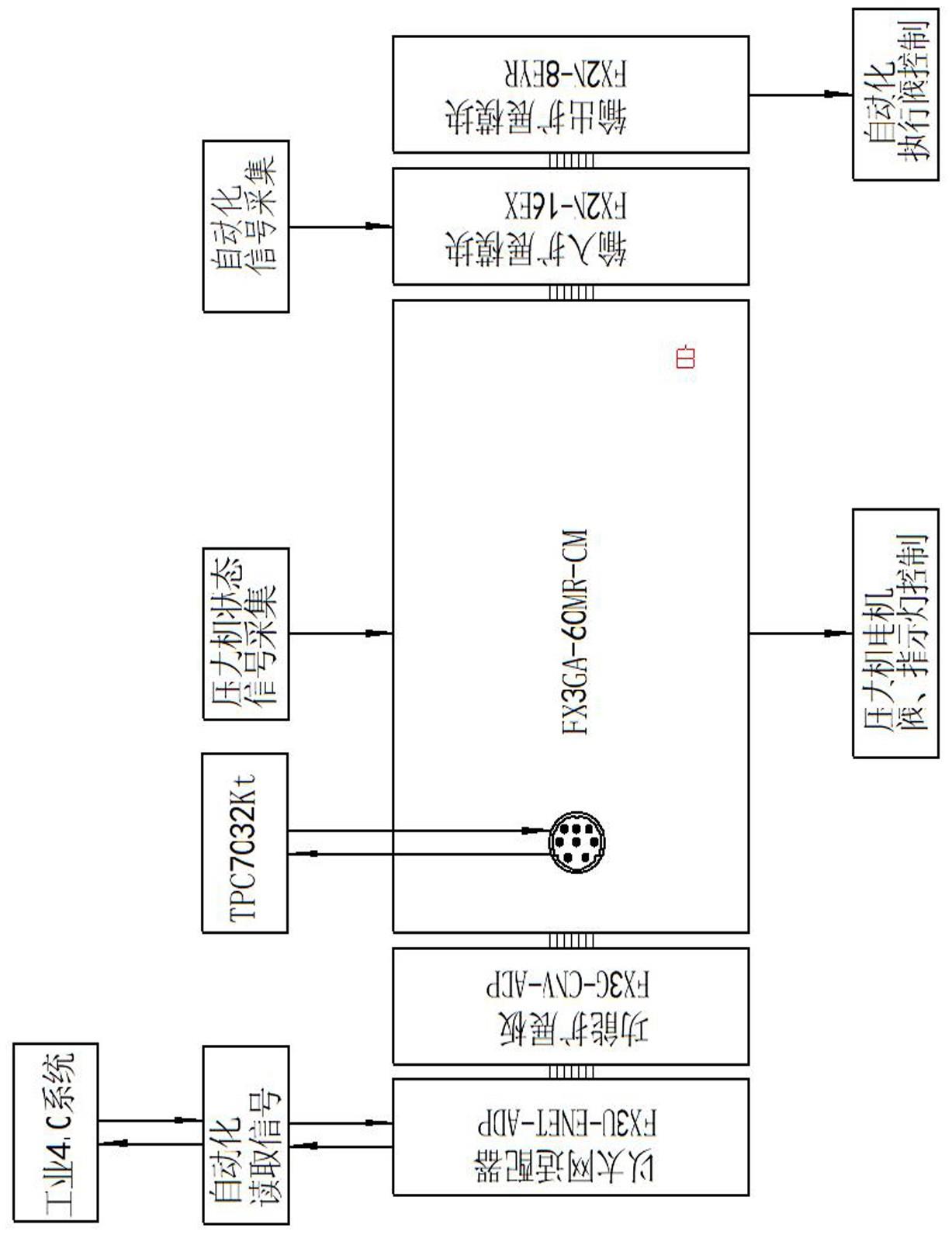
1.本发明涉及压力机领域内的细长类零件端部自动化锻造装置和方法。
背景技术:2.气门零件生产装置由压力机、模具单台组成。将加热炉内的零件取出后放入压力机的模具中,由操作人员操控压力机进行单次规范进行加工后,之后人工取料。由于整个过程中,均为人工操作,无法实现工件的自动抬起、取料、冷却等工序,导致工作效率低,操作繁琐,易导致工人疲劳生产。
技术实现要素:3.本发明的目的是提供一种细长类零件端部自动化锻造装置以及方法,能够提高一种细长类零件端部自动化锻造的便利性,提高生产效率,降低生产成本,且预留mes通讯接口,实现智能化工业生产。
4.为实现上述目的,本发明提供了一种细长类零件端部自动化锻造装置,包括加热炉和压力机,所述加热炉和压力机之间设置有上料机器人,所述上料机器人设置在压力机的一侧,所述压力机配套设置有下料机械臂组、自动喷墨机构,所述下料机械臂组设置在龙门单点机的另一侧,所述自动喷墨机构设置在龙门单电机的正后方,所述加热炉、压力机、上料机器人、下料机械臂组以及自动喷墨机构均与控制柜相连。
5.与现有技术相比,本发明的有益效果在于,通过加热炉批量加热零件,在零件发红后,通过上料机器人将零件放入压力机中,通过压力机对零件进行冲压,冲压完成后,通下料机械臂组将零件从压力机中取出,自动喷墨机构对压力机的下模具进行喷墨,以防止烧红的零件粘在下模具中,不断重复上述过程进行零件的冲压;上述整个过程由控制柜配合检测信号编码器、行程开关,执行元件气动阀,控制元件可编程控制器、以太网通讯模块、触摸屏来实现工件的自动抬起、取料、冷却等工序,提高生产效率,降低生产成本,且预留mes通讯接口,实现智能化工业生产,本发明可以用于细长类零件端部自动化锻造。
6.作为本发明的进一步改进,所述下料机械臂组包括下料架,所述下料架上设置有起升板,所述起升板与设置在下料架下方的下料升降气缸相连,所述起升板上设置有下料伸缩气缸,所述下料伸缩气缸与夹钳相连,所述夹钳还配套设置有导料槽。
7.这样当零件放入压力机后,下料伸缩气缸动作,带动夹钳朝着零件伸出,夹钳将零件夹紧,下料升降气缸动作,带动起升板上升,使得夹钳夹着零件整体上升,之后下料伸缩气缸动作,带动夹钳回缩,同时夹钳松开,零件落入导料槽中,下料伸缩气缸回到初始位置,下料升降气缸带动起升板下降回到初始位置。
8.作为本发明的进一步改进,所述自动喷墨机构包括喷墨架,所述喷墨架上设置有喷墨伸缩气缸,所述喷墨伸缩气缸与喷墨机相连;这样下料伸缩气缸缩回后,喷墨伸缩气缸动作,带动喷墨机朝着压力机的下模具移动并对下模具进行喷墨,避免下模具因为被烧红的零件加热后温度过高,导致零件与下模具之间形成粘黏。
