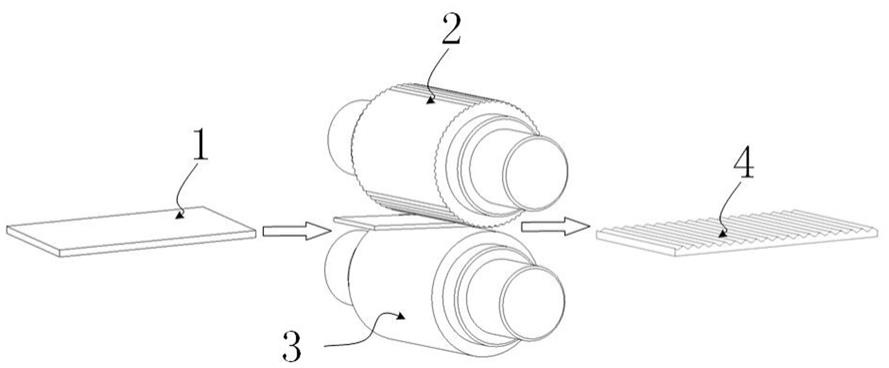
1.本发明涉及金属复合板轧制技术领域,具体是一种形成交织结合界面的金属复合板轧制方法。
背景技术:2.金属复合板是由两层或者多层异质金属经特殊工艺加工叠合在一起,实现界面冶金结合的复合材料。它可以集成组元金属材料高强度、高韧性、耐磨损、耐腐蚀等优异性能,同时金属复合板还能够节约贵重金属材料、降低产品成本。目前金属复合板的制造方法有爆炸复合法、扩散复合法、热/冷轧复合法等。其中爆炸复合法和扩散复合法普遍存在界面结合率低、结合不均匀、污染环境等缺点,相比之下热/冷轧复合法具有生产效率高、尺寸精度高、性能稳定、低污染、低能耗等优点,得到了迅速的发展并且潜力巨大。但是,由于两种不同金属性能上的差异,采用现有轧制方法制成的金属复合板仍存在结合强度低、容易翘曲、成材率低等问题。
技术实现要素:3.本发明旨在解决采用现有轧制方法制成的金属复合板界面结合强度低、容易翘曲、成材率低等技术问题。
4.本发明解决其技术问题所采用的技术方案是:
5.一种形成交织结合界面的金属复合板轧制方法,依次包括如下步骤:
6.s1、准备:选取变形抗力相对较小的金属板为基板,选取变形抗力相对较大的金属板为复板(这里的相对较小和相对较大是将基板和复板的变形抗力进行对比得出的结论),使用上轧辊为单向波纹辊、下轧辊为平辊的波平轧机分别轧制基板和复板,分别得到基板板坯和复板板坯,基板板坯和复板板坯的上表面皆为单向波纹面且下表面皆为平面;
7.s2、制坯:使用钢丝刷对基板板坯和复板板坯待结合的单向波纹面进行打磨,去除表面氧化层和污染物,将基板板坯和复板板坯单向波纹面相对并使波纹方向成90
°
堆叠放置,然后将边缘固连(保证轧制过程中基板和复板受到非均匀的切向力时不会出现错位和跑偏),得到金属复合板板坯;
8.s3、复合板轧制:采用冷轧方法时直接将步骤s2得到的金属复合板板坯送入平辊轧机进行轧制,采用热轧/温轧方法时将步骤s2得到的金属复合板板坯送入加热炉加热至指定温度后再送入平辊轧机进行轧制,所述平辊轧机的上、下轧辊均采用平辊,本工序加工得到结合界面为交织网格面而上、下表面为平面的金属复合板;
9.s4、退火;
10.s5、精整:校直后切边,制成成品。
11.进一步的,步骤s2中,用波纹辊轧机代替所述波平轧机,波纹辊轧机的上轧辊为单向波纹辊且下轧辊为交叉波纹辊,所述交叉波纹辊的表面由横向波纹和纵向波纹交叉形成,制得的基板板坯和复板板坯的上表面皆为单向波纹面且下表面皆为交叉波纹面。
12.本发明的有益效果是:
13.1)基板和复板在待结合表面上制备出单向波纹面,并且将两单向波纹面交叉叠放,可以在轧制过程中在两种板材之间形成交织网格界面,产生较强的机械结合和不均匀变形作用,能够极大限度地促进结合界面处氧化层的破裂和新鲜、活化的金属原子的挤出,使两种金属原子之间有更大的扩散概率,实现两种金属之间更大范围的冶金结合,有效提高其结合强度;
14.2)相比于传统的复合板轧制方法,本方法在一台波平轧机上即可对基板和复板进行波纹表面的制备,工艺简单、容易实现、对设备要求低,产生的结合效果好;
15.3)对基板和复板待复合表面预制波纹过程中,会形成单一方向的波纹结构,这种结构能够使板坯在垂直于波纹方向上有较好的抗弯强度,而制备复合板板坯时是将基板和复板波纹成90
°
堆叠放置,内部残余应力宏观取向相互垂直、彼此制约,进而可以抑制复合板的翘曲,提高板形质量;
16.4)在基板和复板表面分别预制出的交叉波纹能够在板材表面形成特定的棱脊结构,将板材划分为多个彼此相连的小区域,这些小的区域能够调控轧后金属板材内部的残余应力分布,避免翘曲的产生,提高板形质量;
