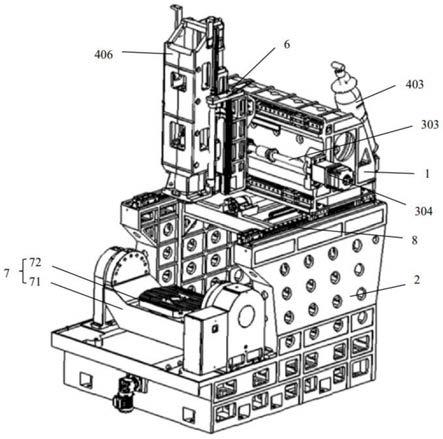
1.本发明涉及机械加工设备领域,具体地,涉及一种五轴摇篮加工机床。
背景技术:2.随着科技发展,国内社会对汽车的需求量日益上升,汽车生产需求量逐渐增大,对于汽车内主要零件(轮毂)的机械加工产量需求也是不断加大。由于其配合尺寸及表面要求高的特殊性,需采用机床对轮毂进行精密加工。
3.卡巴轮毂具有质量大,尺寸大,表面硬度大,表面加工精度要求高,加工结构复杂的特点。目前国内对于轮毂的加工大多采用通用标准机床进行加工,由此便产生了加工精度不达标,机床浪费度极大,加工效率低下等等重点问题。
4.现有公开号为cn204912949u的中国专利,其公开了一种轮毂加工专用机床,包括床身,所述切削装置包括固定在支撑板上的第一刀架、横向滑移连接于支撑板的第二刀架,所述支撑板上还设有用于驱动第二刀架滑移的第三动力部,所述第一刀架上设有用于加工轮毂端面的第一切削刀和第二切削刀以及驱动第一切削刀和第二切削刀转动的第一驱动部,所述第二刀架上设有用于加工轮毂轮辋的第三切削刀、用于加工轮缘倒角的第四切削刀和用于切断轮毂废料的第五切削刀以及驱动第三切削刀、第四切削刀和第五切削刀转动的第二驱动部。
5.发明人认为现有技术中的机床难以对轮毂进行多工序加工,精密性低、效率差,存在待改进之处。
技术实现要素:6.针对现有技术中的缺陷,本发明的目的是提供一种五轴摇篮加工机床。
7.根据本发明提供的一种五轴摇篮加工机床,包括龙门式底座、横梁、主轴箱以及摇篮工作台,所述横梁滑动设置在龙门式底座上,所述主轴箱上滑动设置有滑鞍,所述滑鞍的运动方向与横梁的运动方向相互垂直,所述主轴箱升降设置在滑鞍上;所述横梁的运动方向为y轴方向,所述滑鞍的运动方向为x轴方向,所述主轴箱的运动方向为z轴方向;所述摇篮工作台转动设置在龙门式底座上,所述摇篮工作台位于主轴箱的下方,且所述摇篮工作台能够绕x轴方向和z轴方向转动。
8.优选地,所述横梁、滑鞍以及主轴箱三者均通过驱动组件分别驱动,所述驱动组件包括丝杆和驱动电机,且任一所述丝杆的轴向均与对应的横梁、滑鞍或主轴箱的运动方向同向。
9.优选地,所述丝杆与机床之间连接有支撑装置,所述支撑装置包括电机端支撑组和尾座端支撑组,所述丝杆的一端转动安装在电机端支撑组内,所述丝杆的另一端转动安装在尾座端支撑组内;所述电机端支撑组包括电机座,所述丝杆的一端探入电机座内,且所述丝杆与电机座之间连接有第一角接触球轴承;所述尾座端支撑组包括轴承座,所述丝杆的另一端探入轴承座内,所述丝杆与轴承座之间连接有第二角接触球轴承,所述轴承座靠
近电机端支撑组的一侧紧固连接有第二轴承压盖,所述第二轴承压盖与轴承座之间设置有拉伸调整垫。
10.优选地,所述机床上设置有重心平衡装置,所述重心平衡装置用于平衡主轴箱自身的重力。
11.优选地,所述重心平衡装置包括平衡气缸和储气装置,所述平衡气缸的缸体与机床滑鞍紧固连接,所述平衡气缸的活塞杆与主轴箱的外壁铰接连接;所述平衡气缸在主轴箱的两侧分别安装有一个,且所述储气装置的出气口与两个平衡气缸分别连通。
12.优选地,所述主轴箱上设置有用于对工件喷射冷却液的环喷冷却装置。
13.优选地,所述环喷冷却装置包括安装壳体,所述安装壳体内设置有流通腔体,所述流通腔体首尾连通形成封闭式结构,所述安装壳体上开设有冷却进口,所述冷却进口与流通腔体连通;所述安装壳体上安装有环喷嘴,所述环喷嘴与流通腔体连通。
14.优选地,所述龙门式底座包括基台、立柱以及连接梁,所述立柱在基台上至少竖直设置有两个,所述连接梁设置在立柱的顶部,且所述连接梁用于连接多个立柱;所述立柱的侧壁上设置有排砂通气孔;所述基台上设置有排屑漏斗,所述排屑漏斗的底部设置有与基台外部连通的排屑通道。
15.优选地,所述摇篮工作台设置在排屑漏斗的上方,且所述摇篮工作台与排屑漏斗之间形成有允许废液和废屑通过的间隙。
16.优选地,所述摇篮工作台包括支撑部和摇篮部,所述摇篮部用于装夹待加工的工件,所述支撑部转动设置在龙门式底座上,且所述支撑部能够绕x轴方向转动;所述摇篮部转动设置在支撑部上,当所述支撑部处于水平状态时,所述摇篮部能够绕z轴方向转动。
17.与现有技术相比,本发明具有如下的有益效果:
18.1、本发明通过沿y轴方向滑移的横梁、沿x轴方向滑移的滑鞍、沿z轴方向滑移的主轴箱以及绕z轴轴线和y轴轴线运动的摇篮工作台配合作用,使机床具有五轴联动特性,实现了对工件的多工序加工,有助于提高加工精度和加工效率;
