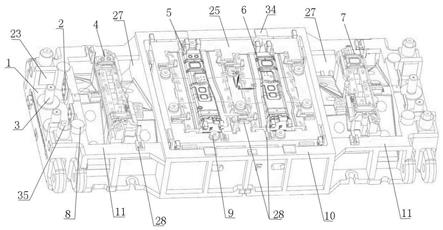
1.本实用新型涉及模具领域,具体涉及一种车辆纵梁角板和大梁加强板同步成型模具。
背景技术:2.车辆纵梁角板和大梁加强板属于结构上有一定相似性,而且挤压成型应力相似的两种零件。现有技术中,这两个零件均是由分开的两组模具分别加工,并不能实现在一组模具中同时实现对这两个零件的加工。而且,现有技术中,这两个零件的拉延成型和切边模具也是分开的两组模具,制造过程麻烦,模具成本高。
技术实现要素:3.本实用新型旨在提供一种车辆纵梁角板和大梁加强板同步成型模具,该车辆纵梁角板和大梁加强板同步成型模具能够同时加工这两个零件,并且将两个零件的拉延成型和切边工序集成在一个模具中进行,大大节约了人力物力。
4.本实用新型的技术方案如下:
5.所述的车辆纵梁角板和大梁加强板同步成型模具,包括上模和下模;
6.所述的下模包括下模座、导向槽、导板ⅰ、导柱、导槽ⅰ、纵梁角板剪边凸模、纵梁角板成型凸模、大梁加强板成型凸模、大梁加强板剪边凸模、侧限位块;
7.所述的下模座顶面的两端的中部分别设有导向槽,所述的导向槽的底面上设有导柱,所述的导向槽的前后侧面上设有导槽ⅰ,所述的导向槽内靠近下模座中心的侧壁上设有导板ⅰ;
8.所述的下模座包括位于中部的凸台座ⅰ和位于凸台座ⅰ左右两侧的侧台座ⅰ,所的凸台座ⅰ的顶面的竖直高度高于侧台座ⅰ顶面的竖直高度;所述的纵梁角板剪边凸模设于左侧的侧台座ⅰ的顶面上,所述的大梁加强板剪边凸模设于右侧的侧台座ⅰ的顶面上,所述的纵梁角板成型凸模、大梁加强板成型凸模分别沿左右方向依次设于凸台座ⅰ的顶面上;所述的侧限位块设有四组,分别设于纵梁角板剪边凸模左侧的下模座的顶面的前后两侧和大梁加强板剪边凸模右侧的下模座的顶面的前后两侧上;所述的纵梁角板剪边凸模、大梁加强板剪边凸模的顶面与纵梁角板成型凸模、大梁加强板成型凸模的顶面齐平;
9.所述的中间限位块设于凸台座ⅰ顶面上,环绕梁角板成型凸模、大梁加强板成型凸模周围间隔均匀设置;
10.所的上模包括上模座、导向板、导板ⅱ、导槽ⅱ、导柱套、纵梁角板剪边凹模、纵梁角板成型凹模、大梁加强板成型凹模、大梁加强板剪边凹模、侧限位导套;
11.所述的上模座底面的两端的中部分别设有对应导向槽的导向板,所述的导向板的左右侧面上设有对应导槽ⅰ的导板ⅱ,导向板靠近下模座中心的侧面上设有对应导板ⅰ的导槽ⅱ,所述的导向板的底面上设有对应导柱的导柱套,所述的导向槽、导向板、导槽ⅰ、导板ⅱ、导板ⅰ、导槽ⅱ、导柱、导柱套共同组成导向上模座移动的导向结构;
12.所述的上模座包括位于中部的凸台座ⅱ和位于凸台座ⅱ左右两侧的侧凸台座ⅱ,所述的凸台座ⅱ和两个侧凸台座ⅱ分别对应凸台座ⅰ和两个侧台座ⅰ设置;所述的纵梁角板剪边凹模设于左侧的侧凸台座ⅱ的底面上,所述的大梁加强板剪边凹模设于右侧的侧凸台座ⅱ的底面上,所述的纵梁角板成型凹模、大梁加强板成型凹模分别沿左右方向依次设于凸台座ⅱ的底面上;所述的所述的纵梁角板剪边凹模、大梁加强板剪边凹模的底面与纵梁角板成型凹模、大梁加强板成型凹模的底面齐平;所述的侧限位导套对应侧限位块设置与上模座的底面上,侧限位块能够嵌套插入侧限位导套中,对合模时的上模和下模起到限位作用。