17.5)在基板和复板表面分别预制出交叉波纹形状,这种交叉波纹会在金属板材任意截面处形成波纹形状,包括板材边缘,该种截面能够使金属流动和板材宽展均有足够的裕量和空间,从原理上抑制边裂的产生,尤其对于塑性较差的金属,效果更为明显。
附图说明
18.为了更清楚地说明本申请实施例或现有技术中的技术方案,下面将对实施例或现有技术描述中所需要使用的附图作简单地介绍,显而易见地,下面描述中的附图仅仅是本申请的一些实施例,对于本领域技术人员来讲,在不付出创造性劳动的前提下,还可以根据这些附图获得其他的附图。
19.图1为基板板坯制备示意图;
20.图2为复板板坯制备示意图;
21.图3为复合板板坯制备示意图;
22.图4为平轧金属复合板示意图;
23.图5为表面预制交叉波纹的基板板坯制备示意图;
24.图6为表面预制交叉波纹的复板板坯制备示意图;
25.图7为表面预制交叉波纹的复合板板坯制备示意图;
26.图8为冷轧步骤流程图;
27.图9为热轧步骤流程图。
28.图中:
[0029]1┄
基板;2
┄
单向波纹辊;3
┄
平辊;4
┄
基板板坯;5
┄
复板;6
┄
复板板坯;7
┄
金属复合板板坯;8
┄
金属复合板;9
┄
交叉波纹辊;10
┄
加热炉。
具体实施方式
[0030]
为了使本申请的目的、技术方案及优点更加清楚明白,以下结合附图及实施例,对
本申请进行进一步详细说明。应当理解,此处所描述的具体实施例仅仅用以解释本申请,并不用于限定本申请。
[0031]
实施例一:
[0032]
参照图1
‑
9,一种形成交织结合界面的mg/al复合板轧制方法,包括以下步骤:
[0033]
s1、准备:选取变形抗力相对较小的5052牌号铝合金板为基板1,长宽高分别为100mm、100mm、2mm,选取变形抗力相对较大的az31牌号镁合金板作为复板5,长宽高分别为100mm、100mm、2mm,使用上轧辊为单向波纹辊2、下轧辊为交叉波纹辊9的波纹辊轧机分别轧制基板1和复板5,所述交叉波纹辊9的径向截线方程为其中r为交叉波纹辊9的半径,0≤t≤1,轴向截线方程为其中0≤t≤1,单向波纹辊2与交叉波纹辊9对应方向的波纹曲线参数相同,单向波纹辊2和交叉波纹辊9的线速度均为7.5m/min,压下率为20%,本步骤分别得到基板板坯4和复板板坯6,基板板坯4和复板板坯6的上表面皆为单向波纹面且下表面皆为交叉波纹面;
[0034]
s2、制坯:使用钢丝刷对基板板坯4和复板板坯6待结合的单向波纹面进行打磨,去除表面氧化层和污染物,将基板板坯4和复板板坯6单向波纹面相对堆叠放置,并将边缘固连,得到金属复合板板坯7;
[0035]
s3、复合板轧制:采用热轧,将步骤s2得到的金属复合板板坯7送入加热炉10加热至400℃保温5min,再送入平辊轧机进行轧制,所述平辊轧机的上、下轧辊均采用平辊3,本步骤中的平辊轧机的上、下轧辊尺寸相同,压下率选择40%,本工序加工得到上、下表面为平面而结合界面为交织网格面的金属复合板8;
[0036]
s4、将平轧后的金属复合板8放入加热炉10进行退火处理,退火温度为300℃,时间是30min;
[0037]
s5、精整:校直后切边,制成成品。
[0038]
实施例二:
[0039]
参照图1
‑
4,一种形成交织结合界面的mg/al复合板轧制方法,包括以下步骤:
[0040]
