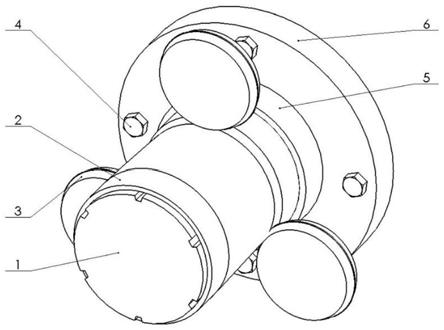
1.本发明涉及金属塑性加工技术领域,具体地,涉及一种金属筒形件的内筋填充装置、填充能力评价方法。
背景技术:2.带内筋薄壁筒体结构是运载箭体燃料贮箱的主体结构。基于新一代运载火箭服役性能极端化的设计需求和结构轻量化的发展方向,亟需发展先进的整体化结构取代传统拼焊结构,提高燃料贮箱承载性能,降低制造成本,推进航天装备结构轻量化发展进程。
3.流动旋压成形工艺被开始被用于带内筋薄壁铝合金筒体整体化工程制造。筒体内筋旋压填充性能是工程应用中被关心的问题。在流动旋压加工中,内筋填充性能包括内筋填充高度、外表面凹陷度、内筋截面填充度,这些与内筋截面宽度、工艺压下量、材料塑性等因素息息相关。同时,内筋填充极限高度是指在流动旋压过程中金属不发生破裂的前提下所能被压制内筋的最大高度,是带内筋薄壁筒体的可旋性评价指标。上述填充性能三种指标和可旋性指标是评价带内筋薄壁筒体旋压性能的重要组成部分。在现有强力旋压过程中,主要采用卡尔巴克赛格路提出的筒形件可旋性试验的方法,主要用于评价无筋筒坯材料极限变薄率。具体方法如下:将壁厚为t0的带底毛坯套在圆柱形芯模上,并由尾座顶紧以防止毛坯和芯模发生相对滑动,当毛坯与芯模随同主轴转动后,使具有接触角α
ρ
和圆角半径r
ρ
的旋轮以进给速度v
f
并与芯模母线成很小的角运动轨迹进给,从而把毛坯壁厚从t0变薄到t
f
,从而可以获得壁厚的极限变薄率。
4.现有技术中,已有针对于无筋筒形件的可旋性试验方法,这种试验方法可以获得在无破裂情况下单道次中的筒坯材料极限变薄率。然而,该试验方法未考虑带内筋薄壁筒体可旋性评价参数,无法用于带内筋薄壁筒体内筋填充性能和填充极限高度等性能参数的试验评估研究。
5.专利文献cn112404180a(申请号:cn202011346706.5)公开了一种旋平装置,包括底座、旋平架、推弯装置、推平装置、芯模;旋平架设于底座上方,推弯装置和推平装置均可水平移动设置在旋平架的下部,推弯装置和推平装置分别设于芯模的左右两侧方。一种轮毂筒坯的制造方法,包括以下步骤:将长方形的平板卷圆,形成筒形件;对筒形件的对口焊接使对口闭合,通过冲压机冲压筒形件,筒形件被冲压成碗形件;对碗形件进行旋压使碗形件的收缩端贴在芯模的表面。
技术实现要素:6.针对现有技术中的缺陷,本发明的目的是提供一种金属筒形件的内筋填充装置、填充能力评价方法。
7.根据本发明提供的金属筒形件的内筋填充装置,包括:金属芯模、筒坯、旋轮、螺栓、夹紧环和基座;
8.所述金属芯模紧固于旋压机上;
9.所述筒坯套装在金属芯模上;
10.所述旋轮安装在筒坯外表面上,对应金属芯模的筋槽位置;
11.所述夹紧环通过螺栓与筒坯预紧固定;
12.所述基座通过螺栓与旋压机的机床主轴连接。
13.优选的,所述旋轮的数量为3个,且沿筒坯周向等距分布;
14.采用反向强力旋压方式,旋轮的运动轨迹为初始与筒坯接触点到筒坯旋压破裂时的接触点,所述旋轮与筒坯的倾斜角范围为2
°
~4
°
。
15.根据本发明提供的金属筒形件的内筋填充能力评价方法,包括如下步骤:
16.步骤s1:在外径为d的金属芯模上加工出内筋截面宽度为w
i
、截面高度为h
i
的筋槽,宽度w
i
大于截面高度h
i
;
17.步骤s2:取内径为d的筒形件作为筒坯;
18.步骤s3:将金属芯模紧固于旋压机上,并将筒坯套装到金属芯模上,使用三旋轮工艺对筒坯进行反向旋压,直至筒坯发生破裂为止;
19.步骤s4:将旋压后的带筋金属筒形件取出,沿轴线方向进行半剖,然后使用三坐标扫描仪器对半剖零件内、外表面进行扫描,获得旋压后带筋金属筒形件云图数据;
20.步骤s5:将得到的旋压后带筋金属筒形件云图数据进行几何重构处理,得到带内筋筒体的内筋截面宽度与内筋填充极限高度的图形,并根据重构后的图形对内筋填充能力进行评价。
