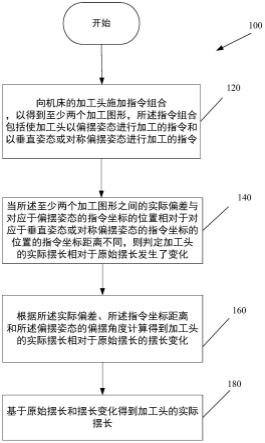
1.本发明涉及机床领域,更具体地涉及用于对机床加工头的实际摆长进行测量的方法及装置。
背景技术:2.对于带有旋转轴的机床,其加工头可以根据加工要求旋转摆动为各种姿态,如图10所示,该可以进行旋转摆动的长度即为加工头的摆长。由于在加工过程中会发生损耗,随着时间的推移,加工头的实际摆长相对于原始摆长会发生变化。更重要的是,在加工不同零件时会有不同的工艺要求,有时会使用不同尺寸的加工头,比如,一台激光切割机床在切割不同零件时就需要使用不同的喷嘴,这些喷嘴的尺寸各不相同,由此也就使得该用于切割的加工头的实际摆长在使用不同喷嘴时也各不相同。
3.从图10可以清楚地看到,不同摆长的加工头((a)中的摆长短于(b)中的摆长)要加工出相同的轨迹(l1=l2时),需要的运动行程是不一样的(c1《c2)。因此,如果机床加工头的实际摆长相对于原始摆长已经有了偏差,那么仍然按照原始摆长值进行的加工就会发生加工轨迹变形,从而严重影响加工精度。因此,需要在机床加工过程中,特别是加工头尺寸有变化时,及时且准确地对加工头的摆长进行测量和修正。根据该修正后的实际摆长及时调整机床加工方案,这样才能保证加工精度。
4.但直接测量加工头的摆长非常困难,且现有的方法也都非常复杂。而且,对于比如前述的激光切割机床来说,换喷嘴又是高频操作,如果每次换喷嘴后都要耗费很多时间来测量摆长,显然会严重影响工作效率。
5.因此,亟需一种新的技术能够以简单且快捷的方式来对加工头的实际摆长进行准确的测量。
技术实现要素:6.本发明就旨在克服现有技术中的上述和/或其它问题。通过本发明所提供的对机床加工头的实际摆长进行测量的方法及装置,只需要最少采样两个加工图形,就能准确、方便地测量出加工头的实际摆长。
7.根据本发明的第一方面,提供一种用于对机床加工头的实际摆长进行测量的方法,包括如下步骤:a)向所述机床的加工头施加指令组合,以得到至少两个加工图形,所述指令组合包括使所述加工头以偏摆姿态进行加工的指令和以垂直姿态或对称偏摆姿态进行加工的指令,所述加工头在所述偏摆姿态下相对于竖直方向偏摆一定角度,所述加工头在所述垂直姿态下垂直于加工表面,所述加工头在所述对称偏摆姿态下相对于竖直方向朝另一方向偏摆所述偏摆姿态的偏摆角度,该偏摆角度小于90
°
,所述偏摆姿态、所述垂直姿态和所述对称偏摆姿态下的所述加工头位于一个平面内;b)当所述至少两个加工图形之间的实际偏差与对应于所述偏摆姿态的指令坐标的位置相对于对应于所述垂直姿态或所述对称偏摆姿态的指令坐标的位置的指令坐标距离不同,则判定所述加工头的实际摆长相对
于原始摆长发生了变化;c)根据所述实际偏差、所述指令坐标距离和所述偏摆姿态的偏摆角度计算得到所述加工头的实际摆长相对于原始摆长的摆长变化;以及d)基于所述原始摆长和所述摆长变化得到所述加工头的实际摆长。
8.根据本发明的第二方面,提供一种用于对机床加工头的实际摆长进行测量的装置,包括采样单元、判定单元和计算单元。所述采样单元用于:向所述机床的加工头施加指令组合,以得到至少两个加工图形,所述指令组合包括使所述加工头以偏摆姿态进行加工的指令和以垂直姿态或对称偏摆姿态进行加工的指令,所述加工头在所述偏摆姿态下相对于竖直方向偏摆一定角度,所述加工头在所述垂直姿态下垂直于加工表面,所述加工头在所述对称偏摆姿态下相对于竖直方向朝另一方向偏摆所述偏摆姿态的偏摆角度,该偏摆角度小于90
°
,所述偏摆姿态、所述垂直姿态和所述对称偏摆姿态下的所述加工头位于一个平面内。所述判定单元用于:当所述至少两个加工图形之间的实际偏差与对应于所述偏摆姿态的指令坐标的位置相对于对应于所述垂直姿态或所述对称偏摆姿态的指令坐标的位置的指令坐标距离不同时判定所述加工头的实际摆长相对于原始摆长发生了变化。所述计算单元用于:根据所述实际偏差、所述指令坐标距离和所述偏摆姿态的偏摆角度计算得到所述加工头的实际摆长相对于原始摆长的摆长变化,并基于所述原始摆长和所述摆长变化得到所述加工头的实际摆长。
