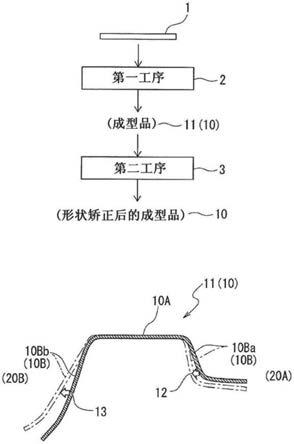
1.本发明涉及提供由是部件形状构成的成型品(冲压部件)的技术,该部件形状是截面礼帽型形状,且具有沿着顶板部的长度方向以在俯视观察时向顶板部的宽度方向的一方凸出的方式弯曲的弯曲部。需要说明的是,上述部件形状的截面礼帽型形状可以具有与纵壁部连续的凸缘部,也可以没有凸缘部。
背景技术:2.近年来,为了车身的轻量化、碰撞安全性提高,汽车的车身骨架部件被要求超高抗拉强度件的应用。但是,超高抗拉强度件缺乏延展性,因此容易产生裂纹。而且,超高抗拉强度件由于强度高,所以具有由褶皱、回弹引起的尺寸精度的不良变大的倾向。
3.另外,前柱、梁部件等车身部件是具有顶板部和与其连续的纵壁部及凸缘部的礼帽型截面形状且在长度方向上弯曲的形状的成型品。这样的形状的成型品因回弹(弹性恢复)而不仅是截面的变化,也容易产生部件长度方向的端部抬起或下沉之类的长度方向的翘曲,或者产生部件端部的截面相对于部件长度中央的截面扭转之类的不良。而且,由于是在长度方向上长条的部件形状,所以即使在长度方向中央附近是小的翘曲、扭转之类的小的尺寸精度不良,在部件长度方向端部也会成为大的翘曲、扭转。因而,如上所述的部件形状的成型品具有尺寸精度的确保非常困难的倾向。
4.作为这样的具有礼帽型截面且沿着长度方向弯曲的长条部件的尺寸精度不良对策,提出了一些技术。
5.例如在专利文献1中提出了以下的冲压成型方法:对于具有礼帽型截面且在长度方向上弯曲的长条部件,通过将弯曲内侧(弯曲部凹侧)的凸缘部在第一成型工序中小幅折弯,进一步在第二工序中直到成为产品形状为止追加折弯,从而使成为部件端部的扭转的要因的应力降低。
6.另外,在专利文献2中提出了以下的冲压成型方法:在冲压成型前的金属板设置余壁部,通过在冲压成型中将上述余壁部向纵壁部成型部钩挂,来促进金属板的面内的材料旋转而使成为扭转、长度方向的翘曲的要因的应力降低。
7.现有技术文献
8.专利文献
9.专利文献1:日本专利第5382281号公报
10.专利文献2:日本专利第6376048号公报
技术实现要素:11.发明所要解决的课题
12.但是,在专利文献1所记载的冲压成型方法中,能够降低成为扭转的要因的在长度方向弯曲部的凹侧(弯曲内侧)的凸缘部产生的长度方向板厚中心的拉伸应力。但是,在专利文献1所记载的方法中,降低部件长度方向的翘曲的效果小。
13.另外,在专利文献2所记载的冲压成型方法中,由于在成型前的金属板设置余壁部,所以存在材料的成品率恶化这一问题。而且,将余壁部钩挂于纵壁部的状态下的成型在考虑了通过冲压成型的量产的情况下成为非常不稳定的状态下的处理。另外,在这样的方法中,若冲压成型前的金属板的放置位置、金属板与模具之间的摩擦系数变动,则向金属板赋予的面内的旋转量会变动,因此尺寸精度的改善量也会变动。
14.本发明着眼于如上所述的课题而完成,目的在于抑制由部件形状构成的成型品中的长度方向的翘曲、扭转,上述部件形状是截面礼帽型形状,且具有沿着顶板部的长度方向以在俯视观察时向顶板部的宽度方向的一方凸出的方式弯曲的弯曲部。
15.用于解决课题的手段
16.若从成为材料的金属板冲压成型部件形状的成型品,该部件形状是具有顶板部和与其连续的纵壁部及凸缘部的截面礼帽型形状,且具有沿着上述顶板部的长度方向以在俯视观察时向上述顶板部的宽度方向的一方凸出的方式弯曲的弯曲部,则在将模具脱模时,在成型品产生回弹。本发明人关于因将该模具脱模时产生的回弹而部件长度方向端部抬起或下沉之类的截面的翘曲的抑制和抑制了与其联动地产生的截面的扭转的冲压成型的方法进行了锐意研究。该研究的结果,发明人得到了以下见解:通过根据部件长度方向端部的由回弹引起的翘曲方向而以使长度方向弯曲部的凹侧(内侧)及弯曲部的凸侧(外侧)的纵壁部相对于顶板部所成的角度变化的方式矫正形状,能够向抑制部件端部的由回弹引起的翘曲的方向冲压成型。本发明基于这样的见解而完成。
17.即,为了解决课题,本发明的一方案是冲压部件的制造方法,将金属板冲压成型为目的的部件形状而制造成型品,该目的的部件形状是纵壁部经由折弯部而与顶板部的宽度方向两侧连续的截面礼帽型形状且具有沿着上述顶板部的长度方向以在俯视观察时向上述顶板部的宽度方向的一方凸出的方式弯曲的弯曲部的部件形状,其主旨在于,包括使用第一模具将金属板冲压成型为上述部件形状的第一工序和使用第二模具对上述第一工序后的成型品进行冲压成型的第二工序,在将从上述第一模具脱模后的成型品的部件形状设为了第一部件形状时,在因由从上述第一模具的脱模引起的弹性恢复而部件长度方向端部向上述顶板部的表面侧抬起的情况下,在第二工序中执行进行第一成型及第二成型中的至少一方的成型的冲压成型,上述第一成型使在上述弯曲部的凹侧处上述纵壁部相对于上述顶板部所成的角度比上述第一部件形状小,上述第二成型使在上述弯曲部的凸侧处上述纵壁部相对于上述顶板部所成的角度比上述第一部件形状大,在因由从上述第一模具的脱模引起的弹性恢复而部件长度方向端部向上述顶板部的背面侧下沉的情况下,在第二工序中执行进行第三成型及第四成型中的至少一方的成型的冲压成型,上述第三成型使在上述弯曲部的凹侧处上述纵壁部相对于上述顶板部所成的角度比上述第一部件形状大,上述第四成型使在上述弯曲部的凸侧处上述纵壁部相对于上述顶板部所成的角度比上述第一部件形状小。
18.另外,本发明的其他的方案是形状矫正用模具,该形状矫正用模具是利用第一模具冲压成型为部件形状的成型品的形状矫正用的模具,该部件形状是纵壁部经由折弯部而与顶板部的宽度方向两侧连续的截面礼帽型形状,且具有沿着上述顶板部的长度方向以在俯视观察时向上述顶板部的宽度方向的一方凸出的方式弯曲的弯曲部,并且,上述形状矫正用模具是因由从上述第一模具的脱模引起的弹性恢复而部件长度方向端部向上述顶板
部的表面侧抬起的情况下的形状矫正用模具,其主旨在于,将位于上述弯曲部的凹侧的上述折弯部的至少一部分成型的部分的从上述顶板部去往上述纵壁部的模具成型面的形状为与上述第一模具不同的形状。