9.为实现上述目的,本发明还提供了一种细长类零件端部自动化锻造方法,具体内容如下,步骤1,设备通电,进行设备自检;步骤2,上料;步骤3,锻造;步骤4,下料;步骤5,喷墨;步骤6,重复步骤2-5。
10.作为本发明的进一步改进,所述步骤1具体内容如下,设备通电,检测加热炉、上料机器人的状态、压力机设备是否正常;如有故障,加热炉不升温加热,上料机器人和压力机不运转,控制柜的触摸屏上显示具体的故障类型与位置;如一切正常,加热炉通电加温,到达设置温度时保持温度;机器人进行准备状态;压力机启动主电机,主电机正反转钥匙拨至正转位置,按压主电机启动按钮,经可编程控制逻辑编程,主电机启动交流接触器得电,通过接触器的主触点接通主电机三相电源,主电机启动运转;选择点动模式,同时按压双手a与双手b按钮,经可编程控制逻辑编程,双联阀线圈1、2同时工作,压力机上的滑块运行至原点位置,运行准备指示灯(hl1)亮;选择单次模式,给出压力机空闲信号。
11.作为本发明的进一步改进,所述步骤2的具体内容如下,压力机空闲状态下,上料机器人将零件从加热炉中取出后置入压力机的下模具中,之后给出一个开始启动信号至压力机。
12.作为本发明的进一步改进,所述步骤3的具体内容如下,步骤3,压力机空闲信号关闭,压力机从原点位置开始冲压,滑块从原点向下滑动到下模具,对放置在下模具中的零件进行冲压,冲压完成后,滑块回到压力机原点处,下顶缸将下模具内冲压后的零件向上顶出。
13.作为本发明的进一步改进,所述步骤4的具体内容如下,下顶缸顶出后0.5秒下料伸缩气缸阀得电,开始伸入,伸出到位后,下料伸缩传感器检测到位后,夹钳的取料爪夹阀得电,夹钳开始夹紧,夹紧0.5秒后,下料升降气缸得电,开始抬升,下料升降传感器检测抬升到位后,下料伸缩气缸失电缩回,下料伸缩传感器检测缩回到位后,取料爪夹阀失电,夹钳松开,同时下料升降气缸失电,开始下降,冲压后的零件落入导料槽中。
14.作为本发明的进一步改进,所述步骤5的具体内容如下,在下料伸缩气缸缩回过程中有一个下料收缩喷墨检测传感器,下料收缩喷墨检测传感器得到信号后,喷墨伸缩气缸得电,开始伸出,喷墨伸缩到位传感器检测伸出到位后喷墨机开始喷墨,喷墨延时0.5秒,喷墨伸缩气缸失电,开始缩回并且有喷墨缩回检测传感器检测缩回到位。
15.作为本发明的进一步改进,步骤2-5为一个工作周期,在触摸屏上设置工作周期为4秒,当实际的工作周期超过4秒后,输出报警信号给总控,总控发出指令,停止将加热炉中发红的零件放入压力机下模具中;在工作周期内,处于导料槽末端的取料有效传感器没有感应到信号,输出报警信号给总控,并提醒操作人员进行排查,防止工件卡死未取出,导致重复冲压,模具损坏;若取料有效传感器检测到导料槽有工件经过的上升沿信号,所有气缸同时回退到位,取料完成,压力机输出空闲信号给总控,然后进行下一个工件生产。
附图说明
16.图1为本发明结构示意图。
17.图2为本发明结控制柜结构示意图。