9.如果机床加工头的实际摆长相对于原始摆长并未变化,那么在上述指令组合下,无论加工头以何种姿态移动了多少距离(包括距离为零,此时为定点加工),其加工出来的图形之间的偏差应该始终与对应指令坐标的位置之间的距离相等(如果是定点加工,加工图形之间的偏差应该为零,即重合)。因此一旦加工图形之间的偏差与对应姿态下指令坐标的位置之间的距离不同,就说明实际摆长相对于原始摆长发生了变化。本发明的上述方法和装置正巧妙地利用了该原理,将加工头的实际摆长与原始摆长的差异映射到加工图形的偏差距离与指令坐标距离的比较上,指令坐标是已知的,从而只要测量最少一个偏摆姿态指令下的加工图形与最少一个垂直姿态或对称偏摆姿态下的加工图形之间的距离,再结合已知的偏摆姿态下的偏摆角度,就能得到加工头的实际摆长相对于原始摆长的差异,从而对实际摆长进行修正。相比于直接测量摆长,本发明大大地降低了测量难度,且操作起来也十分方便,而且也不需要额外安装硬件设备,能够快速且准确地对加工头的摆长进行测量,从而同时保证加工的精度和效率。
10.如前面所述地,如果机床加工头的实际摆长相对于原始摆长并未变化,那么在上述指令组合下的加工图形之间的偏差应该始终与对应指令坐标的位置之间的距离相等。因此,当所述至少两个加工图形之间的实际偏差与所述指令坐标距离相等,则可以判定所述加工头的实际摆长相对于原始摆长未发生变化,即实际摆长等于原始摆长。
11.较佳地,当上述指令组合涉及垂直姿态下的加工指令,也可以多采样几组偏摆姿态指令下的加工图形。具体地,所述指令组合可包括使所述加工头以所述垂直姿态进行加工的指令和使所述加工头以n个所述偏摆姿态进行加工的指令,n为≥2的自然数。可根据各个偏摆姿态i下的偏摆角度、各个偏摆姿态i下所得到的加工图形相对于所述垂直姿态下的加工图形的实际偏差、以及对应于各个偏摆姿态i的指令坐标的位置相对于对应于所述垂直姿态的指令坐标的位置的指令坐标距离计算得到n个摆长变化(i为1~n),并对所述n个摆长变化求平均值,以得到最终的摆长变化。由此可进一步提高摆长变化的测量精度,从而
更加准确地对加工头的摆长值进行修正。
12.同样地,当所述指令组合涉及对称偏摆姿态下的加工指令,也可以多采样几组偏摆姿态指令下的加工图形和对称偏摆姿态指令下的加工图形。具体地,所述指令组合可包括使所述加工头以n个所述偏摆姿态和n个所述对称偏摆姿态进行加工的指令,n为≥2的自然数。可根据各个偏摆姿态i下的偏摆角度、各个偏摆姿态i下所得到的加工图形相对于各个对应的对称偏摆姿态i下所得到的加工图形的实际偏差、以及对应于各个偏摆姿态i的指令坐标的位置相对于对应于各个对称偏摆姿态i的指令坐标的位置的指令坐标距离计算得到n个摆长变化(i为1~n),并对所述n个摆长变化求平均值,以得到最终的摆长变化。由此可进一步提高摆长变化的测量精度,从而更加准确地对加工头的摆长值进行修正。
13.或者,也可以将上述两种方式结合起来,一部分通过偏摆姿态和对称偏摆姿态的采样来计算摆长变化,另一部分通过偏摆姿态和垂直姿态的采样来计算摆长变化,再将这两部分的摆长变化相加后求平均值。具体地,所述指令组合可包括使所述加工头以(m1+m2)个所述偏摆姿态和m1个所述对称偏摆姿态进行加工的指令以及使所述加工头以所述垂直姿态进行加工的指令,m1和m2皆为≥1的自然数。可根据所述m1个偏摆姿态中各个偏摆姿态i下的偏摆角度、所述m1个偏摆姿态中各个偏摆姿态i下所得到的加工图形相对于所述m1个对称偏摆姿态中各个对应的对称偏摆姿态i下所得到的加工图形的实际偏差、以及对应于各个偏摆姿态i的指令坐标的位置相对于对应于各个对称偏摆姿态i的指令坐标的位置的指令坐标距离计算得到m1个摆长变化(i为1~m1),且可根据所述m2个偏摆姿态中各个偏摆姿态i’下的偏摆角度、所述m2个偏摆姿态中各个偏摆姿态i’下所得到的加工图形相对于所述垂直姿态下的加工图形的实际偏差、以及对应于各个偏摆姿态i’的指令坐标的位置相对于对应于所述垂直姿态的指令坐标的位置的指令坐标距离计算得到m2个摆长变化(i’为1~m2),并对所述(m1+m2)个摆长变化求平均值,以得到最终的摆长变化。由此可进一步提高摆长变化的测量精度,从而更加准确地对加工头的摆长值进行修正。