19.另外,本发明的其他的方案是形状矫正用模具,该形状矫正用模具是利用第一模具冲压成型为部件形状的成型品的形状矫正用的模具,该部件形状是纵壁部经由折弯部而与顶板部的宽度方向两侧连续的截面礼帽型形状,且具有沿着上述顶板部的长度方向以在俯视观察时向上述顶板部的宽度方向的一方凸出的方式弯曲的弯曲部,并且,上述形状矫正用模具是因由从上述第一模具的脱模引起的弹性恢复而部件长度方向端部向上述顶板部的背面侧下沉的情况下的形状矫正用模具,其主旨在于,将位于上述弯曲部的凸侧的上述折弯部的至少一部分成型的部分的从上述顶板部去往上述纵壁部的模具成型面的形状为与上述第一模具不同的形状。
20.在此,在本说明书中,纵壁部相对于顶板部所成的角度是钝角侧的角度,是指顶板部的背面与纵壁部的内表面所成的角度。
21.发明效果
22.根据本发明的方案,在通过冲压成型制造了由部件形状构成的成型品,该部件形状是截面礼帽型形状且具有沿着顶板部的长度方向以在俯视观察时向顶板部的宽度方向的一方凸出的方式弯曲的弯曲部时,能够抑制在该冲压部件产生的长度方向的翘曲、扭转。
附图说明
23.图1是示出基于本发明的实施方式的成型品的部件形状的图,(a)示出立体图,(b)示出俯视图,(c)示出图1(b)的弯曲部位置处的a
‑
a
′
剖视图。
24.图2是说明基于本发明的实施方式的制造方法的工序的图。
25.图3是示出拉拔成型用的模具的例子的图。
26.图4是说明拉拔成型的处理例的图。
27.图5是示出折弯成型用的模具的例子的图。
28.图6是说明折弯成型的处理例的图。
29.图7是说明第一工序后的成型品(成型品11)的状态的图。
30.图8是说明第一工序的第一模具(a)与第二工序的第二模具(b)的关系的示意图。
31.图9是说明相对于第一翘曲模式的第二工序的处理例的。
32.图10是说明将折弯部的截面形状设为了在多处阶段性地折弯的形状的例子的图。
33.图11是说明相对于第二翘曲模式的第二工序的处理例的。
34.图12是说明使弯曲部凸侧的纵壁部以打开的方式变形时的作用的图。
35.图13是说明使弯曲部凸侧的纵壁部以打开的方式变形时的作用的图。
36.图14是说明使弯曲部凹侧的纵壁部以打开的方式变形时的作用的图。
37.图15是说明使弯曲部凹侧的纵壁部以打开的方式变形时的作用的图。
38.图16是说明增大了位于弯曲部的折弯部的曲率半径时的作用的图。
39.图17是说明减小了位于弯曲部的折弯部的曲率半径时的作用的图。
40.图18是说明使折弯部的截面形状变形成在多处阶段性地折弯的形状时的作用的图。
41.图19是示出实施例中的成型品的部件形状的图,(a)示出立体图,(b)示出俯视图,(c)示出图1(b)的弯曲部位置处的a
‑
a
′
剖视图。
42.图20是示出实施例中的再成型用的模具的截面形状的图。
43.图21是示出实施例中的再成型用的模具的其他的截面形状的图。
44.图22是示出使用了图20的模具的情况下的截面形状的变化的图。
45.图23是示出使用了图21的模具的情况下的截面形状的变化的图。
具体实施方式
46.接着,参照附图来对本发明的实施方式进行说明。
47.本实施方式是以下技术的说明:将金属板1冲压成型为如图1所示的是纵壁部10b经由折弯部10d而在顶板部10a的宽度方向两侧连续的截面礼帽型形状且具有沿着上述顶板部10a的长度方向以在俯视观察时向上述顶板部10a的宽度方向的一方凸出的方式弯曲的弯曲部20的部件形状(以下,也记载为长条弯曲部件形状),制造由设为目的的成型品10构成的冲压部件的。长条是指与顶板部的宽度相比长度方向的长度长。
48.在以下的说明中,以将如图1所示的由在纵壁部10b的端部具有凸缘部10c的截面礼帽型形状的长条弯曲部件形状构成的成型品10作为目的的成型品10来制造的情况为例进行说明。不过,本发明即使是由不具有凸缘部10c的截面礼帽型形状的长条弯曲部件形状构成的成型品的制造也能够应用。另外,制造出的成型品10可以是最终产品也可以是中间品。
49.在本实施方式中,作为冲压工序,如图2所示,至少具备第一工序2和第一工序2后的第二工序3。
50.<金属板1>
51.被冲压成型的金属板1例如是成为了将设为目的的成型品10的部件形状展开后的坯料形状的金属板1。但是,若是成品率被容许的范围内,则也可以将比部件形状所需的面积大的面积的金属板1作为坯件(被冲压成型的金属板1)来应用。金属板1的形状没有特别的限定。
52.本实施方式尤其能够在将由拉伸强度为440mpa以上(优选为980mpa以上)的钢板(高抗拉强度件)构成的金属板1冲压成型为长条弯曲部件形状时使用。在该情况下,能够更有效地降低尺寸精度不良。
53.<第一工序2>
54.在第一工序2中,进行将金属板1(坯件)使用第一模具而冲压成型为上述的部件形状的处理。在此,也存在将设为目的的成型品10通过多阶段的冲压工序来制作的情况。在该情况下,例如,能够将多阶段的冲压工序的最后的冲压工序设为第一工序2。这样,也可以作为第一工序2的前处理而具有1个或2个以上的其他的冲压工序。
55.<模具及冲压成型方法>
56.在第一工序2的冲压成型中,例如采用拉拔成型或折弯成型。
57.在第一工序2是拉拔成型的情况下,第一模具成为例如如图3所示的结构。在图3中,第一模具由由凹模50构成的上模和由冲头51及坯料保持器52构成的下模构成。并且,如图4所示,在该例子的拉拔成型中,从在成型前将金属板1载置于坯料保持器52上的状态(参
照图4(a))起成型开始。在该状态下凹模50下降而由凹模50和坯料保持器52夹着金属板1(参照图4(b))。之后,一边向与坯料保持器42的冲压方向对向的方向施加压力,一边进一步使凹模50下降(参照图4(c)),通过最终到达下止点而加工完成(参照图4(d))。