19.2、本发明通过驱动电机、丝杆以及导轨的配合实现对横梁、滑鞍或主轴箱的驱动,有助于提高横梁、滑鞍以及主轴箱运动的稳定性;
20.3、本发明通过在主轴上安装光栅尺,将到位检测结果进行反馈,行程系统闭环回路,有助于提高机床精度。
附图说明
21.通过阅读参照以下附图对非限制性实施例所作的详细描述,本发明的其它特征、目的和优点将会变得更明显:
22.图1为本发明主要体现机床整体结构的示意图;
23.图2为本发明主要体现龙门式底座整体结构示意图;
24.图3为本发明主要体现基台整体结构的剖面示意图;
25.图4为本发明主要体现龙门式底座侧面整体结构的剖面示意图;
26.图5为本发明主要体现横梁整体结构的示意图;
27.图6为本发明主要体现横梁横截面整体结构的示意图;
28.图7为本发明主要体现承托筋板整体结构的俯视图;
29.图8为本发明主要体现支撑结构整体结构的示意图;
30.图9为本发明主要体现电机端支撑组整体结构的示意图;
31.图10为本发明主要体现尾座端支撑组整体结构的示意图;
32.图11为本发明主要体现平衡装置整体结构的示意图;
33.图12为本发明主要体现平衡装置底部结构的示意图;
34.图13为本发明主要体现冷却装置整体结构的上表面示意图;
35.图14为本发明主要体现冷却装置整体结构的下表面示意图;
36.图15为本发明主要体现冷却装置整体结构的剖面示意图;
37.图16为本发明主要体现龙门式底座上侧结构的示意图。
38.图中所示:
39.横梁1
ꢀꢀꢀꢀꢀꢀꢀꢀꢀꢀꢀꢀꢀꢀꢀꢀꢀꢀꢀ
电机端支撑组301
ꢀꢀꢀꢀꢀꢀꢀꢀꢀ
储气装置401
40.横梁主体101
ꢀꢀꢀꢀꢀꢀꢀꢀꢀꢀꢀꢀꢀ
尾座端支撑组302
ꢀꢀꢀꢀꢀꢀꢀꢀꢀ
高压管402
41.竖直板1011
ꢀꢀꢀꢀꢀꢀꢀꢀꢀꢀꢀꢀꢀꢀ
丝杆303
ꢀꢀꢀꢀꢀꢀꢀꢀꢀꢀꢀꢀꢀꢀꢀꢀꢀ
平衡气缸403
42.侧板1012
ꢀꢀꢀꢀꢀꢀꢀꢀꢀꢀꢀꢀꢀꢀꢀꢀ
驱动电机304
ꢀꢀꢀꢀꢀꢀꢀꢀꢀꢀꢀꢀꢀ
安装部404;
43.背板1013
ꢀꢀꢀꢀꢀꢀꢀꢀꢀꢀꢀꢀꢀꢀꢀꢀ
电机座305
ꢀꢀꢀꢀꢀꢀꢀꢀꢀꢀꢀꢀꢀꢀꢀ
主轴箱406
44.圆弧部1014
ꢀꢀꢀꢀꢀꢀꢀꢀꢀꢀꢀꢀꢀꢀ
安装槽3051
ꢀꢀꢀꢀꢀꢀꢀꢀꢀꢀꢀꢀꢀꢀ
平衡架407
45.平板部1015
ꢀꢀꢀꢀꢀꢀꢀꢀꢀꢀꢀꢀꢀꢀ
梅花联轴器306
ꢀꢀꢀꢀꢀꢀꢀꢀꢀꢀꢀ
重心409
46.承托筋板102
ꢀꢀꢀꢀꢀꢀꢀꢀꢀꢀꢀꢀꢀ
第一锁紧螺母307
ꢀꢀꢀꢀꢀꢀꢀꢀꢀ
平衡点4010
47.立筋板1021
ꢀꢀꢀꢀꢀꢀꢀꢀꢀꢀꢀꢀꢀꢀ
第一隔套308
48.横筋板1022
ꢀꢀꢀꢀꢀꢀꢀꢀꢀꢀꢀꢀꢀꢀ
第一骨架油封309
ꢀꢀꢀꢀꢀꢀꢀꢀꢀ
上壳体501
49.斜筋板1023
ꢀꢀꢀꢀꢀꢀꢀꢀꢀꢀꢀꢀꢀꢀ
第一轴承压盖3010
ꢀꢀꢀꢀꢀꢀꢀꢀ
下封板502
50.空心腔体103
ꢀꢀꢀꢀꢀꢀꢀꢀꢀꢀꢀꢀꢀ
第一角接触球轴承3011
ꢀꢀꢀꢀ
连接螺钉503
51.排沙通气孔104
ꢀꢀꢀꢀꢀꢀꢀꢀꢀꢀꢀ
第二骨架油封3014
ꢀꢀꢀꢀꢀꢀꢀꢀ
环喷嘴504
52.窄型加强筋板105
ꢀꢀꢀꢀꢀꢀꢀꢀꢀ
第二轴承压盖3015
ꢀꢀꢀꢀꢀꢀꢀꢀ
锁紧螺钉505
53.减重空腔106
ꢀꢀꢀꢀꢀꢀꢀꢀꢀꢀꢀꢀꢀ
拉伸调整垫3016
ꢀꢀꢀꢀꢀꢀꢀꢀꢀꢀ
工艺堵头506
54.ꢀꢀꢀꢀꢀꢀꢀꢀꢀꢀꢀꢀꢀꢀꢀꢀꢀꢀꢀꢀꢀꢀꢀꢀ
轴承座3017
ꢀꢀꢀꢀꢀꢀꢀꢀꢀꢀꢀꢀꢀꢀ
第一密封圈507
55.龙门式底座2
ꢀꢀꢀꢀꢀꢀꢀꢀꢀꢀꢀꢀꢀ
第二隔套3018
ꢀꢀꢀꢀꢀꢀꢀꢀꢀꢀꢀꢀ
第二密封圈508
56.基台201
ꢀꢀꢀꢀꢀꢀꢀꢀꢀꢀꢀꢀꢀꢀꢀꢀꢀ
第二角接触球轴承3019
ꢀꢀꢀꢀ
第三密封圈509
57.立柱202
ꢀꢀꢀꢀꢀꢀꢀꢀꢀꢀꢀꢀꢀꢀꢀꢀꢀ
第三轴承压盖3020
ꢀꢀꢀꢀꢀꢀꢀꢀ
冷却进口5010
58.导轨支撑平面203
ꢀꢀꢀꢀꢀꢀꢀꢀꢀ
第三隔套3022
ꢀꢀꢀꢀꢀꢀꢀꢀꢀꢀꢀꢀ
中通道5011
59.连接梁204
ꢀꢀꢀꢀꢀꢀꢀꢀꢀꢀꢀꢀꢀꢀꢀ
第二锁紧螺母3023
ꢀꢀꢀꢀꢀꢀꢀꢀ
流通腔体5012
60.排砂通气孔205
ꢀꢀꢀꢀꢀꢀꢀꢀꢀꢀꢀꢀꢀꢀꢀꢀꢀꢀꢀꢀꢀꢀꢀꢀꢀꢀꢀꢀꢀꢀꢀꢀꢀꢀꢀ
