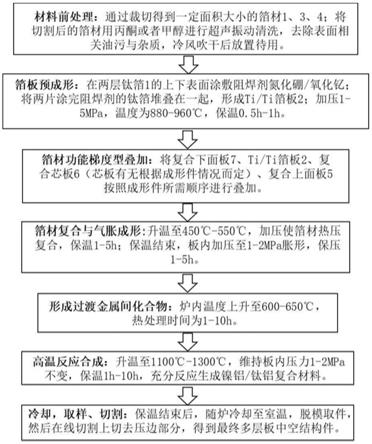
1.本发明涉及金属结构件加工方法领域,尤其涉及由不同种金属箔材形成的金属间化合物层状复合材料的制备以及高温下结构气胀成形与扩散焊接的加工方法。
背景技术:2.为满足航空航天领域飞行器结构轻质、高强、减振、耐腐蚀、耐高温的要求,复合材料构件以及中空结构件被广泛的运用在该领域。
3.镍铝和钛铝材料具有轻质、高强、耐腐蚀、耐高温的作用,是具有良好前景的材料,该层状复合材料可以通过箔材叠加以及结合相关复合方法制备得到。目前,针对层状复合材料的制备,国内外大多数是采用热压复合法、轧制复合法以及爆炸复合法,由于热压复合法工艺简单,针对该方法的相关研究在国内外是较为成熟的。多层板中空结构件具有轻质、减振的作用,国内外针对该类结构件的成形大多数是采用超塑成形/扩散连接工艺,目前该工艺也被广泛运用于航空航天领域。
4.国家专利局于2013年4月24日公告了一份名为“一种层状材料及其制备方法”、申请号为“201310026951.1”的中国发明专利,其中提出了镍铝层状复合材料制备方法。其主要流程为:首先对箔材进行相关前处理,然后将镍箔与铝箔交替叠加,层合板上下表面都是镍箔;将叠层好的箔材放入模具中,升高温度并施加一定的压力,保温一段时间后卸压,得到初始层合板材料;继续升高温度,保温一段时间,然后降至中高温,同时增大施加压力,保温一段时间后随炉冷却至室温,即可得到镍铝层状复合材料板。该发明解决了现有镍铝材料制备方法所制备的镍铝材料本质脆性的问题,为制备该类层状复合材料提供了很好的借鉴,尤其为钛、镍、铝三种材料的热压复合制备提供良好的借鉴,但是,镍铝材料在何种条件下的塑性能力比较好依然是需要继续探究的问题。
5.国家专利局于2018年7月27日公告了一份名为“一种超塑成形/扩散连接三层空心构件制备方法”、申请号为“201611016005.9”的中国发明专利,其中提出了三层空心结构的制备方法。其主要流程为:首先对芯板和面板进行表面处理,对芯板涂覆阻焊剂,将芯板放入上下面板之间,并在面板上下两侧加上包套,最终形成五层板材;对五层板材进行封焊,并留有气道,然后焊接气管;检测密封板的气密性后,装炉加热升温,扩散连接;扩散连接完后,缓慢通气加压胀形,胀形结束后,保压一段时间;最后随炉冷却后,拆除包套,得到最终结构件。该发明采用硬包套成形的方法,高温条件下硬包套能提供足够的表面摩擦力和协调面板的变形速率,使内部加强筋成形过程中对面板的拉应力不足以使面板产生变形,与此同时,成形过程中采用了变温控制以实现成形速率的控制,这些方式都为提高三层板成形精度提供了良好的借鉴。但是由于本身面板并不是层状复合材料板,依然需要探究层状复合材料制备与三层板结构气胀成形工艺耦合问题,同时,也需要考虑通气过程中箔材漏气、窜气问题。
6.针对现有需求,有人提出了将镍铝/钛铝功能梯度型层状复合材料的制备与多层板中空结构件的成形相结合的一体化工艺,即镍铝/钛铝采用热压复合法制备,多层板中空
件采用高温气胀成形的方法。但是,针对现有工艺,依然存在以下几个关键性技术问题:1、箔材如何叠加实现功能梯度型层状复合材料;2、采用何种热压复合流程能够解决气胀时箔材分离,加压不漏气、不窜气的问题;3、由于镍铝/钛铝材料本身的脆性问题,将采用何种工艺参数去很好的实现芯板的胀形过程;4、如何实现材料复合制备与气胀成形的工艺耦合问题。
技术实现要素:7.本发明针对以上问题,提出了一种层状复合材料多层板中空结构制备方法,可将钛铝/镍铝功能梯度型层状复合材料制备和多层板中空结构气胀成形工艺有机结合,很好的实现了中空结构件轻质、高强、减振、耐腐蚀、耐高温的功能,以满足航空航天领域飞行器结构轻质、高强、减振、耐腐蚀、耐高温的要求。
