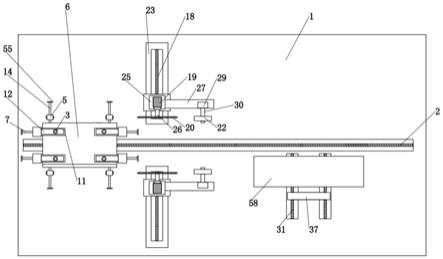
1.本发明涉及铝板加工领域,特别是一种铝板全自动剪板、叠板生产线。
背景技术:2.铝板在生产时,由于尺寸需求不同或者为了便于后期加工需要进行合理的切割,但是传统的切割方式均采用人工手动切割,切割方式单一,人工手动操作切割工作效率低,并且切割时,人工手动切割具有一定的危险,同时在铝板切割后,经常进行冲压形成波浪型叠板,传统操作方式,费时费力,工作效率低,无法满足工作效率。
技术实现要素:3.本发明的目的是为了解决上述问题,设计了一种铝板全自动剪板、叠板生产线。
4.实现上述目的本发明的技术方案为,一种铝板全自动剪板、叠板生产线,包括:
5.条形台;
6.第一移动送料结构,所述第一移动送料结构固定安装在条形台上;
7.切割结构,所述切割结构安置于条形台上,且位于第一移动送料结构两侧;
8.第二移动送料结构,所述第二移动送料结构固定安装条形台上,且位于切割结构右侧;
9.冲压结构,所述冲压结构安置于条形台上且位于第二移动送料结构上方。
10.所述第一移动送料结构包括:第一电动丝杠模组、第一伸缩电机、第一滚轮以及第一托架;
11.所述条形台上壁面开设有第一条形凹槽,所述第一电动丝杠模组安置于第一条形凹槽内部,所述第一电动丝杠模组移动端上安装有第一支座,所述第一支座上安装有支撑架,所述支撑架左右两侧壁面固定有第一导杆,每个所述第一导杆上均插装有第一滑架,每个所述第一滑架上均固定有第一支架,每个所述第一支架上均安装有第一支柱,所述第一支柱上固定有第二支架,所述第二支架上安装有第一折型架,所述第一伸缩电机安置于第一折型架上,所述第一伸缩电机驱动端上安装有第一压板,所述支撑架前后两侧壁面均固定有第二导杆,所述第二导杆上套装有第二滑架,所述第二滑架上安装有第三支架,所述第三支架上安装有第二支柱,所述第一托架安置于每个所述第二支柱上,所述第一滚轮分别安置于第一滑架以及第二滑架下壁面。
12.所述切割结构包括:第二电动丝杠模组、第一伺服电机、切割刀、第一轴承以及滚盘;
13.所述条形台上壁面且位于第一条形凹槽前后两侧固定有位置相对应的条形架,所述条形架上壁面开设有第二条形凹槽,所述第二电动丝杠模组安置于第二条形凹槽内部,所述第二电动丝杠模组移动端上安装有第二支座,所述第二支座上固定有第一驱动安装座,所述第一伺服电机安置于第一驱动安装座上壁面,所述第一伺服电机驱动端上安装有第一连接杆,所述切割刀安置于第一连接杆上,所述第二支座侧壁面固定有第二驱动安装
座,所述第二驱动安装座上安装有第二伸缩电机,所述第二伸缩电机驱动端上固定有承载架,所述承载架上开设有第一圆形凹槽,所述第一轴承安置于第一圆形凹槽内部,所述第一轴承上固定有第一支杆,所述滚盘安置于第一支杆上。
14.所述第二移动送料结构包括:第三电动丝杠模组、步进电机、第三伸缩电机、第四电动丝杆模组以及第二托架;
15.所述条形台上且位于切割结构右侧开设有一对第三条形凹槽,所述第三电动丝杠模组安置于第三条形凹槽内部,所述第三电动丝杠模组移动端上安装有第三支座,一对所述第三支座上安装有门型架,所述门型架下壁面固定有支板,所述支板上开设有第四条形凹槽,所述第四电动丝杆模组安置于第四条形凹槽内部,所述第四电动丝杆模组移动端上安装有第四支座,所述第四支座上固定有连接架,所述连接架上固定有第三驱动安装座,所述步进电机安置于第三驱动安装座上,所述步进电机驱动端上安装有第二连接杆,所述第二托架安置于第二连接杆上,所述第二托架上壁面固定有第二折型架,所述第三伸缩电机驱动端上安装有第三连接杆,所述第三连接杆上安装有第二压板。
16.所述冲压结构包括:气缸、上模具以及下模具;
17.所述条形架上壁面且横跨第三条形凹槽安装有安装架,所述气缸安置于安装架下壁面,所述气缸驱动端上安装有安装座,所述上模具安置于安装座上,所述下模具安置于条形台上壁面且与上模具位置相对应。