14.较佳地,对应于所述偏摆姿态、所述垂直姿态和所述对称偏摆姿态的指令坐标的位置可完全相同,即,上述指令组合为定点加工的指令组合,所述指令坐标距离为0。
15.在这种情况下,当所述实际偏差大于0,就可判定所述加工头的实际摆长相对于原始摆长发生了变化,并可根据所述实际偏差和所述偏摆角度直接计算得到所述摆长变化。在通过上述多组采样进行摆长修正时,同样不再需要考虑指令坐标距离。
16.如果机床加工头的实际摆长相对于原始摆长并未变化,那么在上述定点加工指令下,无论加工头呈现何种姿态,其加工出来的图形应该都是重合的,即,偏差距离为0。因此一旦不重合,就说明实际摆长相对于原始摆长有了偏差。由此,可将加工头的实际摆长与原始摆长的差异直接映射到加工图形之间的距离上,从而只要测量最少一个偏摆姿态指令下的加工图形与最少一个垂直姿态或对称偏摆姿态下的加工图形之间的距离,再结合已知的偏摆姿态下的偏摆角度,就能得到加工头的实际摆长相对于原始摆长的差异,从而可以更快、更方便地对实际摆长进行修正。
17.上述加工图形可以是点、直线或曲线。
18.根据本发明的第三方面,还提供一种计算机可读存储介质,其上记录有经编码的指令,当执行该指令时实现如上所述的根据本发明的用于对机床加工头的实际摆长进行测量的方法。
19.通过下面结合附图的详细描述,本发明的其它特征和方面会变得更加清楚。
附图说明
20.通过结合附图对于本发明的示例性实施例进行描述,可以更好地理解本发明,在附图中:
21.图1为根据本发明的用于对机床加工头的实际摆长进行测量的方法的流程图;
22.图2示例性地示出了加工头的偏摆姿态、垂直姿态和对称偏摆姿态;
23.图3(a)和图3(b)分别示出了加工头在摆长不变和摆长发生变化两种情况下在偏摆加工指令下的加工情况;
24.图4示出了偏摆姿态和对称偏摆姿态下加工头的各个参数之间的关系;
25.图5示出了根据本发明的用于对机床加工头的实际摆长进行测量的方法的第一实施方式;
26.图6示出了根据本发明的用于对机床加工头的实际摆长进行测量的方法的第二实施方式;
27.图7示出了根据本发明的用于对机床加工头的实际摆长进行测量的方法的第三实施方式;
28.图8示例性地示出了加工头在定点加工指令下的偏摆姿态、垂直姿态和对称偏摆姿态;
29.图9为根据本发明的用于对机床加工头的实际摆长进行测量的装置的结构框图;以及
30.图10示意性地示出了机床加工头的摆长。
具体实施方式
31.下面将结合具体实施例和附图对本发明作进一步说明,在以下的描述中阐述了更多的细节以便于充分理解本发明,但是本发明显然能够以多种不同于此描述的其它方式来实施,本领域技术人员可以在不违背本发明精神的情况下根据实际应用情况作类似推广、演绎,因此不应以此具体实施例的内容限制本发明的保护范围。
32.除非另作定义,权利要求书和说明书中使用的技术术语或者科学术语应当为本发明所属技术领域内具有一般技能的人士所理解的通常意义。本技术的说明书以及权利要求书中使用的“第一”、“第二”以及类似的词语并不表示任何顺序、数量或者重要性,而只是用来区分不同的组成部分。“一个”或者“一”等类似词语并不表示数量限制,而是表示存在至少一个。“包括”或者“包含”等类似的词语意指出现在“包括”或者“包含”前面的元件或者物件涵盖出现在“包括”或者“包含”后面列举的元件或者物件及其等同元件,并不排除其他元件或者物件。“连接”或者“相连”等类似的词语并非限定于物理的或者机械的连接,也不限于是直接的还是间接的连接。
33.根据本发明的实施例,提供一种用于对机床加工头的实际摆长进行测量的方法。
34.参考图1,其中示出了根据本发明的用于对机床加工头的实际摆长进行测量的方法100。该方法100包括步骤120至步骤180。
35.在步骤120中,向机床的加工头施加指令组合,以得到至少两个加工图形,所述指