8.本发明的技术方案为:按以下步骤进行制备:步骤1、材料前处理;步骤1.1、将箔材通过裁切得到预设面积的钛铂1、镍箔3以及铝箔4;步骤1.2、将切割后的钛铂1、镍箔3以及铝箔4进行清洗,去除表面相关油污与杂质,冷风吹干后放置待用;步骤2、箔板预成形:将两片钛铂1堆叠在一起通过扩散连接形成ti/ti箔板2,并在ti/ti箔板2中留有多个气道;步骤3、箔材功能梯度型叠加:先将镍箔3、钛箔1、铝箔4遵从功能梯度型的材料设计要求堆叠形成复合下面板7、复合芯板6、复合上面板5,其中,根据成形件中是否具有复合芯板6来确定是否堆叠复合芯板6,后在面板接触处放入ti/ti箔板2;同时,在各个气道的道口处焊接上通气管;步骤4、箔材复合与气胀成形:将堆叠好的箔材放入真空炉里的胀形模具中,加热加压,并通气管缓慢对ti/ti箔板2内部加压;步骤5、形成过渡金属间化合物:维持物料内外的压力,加热至600-650℃,进行低温热处理;步骤6、nial/tial高温反应合成:维持物料内外的压力,加热至1100-1300℃,进行高温热处理;步骤7、随炉冷却,取样:将结构随炉冷却,待冷却至室温后,脱模取件。
9.步骤1.1中所用原材料分别为纯镍箔、纯钛箔以及纯铝箔,箔材厚度比为钛箔:铝箔:镍箔=1:1:0.6,箔材切割面积为200mm
×
200mm。
10.步骤2具体为:步骤2.1、在两层钛铂1的上下表面分别涂覆多道阻焊剂,所述阻焊剂为氮化硼或氧化钇;相邻两道阻焊剂之间留有空隙,从而在焊接之后在多道阻焊剂所在的位置形成多个气道;步骤2.2、将涂覆阻焊剂的两片钛铂1堆叠在一起;步骤2.3、将叠加好的两片钛铂1放入真空扩散炉里的热压模具中,先对模具加热升温,加热到880-960℃,升温速率为10℃/min,然后对模具加载1-5mpa的压力,保温0.5-1h后冷却,得到经扩散连接的ti/ti箔板2。
11.步骤5低温热处理时间为1-10h,步骤6高温热处理时间为1-10h。
12.在加工两层板中空整体壁板时,步骤3、步骤4具体为:步骤3、箔材功能梯度型叠加;步骤3.1a、先将镍箔3、钛箔1、铝箔4遵从功能梯度型的材料设计要求堆叠形成复合下面板7以及复合上面板5;复合上面板以及复合下面板都分为上半部分和下半部分;复合上面板的上半部分包括交替堆叠的镍箔和铝箔,并且复合上面板的上半部分的顶层为镍箔、底层为铝箔;复合上面板的下半部分包括交替堆叠的钛箔和铝箔,并且复合上面板的下半部分的顶层为钛箔、底层为钛箔;复合下面板的上半部分包括交替堆叠的钛箔和铝箔,并且复合下面板的上半部分的顶层为铝箔、底层也为钛箔;复合下面板的下半部分包括交替堆叠的镍箔和铝箔,并且复合下面板的下半部分的顶层为铝箔、底层为镍箔;步骤3.2a、将复合下面板7、ti/ti箔板2、复合上面板5从下到上依次进行叠加;步骤3.3、在堆叠好的箔材四周用氩弧焊点焊一下,防止箔材错位,同时在各个气道的道口处焊接上通气管;步骤4、箔材复合与气胀成形;步骤4.1a、将堆叠好的箔材放入真空炉里的胀形模具中,先对模具缓慢升温,达到温度后,对上模进行加压,然后进行保温,使得箔材能充分焊合;步骤4.2、保温结束后,先增大上模压力,使其大于胀形压力,维持上模压力一直到实验结束,然后经由通气管缓慢对ti/ti箔板2内部缓慢加载压力并保压。
13.步骤4中热压复合加载压力为3-10mpa,升温温度为450-500℃,升温速率为10℃/min,达到温度后,保温时间为1-5h;保温结束后,胀形加载压力为1-2mpa,保压时间为1-5h。
