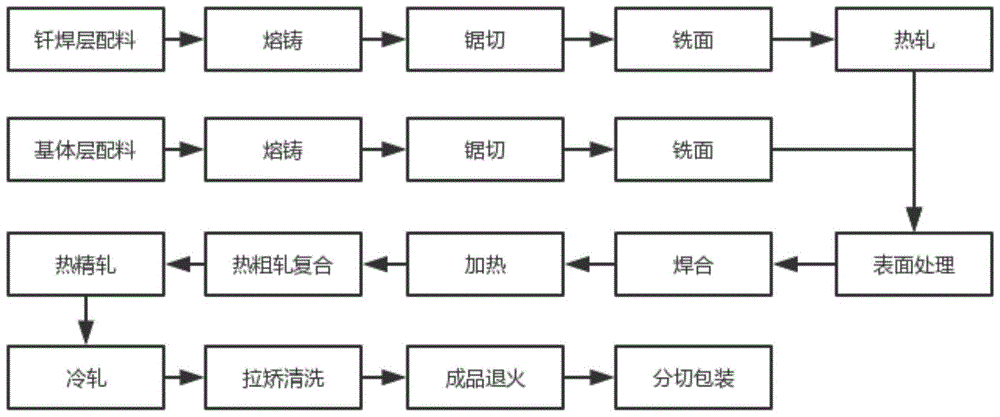
本发明属于铝合金制造
技术领域:
,涉及一种钎焊用铝合金三层复合材的制备方法,尤其涉及一种综合性能优良的钎焊用铝合金三层复合材的制备方法。
背景技术:
:常见的钎焊用铝合金复合材实质为金属层状复合结构,按照不同材料层的作用可分为钎焊层、基体层和牺牲阳极保护层。其中,钎焊层采用4系低熔点的al-si合金,基体层一般采用熔点高于4系的3系al-mn合金,而牺牲阳极保护层采用腐蚀电位较低的7系al-zn-mg合金。根据零件结构钎焊需求的不同,三层钎焊用铝合金复合材一般为“钎焊层+基体层+钎焊层”或“钎焊层+基体层+牺牲阳极氧化层”的组合方式。按照不同的轧制厚度可分为钎焊用复合铝板、铝带和铝箔三种形式。现有技术钎焊用铝合金复合材工艺繁琐复杂,以4343/3003/4343三层复合材为例,多层结构的成分设计和制备过程中面临许多问题,现有的技术仍存在以下不足:1、钎焊层铝锭和和基体层铝锭的均匀化热处理和热轧加热分别进行,不仅延长工时还造成较大的能源消耗;2、焊合前表面处理工序较多且效率不高,对表面进行人工打磨或使用强酸强碱处理造成粉尘污染和化学污染;3、高温钎焊后材料强度过低,抗下垂性能不达标,实际装配使用后造成换热器塌陷;4、成分设计不能兼顾复合材腐蚀性能和力学性能,刻意提高力学性能可能导致零件腐蚀失效。技术实现要素:有鉴于此,本发明为了解决现有技术中三层钎焊复合材生产工艺复杂、能源消耗大、环境污染以及钎焊后腐蚀性及强度不兼顾的问题,提供一种工艺简单可靠、环境友好且能源消耗低的钎焊用铝合金三层复合材的制备方法。为达到上述目的,本发明提供一种钎焊用铝合金三层复合材的制备方法,包括以下步骤:a、配料:将钎焊层和基体层铸锭所用的原材料分别配料;b、熔铸:将配制好的钎焊层和基体层原料采用半固态铸造法熔铸分别得到钎焊层铸锭和基体层铸锭,其中钎焊层合金精炼扒渣后加入al-sr中间合金进行变质处理;c、锯切铣面:将钎焊层铸锭和基体层铸锭头尾端锯切至合适的长度,其中主铣量≥15mm,侧铣量≥10mm,基体层铸锭铣面后铸锭厚度为h;d、钎焊层铸锭热轧:钎焊层铸锭加热至480℃保温3小时,出炉轧制至目标厚度h,轧制道次为17~25,当设计包覆率为a%时,基体层铸锭厚度h和钎焊层铸锭厚度h应满足如下关系:a%=h/(h+h)×100%;e、表面处理和焊合:先将与基体层铸锭贴合一面的钎焊层铸锭打磨,再将基体层铸锭上下表面使用气枪吹去表面粉尘后喷洒航空煤油,随后用吸油纸或吸油布擦拭;将打磨好的钎焊层铸锭和擦拭后的基体层铸锭吊装贴合,使用co2气体保护焊对两边局部焊接,最后使用若干钢带将组合后的复合材箍紧装炉;f、热轧加热:采用双级加热方式将基体铸锭均匀化与复合材热轧加热合并进行,即在520℃下保温6~8小时后降温至480℃保温2小时,复合材热轧加热出炉后去除钢带;g、热粗轧复合:复合材的热粗轧开轧温度为480℃,热轧道次为25~30,前5-8道次采用小压下量,轧制速度控制在1m/s以下,保证钎焊层和基体层之间的缝隙被充分压合并排尽气体,中间道次逐渐增加压下量和轧制速度使得钎焊材和基体充分延展复合,热粗轧中间坯厚度为40~50mm,热粗轧终轧温度控制在410±15℃;h、热精轧:将热粗轧得到中间坯料进行热精四连轧,终轧制温度控制在330℃±10℃,并切边卷曲成卷;i、冷轧、拉矫清洗和成品退火:热精轧后的卷材根据最终需求,通过冷轧以及成品退火来制备不同厚度和状态的冷轧产品,冷轧道次总加工量不低于30%,拉伸矫直延伸率在0.5~1.5%之间,清洗方式采用碱洗。