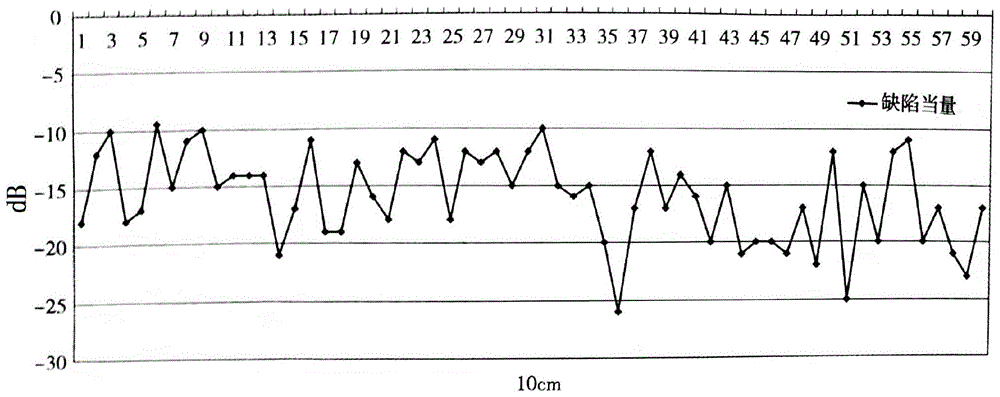
本发明涉及一种基于钢锭内部缺陷分级的钢锭锻造工艺选择的方法,属于钢锭无损检测和热锻工艺选择的
技术领域:
。
背景技术:
:现代使用的钢材品种,都是由钢锭轧制或锻造而成的,因此在钢铁产业飞速发展的今天,对钢锭质量的追求一直是大型钢铁企业追求的目标。在钢锭的生产过程中,钢锭质量检测是最重要的一个环节。企业只有及时准确对产品进行质量检测,才能够根据具体生产情况正确的调整生产策略。可以看出有效的钢锭的质量检测能保证其生产效率和产品质量,同时也是企业获得经济效益的有力保障。深海采油设备弯头锻件应用于深海环境,需要承受水深带来的高压,以及水下暗流的冲击,需要有非常强的承压能力,很高的冲击功。深海采油设备弯头锻件的质量保障要用源头做起,一旦中途有产品质量问题,必须报废,将会造成非常高的经济损失,按照申请人单位的申请量,若一日内锻造处理量均为报废品,日损失达50万。可见对于锻件的选材,即钢锭坯料的判定具有非常高的工作指导意义。技术实现要素:为了解决上述技术问题,本发明提供一种基于钢锭内部缺陷分级指导深海采油设备弯头锻件的锻造工艺选择方法,其具体技术方案如下:基于钢锭内部缺陷分级指导深海采油设备弯头锻件的锻造工艺选择方法,包括以下步骤:步骤1:钢锭内部缺陷检测:选取钢锭,钢锭的长度和当量直径的比值小于2.5~3,将其静置,使用超声波探测仪,从钢锭长度方向的一端检测另一端,得到超声波探伤的波形;步骤2:检测结果分级:根据探伤的波形将探伤分为5个级别,具体为:当探伤波形为降低草状时,钢锭无明显缺陷,晶粒呈粗大状,命名探伤等级为0级,当探伤波形为中心疏松时,钢锭中心有分散细小孔洞,命名探伤等级为1级,当探伤波形为中心疏松+缩孔时,钢锭中心有分散细小孔洞,且有小的集中孔洞,命名探伤等级为2级,当探伤波形为中心缩孔+疏松时,钢锭有集中孔洞,且有少量分散细小孔洞,命名探伤等级为3级,当探伤波形为中心缩孔时,钢锭中心有较大集中孔洞,命名探伤等级为4级;步骤3:根据探伤分级选定锻造工艺:随着探伤等级的增大,锻造的温度升高,锻造比增大,锻造速度增大,锻造次数增多。进一步的,所述步骤1在超声波探伤检测前需要对坯料进行预处理,预处理具体为:当坯料检测表面粗糙度大于30μm时,打磨检测表面,直到其粗糙度为10~30μm,当坯料检测表面可见光亮小于50%时,打磨检测表面,直到可见50%以上光亮。进一步的,所述打磨坯料表面的方法为:采用0°、45°、90°或0°、120°、240°间隔方式打磨,打磨的宽度不小于100mm,沿着坯料钢锭的长度方向打磨,且从长度方向的一端打磨到另一端,形成纵向通条,所述纵向通条至少3条,顺序标识。进一步的,沿着纵向通条顺序取100mmx100mm的区域分别进行探伤测定,得到各段的探伤等级,并根据探伤测定结果以及其所在位置制表,得到坯料钢锭在其长度方向上,各个位置的探伤缺陷的大小和等级,并根据制表数据,绘制钢锭坯料长度方向上探伤缺陷大小的分布图和坯料钢锭长度方向上探伤缺陷等级的分布图,根据钢锭坯料长度方向上探伤缺陷大小的分布图和坯料钢锭长度方向上探伤缺陷等级的分布图得到钢锭的整体探伤等级。进一步的,当缺陷等级达到4级的数量超过30%时,判定缺陷等级为4级;当缺陷等级达到4级的数量不超过30%,缺陷等级超过3级的数量超过30%时,判定缺陷等级为3级;当缺陷等级超过3级的数量不超过30%时,根据计算公式计算钢锭的缺陷等级,计算公式为:钢锭的整体探伤等级=探伤缺陷等级的总和/钢锭长度/100,其中钢锭长度的单位是mm。