14.在加工三层板中空舵翼时,步骤3、步骤4具体为:步骤3、箔材功能梯度型叠加;步骤3.1b、将镍箔3、钛箔1、铝箔4遵从功能梯度型的材料设计要求堆叠形成复合下面板7、复合芯板6以及复合上面板5;复合上面板以及复合下面板都分为上半部分和下半部分;复合上面板的上半部分包括交替堆叠的镍箔和铝箔,并且复合上面板的上半部分的顶层为镍箔、底层为铝箔;复合上面板的下半部分包括交替堆叠的钛箔和铝箔,并且复合上面板的下半部分的顶层为钛箔、底层也为钛箔;复合芯板包括交替堆叠的钛箔和铝箔,并且复合芯板的顶层为铝箔、底层为钛箔;复合下面板的上半部分包括交替堆叠的钛箔和铝箔,并且复合下面板的上半部分的顶层为铝箔、底层为钛箔;复合下面板的下半部分包括交替堆叠的镍箔和铝箔,并且复合下面板的下半部分的顶层为铝箔、底层为镍箔;步骤3.2b、将复合下面板7、第一块ti/ti箔板2、复合芯板6、第二块ti/ti箔板2、复
合上面板5从下到上依次进行叠加;步骤3.3、在堆叠好的箔材四周用氩弧焊点焊一下,防止箔材错位,同时在各个气道的道口处焊接上通气管;步骤4、箔材复合与气胀成形;步骤4.1b、将堆叠好的箔材放入真空炉里的胀形模具中,先对上模进行加压,使其大于胀形压力,维持压模压力一直到实验结束,进一步对模具内抽真空,抽完真空后对模具缓慢升温,达到温度后,充气加压,然后进行保温,使得箔材能充分焊合;步骤4.2、保温结束后,将模具内压力卸至为零,然后经由通气管缓慢对ti/ti箔板2内部缓慢加压并保压。
15.步骤4中模具真空度在1
×
10-3
pa以下,抽真空后先升温至450-500℃,升温速率为10℃/min,达到温度后,加载压力为3-10mpa,然后保温1-5h;保温结束后,加载压力为1-2mpa,保压时间为1-5h。
16.本发明可以满足航空航天领域飞行器结构轻质、高强、减振、耐腐蚀、耐高温的要求,同时为了解决层状复合材料制备与结构成形工艺耦合问题、气胀时箔材分离、箔材间漏气与窜气问题以及钛铝和镍铝本身脆性难塑性成形问题。
17.总的来说,本发明具有以下有益效果:一、本发明能够实现三层板中空结构层状复合材料制备以及结构气胀成形一体化工艺,该一体化成形是本案的创新点一,能够节省加工时间以及加工成本。
18.二、本发明采取了预成形箔板的方法,该方法是本案的创新点二,能够解决钛合金在低温无法扩散焊接的问题、气胀时箔材分离问题以及通气时漏气、窜气的现象。首先纯钛在低温无法扩散焊合,预成形可以解决焊合问题;上、中、下面板接触处是气胀时通气的区域,通过将上、中、下面板接触处的箔材先预焊成箔板,保证了通气区域焊接质量,使得通气时不漏气、不窜气;即使上、中、下复合面板之间的箔材未焊合好,由于先预成形了箔板,箔板间通气部位焊合质量好,这样可以使得气胀过程正常进行,待胀形结束时,未焊合箔材在压力作用下,能继续焊合。
19.三、本发明采取了箔材低温复合时气胀成形的方法,然后高温形成nial/tial层状复合材料,这样很好的解决了nial/tial材料由于脆性大而难以较大变形的问题,这是本案创新点三。在450℃-550℃时箔材之间未生成金属间化合物或者生成少量金属间化合物,此时,整个材料塑性性能较好,是完成芯板胀形的最佳时刻。
20.四、本发明上、中、下层合面板箔材叠加方式是呈现功能梯度型,这样上下面板能够实现外表面耐高温,内部不需要耐高温的温度梯度型结构,这是本案的创新点四。超高音速飞行器需要满足耐高温的要求,层合面板上表面采用ni/al箔材叠加方式,下表面采取ti/al箔材叠加方式,中间以al箔作为过渡材料,这样得到的复合材料能够很好的满足功能性要求。
21.五、本发明采用了多层板中空结构,材料采用nial/tial功能梯度型层状复合材料,能够使结构满足轻质、高强、减振、耐腐蚀、耐氧化的要求。多层板中空结构本身就有轻质减振的作用,nial/tial功能梯度型层状复合材料满足密度小,强度高,耐腐蚀以及耐氧化的作用。