58.在第一工序2是折弯成型的情况下,第一模具成为例如如图5所示的结构。在图5中,第一模具由由凹模55及垫57构成的上模和由冲头56构成的下模构成。并且,如图6所示,在该例子的折弯成型中,从在成型前将金属板1载置于冲头56上的状态(参照图6(a))起成型开始。在该状态下,上模下降,部件的顶板部10a由垫57和冲头56夹着(参照图6(b))。之后,一边施加与垫57的冲压方向相同的方向的压力,一边进一步使上模下降(参照图6(c)),通过最终到达下止点而加工完成(参照图6(c))。
59.在此,在第二工序3中,使用与如图5所示的模具同样的折弯成型用的模具,通过折弯成型来进行冲压成型。
60.<第二工序3>
61.在第二工序3中,进行将第一工序2后的成型品10使用第二模具而冲压成型而对成型品11(冲压部件)实施形状矫正的处理。即,在第二工序3中,进行用于矫正在从第一模具脱模后的部件形状(也记载为第一部件形状)的成型品10因由从第一模具的脱模引起的弹性恢复而产生的部件长度方向的翘曲的冲压成型。在第二工序3中使用的第二模具构成型状矫正用模具。
62.接着,对第二工序3中的冲压成型进行说明。
63.在第二工序3中,如图7(c)所示,判定因由从第一模具的脱模引起的弹性恢复而在由第一部件形状构成的成型品11产生的翘曲是第一翘曲模式h还是第二翘曲模式l。第一翘曲模式h是部件长度方向端部向顶板部10a的表面侧10aa抬起的翘曲模式。第二翘曲模式l是部件长度方向端部向顶板部10a的背面侧10ab下沉的翘曲模式。并且,在第二工序3中,根据翘曲模式是第一翘曲模式h还是第二翘曲模式l,作为使用的第二模具而使用不同的模具。在此,由弹性恢复引起的翘曲的模式能够通过成型解析、实际实施了第一工序2的处理的实施品而事先决定。
64.在此,在以后的说明中,关于第一工序2中的第一模具与第二工序3中的第二模具的关系,参照图8来说明。图8所示的模具是示意性地图示了上模的凹模的成型面(模具内的形状)的图,下模的冲头的成型面成为了与凹模的成型面同样的形状。图8(a)示出第一模具60,标号60a是与顶板部10a的表面抵接的成型面,标号60b是与纵壁部10b抵接的成型面,标号60d是将折弯部10d成型的成型面。图8(b)示出第二模具61,标号61a是与顶板部10a的表面抵接的成型面,标号61b是与纵壁部10b抵接的成型面,标号61d是将折弯部10d成型的成型面。需要说明的是,向顶板部10a的抵接也包括经由垫而抵接的情况。
65.将第一工序2结束且脱模后的成型品10的形状也记载为第一部件形状。
[0066]“第一翘曲模式h的情况”[0067]
在第一工序2的冲压成型中因由从第一模具的脱模引起的弹性恢复而在由第一部件形状构成的成型品11产生了部件长度方向端部向顶板部10a的表面侧10aa抬起的第一翘曲模式h的情况下,在第二工序3中,对成型品11进行接下来的冲压成型。
[0068]
即,如图9所示,在第二工序3中,执行进行第一成型(图9中标号12的处理)及第二成型(图9中标号13的处理)中的至少一方的成型的冲压成型。第一成型(图9中标号12的处
理)进行使由第一部件形状构成的长条弯曲部件形状中的弯曲部20的凹侧20a的纵壁部10ba相对于顶板部10a所成的角度比第一部件形状小的成型。第二成型(图9中标号13的处理)进行使由第一部件形状构成的长条弯曲部件形状中的弯曲部20的凸侧20b的纵壁部10bb相对于顶板部10a所成的角度比第一部件形状大的成型。
[0069]
(1)关于第一成型(图9中标号12的处理)
[0070]
(1
‑
1)第一成型的第一方法
[0071]
作为第一成型,将位于弯曲部20的凹侧20a的顶板部10a与纵壁部10ba之间的折弯部10d的至少一部分的折弯部10d的曲率半径以与第一工序2中的曲率半径不同的半径成型。
[0072]
在该情况下,例如,作为第二模具,采用将位于弯曲部20的凹侧20a的折弯部10d的至少一部分成型的部分的模具成型面61d的曲率半径r2a成为了与第一模具中的将位于弯曲部20的凹侧20a的折弯部10d的至少一部分成型的部分的模具成型面60d的曲率半径r1a不同的半径的模具。
[0073]
在此,在本说明书中,“折弯部10d的至少一部分”是指位于弯曲部20的折弯部10d中的部件长度方向的一部分。一部分优选将弯曲部20的折弯部10d的1/4以上(优选是全域)的折弯部10d设为对象。在以下的说明中也是同样。
[0074]
另外,在本说明书中,“曲率半径”是将从顶板部10a去往纵壁部10b的折弯部10d成型的面的曲率半径。
[0075]
需要说明的是,将折弯部10d等成型的模具由上模和下模构成,通过利用上模和下模将金属板1夹入而成型。因而,成型面存在于上模(凹模)和下模(冲头)双方,但折弯部10d成型面的形状成为大致同一形状,因此不管是哪个成型面都行。在假设对向的上模的成型面和下模的成型面是不同的截面形状的情况下,针对上模和下模分别变更截面形状来应对即可。在以下的成型中也是同样。
[0076]
另外,上述的曲率半径不同是指:可以是比第一模具中的曲率半径大的半径,也可以是比第一模具中的曲率半径小的半径。
[0077]
如后所述,作为第二模具的形状,使用将上述的折弯部10d的至少一部分成型的部分的模具成型面的曲率半径r2a与第一模具的形状不同的模具,利用该第二模具进行冲压成型。由此,能够以使弯曲部20的凹侧20a的纵壁部10b相对于顶板部10a所成的角度比第一部件形状小的方式成型。其结果,如后所述,向顶板部10a的表面侧10aa抬起的长度方向的翘曲被矫正。
[0078]
此时,优选第一模具中的与纵壁部10b抵接的成型面相对于与顶板部10a抵接的成型面所成的角度αa、αb和第二模具中的与纵壁部10b抵接的成型面相对于与顶板部10a抵接的成型面所成的角度βa、βb构成为相同的角度。
[0079]
例如,关于将上述折弯部10d的至少一部分成型的部分的模具成型面以外,将第二模具的成型面设为与第一模具的成型面相同的面形状。不过,也可以使与纵壁部10b抵接的成型面相对于与顶板部10a抵接的成型面所成的角度βa、βb以外的成型面的形状与第一模具不同。