18.图3为本发明原理框图。
19.图4为本发明电气控制图。
20.图5为本发明可编程控制器输入端定义表一。
21.图6为本发明可编程控制器输入端定义表二。
22.图7为本发明压力机油压、气压状态、工件生产量、机械臂组位置检测等数据表。
23.图8为本发明可编程控制器扩展模块(fx2n-16ex)的输入定义表。
24.图9为本发明可编程控制器扩展模块(fx2n-8eyr)的输出定义表。
25.其中,1加热炉,2上料机器人,3压力机,4下顶缸,5夹钳,6导料槽,7下料伸缩气缸,8起升板。
具体实施方式
26.下面结合附图对本发明进一步说明:如图1-2所示的一种细长类零件端部自动化锻造装置,包括加热炉和压力机,加热炉和压力机之间设置有上料机器人,上料机器人设置在压力机的一侧,压力机配套设置有下料机械臂组、自动喷墨机构,下料机械臂组设置在龙门单点机的另一侧,自动喷墨机构设置在龙门单电机的正后方,加热炉、压力机、上料机器人、下料机械臂组以及自动喷墨机构均与控制柜相连。
27.下料机械臂组包括下料架,下料架上设置有起升板,起升板与设置在下料架下方的下料升降气缸相连,起升板上设置有下料伸缩气缸,下料伸缩气缸与夹钳相连,夹钳还配套设置有导料槽。
28.自动喷墨机构包括喷墨架,喷墨架上设置有喷墨伸缩气缸,喷墨伸缩气缸与喷墨机相连。
29.如图3-9所示一种细长类零件端部自动化锻造方法,具体内容如下,步骤1,设备通电,进行设备自检;设备通电,检测加热炉、上料机器人的状态、压力机设备是否正常;如有故障,加热炉不升温加热,上料机器人和压力机不运转,控制柜的触摸屏上显示具体的故障类型与位置;如一切正常,加热炉通电加温,到达设置温度时保持温度;机器人进行准备状态;压力机启动主电机,主电机正反转钥匙拨至正转位置,按压主电机启动按钮,经可编程控制逻辑编程,主电机启动交流接触器得电,通过接触器的主触点接通主电机三相电源,主电机启动运转;选择点动模式,同时按压双手a与双手b按钮,经可编程控制逻辑编程,双联阀线圈1、2同时工作,压力机上的滑块运行至原点位置,运行准备指示灯(hl1)亮;选择单次模式,给出压力机空闲信号。
30.步骤2,上料;压力机空闲状态下,上料机器人将零件从加热炉中取出后置入压力机的下模具中,之后给出一个开始启动信号至压力机。
31.步骤3,锻造;
压力机空闲信号关闭,压力机从原点位置开始冲压,滑块从原点向下滑动到下模具,对放置在下模具中的零件进行冲压,冲压完成后,滑块回到压力机原点处,下顶缸将下模具内冲压后的零件向上顶出。
32.步骤4,下料;下顶缸顶出后0.5秒下料伸缩气缸阀得电,开始伸入,伸出到位后,下料伸缩传感器检测到位后,夹钳的取料爪夹阀得电,夹钳开始夹紧,夹紧0.5秒后,下料升降气缸得电,开始抬升,下料升降传感器检测抬升到位后,下料伸缩气缸失电缩回,下料伸缩传感器检测缩回到位后,取料爪夹阀失电,夹钳松开,同时下料升降气缸失电,开始下降,冲压后的零件落入导料槽中。
