的处理区域15进行表面处理。以下作为一个例子表示了该表面处理所使用的喷射颗粒、喷射装置和喷射条件。喷射颗粒本发明的表面处理方法所使用的大致球状的喷射颗粒的“大致球状”不必是严格意义上的“球”,只要是通常作为“喷丸”所使用的无棱角形状的颗粒即可,即使是例如椭圆形或袋状等形状的颗粒,也包含在本发明所使用的“大致球状的喷射颗粒”中。喷射颗粒的材质可以使用金属系、陶瓷系的任意一种材质,作为一个例子,金属系的喷射颗粒的材质能够列举合金钢、铸铁、高速工具钢(高速钢、skh)、钨(w)、不锈钢(sus)等,另外,陶瓷系的喷射颗粒的材质能够列举氧化铝(al2o3)、氧化锆(zro2)、锆石(zrsio4)、硬质玻璃、玻璃、碳化硅(sic)等。优选使用的喷射颗粒的材质相对于作为处理对象的加工刀具的母材具有同等以上的硬度。使用的喷射颗粒的粒径可以是中位直径(d50)为1~20μm的范围,如果是铁系的喷射颗粒,则中位直径(d50)为1~20μm,优选5~20μm,如果是陶瓷系的喷射颗粒,则中位直径(d50)为1~20μm,优选4~16μm的范围,从这些粒径的喷射颗粒之中,根据作为处理对象的加工刀具的材质等,选择能够以后述的直径和深度形成凹坑的喷射颗粒来使用。喷射装置能够使用将研磨材料与压缩气体一起喷射的已知的喷丸加工装置,作为将所述喷射颗粒朝向处理区域的表面喷射的喷射装置。作为这样的喷丸加工装置,市场上销售有如下的喷丸加工装置:利用由压缩气体的喷射产生的负压来喷射研磨材料的吸引式喷丸加工装置;使从研磨材料容器落下的研磨材料随着压缩气体一起喷射的重力式喷丸加工装置;向已投入研磨材料的容器内导入压缩空气,使来自研磨材料容器的研磨材料流与另行提供的来自压缩气体供给源的压缩气体流汇合并喷射的直压式喷丸加工装置;以及使所述直压式的压缩气体流随着鼓风单元产生的气体流一起喷射的鼓风式喷丸加工装置等。上述任意一种喷丸加工装置都能够用于所述喷射颗粒的喷射。处理条件作为一个例子,能够在喷射压力为0.01mpa~0.7mpa、优选0.05~0.5mpa的范围使用所述喷丸加工装置进行喷射颗粒的喷射,考虑到与作为处理对象的加工刀具的材质等的关系,来形成当量直径为1~18μm、优选1~12μm,深度为0.02~1.0μm以下的凹坑16,并且使凹坑16的形成面积(投影面积)相对于处理区域表面的面积为30%以上。后处理如上所述,加工刀具10利用喷射颗粒的喷射在处理区域形成凹坑16,并且进行了表面附近的晶粒的细化等,所述加工刀具10可以直接用于切削加工等机械加工,但是也可以如下所述的那样实施事后研磨,该事后研磨在形成有凹坑16之后的处理区域15上喷射与作为预处理说明的弹性研磨材料同样的弹性研磨材料并使其滑动,来去除形成凹坑16时产生的微小的突起17。即,通过使所述的喷射颗粒碰撞处理区域15而形成凹坑16,由此如图3所示,在处理区域15中,由于喷射颗粒的碰撞而挤出的构成材料在凹坑16的周向边缘隆起而形成突起17,如此形成的突起17在接触被加工物20的表面或者切屑21时会增大接触阻力。因此,优选利用弹性研磨材料的喷射进行所述的事后研磨,由此保留了凹坑16,并且去除了形成凹坑16时产生的微小的突起17。此外,还可以在喷射了喷射颗粒之后的处理区域、或者根据情况进一步在进行了所述弹性研磨材料的喷射之后的处理区域,形成tialn或tic等陶瓷系涂覆层。优选将形成凹坑之后形成于处理区域上的涂覆层形成为1~10μm的膜厚。这样的涂覆层可以使用以溅射等为代表的物理蒸镀(pvd)或化学蒸镀(cvd)等已知的各种成膜技术。作用和效果等如以上说明的那样,在本发明的表面处理方法中,通过喷射预定直径的喷射颗粒,在加工刀具10的刀刃11和距该刀刃为一定范围内的处理区域15形成预定直径、预定深度的凹坑16,使该处理区域15凹凸不平。