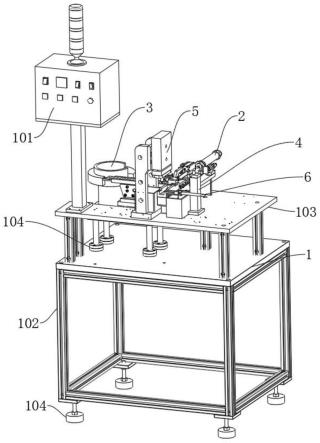
1.本发明涉及机械加工技术领域,尤其涉及一种钢球挤压内孔自动化设备。
背景技术:2.在机加工工艺中,要想得到高质量的加工表面,通常采用铰、拉、磨、镗、研磨、电解加工以及特种加工等来改善零件孔的加工表面质量,零件孔径表面质量的好坏,很大程度取决于零件表面的粗糙程度和硬度。
3.但是,这些加工方法通常会受到一定的局限性,例如,零件内孔的铰和拉削加工,在通常条件下,对零件内孔加工的表面粗糙度只能达到ra1.6~0.8μm,加工的质量较低,而采用钢球挤压内孔加工工艺,可以用简便的办法获得较高的加工质量,因此,急需一种钢球挤压内孔自动化设备来更高效率、更高质量的保证挤压加工工艺。
技术实现要素:4.本发明的目的是为了解决现有的加工方法对零件内孔的加工质量和效率较低的问题,而提出的一种钢球挤压内孔自动化设备。
5.为了实现上述目的,本发明采用了如下技术方案:
6.一种钢球挤压内孔自动化设备,包括:防震机架;控制电箱,安装在所述防震机架的一侧;工件送料机构,安装在所述防震机架上;定位机构,通过安装架安装在所述防震机架靠近工件送料机构的一端,其中,所述定位机构包括凹形板、第一气缸、推动杆、承接板、转动杆、压紧块、t型滑动板、第二气缸,所述凹形板安装在安装架靠近工件送料机构出料口的位置,且靠近所述工件送料机构的位置设有进料口,所述第二气缸安装在所述安装架远离凹形板的一端,所述t型滑动板通过滑轨滑动连接在安装架上,且远离所述第二气缸的一端滑动连接在凹形板内,所述t型滑动板上设有放置有工件的凹槽,所述t型滑动板与第二气缸的伸缩端固定连接,所述第一气缸安装在t型滑动板远离凹形板的一端,所述推动杆安装在第一气缸的伸缩端,所述承接板固定连接在t型滑动板靠近推动杆的下端,所述转动杆转动连接在承接板靠近凹形板的一端,所述压紧块固定连接在转动杆靠近凹形板的一端,且位于所述t型滑动板凹槽的正上方,所述压紧块上设有定位导向孔;钢球送料机构,安装在所述防震机架靠近压紧块的位置;挤压机构,安装在所述防震机架上,且位于所述凹形板远离安装架的一侧;卸料机构,安装在所述防震机架上,且位于所述凹形板远离挤压机构的一侧。
7.优选地,所述安装架上交错设置有两组微调限位组件和缓冲组件。
8.为了便于提高工件内孔加工的精准度,同时还可以对t型滑动板起到缓冲的作用,进一步地,所述微调限位组件包括第一支座、微调螺栓,所述缓冲组件包括第二支座、缓冲器,所述第一支座、第二支座交错设置在安装架的两侧,所述微调螺栓通过螺纹转动连接在第一支座上,所述缓冲器固定连接在第二支座上,所述缓冲器的伸缩端与t型滑动板之间通过连接板固定连接。
9.为了便于提高该设备的整体稳定性,优选地,所述防震机架包括机架底座、安装板,所述安装板通过支腿安装在机架底座上,所述机架底座与安装板的底部均设有防震脚垫,设置在所述安装板底部的防震脚垫通过连接杆与安装板连接,设置在所述安装板底部的防震脚垫坐落在机架底座上。
10.进一步地,所述工件送料机构包括底盘、通震盘、逆时针输送条、直震器、直线导轨,所述底盘安装在安装板上,所述通震盘固定连接在底盘的底部,所述逆时针输送条套接在底盘上,所述直线导轨固定连接在逆时针输送条的下料口处,所述直线导轨远离逆时针输送条的一端与凹形板的进料口固定连接,所述直震器安装在直线导轨的下方。
11.进一步地,所述钢球送料机构包括电机、升降轴、固定板、支撑柱、盖板、导管,所述电机安装在安装板靠近凹形板的位置,所述固定板固定连接在安装板靠近电机的正上方,所述支撑柱固定连接在固定板上,所述升降轴固定连接在电机的输出端,且向上延伸出支撑柱,所述盖板固定连接在支撑柱的上方,所述支撑柱靠近凹形板的一侧上端设有出球孔,所述导管安装在支撑柱靠近出球孔的位置,所述导管远离支撑柱的一端向下倾斜,且与所述压紧块的定位导向孔相贴。
12.更进一步地是,所述凹形板的下端固定连接有传送块,所述传送块的内部设有输送轨道,所述凹形板上设有与输送轨道相贯通的贯穿孔,所述所述传送块靠近支撑柱的一端设有钢球收集盒,所述钢球收集盒靠近输送轨道的出料口处设有相贯通的连接孔。
13.更进一步地是,所述挤压机构包括固定支架、第三气缸、压板、压头,所述固定支架安装在所述安装板上,且位于所述凹形板远离安装架的一侧所述第三气缸固定连接在固定支架靠近凹形板的一侧上端,所述压板固定连接在第三气缸的伸缩端,所述压头安装在压板的下端,且位于所述贯穿孔的正上方。