33.步骤5,喷墨;在下料伸缩气缸缩回过程中有一个下料收缩喷墨检测传感器,下料收缩喷墨检测传感器得到信号后,喷墨伸缩气缸得电,开始伸出,喷墨伸缩到位传感器检测伸出到位后喷墨机开始喷墨,喷墨延时0.5秒,喷墨伸缩气缸失电,开始缩回并且有喷墨缩回检测传感器检测缩回到位。
34.步骤6,重复步骤2-5。
35.其中步骤2-5为一个工作周期,在触摸屏上设置工作周期为4秒,当实际的工作周期超过4秒后,输出报警信号给总控,总控发出指令,停止将加热炉中发红的零件放入压力机下模具中;在工作周期内,处于导料槽末端的取料有效传感器没有感应到信号,输出报警信号给总控,并提醒操作人员进行排查,防止工件卡死未取出,导致重复冲压,模具损坏;若取料有效传感器检测到导料槽有工件经过的上升沿信号,所有气缸同时回退到位,取料完成,压力机输出空闲信号给总控,然后进行下一个工件生产。
36.本发明中,细长类零件的加工设备包括的加热炉,上料机器人,龙门单点压力机,下料机械臂组,自动喷墨机构,上述设备由自动化控制系统进行控制,自动化控制系统通过控制柜配合位置检测信号编码器、行程开关,执行元件气动阀,控制元件可编程控制器、以太网通讯模块、触摸屏进行对零件加工过程的自动化控制。
37.加热炉:用于细长类零件的加热,强度降低,做好冲压成形前的准备。
38.上料机器人:用于将加热好的零件从加热炉取出置入压力机下模中。
39.压力机:为龙门单点压力机,用于细长类零件的冲压成型。主要包含有以下几个部件:机身、滑块、电控、主电机、双联阀,主电机和双联阀在机身内部。
40.下料机械臂组:用于冲压完工件自动取料,包含各个采集信号开关及气缸阀。
41.设备通电,检测加热炉、机器人状态、压力机设备是否正常。如有故障,加热炉不升温加热,机器人、压力机不运转,触摸屏上显示具体的故障类型与位置。如一切正常,加热炉通电加温,到达设置温度时保持温度。机器人进行准备状态。压力机启动主电机,主电机正反转钥匙(sa1)拨至正转位置,按压主电机启动按钮(sb1),经可编程控制逻辑编程,主电机启动交流接触器(km1)得电,通过接触器(km1)的主触点接通主电机三相电源,主电机启动运转。选择点动模式,需同时按压双手a(sb3)与双手b按钮,经可编程控制逻辑编程,双联阀线圈1、2同时工作,滑块运行至原点位置,运行准备指示灯(hl1)亮。选择单次模式,给出压力机空闲信号(ka1)。