[0080]
(1
‑
2)第一成型的第二方法
[0081]
作为第一成型,关于位于弯曲部20的凹侧20a的顶板部10a与纵壁部10ba之间的折
弯部10d的至少一部分,成型为从顶板部10a朝向纵壁部10b在多处阶段性地折弯的形状。例如,作为第二模具的成型面,将将位于弯曲部20的凹侧20a的顶板部10a与纵壁部10b之间的折弯部10d的至少一部分成型的部分的模具成型面的形状设为从顶板部10a朝向纵壁部10b在多处阶段性地折弯的面形状。并且,采用与第一模具中的将位于弯曲部20的凹侧20a的顶板部10a与纵壁部10ba之间的折弯部10d的至少一部分成型的部分的模具成型面的形状不同的模具。
[0082]
从顶板部10a朝向纵壁部10b在多处阶段性地折弯的形状例如通过如图10所示那样将第一模具中的上述折弯部10d的圆弧状的截面形状60d变更为倒角后的倒角形状61d来实现。在该情况下,成为从顶板部10a朝向纵壁部10b在2处阶段性地折弯的形状。
[0083]
如后所述,作为第二模具,使用折弯部10d的形状从第一模具的折弯部10d的圆弧状的形状变更为在多处阶段性地折弯的形状的模具,利用该第二模具进行冲压成型。由此,能够以使弯曲部20的凹侧20a的纵壁部10b相对于顶板部10a所成的角度比第一部件形状小的方式成型。其结果,如后所述,向顶板部10a的表面侧10aa抬起的翘曲被矫正。
[0084]
此时,优选第一模具中的与纵壁部10b抵接的成型面相对于与顶板部10a抵接的成型面所成的角度αa、αb和第二模具中的与纵壁部10b抵接的成型面相对于与顶板部10a抵接的成型面所成的角度βa、βb构成为相同的角度。
[0085]
例如,关于将上述折弯部10d的至少一部分成型的部分的模具成型面以外,第二模具的成型面设为与第一模具的成型面相同的面形状。不过,也可以使与纵壁部10b抵接的成型面相对于与顶板部10a抵接的成型面所成的角度以外的成型面的形状与第一模具不同。
[0086]
(1
‑
3)第一成型的第三方法
[0087]
作为第一成型,使用关于将位于弯曲部20的凹侧20a的纵壁部10b的部分中的长度方向的至少一部分的纵壁部10b成型的第二模具的成型面与利用第一模具将同一部位成型的成型面处的角度αa相比减小了与纵壁部10b抵接的成型面相对于与顶板部10a抵接的成型面的角度βa的第二模具来成型。
[0088]
(2)关于第二成型(图9中标号13的处理)
[0089]
作为第二成型,使用关于将位于弯曲部20的凸侧20b的纵壁部10b的部分中的长度方向的至少一部分的纵壁部10b成型的第二模具的成型面处的角度αb与利用第一模具将同一部位成型的成型面相比增大了与纵壁部10b抵接的成型面相对于与顶板部10a抵接的成型面的角度βb的第二模具来成型。
[0090]
或者,作为第二成型,也可以将位于弯曲部20的凸侧20b的顶板部10a与纵壁部10b之间的折弯部10d的至少一部分的折弯部10d的截面形状设为与第一工序2中的截面形状不同的形状,以使弯曲部20的凸侧20b的纵壁部10b相对于顶板部10a所成的角度比第一部件形状大的方式成型。如后所述,通过调整上述截面形状,能够向纵壁部10b打开的方向变形。
[0091]“第二翘曲模式的情况l”[0092]
在第一工序2的冲压成型中因由从第一模具的脱模引起的弹性恢复而在由第一部件形状构成的成型品10产生了部件长度方向端部向上述顶板部10a的背面侧10ab下沉的第二翘曲模式l的情况下,在第二工序3中,对第一部件形状的成型品10进行以下的冲压成型。
[0093]
即,如图11所示,在第二工序3中,进行第三成型(图11中标号14的处理)及第四成型(图11中标号15的处理)中的至少一方的成型。第三成型(图11中标号14的处理)进行使第
一部件形状的长条弯曲部件形状中的弯曲部20的凹侧20a的纵壁部10ba相对于顶板部10a所成的角度比第一部件形状大的成型。第四成型(图11中标号15的处理)进行使第一部件形状的长条弯曲部件形状中的弯曲部20的凸侧20b的纵壁部10bb相对于顶板部10a所成的角度比第一部件形状小的成型。
[0094]
(1)关于第三成型(图11中标号14的处理)
[0095]
作为第三成型,使用关于将位于弯曲部20的凹侧20a的纵壁部10ba的部分中的长度方向的至少一部分的纵壁部10b成型的第二模具的成型面与利用第一模具将同一部位成型的成型面相比增大了与纵壁部10b抵接的成型面相对于与顶板部10a抵接的成型面的角度βa的第二模具来成型。
[0096]
或者,作为第二成型,也可以将位于弯曲部20的凹侧20a的顶板部10a与纵壁部10ba之间的折弯部10d的至少一部分的折弯部10d的截面形状设为与第一工序2中的截面形状不同的形状,使弯曲部20的凸侧20b的纵壁部10bb相对于顶板部10a所成的角度比第一部件形状大。如后所述,通过调整上述截面形状,能够向纵壁部10b打开的方向变形。
[0097]
(2)关于第四成型(图11中标号15的处理)
[0098]
(2
‑
1)第四成型的第一方法
[0099]
作为第四成型,将位于弯曲部20的凸侧20b的顶板部10a与纵壁部10bb之间的折弯部10d的至少一部分的曲率半径r2b以与第一工序2中的曲率半径不同的半径成型。
[0100]
在该情况下,例如,作为第二模具,采用将位于弯曲部20的凸侧20b的折弯部10d的至少一部分成型的部分的模具成型面的曲率半径r2b成为了与第一模具中的将位于弯曲部20的凸侧20b的折弯部10d的至少一部分成型的部分的模具成型面的曲率半径r1b不同的半径的模具。
[0101]
如后所述,作为第二模具的形状,使用将上述的折弯部10d的至少一部分成型的部分的模具成型面的曲率半径r2b与第一模具的形状不同的模具,通过利用该第二模具进行冲压成型,能够以使弯曲部20的凸侧20b的纵壁部10bb相对于顶板部10a所成的角度比第一部件形状小的方式成型。由此,如后所述,向顶板部10a的背面侧10ab下沉的长度方向的翘曲被矫正。