18.所述第二驱动安装座下壁面固定有第一顶杆,所述第一顶杆下壁面固定有第二滚轮。
19.所述条形台下壁面且靠近四角处均固定有第二顶杆,每个所述第二顶杆下壁面均安装有垫片。
20.所述第一导杆以及第二导杆上均固定有垫圈。
21.所述第一滑架上开设有第一螺纹口,所述第一导杆上开设有与第一螺纹口相匹配的第一螺纹槽,所述第一螺纹口内插装有与第一螺纹槽相搭接的第一螺钉。
22.所述第二滑架上开设有第二螺纹口,所述第二导杆上开设有与第二螺纹口相匹配的第二螺纹槽,所述第二螺纹口内插装有与第二螺纹槽相搭接的第二螺钉。
23.利用本发明的技术方案制作的一种铝板全自动剪板、叠板生产线,通过第一移动送料结构,便于将需要加工的铝板夹取支撑后进行移动,向切割结构以及冲压结构方向移动,无需人工手动支撑拿取铝板,通过切割结构,便于对铝板进行切割,提高切割效率,无需人工切割操作,通过第二移动送料结构,将切割后的铝板放置冲压结构上,通过冲压结构进行冲压成型。
附图说明
24.图1是本发明所述一种铝板全自动剪板、叠板生产线的结构示意图;
25.图2是本发明所述一种铝板全自动剪板、叠板生产线的第一移动送料结构侧视图;
26.图3是本发明所述一种铝板全自动剪板、叠板生产线的切割结构的主视图;
27.图4是本发明所述一种铝板全自动剪板、叠板生产线的第一移动送料结构主视图;
28.图5是本发明所述一种铝板全自动剪板、叠板生产线的第二移动送料结构以及冲压结构侧剖视图;
29.图6是本发明所述一种铝板全自动剪板、叠板生产线的第二移动送料结构以及冲压结构主视图;
30.图7是本发明所述一种铝板全自动剪板、叠板生产线的冲压结构主视图;
31.图8是本发明所述一种铝板全自动剪板、叠板生产线的切割结构主视图;
32.图9是本发明所述一种铝板全自动剪板、叠板生产线的门型架侧视剖视图;
33.图10是本发明所述一种铝板全自动剪板、叠板生产线的滚盘侧视图;
34.图中,1、条形台;2、第一电动丝杠模组;3、第一伸缩电机;4、第一伸缩电机;5、第一托架;6、支撑架;7、第一导杆;8、第一滑架;9、第一支架;10、第一支柱;11、第二支架;12、第一折型架;13、第一压板;14、第二导杆;15、第二滑架;16、第三支架;17、第二支柱;18、第二电动丝杠模组;19、第一伺服电机;20、切割刀;21、第一轴承;22、滚盘;23、条形架;24、第二支座;25、第一驱动安装座;26、第一连接杆;27、第二驱动安装座;28、第二伸缩电机;29、承载架;30、第一支杆;31、第三电动丝杠模组;32、步进电机;33、第三伸缩电机;34、第四电动丝杆模组;35、第二托架;36、第三支座;37、门型架;38、支板;39、第一支座;40、第四支座;41、连接架;42、第三驱动安装座;43、第二连接杆;44、第二折型架;45、第三连接杆;46、第二压板;47、气缸;48、上模具;49、下模具;50、安装座;51、第一顶杆;52、第二滚轮;53、第二顶杆;54、垫片;55、垫圈;56、第一螺钉;57、第二螺钉;58、安装架。
具体实施方式
35.下面结合附图对本发明进行具体描述,如图1至10所示,一种铝板全自动剪板、叠板生产线,包括:条形台1;第一移动送料结构,第一移动送料结构固定安装在条形台1上;切割结构,切割结构安置于条形台1上,且位于第一移动送料结构两侧;第二移动送料结构,第二移动送料结构固定安装条形台1上,且位于切割结构右侧;冲压结构,冲压结构安置于条形台1上且位于第二移动送料结构上方;第一移动送料结构包括:第一电动丝杠模组2、第一伸缩电机3、第一滚轮4以及第一托架5;条形台1上壁面开设有第一条形凹槽,第一电动丝杠模组2安置于第一条形凹槽内部,第一电动丝杠模组2移动端上安装有第一支座39,第一支座39上安装有支撑架6,支撑架6左右两侧壁面固定有第一导杆7,每个第一导杆7上均插装有第一滑架8,每个第一滑架8上均固定有第一支架