进一步的,当钢锭锻件的长度和直径的比值为为2.2~3.5时,所述步骤3具体为:当探伤等级为0级时,采用以下锻造工艺:步骤(01):将钢锭坯料加入到加热炉内加热至1200℃,转移到自由锻锤上锻粗,镦造比为1.5±0.1;步骤(02):将镦粗后的钢锭坯料再次投入到加热炉内,加热至1200℃,拔长至长度为截面当量直径的1.7±0.2倍;步骤(03):进入热处理工艺;当探伤等级为1级时,采用以下锻造工艺:步骤(11):将钢锭坯料加入到加热炉内加热至1250~1280℃,转移到自由锻锤上锻粗,镦造比为1.7~1.9;步骤(12):将镦粗后的钢锭坯料再次投入到加热炉内,加热至1250~1280℃,拔长至长度为截面当量直径的1.9~2.1倍;步骤(13):进入热处理工艺;当探伤等级为2级时,采用以下锻造工艺:步骤(21):将钢锭坯料加入到加热炉内加热至1280~1320℃,转移到自由锻锤上锻粗,镦造比为1.9~2.0;步骤(22):将镦粗后的钢锭坯料再次投入到加热炉内,加热至1280~1320℃,拔长至长度为截面当量直径的2.0~2.2倍;步骤(23):重复步骤(21)和(22)一次;步骤(24):进入热处理工艺;当探伤等级为3级时,采用以下锻造工艺:步骤(31):将钢锭坯料加入到加热炉内加热至1320~1350℃,转移到自由锻锤上锻粗,镦造比为1.9~2.0;步骤(32):将镦粗后的钢锭坯料再次投入到加热炉内,加热至1280~1350℃,拔长至长度为截面当量直径的2.0~2.2倍;步骤(33):重复步骤(31)和(32)一次;步骤(34):进入热处理工艺;当探伤等级为4级时,判定钢锭为次品,不可用于深海采油设备弯头锻件的锻造。进一步的,当钢锭锻件的长度和直径的比值为小于2.2时,所述步骤3具体为:当探伤等级为0级时,采用以下锻造工艺:步骤(01):将钢锭坯料加入到加热炉内加热至1200℃,拔长至长度为截面当量直径的1.7±0.2倍;步骤(02):将镦粗后的钢锭坯料再次投入到加热炉内,加热至1200℃,转移到自由锻锤上锻粗,镦造比为1.5±0.1;步骤(03):进入热处理工艺;当探伤等级为1级时,采用以下锻造工艺:步骤(11):将钢锭坯料加入到加热炉内加热至1250~1280℃,拔长至长度为截面当量直径的1.9~2.1倍;步骤(12):将镦粗后的钢锭坯料再次投入到加热炉内,加热至1250~1280℃,转移到自由锻锤上锻粗,镦造比为1.7~1.9;步骤(13):进入热处理工艺;当探伤等级为2级时,采用以下锻造工艺:步骤(21):将钢锭坯料加入到加热炉内加热至1280~1320℃,拔长至长度为截面当量直径的2.0~2.2倍;步骤(22):将镦粗后的钢锭坯料再次投入到加热炉内,加热至1280~1320℃,转移到自由锻锤上锻粗,镦造比为1.9~2.0;步骤(23):重复步骤(21)和(22)一次;步骤(24):进入热处理工艺;当探伤等级为3级时,采用以下锻造工艺:步骤(31):将钢锭坯料加入到加热炉内加热至1320~1350℃,拔长至长度为截面当量直径的2.0~2.2倍;步骤(32):将镦粗后的钢锭坯料再次投入到加热炉内,加热至1280~1350℃,转移到自由锻锤上锻粗,镦造比为1.9~2.0;步骤(33):重复步骤(31)和(32)一次;步骤(34):进入热处理工艺;当探伤等级为4级时,判定钢锭为次品,不可用于深海采油设备弯头锻件的锻造。