14.更进一步地是,所述卸料机构包括第四气缸、安装支架、推板,所述第四气缸通过安装支架安装在凹形板靠近第三气缸的正对面,所述固定支架上放置有接料盒。
15.与现有技术相比,本发明提供了一种钢球挤压内孔自动化设备,具备以下有益效果:
16.1、该种钢球挤压内孔自动化设备,通过控制电箱,定位机构、工件送料机构、钢球送料机构、挤压机构、卸料机构的配合使用,与现有加工技术相比,可以自动对工件的内孔进行加工,不仅可以降低工作人员的劳动量,而且加工效率也得到了大大的提升;
17.2、该种钢球挤压内孔自动化设备,通过采用钢球挤压的方式对工件的内孔进行加工,不仅可以对工件的损伤降到最小,而且还可以提高对工件内孔加工的质量,满足了实际工作中的需求,实用性较高;
18.3、该种钢球挤压内孔自动化设备,通过微调限位组件、缓冲组件的设置,提高工件内孔加工的精准度,防止发生错位,对工件造成损坏,还可以对t型滑动板起到缓冲的作用,从而防止t型滑动板发生碰撞,有效的提高了该设备的稳定性。
19.该装置中未涉及部分均与现有技术相同或可采用现有技术加以实现,本发明通过采用钢球挤压的方式对工件的内孔进行加工,与现有的采用铰、拉、磨、镗、研磨、电解等加工技术相比,不仅可以对工件的损伤降到最小,而且还可以提高对工件内孔加工的质量,通过使该设备自动化进行加工,不仅可以降低工作人员的劳动量,而且加工效率也得到了大大的提升,满足了实际工作中的需求,实用性较高,适于推广使用。
附图说明
20.图1为本发明提出的一种钢球挤压内孔自动化设备的整体示意图;
21.图2为本发明提出的一种钢球挤压内孔自动化设备中定位机构与传送块、输送轨道的结构示意图;
22.图3为本发明提出的一种钢球挤压内孔自动化设备中工件送料机构的结构示意图;
23.图4为本发明提出的一种钢球挤压内孔自动化设备中钢球送料机构的结构示意图;
24.图5为本发明提出的一种钢球挤压内孔自动化设备中挤压机构的结构示意图;
25.图6为本发明提出的一种钢球挤压内孔自动化设备图1中的局部结构示意图;
26.图7为本发明提出的一种钢球挤压内孔自动化设备图6中a部分的结构示意图。
27.图中:1、防震机架;101、控制电箱;102、机架底座;103、安装板;104、防震脚垫;2、定位机构;201、凹形板;2001、贯穿孔;202、第一气缸;203、推动杆;204、承接板;205、转动杆;206、压紧块;207、定位导向孔;208、第一支座;209、微调螺栓;2010、t型滑动板;2011、第二支座;2012、缓冲器;2013、连接板;2014、第二气缸;3、工件送料机构;301、底盘;302、通震盘;303、逆时针输送条;304、直震器;305、直线导轨;4、钢球送料机构;401、电机;402、升降轴;403、固定板;404、支撑柱;405、盖板;406、导管;407、钢球收集盒;4071、连接孔;5、挤压机构;501、固定支架;502、第三气缸;503、压板;504、压头;505、接料盒;6、卸料机构;601、第四气缸;602、安装支架;603、推板;7、传送块;701、输送轨道。
具体实施方式
28.下面将结合本发明实施例中的附图,对本发明实施例中的技术方案进行清楚、完整地描述,显然,所描述的实施例仅仅是本发明一部分实施例,而不是全部的实施例。
29.在本发明的描述中,需要理解的是,术语“上”、“下”、“前”、“后”、“左”、“右”、“顶”、“底”、“内”、“外”等指示的方位或位置关系为基于附图所示的方位或位置关系,仅是为了便于描述本发明和简化描述,而不是指示或暗示所指的装置或元件必须具有特定的方位、以特定的方位构造和操作,因此不能理解为对本发明的限制。
30.实施例1:
31.参照图1-图7,一种钢球挤压内孔自动化设备,包括:防震机架1;控制电箱101,安装在防震机架1的一侧;工件送料机构3,安装在防震机架1上;定位机构2,通过安装架安装在防震机架1靠近工件送料机构3的一端,其中,定位机构2包括凹形板201、第一气缸202、推动杆203、承接板204、转动杆205、压紧块206、t型滑动板2010、第二气缸2014,凹形板201安装在安装架靠近工件送料机构3出料口的位置,且靠近工件送料机构3的位置设有进料口,第二气缸2014安装在安装架远离凹形板201的一端,t型滑动板2010通过滑轨滑动连接在安装架上,且远离第二气缸2014的一端滑动连接在凹形板201内,t型滑动板2010上设有放置有工件的凹槽,t型滑动板2010与第二气缸2014的伸缩端固定连接,第一气缸202安装在t型滑动板2010远离凹形板201的一端,推动杆203安装在第一气缸202的伸缩端,承接板204固定连接在t型滑动板2010靠近推动杆203的下端,转动杆205转动连接在承接板204靠近凹形板201的一端,压紧块206固定连接在转动杆205靠近凹形板201的一端,且位于t型滑动板
2010凹槽的正上方,压紧块206上设有定位导向孔207;钢球送料机构4,安装在防震机架1靠近压紧块206的位置;挤压机构5,安装在防震机架1上,且位于凹形板201远离安装架的一侧;卸料机构6,安装在防震机架1上,且位于凹形板201远离挤压机构5的一侧;
32.工件送料机构3包括底盘301、通震盘302、逆时针输送条303、直震器304、直线导轨305,底盘301安装在安装板103上,通震盘302固定连接在底盘301的底部,逆时针输送条303套接在底盘301上,直线导轨305固定连接在逆时针输送条303的下料口处,直线导轨305远离逆时针输送条303的一端与凹形板201的进料口固定连接,直震器304安装在直线导轨305的下方;
33.钢球送料机构4包括电机401、升降轴402、固定板403、支撑柱404、盖板405、导管406,电机401安装在安装板103靠近凹形板201的位置,固定板403固定连接在安装板103靠近电机401的正上方,支撑柱404固定连接在固定板403上,升降轴402固定连接在电机401的输出端,且向上延伸出支撑柱404,盖板405固定连接在支撑柱404的上方,支撑柱404靠近凹形板201的一侧上端设有出球孔,导管406安装在支撑柱404靠近出球孔的位置,导管406远离支撑柱404的一端向下倾斜,且与压紧块206的定位导向孔207相贴;
34.挤压机构5包括固定支架501、第三气缸502、压板503、压头504,固定支架501安装在安装板103上,且位于凹形板201远离安装架的一侧第三气缸502固定连接在固定支架501靠近凹形板201的一侧上端,压板503固定连接在第三气缸502的伸缩端,压头504安装在压板503的下端,且位于贯穿孔2001的正上方;
35.卸料机构6包括第四气缸601、安装支架602、推板603,第四气缸601通过安装支架602安装在凹形板201靠近第三气缸502的正对面,固定支架501上放置有接料盒505;
36.凹形板201的下端固定连接有传送块7,传送块7的内部设有输送轨道701,凹形板201上设有与输送轨道701相贯通的贯穿孔2001,传送块7靠近支撑柱404的一端设有钢球收集盒407,钢球收集盒407靠近输送轨道701的出料口处设有相贯通的连接孔4071;
37.在使用时,工作人员首先将该设备移动到工作指定位置,然后再对其进行固定,防止在进行工作时该设备因发生震动而影响工件的加工精度,固定好后,工作人员再将工件依次放置在逆时针输送条303上,然后再将若干个钢球放置在支撑柱404与升降轴402之间的空腔内,接着再对该设备上的用电设备进行接通电源;
38.前序工作准备好后,此时工作人员再通过控制电箱101控制该设备上的机器进行工作,其中,控制电箱101具备有急停,暂停,启动,计数,故障报警灯等功能,控制整套设备的安全运行,此时工作人员首先控制通震盘302和直震器304进行工作,然后逆时针输送条303上的工件便会在通震盘302的作用下向直线导轨305处移动,当工件移动到直线导轨305上后,工件便会在直震器304的作用下向凹形板201的位置移动,然后最前排的工件便会进入到t型滑动板2010上的凹槽内,通过通震盘302、直震器304的设置,可以使工件稳定的向凹形板201的方向移动,防止出现工件向后移动的现象,有效的提高了该设备在工作时的稳定性,当最前排的工件移动至t型滑动板2010上的凹槽内后,此时启动第一气缸202,使第一气缸202推动推动杆203向凹形板201的一侧移动,然后转动杆205便会在推动杆203的作用下进行轻微转动,然后压紧块206便会对工件进行压紧,接着再启动电机401,使电机401带动升降轴402进行旋转,然后升降轴402再在支撑柱404的配合下使钢球向上移动,当钢球移动到支撑柱404上端出球孔的位置后,便会通过出球孔掉落到导管406上,然后钢球再在自
