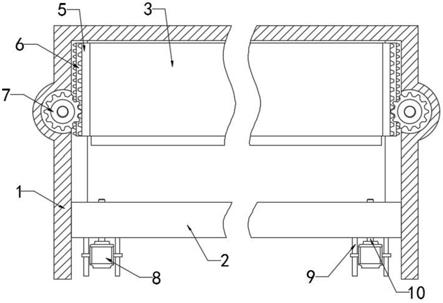
1.本技术涉及折弯机的技术领域,尤其是涉及一种折弯机进刀深度调节机构。
背景技术:2.折弯机是一种能够对薄板进行折弯的机器,其结构主要包括支架、工作台和夹紧板,工作台置于支架上,工作台由底座和压板构成,底座通过铰链与夹紧板相连,底座由座壳、线圈和盖板组成,线圈置于座壳的凹陷内,凹陷顶部覆有盖板。使用时由导线对线圈通电,通电后对压板产生引力,从而实现对压板和底座之间薄板的夹持。由于采用了电磁力夹持,使得压板可以做成多种工件要求,而且可对有侧壁的工件进行加工,操作上也十分简便。
3.但是,现有的弯折机的弯折机构中压板大多通过液压机构等进行驱动,压板在下压过程中运行速度一致,不便于对压板的下压精度进行控制,从而导致折弯机在进行非90
°
的弯折时存在一定的偏差,导致弯折效果不佳。因此,本领域技术人员提供了一种折弯机进刀深度调节机构,以解决上述背景技术中提出的问题。
技术实现要素:4.为了解决上述背景技术中提出的问题,本技术提供一种折弯机进刀深度调节机构。
5.本技术提供的一种折弯机进刀深度调节机构采用如下的技术方案:
6.一种折弯机进刀深度调节机构,包括支架,所述支架的底端水平固定连接有支撑板,且支架的内侧滑嵌有压板,所述支架两侧竖直端均设置有第一伺服电机,且第一伺服电机的外侧通过电动伸缩杆和支架之间传动连接,所述第一伺服电机的输出轴上均套设有第一齿轮盘和第二齿轮盘,所述压板的两侧均设置有第一卡齿条和第二卡齿条,所述第一卡齿条对应第一齿轮盘设置,第二卡齿条对应第二齿轮盘设置,所述第一齿轮盘和第二齿轮盘之间间距大于第一卡齿条和第二卡齿条之间间距,且第一齿轮盘直径大于第二齿轮盘。
7.通过采用上述技术方案,电动伸缩杆对第一伺服电机的位置进行传动,对第一齿轮盘和第二齿轮盘与压板之间的的啮合与否进行控制,从而对传动的方式进行变化,提升传动的效果。
8.优选的,所述第一卡齿条的卡齿密度小于第二卡齿条的卡齿密度,所述第一齿轮盘和第二齿轮盘的卡齿分别对应第一卡齿条和第二卡齿条设置。
9.通过采用上述技术方案,第一卡齿条和第二卡齿条密度不同,使得两个齿轮盘对两个卡齿条的传动效果不同,一个可以获得更大的行程,另一个可以获得更大的精度。
10.优选的,所述支撑板两侧的下方均设置有第二伺服电机,且第二伺服电机的输出轴均固定连接有螺纹杆,并且螺纹杆贯穿支撑板与其螺纹连接,所述第二伺服电机的外侧均设置有用于其径向限位的限位杆。
11.通过采用上述技术方案,第二伺服电机对螺纹杆的传动,实现螺纹杆在轴向上的
位置调节,显示对螺纹杆顶端位置的精确调整。
12.优选的,所述螺纹杆的顶端转动连接有转动块,且转动块的外侧中心对称固定连接有两个滑移杆,且两个滑移杆分别贯穿支撑板滑嵌于限位杆中。
13.通过采用上述技术方案,转动块通过滑移杆进行径向的限位,保证其和压板的始终对应,便于对压板位置进行监控。
14.优选的,所述转动块上开设有凹槽,且凹槽与压板位置对应设置,并且转动块的内侧设置有压力传感器,所述压力传感器通过处理器和第一伺服电机之间通讯连接。
15.通过采用上述技术方案,压力传感器对压板位置进行监控,从而通过处理器对第一伺服电机的转动进行控制,提升装置下压的精度。
16.综上所述,本技术包括以下有益技术效果:
17.通过在压板的两侧均设置两组卡齿条,两组卡齿条和第一伺服电机输出轴上两个齿轮盘之间分别进行啮合,即实现了快速传动,又可以实现提升装置的精度,以此提升第一伺服电机对于压板精度的控制,提升装置的实用性;通过在支撑板的两侧均设置第二伺服电机,第二伺服电机对螺纹杆顶端的转动块进行精确的位置调节,转动块内侧的压力传感器和压板下边缘位置接触,进一步提升对压板下行距离的精确监控,同时对压板的水平度进行检测,避免板材出现两侧弯折程度不同的情况。
附图说明
18.图1是本技术实施例中一种折弯机进刀深度调节机构的纵剖正视结构示意图;
19.图2是本技术实施例中一种折弯机进刀深度调节机构的传动机构俯视结构示意图;
20.图3是本技术实施例中一种折弯机进刀深度调节机构的限制机构俯视结构示意图。
