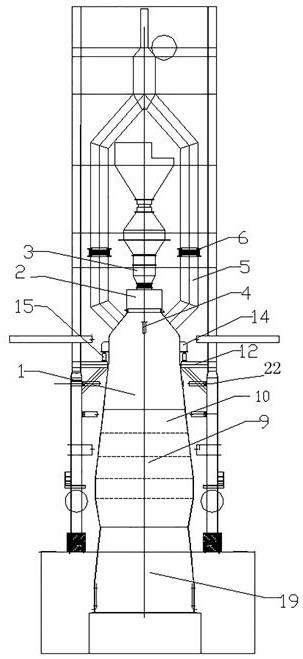
1.本发明涉及炼铁高炉炉体维修技术领域,具体涉及一种炼铁高炉炉体中段变形开裂整体更换方法。
背景技术:2.炼铁高炉生产过程中,因为冶炼方式、高炉炉壳结构形式或者炉壳冷却能力不足等因素的影响。经常会出现炉本体中段炉内冷却设施(冷却壁)大面积破损的情况,冷却壁大面积破损之后,炉内炽热的炉料与炉壳直接接触,此时炉外采用打水降温护炉,在内外大温差(400℃-800℃)的影响下,对应的炉壳钢结构发生开裂、变形,造成炉内煤气泄漏、炉体顶部下沉、炉顶设备受到拉伸也发生泄漏或破裂,炉体上煤气含量严重超标,直接造成高炉无法进行正常生产操作。此时,炉本体上部和下部(炉缸)往往尚处于完好状况。
3.这种状况下,如果采取炉体整体拆除重建,不但工期长、且浪费大,因此采用更换炉本体中段的维修方式是最经济、施工周期最短的方法。而常规的施工方法一种是对炉壳分块进行更换,然后安装冷却壁,这种方法因焊口多应力集中、施工周期长,很少采用。另一种则是对炉本体上段进行固定支撑,这种方法克服了炉壳分块更换的缺点,但无法实现炉体结构复原及无法恢复炉喉钢圈的标高及水平度,现有技术无法解决上述技术问题。
技术实现要素:4.本发明的目的是为了解决现有技术高炉炉体中段更换中存在的技术问题,提供了一种一种炼铁高炉炉体中段变形开裂整体更换方法。
5.为了达到上述目的,本发明采用以下技术方案:1)确定炉体需要整体更换的位置及数量并核算炉体上部利旧段(1)的重量、外形尺寸,并确定与其连接的炉顶备件;2)加工新冷却壁及新炉壳,且加工与炉体上部利旧段连接的终带新炉壳时,终带新炉壳的高度为设计高度加富裕量;3)高炉休风降料面停炉后,在炉体上部利旧段两侧的炉体框架处安装支撑顶升钢结构框架,并在炉体上部利旧段上固定支撑座;4)完成炉体中部更换段冷却壁的拆除及炉外水冷管道的割除;并将炉体上部利旧段上部连接的工艺管道拆除;5)在支撑顶升钢结构框架和支撑座之间安装同步液压千斤顶,并对炉体上部利旧段进行预顶,预顶力为炉体上部利旧段重量的1.2倍;6)测量出炉体上部利旧段顶部炉喉钢圈的标高、上表面水平偏差,确定当下炉喉钢圈因炉体结构变形产生的下沉量和侧倾量,并在与炉喉钢圈同一平面的炉顶框架上作标记点,确定当下炉喉钢圈相对炉顶框架的位置关系;7)将炉体上部利旧段与炉体中部更换段之间的原炉壳带间安装焊缝进行切割分离;
8)操作液压千斤顶,继续顶升炉体上部利旧段,顶升量为终带新炉壳高度中的富裕量再加上40-50毫米,然后安装保护支墩,并在保护支墩的顶部支垫钢垫板,并保证钢垫板与支撑座之间留有间隙,之后操作液压千斤顶回落,使保护支墩承载达到顶升载荷的80%;9)拆除炉体中部更换段的全部炉壳并清理掉炉体下部利旧段与炉体中部更换段之间的接缝;10)之后安装炉体中部更换段的新炉壳,逐带调整炉体中心线,直至所有炉壳全部安装完成,并将除终带新炉壳上环缝以外的所有炉壳焊缝焊接完成;11)切割调整终带新炉壳高度中的富裕量,使炉体上部利旧段与炉体中部更换段炉壳之间的间隙量为炉喉钢圈实测标高-设计标高-(3mm-5mm);12)按照炉壳间连接环焊缝加工要求,热切割终带新炉壳与炉体上部利旧段之间的坡口并进行修磨;13)操作液压千斤顶起升10毫米,之后拆除全部保护支墩,并支垫钢垫板;14)之后完成终带新炉壳与炉体上部利旧段炉壳焊缝的焊接,之后进行焊缝无损检测,达到合格后拆除清理支撑顶升钢结构框架、支撑座。
6.15)之后完成炉体中部更换段冷却壁的安装、焊接及配管,完成全部炉体中部更换段的更换施工,并连接好炉体上部利旧段上的工艺管道。
7.进一步地,步骤1)中根据高炉炉体变形开裂状况、炉内冷却壁损坏程度及炉顶钢圈标高、水平位移变化程度,确定炉体需要整体更换的位置及数量。