42.压力机空闲状态下,机器人将零件从加热炉中取出,经过运转,置入压力机下模具中,后给出一个开始启动信号(sb6)给压力机,压力机空闲信号(ka1)关闭。压力机从原点位置开始冲压,滑块到下顶缸顶出角度(sq19)(可通过电子凸轮可以设定,可调范围为180度-270度),下顶缸(yv13)顶出,顶出后0.5秒下料伸缩气缸阀(yv10)得电,开始伸入,伸出到位传感器检测到位(sq10)后,取料爪夹阀(yv15)得电,开始夹紧,取料爪夹阀(yv15)夹紧0.5秒后,下料升降气缸(yv11)得电,开始抬升,下料升降传感器检测抬升到位(sq11)后,下料伸缩气缸(yv10)失电缩回,下料伸缩传感器检测缩回(sq12)到位后,取料爪夹阀(yv15)失电,夹钳松开,同时下料升降气缸(yv11)失电,开始下降。在伸缩气缸缩回过程中有一个传感器(sq17),传感器得到信号后,喷墨伸缩气缸(yv12)得电,开始伸出,喷墨伸缩传感器检测伸出到位(sq13)后开始喷墨,喷墨延时一定时间(触摸屏中可调,本案例经实测为0.5秒),喷墨伸入气缸(yv12)失电,开始缩回并且有传感器检测缩回到位(sq16)。导料槽末端安装有工件取料有效传感器(sq15),检测到导料槽有工件经过的上升沿信号,所有气缸同时回退到位,取料完成。压力机输出空闲信号(ka1)给总控,然后进行下一个工件生产。
43.安全装置:(1)从压力机开始打击到传感器检测到喷墨伸入气缸缩回到位为一个工作周期,触摸屏设置为4秒,实际的工作周期超出设定时间,输出报警信号(ka11)给总控,总控停止将发红工件放入压力机下模具中。
44.(2)在工作周期内,取料有效传感器没有感应到信号,输出报警信号(ka10)给总控,并提醒操作工进行排查,防止工件卡死未取出,导致重复冲压,模具损坏。
45.控制回路:可编程控制器fx3g-60mr-cm为主要控制单元,可编程控制器的输入端分别接入压力机的各功能控制按钮(详见图5),输出端分别接入压力机的执行元件及信号指示(详见图6),用于控制压力机的正确完成冲压过程。
46.在可编程控制器左侧扩展了1个以太网通讯模块,左侧第一个为功能扩展板fx3g-cnv-adp,用于plc与以太网通讯模块的硬件连接。左侧第二个为以太网通讯模块fx3u-enet-adp,用于与智能化工业4.0生产系统连接,实时数据读取,压力机油压、气压状态、工件生产量、机械臂组位置检测等数据(详见图7)。
47.在可编程控制器右侧扩展了2个扩展模块,右侧第一个为输入扩展模块fx2n-16ex,用于采集自动化所需的各类位置信号(详见图8)。右侧第二个为输出扩展模块fx2n-8eyr,用于控制自动化中各气动阀,执行升降、伸缩、喷墨动作,故障指示等(详见图9)。
48.本发明可以提高一种细长类零件端部锻造装置的生产速度,由多人工序变为一机工序,且降低工人操作难度;含有各位置检测,确保工件顶出、取料、喷墨互相协调工作,不相干涉;含有工件检出装置,确保一次一工件,无信号则故障报警,不会出现叠铆现象;含有工件生产周期时间检测功能,在指定周期内完成,如超时故障报警;配有以太网通讯模块,相关工件生产次数、自动化故障等信号能实时发送给智能工业生产系统,以便于计划排产和维护等。