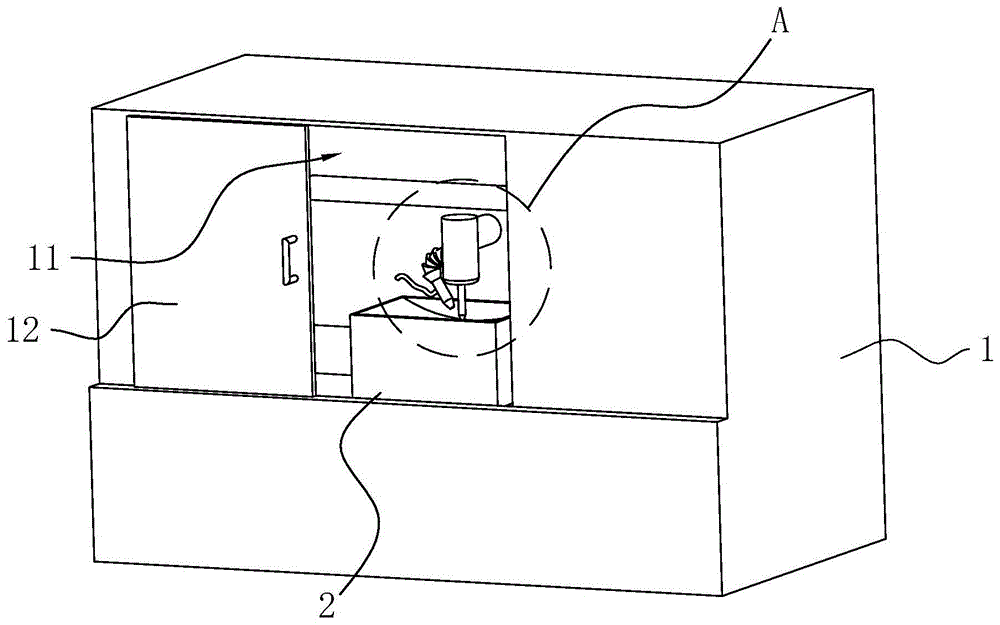
本发明涉及模具加工设备,特别涉及提高注射模具加工精度的加工设备及其加工工艺。
背景技术:
:注射模具是一种高分子材料成型加工用的设备。注射模具使用时,将高分子材料受热熔融后浇筑或注射入注射模具的模具型腔,高分子材料在模具型腔内流动并填充模具型腔,然后等待高分子材料冷却硬化定型后获得高分子材料成型件。由此模具的模具型腔表面的加工精度有严格的要求,加工精度越高,所得高分子材料成型件表面越平滑,毛刺越少,注塑成型效果越好。现有注射模具大多有上模、下模等多个金属的模具模块组成,当下注射模具的模具型腔表面多采用多轴自动机床,利用高速转动的刀具进行高精密的金属加工。但现有多轴自动机床在高转速的高精密金属加工时,加工刀具与模具模块的加工面会产生大量的热量,造成局部高温。作为注射模具材质的金属,在高温下受到加工刀具抵压会发生塑性变形,而该塑性变形在金属自由冷却过程中可缓慢恢复,不同加工面和加工加度,导致的塑性变形量不同,若任由其自由缓慢恢复,会使得型腔面加工尺寸存在不可控不可预期的偏差,降低加工精度。由此现有加工机床多会对加工刀具以及注射模具加工处进行强制冷却,减少塑性变形的恢复,进而提高模具模块的加工精度,其中冷却效率越高,对模具加工精度的提升越大。例如授权公告号为cn209077872u的中国专利“具有随动冷却结构的模具加工装置”,公开了一种冷却结构,其在刀具周围朝向刀具的喷嘴,喷嘴在加工装置工作时向刀具喷射冷却液,对刀具进行冷却。但对于多轴自动加工机床加工模具而言,高转速的切削加工,冷却液喷射初始动能小,渗透难;另一方面,高转速的切削产生的高温足以将冷却液汽化,汽化后的冷却液形成滞留层,而又阻碍膨胀对后续冷却液的渗透,由此冷却液冷却的方式难以满足模具加工对冷却的需求。对此现有技术又改进采用的喷雾冷却的方式,例如授权公告号为cn106863002b的中国专利“一种低温水雾油雾切削冷却润滑供应系统”,其公开了一种喷雾冷却的方式,其将冷却油和压缩空气混合流动通过文丘里管破碎呈大量的小液珠分散在雾化室内的空气中以形成油雾,沿管道输送至涡流雾化喷嘴中与压缩空气进行进一步混合后喷射而出,形成低温油雾,甚至在涡流雾化喷嘴中输送水,混合形成低温的油水混合喷雾,以此进行冷却。此处将低温油雾和低温的油水混合喷雾统称为冷却液喷雾,冷却液喷雾属于两相流体,具有较高的初始速度,动能较大,可冲走滞留层,渗透能力较强,此外冷却液喷雾中液体以微小尺寸的液珠存在,遇到温度较高的金属极易汽化,可从多个方面向刀具前刀面渗透,冷却效率显著优于冷却液喷射冷却。但其不足之处在于油雾在雾化室内形成后沿管道向涡流雾化喷嘴输送流动,油雾中液珠易相互碰撞凝聚成大液珠粘附于管道壁面,或者直接撞击在管道壁面上并滞留在管道壁面。这要求雾化室与涡流雾化喷嘴之间输送距离尽可能的小且输送路线尽可能为直线,但对于加工过程中需要灵活转动且不断调节加工刀具位置、角度的多轴自动机床而言,难以实现,导致实际组合使用时冷却液喷雾中液体含量少,冷却效果没有达到预期目的,对模具加工精度提高有限,且常常在涡流雾化喷嘴处滴漏液体,故期望一种更为高效更为适合多轴自动机床的冷却方式,获得一种更好的为注塑模具加工提高加工精度的加工设备。技术实现要素:针对现有技术存在的不足,本发明的第一个目的在于提供提高注射模具加工精度的加工设备,高效冷却减少塑性变形恢复,进而提高注塑模具加工生产过程中的加工精度,提高高分子材料成型件的成型效果。