8.进一步地,步骤2)中终带新炉壳的富裕量为为停炉后检测炉喉钢圈与设计标高之间的差值+2倍的炉壳环焊缝宽度。
9.进一步地,步骤5)中同步液压千斤顶的可顶升量为终带新炉壳高度中的富裕量再加上50~60毫米。
10.进一步地,步骤8)中钢垫板与支撑座之间的间隙为5 mm
ꢀ‑
10mm,并测量确认各支撑点钢垫板上平面与支撑座下平面间间距偏差小于1毫米后,操作液压千斤顶回落。
11.进一步地,步骤9)中清理掉炉体下部利旧段与炉体中部更换段之间的接缝,将其热切割,使每一部分均处于同一水平面,水平偏差不大于2毫米,然后按照焊接要求将其表面及内外两侧打磨平滑,确保85%以上的表面露出金属光泽。
12.进一步地,步骤12)中,坡口修磨后在终带新炉壳的上沿均布每间隔1~1.5米安装导向板,导向板的厚度不小于炉壳厚度的0.6倍。
13.进一步地,步骤13)中,作液压千斤顶多次回落、起升,每次回落确保液压千斤顶缸头与支撑座下平面出现3~5毫米的间隙,起升时,炉体上部利旧段的炉壳脱离导向板;且在液压千斤顶反复起升、回落过程中,检查炉喉钢圈中心点相对炉体中心线之间的位移,以及炉喉钢圈上平面的水平偏差,计算调整终带新炉壳与炉体上部利旧段炉壳的焊接坡口调整垫板的厚度,直至检查炉喉钢圈中心点相对炉体中心线之间的位移、炉喉钢圈上平面水平偏差均优于设计要求。
14.进一步地,步骤14)中,组对终带新炉壳与炉体上部利旧段炉壳,完成组对焊缝的焊接。
15.本发明相对于现有技术,具有以下有益效果:
本发明充分利用如今普遍采用的框架式高炉的高炉框架、大吨位电动同步液压千斤顶顶升控制系统、全面考虑炉役后期炉体结构与原始设计之间的差异,通过综合考虑损失量补偿、施工安全、施工效益、施工质量保证等诸多方面,辅以对应的操作方式和施工方法,安全、优质、高效的实现了高炉炉体中段变形开裂整体更换,使维修后的高炉炉体及炉顶结构恢复到原始设计状态。通过此发明的实施,实现了高炉炉体结构再造,本发明可以彻底消除了高炉炉体下沉、进而避免炉顶设备受拉伸频繁开裂的危险。
16.本发明通过支撑顶升操作时,通过适当参数的设置,彻底消除了炉顶钢圈因炉体变形产生的偏移和倾斜。本发明通过支撑顶升,为炉体上部炉壳与新炉壳之间焊缝坡口的现场加工、修磨及间隙调整提供了有力的保障,进而保证了焊缝的焊接质量,整体上保证了高炉的施工质量,实现了“修旧为新”最大程度保证了高炉大中修后的施工质量和炉役寿命。
附图说明
17.图1为本发明炼铁高炉炉体整体示意图的主视图。
18.图2为本发明炼铁高炉炉体示意图。
19.图3为本发明支撑架构示意图。
20.图4为本发明炉体中段拆除后示意图。
21.图5为本发明终带新炉壳安装图。
22.图6为图5中新旧炉壳安装调整位置的放大图。
23.附图标记含义如下:1. 炉体上部利旧段;2.布料器;3.流下密阀;4.探尺(法兰);5.上升管道;6.膨胀节;7.新冷却壁;8.新炉壳;9.炉体中部更换段;10.终带新炉壳;11.炉后钢圈;12.支撑顶升钢结构框架;13.支撑座;14.炉外水冷管道;15.同步液压千斤顶;16.安装焊缝;17.保户支墩;18.钢垫板;19.炉体下部利旧段;20.导向板;21. 焊接坡口调整垫板;22.炉口框架。
具体实施方式
24.下面结合附图和具体实施例对本发明作进一步说明。
25.如图1-6所示,一种炼铁高炉炉体中段变形开裂整体更换方法,其特征是,包括以下步骤:1)根据高炉炉体变形开裂状况、炉内冷却壁损坏程度及炉顶钢圈11标高、水平位移变化程度,确定炉体需要整体更换的位置及数量,并核算炉体上部利旧段1的重量、外形尺寸,并确定与其连接的炉顶备件。
26.2)加工新冷却壁及新炉壳,且加工与炉体上部利旧段1连接的终带新炉壳10时,终带新炉壳10的高度为设计高度加富裕量。终带新炉壳10的富裕量为为停炉后检测炉喉钢圈11与设计标高之间的差值+2倍的炉壳环焊缝宽度(根据现场测量结果确定)。