[0102]
此时,优选第一模具中的与纵壁部10b抵接的成型面相对于与顶板部10a抵接的成型面所成的角度和第二模具中的与纵壁部10b抵接的成型面相对于与顶板部10a抵接的成型面所成的角度构成为相同。
[0103]
例如,关于将上述折弯部10d的至少一部分成型的部分的模具成型面以外,将第二模具的成型面设为与第一模具的成型面相同的面形状。不过,也可使与纵壁部10b抵接的成型面相对于与顶板部10a抵接的成型面所成的角度βa、βb以外的成型面的形状与第一模具不同。
[0104]
(2
‑
2)第四成型的第二方法
[0105]
作为第一成型,关于位于弯曲部20的凸侧20b的顶板部10a与纵壁部10bb之间的折弯部10d的至少一部分,成型为从顶板部10a朝向纵壁部10b在多处阶段性地折弯的形状。例如,作为第二模具,采用将位于弯曲部20的凸侧20b的顶板部10a与纵壁部10bb之间的折弯部10d的至少一部分成型的部分的模具成型面设为从顶板部10a朝向纵壁部10b在多处阶段性地折弯的面形状且与第一模具中的将位于弯曲部20的凸侧20b的顶板部10a与纵壁部
10bb之间的折弯部10d的至少一部分成型的部分的模具成型面的形状不同的模具。
[0106]
从顶板部10a朝向纵壁部10b在多处阶段性地折弯的形状例如通过如图10所示那样将第一模具中的上述折弯部10d的圆弧状的截面形状变更为倒角后的倒角形状来实现。在该情况下,成为从顶板部10a朝向纵壁部10b在2处阶段性地折弯的形状。
[0107]
如后所述,作为第二模具,使用折弯部10d的形状从第一模具的折弯部10d的圆弧状的形状变更为在多处阶段性地折弯的形状的模具,利用该第二模具进行冲压成型。由此,以使弯曲部20的凸侧20b的纵壁部10bb相对于顶板部10a所成的角度比第一部件形状小的方式成型。其结果,如后所述,向顶板部10a的表面侧10aa抬起的翘曲被矫正。
[0108]
此时,优选第一模具中的与纵壁部10b抵接的成型面相对于与顶板部10a抵接的成型面所成的角度和第二模具中的与纵壁部10b抵接的成型面相对于与顶板部10a抵接的成型面所成的角度构成为相同的角度。
[0109]
例如,关于将上述折弯部10d的至少一部分成型的部分的模具成型面以外,第二模具的成型面设为与第一模具的成型面相同的面形状。不过,也可以使与纵壁部10b抵接的成型面相对于与顶板部10a抵接的成型面所成的角度以外的成型面的形状与第一模具不同。
[0110]
(2
‑
3)第四成型的第三方法
[0111]
作为第一成型,使用关于将位于弯曲部20的凸侧20b的纵壁部10bb的部分中的长度方向的至少一部分的纵壁部10b成型的第二模具的成型面与利用第一模具将同一部位成型的成型面相比减小了与纵壁部10b抵接的成型面相对于与顶板部10a抵接的成型面的角度βb的第二模具来成型。
[0112]
在此,在上述的说明中,作为第一成型的第一、第二方法及第四成型的第一、第二方法中的在第二工序3和第一工序2中使折弯部10d的截面形状不同的方法,例示了改变圆弧的曲率半径的方法和变更为阶段性地折弯的截面形状的情况。在第二工序3和第一工序2中折弯部10d的截面形状设为不同的形状的方法不限定于此。只要是在与第一模具的关系中向纵壁部10b关闭的方向位移的力矩产生于折弯部10d的截面形状即可,没有特别的限定。即使在第二成型及第三成型中对第一模具改变截面形状的情况下也是同样。
[0113]
<作用及其他>
[0114]
若将金属板1冲压成型为上述的长条弯曲部件形状后将模具脱模,则如图7那样,相对于成型品11,不仅是图7(b)那样的由回弹引起的截面的变化,也产生图7(c)那样的部件长度方向的端部抬起或下沉之类的长度方向的翘曲,或者如图7(d)那样部件端部的截面相对于部件长度中央的截面扭转,成型品10的尺寸精度恶化。
[0115]
即,如图7(b)所示,若着眼于部件的截面形状,则例如因在处于顶板部10a与纵壁部10b的边界的折弯部10d产生的角度变化、纵壁部10b的翘曲而产生截面打开的回弹。而且,如图7(c)那样,根据部件形状,因弹性恢复而向部件的两端抬起或下沉的方向产生长度方向的翘曲。而且,如图7(d)那样,若部件长度方向的弯曲的外侧和内侧的长度方向的翘曲的平衡失衡,则仅顶板部10a的一方在长度方向上翘曲,由此,在部件的两端附近有可能产生表观上扭转。
[0116]
如以上那样,在冲压成型为上述的长条弯曲部件形状的情况下,部件的尺寸精度恶化。
[0117]
相对于此,在本实施方式中,通过在第二工序3中进行用于形状矫正的冲压成型,
长度方向的翘曲被抑制,伴随于此,部件的两端附近的表观上扭转也降低。
[0118]
即,在本实施方式中,在因第一工序2的成型而对图7所示的具有礼帽型截面且在长度方向上弯曲的成型品11产生了长度方向的翘曲及扭转时,通过在第二工序3中以向打开或关闭长度方向弯曲部20的凹侧20a(内侧)及凸侧20b(外侧)的至少一方的纵壁部10b的方向成型的方式进行控制,长度方向的翘曲被抑制,伴随于此,部件的两端附近的表观上扭转也降低。
[0119]
[翘曲抑制的机制]
[0120]
以下说明该翘曲抑制的机制。
[0121]
在图12~图15中示出是具有顶板部10a和与其连续的纵壁部10b的礼帽型截面形状且在长度方向上弯曲的简易的长条弯曲部件形状。在该形状中,为了使说明简易,设为沿着长度方向的全长只是弯曲部20的情况。另外,在该简易的部件形状中不存在凸缘部10c,但可以认为:在存在凸缘部10c的情况下,出现的现象也是同样。
[0122]
(1)将弯曲部20的凸侧20b的纵壁部10bb相对于顶板部10a的角度增大变形的情况
[0123]