因此,如本发明所要解决的问题的段落中所说明的那样,按照在表面形成有凹凸的刀刃11部分容易形成积屑瘤25这样的本领域的技术常识,可以预测在形成凹坑16使刀刃11部分凹凸不平的加工刀具10中,会促进积屑瘤25的生成。但是,使用由本发明的处理方法对刀刃11部分进行处理后的刀具10来进行加工(切削加工)时,与按照所述技术常识预测的结果相反,确认到能够防止以生成积屑瘤25为代表的被加工物20相对于刀刃11部分的粘合。可以认为这样的被加工物20的粘合防止效果是由以下的原理得到的。在由本发明的方法对刀刃部分进行了表面处理的加工刀具10中,在刀刃(刃)11和距刀刃11为预定范围的区域(处理区域)15形成与喷射颗粒的粒径对应的比较小的凹坑16。由于形成该凹坑16,所以在进行了本发明的表面处理的加工刀具10中,润滑油容易供给到刀刃11,并且该凹坑16作为油槽发挥功能而保持润滑油,由此在距刀刃11处于一定范围内的前刀面12或后刀面13上形成油膜,能够大幅度地降低加工刀具10的顶端部与被加工物20的切屑21或成品面24接触时的摩擦阻力。在此,由于切屑21与刀具10的前刀面12之间产生的压力、大的摩擦阻力以及高的切削热,切屑21的一部分发生物理性、化学性变化,粘合到刀刃11附近的前刀面12,从而生成所述积屑瘤25。但是,如上所述,通过进行本发明的表面处理,在前刀面12形成保持油膜的凹坑16,由此能够大幅度地减小切屑21与前刀面12的接触阻力,所以应用本发明的处理方法时,积屑瘤25的生成条件全都不能存在。其结果,在实施了本发明的表面处理方法的加工刀具10中,难以生成积屑瘤25,所以能够消除伴随积屑瘤25的生成而产生的问题,例如刀刃11的钝化、由于切入量的增大而导致的加工精度降低、以及伴随切削阻力因摩擦或过切削而增大所导致的切削时的温度上升和切削刀具的早期磨损。另外,刀具的后刀面13也形成有保持润滑油的凹坑16时,被加工物20的成品面24与后刀面13的接触也变得平滑,进一步能够以一定的切削阻力利用连续的剪切进行切削。其结果,能够更进一步地适当防止在加工面产生凹凸等加工粗糙。在使用由本发明的表面处理方法进行了刀刃部分的表面处理的加工刀具的切削中,切屑不会成为“剪切型”、“撕裂型”、“龟裂型”,而是成为顺畅地连续产生的“流动型”,由此也可以确认到进行了切削阻力一定的连续的剪切。此外,在由本发明的表面处理方法进行了刀刃部的处理的加工刀具10中,由于所述的喷射颗粒的碰撞,在距处理区域15的表面约为3μm的范围发生晶粒细化。并且,利用该细化,能够抑制由于切削加工时产生的热量导致的膨胀和收缩而产生的热龟裂(热裂纹)的发生,可以实现高耐久性和长寿命化。特别是在处理对象为skd11制的加工刀具10时,能够将处理区域的表面附近的晶粒细化到纳米水平,能够实现更高的耐久性和长寿命化。另外,在由本发明的处理方法处理的加工刀具10中,不仅处理区域的表面附近的组织被细化,而且在测定其残留应力时,还能够确认到被赋予了高的压缩残留应力。这样的压缩残留应力的存在会带来耐久性的提高,利用所述的细化和压缩残留应力,本发明的刀刃处理实现了高硬度化、高强度化,能够替代渗碳和氮化等热处理或形成陶瓷系的硬质涂覆层的处理。对加工区域形成有陶瓷系涂覆层的加工刀具进行处理时,也同样能够得到这样的细化和压缩残留应力的赋予。此外,如上所述,被喷射颗粒碰撞的处理区域随着细化而表面硬度升高。在该处理区域上形成陶瓷系涂覆层时,通过使母材和涂覆层的硬度差变小,从而涂覆层的附着强度提高,另一方面,在形成有凹坑的母材上以大致均匀的膜厚形成的涂覆层的表面,形成有与母材层的表面形状对应的凹坑,也能够同样享受凹坑的形成带来的效果。(实施例)以下,使用由本发明的表面处理方法进行了刀刃部的表面处理的加工刀具进行加工,将其效果确认试验的结果表示为试验例。(试验例1:针对切削刀具的效果确认试验)试验的概要分别使用由本发明的表面处理方法进行了刀刃部的处理的切削刀具(实施例)、未处理品、以及按照偏离了本发明中规定的条件的处理条件处理了刀刃部的切削刀具(比较例),来进行切削加工,以刀刃的崩缺以及发生粘合为寿命,评价了各自的寿命。