进一步,步骤a中钎焊层和基体层铸锭所用的原材料以重量百分比的形式配料,其中钎焊层原料成分为si:7.5~7.9%,fe≤0.3%,mg≤0.02%,cu:0.1~0.2%,mn≤0.1%,cr≤0.05%,zn:0.1~0.2%,ti≤0.03%,sr≤0.03%,单个杂质≤0.05%,杂质合计≤0.15%,余量为al,基体层原料成分为mn:1.3~1.4%,zn:0.9~1.0%,si:0.3~0.4%,fe:0.25~0.35%,cu:0.1~0.2%,mg≤0.05%,cr≤0.05%,ti≤0.03%,sr≤0.03%,单个杂质≤0.05%,杂质合计≤0.15%,余量为al。进一步,步骤a中基体层原料中除mg和zn以合金锭的方式加入以外,其他元素均以中间合金的形式加入。进一步,步骤b钎焊层和基体层原料熔炼过程为静置、精炼、扒渣、在线除气、过滤、铸造,熔炼温度为740~760℃,精炼温度730~750℃,铸造温度670~690℃。进一步,步骤b钎焊层合金精炼扒渣采用双转子snif在线除气,转速为460~500rpm,氩气量范围控制在5~6nm3/hr,精炼过程中加入al-5ti-1b丝精炼剂,过滤方式采用深床过滤或管式过滤。进一步,步骤e基体层铸锭打磨采用装有钢丝滚刷的皮带打磨机,打磨过程中应打开抽风系统吸除粉尘,打磨后使用气枪吹去金属粉尘,使用co2气体保护焊进行边部焊接时应使用压合机压紧钎焊层和基体层。进一步,步骤i碱洗方式为将拉伸矫直后的复合卷材置于质量分数为15~25%的naoh溶液中蚀洗2~10min,再用水冲洗3~5次吹干。进一步,步骤i成品卷材退火温度为200~350℃,退火时间为3h。本发明的有益效果在于:1、本发明所公开的钎焊用铝合金三层复合材的制备方法中,钎焊层采用4343铝合金,成分范围如下:si元素是4343合金的主合金元素,控制si元素含量能够使得钎焊层材料在熔融状态下具有良好的流动性和润湿性,但si元素过量会导致钎焊过程中si元素扩散严重并造成钎焊后性能下降,因此si元素控制在7.5~7.9%。fe元素可以形成不同于铝的金属间化合物,提高合金强度也硬度,但fe含量过多时会导致生成粗大的almfe相,造成合金塑性下降,因此fe元素≤0.3%。mg元素含量根据钎焊方式的不同而有所调整,当采用可控气体保护焊时为避免mg与混入的空气接触在高温时发生烧损逸出影响钎焊,应严格控制,故mg元素含量应≤0.02%。此外还需添加一定质量的sr元素作为变质剂,其含量应该根据4343的共晶si的变质效果进行调整优化,最终添加量以结果为准,一般来说≤0.03%。基体层合金成分是基于3003铝合金进行修改,为al-mn-zn系铝合金,其成分范围如下:mn元素作为主要的合金元素能够和al形成al6mn合金化合物,提高合金的强度和硬度,合适的mn含量还能够提高合金的抗腐蚀性,并在退火后形成粗大长条状再结晶以提高复合材钎焊后的抗下垂性能,但mn元素过高会导致合金脆性增大,故mn含量控制在1.3~1.4%。