21.优选的,所述筋槽具有肩部圆角和拔模角度,相同内筋截面宽度的筋槽对称分布,相邻筋槽的内筋截面宽度不相同,用以测量单道次旋压中不同内筋截面宽度条件下的内筋填充能力。
22.优选的,扫描云图数据包括所有旋轮在内、外表面的运动轨迹。
23.优选的,从几何重构后的图形中提取参数,对外表面凹陷度β进行评价,表达式为:
[0024][0025]
其中:r1为筒形件外壁凹陷的曲率半径、r2为无筋区域的外表面曲率半径,外表面凹陷度越低,表明内筋填充能力越好。
[0026]
优选的,计算引入凹陷度的在濒临断裂位置的内筋填充高度,作为内筋填充极限高度和筋高成形的评价指标,表达式为:
[0027][0028]
其中:t1为内筋位置左侧壁板厚、t2为筒形件外壁的高度、t3为内筋位置右侧壁板厚、r2为无筋区域的外表面曲率半径,引入凹陷度的在濒临断裂位置的内筋填充高度越高,表明内筋填充能力越好。
[0029]
优选的,计算内筋截面饱满度,作为内筋填充能力评价指标,表达式为:
[0030][0031]
其中:s1为内筋横截面积、s为理论横截面积,内筋截面饱满度越大,表明内筋填充能力越好。
[0032]
与现有技术相比,本发明具有如下的有益效果:
[0033]
(1)本发明可建立带内筋薄壁筒形件内筋填充性能,包括内筋填充极限高度、给定内筋截面宽度条件下工艺压下量与内筋填充高度、外表面凹陷度、内筋截面填充度的关系,对带筋筒形件整体化制造的结构设计和工艺设计有重要的意义;
[0034]
(2)本发明通过对金属芯模模具上设计关于圆心对称的不同内筋截面宽度的多条筋槽,在旋压过程中,工艺压下量不断递增至筒坯壁板断裂,从而可以在单道次旋压中获得带内筋薄壁筒形件多个内筋截面宽度的填充能力的实验数据,减少了实验次数,节省了成本。
附图说明
[0035]
通过阅读参照以下附图对非限制性实施例所作的详细描述,本发明的其它特征、目的和优点将会变得更明显:
[0036]
图1为本发明芯模与筒坯装配结构示意图;
[0037]
图2为本发明的筋槽放大图;
[0038]
图3为本发明筒坯尺寸示意图;
[0039]
图4为本发明旋压后筒形件几何重构内筋界面示意图;
[0040]
图中:1
‑
金属芯模;2
‑
筒坯;3
‑
旋轮;4
‑
螺栓;5
‑
夹紧环;6
‑
基座。
具体实施方式
[0041]
下面结合具体实施例对本发明进行详细说明。以下实施例将有助于本领域的技术人员进一步理解本发明,但不以任何形式限制本发明。应当指出的是,对本领域的普通技术人员来说,在不脱离本发明构思的前提下,还可以做出若干变化和改进。这些都属于本发明的保护范围。
[0042]
实施例:
[0043]
如图1~图4,本发明提供了一种金属筒形件的内筋填充装置,包括:金属芯模1、筒坯2、旋轮3、螺栓4、夹紧环5和基座6;所述金属芯模1紧固于旋压机上;所述筒坯2套装在金属芯模1上;所述旋轮3安装在筒坯2外表面上,对应金属芯模1的筋槽位置;所述夹紧环5通过螺栓4与筒坯2预紧固定;所述基座6通过螺栓4与旋压机的机床主轴连接。
[0044]
根据本发明提供的一种带内筋金属筒形件填充性能测试方法,包括如下步骤:
[0045]
步骤s1:在外径为d的金属芯模1上加工出内筋截面宽度为w
i
、截面高度为h
i
的筋槽结构,宽度w
i
大于截面高度h
i
;
[0046]
步骤s2:取内径为d、初始厚度为t0、长度为l0的筒形件作为筒坯2;
[0047]
步骤s3:将金属芯模1紧固于旋压机上,并将筒坯2套装到金属芯模1上,运用三旋轮3工艺对筒坯2进行反向旋压,直至筒坯2发生破裂为止;
[0048]
步骤s4:将旋压后的带筋金属筒形件取出,沿轴线方向进行半剖,然后使用三坐标扫描仪器对半剖零件内、外表面进行扫描,获得旋压后带筋金属筒形件云图数据;
