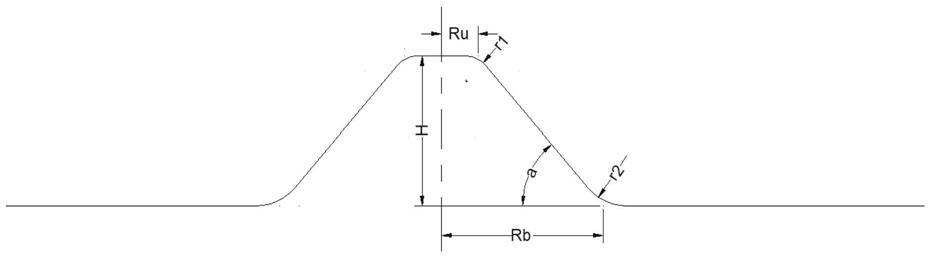
1.本发明涉及一种模组背板凸包的成形加工方法,尤其涉及一种提高成形性、减小开裂发生率的模组背板凸包二道次成形加工方法。
背景技术:2.模组背板是液晶电视机里面最重要的金属结构件,用于支撑液晶模组机各种电子元器件。整体设计上表现为大尺寸、平面(少量曲面)、浅冲压的钣金件,局部成形特征表现为大量的凸包、加强筋,主要作为各种电子元器件的安装基座,如图1所示,现有技术中,典型凸包设计为圆台形,上台面半径为ru,下台面半径为rb,凸包高度为h,倾角为a,上下圆角半径r1、r2过渡。一般情况下,凸包高度h为0~30mm不等,倾角a多为45
°
~60
°
。
3.另一方面,凸包开裂是模组背板成形加工中的主要风险点,由于凸包的设计特点,传统成形加工一般采用两个道次成形,其中第一道次预成形为半球面形,第二道次整形为设计形状,如图2所示,图中的两条线分别代表了第一道次和第二道次的结构轮廓。其中,半球面形状多由两段圆弧r3、r4组成,高度大致与凸包高度h相当,下台面半径(包括圆弧倒角段)rb2,较凸包设计的下台面(包括圆弧段)rb1略大。
4.尽管目前模组背板原材料已经采用了屈服强度较低、成形性较好的软钢(屈服强度150~160mpa左右),但是仍旧时常发生凸包开裂。特别是为了解决电视机整体结构强度刚度问题,部分模组背板采用强度较高的材料,如屈服强度达到200mpa,那凸包成形加工时开裂的风险将急剧增加,极大的影响模组背板冲压成形加工生产的稳定性。
5.而且考虑到凸包设计的布置以及模组背板成形后的尺寸精度要求,凸包成形第一道次预成形不宜过大,即rb2-rb1的差值不宜太大。预成形大当然对该凸包第二道次整形的成形性提供较好的基础,但是流入该凸包参与成形的材料过多,一方面影响临近凸包的成形,重要一点容易造成模组背板整体内应力较大且分布不均,导致整体容易发生翘曲等尺寸精度问题。
技术实现要素:6.本发明所要解决的技术问题在于提供一种可提高成形性、减小开裂发生率的模组背板凸包二道次成形加工方法。
7.其所要解决的技术问题可以通过以下技术方案来实施。
8.一种模组背板凸包二道次成形加工方法,包括预成形的第一道次和整形为设计形状的第二道次,第一道次预成形后进行第二道次整形加工,整形模具型面设计与原凸包设计相同;所述预成形的第一道次采用如下成形方法:
9.以原凸包设计中心为中心轴线,按中间为“山谷”形两侧为“山峰”形的“峰-谷-峰”造型为旋转曲面冲压成形;
10.其中,沿中心轴线,所述旋转曲面包括相对于所述中心轴线中心对称的谷形第一段圆弧以及依次向外的峰形第二段圆弧、坡形第三段圆弧和连接背板表面的第四段圆弧;
11.并且,
12.(1)所述第一段圆弧的弧底位于所述中心轴线上,其弧底距离背板表面所在平面的高度h1=1/2h,所述h为凸包设计高度;所述第二段圆弧的弧顶距离背板表面所在平面的高度h2=3/4h,所述第二段圆弧的弧顶距离所述中心线的距离rc=1/2rb,所述rb为不包括圆弧倒角的凸包下台面设计半径;
13.(2)所述第二段圆弧的半径r6=1/4h,所述第一段圆弧的半径r5=rb^2/(8r6)-r6/2;
14.(3)以所述第四圆弧与连接背板表面相接处距离所述中心轴线的距离为底部成形区半径rb2,其满足:rb2=rb1+δr,其中,δr为预成形半径增量,rb1为包括圆弧倒角的凸包下台面设计半径。
15.作为本技术方案的进一步改进,所述第四段圆弧为过渡圆角。
16.作为本技术方案的更进一步改进,所述第四段圆弧的半径r8=3~4mm。
17.也作为本技术方案的进一步改进,所述第三段圆弧的半径r7根据现有约束条件设定。
18.还作为本技术方案的进一步改进,δr=1~3mm。
19.采用上述技术方案的一种新的两道次模组背板凸包成形加工方法,主要是第一道次预成形的成形加工方法,在控制材料流入的前提下,降低凸包成形开裂发生率以及凸包对原材料成形性能的要求,保证高强材料凸包的成形性以及模组背板整体尺寸精度,增加背板原材料的适应窗口。