9,每个第一支架9上均安装有第一支柱10,第一支柱10上固定有第二支架11,第二支架11上安装有第一折型架12,第一伸缩电机3安置于第一折型架12上,第一伸缩电机3驱动端上安装有第一压板13,支撑架6前后两侧壁面均固定有第二导杆14,第二导杆14上套装有第二滑架15,第二滑架15上安装有第三支架16,第三支架16上安装有第二支柱17,第一托架5安置于每个第二支柱17上,第一滚轮4分别安置于第一滑架8以及第二滑架15下壁面;切割结构包括:第二电动丝杠模组18、第一伺服电机19、切割刀20、第一轴承21以及滚盘22;条形台1上壁面且位于第一条形凹槽前后两侧固定有位置相对应的条形架23,条形架23上壁面开设有第二条形凹槽,第二电动丝杠模组18安置于第二条形凹槽内部,第二电动丝杠模组18移动端上安装有第二支座24,第二支座24上固定有第一驱动安装座25,第一伺服电机19安置于第一驱动安装座25上壁面,第一伺服电机19驱动端上安装有第一连接杆26,切割刀20安置于第一连接杆26上,第二支座24侧壁面固定有第二驱动安装座27,第二驱动安装座27上安装有第二伸缩电机28,第二伸缩电机28驱动端上固定有承载架29,承载架29上开设有第一圆形凹槽,第一轴承21安置于第一
圆形凹槽内部,第一轴承21上固定有第一支杆30,滚盘22安置于第一支杆30上;第二移动送料结构包括:第三电动丝杠模组31、步进电机32、第三伸缩电机33、第四电动丝杆模组34以及第二托架35;条形台1上且位于切割结构右侧开设有一对第三条形凹槽,第三电动丝杠模组31安置于第三条形凹槽内部,第三电动丝杠模组31移动端上安装有第三支座36,一对第三支座36上安装有门型架37,门型架37下壁面固定有支板38,支板38上开设有第四条形凹槽,第四电动丝杆模组34安置于第四条形凹槽内部,第四电动丝杆模组34移动端上安装有第四支座40,第四支座40上固定有连接架41,连接架41上固定有第三驱动安装座42,步进电机32安置于第三驱动安装座42上,步进电机32驱动端上安装有第二连接杆43,第二托架35安置于第二连接杆43上,第二托架35上壁面固定有第二折型架44,第三伸缩电机33驱动端上安装有第三连接杆45,第三连接杆45上安装有第二压板46;冲压结构包括:气缸47、上模具48以及下模具49;条形架23上壁面且横跨第三条形凹槽安装有安装架58,气缸47安置于安装架58下壁面,气缸47驱动端上安装有安装座50,上模具48安置于安装座50上,下模具49安置于条形台1上壁面且与上模具48位置相对应;第二驱动安装座27下壁面固定有第一顶杆51,第一顶杆51下壁面固定有第二滚轮52;条形台1下壁面且靠近四角处均固定有第二顶杆53,每个第二顶杆53下壁面均安装有垫片54;第一导杆7以及第二导杆14上均固定有垫圈55;第一滑架8上开设有第一螺纹口,第一导杆7上开设有与第一螺纹口相匹配的第一螺纹槽,第一螺纹口内插装有与第一螺纹槽相搭接的第一螺钉56;第二滑架15上开设有第二螺纹口,第二导杆14上开设有与第二螺纹口相匹配的第二螺纹槽,第二螺纹口内插装有与第二螺纹槽相搭接的第二螺钉57。
36.本实施方案的特点为,包括:条形台1;第一移动送料结构,第一移动送料结构固定安装在条形台1上;切割结构,切割结构安置于条形台1上,且位于第一移动送料结构两侧;
37.第二移动送料结构,第二移动送料结构固定安装条形台1上,且位于切割结构右侧;冲压结构,冲压结构安置于条形台1上且位于第二移动送料结构上方,通过第一移动送料结构,便于将需要加工的铝板夹取支撑后进行移动,向切割结构以及冲压结构方向移动,无需人工手动支撑拿取铝板,通过切割结构,便于对铝板进行切割,提高切割效率,无需人工切割操作,通过第二移动送料结构,将切割后的铝板放置冲压结构上,通过冲压结构进行冲压成型。
38.在本实施方案中,条形台1;
39.第一移动送料结构,第一移动送料结构固定安装在条形台1上;
