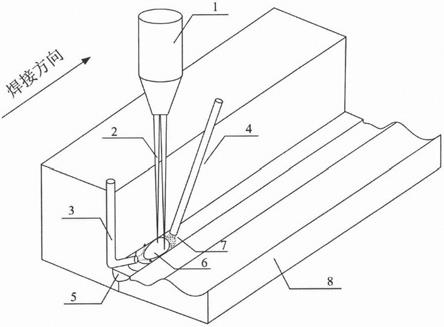
1.本发明涉及激光焊接技术领域,具体涉及一种厚板钛合金窄间隙双激光束填粉焊接方法。
背景技术:2.随着重型工业的高速发展,运用于船舶制造、核电设施、压力容器等装备上的构件逐渐呈现厚壁化趋势,如何实现厚板钛合金的良好焊接成为了钛合金焊接的研究重点之一。窄间隙激光填丝技术是利用激光熔化焊丝对焊缝间隙进行填充从而实现厚板的焊接,但激光填丝对送丝设备精度以及送丝工艺要求极为严格,焊接过程中容易出现顶丝现象,同时激光的利用率较低。同时有研究人员提出激光-mig复合焊接,但电弧的引入会增大热输入,造成较大的焊接变形,如果激光不能有效稳弧,也会引发飞溅等缺陷。激光摆动焊可以一定程度上减小焊接气孔倾向,但无疑对设备提出了更高的要求。
3.研究发现,当双光束激光作用于一个熔池中时,可以形成较大的熔池与匙孔,提高匙孔的稳定性,改善熔池的流动性,优化焊缝成形,降低气孔的倾向性。与激光填丝相比,激光填粉焊接填充焊料多元化,易于调节焊缝元素成分;减小焊接表面凹陷、咬边等缺陷的产生,改善焊接质量;粉末送进速度和方向受制约程度明显降低;同时粉末颗粒提高了激光能量利用率,减少能量损失。
4.厚板钛合金的窄间隙双激光束填粉焊接技术是在原来窄间隙激光焊接技术的基础上,针对焊接过程稳定性差、熔池波动大、极易产生气孔等问题,进一步提出的方法,结合了双激光束焊接及激光填粉焊接的优势,此技术对推进厚板钛合金的焊接具有重要的研究与应用意义。
技术实现要素:5.针对上述存在的问题,本发明旨在提供一种厚板钛合金窄间隙双激光束填粉焊接方法,以解决现有技术中窄间隙激光焊接厚板时存在的焊缝成形不良、焊接气孔、裂纹较多等问题,本发明的方法能够有效改善焊接缺陷,提高焊接过程稳定性,同时焊接效率高,并且设备简单、易于实现。
6.为了达到上述目的,本发明提供一种厚板钛合金窄间隙双激光束填粉焊接方法,包括以下步骤:
7.(1)坡口设计及焊前处理:焊件厚度100-130mm,为减小填充体积同时避免热量积累,设计开带钝边的u型坡口,钝边10-15mm,底边坡口宽度3-6mm,焊前先对坡口附近进行机械打磨和化学清洗,去除表面氧化膜、水分、油污等,吹干后利用夹具将焊件装夹固定在工作台上。
8.(2)激光自熔打底焊:利用大功率激光器对钝边进行激光深熔打底,实现一次性焊透成形。工艺参数设置为:激光功率为10kw-30kw,光斑直径为2-8mm。焊接速度为1.0-5.0m/min,焊接过程中侧吹流量为15l/min的99.9%氩气气体作为保护气体以避免焊件氧化。
9.(3)双激光束填粉填充焊:在打底焊缝上端以一定距离依次排列送粉管、激光器和送气管,送粉方式采用非同轴侧向送粉,开启送粉管在前方预置粉末,通过送粉器调节送粉速率,保证焊接时金属粉末量充足,同时开启激光器和送气管开始焊接,通过运动机构使送气管、激光头、送粉管以相同的速度向前同步移动,进行多层单道焊接,每层采用直线焊接路径,焊接方向一致,完成单层焊接后待焊缝冷却至室温再进行下一层的施焊,并对层间焊缝进行清理。具体工艺参数为:激光功率2000w-6000w,离焦量-2-+2mm,焊接速度0.5-1.5m/min,保护气采用99.9%纯氩气,保护气体流量为15l/min,焊料选用球磨制备的合金粉末,颗粒直径为100-150μm。
10.进一步地,所述双光束可以为同种激光采用光学分离方法分成两个独立的光束或双激光器同时作业,所用双光束的光束排列方式、光斑间距、光束角度均可人为调控。