如图12那样,考虑弯曲部20的凸侧20b的纵壁部10bb向截面打开的方向(相对于顶板部10a的角度变大的方向)进行了变形的情况。在如图12(a)(b)那样弯曲部20的凸侧20b的纵壁部10bb向打开的方向进行了变形的情况下,纵壁部10bb的端部(下端)若长度方向的线长不增加则在几何学上不成立(参照图12(c)的左图)。但是,由于纵壁部10bb端部的线长在变形前后不变化,所以在表观上,纵壁部10bb端部成为在长度方向上被收缩的变形(参照图12(c)的右图)。此时,在纵壁部10bb的截面向打开的方向变形时,若纵壁部10bb端部向收缩的方向变形,则纵壁部10bb上部及顶板部10a被该变形拖拽而要伸展,因此,作为结果,部件长度方向的两端向下沉的方向变形(参照图12(c)的右图)。
[0124]
这样,通过在第二工序3中向弯曲部20的凸侧20b的纵壁部10bb相对于顶板部10a所成的角度变大的方向变形,能够矫正抬起方向的长度方向的翘曲。需要说明的是,由于是长条且弯曲的形品,所以即使在折弯部10d的纵壁部10bb产生1度左右的角度变化,也能够大幅矫正长度方向的翘曲。
[0125]
(2)将凸侧20b的纵壁部10bb相对于顶板部10a的角度减小变形的情况
[0126]
如图13那样,考虑长度方向弯曲部20的凸侧20b的纵壁部10bb向截面关闭的方向(相对于顶板部10a的角度变小的方向)进行了变形的情况。在如图13(a)(b)那样弯曲部20的凸侧20b的纵壁部10bb向关闭的方向进行了变形的情况下,纵壁部10bb的端部若长度方向的线长不减少则在几何学上不成立(参照图13(c)的左图)。但是,由于纵壁部10bb端部的线长在变形前后不变化,所以在表观上,纵壁部10bb端部成为被伸展的变形(参照图13(c)的右图)。此时,在将纵壁部10bb向截面关闭的方向变形时,若纵壁部10bb端部向伸展的方向变形,则纵壁部10bb上部及顶板部10a被该变形拖拽而要收缩,因此,作为结果,部件长度方向的两端向抬起的方向变形(参照图13(c)的右图)。
[0127]
这样,通过在第二工序3中在弯曲部20的凸侧20b向纵壁部10bb相对于顶板部10a所成的角度变小的方向变形,能够矫正下沉的方向的长度方向的翘曲。需要说明的是,由于是长条且弯曲的形品,所以即使在折弯部10d的纵壁部10bb产生1度左右的角度变化,也能够大幅矫正长度方向的翘曲。
[0128]
(3)将凹侧20a的纵壁部10ba相对于顶板部10a的角度增大变形的情况
[0129]
如图14所示,考虑长度方向弯曲部20的凹侧20a的纵壁部10ba向截面打开的方向(相对于顶板部10a的角度变大的方向)进行了变形的情况。在弯曲部20的凹侧20a的纵壁部10ba向打开的方向进行了变形的情况下,纵壁部10ba的端部若长度方向的线长不减少则在几何学上不成立(参照图14(c)的左图)。但是,由于纵壁部10ba端部的线长在变形前后不变化,所以在表观上,纵壁部10ba端部成为被伸展的变形(参照图14(c)的右图)。此时,在将纵壁部10ba向截面打开的方向进行了变形时,若纵壁部10ba端部向伸展的方向变形,则纵壁部10ba上部及顶板部10a被该变形拖拽而要收缩,因此,作为结果,部件的两端向抬起的方向变形(参照图14(c)的右图)。
[0130]
这样,通过在第二工序3中在弯曲部20的凹侧20a向纵壁部10ba相对于顶板部10a所成的角度变大的方向变形,能够矫正下沉的方向的长度方向的翘曲。需要说明的是,由于是长条且弯曲的形品,所以即使在折弯部10d的纵壁部10ba产生1度左右的角度变化,也能够大幅矫正长度方向的翘曲。
[0131]
(4)将凹侧20a的纵壁部10ba相对于顶板部10a的角度减小变形的情况
[0132]
如图15所示,考虑长度方向弯曲部20的凹侧20a的纵壁部10ba向截面关闭的方向(相对于顶板部10a的角度变小的方向)进行了变形的情况。在弯曲部20的凹侧20a的纵壁部10ba向关闭的方向进行了变形的情况下,纵壁部10ba的端部若长度方向的线长不增加则在几何学上不成立(参照图15(c)的左图)。但是,由于纵壁部10ba端部的线长在变形前后不变化,所以在表观上,纵壁部10ba端部成为被收缩的变形(参照图15(c)的右图)。此时,若在将纵壁部10ba向截面关闭的方向进行了变形时纵壁部10ba端部向收缩的方向变形,则纵壁部10ba上部及顶板部10a被该变形拖拽而要伸展,因此,作为结果,部件的两端向下沉的方向变形(参照图15(c)的右图)。
[0133]
这样,通过在第二工序3中在弯曲部20的凹侧20a向纵壁部10ba相对于顶板部10a所成的角度变小的方向变形,能够矫正抬起的方向的长度方向的翘曲。需要说明的是,由于是长条且弯曲的形品,所以即使在折弯部10d的纵壁部10ba产生1度左右的角度变化,也能够大幅矫正长度方向的翘曲。
[0134]
基于以上这样的见解,关于实施直到第一工序2为止的冲压成型而制作出的长条弯曲部件形状的成型品10,实施一次成型解析或实际冲压成型试验,求出产生的部件的长度方向的翘曲的方向、大小。然后,在第二工序3中,以向与该得到的翘曲的方向相反的方向变形的方式对弯曲部20的一部分实施冲压成型。关于在第二工序3中变形的纵壁部10b的角度变化量,利用成型解析求出上述的翘曲降低的角度,以变形该角度的方式在第二工序3中实施冲压成型即可。由于是长条的部件,所以如上所述,能够以1度以上的角度左右充分发挥翘曲矫正效果,对部件的尺寸精度提高是有效的。
[0135]
即,在使部件两端向下沉的方向变形的情况下,使长度方向弯曲部20的凸侧20b的纵壁部10bb向截面打开的方向变形或者使长度方向弯曲部20的凹侧20a的纵壁部10ba向截面关闭的方向变形的方法是有效的。或者,使长度方向弯曲部20的凸侧20b的纵壁部10bb向截面打开的方向变形,并且使长度方向弯曲部20的凹侧20a的纵壁部10ba向截面关闭的方向变形。
[0136]
相反,在使长度方向的端部向抬起的向变形的情况下,使长度方向弯曲部20的凸侧20b的纵壁部10bb向截面关闭的方向变形或者使长度方向弯曲部20的凹侧20a的纵壁部