附图说明
20.图1为现有技术中的典型凸包设计结构示意图;
21.图2为传统两道次成形加工凸包结构示意图,其中,第一道次加工成半球面形,第二道次整形为设计形状;
22.图3为本发明成形加工方法中,第一道次模具型面设计结构示意;
23.图4为本发明实施例中某模组背板典型凸包设计结构示意;
具体实施方式
24.本发明的目的在于提供一种新的两道次模组背板凸包成形加工方法,主要是第一道次预成形的成形加工方法,在控制材料流入的前提下,降低凸包成形开裂发生率以及凸包对原材料成形性能的要求,保证高强材料凸包的成形性以及模组背板整体尺寸精度,增加背板原材料的适应窗口。
25.为了实现本发明的目的,提供了一种新的两道次模组背板凸包成形加工方法,主要是第一道次预成形的成形加工方法:
26.1)凸包成形加工分为两个道次进行,第一道次为预成形,第二道次整形为设计形状。如图3所示,其中第一道次预成形加工为以原凸包设计中心为轴心,中心截面为中间“山谷”、两侧“山峰”的“峰-谷-峰”造型的旋转曲面现状。
27.2)该旋转曲面母线由4段圆弧组成,从中心线开始,第一段圆弧为“山谷”,半径r5;第二段圆弧为“山峰”,半径r6,第三段圆弧为“山坡”,半径r7,第四段圆弧为底部过渡圆角,
半径r8。
28.3)第一段圆弧“山谷”圆心位于中心线上,“谷底”即圆弧与中心线交点高度h1=1/2h(h为凸包设计高度);第二段圆弧“山峰”顶点高度h2=3/4h,半径rc=1/2rb,rb为不包括圆弧倒角的凸包下台面设计半径。
29.4)底部成形区半径rb2=rb1+δr,其中δr为预成形半径增量,δr=1~3mm;rb1为包括圆弧倒角的凸包下台面设计半径。
30.5)第二段圆弧半径r6=1/4h,第一段圆弧半径r5=rb^2/(8r6)-r6/2,第四段圆弧半径r8=3~4mm,第三段圆弧半径r7根据现有约束条件设定。
31.6)第一道次预成形后进行第二道次整形加工,整形模具型面设计与原凸包设计相同。
32.如图3所示,图中,标号30的虚线代表凸包设计的外形,标号20为现有的半球形第一道次结构;图中的粗实线代表本发明第一道次的结构,其包括中间的山谷11(第一段圆弧),以及向外依次接续的山峰12(第二段圆弧)、山坡13(第三段圆弧)和过渡圆角14,其中过渡圆角与模组背板40相接续;标号50为旋转曲面的中心轴线。
33.这样在控制凸包外材料流入的前提下,通过凸包内材料充分变形,保证不劣化模组背板尺寸精度的同时实现了凸包的高成形性,扩大模组背板冲压成形加工对原材料的适应窗口。
34.下面将结合具体实施例和附图对本发明的模组背板凸包二道次成形加工方法做出进一步的说明。
35.参照图4,本实施例中,针对某模组背板为了保证足够的结构强度刚度,采用原材料厚度t=0.8mm,屈服强度200mpa材料进行冲压上。背板上典型凸包设计,高度h=12mm,倾角a=50
°
,上台面半径ru=2.93mm,下台面半径rb=13mm,包括过渡圆弧的下台面半径rb1=16.04mm;上下过渡圆角半径分别为r1=2mm,r2=4mm。其中,图中数字尺寸对应的内容可参考图1中对应的各处标注。
36.由于采用传统的第一道次半球面型面预成形、第二道次整形发生较严重开裂。而采用本发明的“峰-谷-峰”造型的旋转曲面作为第一道次预成形模具型面,其中预成形半径增量与采用半球形型面设计保持一样,δr=1.89mm,底部成形区半径rb2=17.93mm,谷峰顶点高度分别为h1=6mm、h2=9mm,四段圆弧半径分别为r5=5.54mm,r6=3mm,r7=35.41mm,r8=3mm,第二道次成形加工采用原凸包设计型面进行整形,最终凸包成形良好,没有发生开裂现象。这样保证了不劣化模组背板尺寸精度的前提下,实现了凸包在高强材料下的两道次成形。