安装壳体5013
61.排屑漏斗206
ꢀꢀꢀꢀꢀꢀꢀꢀꢀꢀꢀꢀꢀ
滑鞍6
62.排屑通道207
ꢀꢀꢀꢀꢀꢀꢀꢀꢀꢀꢀꢀꢀ
摇篮工作台7
ꢀꢀꢀꢀꢀꢀꢀꢀꢀꢀꢀꢀꢀ
导轨8
63.方形筋板208
ꢀꢀꢀꢀꢀꢀꢀꢀꢀꢀꢀꢀꢀ
支撑部71
ꢀꢀꢀꢀꢀꢀꢀꢀꢀꢀꢀꢀꢀꢀꢀꢀ
光栅尺9
64.贯穿式筋板209
ꢀꢀꢀꢀꢀꢀꢀꢀꢀꢀꢀ
摇篮部72
65.驱动件安装架2010
具体实施方式
66.下面结合具体实施例对本发明进行详细说明。以下实施例将有助于本领域的技术人员进一步理解本发明,但不以任何形式限制本发明。应当指出的是,对本领域的普通技术人员来说,在不脱离本发明构思的前提下,还可以做出若干变化和改进。这些都属于本发明的保护范围。
67.如图1所示,根据本发明提供的一种五轴摇篮加工机床,包括龙门式底座2、横梁1、主轴箱406以及摇篮工作台7,横梁1滑动设置在龙门式底座2上,主轴箱406上滑动设置有滑鞍6,滑鞍6的运动方向与横梁1的运动方向相互垂直,且主轴箱406升降设置在滑鞍6上。横梁1的运动方向为y轴方向,所述滑鞍6的运动方向为x轴方向,所述主轴箱406的运动方向为z轴方向。摇篮工作台7转动设置在龙门式底座2上,所述摇篮工作台7位于主轴箱406的下方,且所述摇篮工作台7能够绕x轴方向和z轴方向转动。
68.通过沿x轴方向运动的滑鞍6、沿y轴方向运动的横梁1、沿z轴方向运动的主轴箱406以及绕x轴方向和z轴方向转动的摇篮工作台7,实现了机床的五轴联动特性。机床可配套轮毂专用液压夹具,可实现对卡巴轮毂的装夹,粗加工,精加工,下料等全套加工过程。有效地解决了目前卡巴轮毂加工过程中的多工序,多机床等等繁琐问题。提升了卡巴轮毂加工的精密性,稳定性和效率等。
69.如图2所示,龙门式底座2是横梁1、主轴箱406以及摇篮工作台7的安装基础,龙门式底座2包括基台201、立柱202以及连接梁204,基台201、立柱202以及连接梁204三者均为铸造一体成型,并配合形成龙门结构,提高了龙门式底座2整体结构的结构强度和刚度。
70.基台201底部通过地脚垫铁水平安装在地面上,结构稳固,基台201为底座下方最基础部分。立柱202在基台201后部的左右两侧分别竖直成型有一个,两个立柱202的形状、大小以及结构均相同。连接梁204铸造成型在两个立柱202的顶部,且连接梁204与基台201呈水平间隔设置。基台201的上侧形成有加工区域,加工区域与连接梁204在基台201上的竖直投影区域呈相邻设置。
71.如图2所示。所示基台201内一体成型有排屑漏斗206,排屑漏斗206位于加工区域的中部,排屑漏斗206的底部一体成型有排屑通道207位于基台201的中部,并使基台201以排屑通道207为对称轴呈左右对称。排屑通道207的两端均贯穿基台201并与外界连接,排屑漏斗206开口的形状呈矩形,排屑漏斗206的侧壁自上向下朝排屑通道207逐渐收缩。工作中产生的废液和废屑落入排屑漏斗206,并沿排屑漏斗206的侧壁落入排屑通道207并排出,侧壁为大角度的排屑漏斗206,排屑、排液顺畅,外观美观实用;采用前后贯穿式的排屑通道207,排屑顺畅,集屑方便,节省空间。
72.如图2和图3所示,基台201内部呈镂空结构,基台201内一体成型有方形筋板208,方形筋板208在基台201内成型有两层,且方形筋板208整齐布局于基台201整个内腔,并以排屑通道207为对称轴呈左右对称设置。镂空式得结构降低了基台201的重量,呈均匀对称分布的方形筋板208一方面增强了基台201的结构强度,另一方面使基台201的质量分布均匀,提高了稳定性。
73.如图2和图4所示,两个立柱202的顶部均形成有导轨支撑平面203,两个导轨支撑平面203均位于同一平面内,两个立柱202的侧壁上均开设有排砂通气孔205,排砂通气孔205在立柱202的侧壁上呈均匀分布。两个立柱202均为镂空结构,两个立柱202内均一体成
型有贯穿式筋板209,贯穿式筋板209呈上下贯穿分布,贯穿式筋板209的下侧与基台201内部的方形筋板208相连,铸造一体,贯穿式筋板209的上侧延伸到立柱202顶部,且贯穿式筋板209与排砂通气孔205呈相邻设置。