zn元素的含量是本发明基体层合金成分的关键控制点,zn元素在基体中以固溶的形式存在,能够显著提高合金的强度和硬度,同时zn元素的能够有效促进热处理过程中硬脆相al6(fe,mn)相向α-al12(fe,mn)3si相的转变,zn元素还能够降低基体中的空位浓度,从而降低mn原子扩散速率使得形成的相更加细小,分布更加均匀,最终提高合金塑性。同时,zn元素会降低基体层的腐蚀电位,适当的调低翅片用复合材的腐蚀电位对换热装置整体腐蚀抗性有好处,但zn元素过量会导致基体层腐蚀电位差过低,严重影响复合材和换热装置整体的耐腐蚀性。因此将zn元素控制在0.9~1.0%。此外还需添加一定质量的sr元素作为变质剂,其含量应该根据4343的共晶si的变质效果进行调整优化,最终添加量以结果为准,一般来说≤0.03%。上述合金元素中除mg和zn以合金锭的方式加入以外,其他元素均以中间合金的形式加入。2、本发明所公开的钎焊用铝合金三层复合材的制备方法,通过成分优化设计,能够提高复合材的强度和高温钎焊后的抗下垂性能,同时保证力学性能和腐蚀性能的平衡,能够很好的满足可控气体保护焊的钎焊要求。3、本发明所公开的钎焊用铝合金三层复合材的制备方法,将钎焊材和基体铸锭组合后同时进行均匀化热处理和热轧加热的双级加热方式,能够极大地提高生产效率同时减少能源消耗,并且满足产品性能要求,能够在保证力学性能的同时兼顾腐蚀性能。4、本发明所公开的钎焊用铝合金三层复合材的制备方法,采用一种简单高效的表面处理工艺,能够获得洁净且满足钎焊用三层复合材热轧复合要求的结合面,提高生产效率且避免了粉尘和化学污染,满足绿色生产的要求。本发明的其他优点、目标和特征在某种程度上将在随后的说明书中进行阐述,并且在某种程度上,基于对下文的考察研究对本领域技术人员而言将是显而易见的,或者可以从本发明的实践中得到教导。本发明的目标和其他优点可以通过下面的说明书来实现和获得。附图说明为了使本发明的目的、技术方案和优点更加清楚,下面将结合附图对本发明作优选的详细描述,其中:图1为本发明钎焊用铝合金三层复合材的制备方法的流程图。具体实施方式以下通过特定的具体实例说明本发明的实施方式,本领域技术人员可由本说明书所揭露的内容轻易地了解本发明的其他优点与功效。本发明还可以通过另外不同的具体实施方式加以实施或应用,本说明书中的各项细节也可以基于不同观点与应用,在没有背离本发明的精神下进行各种修饰或改变。根据如图1所示的本发明钎焊用铝合金三层复合材的制备方法的流程图,一种钎焊用铝合金三层复合材的制备方法,包括以下步骤:a、配料:计算制备钎焊层和基体层铸锭所用的各种合金锭和中间合金的用量并按照配比备料,其中4343钎焊层采用4343铝合金,基体层合金成分是基于3003铝合金进行修改,为al-mn-zn系铝合金,钎焊层和基体层各元素的质量百分比如下:合金成分sifecumnmgcrzntisral钎焊层7.60.150.140.020.0090.0010.150.0160.01余量基体层0.330.310.151.320.020.0010.920.0160.01余量将钎焊层和基体层铸锭所用的原材料分别配料;b、熔铸:将配制好的钎焊层和基体层原料分别加入到各自的熔炼炉中均匀混合熔炼为熔融液态金属,经过静置、精炼、扒渣、在线除气、过滤等工艺流程,采用半固态铸造法熔铸分别得到钎焊层铸锭和基体层铸锭,其中熔炼温度为750±5℃,精炼温度740±5℃,铸造温度675±5℃,钎焊层合金精炼扒渣后加入al-sr中间合金进行变质处理,并取样检验变质效果,铸造方式采用半固态