s1、准备:选取变形抗力相对较小的5052牌号铝合金板为基板1,长宽高分别为100mm、100mm、2mm,选取变形抗力相对较大的az31牌号镁合金板作为复板2,长宽高分别为100mm、100mm、2mm,使用上轧辊为单向波纹辊2、下轧辊为平辊3的波纹辊轧机分别轧制基板1和复板5,所述单向波纹辊2的径向截面方程为的径向截线方程为其中r为交叉波纹辊9的半径,0≤t≤1,单向波纹辊2和平辊3的线速度均为7.5m/min,压下率为20%,本步骤分别得到基板板坯4和复板板坯6,基板板坯4和复板板坯6的上表面皆为单向波纹面且下表面皆为平面;
[0041]
s2、制坯:使用钢丝刷对基板板坯4和复板板坯6待结合的单向波纹面进行打磨,去除表面氧化层和污染物,将基板板坯4和复板板坯6单向波纹面相对堆叠放置,并将边缘固连,得到金属复合板板坯7;
[0042]
s3、复合板轧制:采用热轧,将步骤s2得到的金属复合板板坯7送入加热炉10加热
至400℃保温5min,再送入平辊轧机进行轧制,所述平辊轧机的上、下辊均采用平辊3,本步骤中的平辊轧机的上、下轧辊尺寸相同,压下率选择40%,本工序加工得到上、下表面为平面而结合界面为交织网格面的金属复合板8;
[0043]
s4、将平轧后的金属复合板8放入加热炉10进行退火处理,退火温度为300℃,时间是30min;
[0044]
s5、精整:校直后切边,制成成品。
[0045]
对比例一:
[0046]
参照图1
‑
9,平辊轧制mg/al复合板,包括以下步骤:
[0047]
s1、准备:选取变形抗力相对较小的5052牌号铝合金板为基板1,长宽高分别为100mm、100mm、2mm,选取变形抗力相对较大的az31牌号镁合金板作为复板5,长宽高分别为100、100、2mm,使用上、下轧辊均为平辊3的平辊轧机分别轧制基板1和复板5,平辊3的线速度均为7.5m/min,压下率为20%,本步骤分别得到基板板坯4和复板板坯6,基板板坯4和复板板坯6的上、下表面皆为平面;
[0048]
s2、制坯:使用钢丝刷对基板1和复板5待结合表面进行打磨,去除表面氧化层和污染物,后将两板相对堆叠放置,并将边缘固连,得到金属复合板板坯7;
[0049]
s3、复合板轧制:采用热轧,将步骤s2得到的金属复合板板坯7送入加热炉10加热至400℃保温5min,再送入平辊轧机进行轧制,所述平辊轧机的上、下轧辊均采用平辊3,本步骤中的平辊轧机的上、下轧辊尺寸相同,压下率选择40%,本工序加工得到上、下表面为平面而结合界面为交织网格面的金属复合板8;
[0050]
s4、将平轧后的金属复合板8放入加热炉10进行退火处理,退火温度为300℃,时间是30min;
[0051]
s5、精整:校直后切边,制成成品。
[0052]
对比例二:
[0053]
参照图1
‑
9,采用交叉波纹辊轧制mg/al复合板,包括以下步骤:
[0054]
s1、准备:选取变形抗力相对较小的5052牌号铝合金板为基板1,长宽高分别为100mm、100mm、2mm,选取变形抗力相对较大的az31牌号镁合金板作为复板2,长宽高分别为100mm、100mm、2mm;将基板1放入平辊轧机进行轧制,所述平辊轧机的上、下轧辊均采用平辊3,压下率为20%,得到基板板坯;将复板2放入波纹辊轧机轧制,该波纹辊轧机的上轧辊为表面设有纵向波纹的单向波纹辊2,下轧辊为平辊3,单向波纹辊2的径向截线方程为其中r为交叉波纹辊9的半径,0≤t≤1,下辊为平辊4,上、下轧辊线速度均为7.5m/min,压下率为20%;轧制后将复板2水平旋转90
°
后再次送入波纹辊轧机,各轧制条件不变,最终得到上表面为交叉波纹面,下表面为平面的复板板坯2;
[0055]
s2、制坯:使用钢丝刷对基板1和复板5待结合表面进行打磨,去除表面氧化层和污染物,后将两板相对堆叠放置,并将边缘固连,得到金属复合板板坯7;