13.所述的凸台座ⅰ设有压边圈,所述的压边圈整体包裹住纵梁角板成型凸模和大梁加强板成型凸模,所述的凸台座ⅱ的底面上,纵梁角板成型凹模的右侧和前侧边沿上,以及大梁加强板成型凹模的左侧和前侧边沿上分别间隔设有多个迫紧块,在上模和下模合模时,迫紧块和压边圈分别从上下压紧毛坯料板周边。
14.所述的压边圈上围绕纵梁角板成型凸模、大梁加强板成型凸模间隔设有多组定位块用于压住坯料。
15.所述的车辆纵梁角板和大梁加强板同步成型模具,还包括中间限位块和中间限位导套,所述的压边圈上沿其周围边沿间隔设有多组中间限位块;所述的中间限位导套对应中间限位块设置于凸台座ⅱ的底面上,中间限位块能够嵌套插入中间限位导套中,对合模时的上模和下模起到限位作用。
16.所述的凸台座ⅰ上,压边圈的前后两侧分别间隔设有两组盖板,用于限制压边圈的位置。
17.所述的左侧和右侧的侧台座ⅰ的顶面上,纵梁角板剪边凸模的周围和大梁加强板剪边凸模的周围分别设有一圈切边槽,纵梁角板剪边凸模和大梁加强板剪边凸模的切边槽的前后两端分别设有一组定位块,用于压住成型后的坯料边沿;
18.所述的纵梁角板剪边凹模和大梁加强板剪边凹模内分别设有压料板,用于合模时压紧坯料。
19.所述的定位块包括滑座、滑槽、滑块、压杆,所述的滑座固定安装于侧台座ⅰ的顶面上,滑座的顶面设有朝向纵梁角板剪边凸模的或大梁加强板剪边凸模的滑槽,所述的压杆的末端通过滑块安装于滑槽内,能够沿着滑槽滑动至毛坯料板处,压住毛坯料板;所述的滑槽的底面沿其纵向间隔设有多个定位螺孔,所述的滑块上设有一个固定螺孔,通过螺栓旋入固定螺孔和任一定位螺孔中,实现对滑块的定位,同时提供对毛坯料板的压力。
20.所述的车辆纵梁角板和大梁加强板同步成型模具,还包括缓冲器,所述的缓冲器为优力胶制成的圆柱体,竖直设于下模座顶面的四个角处。
21.本实用新型通过巧妙设计的上模座和下模座结构,通过设计较高的凸台座ⅰ,在凸台座ⅰ上设计应力相对较大纵梁角板成型凸模和大梁加强板成型凸模,有效隔离了拉延成型工序号额压边工序,避免相互影响,能够更好的对零件进行拉延成型。成型凸模和切边凸模坐在模座面的落差,也更好的为成型后零件的输送至切边工序提供了便利。
22.本实用新型通过导向槽、导板ⅰ、导柱、导槽ⅰ、导向板、导板ⅱ、导槽ⅱ、导柱套相互配合,形成了更为稳定精确的导向结构,进一步保证了拉延成型的精度和稳定性,同时也满足了本发明存在高起的凸台座ⅰ和较低的侧台座ⅰ存在情况下,成型和切边的精度。
23.本实用新型通过切边槽和定位块,在上下模合模切边工序,能够很好的压住成型后的坯料边沿,结合压料板共同压紧坯料,保证切边稳定准确,避免误差,能够更好的保证精度。
24.本实用新型采用缓冲器,所述的缓冲器在上模和下模合模时,能够起到缓冲作用,有效避免模具损伤。
附图说明
25.图1为本实用新型提供的下模的结构示意图;