附图说明
22.图1是本发明的工作流程图;图2是ti/ti箔板预成形流程图;图3是两层中空整体壁板的加工流程图;图4是三层板中空舵翼的加工流程图;图5是两层中空整体壁板最终成形结构图;图6是三层板中空舵翼最终成形结构图。
23.图中1是钛箔,2是ti/ti箔板,3是镍箔,4是铝箔,5是复合上面板,6是复合芯板,7是复合下面板,8是上模,9是下模。
具体实施方式
24.为能清楚说明本专利的技术特点,下面通过具体实施方式,并结合其附图,对本专利进行详细阐述。
25.实施例一:本案例为两层板中空整体壁板结构成形,如图1-3和5所示,其中,所用箔材为n6纯镍箔、ta2纯钛箔以及1060纯铝箔,下面结合附图进行详细说明,按以下步骤进行制备:步骤1、材料前处理;步骤1.1、将箔材通过裁切得到预设面积的钛铂1、镍箔3以及铝箔4;其中所用原材料分别为n6纯镍箔、ta2纯钛箔以及1060纯铝箔,箔材厚度比为钛箔:铝箔:镍箔=1:1:0.6,三种箔材厚度大小为钛箔为0.1mm,铝箔为0.1mm,镍箔为0.06mm,箔材切割面积为200mm
×
200mm。
26.步骤1.2、将切割后的钛箔1、镍箔3以及铝箔4用丙酮或者甲醇进行15-30min超声振动,去除表面相关油污与杂质,冷风吹干后放置待用。
27.步骤2、箔板预成形;步骤2.1、在两层钛箔1的上下表面分别涂覆多道阻焊剂,所述阻焊剂为氮化硼或氧化钇;相邻两道阻焊剂之间留有空隙,从而在焊接之后在多道阻焊剂所在的位置形成多个气道。
28.步骤2.2、将涂覆阻焊剂的两片钛箔1堆叠在一起。
29.步骤2.3、将叠加好的两片钛箔1放入真空扩散炉里的热压模具中,先对模具加热升温,加热到880-960℃,升温速率为10℃/min,然后对模具加载3-5mpa的压力,保温0.5-1h后冷却,得到经扩散连接的ti/ti箔板2。
30.预成形ti/ti箔板的方法是本案例的一个创新点,能够解决钛合金在低温无法扩散焊接的问题、气胀时箔材分离问题以及通气时漏气、窜气的现象。首先纯钛在低温无法扩散焊合,预成形可以解决焊合问题;而上、下面板之间是气胀时通气的区域,通过先将上、下面板之间的箔材预焊成箔板,可有效保证通气区域焊接质量,使得通气时不漏气、不窜气;即使上、下复合面板与箔板之间未焊合好,但由于先预成形了箔板,箔板间通气部位焊合质量好,这样可以使得气胀过程正常进行,待胀形结束时,未焊合箔材在压力作用下,还能继续焊合。
31.步骤3、箔材功能梯度型叠加;
步骤3.1a、先将镍箔3、钛箔1、铝箔4遵从功能梯度型的材料设计要求堆叠形成复合下面板7以及复合上面板5;复合上面板以及复合下面板都分为上半部分和下半部分;复合上面板的上半部分包括交替堆叠的镍箔和铝箔,并且复合上面板的上半部分的顶层为镍箔、底层为铝箔;复合上面板的下半部分包括交替堆叠的钛箔和铝箔,并且复合上面板的下半部分的顶层为钛箔、底层为钛箔;复合下面板的上半部分包括交替堆叠的钛箔和铝箔,并且复合下面板的上半部分的顶层为铝箔、底层也为钛箔;复合下面板的下半部分包括交替堆叠的镍箔和铝箔,并且复合下面板的下半部分的顶层为铝箔、底层为镍箔;步骤3.2a、将复合下面板7、ti/ti箔板2、复合上面板5从下到上依次进行叠加。
32.步骤3.3、在堆叠好的箔材四周用氩弧焊点焊一下,防止箔材错位,同时在气道的道口处焊接上通气管。
33.本案例中上、下复合面板箔材叠加方式是呈现功能梯度型,这样上下面板能够实现外表面耐高温,内部不需要耐高温的温度梯度型结构,这是本案例的另一个创新点。超高音速飞行器需要满足耐高温的要求,层合面板上部采用ni/al箔材叠加方式,下部采取ti/al箔材叠加方式,中间以al箔作为过渡材料,这样得到的复合材料能够很好的满足功能性要求。