作为处理对象的切削刀具将下述表1所示的切削刀具作为对象。(表1)作为试验对象的切削刀具表面处理条件按照下述的表2~表13所示的条件对上述的各切削刀具的刀刃以及距刀刃为5mm的范围进行了表面处理。(表2)直钻头(skh51)(表3)球头立铣刀(skh51)(表4)车刀(超硬)(表5)车刀(氧化铝)(表6)车刀(金属陶瓷)(表7)丝锥(skh57)(表8)拉刀(skh51)(表9)平铣刀(skh51)(表10)侧铣刀(skh57)(表11)滚刀(skh57)(表12)铰刀(skh57)(表13)金属锯(超硬合金)此外,在所述表2~表13中,“喷射方式”表示使用的喷丸加工装置的喷射方式,分别表示使用下述的喷射方式的喷丸加工装置。sf:吸引喷射方式(株式会社不二制作所制造的“sfk-2”)fd:直压喷射方式(株式会社不二制作所制造的“fdq-2”)ld:重力喷射方式(株式会社不二制作所制造的“ldq-3”)通过“sirius(シリウス)加工”(不二制作所)进行弹性研磨材料的研磨。另外,下述的表14表示使用的喷射颗粒的每种材质的硬度。(表14)喷射颗粒的材质和硬度材质硬度(hv)合金钢870高速钢840氧化铝1800氧化锆1300锆石700玻璃550确认凹坑的形成状态利用电子显微镜照片进行确认利用电子显微镜照片观察按照以上说明的实施例1~22的处理条件喷射了喷射颗粒后的处理区域,其结果确认到无论哪种加工条件都形成了凹坑。作为一个例子,图4表示按照实施例3的处理条件进行了表面处理的高速工具钢(skh51)制的球头立铣刀的刀刃部的电子显微镜照片。在图4中,将比较清楚地显现的凹坑用虚线圆圈起来表示。根据图4可知,在作为刀刃(刃)11的棱线上以及以该刀刃11为中心的两倾斜面上都大致同样地形成直径较小且浅的凹坑。另外,图5表示由本发明的方法处理的切削刀具的刀刃部的状态照片。在该图5中,(a)为未处理的切削刀具的刀刃部的状态照片,(b)和(d)为由本发明的方法处理的切削刀具的刀刃部的状态照片,(c)和(e)为由比较例的方法处理的切削刀具的刀刃部的状态照片,(b)~(d)都是吸引喷射方式(sf式),(b)是以喷射压力0.5mpa来喷射合金钢制的喷射颗粒(中位直径为18μm)3秒,(c)是以喷射压力0.5mpa来喷射高速钢制的喷射颗粒(中位直径为50μm)3秒,(d)是以喷射压力为0.1mpa来喷射合金钢制的喷射颗粒(中位直径为18μm)3秒,(e)是以喷射压力为0.1mpa来喷射高速钢制的喷射颗粒(中位直径为50μm)3秒。在本发明的表面处理方法中,由于是以0.01mpa~0.7mpa的喷射压力喷射中位直径为1~20μm这样的微小的喷射颗粒来形成凹坑,所以如图5的(b)、(d)所示,不会使加工刀具的刀刃损伤、卷曲,能够在保持刀刃的锋利性的状态下形成凹坑。对此,在喷射超过所述粒径范围的中位直径为50μm的喷射颗粒进行加工的加工刀具中,如图5的(c)、(e)所示,确认到会损伤刀刃而使其钝化。如此,在由本发明的表面处理方法进行的处理中,能够不使刀刃钝化而是在保持锋利性的状态下形成凹坑,所以不会产生成品面的粗糙和随着切入量的变化而导致的加工精度的降低。凹坑直径、深度、投影面积的测定下述的表15(实施例)和表16(比较例)分别表示按照以上说明的实施例1~22的处理条件和比较例1~12的处理条件进行了表面处理之后的切削刀具的刀刃部上形成的凹坑的直径、深度和投影面积的测定结果。此外,凹坑的直径(当量直径)和深度使用形状解析激光显微镜(基恩士公司制“vk-x250”)进行测定。在测定中,能够直接测定切削刀具的刀刃部分的表面时就直接测定,不能直接测定时,向乙酰纤维素薄膜滴加乙酸甲酯,融合到切削刀具的刀刃部分的表面之后,在干燥后剥离,根据被转印复制到乙酰纤维素薄膜上的凹坑进行测定。