27.3)高炉休风降料面停炉后,在炉体上部利旧段1两侧的炉体框架处安装支撑顶升钢结构框架12,并在炉体上部利旧段1上固定支撑座13。支撑顶升钢结构框架12包括与炉体框架22水平安装的支持架体以及倾斜安装在炉体框架22上的倾斜支撑架。
28.4)完成炉体中部更换段9冷却壁的拆除及炉外水冷管道14的割除。施工过程中,通
过探尺4法兰设置炉内施工活动吊盘,拆除布料器2、节流下密阀3后,在炉喉钢圈11上方设置施工用吊装设施,拆除上升管道上的膨胀节6,实现炉壳与工艺管道的连接拆除。
29.5)在支撑顶升钢结构框架12和支撑座13之间安装同步液压千斤顶15,并对炉体上部利旧段1进行预顶,预顶力为炉体上部利旧段1重量的1.2倍。
30.6)测量出炉体上部利旧段1顶部炉喉钢圈11的标高、上表面水平偏差,通过对比炉喉钢圈11的设计标高,确定当下炉喉钢圈11因炉体结构变形产生的下沉量和侧倾量,并在与炉喉钢圈11同一平面的炉顶框架上作标记点,确定当下炉喉钢圈11相对炉顶框架的位置关系。
31.7)将炉体上部利旧段1与炉体中部更换段9之间的原炉壳带间安装焊缝16使用热切割工具进行切割分离。此时观察大吨位同步电动液压千斤顶15的预顶力逐渐下降,直至稳定。检查确认炉体上部利旧段1与周围结构全部分离,且液压千斤顶15可顶升量为终带新炉壳10高度中的富裕量再加上50~60毫米。
32.8)操作液压千斤顶15,继续顶升炉体上部利旧段1,顶升量为终带新炉壳10高度中的富裕量再加上40-50毫米,然后安装保护支墩17,并在保护支墩17的顶部支垫钢垫板18,钢垫板18与支撑座13之间的间隙为5 mm
ꢀ‑
10mm,并测量确认各支撑点钢垫板18上平面与支撑座13下平面间间距偏差小于1毫米后,操作液压千斤顶15回落,使保护支墩17承载达到顶升载荷的80%。
33.9)拆除炉体中部更换段9的全部炉壳并清理掉炉体下部利旧段19与炉体中部更换段9之间的接缝,将其热切割,使每一部分均处于同一水平面,水平偏差不大于2毫米,然后按照焊接要求将其表面及内外两侧打磨平滑,确保85%以上的表面露出金属光泽。
34.10)之后安装炉体中部更换段9的新炉壳,逐带调整炉体中心线,直至所有炉壳全部安装完成,并将除终带新炉壳10上环缝以外的所有炉壳焊缝焊接完成。
35.11)切割调整终带新炉壳10高度中的富裕量,使炉体上部利旧段1与炉体中部更换段9炉壳之间的间隙量为炉喉钢圈11实测标高-设计标高-(3mm-5mm),并参照炉喉钢圈11上平面水平偏差值,对间隙量进行微调。
36.12)按照炉壳间连接环焊缝加工要求,热切割终带新炉壳10与炉体上部利旧段1之间的坡口并进行修磨。坡口修磨后在终带新炉壳10的上沿均布每间隔1~1.5米点焊安装导向板20,导向板20的厚度不小于炉壳厚度的0.6倍。
37.13)操作液压千斤顶15起升10毫米,之后拆除全部保护支墩17,并支垫钢垫板18。作液压千斤顶15多次回落、起升,每次回落确保液压千斤顶15缸头与支撑座13下平面出现3~5毫米的间隙,起升时,炉体上部利旧段1的炉壳脱离导向板20;且在液压千斤顶15反复起升、回落过程中,检查炉喉钢圈11中心点相对炉体中心线之间的位移,以及炉喉钢圈11上平面的水平偏差,计算调整终带新炉壳10与炉体上部利旧段1炉壳的焊接坡口调整垫板21的厚度,直至检查炉喉钢圈11中心点相对炉体中心线之间的位移、炉喉钢圈11上平面水平偏差均优于设计要求。
38.14)之后组对终带新炉壳10与炉体上部利旧段1炉壳,完成组对焊缝的焊接。焊接到垫板时就拆掉导向板20。之后进行焊缝无损检测,达到合格后拆除清理支撑顶升钢结构框架12、支撑座13。
39.15)之后完成炉体中部更换段9冷却壁的安装、焊接及配管,完成全部炉体中部更
换段9的更换施工,并连接好炉体上部利旧段1上的工艺管道。