令组合包括使加工头以偏摆姿态进行加工的指令和以垂直姿态或对称偏摆姿态进行加工的指令,加工头在所述偏摆姿态下相对于竖直方向偏摆一定角度,加工头在所述垂直姿态下垂直于加工表面,加工头在所述对称偏摆姿态下相对于竖直方向朝另一方向偏摆所述偏摆姿态的偏摆角度,该偏摆角度小于90
°
,偏摆姿态、垂直姿态和对称偏摆姿态下的加工头位于一个平面内。
36.图2中以激光加工头为例示出了加工头的偏摆姿态、垂直姿态和对称偏摆姿态,其中激光束在加工表面上的落点可以保持不变,也可以如图2所示地发生变化。图中的z轴为竖直方向,一般情况下其垂直于加工表面。如图中所示,对加工头施加以偏摆姿态进行加工的指令,偏摆角度为θ,接着再对加工头施加以垂直姿态或对称偏摆姿态进行加工的指令,从而可以得到至少两个加工图形。为方便比较,图2中把三个姿态下的加工图形都标了出来。需要说明的是,如果选择改变激光束在加工表面上的落点位置,那么在不同姿态间进行转换,可以先平移加工头到预期位置、再旋转加工头到预期姿态,也可以先旋转加工头到预期姿态、再平移加工头到预期位置,还可以旋转加工头到预期姿态和平移加工头到预期位置同时进行。
37.在图2所示的例子中,加工后所得到的图形是一条直线,但可以理解,实际操作中也可以对加工头施加指令以得到点或曲线(比如,圆或椭圆)的加工图形。另外,图2中所示出的偏摆姿态和对称偏摆姿态从垂直于纸面的方向观察分别是左偏摆和右偏摆,但可以理解,这两个姿态的偏摆方向也可以互换。
38.回到方法100,接下来在步骤140中,当所述至少两个加工图形之间的实际偏差与对应于偏摆姿态的指令坐标的位置相对于对应于垂直姿态或对称偏摆姿态的指令坐标的位置的指令坐标距离不同,则可判定加工头的实际摆长相对于原始摆长发生了变化。
39.向机床加工头施加加工指令,该加工指令含有指令坐标,该指令坐标基于的是原始尺寸,如果加工头的实际摆长相对于原始摆长并未变化,那么无论加工头怎么偏摆、是否偏摆,所得到的加工图形之间的偏差都应该与对应姿态下指令坐标的位置之间的距离相等,如以上图2所示(由于激光加工时要依靠加工头末端出射的激光射束来进行非接触式加工,所以图2中所示的激光加工中的指令坐标对应的是激光射束在加工表面上的落点的指令坐标)。因此一旦发现所得到的至少两个加工图形之间的偏差与对应姿态下指令坐标的位置之间的距离不同,就说明实际摆长相对于原始摆长有了变化。
40.回到方法100,接下来在步骤160中,根据所述实际偏差、所述指令坐标距离和所述偏摆姿态的偏摆角度计算得到加工头的实际摆长相对于原始摆长的摆长变化。
41.发明人经过潜心研究,发现不仅可以通过观测上述至少两个加工图形之间的实际偏差是否与对应姿态下指令坐标的位置之间的指令坐标距离相等来判断加工头的摆长是否发生了变化,更重要地还可以基于该实际偏差、该指令坐标距离和上述偏摆姿态的偏摆角度直接计算出摆长变化值。
42.如图3(a)所示,假设加工头的当前摆长为l,加工头距离加工表面的垂直距离为h,为了完成从垂直姿态到偏摆姿态的偏摆动作,指令需要通过旋转轴让加工头偏摆角度θ,同时还需要通过平动轴使加工头分别在x轴和z轴方向上运动dx和dz。如果加工头的摆长一直是l,则dx=sin(θ)*(l+h)+x,dz=(1-cos(θ))*(l+h),x即为从垂直姿态下的指令坐标位置到偏摆姿态下的指令坐标位置的距离,即上述指令坐标距离,其可从指令坐标计算而得。
43.但如果摆长发生了变化,不是l,而是l-dl,如图3(b)所示,那么再向加工头发送相同的运动指令(通过旋转轴偏摆角度θ,通过平动轴在x轴和z轴方向上分别运动dx和dz),就将会导致偏摆过程中激光束的落点在x轴方向上相对于指令坐标中的x坐标发生偏移。如图3(b)所示,该偏移s=w-x,其可以从摆长变化值dl和偏摆角度θ直接计算得到,即,s=dl*tan(θ)。
44.因此,只要通过垂直姿态和偏摆姿态的加工指令获得两个加工图形,就可以基于这两个加工图形之间的实际偏差w、垂直姿态下的指令坐标位置到偏摆姿态下的指令坐标位置的距离x以及偏摆角度θ来计算得到摆长变化值dl=(w-x)/tan(θ)。加工图形如果是直线或点,它们之间的偏差即为这两条直线或两个点之间的距离。加工图形如果是曲线,比如圆或椭圆,它们之间的偏差即为这两个圆的圆心或这两个椭圆的中心之间的距离;或者如果加工图形只是一段弧,它们之间的偏差即为这两段弧对应点之间的距离。