本发明的有益效果是:本发明首先对钢锭坯料进行无损超声波检测,判定钢锭内部的缺陷等级,绘制出对应的缺陷图,然后计算出钢锭的整体缺陷等级,等级确认后,根据等级以及钢锭的长度和直径当量的比值,选用对应的工艺,最大降低锻造的能量消耗,以及确保锻件的质量。附图说明图1是本发明的实施1长度方向上探伤缺陷大小的分布图,图2是本发明的实施1长度方向上探伤缺陷等级的分布图。具体实施方式现在结合具体实施方式进一步说明本发明的技术方案和达到效果。实施例1:下面以选用连铸坯材料为aisi4130,尺寸为直径600mm,长度6000mm的圆形钢锭为例,说明本发明的一个具体应用。使用超声波无损探伤检测时,从其头部到胃部每个10cm探伤一次。探伤灵敏度采用试块dac法,将底波调到合适高度,再提高18db作为探伤灵敏度,探伤当量结果和探伤等级划分如表1所示。表1:探伤大小和分级距离(cm)≤102030405060708090100110120130140150当量(db)-18-12-10-18-17-9.5-15-11-10-15-14-14-14-21-17等级044002024200100距离(cm)160170180190200210220230240250260270280290300当量(db)-11-19-19-13-16-18-12-13-11-18-12-13-12-15-12等级202220121021201距离(cm)310320330340350360370380390400410420430440450当量(db)-10-15-16-15-20-26-17-12-17-14-16-20-15-21-20等级120000010120220距离(cm)460470480490500510520530540550560570580590600当量(db)-20-21-17-22-12-25-15-20-12-11-20-17-21-23-17等级020010000210000将表1的数据结合无损探伤检测的大小和分级做出图1和图2,结合附图可见,对于一个连铸坯,从头部到尾部,其探伤缺陷当量大小是变化的,探伤等级也是变化的,这就需要计算出连铸坯的整体缺陷等级,在此需要计算得出坯料的整体坯料缺陷等级,然后根据缺陷等级,选择对应锻造工艺。首先,当缺陷等级达到4级的数量超过30%时,判定缺陷等级为4级;当缺陷等级达到4级的数量不超过30%,缺陷等级超过3级的数量超过30%时,判定缺陷等级为3级;当缺陷等级超过3级的数量不超过30%时,根据计算公式计算钢锭的缺陷等级,计算公式为:钢锭的整体探伤等级=探伤缺陷等级的总和/钢锭长度/100,其中钢锭长度的单位是mm。连铸坯的缺陷等级确认后,根据连铸坯的形状来选定锻造工艺:当钢锭锻件的长度和直径的比值为为2.2~3.5时,所述步骤3具体为:当探伤等级为0级时,采用以下锻造工艺:步骤(01):将钢锭坯料加入到加热炉内加热至1200℃,转移到自由锻锤上锻粗,镦造比为1.5±0.1;步骤(02):将镦粗后的钢锭坯料再次投入到加热炉内,加热至1200℃,拔长至长度为截面当量直径的1.7±0.2倍;步骤(03):进入热处理工艺;当探伤等级为1级时,采用以