11.进一步地,送粉管、激光作用位置、送气管之间的相对位置保持不变,其中送粉管与激光作用位置间距为1-100mm,送气管与激光作用位置间距为1-100mm。
12.进一步地,所用送粉管和送气管直径可根据坡口宽度改变,双管均深入到坡口内部,送粉角度可通过装夹设备调节。
13.本发明的有益效果为:
14.本发明采用激光填粉代替现有技术中常用的激光填丝作为填料方式,在工艺上不受焊丝制备的制约,填充材料的选择多元化,方便焊缝化学成分、微观组织的调控,粉末送进易于调控,设备要求明显降低,工艺灵活,粉末颗粒相互反射吸收激光,能量利用率大大提高,同时有利于光致等离子体的控制,从而稳定熔池。在此基础上采用双激光束作为热源,改善了熔池及匙孔行为,因此有利于焊缝成形,提高了焊接过程稳定性,抑制了气孔、裂纹等缺陷的产生。本发明设备简单、易于实现,对促进厚板窄间隙激光焊接在提高焊接效率及焊接稳定性、减小焊接缺陷上具有一定的意义。
附图说明
15.图1为本发明所述窄间隙双激光束填粉焊接整体结构及装置示意图。
16.图2为本发明所述激光自熔打底焊方法示意图。
17.图3为本发明所述双激光束填粉填充焊方法示意图。
18.图中,1-激光头,2-双光束,3-送气管,4-送粉管,5-焊缝,6-焊接熔池,7-填充粉末,8-母材,9-单光束。
具体实施方案
19.为了便于本领域技术人员的理解,以下结合附图对本发明进行进一步的描述,应当理解,在此提供的附图都是为了说明的目的,附图不一定是按比例绘制的。
20.本发明提供的窄间隙激光焊接方法主要由激光自熔打底焊和双激光束填粉填充焊组成,利用双光束稳定焊接过程、减少气孔或裂纹等缺陷的特点以及激光填粉工艺灵活的优势,改善焊接成形,提高焊接接头的质量,具体步骤如下:
21.步骤一,如图1所示,待焊焊件厚度100mm,为减小填充体积同时避免热量积累,设计开带钝边的u型坡口,钝边15mm,底边坡口宽度4mm,焊前先对坡口附近进行机械打磨和化学清洗,去除表面氧化膜、水分、油污等,吹干后利用夹具将焊件装夹固定在工作台上。
22.步骤二,如图2所示,首先将激光束9聚焦于焊接起始位置,送气管3位于焊接路径的后方,与激光束9保持一定的距离,同时开启激光器和送气装置,激光束9和送气管3以相同的速度向前移动,实现钝边的激光深熔打底。工艺参数设置为:激光功率为15kw,光斑直径为2mm。焊接速度为6m/min,焊接过程中侧吹流量为15l/min的99.9%氩气气体作为保护气体以避免焊件氧化。
23.步骤三,如图3所示,首先将双光束2聚焦于焊接起始位置,移动送粉管4在激光束前方预置粉末,同时开启激光器进行焊接,双光束2照射在填充粉末8上对焊缝间隙进行填充,送气管3在双光束2后方侧吹保护气对焊接熔池及焊缝刚凝固区域进行保护,焊接过程中送气管3、激光束2和送粉管4之间保持一定的距离不变,完成单道焊接后,将送气管3、激光束2、送粉管4整体上移并回到焊接起始位置,进行多层单道焊接,每层采用直线焊接路径,焊接方向一致,完成单层焊接后待焊缝冷却至室温再进行下一层的施焊,并对层间焊缝进行清理。具体工艺参数为:激光功率6000w,离焦量0mm,焊接速度0.8m/min,保护气采用99.9%纯氩气,保护气体流量为15l/min,焊料选用球磨制备的合金粉末,颗粒直径为100μm。
24.应当理解,上述的实施方式仅是示例性的,而非限制性的,只要在本发明的实质精神范围内,对上述细节做出的各种简单修改或替换,都将包含于本发明的权利要求范围内。