34.步骤4、箔材复合与气胀成形;步骤4.1a、将堆叠好的箔材放入真空炉里的胀形模具中,所述模具包括上摸8和下模9,,先对模具缓慢升温至450-550℃,达到温度后,对上模进行加压至5-10mpa,保温3-5h,使得箔材能充分焊合。
35.步骤4.2、保温结束后,先增大上模压力,使其大于胀形压力,维持上模压力一直到实验结束,然后经由通气管缓慢对ti/ti箔板2内部缓慢加载1-2mpa的压力,保压3-5h。
36.本案例中采取了箔材复合时气胀成形的方法,然后高温形成nial/tial层状复合材料,这样很好的解决了nial/tial材料由于脆性大而难以较大变形的问题,这是本案例又一个创新点。在450℃-550℃时箔材之间未生成金属间化合物或者生成少量金属间化合物,此时,整个材料塑性性能较好,是完成芯板胀形的最佳时刻。
37.步骤5、形成过渡金属间化合物;保压结束后,将炉内继续上升至600-650℃,维持ti/ti箔板2内的压力不变,在该温度下热处理5-10h。
38.该热处理过程是使箔材间充分反应生成nial3和tial3,金属间化合物nial3和tial3具有高熔点,可以有效避免高于660℃时铝箔熔化,这样为后面高温反应生成nial和tial做准备。
39.步骤6、nial/tial高温反应合成;低温热处理结束后,将炉内温度继续上升至1100-1300℃,维持ti/ti箔板2内的压力不变,保温5-10h。
40.保温结束后,箔材间充分反应生成nial和tial,最终形成具备nial及tial层状复
合材料的两层板中空整体壁板结构。
41.步骤7、随炉冷却,取样;将结构随炉冷却,待冷却至室温后,脱模取件。
42.最后,可借助线切割切去压边部分,得到最终的多层板中空结构件。
43.实施例二:本案例为三层板中空舵翼结构成形,如图1、2、4、6所示,其中,所用箔材为n6纯镍箔、ta2纯钛箔以及1060纯铝箔,下面结合附图进行详细说明,按以下步骤进行制备:步骤1、材料前处理;步骤1.1、将箔材通过裁切得到预设面积的钛铂1、镍箔3以及铝箔4;其中所用原材料分别为n6纯镍箔、ta2纯钛箔以及1060纯铝箔,箔材厚度比为钛箔:铝箔:镍箔=1:1:0.6,三种箔材厚度大小为钛箔为0.1mm,铝箔为0.1mm,镍箔为0.06mm,箔材切割面积为200mm
×
200mm。
44.步骤1.2、将切割后的钛箔1、镍箔3以及铝箔4用丙酮或者甲醇进行15-30min超声振动,去除表面相关油污与杂质,冷风吹干后放置待用。
45.步骤2、箔板预成形;步骤2.1、在两层钛箔1的上下表面分别涂覆多道阻焊剂,所述阻焊剂为氮化硼或氧化钇;相邻两道阻焊剂之间留有空隙,从而在焊接之后在多道阻焊剂所在的位置形成多个气道。
46.步骤2.2、将涂覆阻焊剂的两片钛箔1堆叠在一起。
47.步骤2.3、将叠加好的两片钛箔材1放入真空扩散炉里的热压模具中,先对模具加热升温,加热到880-960℃,升温速率为10℃/min,然后对模具加载3-5mpa的压力,保温0.5-1h时间后冷却,得到经扩散连接的ti/ti箔板2。
48.预成形ti/ti箔板的方法是本案例的一个创新点,能够解决钛合金在低温无法扩散焊接的问题、气胀时箔材分离问题以及通气时漏气、窜气的现象。首先纯钛在低温无法扩散焊合,预成形可以解决焊合问题;上、中、下面板三者之间都是气胀时通气的区域,通过将上、中、下面板之间的箔材先预焊成箔板,保证了通气区域焊接质量,使得通气时不漏气、不窜气;即使上、中、下复合面板与箔板之间未焊合好,由于先预成形了箔板,箔板间通气部位焊合质量好,这样可以使得气胀过程正常进行,待胀形结束时,未焊合箔材在压力作用下,能继续焊合。