[0049]
步骤s5:将得到的旋压后带筋金属筒形件云图数据进行几何重构处理,可得到带内筋筒体的内筋截面宽度与内筋填充极限高度的图形;给定内筋截面宽度条件下工艺压下量与内筋填充高度、外表面凹陷度、内筋截面填充度的图形。
[0050]
步骤s1中,所述加工的筋槽带有一定的肩部圆角r和拔模角度θ,且相同内筋截面宽度的筋槽对称分布,相邻筋槽的内筋截面宽度各不相同,用以实现单道次旋压中测量出不同内筋截面宽度条件下的内筋填充能力。
[0051]
步骤s3中,所述紧固装置包括基座6和夹紧环5,其中基座6与机床主轴通过螺栓4连接,夹紧环5与筒坯2通过螺栓4预紧固定。所述的三旋轮3沿周向等距分布,采用反向强力旋压方式,旋轮3运动轨迹为初始与筒坯2接触点到筒坯2旋压破裂时的接触点,其倾斜角在2
°
至4
°
之间。
[0052]
步骤s4中,所述扫描云图数据包括所有旋轮3运动轨迹发生的内、外表面。
[0053]
步骤s5中,从重构的几何模型中提取的参数包括:筒形件外壁的高度t2,筒形件外壁凹陷的曲率半径r1,无筋区域的外表面曲率半径r2,内筋位置左侧壁板厚t1和右侧壁板厚t3,内筋横截面积s1。
[0054]
对成形筋的评价指标有如下几点:
[0055]
表面凹陷是带筋筒形件的外表面缺陷,在内筋未填满的情况下其外表面在旋压过程中会留下一定深度的压痕,外表面凹陷度计算公式为可得到凹陷度β评价指标;
[0056]
计算出引入凹陷度的内筋填充高度在濒临断裂位置的内筋填充高度被认为是内筋填充极限高度h
c
可得到关于筋高成形的评价指标;
[0057]
计算出内筋截面饱满度其中s是理论横截面积,可得到筋的填充能力评价指标。
[0058]
实施例结果表明,本发明设计的芯模、旋压方式以及评估筋截面质量的方式可以实现带筋筒形件的填充能力的可旋性试验方法与检测,获取筒形件筋的截面质量,并建立带内筋薄壁筒形件内筋填充性能,包括内筋填充极限高度、给定内筋截面宽度条件下减薄率与内筋填充高度、外表面凹陷度、内筋截面填充度的关系,绘制出筋的填充能力关系曲线图,对带筋筒形件整体化制造的结构设计和工艺设计有重要的意义。
[0059]
在本技术的描述中,需要理解的是,术语“上”、“下”、“前”、“后”、“左”、“右”、“竖直”、“水平”、“顶”、“底”、“内”、“外”等指示的方位或位置关系为基于附图所示的方位或位置关系,仅是为了便于描述本技术和简化描述,而不是指示或暗示所指的装置或元件必须具有特定的方位、以特定的方位构造和操作,因此不能理解为对本技术的限制。
[0060]
在本技术的描述中,需要注意的是,并未对旋压方式做出限制,比如正旋或反旋,而是重在对带筋筒形件的填充性可试验的一种评估方法,因此不能只理解为本文所描述的模具和工艺轨迹,基于本文思路的对带筋筒形件可填充性能的测试方法的设计都应属于本发明的保护内容。
[0061]
本领域技术人员知道,除了以纯计算机可读程序代码方式实现本发明提供的系统、装置及其各个模块以外,完全可以通过将方法步骤进行逻辑编程来使得本发明提供的系统、装置及其各个模块以逻辑门、开关、专用集成电路、可编程逻辑控制器以及嵌入式微控制器等的形式来实现相同程序。所以,本发明提供的系统、装置及其各个模块可以被认为是一种硬件部件,而对其内包括的用于实现各种程序的模块也可以视为硬件部件内的结
构;也可以将用于实现各种功能的模块视为既可以是实现方法的软件程序又可以是硬件部件内的结构。
[0062]
以上对本发明的具体实施例进行了描述。需要理解的是,本发明并不局限于上述特定实施方式,本领域技术人员可以在权利要求的范围内做出各种变化或修改,这并不影响本发明的实质内容。在不冲突的情况下,本技术的实施例和实施例中的特征可以任意相互组合。