26.图2为本实用新型提供的上模的结构示意图;
27.图3为本实用新型提供的定位块的结构示意;
28.图中各部分名称及序号如下:
[0029]1‑
导向槽,2
‑
导板ⅰ,3
‑
导柱,4
‑
纵梁角板剪边凸模,5
‑
纵梁角板成型凸模,6
‑
大梁加强板成型凸模,7
‑
大梁加强板剪边凸模,8
‑
侧限位块,9
‑
中间限位块,10
‑
凸台座ⅰ,11
‑
侧台座ⅰ,12
‑
导向板,13
‑
导板ⅱ,14
‑
导柱套,15
‑
纵梁角板剪边凹模,16
‑
纵梁角板成型凹模,17
‑
大梁加强板成型凹模,18
‑
大梁加强板剪边凹模,19
‑
侧限位导套,20
‑
中间限位导套,21
‑
凸台座ⅱ,22
‑
侧凸台座ⅱ,23
‑
导槽ⅰ,24
‑
导槽ⅱ,25
‑
压边圈,26
‑
迫紧块,27
‑
切边槽,28
‑
定位块,29
‑
压料板,30
‑
滑座,31
‑
滑槽,32
‑
滑块,33
‑
压杆,34
‑
盖板,35
‑
缓冲器。
具体实施方式
[0030]
下面结合附图和实施例具体说明本实用新型。
[0031]
实施例1
[0032]
如图1
‑
3所示,所述的下模包括下模座、导向槽1、导板ⅰ2、导柱3、导槽ⅰ23、纵梁角板剪边凸模4、纵梁角板成型凸模5、大梁加强板成型凸模6、大梁加强板剪边凸模7、侧限位块8;
[0033]
所述的下模座顶面的两端的中部分别设有导向槽1,所述的导向槽1的底面上设有导柱3,所述的导向槽1的前后侧面上设有导槽ⅰ23,所述的导向槽1内靠近下模座中心的侧壁上设有导板ⅰ2;
[0034]
所述的下模座包括位于中部的凸台座ⅰ10和位于凸台座ⅰ10左右两侧的侧台座ⅰ11,所的凸台座ⅰ10的顶面的竖直高度高于侧台座ⅰ11顶面的竖直高度;所述的纵梁角板剪边凸模4设于左侧的侧台座ⅰ11的顶面上,所述的大梁加强板剪边凸模7设于右侧的侧台座ⅰ11的顶面上,所述的纵梁角板成型凸模5、大梁加强板成型凸模6分别沿左右方向依次设于凸台座ⅰ10的顶面上;所述的侧限位块8设有四组,分别设于纵梁角板剪边凸模4左侧的下模座的顶面的前后两侧和大梁加强板剪边凸模7右侧的下模座的顶面的前后两侧上;所述的纵梁角板剪边凸模4、大梁加强板剪边凸模7的顶面与纵梁角板成型凸模5、大梁加强板成型凸模6的顶面齐平;所述的中间限位块9设于凸台座ⅰ10顶面上,环绕梁角板成型凸模5、大梁加强板成型凸模6周围间隔均匀设置;
[0035]
所的上模包括上模座、导向板12、导板ⅱ13、导槽ⅱ24、导柱套14、纵梁角板剪边凹模15、纵梁角板成型凹模16、大梁加强板成型凹模17、大梁加强板剪边凹模18、侧限位导套19;
[0036]
所述的上模座底面的两端的中部分别设有对应导向槽1的导向板12,所述的导向板12的左右侧面上设有对应导槽ⅰ23的导板ⅱ13,导向板12靠近下模座中心的侧面上设有对应导板ⅰ2的导槽ⅱ24,所述的导向板12的底面上设有对应导柱3的导柱套14,所述的导向槽1、导向板12、导槽ⅰ23、导板ⅱ13、导板ⅰ2、导槽ⅱ24、导柱3、导柱套14共同组成导向上模座移动的导向结构;