本发明的上述技术目的是通过以下技术方案得以实现的:提高注射模具加工精度的加工设备,包括冷却系统、刀具安装座和安装在刀具安装座上的加工刀具,所述冷却系统包括汽化室、冷气源管和冷却喷头,所述冷却喷头与刀具安装座相对固定且朝向加工刀具,所述汽化室连接有输入冷却液的冷却液供管和与冷却喷头连通的热气源管,所述汽化室内还安装有汽化冷却液的汽化组件,所述冷气源管一端连接高于大气压的低温气体,所述冷气源管的另一端和热气源管共同接入冷却喷头内。通过采用上述技术方案,将冷却液在汽化室内进行汽化,形成冷却液的蒸汽并流向冷却喷头,再在冷却喷头内与低温气体混合,冷却液蒸汽受低温气体低冷刺激下冷凝产生液珠,继而再与低温气体混合后形成喷雾,喷射而出对加工刀具以及模具模块进行冷却。在此过程中冷却液转化为蒸汽进行输送,避免雾化冷却液时液珠自聚凝结或粘附在管道内壁上,以此增大最终朝向加工刀具以及模具模块喷射而出的冷却液中冷却液含量,提高冷却量和冷却效率,减少塑性变形恢复,进而提高注塑模具加工生产过程中的加工精度,提高高分子材料成型件的成型效果。同时较雾化后的冷却液喷雾而言,冷却液蒸汽输送更快且更为便利,通过调节冷气源管中的气流流速即可控制冷却喷头喷射出的喷雾中冷却液含量。本发明进一步设置为所述汽化组件包括加热件。通过采用上述技术方案,采用加热件加热冷却液的方式汽化冷却液,可产生过热的冷却液蒸汽,进而保证冷却液蒸汽可输送更远距离,增加冷却喷头所喷喷雾中冷却液含量上限。本发明进一步设置为:所述冷却液供管连接汽化室的一端设置有雾化喷嘴。通过采用上述技术方案,冷却液通过雾化喷嘴雾化喷入汽化室内,继而以液雾的形式与加热件接触,液雾中液珠易汽化,无需使液体汇集状下的冷却液整片沸腾即可得到充足的冷却液蒸汽,且获得的冷却液蒸汽因液珠汽化快,可使蒸汽温度下限接近饱和蒸汽的温度,蒸汽温度低,可调节适应于对蒸汽温度要求低的短距离蒸汽运输,降低能耗。本发明进一步设置为:所述汽化室还连接有汽化推流管,所述汽化推流管内接通有压缩气源。通过采用上述技术方案,汽化推流管向汽化室内输入压缩气源的压缩气体,压缩气体与汽化室内的冷却液蒸汽混合后,主动流入热源气管内,继而加快冷却液蒸汽的输送速度,减少冷却液蒸汽在输送过程中自凝。本发明进一步设置为:所述汽化室还连接有汽化推流管,所述汽化推流管内接通有压缩气源,所述汽化组件包括加热件,所述冷却液供管连接汽化室的一端设置有雾化喷嘴,所述雾化喷嘴倾斜向上设置,所述汽化推流管和雾化喷嘴均位于汽化室的一侧,所述热气源管位于汽化室相对的另一侧,所述加热件位于热气源管和汽化推流管之间。通过采用上述技术方案,雾化喷嘴倾斜向上朝向加热件所在一侧喷射,同时汽化推流管内压缩气体推动雾化喷嘴喷出的喷雾向加热件移动。粒径较大的液珠在雾化喷头喷出时朝向加热件方向运动的初始速度较小,且由于质量加大,粒径较大的液珠受汽化推流动管推动加速速度较小,故较粒径较小的液珠而言,粒径较大的液珠在距加热件更远处下落,继而对雾化喷嘴中喷射出的液珠进行筛选,使得加热件接触加热的液珠更为细小易蒸发,且加热件的表面温度分布更为均匀,减少局部粘附冷却液过多导致的区域降温,稳定加热件加热汽化效率,维持热气源管内冷却液气相含量稳定,保证冷却效果稳定,提高模具加工精度以及高分子材料成型件成型效果。本发明进一步设置为:所述低温气体为氮气。