45.但发明人同时也发现,其实要获得摆长变化值dl,并非一定要通过垂直姿态和偏摆姿态的加工指令来获得两个加工图形,也可以通过偏摆姿态和对称偏摆姿态的加工指令来获得两个加工图形。如图4所示,假设偏摆姿态的加工头和对称偏摆姿态的加工头之间仍然有一个垂直姿态的加工头,同时假设偏摆姿态下的加工头的指令坐标位置与垂直姿态下的加工头的指令坐标位置相距x1,偏摆姿态和垂直姿态下加工出来的图形实际相距w1,那么按照前述公式可得dl=(w1-x1)/tan(θ);又假设对称偏摆姿态下的加工头的指令坐标位置与垂直姿态下的加工头的指令坐标位置相距x2,对称偏摆姿态和垂直姿态下加工出来的图形实际相距w2,那么按照前述公式可得dl=(w2-x2)/tan(θ)。由此,可以进一步得到dl=[(w1+w2)-(x1+x2)]/(2*tan(θ)),此时将上述假设的垂直姿态的加工头移除,w1+w2=w,即为偏摆姿态和对称偏摆垂直姿态下加工出来的图形之间的实际偏差,x1+x2=x(x1和x2可以相同,也可以不同),即为偏摆姿态下的加工头的指令坐标位置与对称偏摆姿态下的加工头的指令坐标位置之间的距离。这样,基于偏摆姿态和对称偏摆姿态下加工出来的两个图形之间的偏差w、偏摆姿态下的指令坐标位置到对称偏摆姿态下的指令坐标位置的距离x以及偏摆角度θ同样能计算得到摆长变化值dl=(w-x)/(2*tan(θ))。
[0046]
需要特别说明的是,图3(b)中示出的摆长相对于原始摆长是缩短的,可以理解,如果摆长相对于原始摆长是伸长的,即l+dl,此时再向加工头发送相同的运动指令(通过旋转轴偏摆角度θ,通过平动轴在x轴和z轴方向上分别运动dx和dz),激光束的落点将沿着x轴方向相对于指令坐标中的x坐标反向偏移,即,w《x。通过确定w是大于x还是小于x,可以判定加工头的摆长是缩短还是伸长。
[0047]
回到方法100,接下来在步骤180中,基于原始摆长和摆长变化得到加工头的实际摆长。
[0048]
如果原始摆长为l1,当前实际摆长为l2,当计算得到摆长变化值dl后,可以得到实际摆长l2=l
1-dl。如果w》x,说明实际摆长相对于原始摆长缩短了,l2《l1,如图3(b)所示。如果w《x,则说明实际摆长相对于原始摆长伸长了,则l2》l1。
[0049]
上述根据本发明的机床加工头摆长测量方法无需额外安装任何硬件设备,通过巧妙地将加工头的摆长变化映射到加工图形的偏差距离与指令坐标距离(指令坐标是已知的)的比较上,将原本难度较高且较为复杂的摆长测量转化为容易且简单方便操作的图形间的偏差测量。只需要最少一个偏摆姿态指令下的加工图形与最少一个垂直姿态或对称偏
摆姿态下的加工图形,不仅可以快速判断出加工头的摆长是否发生了变化,基于这两个加工图形之间的偏差再结合已知的对应姿态下的指令坐标位置之间的距离和偏摆姿态下的偏摆角度,还能快速准确地计算出摆长变化了多少,从而对实际摆长进行及时修正。相比于传统测量摆长的方法,本发明能够快速且准确地对加工头的摆长进行测量,从而在兼顾加工精度的同时也保证了工作效率。
[0050]
如前面所述地,如果机床加工头的实际摆长相对于原始摆长并未变化,那么在上述加工指令下的加工图形之间的偏差应该与对应姿态下指令坐标的位置之间的距离相等。因此,在上述步骤140中,当所述加工图形之间的偏差与所述指令坐标距离相等,则可以判定所述加工头的实际摆长相对于原始摆长未发生变化,即测量的结果是:实际摆长等于原始摆长。
[0051]
尽管本发明通过采样两个加工图形间的偏差已经能够准确地计算出加工头的摆长变化值,但可选地,也可以通过增加采样的组数来进一步提高摆长变化的计算准确性。
[0052]
具体地,可以对加工头施加以垂直姿态进行加工的指令和以n个偏摆姿态进行加工的指令,n为≥2的自然数。由此,可以得到一个在垂直姿态下加工的图形和n个在偏摆姿态下加工的图形。