74.两个立柱202内部的贯穿式筋板209直接支撑导轨支撑平面203和下部的地脚垫铁位置,可将承托在直线导轨上的所有载荷直接传递于大地,保证机床底座整体的稳定性。两个立柱202的对称性设计,既保证了底座两侧承载力的一致性,又保证了热载荷在底座内的均匀性。贯穿式筋板209加强了立柱202和基台201的结构强度,且镂空式的设计,减轻了底座的自重。立柱202外表面设计有多个排砂通气孔205,排布左右严格对称,方便铸造工艺排砂,散热效果显著,降低底座质量,得到最优的底座静动态性能。
75.如图2所示,连接梁204的上表面为驱动件安装面,且连接梁204上表面的中心位置设置有驱动件安装架2010,使驱动件保持在上方运动部件的正中心,符合重心驱动的设计理念,极大地提高了底座上方运动部件的运行平稳性和顺畅度。经fea计算得到此优化后的一体式龙门封闭框架结构,结果显示,此结构机床底座刚性达到最大化,强度最优,低阶模态性能符合机床加工工况。
76.两个导轨支撑平面203上均铺设有用于引导横梁1运动的导轨8,两个导轨8的长度方向均与y轴方向同向,横梁1通过两条间隔的导轨8架设在连接梁204上。驱动横梁1运动的驱动组件通过驱动件安装架2010安装在连接梁204和横梁1之间。且驱动组件包括丝杆303和驱动电机304。
77.如图5所示,横梁1包括横梁主体101和承托筋板102,横梁主体101和承托筋板102二者通过一体铸造成型,且承托筋板102位于横梁主体101的下方。横梁主体101包括空心腔体103,空心腔体103为圆筒形腔体,横梁主体101的侧壁上开设有排沙通气孔104,且排沙通气孔104与空心腔体103连通。
78.圆形的空心腔体103结构具有较大的抗弯扭能力,采用圆筒式的空心腔体103和承托筋板102结合的方式,能够有效降低机床在加工过程中横梁1的弯扭变形,通过fea优化后得到最优静、动态性能。且空心腔体103能够增强横梁1内部的通风与散热能力吸收机床热应力,有效防止横梁1产生热变形而影响加工精度。横梁1截面尺寸大,增大了机床的支撑跨距,提高了横梁1的稳定性。
79.横梁主体101还包括竖直板1011、侧板1012和背板1013,空心腔体103、侧板1012以及背板1013三者通过铸造为一体。侧板1012在空心腔体103轴向的两端分别一体成型有一个,背板1013一体成型在空心腔体103的背部。背板1013包括圆弧部1014和平板部1015,圆弧部1014与空心腔体103外壁的上侧圆弧贴合,平板部1015自其与圆弧部1014的连接处自上向下朝远离空心腔体103的一侧延伸,且平板部1015的下端延伸至承托筋板102并与其铸造为一体。竖直板1011一体成型在横梁主体101背离背板1013的一侧,且竖直板1011靠近空心腔体103外壁的一侧与空心腔体103的外壁贴合。
80.进一步地,两块侧板1012上均一体成型有窄型加强筋板105,窄型加强筋板105在两块侧板1012上均呈竖直交错设置有多条,从而提高两块侧板1012的强度。排沙通气孔104在两块侧板1012上分别开设有一个,两个位于侧板1012上的排沙通气孔104的轴线均与空心腔体103的轴线共线。排沙通气孔104在背板1013的平板部1015的上侧和下侧分别开设有两组,两组排沙通气孔104均包括四个沿空心腔体103轴线呈等间隔设置的排沙通气孔104,
排沙通气孔104在竖直板1011上也开设有两组,且背板1013上的排沙通气孔104与竖直板1011上的排沙通气孔104呈一一对应设置。排沙通气孔104在横梁主体101的顶部沿横梁主体101的轴线等间隔开设有四个。
81.如图5和图6所示,借助开设在横梁主体101正面、背面、侧面以及顶部的排沙通道,可以起到排砂、散热的作用,也达到了减重的效果。空心腔体103、竖直板1011、背板1013、两块侧板1012以及承托筋板102五者配合形成有多个减重空腔106,进一步的提高了到减重效果,且提高了横梁1固有频率,防止机床在加工过程中产生共振而影响加工精度的隐患。
82.如图7所示,承托筋板102包括立筋板1021、横筋板1022以及斜筋板1023,立筋板1021、横筋板1022以及斜筋板1023三者相互交叉形成米字形排布。从俯视图来看,立筋板1021、横筋板1022以及斜筋板1023三者在承托筋板102上配合形成有两个米字形结构。
83.如图5和图7所示,借助安装在横梁主体101下方的米字形加强筋和圆筒形的空心腔体103配合,进一步的加强了横梁1的抗弯扭能力。且采用最优的圆形与米字形筋相结合的方式,能够有效消除机床由于各种因素产生的应力、变形等等,提高机床整体加工精度和使用寿命。