10ba向截面打开的方向变形的方法是有效的。或者,使长度方向弯曲部20的凸侧20b的纵壁部10bb向截面关闭的方向变形,并且使长度方向弯曲部20的凹侧20a的纵壁部10ba向截面打开的方向变形。
[0137]
在以上的说明中,通过打开或关闭纵壁部10b的截面而成型,来说明翘曲的矫正控制,但未必需要使长度方向全部的纵壁部10b的截面直接变化,即使通过以使折弯部10d中的长度方向一部分的折弯部10d的截面形状相对于第一模具不同的方式成型,也能够通过在脱模时在折弯部产生的力矩来打开或关闭纵壁部10b的截面而控制长度方向的翘曲。
[0138]
另外,使上述折弯部10d的曲率半径变化的对策也可以不对部件的长度方向全部实施,也可以至少对弯曲部20的一部分实施。
[0139]
[关于使折弯部10d的截面形状变化的作用]
[0140]
接着,对通过使弯曲部20中的折弯部10d的截面形状在第一模具和第二模具中不同而能够以使设为对象的纵壁部10b部分的截面关闭或打开的方式成型的理由进行说明。
[0141]
以下,对如上述的“第一成型的第一、第二方法”、“第四成型的第一、第二方法”等那样将设为第二模具中的对象的折弯部10d的截面形状设为与第一工序2中的同一位置处的截面形状不同的形状的作用进行说明。
[0142]
(1)首先,对将第一工序2的折弯部10d的曲率半径和第二工序3的折弯部10d的曲率半径设为不同的半径而变更截面形状的情况进行说明。
[0143]
在图16、图17中示出通过使存在于顶板部10a与纵壁部10b的边界的折弯部10d的曲率半径在第一工序2与第二工序3之间变化来使纵壁部10b的变形方式变化的手法。
[0144]
通过存在于顶板部10a与纵壁部10b的边界的折弯部10d的曲率半径变化,纵壁部10b相对于顶板部10a的倾斜变化。即,通过产生向使折弯部10d的曲率半径比第一工序2大的方向的力矩,纵壁部10b与现状相比向截面打开的方向变形。另一方面,通过产生向使上述折弯部10d的曲率半径比现状小的方向的力矩,纵壁部10b与现状相比向截面关闭的方向变形。
[0145]
需要说明的是,使上述折弯部10d的曲率半径变化的对策也可以不对弯曲部20的部件长度方向全部实施,也可以对至少一部分实施。
[0146]
(1
‑
1)第一工序2的折弯部10d的曲率半径<第二工序3的折弯部10d的曲率半径的情况(参照图16)
[0147]
在第一工序2中,如图16(a)那样,在折弯部10d产生截面打开的方向的力矩。接着,如图16(b)所示,在第一工序的折弯部10d的曲率半径比第二工序3的折弯部10d的曲率半径小的情况下,在第二工序3中,若以比第一工序2中的折弯部10d的曲率半径大的曲率半径成型,则折弯部10d中心附近的曲率半径变大。其结果,产生截面关闭的方向的力矩。另一方面,在第一工序2中未折弯变形的折弯部10d的两相邻部因第二工序3而产生折弯变形,因此产生截面关闭的方向的力矩。
[0148]
通过调整这两个折弯力矩,能够在折弯部10d产生作为整体而使纵壁部10b向关闭方向变化的折弯力矩。即,通过将第一工序2和第二工序3中的折弯部10d的曲率半径合适地组合,通过在第二工序3的成型后将模具脱模,能够使纵壁部10b的截面关闭的方向的弹性恢复通过冲压成型而产生。
[0149]
(1
‑
2)第一工序2的折弯部10d的曲率半径>第二工序3的折弯部10d的曲率半径的
情况(参照图17)
[0150]
在第一工序2中,如图17(a)那样,在折弯部10d产生截面打开的方向的力矩。如图17(b)所示,在第一工序2的折弯部10d的曲率半径比第二工序3的折弯部10d的曲率半径大的情况下,在第二工序3中,若以比第一工序2中的折弯部10d的曲率半径小的曲率半径成型,则折弯部10d中心附近的曲率半径变小。其结果,产生截面打开的方向的力矩。另一方面,在第一工序2中折弯变形的折弯部10d的两相邻部通过第二工序3而被成型为直线形状侧的轮廓,因此产生截面关闭的方向的力矩。
[0151]
通过调整这两个折弯力矩,能够在折弯部10d产生作为整体而使纵壁部10b向关闭方向变化的折弯力矩。即,通过将第一工序2和第二工序3中的折弯部10d的曲率半径合适地组合,通过在第二工序3的成型后将模具脱模,能够使纵壁部10b的截面关闭的方向的弹性恢复通过冲压成型而产生。
[0152]
(2)对作为折弯部10d处的从顶板部10a朝向纵壁部10b在多处阶段性地折弯的面形状而变更第一工序2的折弯部10d的截面形状和第二工序3的折弯部10d的截面形状的情况进行说明。
[0153]
在此,以作为从顶板部10a朝向纵壁部10b在多处阶段性地折弯的面形状而如图18所示那样设为对折弯部10d的圆弧形状的截面形状的中央部进行了倒角的倒角形状的情况来说明。
[0154]
在第一工序2中,如图18(a)那样,在折弯部10d产生截面打开的方向的力矩。在第二工序3中,通过在上述折弯部10d成型倒角形状,如图18(b)所示,折弯部10d的中央部被成型为直线形状,因此与增大了曲率半径的情况同等,如图18(c)所示,在折弯部10d中央侧产生截面关闭的方向的力矩。另一方面,在倒角部(直线部)的两相邻部的折弯部10d中,产生截面打开的方向的力矩。
[0155]
通过调整这两个折弯力矩,能够在折弯部10d产生作为整体而使纵壁部10b向关闭方向变化的折弯力矩。即,通过将第一工序2和第二工序3中的折弯部10d的截面形状合适地组合,通过在第二工序3的成型后将模具脱模,能够使纵壁部10b的截面关闭的方向的弹性恢复通过冲压成型而产生。
[0156]
需要说明的是,在上述折弯部10d处在第二工序3中成型为倒角形状的对策也可以不对部件的长度方向全部实施,也可以对至少一部分实施。
[0157]
如以上那样,即使在第一模具和第二模具中将与顶板部10a抵接的成型面和与纵壁部10b抵接的成型面设定为相同,通过使第一模具中的将折弯部10d成型的部分的截面形状和第二模具中的将折弯部10d成型的部分的截面形状不同,也就是说,通过相对于设为第一工序2的对象的折弯部10d的截面形状而相对地控制设为第二工序3的对象的折弯部10d的截面形状,能够以向关闭对象的纵壁部10b的截面的方向变形的方式冲压成型。