[0053]
回到上述方法100的摆长变化计算步骤160,其可进一步包括子步骤1612和子步骤1614,如图5所示。
[0054]
在子步骤1612中,基于上述n个偏摆姿态中的各个偏摆姿态i下的偏摆角度θi、各个偏摆姿态i下所得到的加工图形相对于垂直姿态下的加工图形的实际偏差wi以及对应于各个偏摆姿态i的指令坐标的位置相对于对应于垂直姿态的指令坐标的位置的指令相对距离xi计算得到n个摆长变化dli(i为1~n)。即,摆长变化dli=(w
i-xi)/tan(θi)。
[0055]
在子步骤1614中,对上述n个摆长变化dli求平均值,以得到最终的摆长变化dl。即,最终的摆长变化:
[0056][0057]
再通过上述方法100中的步骤180,可得到实际摆长:
[0058][0059]
同样地,也可以对加工头施加以n个偏摆姿态和n个对称偏摆姿态进行加工的指令,n为≥2的自然数。由此,可以得到n个在偏摆姿态下加工的图形和n个在对称偏摆姿态下加工的图形。
[0060]
再次回到上述方法100的摆长变化计算步骤160,其可进一步包括子步骤1622和子步骤1624,如图6所示。
[0061]
在子步骤1622中,基于上述n个偏摆姿态中的各个偏摆姿态i下的偏摆角度θi、各个偏摆姿态i下所得到的加工图形相对于对应的对称偏摆姿态i下所得到的加工图形的实际偏差wi以及对应于各个偏摆姿态i的指令坐标的位置相对于对应于各个对称偏摆姿态i的指令坐标的位置的指令相对距离xi计算得到n个摆长变化dli(i为1~n)。即,摆长变化dli=(w
i-xi)/(2*tan(θi))。
[0062]
在子步骤1624中,对上述n个摆长变化dli求平均值,以得到最终的摆长变化dl。
即,最终的摆长变化:
[0063][0064]
再通过上述方法100中的步骤180,可得到实际摆长:
[0065][0066]
作为还有一种选择,也可以将上述两种方式结合起来,一部分通过偏摆姿态和对称偏摆姿态的采样来计算摆长变化,另一部分通过偏摆姿态和垂直姿态的采样来计算摆长变化,再将这两部分的摆长变化相加后求平均值。具体地,可以对加工头施加以(m1+m2)个偏摆姿态和m1个对称偏摆姿态进行加工的指令以及以垂直姿态进行加工的指令,m1和m2皆为≥1的自然数。由此,可以得到一个在垂直姿态下加工的图形、(m1+m2)个在偏摆姿态下加工的图形以及m1个在对称偏摆姿态下加工的图形。
[0067]
再次回到上述方法100的摆长变化计算步骤160,其可进一步包括子步骤1632~子步骤1636,如图7所示。
[0068]
在子步骤1632中,根据上述m1个偏摆姿态中各个偏摆姿态i下的偏摆角度θi、上述m1个偏摆姿态中各个偏摆姿态i下所得到的加工图形相对于上述m1个对称偏摆姿态中各个对应的对称偏摆姿态i下所得到的加工图形的实际偏差wi、以及对应于各个偏摆姿态i的指令坐标的位置相对于对应于各个对称偏摆姿态i的指令坐标的位置的指令坐标距离xi计算得到m1个摆长变化dli(i为1~m1)。即,摆长变化dli=(w
i-xi)/(2*tan(θi))。
[0069]
在子步骤1634中,根据上述m2个偏摆姿态中各个偏摆姿态i’下的偏摆角度θ
i’、上述m2个偏摆姿态中各个偏摆姿态i’下所得到的加工图形相对于垂直姿态下的加工图形的实际偏差w
i’、以及对应于各个偏摆姿态i’的指令坐标的位置相对于对应于垂直姿态的指令坐标的位置的指令坐标距离x
i’计算得到m2个摆长变化dl
i’(i’为1~m2)。即,摆长变化dl
i’=(wi’-x
i’)/tan(θ
i’))。
[0070]
在子步骤1636中,对上述m1个摆长变化dli和m2个摆长变化dl
i’求平均值,以得到最终的摆长变化dl。即,最终的摆长变化:
[0071][0072]
再通过上述方法100中的步骤180,可得到实际摆长:
[0073][0074]
通过上述多次采样而计算所得的摆长变化,充分考虑了随机误差对计算带来的影响,因此可以进一步保证所修正的实际摆长符合精度要求。
[0075]