84.横梁1靠近基台201上的加工区域的一侧铺设有用于引导滑鞍6运动的导轨8,该导轨8的长度方向平行于x轴方向,横梁1上安装有用于驱动滑鞍6运动的驱动组件,驱动组件包括丝杆303和驱动电机304,该驱动电机304固定安装在横梁1上,该丝杆303的轴向与x轴方向同向,且该丝杆303水平穿设横梁1。
85.主轴箱406也是通过导轨8和驱动组件安装在滑鞍6上,且铺设在滑鞍6上的导轨8的长度方向与z轴方向同向,安装在滑鞍6上的驱动组件也包括驱动电机304和丝杆303,该丝杆303的长度方向与z轴方向同向。
86.分别用于驱动横梁1、滑鞍6以及主轴箱406运动的三个丝杆303均通过支撑装置安装在机床对应的位置,且三个丝杆303的支撑装置的结构、安装方式以及工作原理均相同,现以一组支撑装置为例进行阐述:
87.如图8所示,包括电机端支撑组301和尾座端支撑组302,丝杆303的一端转动安装在电机端支撑组301内,丝杆303的另一端转动安装在尾座端支撑组302内。
88.如图8和图9所示,电机端支撑组301包括电机座305,电机座305是电机端支撑组301的安装基础,电机座305靠近尾座端支撑组302的内部一体成型有用于安装轴承的安装槽3051,安装槽3051内同轴嵌设安装有两组第一角接触球轴承3011,两个第一角接触球轴承3011均为双列结构,两个第一角接触球轴承3011采用面对面的方式安装。
89.安装槽3051靠近尾座端支撑组302的一侧的开口的直径不允许第一角接触球轴承3011通过,安装槽3051远离尾座端支撑组302的一侧开口处安装有第一轴承压盖3010,第一轴承压盖3010与靠近其的第一角接触球轴承3011的外环端面抵紧配合,且丝杆303穿设第一轴承压盖3010并与其转动配合。借助安装槽3051靠近尾座端支撑组302的内壁与第一轴承压盖3010配合将两个第一角接触球轴承3011夹紧在安装槽3051内,并使两个第一角接触球轴承3011的外环与安装槽3051的内壁紧固连接。
90.丝杆303的一端自安装槽3051靠近尾座端支撑组302的一侧的开口同轴穿入两个第一角接触球轴承3011的内环中。第一角接触球轴承3011靠近尾座端支撑组302的一侧的内环端面通过第一隔套308与丝杆303的轴肩抵紧配合,丝杆303穿过安装槽3051的一侧螺
纹配合有第一锁紧螺母307,第一锁紧螺母307与第一角接触球轴承3011远离尾座端支撑组302的一侧的内环端面通过第一隔套308抵紧配合。借助丝杆303的轴肩与第一角接触球轴承3011靠近尾座端支撑组302的一侧的内环端面的抵紧配合、第一锁紧螺母307与第一角接触球轴承3011远离尾座端支撑组302的一侧的内环端面的抵紧配合,从而实现了丝杆303与两个第一角接触球轴承3011内环的紧固连接。
91.安装槽3051靠近尾座端支撑组302的外壁、第一轴承压盖3010背离安装槽3051的一侧外壁上均嵌设安装有第一骨架油封309,由两个第一骨架油封309对安装槽3051的两侧开口分别进行密封,保证了安装槽3051内两个第一角接触球轴承3011运动的稳定性和可靠性。
92.电机座530远离尾座端支撑组302的一侧通过螺栓固定安装有驱动电机304,丝杆303穿出安装槽3051背离尾座端支撑组302的开口的一侧通过梅花联轴器306与驱动电机304的输出中同轴固定连接,实现了丝杆303与驱动电机304输出轴的直线连接方式,提高了丝杆303运动的稳定性。
93.如图8和图10所示,尾座端支撑组302包括轴承座3017,丝杆303的另一端穿入轴承座3017内,丝杆303与轴承座3017之间连接有第二角接触球轴承3019,第二角接触球轴承3019为双列结构。第二角接触球轴承3019在轴承座3017内同轴安装有两组,两个第二角接触球轴承3019采用面对面的方式安装,且两个第二角接触球轴承3019之间安装有第二隔套3018用于将两个第二角接触球轴承3019分隔。此种方式既提高了对丝杆303的定位能力,又加长了两组第二角接触球轴承3019的轴向作用点距离,增大了对丝杆303的支撑刚性。
94.轴承座3017靠近电机座305的一侧紧固安装有第二轴承压盖3015,轴承座3017的另一侧通过螺栓紧固安装有第三轴承压盖3020,第三轴承压盖3020与远离电机座305的第二角接触球轴承3019的外环端面抵紧配合,丝杆303依次穿过第二轴承压盖3015和第三轴承压盖3020并分别与二者转动配合。