通过采用上述技术方案,以氮气作为低温气体,在喷雾冷却冲走加工刀具与模具模块接触处的空气后隔绝空气放回,避免高温下氧气对模具模块氧化形成氧化层,减少模具模块上因加工产生的氧化层黏连高分子材料而导致高分子材料成型件脱模时表面变形或破损的可能。本发明进一步设置为:所述冷却液选用水。通过采用上述技术方案,与一般现有冷却喷雾不同,本申请采用以水作为冷却液,因以氮气作为低温气体对模具模块和加工刀具隔绝氧气进行保护的情况下,选用水作为冷却液,避免了原有选用水作为冷却液时高温下水蒸气催化氧气氧化金属的问题,同时对本申请而言,水具有更低的沸点,汽化后蒸汽温度下限低,有利于减少冷却液蒸汽在热气源管中输送时自冷凝。本发明进一步设置为:所述冷却喷头包括内喷管和套在内喷管外的外喷管,所述内喷管和外喷管之间形成有夹腔,所述内喷管与热气源管连通,所述夹腔与冷气源管连通。通过采用上述技术方案,冷却液蒸汽与低温气体并非在冷却喷头内直接混合,而是内喷管与夹腔连通的一端混合并同时喷出。喷出时两股气流呈层流流动,低温气体包裹冷却液蒸汽,约束冷却液蒸汽在喷出后扩散,使得冷却液蒸汽冷凝的液珠喷射轨迹收束集中,同时冷却液蒸汽自身由于与低温气体接触冷却收缩,形成负压,反向作用低温气体向中心流动收束,由此对冷却喷头所喷出的喷雾进行收束约束,集中冷却喷雾喷射点,提高冷却效率,提高模具加工精度以及高分子材料成型件成型效果。本发明进一步设置为:所述内喷管与热气源管之间安装有热气流量调节阀,所述夹腔和冷气源管之间安装有冷气流量调节阀。通过采用上述技术方案,多轴加工机床在加工模具模块,根据工艺需求,不仅仅是小区域的高精度加工,还包括大区域的切削挖槽,如模具加工初期加工形成型腔面的凹凸趋势,此时刀具吃进深度大,切削面大,故对冷却系统而言需要更大的冷却面积,此时可调节热气流量调节阀和冷气流量调节阀,使得冷却液蒸汽流速接近或大于低温气体流速,进而使冷却喷头喷出两者时流动相呈湍流,继而气流扰动,不再收束,以此提供更大的冷却面积。针对现有技术存在的不足,本发明的第二个目的在于提供一种提高注射模具加工精度的加工工艺,提高注射模具加工精度,以此提升高分子材料成型件的成型效果。本发明的上述技术目的是通过以下技术方案得以实现的:一种提高注射模具加工精度的加工工艺,上述的提高注射模具加工精度的加工设备对模具模块加工,包括以下使用步骤:启动冷却系统,在对模具模块加工时,使用冷却喷头朝向模具模块加工处进行喷雾冷却。通过采用上述技术方案,在模具模块加工时,对模具模块进行高效的强制冷却,减少塑性变形恢复,提高注射模具加工精度,提升高分子材料成型件的成型效果,减少高分子材料成型件表面毛刺和不平整。综上所述,本发明具有以下有益效果:1.将冷却液汽化形成冷却液蒸汽,并在冷却喷头中与低温气体混合形成冷却喷雾,再向外喷射对模具模块进行冷却,避免雾化冷却液时液珠粘附在管道内壁上的问题,以此增大最终朝向刀具以及模具模块喷射喷雾中冷却液含量,提高冷却量和冷却效率,减少塑性变形恢复,进而提高注塑模具加工生产过程中的加工精度,提高高分子材料成型件的成型效果;2.在汽化室内雾化冷却液,再对冷却液进行筛分,以小液珠接触加热件汽化获取充足的冷却液蒸汽,提高汽化效率;3.以压缩气体推送输送冷却液蒸汽,加快冷却液蒸汽的输送速度,减少冷却液蒸汽在输送过程中自凝;4.低温气体为氮气,冷却液选用水,氮气在喷雾冷却时对模具模块保护,减少氧化形成氧化层,减少模具模块上因加工产生的氧化层黏连高分子材料而导致高分子材料成型件脱模时表面变形或破损的可能。