40.切割结构,切割结构安置于条形台1上,且位于第一移动送料结构两侧;
41.第二移动送料结构,第二移动送料结构固定安装条形台1上,且位于切割结构右侧;
42.冲压结构,冲压结构安置于条形台1上且位于第二移动送料结构上方;
43.需要说明的是:第一移动送料结构便于将铝板进行固定支撑之后,进行运输,通过切割结构,便于对铝板两侧或者单侧进行切割,切割完成之后,通过第二移动送料结构运输,运输到冲压结构上,通过冲压结构进行压形,形成叠板。
44.第一移动送料结构包括:第一电动丝杠模组2、第一伸缩电机3、第一滚轮4以及第一托架5;
45.条形台1上壁面开设有第一条形凹槽,第一电动丝杠模组2安置于第一条形凹槽内
部,第一电动丝杠模组2移动端上安装有第一支座39,第一支座39上安装有支撑架6,支撑架6左右两侧壁面固定有第一导杆7,每个第一导杆7上均插装有第一滑架8,每个第一滑架8上均固定有第一支架9,每个第一支架9上均安装有第一支柱10,第一支柱10上固定有第二支架11,第二支架11上安装有第一折型架12,第一伸缩电机3安置于第一折型架12上,第一伸缩电机3驱动端上安装有第一压板13,支撑架6前后两侧壁面均固定有第二导杆14,第二导杆14上套装有第二滑架15,第二滑架15上安装有第三支架16,第三支架16上安装有第二支柱17,第一托架5安置于每个第二支柱17上,第一滚轮4分别安置于第一滑架8以及第二滑架15下壁面;
46.实际操作时:第一电动丝杠模组2移动端能够移动,带动第一支座39上的支撑架6移动,支撑架6上的第一导杆7上安装的第一滑架8能够移动,调整位置,达到调整第一滑架8上第一支柱10支撑的第二支架11之间距离,第一折型架12上的第一伸缩电机3驱动端能够伸缩,从而带动第一压板13上下移动,在根据铝板长度调整第二支架11位置,便于铝板两端放置在第二支架11上,之后通过第一伸缩电机3驱动端下降,通过第一压板13压住铝板,使其固定放置,第二导杆14上的第二滑架15移动,调整第二支柱17上的第一托架5使用位置,通过第一托架5用于支撑铝板下壁面,第二滑架15移动,调整第一托架5使用位置,便于根据不同宽度的铝板调整使用位置,第一滚轮4,便于第一滑架8和第二滑架15移动时起到移动支撑作用。
47.切割结构包括:第二电动丝杠模组18、第一伺服电机19、切割刀20、第一轴承21以及滚盘22;
48.条形台1上壁面且位于第一条形凹槽前后两侧固定有位置相对应的条形架23,条形架23上壁面开设有第二条形凹槽,第二电动丝杠模组18安置于第二条形凹槽内部,第二电动丝杠模组18移动端上安装有第二支座24,第二支座24上固定有第一驱动安装座25,第一伺服电机19安置于第一驱动安装座25上壁面,第一伺服电机19驱动端上安装有第一连接杆26,切割刀20安置于第一连接杆26上,第二支座24侧壁面固定有第二驱动安装座27,第二驱动安装座27上安装有第二伸缩电机28,第二伸缩电机28驱动端上固定有承载架29,承载架29上开设有第一圆形凹槽,第一轴承21安置于第一圆形凹槽内部,第一轴承21上固定有第一支杆30,滚盘22安置于第一支杆30上;
49.需要说明的是:第二电动丝杠模组18移动端能够前后移动,调整第二支座24上第一驱动安装座25支撑的第一伺服电机19使用位置,第一伺服电机19驱动端能够转动,带动第一连接杆26上的切割刀20转动,根据需要切割尺寸调整切割刀20位置,之后第一伺服电机19转动,带动切割刀20转动,铝板与切割刀20接触,从而进行切割,第二伸缩电机28驱动端能够升降,带动第一轴承21上的滚盘22上下调整高度,在切割时,第二伸缩电机28升起,滚盘22高于铝板,之后第二伸缩电机28驱动端下降,带动滚盘22下降,将切割废料通过滚盘22下压,便于切割口产生缝隙,便于切割完成的废料掉落,滚盘22能够滚动,减少摩擦力。
50.第二移动送料结构包括:第三电动丝杆模组31、步进电机32、第三伸缩电机33、第四电动丝杆模组34以及第二托架35;