身重力作用下落入压紧块206的定位导向孔207内,然后再顺着定位导向孔207移动到工件的预加工孔上,接着再启动第二气缸2014,使第二气缸2014推动t型滑动板2010进行移动,从而将工件推送至压头504的正下方,接着再启动第三气缸502,使第三气缸502带动压板503向下移动,压板503再带动压头504向下移动,使压头504穿过压紧块206上的定位导向孔207,并对钢球进行施压,然后钢球便会对工件上的预加工孔进行挤压,当挤压完成后,此时钢球便会通过凹形板201上的贯穿孔2001掉落进传送块7的输送轨道701内,然后钢球便会通过输送轨道701掉落进钢球收集盒407内进行收集,以便下次继续使用,当钢球掉落之后,此时在控制第一气缸202进行回缩,从而使第一气缸202带动推动杆203回到初始位置,然后转动杆205便不会再对压紧块206进行施加压力,从而使压紧块206松开工件;
39.接着工作人员再控制第四气缸601进行工作,使第四气缸601推动推板603进行移动,推板603再将加工好的工件推出凹形板201,并使其掉落进接料盒505内进行收集,最后再控制第二气缸2014、第三气缸502、第四气缸601回缩到初始位置即可完成整个加工过程,然后在重复上述步骤即可连续的对工件进行加工作业;
40.本设备通过采用钢球挤压的方式对工件的内孔进行加工,与现有的采用铰、拉、磨、镗、研磨、电解等加工技术相比,不仅可以对工件的损伤降到最小,而且还可以提高对工件内孔加工的质量,通过使该设备自动化进行加工,不仅可以降低工作人员的劳动量,而且加工效率也得到了大大的提升,满足了实际工作中的需求,实用性较高,适于推广使用。
41.实施例2:
42.参照图1-图7,一种钢球挤压内孔自动化设备,与实施例1基本相同,更进一步的是:安装架上交错设置有两组微调限位组件和缓冲组件,微调限位组件包括第一支座208、微调螺栓209,缓冲组件包括第二支座2011、缓冲器2012,第一支座208、第二支座2011交错设置在安装架的两侧,微调螺栓209通过螺纹转动连接在第一支座208上,缓冲器2012固定连接在第二支座2011上,缓冲器2012的伸缩端与t型滑动板2010之间通过连接板2013固定连接;
43.通过微调限位组件的设置,当第二气缸2014推动t型滑动板2010进行移动时,可以对t型滑动板2010起到微调限位的作用,使压紧块206上的定位导向孔207可以与压头504正对其,从而提高工件内孔加工的精准度,防止发生错位,对工件造成损坏,有效的提高了该设备加工的精准度,通过缓冲组件的设置,当第二气缸2014带动t型滑动板2010进行前后移动时,可以对t型滑动板2010起到缓冲的作用,从而防止t型滑动板2010发生碰撞,有效的提高了该设备的稳定性。
44.实施例3:
45.参照图1-图7,一种钢球挤压内孔自动化设备,与实施例1基本相同,更进一步的是:防震机架1包括机架底座102、安装板103,安装板103通过支腿安装在机架底座102上,机架底座102与安装板103的底部均设有防震脚垫104,设置在安装板103底部的防震脚垫104通过连接杆与安装板103连接,设置在安装板103底部的防震脚垫104坐落在机架底座102上,通过在机架底座102与安装板103的底部均设有防震脚垫104,当该设备进行工作时,可以有效的对产生的震动进行缓冲防震,有效的提高了该设备的整体稳定性。
46.本发明通过采用钢球挤压的方式对工件的内孔进行加工,与现有的采用铰、拉、磨、镗、研磨、电解等加工技术相比,不仅可以对工件的损伤降到最小,而且还可以提高对工
件内孔加工的质量,通过使该设备自动化进行加工,不仅可以降低工作人员的劳动量,而且加工效率也得到了大大的提升,满足了实际工作中的需求,实用性较高,适于推广使用。
47.以上所述,仅为本发明较佳的具体实施方式,但本发明的保护范围并不局限于此,任何熟悉本技术领域的技术人员在本发明揭露的技术范围内,根据本发明的技术方案及其发明构思加以等同替换或改变,都应涵盖在本发明的保护范围之内。