95.第二轴承压盖3015与轴承座3017锁紧固定,第二轴承压盖3015与第二角接触球轴承3019的外环端面抵紧配合,第二角接触球轴承3019靠近电机座305的一侧内环端面与丝杆303的轴肩抵紧配合,且第二轴承压盖3015与轴承座3017之间安装有拉伸调整垫3016。第二轴承压盖3015连接于轴承座3017上,并将第二轴承压盖3015向轴承座3017的尾端不断进行压紧,此时由于丝杆303的一端固定在电机座305上,会将丝杆303向轴承座3017的尾端不断拉伸。当丝杆303拉伸达到理论拉伸量时,测量此时第二轴承压盖3015和轴承座3017之间的实际间隙,以此实测间隙为准配磨拉伸调整垫3016的厚度到此数值,然后安装拉伸调整垫3016,至此丝杆303拉伸结束。
96.丝杆303上同轴套设有第三隔套3022,第三隔套3022穿过第三轴承压盖3020并与其转动配合,丝杆303远离电机座305的一端螺纹配合有第二锁紧螺母3023,第二锁紧螺母3023抵紧第三隔套3022并将其压紧在第二角接触球轴承3019背离电机座305的内环端面。
97.第二轴承压盖3015和第三轴承压盖3020二者配合夹紧安装在轴承座3017内的第二角接触球轴承3019两侧的外环端面,从而使两个第二角接触球轴承3019的外环均与轴承座3017紧固连接。借助丝杆303的轴肩和第三隔套3022的配合将两个第二角接触球轴承3019的内环均与丝杆303紧固连接,实现了丝杆303与轴承座3017的转动配合,且第二轴承压盖3015和第三轴承压盖3020相互背离的外壁上均嵌设安装有第二骨架油封3014,由两个
第二骨架油封3014对轴承座3017的两侧开口分别进行密封,保证了安装在轴承座3017内的两个第二角接触球轴承3019运动的稳定性和可靠性。
98.如图11所示,机床上还安装有重心平衡装置,重心平衡装置用于平衡主轴箱406自身的重力。重心平衡装置包括平衡气缸403和储气装置401,平衡气缸403的缸体与机床的滑鞍6紧固连接,平衡气缸403的活塞杆与主轴箱406的外壁铰接连接,且主轴箱406在机床上做升降运动。平衡气缸403在主轴箱406的两侧分别安装有一个,两个平衡气缸403以主轴箱406的重心409呈对称设置,且储气装置401分别与两个平衡气缸403连通。
99.借助两个以主轴箱406的重心409呈对称设置的平衡气缸403同时作用于主轴箱406,并对主轴箱406起到支撑作用,平衡主轴箱406自身的重力,以达到优化机床动态性能的目的。
100.如图11所示,机床的滑鞍6包括两个水平向外延伸的安装部404,两个安装部404分别位于主轴箱406的两侧,两个安装部404均与主轴箱406呈间隔设置,且两个安装部404分别为两个平衡气缸403的安装基础,并使两个平衡气缸403不参与主轴箱406沿竖直方向的运动。两个平衡气缸403的缸体均竖直紧固安装在对应的安装部404的下侧,且两个平衡气缸403的活塞杆均自下向上竖直穿设安装部404并与其滑移配合。
101.主轴箱406的上侧紧固安装有平衡架407,平衡架407的上端水平向远离主轴箱406的一侧延伸,平衡架407与安装部404呈一一对应设置,且平衡架407位于安装部404的上侧。两个平衡气缸403竖直穿出安装部404的活塞杆的端部均通过万向活动接头铰接连接在对应的平衡架407上。通过活动接头将平衡气缸403的活塞杆安装在平衡架407上,实现了平衡气缸403的活塞杆与平衡架407的活动连接,提高了平衡气缸403的使用寿命。
102.平衡气缸403的平衡点4010位于平衡气缸403与滑鞍6的连接点的竖直轴线上,优选地平衡点4010位于平衡气缸403与安装部404的连接处,两个平衡气缸403的平衡点4010以主轴箱406的重心409为对称点呈对称设置。安装时,将主轴箱406的重心409和两个平衡气缸403的平衡点4010三者安装在同一直线上,此设计能够增强此平衡装置的平衡效率,进而提高主轴箱406运动的动态响应性能,符合重心409平衡的设计理念。