[0158]
需要说明的是,也能够设定成:通过将第一模具中的将折弯部10d成型的部分的截面形状和第二模具中的将折弯部10d成型的部分的截面形状控制成不同的截面形状,通过脱模时的回弹而以向打开对象的纵壁部10b的截面的方向变形的方式冲压成型。
[0159]
不过,在第一工序2中,纵壁部10b的截面向打开的方向回弹,因此,在第二工序3中,优选以向纵壁部10b的截面关闭的方向变形的方式控制。
[0160]
<效果>
[0161]
如以上说明那样,根据本实施方式,在通过冲压成型而制造了由部件形状构成的成型品10,该部件形状是截面礼帽型形状且具有沿着顶板部10a的长度方向以在俯视观察时向顶板部10a的宽度方向的一方凸出的方式弯曲的弯曲部20时,能够抑制长度方向的翘曲、扭转。
[0162]
尤其是,在弯曲部20中将第二工序3中的折弯部10d的截面形状通过变更第一工序2中的折弯部10d的截面形状而矫正的情况下,能够抑制对其他的部件形状的不良影响且简易地抑制长度方向的翘曲、扭转。
[0163]
这样,根据本实施方式的方法,能够提供具有优异的形状冻结性的长条弯曲部件形状的成型品10。
[0164]
实施例
[0165]
接着,对基于本发明的实施例进行说明。
[0166]
作为金属板1,设定980mpa级冷轧钢板(板厚1.2mm)的材料条件,将成型为是由如图19所示的尺寸构成的部件形状且具有顶板部10a、与其连续的纵壁部10b及凸缘部10c且在俯视观察时沿着部件长度方向弯曲的成型品形状的成型解析作为第一工序2的冲压成型而实施。
[0167]
在成型中使用的模具设为了使用图3所示的拉拔成型用模具的条件。此时,作为成型条件,在上述模具中,将坯料保持器的压力设为了80ton,将坯料保持器的行程设为了80mm。另外,模具与金属板1之间的摩擦系数设为了0.12且恒定。
[0168]
在如图4那样拉拔成型后,将不需要的部分修剪后,实施了回弹解析。
[0169]
此时,通过利用第一工序2的冲压成型而成型为本部件形状后的脱模,第一部件形状产生向长度方向端部分别抬起的方向翘曲的回弹,由该脱模引起的翘曲的量在长度方向的两端部都是7.2mm。
[0170]
接着,作为第二工序2的冲压成型,将上述的在长度方向端部产生了翘曲的第一部件形状的第一部件利用具有图20及图21所示的截面形状的2种模具成型而制作了具有第二部件形状的第二部件。
[0171]
在此,关于图20所示的模具的截面形状,存在于顶板部和与其连续的纵壁部的边界的折弯部中的弯曲部的凸侧(也记载为弯曲外侧)的折弯部与第一成型模具同样,设为曲率半径r7mm的圆角形状,弯曲部的凹侧(也记载为弯曲内侧)的折弯部以使直线部c7成为7mm的方式具有倒角形状。
[0172]
确认了:通过以图20的模具形状将第一部件再成型,顶板部和弯曲外侧的纵壁部所成的角度不变化,但顶板部和弯曲内侧的纵壁部所成的角度向变小的方向变化,由此,部件长度方向的两端部下沉。即,确认了:部件长度方向端部的翘曲向改善的方向发生了变化。
[0173]
另一方面,关于图21所示的截面形状,存在于顶板部和与其连续的纵壁部的边界的折弯部中的弯曲外侧的折弯部以使直线部c7成为7mm的方式具有倒角形状,弯曲内侧的折弯部与第一成型模具同样,设为了曲率半径r7mm的圆角形状。
[0174]
确认了:通过以图21的模具形状将第一部件再成型,顶板部和弯曲外侧的纵壁部所成的角度向变小的方向变化,顶板部和弯曲内侧的纵壁部所成的角度不变化,由此,部件长度方向的两端部分别抬起。即,确认了:部件长度方向端部的翘曲向恶化的方向发生了变
化。
[0175]
利用具有图20及图21所示的截面形状的第二模具分别将上述的第一部件再成型后,实施了回弹解析。
[0176]
将以图20及图21的截面形状再成型且回弹后的截面形状的比较在图22及图23中示出。
[0177]
从图22可知,通过利用图20所示的截面形状的模具再成型,顶板部与弯曲外侧的纵壁部所成的角度几乎没有变化,但顶板部与弯曲内侧的纵壁部所成的角度变小。
[0178]
并且,通过回弹解析确认了:通过截面形状如上述那样变化,部件长度方向端部的翘曲的量相对于设为目的的产品形状在两端都改善为4.5mm。
[0179]
另一方面,从图23可知:通过利用图21所示的截面形状的模具再成型,顶板部与弯曲外侧的纵壁部所成的角度变小,但顶板部与弯曲内侧的纵壁所成的角度未变化。
[0180]
并且,通过回弹解析确认了:通过截面形状如上述那样变化,部件长度方向端部的翘曲在两端都相对于设为目的的产品形状恶化为8.5mm。
[0181]
若将上述结果汇总,则成为表1那样。
[0182]
[表1]
[0183][0184]
从该表1可知,通过使第二工序3中的折弯部10d的形状变化而在弯曲部20中纵壁部10b的截面向关闭方向变形,长度方向的翘曲被控制,能够向目的的方向进行形状矫正。
[0185]
另外,本技术主张优先权的日本国专利申请2019
‑
094834(2019年5月20日申请)的全部内容通过参照而构成本公开的一部分。在此,虽然一边参照有限的数量的实施方式一边进行了说明,但权利范围不限定于它们,基于上述的公开的各实施方式的改变对于本领域技术人员来说是显而易见的。
[0186]
标号说明
[0187]
1 金属板
[0188]
2 第一工序
[0189]
3 第二工序
[0190]
10 成型品
[0191]
10a 顶板部
[0192]
10aa 表面侧
[0193]
10ab 背面侧
[0194]
10b 纵壁部
[0195]
10ba 凹侧的纵壁部
[0196]
10bb 凸侧的纵壁部
[0197]
10c 凸缘部
[0198]
10d 折弯部
[0199]
11 成型品(第一工序后)
[0200]
20 弯曲部
[0201]
20a 凹侧
[0202]
20b 凸侧