49.步骤3、箔材功能梯度型叠加;步骤3.1b、将镍箔3、钛箔1、铝箔4遵从功能梯度型的材料设计要求堆叠形成复合下面板7、复合芯板6以及复合上面板5;复合上面板以及复合下面板都分为上半部分和下半部分;复合上面板的上半部分包括交替堆叠的镍箔和铝箔,并且复合上面板的上半部分的顶层为镍箔、底层为铝箔;复合上面板的下半部分包括交替堆叠的钛箔和铝箔,并且复合上面板的下半部分的顶层为钛箔、底层也为钛箔;复合芯板包括交替堆叠的钛箔和铝箔,并且复合芯板的顶层为铝箔、底层为钛箔;复合下面板的上半部分包括交替堆叠的钛箔和铝箔,并且复合下面板的上半部分
的顶层为铝箔、底层为钛箔;复合下面板的下半部分包括交替堆叠的镍箔和铝箔,并且复合下面板的下半部分的顶层为铝箔、底层为镍箔;步骤3.2b、将复合下面板7、第一块ti/ti箔板2、复合芯板6、第二块ti/ti箔板2、复合上面板5从下到上依次进行叠加。
50.步骤3.3、在堆叠好的箔材四周用氩弧焊点焊一下,防止箔材错位,同时在气道的道口处焊接上通气管。
51.本案例中上、下复合面板及复合芯板叠加方式是呈现功能梯度型,这样上下面板能够实现外表面耐高温,内部不需要耐高温的温度梯度型结构,这是本案例的另一个创新点。超高音速飞行器需要满足耐高温的要求,层合面板上部采用ni/al箔材叠加方式,下部采取ti/al箔材叠加方式,中间以al箔作为过渡材料,这样得到的复合材料能够很好的满足功能性要求。
52.步骤4、箔材复合与气胀成形;步骤4.1b、将堆叠好的箔材放入真空炉里的胀形模具中,所述模具包括上摸8和下模9,先对上模进行加压,使其大于胀形压力,维持压模压力一直到实验结束,进一步对模具内抽真空,真空度在1
×
10-3
pa以下,抽完真空后先对模具缓慢升温至450-500℃,升温速率为10℃/min,达到温度后,充气加载5-10mpa的压力,然后保温3-5h,使得箔材能充分焊合。
53.步骤4.2、保温结束后,将模具内压力卸至为零,然后经由通气管缓慢对ti/ti箔板2内部缓慢加载1-2mpa的压力,保压3-5h。
54.本案例中采取了箔材复合时气胀成形的方法,然后高温形成nial/tial层状复合材料,这样很好的解决了nial/tial材料由于脆性大而难以较大变形的问题,这是本案例又一个创新点。在450℃-550℃时箔材之间未生成金属间化合物或者生成少量金属间化合物,此时,整个材料塑性性能较好,是完成芯板胀形的最佳时刻。
55.步骤5、形成过渡金属间化合物;保压结束后,将炉内继续上升至600-650℃,维持ti/ti箔板2内的压力不变,在该温度下热处理5-10h。
56.该热处理过程是使箔材间充分反应生成nial3和tial3,金属间化合物nial3和tial3具有高熔点,可以有效避免高于660℃时铝箔熔化,这样为后面高温反应生成nial和tial做准备。
57.步骤6、nial/tial高温反应合成;低温热处理结束后,将炉内温度继续上升至1100-1300℃,维持ti/ti箔板2内的压力不变,保温5-10h。
58.保温结束后,箔材间充分反应生成nial和tial,最终形成具备nial/tial层状复合材料的三层板中空舵翼结构。
59.步骤7、随炉冷却,取样;将结构随炉冷却,待冷却至室温后,脱模取件。
60.最后,可借助线切割切去压边部分,得到最终的多层板中空结构件。
61.本发明具体实施途径很多,以上所述仅是本发明的优选实施方式,应当指出,对于本技术领域的普通技术人员来说,在不脱离本发明原理的前提下,还可以作出若干改进,这
些改进也应视为本发明的保护范围。