此外,在上述步骤120中向加工头施加的指令组合可以选择为使对应于所述偏摆姿态、所述垂直姿态和所述对称偏摆姿态的指令坐标的位置完全相同,也即,所述指令组合为定点加工的指令组合,如图8所示。在此情况下,各种姿态下的指令坐标的位置之间的距离为0。
[0076]
如果指令组合是使加工头在偏摆姿态下加工的指令和使加工头在垂直姿态下加工的指令,那么摆长变化值dl=(w-x)/tan(θ)实际上就可以简化为dl=w/tan(θ)。同样地,如果指令组合是使加工头在偏摆姿态下加工的指令和使加工头在对称偏摆姿态下加工的指令,那么摆长变化值dl=(w-x)/(2*tan(θ))也可以简化为dl=w/(2*tan(θ))。
[0077]
在定点加工的指令组合下,如果加工头的实际摆长相对于原始摆长并未变化,那么无论加工头怎么偏摆、是否偏摆,所得到的加工图形都应该是重合的,比如如图8所示。而一旦发现所得到的加工图形不重合,即,加工图形之间的偏差大于0,就说明实际摆长相对于原始摆长有了变化,在此情况下,只要基于加工图形之间的偏差w和偏摆角度θ使用上述公式就能计算得到摆长变化值dl。由此,通过采用定点加工的指令组合,本发明将加工头的摆长变化更巧妙地映射到加工图形之间的距离上,从而可以更加快速方便地对加工头的摆长进行测量。
[0078]
如果以上述定点加工的指令组合进行多次采样,那么当对加工头施加以垂直姿态进行定点加工的指令和以n个偏摆姿态进行定点加工的指令时,各个摆长变化的计算公式可以简化为dli=wi/tan(θi),最终的摆长变化计算公式可以简化为:
[0079][0080]
实际摆长的计算公式可以简化为:
[0081][0082]
同样地,当对加工头施加以n个偏摆姿态和n个对称偏摆姿态进行定点加工的指令时,各个摆长变化的计算公式可以简化为dli=wi/(2*tan(θi)),最终的摆长变化计算公式可以简化为:
[0083][0084]
实际摆长的计算公式可以简化为:
[0085][0086]
而当对加工头施加以(m1+m2)个偏摆姿态和m1个对称偏摆姿态进行定点加工的指令以及以垂直姿态进行定点加工的指令时,最终的摆长变化计算公式可以简化为:
[0087][0088]
实际摆长的计算公式可以简化为:
[0089][0090]
至此,描述了根据本发明的用于对机床加工头的实际摆长进行测量的方法。相比于传统方法中直接测量摆长,本发明的测量方法巧妙地将加工头的摆长变化映射到加工图形的偏差距离与指令坐标距离(指令坐标是已知的)的比较上,从而将原本难度较高且较为
复杂的摆长测量转化为容易且操作简单的图形间的偏差测量,由此大大地降低了测量难度,且操作起来也十分方便,而且也不需要额外安装硬件设备,就能够快速且准确地对加工头的摆长进行测量。特别当采用指令坐标位置不变(此时指令坐标距离为0)的定点加工进行采样时,本发明的测量方法实际上将加工头的摆长变化直接映射到了加工图形的偏差距离上,从而可以更加迅速方便地对加工头的摆长进行测量。尤其对于加工头更换频繁的加工机床,比如需要根据不同加工要求更换喷嘴的激光切割机床,本发明的摆长测量方法能够方便、快速且准确地对用于切割的加工头的摆长进行修正,从而无论在初次装机还是更换喷嘴后都能保证切割精度符合工艺要求。
[0091]
根据本发明的实施例,还提供一种计算机可读存储介质,其上记录有经编码的指令,当执行该指令时可实现上述用于对机床加工头的实际摆长进行测量的方法。所述计算机可读存储介质可以包括硬盘驱动器、软盘驱动器、光盘读/写(cd-r/w)驱动器、数字通用磁盘(dvd)驱动器、闪存驱动器和/或固态存储装置等。
[0092]
根据本发明的实施例,还相应地提供一种用于对机床加工头的实际摆长进行测量的装置。
[0093]
参考图9,其中示出了根据本发明的用于对机床加工头的实际摆长进行测量的装置600,其包括采样单元620、判定单元640和计算单元660。
[0094]