[0056]
s3、复合板轧制:采用热轧,将步骤s2得到的金属复合板板坯7送入加热炉10加热至400℃保温5min,再送入平辊轧机进行轧制,所述平辊轧机的上、下辊均采用平辊3,本步骤中的平辊轧机的上、下轧辊尺寸相同,压下率选择40%,本工序加工得到上、下表面为平面而结合界面为交织网格面的金属复合板8;
[0057]
s4、将金属复合板8放入加热炉10进行退火处理,退火温度为300℃,时间是30min。
[0058]
s5、精整:校直后切边,制成成品。
[0059]
对实施例一、对比例一以及对比例二轧制成的复合板的特征和性能进行观察和测定,相关项目和参数见下表:
[0060]
评价项目实施例一实施例二对比例一对比例二板材翘曲不明显不明显严重轻微边裂现象不明显轻微严重轻微表面质量一般较好较好较好拉剪强度(轧向)37.62mpa39.69mpa24.93mpa34.50mpa拉剪强度(横向)40.25mpa42.51mpa29.33mpa38.74mpa抗拉强度(轧向)276.65mpa282.33mpa277.76mpa261.85mpa抗拉强度(横向)293.44mpa304.72mpa285.41mpa274.99mpa
[0061]
上表中的实验数据是在dns200电子万能试验机上测得,除加工时采用的轧制方法不同外,其他选择参数皆相同,结果如下:如上表所示,相较于对比例一和对比例二,采用本发明中涉及的方法轧制mg/al复合板,除了拉剪强度和抗拉强度有明显的提升外,边裂现象被明显抑制,说明这种方法对抑制和消除边裂作用非常显著,尤其是实施例一采用的方法。另外,翘曲也有了较大的改善,得益于波纹面的形成对残余应力分布起到调控作用。与对比例一相较,表面质量上差距明显,因为误差复映效应的存在,平轧过程中无法完全消除交叉波纹辊在mg/al复合板表面的印记。与对比例二相较,除表面质量外,其它方面优势明显。综合来看,本发明提出的方法能达到抑制或消除复合板边裂的目的,同时还可以提高两板的结合强度、改善残余应力分布状态和减小板材翘曲。
[0062]
本发明中,单向波纹辊2的表面的波纹方向不定,横向、纵向或斜向皆可,但优选采用横向波纹或纵向波纹。
[0063]
本发明中,形成交叉波纹辊9表面的横向波纹和纵向波纹的几何参数可以相同,也可以不同。优选采用相同,受力更加均匀。
[0064]
具体的,步骤s1中,预制基板板坯4和复板板坯6时压下率在10%至30%之间。前述实施例中,压下率为20%,其他实施例中,压下率也可为10%或30%。
[0065]
具体的,步骤s3中,单道次轧制压下率在30%至50%之间。前述实施例中,压下率为40%,其他实施例中,压下率也可为30%或50%。
[0066]
优选的,单向波纹辊2和交叉波纹辊9的波纹形状为正弦曲线或抛物线或三角形。
[0067]
优选的,步骤s3中,平轧分多个道次进行轧制,直至金属复合板8的厚度满足设计要求。
[0068]
本发明不只适用于双层金属板的复合,三层金属板的复合亦可,即:在步骤s1中,将基板1送入上、下轧辊均为单向波纹辊2的波纹辊轧机中轧制形成基板板坯4,将复板5送入上轧辊为单向波纹辊2、下轧辊为平辊3的波平轧机中轧制形成复板板坯6,在步骤s2中,将两块复板板坯6分别堆叠放置在基板板坯4的正上方和正下方,使基板板坯4和复板板坯6单向波纹面相对且波纹方向成90
°
,然后将边缘固连,得到金属复合板板坯7。
[0069]
以上所述仅为本申请的较佳实施例而已,并不用以限制本申请,凡在本申请的精神和原则之内所作的任何修改、等同替换和改进等,均应包含在本申请的保护范围之内。