使用“多文件解析应用程序(基恩士公司制vk-h1xm)”解析由形状解析激光显微镜拍摄的表面图像的数据(但是,在使用乙酰纤维素薄膜的测定中,是对拍摄的图像进行了转印处理的图像数据)来进行测定。在此,“多文件解析应用程序”是能够使用由激光显微镜测定的数据,进行表面粗糙度、线粗糙度、高度、宽度等的测量,圆当量直径、深度等的解析和基准面设定,以及高度转印等图像处理的应用程序。测定首先使用“图像处理”功能,进行基准面设定(但是,在表面形状是曲面时,使用面形状修正将曲面修正为平面后,进行基准面设定),接着,根据应用程序的“体积和面积测量”功能,将测量模式设定为凹部,测量相对于设定的“基准面”的凹部,根据凹部的测量结果,将“平均深度”、“圆当量直径”的结果的平均值作为凹坑的深度和当量直径。此外,所述基准面根据高度数据使用最小二乘法算出。另外,所述“圆当量直径”或者“当量直径”是测定凹部(凹坑)的投影面积换算为圆形的投影面积时的所述圆形的直径。此外,所述“基准面”是指高度数据中的作为测量的零点(基准)的平面,主要用于垂直方向上的测量,例如深度和高度等。(表15)凹坑的直径、深度和投影面积(实施例)(表16)凹坑的直径、深度和投影面积(比较例)切削加工条件使用进行了所述各表面处理的切削刀具和未处理的切削刀具,对预硬钢(hrc30)进行切削加工。按照下述表17所示的切削条件进行加工。(表17)切削条件评价方法和试验结果分别使用未处理的切削刀具、进行了本发明的表面处理的切削刀具(实施例)以及按照脱离了本发明的表面处理条件的条件进行了表面处理的切削刀具(比较例),按照上述切削条件分别进行切削,以刀刃的粘合和崩缺的发生时点为寿命,来评价耐久性,其结果表示于表18。此外,表18中的“寿命”表示将未处理的切削刀具的寿命设为“1”时,实施例及比较例的切削刀具的寿命相对于该寿命为多少倍。(表18)切削加工试验(耐久试验)结果切削试验结果的考察确认到切削试验的结果为,进行了实施例1~22的表面处理的切削刀具与未处理的切削刀具相比寿命都增长。可以认为这样的长寿命化的原因在于,通过进行本发明的表面处理,提高了切削刀具的刀刃部分的表面硬度,而且,通过在前刀面上形成凹坑而形成油槽,从而提高了前刀面的润滑性,其结果,能够抑制伴随与切屑的摩擦接触而产生的发热,能够顺畅地排出切屑,并且能够防止切屑粘合于前刀面,其结果提高了耐久性。如此,如表15所示,在按照能够提高寿命的实施例1~22的处理条件进行了表面处理的切削刀具的刀刃部形成有比较小的凹坑,凹坑的当量直径处于1~18μm的范围内,深度为0.02~1.0μm以下,但是形成为投影面积在30%以上,可知处于该数值范围内的凹坑的形成对于防止切削刀具的粘合等而提高耐久性是有效的。此外,确认到在针对超硬车刀的实施例中,在利用喷射颗粒的喷射而形成凹坑之前,使用弹性研磨材料进行了预备研磨的实施例7(寿命2.1)以及实施例15(寿命1.8)中,与未进行这样的预备研磨的实施例6(寿命1.5)、实施例14(寿命1.4)相比,能够得到更进一步的长寿命化。由此可以认为,在利用喷射颗粒的喷射而形成凹坑之前,去除了残留于切削刀具表面的刀痕等,然后形成凹坑,并且形成凹凸的高度一致的凹坑,这有助于更进一步提高润滑性。另外,确认到在对直钻头进行了本发明的表面处理的实施例中,即使是利用喷射颗粒的喷射而形成凹坑之后喷射弹性研磨材料进行事后研磨的实施例2(寿命3.0)中,相对于未进行这样的事后研磨的实施例1(寿命2.6),也会长寿命化。由此可以认为,通过如参照图3所说明的那样利用事后研磨去除了形成凹坑时在凹坑的周向边缘部产生的微小的突起,从而也有助于大幅度降低与被加工物或切屑的接触阻力。