连续铸造,除气方式采用双转子snif在线除气,设定转速500rpm,氩气量范围控制在5.9nm3/hr,精炼过程中加入al-5ti-1b丝精炼剂,过滤方式采用深床过滤;c、锯切铣面:将钎焊层铸锭和基体层铸锭头尾端锯切至合适的长度,其中上下表面主铣量15±1mm,侧铣量10±1mm,铣面后应记录铸锭厚度420±2mm,上下表面平整,无隆起、凹坑、反刀痕或其他影响表面粗糙度的缺陷;d、钎焊层铸锭热轧:钎焊层铸锭使用推进式加热炉加热,钎焊层铸锭加热至480℃保温3小时,目标包覆率为10%,故钎焊层铸锭经25道次热轧至目标厚度52.5mm,基体层铸锭厚度和钎焊热轧目标厚度满足包覆率要求;e、表面处理和焊合:热轧后的钎焊材按照基体上下表面尺寸进行精密锯切,使用装有钢丝滚刷的自动打磨机对钎焊材与基体铸锭贴合的一面打磨,使用气枪吹去残留金属粉尘。随后使用气枪吹去铣面后的基体铸锭表面的粉尘,将航空煤油均匀地喷洒在待复合表面,并利用吸油纸擦拭至表面无粉尘、油渍等。随后将打磨好的钎焊材和擦拭后的基体铸锭吊装贴合,在压合机压紧时使用co2气体保护焊对两边进行局部焊接,最后使用3~4根钢带将组合后的复合材箍紧装炉;f、热轧加热:采用双级加热方式将基体铸锭均匀化与复合材热轧加热合并进行,即在520℃下保温6小时后降温至480℃保温2小时,复合材热轧加热出炉后去除钢带;g、热粗轧复合:复合材的热粗轧开轧温度为480℃,热轧道次为27,前8道次采用小压下量,轧制速度控制在0.5m/s以下,保证钎焊层和基体层之间的缝隙被充分压合并排尽气体,中间道次逐渐增加压下量和轧制速度使得钎焊材和基体充分延展复合,热粗轧中间坯厚度为40.3mm,热粗轧终轧温度控制在413℃;h、热精轧:将热粗轧得到中间坯料进行热精四连轧至目标厚度3.5mm,终轧制温度控制在330℃,并切边卷曲成卷;i、冷轧、拉矫清洗和成品退火:热精轧后的卷材经4道次冷轧至0.47mm,冷轧后的卷材经拉矫碱洗,拉矫延伸率为0.5%,碱洗方式为将拉伸矫直后的复合卷材置于质量分数为15~25%的naoh溶液中蚀洗2~10min,再用水冲洗3~5次吹干,碱洗后卷材在200~350℃每隔15℃的温度下均保温3小时退火,得到成品复合卷材。不同退火温度下,成品复合卷材的力学性能测试结果见表1:表1退火温度/℃抗拉强度/mpa屈服强度/mpa延伸率/%20020519011.121519717612.823018916613.924518716114.326018015316.227518115315.32901781491730517314216.53201456921.533514158.522.935013755.527成品h24态复合卷材参照日本焊接工艺学会标准的抗下垂测试方法得到的抗下垂性能结果,模拟钎焊温度为600℃,测试结果见表2:表2从上述力学性能和抗下垂结果可知,本发明制备的钎焊用三层铝合金复合板具有优异的综合性能,其冷轧成品经过不同温度退火后能够满足不同状态的产品的使用要求,同时能够在保证力学性能的同时通过调节zn含量的成分兼顾腐蚀性能。最后说明的是,以上实施例仅用以说明本发明的技术方案而非限制,尽管参照较佳实施例对本发明进行了详细说明,本领域的普通技术人员应当理解,可以对本发明的技术方案进行修改或者等同替换,而不脱离本技术方案的宗旨和范围,其均应涵盖在本发明的权利要求范围当中。当前第1页12