下锻造工艺:步骤(11):将钢锭坯料加入到加热炉内加热至1250~1280℃,转移到自由锻锤上锻粗,镦造比为1.7~1.9;步骤(12):将镦粗后的钢锭坯料再次投入到加热炉内,加热至1250~1280℃,拔长至长度为截面当量直径的1.9~2.1倍;步骤(13):进入热处理工艺;当探伤等级为2级时,采用以下锻造工艺:步骤(21):将钢锭坯料加入到加热炉内加热至1280~1320℃,转移到自由锻锤上锻粗,镦造比为1.9~2.0;步骤(22):将镦粗后的钢锭坯料再次投入到加热炉内,加热至1280~1320℃,拔长至长度为截面当量直径的2.0~2.2倍;步骤(23):重复步骤(21)和(22)一次;步骤(24):进入热处理工艺;当探伤等级为3级时,采用以下锻造工艺:步骤(31):将钢锭坯料加入到加热炉内加热至1320~1350℃,转移到自由锻锤上锻粗,镦造比为1.9~2.0;步骤(32):将镦粗后的钢锭坯料再次投入到加热炉内,加热至1280~1350℃,拔长至长度为截面当量直径的2.0~2.2倍;步骤(33):重复步骤(31)和(32)一次;步骤(34):进入热处理工艺;当探伤等级为4级时,判定钢锭为次品,不可用于深海采油设备弯头锻件的锻造。进一步的,当钢锭锻件的长度和直径的比值为小于2.2时,所述步骤3具体为:当探伤等级为0级时,采用以下锻造工艺:步骤(01):将钢锭坯料加入到加热炉内加热至1200℃,拔长至长度为截面当量直径的1.7±0.2倍;步骤(02):将镦粗后的钢锭坯料再次投入到加热炉内,加热至1200℃,转移到自由锻锤上锻粗,镦造比为1.5±0.1;步骤(03):进入热处理工艺;当探伤等级为1级时,采用以下锻造工艺:步骤(11):将钢锭坯料加入到加热炉内加热至1250~1280℃,拔长至长度为截面当量直径的1.9~2.1倍;步骤(12):将镦粗后的钢锭坯料再次投入到加热炉内,加热至1250~1280℃,转移到自由锻锤上锻粗,镦造比为1.7~1.9;步骤(13):进入热处理工艺;当探伤等级为2级时,采用以下锻造工艺:步骤(21):将钢锭坯料加入到加热炉内加热至1280~1320℃,拔长至长度为截面当量直径的2.0~2.2倍;步骤(22):将镦粗后的钢锭坯料再次投入到加热炉内,加热至1280~1320℃,转移到自由锻锤上锻粗,镦造比为1.9~2.0;步骤(23):重复步骤(21)和(22)一次;步骤(24):进入热处理工艺;当探伤等级为3级时,采用以下锻造工艺:步骤(31):将钢锭坯料加入到加热炉内加热至1320~1350℃,拔长至长度为截面当量直径的2.0~2.2倍;步骤(32):将镦粗后的钢锭坯料再次投入到加热炉内,加热至1280~1350℃,转移到自由锻锤上锻粗,镦造比为1.9~2.0;步骤(33):重复步骤(31)和(32)一次;步骤(34):进入热处理工艺;当探伤等级为4级时,判定钢锭为次品,不可用于深海采油设备弯头锻件的锻造。通过本发明方法可以得到准确的钢锭坯料的制作工艺,正确指导生产,避免出现因原材料(钢锭坯料)的缺陷或者锻造工艺的问题带来锻件的报废,造成材料浪费和财产损失。以上述依据本发明的理想实施例为启示,通过上述的说明内容,相关工作人员完全可以在不偏离本项发明技术思想的范围内,进行多样的变更以及修改。本项发明的技术性范围并不局限于说明书上的内容,必须要根据权利要求范围来确定其技术性范围。当前第1页12