附图说明图1为多轴自动机床的结构示意图;图2为图1在a处体现安装座和加工刀具结构的局部放大图;图3为冷却系统的示意图;图4为汽化室的示意图;图5为冷却喷头的层流喷射时的示意图。附图标记:1、机床外体;11、加工室;12、滑动门;13、加工机构;131、加工刀具;132、安装座;1321、关节调节管;2、模具模块;3、冷却系统;31、冷却液箱;32、冷却喷头;321、外喷管;3211、接气管口;322、内喷管;323、夹腔;33、汽化室;331、冷却液供管;3311、雾化喷嘴;3312、冷却液泵;3313、冷却液截止阀;332、热气源管;3321、热气流量调节阀;333、汽化组件;3331、加热件;3332、固定件;34、冷却气源;341、压缩氮气罐;342、制冷机;343、冷气源管;3431、冷气截止阀;3432、冷气流量调节阀;35、汽化推流管;351、推流气截止阀;352、气流膨胀节;353、推流气流量调节阀。具体实施方式以下结合附图对本发明作进一步详细说明。实施例1,如附图1所示,提高注射模具加工精度的加工设备,其包括有机床外体1。机床外体1的形状可根据实际情况而定,一般机床外体1形状为长方体状,安装在地面或工作台上。机床外体1内设置有加工室11,加工室11在机床外体1的一侧面敞口设置,且敞口处滑动连接有启闭敞口的滑动门12。滑动门12与机床外体1的连接结构为现有技术,且非本发明的创新点,故在此不做进一步阐述。模具模块2放入加工内后,滑动滑动门12关闭加工室11,由加工室11内的加工机构13对模具模块2进行加工,模具模块2根据模具加工生产的工序而定。如附图2所示,加工机构13根据加工机床的加工坐标系而定,可为三轴联动、四轴联动或五轴联动,此处为五轴联动,包括有加工刀具131以及安装加工刀具131的安装座132,安装座132形状可根据实际情况需求而定,此处为柱状,加工刀具131安装与安装座132下端面上且朝向模具模块2上表面。如附图3所示,此外本申请的加工设备还包括有冷却系统3,冷却系统3包括冷却液箱31和冷却喷头32。(附图3中结构大小不代表实际机构/组件/结构大小,仅示意其物料流动路径以及冷却系统3内各组成部分之间的关系)冷却液箱31内部存放有冷却液,冷却液的选用可根据需求选择,此处为水。冷却液箱31与冷却喷头32之间连通,两者之间设置有汽化室33。如附图4所示,汽化室33的形状可根据实际情况而定,其一般呈长条形,内部中空。并且汽化室33长度方向的两端分别设置有连接冷却液箱31的冷却液供管331和连接冷却喷头32的热气源管332。热气源管332上安装有热气流量调节阀3321。如附图3和附图4所示,冷却液供管331的一端连接冷却液箱31的底部。冷却液供管331另一端插入汽化室33内,且冷却液供管331插入汽化室33内的一端朝向汽化室33的另一侧倾斜向上设置,并在冷却液供管331插入汽化室33内的一端端部上安装有雾化喷嘴3311。同时冷却液供管331上还安装接入有冷却液泵3312和冷却液截止阀3313,冷却截止阀位于冷却液泵3312的下游,打开冷却液截止阀3313,并启动冷却液泵3312,可使冷却液箱31中冷却液沿冷却液供管331喷入汽化室33内。如附图4所示,汽化室33内部还安装有汽化组件333,汽化组件333包括加热件3331和固定件3332,加热件3331采用电加热,为电热偶包覆绝缘导热材料制得,绝缘导电材料优选为陶瓷镀层或陶瓷涂层。