[0037]
所述的上模座包括位于中部的凸台座ⅱ21和位于凸台座ⅱ21左右两侧的侧凸台座ⅱ21,所述的凸台座ⅱ21和两个侧凸台座ⅱ22分别对应凸台座ⅰ10和两个侧台座ⅰ11设置;所述的纵梁角板剪边凹模15设于左侧的侧凸台座ⅱ22的底面上,所述的大梁加强板剪边凹模18设于右侧的侧凸台座ⅱ22的底面上,所述的纵梁角板成型凹模16、大梁加强板成型凹模17分别沿左右方向依次设于凸台座ⅱ22的底面上;所述的所述的纵梁角板剪边凹模15、大梁加强板剪边凹模18的底面与纵梁角板成型凹模16、大梁加强板成型凹模17的底面齐平;
[0038]
所述的侧限位导套19对应侧限位块8设置与上模座的底面上,侧限位块8能够嵌套插入侧限位导套19中,对合模时的上模和下模起到限位作用。
[0039]
所述的凸台座ⅰ10设有压边圈25,所述的压边圈25整体包裹住纵梁角板成型凸模5和大梁加强板成型凸模6,所述的凸台座ⅱ21的底面上,纵梁角板成型凹模16的右侧和前侧边沿上,以及大梁加强板成型凹模17的左侧和前侧边沿上分别间隔设有多个迫紧块26,在上模和下模合模时,迫紧块26和压边圈25分别从上下压紧毛坯料板周边。
[0040]
所述的压边圈25上围绕纵梁角板成型凸模5、大梁加强板成型凸模6间隔设有多组定位块28用于压住坯料。
[0041]
所述的车辆纵梁角板和大梁加强板同步成型模具,还包括中间限位块9和中间限位导套20,所述的压边圈25上沿其周围边沿间隔设有多组中间限位块9;所述的所述的中间限位导套20对应中间限位块9设置于凸台座ⅱ21的底面上,中间限位块9能够嵌套插入中间限位导套20中,对合模时的上模和下模起到限位作用。
[0042]
所述的凸台座ⅰ10上,压边圈25的前后两侧分别间隔设有两组盖板34,用于限制压边圈25的位置。
[0043]
所述的左侧和右侧的侧台座ⅰ11的顶面上,纵梁角板剪边凸模4的周围和大梁加强板剪边凸模7的周围分别设有一圈切边槽27,纵梁角板剪边凸模4和大梁加强板剪边凸模7的切边槽27的前后两端分别设有一组定位块28,用于压住成型后的坯料边沿;
[0044]
所述的纵梁角板剪边凹模15和大梁加强板剪边凹模18内分别设有压料板29,用于合模时压紧坯料。
[0045]
所述的定位块28包括滑座30、滑槽31、滑块32、压杆33,所述的滑座30固定安装于侧台座ⅰ11的顶面上,滑座30的顶面设有朝向纵梁角板剪边凸模4的或大梁加强板剪边凸模7的滑槽31,所述的压杆33的末端通过滑块32安装于滑槽31内,能够沿着滑槽31滑动至毛坯料板处,压住毛坯料板;所述的滑槽31的底面沿其纵向间隔设有多个定位螺孔,所述的滑块32上设有一个固定螺孔,通过螺栓旋入固定螺孔和任一定位螺孔中,实现对滑块32的定位,同时提供对毛坯料板的压力。
[0046]
所述的车辆纵梁角板和大梁加强板同步成型模具,还包括缓冲器35,所述的缓冲器35为优力胶制成的圆柱体,竖直设于下模座顶面的四个角处。