103.储气装置401为压力瓶,储气装置401内存储有高压气体,且储气装置401通过抱箍紧固安装在机床上。储气装置401的出气口通过高压管402分别与两个平衡气缸403连通,从而为两个平衡气缸403提供稳定的压力。高压管402与平衡气缸403的连接处均位于平衡气缸403的下部,从而实现对两个平衡气缸403活塞杆的驱动,且储气装置401输出的压力值与主轴箱406整体重力大小呈正比,以达到两个平衡气缸403恰好能平衡主轴箱406自身重力的效果。
104.如图11和图12所示,机床上竖直设置有导轨8,主轴箱406安装在导轨8上并与其滑移配合,且主轴箱406的运动方向与导轨8的长度方向同向。当主轴箱406运动时,借助两个平衡气缸403对主轴箱406重力进行平衡,此平衡装置便是利用重心409平衡设计理念,能够增强平衡效率,直接平衡主轴箱406自身重力,从而减小主轴箱406自身重力对其动态响应性能的影响,达到提高机床整体精度,提高机床静动态性能和使用寿命。
105.如图13、图14和图15所示,进一步地,为了使机床的工作保持稳定,主轴箱406的下侧安装有用于对工件喷射冷却液的环喷冷却装置。环喷冷却装置包括安装壳体5013,安装壳体5013内开设有流通腔体5012,流通腔体5012首尾连通形成封闭式结构,安装壳体5013
上开设有冷却进口5010,冷却进口5010与流通腔体5012连通,安装壳体5013上安装有环喷嘴504,环喷嘴504与流通腔体5012连通。工作时,通过管道将冷却液自冷却进口5010输送至流通腔体5012内,之后再经环喷嘴504将流通腔体5012内的冷却液喷射到加工位置,对工件和刀具进行冷却。
106.如图13和图15所示,安装壳体5013的形状近似为圆环形,安装壳体5013由高强度铝合金制成,安装壳体5013包括上壳体501和下封板502,且上壳体501和下封板502之间连接有锁紧螺钉505,锁紧螺钉505在安装壳体5013上等间隔安装有多个,多个锁紧螺钉505配合将上壳体501和下封板502贴合锁紧。
107.流通腔体5012一体成型于上壳体501内,流通腔体5012的轨迹呈圆环形。上壳体501背离下封板502的一侧开设有冷却进口5010,冷却进口5010的中心轴线平行于安装壳体5013的中心轴线,且冷却进口5010在上壳体501上以安装壳体5013的中心轴线为对称中心对称开设有两个。两个冷却进口5010与流通腔体5012之间均连接有中通道5011,中通道5011的中心轴线垂直于冷却进口5010的中心轴线,且中通道5011的两端分别与对应的冷却进口5010和流通腔体5012连通。
108.两个种通道背离流通腔体5012的一端的侧壁上均安装有工艺堵头506,且保证工艺堵头506处无冷却液泄露。上壳体501上的两个冷却进口5010处均嵌设安装有第一密封圈507,用于对两个冷却进口5010进行密封,从而减少冷却液从管道与冷却进口5010的连接处泄露的情况发生。
109.如图15所示,流通腔体5012靠近下封板502的一侧呈敞开设置,下封板502将流通腔体5012下侧的敞开口封闭,下封板502上嵌设安装有第二密封圈508和第三密封圈509,第二密封圈508和第三密封圈509均为环形密封圈,且第二密封圈508和第三密封圈509分别位于流通腔体5012的两侧,且第一密封圈507和第二密封圈508均与上壳体501紧配。借助第二密封圈508和第三密封圈509配合对流通腔体5012和下封板502的连接处进行密封,减少了冷却液从流通腔体5012和下封板502的连接处流出。
110.如图14和图15所示,环喷嘴504安装在下封板502背离冷却进口5010的一侧,环喷嘴504的喷口从下封板502背离上壳体501的一侧伸出,且环喷嘴504与下封板502之间通过环型接头连接,从而使环喷嘴504能够通过旋转来调整倾斜角度,实现对不同位置的工件和刀具进行喷射冷却液。
111.环喷嘴504位于下封板502的中间位置,且环喷嘴504在下封板502上沿流通腔体5012的轨迹等间隔安装有八个,从而使冷却液经八个环喷嘴504均匀圆周喷射于加工位置。
112.如图13和图15所示,安装壳体5013上安装有用于将安装壳体5013安装到机床上的连接螺钉503,连接螺钉503自上壳体501背离下封板502的一侧伸出,且连接螺钉503在安装壳体5013的中部上绕安装壳体5013的中心轴线等间隔安装有八个。安装壳体5013通过八个连接螺钉503与主轴箱406下底面相连接,其中,主轴鼻端可穿过安装壳体5013内环,且安装壳体5013的整体厚度小于主轴鼻端长度,以保证主轴可以正常加工。