在与未处理品的比较中,相对于确认到都实现了长寿命化的实施例1~22的表面处理条件,在进行了比较例1~12的表面处理的切削刀具中,对车刀(金属陶瓷)的处理例子亦即比较例5(寿命1.1)中,虽然对未处理品得到一点点的寿命提高,但是在其他比较例中,其结果变为一律比未处理品短寿命化。在此,可以认为即使在按照比较例的处理条件进行了表面处理的切削刀具中,由于使喷射颗粒碰撞刀刃部分,所以利用喷射颗粒的碰撞带来的变形,在刀刃部分形成凹坑,并且利用该变形带来的表面硬化,使表面附近的硬度上升。但是,在比较例的处理方法中,用于表面处理的喷射粉体的粒径大于实施例中的粒径,其结果,形成的凹坑大,超过了实施例中的当量直径为1~18μm、深度为0.02~1.0μm以下的范围(参照表16),所以变为与刀刃产生崩缺(缺口)相同的状态,可以认为凹坑不仅不能作为油槽发挥功能,还会使刀刃钝化而降低切削性,其结果,切削阻力增大以及随之而来的发热等也增大,从而与未处理品相比变为短寿命。因此,确认了在本发明的表面处理方法中,使用当量直径为1~18μm的颗粒作为喷射颗粒,从而在刀刃部分形成当量直径为1~18μm、深度为0.02~1.0μm以下的凹坑的有效性。(试验例2:针对冲裁刀具的效果确认试验)试验概要分别使用由本发明的表面处理方法对刀刃部进行了处理的冲裁刀具(实施例)、未处理品以及按照偏离了本发明的处理条件的处理条件进行了表面处理的冲裁刀具(比较例),进行冲压加工,并观察加工后的刀刃部的状态。处理对象和表面处理条件按照下述表19所示的条件对skd11制的冲裁加工用冲头(长度为3cm、直径为0.5cm)的刀刃部分(刀刃以及距刀刃为2mm的范围)进行了表面处理。(表19)针对冲裁加工用冲头的表面处理条件并且,在所述表19中,“喷射方式”中的“sf”表示吸引喷射方式,本试验例中,使用株式会社不二制作所制造的“sfk-2”作为喷丸加工装置。冲裁加工条件和观察方法分别使用由实施例23、比较例13各自的方法进行了表面处理的冲头和未处理的冲头,对ss钢材制的被加工物(厚度为2mm的板材)连续进行9000次冲压加工,通过目视和显微镜来观察该冲压加工后的各冲头的表面状态,从而观察消耗情况。观察结果所述冲压机加工后的各冲头的表面状态如下述的表20所示。(表20)冲压加工后的冲头的表面状态处理条件表面状态实施例23几乎未发现损伤。比较例13确认到在长边方向上存在大量的条状伤痕。未处理1800次不能使用。考察可以认为按照实施例23的处理条件进行了表面处理的冲头在刀刃部分形成当量直径约为13.2μm、深度约为0.71μm的凹坑,这样形成的凹坑作为油槽发挥功能,其结果,提高了冲裁加工时的滑动性,抑制了刀具的磨损。确认到按照比较例13的处理条件处理的冲头的刀刃部分也形成凹坑,但是形成的凹坑的当量直径为50.2μm、深度为2.81μm,与按照实施例23的条件进行了表面处理的凹坑相比更大。其结果,在按照比较例13的处理条件形成了凹坑的例子中,刀刃的形状受损,冲裁加工时的阻力升高,与按照实施例23的条件进行了表面处理的冲头相比,可以认为已早期磨损。此外,在进行了本发明的表面处理(实施例23)的例子中,确认到与未处理的表面硬度约为750hv相比,表面处理后的硬度提高到约为950hv,硬度提高约21%。另外,相对于未加工时的残留应力约为200mpa且为“拉伸”残留应力的情况,进行了本发明的表面处理(实施例23)后的残留应力变为-1200mpa,也能够确认被赋予了高的“压缩”残留应力,可以认为利用这样的高的压缩残留应力也能够提高耐久性。此外,利用作为扫描电子显微镜(sem)进行的晶体分析方法之一的ebsd(electronbackscatterdiffractionpatterns:电子背散射衍射图样),进行实施了本发明的表面处理(实施例23)之后的冲头表面的晶体分析,其结果,能够确认到表面的晶粒细化,可以认为这样的晶粒细化也有助于大幅度提高耐久性。