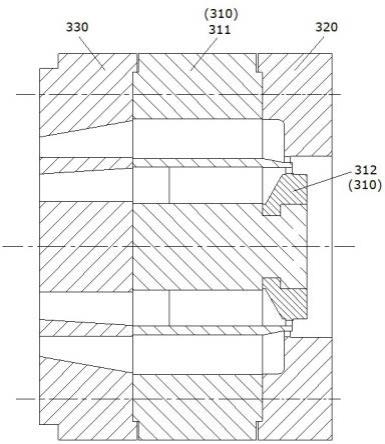
1.本发明涉及电机壳体的挤压模具领域,尤其涉及的是一种电动汽车液冷式电机壳体的挤压模。
背景技术:2.随着新能源电动汽车、大型计算机it设备以及大型矿山设备等行业的发展,开发冷却效率高且适用的新型液冷式电机引起了行业广泛的关注。
3.目前,国产液冷式电机壳铝型材的生产和使用方兴未艾,仍存在有较多的问题,主要表现为两个方面,一方面是型材的大内孔容易出现较大的椭圆现象,即圆度的精度较低,型材在经过锯切成坯料后必须经过二次机械加工,而二次机械加工中容易因为圆度的精度较低造成产品尺寸超差导致报废,若将圆度精度较低的产品投入使用,则会造成电机工作时产生较大噪音,故障率也高;另一方面是型材的大内孔存在有较大的偏心,会导致型材的壁厚出现严重的不均现象,必须经过二次深加工后才能使用,造成二次加工的工作量增大,容易导致局部壁厚出现严重的变薄,降低了产品的强度,在使用过程中易发生穿孔泄漏的现象。
4.而出现这些问题的根本原因还是模具,由于液冷式电机壳型材的结构要复杂得多,实际中的模具所采用的传统结构形式,致使模具的加工复杂、难度大,加工后能达到的精度低,特别是对称性较差、累积误差较大,最终使得挤压成形中各个部位金属流速出现不均匀性或者加大了这种不均匀性的倾向;同时,传统结构形式的模具的制造周期长、互换性较差、寿命偏低,导致型材的生产成本居高不下,制约了国产液冷式电机壳型材的推广使用。
5.如图1所示,图1是现有技术中的典型液冷式电机壳体铝型材断面结构放大图,该液冷式电机壳体100在挤压类产品中属于大型产品,不仅外形尺寸大精度高,其中心处圆形空腔110直径为198mm,用于安装电动机的定子和转子等部件,是电机壳体100的主要安装部位,其尺寸精度特别是圆度和同心度的要求都很高;而且电机壳体100侧壁中的孔腔也较多,侧壁中均布有12个弧形长圆孔作为过水槽120,用于起到冷却的作用。
6.结合图2所示,图2是现有技术中电动汽车液冷式电机壳体挤压模的整体结构图,传统的电动汽车液冷式电机壳体挤压模一般仅由上模210和下模220两部分组成,且上模210的厚度通常是下模220厚度的3倍左右。
7.结合图3和4所示,图3是图2中上模的结构图,图4是图3中上模的左视图;在传统设计的电动汽车液冷式电机壳体挤压模中,上模210由于受到其下模220侧的模芯部位所遮挡,且上模210的厚度也较厚,导致两处模芯部位之间用于供应金属流量形成产品壁厚的分流孔和分流桥的加工难度大大增加,中心处的大模芯部位与其周边12个小模芯部位的内侧位置(即图4中双点划线的椭圆区域c),只能采用铜电极并借助电火花的方式来加工,不仅加工周期长,而且加工材料消耗大。
8.更为重要的是,由于采用这种放电方式的加工精度通常会较低,加工完成后各个
分流孔和分流桥的最终状态特别是一致性会相差较大,使得模具在挤压过程中,各个部位流速的不均匀性大大增加,挤压成型不够稳定,从而导致挤压出的产品质量低,尤其是圆形空腔的圆度以及壁厚的均匀度均难以达到合格产品的要求。
技术实现要素:9.为解决上述技术问题,本发明提供一种电动汽车液冷式电机壳体挤压模,可明显降低模具的加工难度,大大缩短模具的加工周期,显著减少加工耗材的消耗,且挤压成型更稳定,挤压出的产品质量更高。