113.工作中,冷却液首先由两个冷却进口5010进入中通道5011,在冷却进口5010处安装有第一密封圈507以保证此连接位置无冷却液泄露。经冷却进口5010之后冷却液流经中通道5011,此处保证工艺堵头506处无冷却液泄露。经中通道5011之后,冷却液便流入环形的流通腔体5012内,流通腔体5012被下封板502锁紧封住,其中两者之间的第二密封圈508
和第三密封圈509保证流通腔体5012内的冷却液不会从此处泄露。下封板502在流通腔体5012正下方的位置安装八个环喷嘴504,冷却液经环喷嘴504均匀圆周喷射于加工位置。
114.如图1和图16所示,摇篮工作台7安装在排屑漏斗206的上方,且摇篮工作台7与排屑漏斗206之间形成有允许废液和废屑通过的间隙。摇篮工作台7包括支撑部71和摇篮部72,支撑部71通过第一转轴转动架设在排屑漏斗206的上方,第一转轴的轴向与x轴方向同向,且第一转轴能够使支撑部71沿第一转轴的中心轴线转动。
115.摇篮部72通过第二转轴安装在支撑部71的中部,第二转轴的中心轴线垂直于第一转轴的中心轴线,且第二转轴能够使摇篮部72与支撑部71发生相对转动。当支撑部71位于水平位置时,第二转轴的轴向与z轴方向同向,摇篮部72能够绕第二转轴的中心轴线转动。摇篮部72能够安装各种用于夹持卡巴轮毂的工装夹具,实现对待加工的卡巴轮毂的装夹。
116.龙门式底座2为机床整机的基础,通过地脚垫铁与地面固定。龙门式底座2采用框式一体铸造结构,提高机床刚性,跨距大,适合于对卡巴轮毂等大型高硬度零件的粗、精加工。龙门式底座2上安装有用于引导横梁1运动的丝杆303和导轨8,其中丝杆303为丝杆螺母结构,丝杆303两端通过组合轴承进行支撑,轴端直联高性能同步电机,对丝杆303产生旋转驱动,导轨8为大跨距滚柱直线导轨,用于支撑与其连接的横梁1。横梁1采用圆筒筋式排布铸造,抵抗扭转与弯曲能力强,适用于大跨距结构。横梁1上安装有用于引导滑鞍6运动的丝杆303和导轨8,其中通过导轨8对滑鞍6进行刚性支撑,滑鞍6采用阶梯式支撑结构,整体铸造,抵抗扭转能力强。滑鞍6上安装有用于引导主轴箱406运动的丝杆303和导轨8,其中通过导轨8对主轴箱406进行刚性支撑。摇篮工作台7直接与龙门式底座2做刚性连接,绕x轴方向和z轴方向进行旋转。主轴箱406中刚性嵌入机床主轴,对卡巴轮等待加工零件进行加工。此外,各轴均安装有光栅尺9,将到位检测结果进行反馈,行程系统闭环回路,提高机床精度。机床通过cnc控制系统可实现对于沿x轴方向、y轴方向、z轴方向的滑动以及绕x轴中心轴线、z轴中心轴线转动的联动,对卡巴轮等待加工零件进行有效加工。
117.工作原理
118.实际使用中,龙门式底座2为机床整机的基础,通过地脚垫铁与地面固定,龙门式底座2上安装有用于引导横梁1运动的丝杆303和导轨8,其中丝杆303为丝杆螺母结构,丝杆303两端通过组合轴承进行支撑,轴端直联高性能同步电机,对丝杆303产生旋转驱动,导轨8为大跨距滚柱直线导轨,用于支撑与其连接的横梁1;横梁1上安装有用于引导滑鞍6运动的丝杆303和导轨8,其中通过导轨8对滑鞍6进行刚性支撑,滑鞍6上安装有用于引导主轴箱406运动的丝杆303和导轨8,其中通过导轨8对主轴箱406进行刚性支撑,摇篮工作台1直接与龙门式底座2做刚性连接,绕x轴方向和z轴方向进行旋转;各轴均安装有光栅尺9,将到位检测结果进行反馈,行程系统闭环回路,提高机床精度。机床通过cnc控制系统可实现对于沿x轴方向、y轴方向、z轴方向的滑动以及绕x轴中心轴线、z轴中心轴线转动的联动,对卡巴轮等待加工零件进行有效加工。
119.在本技术的描述中,需要理解的是,术语“上”、“下”、“前”、“后”、“左”、“右”、“竖直”、“水平”、“顶”、“底”、“内”、“外”等指示的方位或位置关系为基于附图所示的方位或位置关系,仅是为了便于描述本技术和简化描述,而不是指示或暗示所指的装置或元件必须具有特定的方位、以特定的方位构造和操作,因此不能理解为对本技术的限制。
120.以上对本发明的具体实施例进行了描述。需要理解的是,本发明并不局限于上述
特定实施方式,本领域技术人员可以在权利要求的范围内做出各种变化或修改,这并不影响本发明的实质内容。在不冲突的情况下,本技术的实施例和实施例中的特征可以任意相互组合。