51.条形台1上且位于切割结构右侧开设有一对第三条形凹槽,第三电动丝杠模组31安置于第三条形凹槽内部,第三电动丝杠模组31移动端上安装有第三支座36,一对第三支座36上安装有门型架37,门型架37下壁面固定有支板38,支板38上开设有第四条形凹槽,第
四电动丝杆模组34安置于第四条形凹槽内部,第四电动丝杆模组34移动端上安装有第四支座40,第四支座40上固定有连接架41,连接架41上固定有第三驱动安装座42,步进电机32安置于第三驱动安装座42上,步进电机32驱动端上安装有第二连接杆43,第二托架35安置于第二连接杆43上,第二托架35上壁面固定有第二折型架44,第三伸缩电机33驱动端上安装有第三连接杆45,第三连接杆45上安装有第二压板46;
52.实际操作时:第三电动丝杠模组31移动端能够移动,带动第三支座36上的门型架37移动,便于将第二托架35移动到铝板下方,第二托架35通过步进电机32驱动端的第二连接杆43支撑,步进电机32驱动端能够顺时针转动或者逆时针转动,在使用时,带动第二托架35摆动,调整纵向状态,位于铝板下方,不使用时,步进电机32驱动端逆时针转动,将第二托架35横置,便于收起第二托架35,防止阻碍冲压结构使用,步进电机32通过支板38上的第四电动丝杆模组34支撑,第四电动丝杆模组34竖置摆动,所以第四电动丝杆模组34移动端能够移动升降,调整第二托架35使用高度,第四电动丝杆模组34移动端向下移动,将第二托架35位于铝板下方,第三电动丝杠模组31向后移动,将第二托架35位于铝板下方,第一伸缩电机3驱动端升起,第一压板13远离铝板,之后第三伸缩电机33驱动端下降,压住铝板,之后第三电动丝杠模组31向前移动,将铝板移动到冲压结构上,第三伸缩电机33升起,第二压板46抬起,将铝板放置在下模具49上,第三电动丝杠模组31持续移动,第二托架35远离铝板,便于后续冲压,之后第一电动丝杠模组2移动端向左移动,再次放置铝板。
53.冲压结构包括:气缸47、上模具48以及下模具49;
54.条形架23上壁面且横跨第三条形凹槽安装有安装架58,气缸47安置于安装架58下壁面,气缸47驱动端上安装有安装座50,上模具48安置于安装座50上,下模具49安置于条形台1上壁面且与上模具48位置相对应;
55.实际操作时:条形架23起到支撑作用,用于支撑气缸47,气缸47驱动端下降,带动上模具48上下升降,第二移动送料结构将铝板放置在下模具49上,之后气缸47驱动端下降,带动上模具48下降,对铝板进行冲压形成,成型时,人工可以根据铝板大小进行调整冲压位置,人工可以手动摆放铝板,进行冲压。
56.作为优选的技术方案,更进一步地,第二驱动安装座27下壁面固定有第一顶杆51,第一顶杆51下壁面固定有第二滚轮52;通过第二滚轮52,便于第二驱动安装座27移动时,起到移动支撑作用。
57.作为优选的技术方案,更进一步地,支撑架6下壁面且靠近四角处均固定有第二顶杆53,每个第二顶杆53下壁面均安装有垫片54;通过垫片54,在支撑架6移动时,起到移动支撑作用。
58.作为优选的技术方案,更进一步地,第一导杆7以及第二导杆14上均固定有垫圈55。
59.作为优选的技术方案,更进一步地,第一滑架8上开设有第一螺纹口,第一导杆7上开设有与第一螺纹口相匹配的第一螺纹槽,第一螺纹口内插装有与第一螺纹槽相搭接的第一螺钉56;通过第一螺钉56,用于固定第一滑架8。
60.作为优选的技术方案,更进一步地,第二滑架15上开设有第二螺纹口,第二导杆14上开设有与第二螺纹口相匹配的第二螺纹槽,第二螺纹口内插装有与第二螺纹槽相搭接的第二螺钉57;第二螺钉57用于固定第二滑架15。
61.上述技术方案仅体现了本发明技术方案的优选技术方案,本技术领域的技术人员对其中某些部分所可能做出的一些变动均体现了本发明的原理,属于本发明的保护范围之内。