10.本发明的技术方案如下:一种电动汽车液冷式电机壳体挤压模,包括用于挤压成型电动汽车液冷式电机壳体的上模和下模,电动汽车液冷式电机壳体中心沿其轴向设置有用于安装电动机定子和转子的圆形空腔,围绕该圆形空腔的电机壳体侧壁内部均布有多个用于以液冷方式冷却电机壳体的过水槽,过水槽沿电机壳体轴向延伸,且过水槽的横断面呈弧形长圆孔状;在上模远离下模的一侧设置有用于提前对金属流量进行预分配的配流板,配流板的端面上围绕其中心均布有多个扇形分流孔并形成内外两圈分流孔,内圈分流孔的数量小于外圈分流孔的数量,内外两圈分流孔的外侧壁均为喇叭口朝向上模倾斜的扇面,且外圈分流孔外侧壁的斜度大于内圈分流孔外侧壁的斜度;上模由上模本体和牙嵌型模芯组成,牙嵌型模芯位于上模本体朝向下模一侧的中心位置处,用于挤出成型电机壳体的圆形空腔,且牙嵌型模芯经旋转卡扣在上模本体上。
11.所述的电动汽车液冷式电机壳体挤压模,其中:所述上模本体朝下模方向的端面中心处沿轴向延伸有一圆柱部,圆柱部的侧壁上对称设置有至少两个齿状凸台,齿状凸台的顶面为直径da=2ra-(2~4)mm的圆柱状曲面,ra为上模内圈分流孔靠上模本体一侧内壁的半径,圆柱部的直径de=da-(30~40)mm;齿状凸台沿上模本体的轴向延伸,且齿状凸台的内端面与上模本体朝下模方向的大端面之间的开档h≥25mm,齿状凸台的外端面与圆柱部的外端面相齐平;所述牙嵌型模芯呈圆环状,牙嵌型模芯的中心孔内径与圆柱部外径相适配,中心孔的内壁上对称设置有至少两个适配卡入齿状凸台的齿槽;牙嵌型模芯朝下模方向的端面上设置有与中心孔同轴的台阶孔,台阶孔的侧壁与凹槽的顶面相齐平,且台阶孔的深度使得中心孔的厚度与开档h相适配;牙嵌型模芯远离下模一侧的端面上设置有延伸至其侧壁的倒角面。
12.所述的电动汽车液冷式电机壳体挤压模,其中:所述圆柱部的侧壁上对称设置有4个齿状凸台,中心孔的内壁上对称设置有4个适配卡入齿状凸台的齿槽;牙嵌型模芯嵌入上模本体时通过旋转45
°
后固定。
13.所述的电动汽车液冷式电机壳体挤压模,其中:所述倒角面为锥面,锥面与牙嵌型模芯远离下模一侧的端面之间的角度为30
°
。
14.所述的电动汽车液冷式电机壳体挤压模,其中:所述倒角面的小端设置有宽度为1.5~2mm且与牙嵌型模芯端面相平行的台阶面,台阶面的根部与凹槽的顶面相齐平,且台阶面与牙嵌型模芯远离下模一侧的端面之间为5mm。
15.所述的电动汽车液冷式电机壳体挤压模,其中:在距离所述倒角面大端5mm处的牙
嵌型模芯外侧壁上,一体设置有宽度为10mm高度2mm的环状凸台。
16.所述的电动汽车液冷式电机壳体挤压模,其中:所述电机壳体侧壁内部均布有12个过水槽,配流板端面上均布有4个内圈分流孔和6个外圈分流孔。
17.所述的电动汽车液冷式电机壳体挤压模,其中:所述外圈分流孔外侧壁的斜度为10
°
,内圈分流孔外侧壁的斜度为4
°
。
18.所述的电动汽车液冷式电机壳体挤压模,其中:所述上模本体上均布有12个上模内圈分流孔和12个上模外圈分流孔,配流板上的单个外圈分流孔与上模本体上的相邻两个上模外圈分流孔相对应;配流板上的单个内圈分流孔对应上模本体上的相邻三个上模内圈分流孔相对应。
19.所述的电动汽车液冷式电机壳体挤压模,其中:相邻两上模内圈分流孔之间的上模内圈分流桥的厚度为16mm,上模内圈分流桥的金属流入端与上模本体朝配流板方向的端面间隔50mm,且上模内圈分流桥的金属流入端为宽度6mm的平面,连接该平面的两侧面呈夹角40
°
的对称锥面;上模内圈分流桥的金属流出端与上模本体朝下模方向的大端面相齐平,且上模内圈分流桥的金属流出端为半径1mm的柱面,连接该柱面的两侧面呈夹角60