加热件3331的形状可根据实际需求而定,此处优选为网状,且加热件3331自汽化室33连接冷却液供管331一侧向汽化室33连接热气源管332一侧倾斜向上设置。固定件3332数量为二,其分别固定于加热件3331的上下沿,且两个固定件3332分别与汽化室33的上下面固定,固定方式根据实际需求而定,可采用焊接、粘结的死固定也可采用螺栓连接、卡接、抵紧固定等可拆卸固定。如附图2所示,冷却喷头32安装于安装座132上,冷却喷头32的数量可根据实际情况而定,此处冷却喷头32数量为一。冷却喷头32与安装座132之间连接有关节调节管1321,关节调节管1321为机床生产加工中输送介质用的常用管件,其可进行弯曲调节角度且又可在调节后稳固自己形态,例如授权公告号cn209077872u中所公开的“关节调节管1321”。如附图5所示,冷却喷头32包括外喷管321和插入外喷管321内的内喷管322,外喷管321和内喷管322均呈中空柱状。其中外喷管321一端封堵,另一端敞口与外界连通。内喷管322一端贯穿外喷管321封堵的一端且与热气源管332连通,内喷管322贯穿外喷管321处密封且固定连接,其密封固定连接方式可根据实际情况而定,可为焊接或内喷管322与外喷管321之间一体成型等。而内喷管322的另一端容置在外喷管321内。同时内喷管322和外喷管321内外套接的设置,在内喷管322外侧与外喷管321内侧面之间形成夹腔323,夹腔323在外喷管321敞口的一端内部与内喷管322内部连通。外喷管321远离敞口一端的外侧面上还设有与夹腔323连通的接气管口3211。另一方面,冷却系统3还包括有冷却气源34,冷却气源34为低温的压缩气体,压缩气体的成分可根据实际情况而定,为空气、氮气、氩气等,此处优选为氮气。冷却气源34的低温来源可由压缩气体自身低温而来,或额外的制冷组件,此处冷却气源34包括压缩氮气罐341和制冷机342,压缩氮气罐341与制冷机342相邻,压缩氮气罐341内气体流出后流经制冷机342,以此获得低温的氮气,低温温度可调节控制制冷机342功率和氮气流速得到,一般为2~6℃,此处为5℃。制冷机342还连接有冷气源管343,冷气源管343为外包有保温层的软管,冷气源管343的另一端与进气管口相连接。同时冷气源管343沿低温的氮气流动方向依次安装有冷气截止阀3431和冷气流量调节阀3432。再者,氮气罐还连接有汽化推流管35,汽化推流管35的另一端接通于汽化室33,且汽化推流管35接通位置位于冷却液供管331接通汽化室33位置的同一侧,且汽化推流管35接通位置位于冷却液供管331接通汽化室33位置的上方。同时汽化推流管35沿其内氮气流动方向依次安装有推流气截止阀351、气流膨胀节352和推流气流量调节阀353。本发明的作用流程:当本申请加工设备准备进行加工模具模块2时,需要提供对模具模块2的冷却,启动冷却液泵3312、打开推流气截止阀351以及给予加热件3331接电,冷却液箱31中的冷却液沿冷却液供管331喷入汽化室33形成冷却液喷雾,压缩氮气罐341内氮气沿推进气流管流动流入汽化室33形成推进气流。汽化室33内的冷却液喷雾在推动气流的推动下向加热件3331移动,喷雾中粒径较大的液珠在雾化喷头喷出时朝向加热件3331方向运动的初始速度较小,同时粒径较大的液珠由于质量加大受汽化推流动管推动加速速度较小,故较粒径较小的液珠而言,粒径较大的液珠在距加热件3331更远处下落,继而对雾化喷嘴3311中喷射出的液珠进行筛选,使得加热件3331接触加热的液珠更为细小,更易汽化,提高汽化效率。