21.附图标记说明:1、支架;2、支撑板;3、压板;5、第一卡齿条;6、第二卡齿条;7、第一齿轮盘;8、第二伺服电机;9、限位杆;10、螺纹杆;11、第一伺服电机;12、第二齿轮盘;13、滑移杆;14、转动块;15、压力传感器;16、电动伸缩杆。
具体实施方式
22.以下结合附图1-3对本技术作进一步详细说明。
23.本技术实施例公开一种折弯机进刀深度调节机构。参照图1-3,一种折弯机进刀深度调节机构,包括支架1,支架1的底端水平固定连接有支撑板2,且支架1的内侧滑嵌有压板3,支架1两侧竖直端均设置有第一伺服电机11,第一伺服电机11轴线垂直于压板3端面设置,第一伺服电机11的外侧通过电动伸缩杆16和支架1之间传动连接,电动伸缩杆16的固定端和第一伺服电机11之间固定连接,电动伸缩杆16的输出端和支架1的外壁固定连接,对第一伺服电机11径向进行限位的同时,实现对第一伺服电机11的轴向位置调节,第一伺服电机11的输出轴上均套设有第一齿轮盘7和第二齿轮盘12,压板3的两侧均设置有第一卡齿条5和第二卡齿条6,第一卡齿条5对应第一齿轮盘7设置,第二卡齿条6对应第二齿轮盘12设置,第一齿轮盘7和第二齿轮盘12之间间距大于第一卡齿条5和第二卡齿条6之间间距,且第一齿轮盘7直径大于第二齿轮盘12,第一卡齿条5的卡齿密度小于第二卡齿条6的卡齿密度,
第一齿轮盘7和第二齿轮盘12的卡齿分别对应第一卡齿条5和第二卡齿条6设置,两个卡齿条之间最大间距小于两个齿轮盘之间的最小间距,保证在进行齿轮盘位置切换时,压板3的两侧失去支撑而掉落;
24.支撑板2两侧的下方均设置有第二伺服电机8,且第二伺服电机8的输出轴均固定连接有螺纹杆10,优选的螺纹杆10的螺距采用5mm,提升装置精度,并且螺纹杆10贯穿支撑板2与其螺纹连接,第二伺服电机8的外侧均设置有用于其径向限位的限位杆9支撑板2两侧的下方均设置有第二伺服电机8,且第二伺服电机8的输出轴均固定连接有螺纹杆10,并且螺纹杆10贯穿支撑板2与其螺纹连接,第二伺服电机8的外侧均设置有用于其径向限位的限位杆9,第二伺服电机8和限位杆9之间轴向滑动,转动块14上开设有凹槽,且凹槽与压板3位置对应设置,并且转动块14的内侧设置有压力传感器15,压力传感器15通过处理器和第一伺服电机11之间通讯连接,对压力传感器15进行压力数值的预设,在达到预设值时将信号传输至处理器中,处理器进行处理后,将停止运行指令发送至第一伺服电机11的控制机构,从而第一伺服电机11停止运作,实现对于压板3位置的精确控制,同时处理器对两个压力传感器15的数值进行对比,保证压板3的水平度,从而提升板材的压制效果。
25.本技术实施例一种折弯机进刀深度调节机构的实施原理为:将板材放置在支撑板2上,此时启动第一伺服电机11转动,传动输出轴上第一伺服电机11通过第一齿轮盘7实现对第一卡齿条5的传动,从而压板3在支架1的内侧向下滑移,实现对于板材的折弯操作,在进行非90
°
的折弯操作时,在压板3下行至靠近板材上方位置处时,电动伸缩杆16收缩,传动第一伺服电机11向一侧滑移,此时第一齿轮盘7失去和第一卡齿条5之间的啮合,第二齿轮盘12和第二卡齿条6之间啮合,由于第二卡齿条6卡齿密度小于,从而可以有效提升对于压板3传动距离的精度控制,以此提升对压板3下行距离的精确控制,保证板材的弯曲精度;在压板3下行过程中,第二伺服电机8传动螺纹杆10进行转动,对其顶端的转动块14竖直位置进行精确的调整,位于转动块14上的滑移杆13通过和限位杆9之间相互配合,实现对转动块14的径向进行限制,从而保证其上的凹槽和支撑板2上凹槽方向相同,压板3在下行时,压板3下边缘位置和转动块14内侧压力传感器15上方接触,在压力值达到预设值时,压板3停止向下的运动,以此进一步保证压板3下行的进程,同时,保证对压板3两侧运动的形成进行检测,避免出现由于压板3的两侧行进距离不同,造成板材两侧的压弯效果不同,提升装置的实用性。
26.以上均为本技术的较佳实施例,并非依此限制本技术的保护范围,故:凡依本技术的结构、形状、原理所做的等效变化,均应涵盖于本技术的保护范围之内。