°
的对称锥面。
20.本发明所提供的一种电动汽车液冷式电机壳体挤压模,由于对上模中心处大模芯部位进行分割,采用牙嵌型结构的可拆卸连接方式,明显降低了上模的加工难度,大大缩短了模具的加工周期,并显著减少了加工耗材的消耗;再结合前置的配流板,金属的融合更加充分和均匀,使得挤压成型更稳定,挤压出的产品质量更高。
附图说明
21.在此描述的附图仅用于解释目的,而非意图以任何方式来限制本发明公开的范围;图中各部件的形状和比例尺寸等仅为示意性的,用于帮助对本发明的理解,并非是具体限定本发明各部件的形状和比例尺寸;本领域的技术人员在本发明的教导下,可以根据具体情况选择各种可能的形状和比例尺寸来实施本发明。
22.图1是现有技术中的典型液冷式电机壳体铝型材断面结构放大图;图2是现有技术中电动汽车液冷式电机壳体挤压模的整体结构图;图3是图2中上模的结构图;图4是图3中上模的左视图;图5是本发明电动汽车液冷式电机壳体挤压模实施例的整体结构图;图6是图5中的配流板结构图;图7是图6配流板的左视图;图8是图5中的上模本体(带k向局部)结构图;图9是图8上模本体(带b-b剖面)的左视图;图10是图5中的牙嵌型模芯结构图;图11是图10牙嵌型模芯的左视图;图12是本发明所用配流板的分流孔与上模分流孔在装配状态下的相互重合位置投影图(局部);图13是图5中的下模结构图;
图14是图13下模的左视图。
23.图中各标号汇总:电机壳体100、圆形空腔110、过水槽120、(现有技术中的)上模210、(现有技术中的)下模220、(本发明中的)上模310、上模本体311、圆柱部311a、齿状凸台311b、上模内圈分流孔311c、上模外圈分流孔311d、上模内圈分流桥311d、牙嵌型模芯312、中心孔312a、齿槽312b、台阶孔312c、倒角面312d、台阶面312e、环状凸台312f、(本发明中的)下模320、配流板330、内圈分流孔331、外圈分流孔332。
具体实施方式
24.以下将结合附图,对本发明的具体实施方式和实施例加以详细说明,所描述的具体实施例仅用以解释本发明,并非用于限定本发明的具体实施方式。
25.针对传统的电动汽车液冷式电机壳体挤压模加工难度大、精度低、成本高的缺陷,本发明首先将挤压模设计成三件结构,增加了一件配流板,其次将上模中心处的大模芯部位进行了分割,采用十字形或梅花状的牙嵌型结构,并采用可拆卸连接方式,分开独立加工后再组装成完整的上模。
26.结合图5所示,图5是本发明电动汽车液冷式电机壳体挤压模实施例的整体结构图,本发明电动汽车液冷式电机壳体挤压模包括上模310和下模320,用于挤压成型图1中的电动汽车液冷式电机壳体100;图1中的电动汽车液冷式电机壳体100中心沿其轴向设置有圆形空腔110,用于安装电动机定子和转子,围绕该圆形空腔110的电机壳体侧壁内部均布有多个过液槽120,用于以液冷方式冷却电机壳体100,过液槽120沿电机壳体100轴向延伸,且过液槽120的横断面呈弧形长圆孔状。
27.本发明电动汽车液冷式电机壳体挤压模的改进点在于,一方面,在图5上模310远离下模320的一侧增加有一配流板330,可以提前对金属流量进行预分配,使得金属的流量供应分配更加合理和均匀;另一方面,上模310由上模本体311和牙嵌型模芯312组成,牙嵌型模芯312位于上模本体311朝向下模320一侧的中心位置处,用于挤出成型图1电机壳体100的圆形空腔110,而牙嵌型模芯312需经旋转才能卡扣在上模本体311之上。