汽化室33内的冷却液喷雾与加热件3331接触后汽化形成冷却液蒸汽,冷却液蒸汽与推动气流混合后形成热气流,热气流沿热气源管332向内喷管322输送。另一方面在打开推流气截止阀351的同时打开制冷机342和冷气截止阀3431,压缩氮气罐341内氮气流经制冷机342形成低温气流,低温气流沿冷气源管343进入夹腔323。最终低温气流在外喷管321敞口一侧与热气流接触形成混合气流并同时喷出,混合气流中冷却液蒸汽受低温气体低冷刺激下冷凝产生液珠,继而在与低温气体混合后形成喷雾。调节热气流量调节阀332和冷气流量调节阀3432,调节热气流和低温气流的流速,调节两流体之间的喷出时的流动呈相为层流或湍流,对加工刀具131和模具模块2进行冷却。层流时,约束冷却液蒸汽在喷出后扩散,使得冷却液蒸汽冷凝的液珠喷射轨迹收束集中,同时冷却液蒸汽自身由于与低温气体接触冷却收缩,形成负压,反向作用低温气体向中心流动收束,由此对冷却喷头所喷出的喷雾进行收束约束,集中冷却喷雾喷射点,提高冷却效率,提高模具加工精度以及高分子材料成型件成型效果。湍流时,热气流和冷气流相扰动,不再收束,以此提供更大的冷却面积。最终此上述中冷却液转化为蒸汽进行输送,避免雾化冷却液中液珠自聚凝结或粘附在管道内壁上,以此增大最终朝向加工刀具以及模具模块2喷射喷雾中冷却液含量,提高冷却量和冷却效率,由此对多轴加工机床加工处进行高效冷却,提高模具模块2加工精度以及延长加工刀具的使用寿命。实施例2,实施例1的提高注射模具加工精度的加工工艺,其包括以下步骤:s1:接通电源,为加工机构13、冷却液泵3312以及汽化组件333供电;s2:将模具模块2放置于加工室11内;s3:选择对模具模块2加工进行大面积切削面,调节热气流量调节阀和冷气流量调节阀,使内喷管322内流速与夹腔323内流速之比为0.8~1.2,气压保持2.3bar。s3.5:更换加工刀具131;s4:选择模具模块2加工小区域的高精度切削,调节热气流量调节阀和冷气流量调节阀,使内喷管322内流速与夹腔323内流速之比为0.4~0.54,气压保持2.2bar;s5:加工结束,取下模具模块2。其中s3和s4可根据模具模块2加工次序需求进行替换以及在进行s4步骤后返回重复s3。s3.5可根据实际加工需求选择性实行。根据上述使用工艺,对实施例1的多轴自动机床进行冷却效果的测试测试效果如下表一所示。另外以关闭冷却气源34截止阀,停止加热件3331加热,增大推进气流流量阀开度,使得内喷管322单独出气,且保证内喷管322喷射气压为2.2bar作为对比例。内流速与夹腔内流速之比冷却喷头喷雾温度/℃切削处冷却前温度/℃切削处冷却时温度/℃降温量/℃0.8173561202361193671262411.2203581232350.484351452980.45104461482980.5412438145293对比例20438267171由上表可知,本申请的多轴自动机床具可进行高效冷却,提高模具模块2加工精度以及延长加工刀具的使用寿命。本具体实施例仅仅是对本发明的解释,其并不是对本发明的限制,本领域技术人员在阅读完本说明书后可以根据需要对本实施例做出没有创造性贡献的修改,但只要在本发明的权利要求范围内都受到专利法的保护。当前第1页1 2 3