(试验例3:针对铝合金的端铣试验)试验的概要使用由本发明的表面处理方法对刀刃部进行了处理的切削刀具,将容易形成积屑瘤的铝合金(a5052)作为被加工物进行切削,确认被加工物(切屑)相对于刀刃的粘合以及磨损状态。处理对象和表面处理条件按照下述的表21所示的条件(实施例24)对4枚刃超硬立铣刀(直径为10mm)的刀刃部分(刀刃以及距刀刃为5mm的范围),进行了表面处理。(表21)针对立铣刀的表面处理条件并且,在所述表21中,“喷射方式”中的“sf”表示吸引喷射方式,本试验例中,使用株式会社不二制作所制造的“sfk-2”作为喷丸加工装置。切削条件和观察方法使用按照表21所示的实施例24的条件进行了表面处理的立铣刀和未处理的立铣刀,将铝合金(a5052)制的板材作为被加工物(被切削材料)进行了切削。以切入量为0.2mm、切削速度为100m/min的方式进行切削,测定此时的切削阻力,并且观察了切屑相对于刀刃的粘合状态。由三分量切削测力计(奇石乐(kistler)公司制造)进行切削阻力的测定,使用显微镜(基恩士公司制“vhx600”)和电子显微镜(日立高新技术公司制造的“s6400n”)进行了刀刃观察。此外,在此所谓的“切削阻力”是指持续切削所需要的力,是由主分力、进给分力和推力构成的力,在此,测定了其中的主分力和进给分力。测定、观察结果利用所述方法测定刨削时的切削阻力的测定结果和刀刃的观察结果如下述表22所示。此外,切削阻力的测定结果是与未处理的立铣刀的切削阻力设为1时的比值。(表22)铝刨削试验结果切削阻力磨损粘合实施例240.8无无未处理1有有考察在由本发明的方法进行了表面处理的立铣刀(实施例24)中,通过在刀刃和距刀刃的预定范围形成凹坑,从而润滑油容易遍布于刀刃,其结果,确认到将作为材质较软的材料而容易因粘合生成积屑瘤的铝合金材料作为切削对象时,也能够防止粘合(积屑瘤)的发生。另外,在由本发明的方法进行了表面处理的立铣刀中,通过形成凹坑,能够在刀刃以及刀刃附近的前刀面和后刀面上形成油膜,由此减少了与被加工物表面的接触阻力及与切屑的接触阻力,并且刀刃的硬度升高,而且不会产生由于积屑瘤的生成而导致的刀刃钝化、切削阻力增加、切入量增加等,所以能够得到降低切削阻力的效果,相对于未处理品为0.8倍的切削阻力。(实施例25~27和比较例14)难切削材料的切削加工下面,公开本发明应用于将难切削材料作为被加工物的切削刀具时的实施例。利用本发明的处理在刀刃及其附近形成凹坑的加工刀具,对于减轻加工钛、不锈钢、耐热合金之类的被称为难切削材料的金属时产生的难切削材料的粘合,可以发挥优异的效果。在此,难切削材料大致如下定义:(1)材质自身难以切削的材料(不锈钢、钛合金、镍合金、铁-镍合金、耐热合金(铬镍铁合金、哈氏合金)等具有引起难切削性的材料特性的材料)(2)引起难切削性的材料特性如下:·高硬度·硬脆·容易产生表面硬化·与刀具材料的亲和性大·高温强度高·热传导率小·材料强度高·含有磨蚀性磨损物质·延展性大·被切削性不明,难以最优化。(3)被切削性不明的材料(主要是没有切削数据的新材料等)(4)可燃易燃的材料(镁等)(表23)切削条件切削刀具嵌装刀片(超硬合金+tin涂层)被切削材料纯钛切削速度60m/min进给量0.07mm润滑油无(表24)加工条件(表25)凹坑直径和深度评价方法对被切削材料进行一次加工后,评价刀刃有无粘合考察(表26)评价结果实施例25~27比较例14粘合微小大(表27)切削加工面的表面粗糙度实施例25比较例14表面粗糙度ra(μm)1.341.51在实施例25~27中几乎看不到加工后的粘合。比较例14能够确认到明显的粘合(参照图6)。另外,如果观察切削中的切屑的排出状态,则观察到在比较例中切屑缠绕。但是,如果观察实施例25~27,则观察到切屑不会缠绕而是顺畅地排出(参照图7)。可以认为利用本发明的处理形成的凹坑减轻了切削阻力,并且能够减轻切屑排出时的切屑与刀具的接触阻力,由此改善了粘合。当前第1页12