28.结合图6和图7所示,图6是图5中的配流板结构图,图7是图6配流板的左视图,在配流板330的端面上围绕其中心均布有多个扇形分流孔并形成内外两圈分流孔(331和332),内圈分流孔331的数量小于外圈分流孔332的数量,内外两圈分流孔(331和332)的外侧壁均为喇叭口朝向图5上模310倾斜的扇面(即变量孔),且外圈分流孔332外侧壁的斜度大于内圈分流孔331外侧壁的斜度。
29.变量孔形式的内外两圈分流孔(331和332),从金属进入的截面到金属流出的截面逐渐增大,可以减缓金属的流量速度,降低挤压力,有利于减轻模具的承压力,进一步提高模具的强度;且外侧压力的降低速度要比内侧压力的降低速度稍大,也是基于模具内侧的金属成型难度更大,因为内侧是大模芯部位与其周边12个小模芯部位之间所形成的间隙,产品成型阻力大,相对而言稍大的压力对金属进入更有利。
30.具体的,对于挤压成型图1中侧壁内部均布有12个过液槽120的液冷式电机壳体100来说,可在图7中的配流板330端面上均布4个内圈分流孔331和6个外圈分流孔332;同时,所有外圈分流孔332外侧壁的斜度为10
°
,所有内圈分流孔331外侧壁的斜度为4
°
。
31.结合图8和图9所示,图8是图5中的上模本体(带k向局部)结构图,图9是图8上模本
体(带b-b剖面)的左视图,上模310经过分割处理后,所有得分流孔和分流桥都呈现出裸露得状态,仅采用车削的方式即可完成对上模310机加工,避免了需采用电火花的加工方式,由此大大降低了上模310的加工难度,并可大幅提高上模310的制造精度。
32.具体的,上模本体311朝下模320方向的端面中心处沿轴向延伸有一圆柱部311a,在该圆柱部311a的侧壁上对称设置有2、3、4、5、6、7或8个齿状凸台311b,齿状凸台311b的顶面为圆柱状曲面,该圆柱状曲面的直径da=2ra-(2~4)mm,ra为上模内圈分流孔311c靠上模本体311一侧内壁的半径,圆柱部311a的直径de=da-(30~40)mm;齿状凸台311b沿上模本体311的轴向延伸,且齿状凸台311b的内端面与上模本体311朝下模320方向的大端面之间的开档h≥25mm,齿状凸台311b的外端面与圆柱部311a的外端面相齐平。
33.具体的,结合图10和图11所示,图10是图5中的牙嵌型模芯结构图,图11是图10牙嵌型模芯的左视图,牙嵌型模芯312呈圆环状,牙嵌型模芯312的中心孔312a内径与图8圆柱部311a外径相适配,中心孔312a的内壁上对称设置有2、3、4、5、6、7或8个适配卡入图8齿状凸台311b的齿槽312b;牙嵌型模芯312朝下模320方向的端面上设置有与中心孔312a同轴的台阶孔312c,台阶孔312c的侧壁与凹槽312b的顶面相齐平,且台阶孔312c的深度使得中心孔312a的厚度与开档h相适配;以及,在牙嵌型模芯312远离下模320一侧的端面上还设置有延伸至其侧壁的倒角面312d,用于支撑牙嵌型模芯312,这可提高牙嵌型模芯312的强度。
34.优选地,图8圆柱部311a的侧壁上对称设置有4个齿状凸台311b,图11中心孔312a的内壁上对称设置有4个适配卡入齿状凸台311b的齿槽312b;牙嵌型模芯312嵌入上模本体311时通过旋转45
°
后固定,此时齿状凸台311b与齿槽312b处于相互错位的状态。
35.优选地,倒角面312d为锥面,锥面与牙嵌型模芯312远离下模320一侧的端面之间的角度为30