采样单元620配置为:向机床的加工头施加指令组合,以得到至少两个加工图形,所述指令组合包括使加工头以偏摆姿态进行加工的指令和以垂直姿态或对称偏摆姿态进行加工的指令。其中,加工头在偏摆姿态下相对于竖直方向偏摆一定角度,加工头在垂直姿态下垂直于加工表面,加工头在对称偏摆姿态下相对于竖直方向朝另一方向偏摆所述偏摆姿态的偏摆角度,该偏摆角度小于90
°
。所述偏摆姿态、所述垂直姿态和所述对称偏摆姿态下的加工头位于一个平面内。
[0095]
判定单元640配置为:当所述至少两个加工图形之间的实际偏差与对应于偏摆姿态的指令坐标的位置相对于对应于垂直姿态或对称偏摆姿态的指令坐标的位置的指令坐标距离不同时,判定加工头的实际摆长相对于原始摆长发生了变化。
[0096]
计算单元660配置为:根据所述实际偏差、所述指令坐标距离和偏摆姿态的偏摆角度计算得到加工头的实际摆长相对于原始摆长的摆长变化,并基于原始摆长和摆长变化得到加工头的实际摆长。
[0097]
可选地,判定单元640还可被配置为:当所述实际偏差与所述指令坐标距离相等,则判定加工头的实际摆长相对于原始摆长未发生变化。
[0098]
可选地,所述指令组合可包括使加工头以垂直姿态进行加工的指令和使加工头以n个偏摆姿态进行加工的指令,n为≥2的自然数。在此情形下,计算单元660还可被配置为:根据各个偏摆姿态i下的偏摆角度和各个偏摆姿态i下所得到的加工图形相对于垂直姿态下的加工图形的实际偏差、以及对应于各个偏摆姿态i的指令坐标的位置相对于对应于垂直姿态的指令坐标的位置的指令坐标距离计算得到n个摆长变化,i为1~n;以及对该n个摆长变化求平均值,以得到最终的摆长变化。
[0099]
可选地,所述指令组合可包括使加工头以n个偏摆姿态和n个对称偏摆姿态进行加工的指令,n为≥2的自然数。在此情形下,计算单元660还可被配置为:根据各个偏摆姿态i下的偏摆角度、各个偏摆姿态i下所得到的加工图形相对于各个对应的对称偏摆姿态i下所
得到的加工图形的实际偏差以及对应于各个偏摆姿态i的指令坐标的位置相对于对应于各个对称偏摆姿态i的指令坐标的位置的指令坐标距离计算得到n个摆长变化,i为1~n;以及对该n个摆长变化求平均值,以得到最终的摆长变化。
[0100]
可选地,所述指令组合可包括使加工头以(m1+m2)个偏摆姿态和m1个对称偏摆姿态进行加工的指令以及使加工头以垂直姿态进行加工的指令,m1和m2皆为≥1的自然数。在此情形下,计算单元660还可被配置为:根据所述m1个偏摆姿态中各个偏摆姿态i下的偏摆角度、所述m1个偏摆姿态中各个偏摆姿态i下所得到的加工图形相对于所述m1个对称偏摆姿态中各个对应的对称偏摆姿态i下所得到的加工图形的实际偏差、以及对应于各个偏摆姿态i的指令坐标的位置相对于对应于各个对称偏摆姿态i的指令坐标的位置的指令坐标距离计算得到m1个摆长变化,i为1~m1;根据所述m2个偏摆姿态中各个偏摆姿态i’下的偏摆角度、所述m2个偏摆姿态中各个偏摆姿态i’下所得到的加工图形相对于垂直姿态下的加工图形的实际偏差、以及对应于各个偏摆姿态i’的指令坐标的位置相对于对应于垂直姿态的指令坐标的位置的指令坐标距离计算得到m2个摆长变化,i’为1~m2;以及对上述(m1+m2)个摆长变化求平均值,以得到最终的摆长变化。
[0101]
可选地,可使对应于所述偏摆姿态、所述垂直姿态和所述对称偏摆姿态的指令坐标的位置完全相同。
[0102]
可选地,上述加工图形可包括点、直线和曲线。
[0103]
上述装置600可以实现如前面所述地根据本发明的用于对机床加工头的实际摆长进行测量的方法。上述在本发明的用于对机床加工头的实际摆长进行测量的方法中适用的很多设计构思和细节同样适用于上述装置600,且可以得到相同的有益技术效果,此处不再赘述。
[0104]
以上通过一些示例性实施例对本发明的各个方面进行了描述。然而,应该理解的是,在不脱离本发明精神和范围的情况下,还可以对上述示例性实施例做出各种修改。例如,如果所描述的技术以不同的顺序执行和/或如果所描述的系统、架构、设备或电路中的组件以不同方式被组合和/或被另外的组件或其等同物替代或补充,也可以实现合适的结果,那么相应地,这些修改后的其它实施方式也落入权利要求书的保护范围内。