°
。
36.进一步地,倒角面312d的小端设置有宽度为1.5~2mm且与牙嵌型模芯312端面相平行的台阶面312e,台阶面312e的根部与凹槽312b的顶面相齐平(即df=da+(3~4)mm),且台阶面312e与牙嵌型模芯312远离下模320一侧的端面之间为5mm,用于吊挂和固定牙嵌型模芯312,防止在挤压时牙嵌型模芯312发生变形和变位。
37.进一步地,在距离倒角面312d大端5mm处的牙嵌型模芯312外侧壁上,一体设置有宽度为10mm高度2mm的环状凸台312f,用于增大牙嵌型模芯312的受剪切面积,从而提高牙嵌型模芯312的强度。
38.结合图7、9和12所示,图12是本发明所用配流板的分流孔与上模分流孔在装配状态下的相互重合位置投影图(局部),对于挤压成型图1中侧壁内部均布有12个过水槽120的液冷式电机壳体100来说,可在图9中的上模本体311上均布12个上模内圈分流孔和12个上模外圈分流孔;装配之后,图7配流板330上的单个外圈分流孔332对应图9上模本体311上的相邻两个上模外圈分流孔311d;图7配流板330上的单个内圈分流孔331对应图9上模本体311上的相邻三个上模内圈分流孔311c。
39.此外,为了能够进一步减小产品内侧较大的成型阻力并使金属融合更加充分和均匀,除了配流板330的内外两圈分流孔(331和332)采用变量孔形式外,还可以对位于上模本体311内侧的分流桥的位置和形状进行改进,具体的,如图9中的b-b剖面图所示,b-b剖面图为上模内圈分流桥311d沿金属流动方向的厚度切面图,相邻两上模内圈分流孔311c之间的上模内圈分流桥311d的厚度为16mm,上模内圈分流桥311d的金属流入端与上模本体311朝
配流板330方向的端面间隔50mm,且上模内圈分流桥311d的金属流入端为宽度6mm的平面,连接该平面的两侧面呈夹角40
°
的对称锥面;上模内圈分流桥311d的金属流出端与上模本体311朝下模320方向的大端面相齐平,且上模内圈分流桥311d的金属流出端为半径1mm的柱面,连接该柱面的两侧面呈夹角60
°
的对称锥面。
40.当配流板330内圈分流孔331中的金属进入上模本体311时,金属从12个均等的内圈分流孔331先进入50mm深的上模本体311融合腔中进行均匀融合,再经上模内圈分流桥311d均衡流入12个均等的上模内圈分流孔311c,最后注入下模320的焊合室中,由此使得金属更加充分融合均匀,并达到金属供应均匀和各个部位流速均衡的目的。
41.结合图13和图14所示,图13是图5中的下模结构图,图14是图13下模的左视图;由于本发明的配流板330和上模310均对金属的流动进行了合理、均匀的分配,所以也避免了下模320主体工作带须取级差的传统设计,而只需考虑图1均布于电机壳体100外壁上的开口螺孔部位的成型难易程度,但该开口螺孔部位的壁厚较薄,成型也较难,故在设计时,只需将该开口螺孔部位的工作带取3mm,并与主体部位7mm长的工作带进行直线过渡即可满足成型要求,从而简化了下模320的工作带设计难度。
42.本说明书中未作详细描述的内容均属于本领域普通技术人员公知的现有技术。
43.应当理解的是,以上所述仅为本发明的较佳实施例而已,并不足以限制本发明的技术方案,对本领域普通技术人员来说,在本发明的精神和原则之内,可以根据上述说明加以增减、替换、变换或改进,而所有这些增减、替换、变换或改进后的技术方案,都应属于本发明所附权利要求的保护范围。