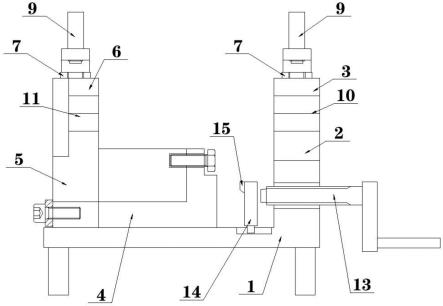
1.本实用新型涉及机械装配技术领域,具体为一种前叉模具工装。
背景技术:2.整体焊接式前叉的上连扳、下连、枢轴、叉腿和叉腿上螺母相互之间的平行度、垂直度和对称度的保证是前叉组装过程中的工艺难点,常规的整体焊台上一起总焊上述各件后焊接应力大,焊后应力释放引起较大的变形,焊后校正工作量大校正力巨大,容易导致零件表面受损,为了改善工艺,一些产线专门设计针对主叉头部的预焊夹具,对焊接应力大、位置度要求高的叉头进行预先焊接,但是现有的预焊时使用的工装在实际使用过程中却存在一些问题,就比如现有的预焊时使用的工装往往是通过将前叉的各个部件通过v型定位押金在工装上,但是v型定位在夹持时存在高度方向误差大且与零件为线接触,导致在使用较大夹紧力时容易挤伤工件的缺点,同时现有的预焊时使用的工装通过拆卸式螺栓固定夹具的方式不仅工作效率低下,而且在螺孔内部很容易堆积杂物导致螺孔堵塞无法安装。
技术实现要素:3.本实用新型的目的在于提供一种前叉模具工装,以解决上述背景技术中提出的定位高度方向误差大、容易挤伤模块和夹持较慢的问题。
4.为实现上述目的,本实用新型提供如下技术方案:一种前叉模具工装,包括枕块、托块、活块、定位块和架设块,所述枕块的一侧上端通过螺栓安装有托块,且托块的上端放置有活块,所述枕块的一侧上表面固定设置有定位块,且定位块的外表面卡合连接有架设块,且架设块与定位块之间通过螺栓固定,所述架设块的上表面放置有卡块,所述活块和卡块的两侧侧表面均固定安装有2个压块,所述托块和架设块的侧表面均安装有转动的回转块,所述回转块的外表面被摇杆所贯穿,所述活块的下表面和托块的上表面均开设有定位槽,所述卡块的下表面和架设块的上表面均开设有中心槽,所述托块的侧表面开设有通槽,且通槽的内部安装有顶杆,所述枕块的上表面连接有滑动的滑板,所述滑板朝向架设块的上端一侧表面固定有顶块。
5.优选的,所述摇杆的一端位于同侧的2个压块之间,且摇杆的一端与2个压块的上表面相贴合。
6.采用上述技术方案,使得摇杆可以通过与压块的卡合和与压块上表面的贴合对活块和卡块进行定位和压紧。
7.优选的,所述摇杆与回转块为螺纹连接,且摇杆的上端为外表面光滑的圆柱形设计。
8.采用上述技术方案,使得摇杆可以通过与回转块的螺纹连接相对压块滑动,同时摇杆通过光滑表面的一端与2个压块卡合定位。
9.优选的,所述定位槽和中心槽均为半圆形设计,且定位槽和中心槽的内侧表面均开设有内凹的槽。
10.采用上述技术方案,使得两个半圆的定位槽和中心槽均能通过相互贴合的方式形成完成的夹持槽,进而对工件进行夹持,而定位槽和中心槽内侧表面开设的内凹槽可以对工件的尖锐部分进行让位防止工件被压伤。
11.优选的,所述顶杆和滑板均设置有3个,且3个滑板分别位于3个定位槽的正下方。
12.采用上述技术方案,使得顶杆可以通过滑板对工件进行稳定的夹持。
13.优选的,所述顶杆与通槽为螺纹连接,且顶杆的一端与滑板的侧表面相贴合。
14.采用上述技术方案,使得顶杆转动时可以相对通槽转动并滑动达到推动滑板移动的目的。
15.与现有技术相比,本实用新型的有益效果是:该前叉模具工装:
16.1.通过托块和活块外表面开设的定位槽与架设块和卡块外表面的中心槽对前叉组件中的主叉上螺母和枢轴进行固定,以保证主叉上螺母和枢轴的高度方向能够保持一致,减少焊接应力的产生,同时通过定位槽和中心槽通过弧形部分与工件接触的方式减少工件被压伤的情况发生;
17.2.通过活块和卡块与托块和架设块之间的拼接结构实现对工装的快速拆卸安装,进而提升工件夹持的速度和简易程度,省去了繁琐的安装定位销等过程;
18.3.通过摇杆与回转块的螺纹连接和回转块与托块和架设块的转动连接,使得摇杆可以通过围绕回转块翻转与2个压块卡合,并通过摇杆相对回转块转动实现对压块的挤压,使得活块和卡块能够被压紧在托块和架设块的上表面,不仅省去了螺栓的安装过程,且由于摇杆始终保持与回转块的连接而使得回转块的螺孔中不会进入杂物导致无法安装。
附图说明
19.图1为本实用新型整体正剖视结构示意图;
20.图2为本实用新型压块与回转块连接正剖视结构示意图;
21.图3为本实用新型架设块与卡块连接侧剖视结构示意图;
22.图4为本实用新型整体安装结构示意图;
23.图5为本实用新型整体工作状态结构示意图。
24.图中:1、枕块;2、托块;3、活块;4、定位块;5、架设块;6、卡块;7、压块;8、回转块;9、摇杆;10、定位槽;11、中心槽;12、通槽;13、顶杆;14、滑板;15、顶块。
具体实施方式
25.下面将结合本实用新型实施例中的附图,对本实用新型实施例中的技术方案进行清楚、完整地描述,显然,所描述的实施例仅仅是本实用新型一部分实施例,而不是全部的实施例。基于本实用新型中的实施例,本领域普通技术人员在没有做出创造性劳动前提下所获得的所有其他实施例,都属于本实用新型保护的范围。
26.请参阅图1-5,本实用新型提供一种技术方案:一种前叉模具工装,包括枕块1、托块2、活块3、定位块4、架设块5、卡块6、压块7、回转块8、摇杆9、定位槽10、中心槽11、通槽12、顶杆13、滑板14和顶块15,枕块1的一侧上端通过螺栓安装有托块2,且托块2的上端放置有活块3,枕块1的一侧上表面固定设置有定位块4,且定位块4的外表面卡合连接有架设块5,且架设块5与定位块4之间通过螺栓固定,架设块5的上表面放置有卡块6,活块3和卡块6的
两侧侧表面均固定安装有2个压块7,托块2和架设块5的侧表面均安装有转动的回转块8,回转块8的外表面被摇杆9所贯穿,摇杆9的一端位于同侧的2个压块7之间,且摇杆9的一端与2个压块7的上表面相贴合,摇杆9与回转块8为螺纹连接,且摇杆9的上端为外表面光滑的圆柱形设计,通过回转块8使得摇杆9可以相对压块7翻转,使得摇杆9可以通过与压块7的位移实现对活块3和卡块6的固定和松夹,省去了频繁安装螺栓的过程,并且通过摇杆9与压块7卡合的方式实现了对活块3和卡块6相对托块2和架设块5的精准定位,使得活块3和卡块6不会错位安装导致工件定位不准的情况发生。
27.如图1-5所示,活块3的下表面和托块2的上表面均开设有定位槽10,卡块6的下表面和架设块5的上表面均开设有中心槽11,定位槽10和中心槽11均为半圆形设计,且定位槽10和中心槽11的内侧表面均开设有内凹的槽,通过定位槽10和中心槽11分别对主叉上螺母和枢轴进行固定,使得前叉的主体先对位置固定,从而使得在后续上、下连板和叉腿管安装时不会造成工件之间相对位置的偏差。
28.如图1、图2、图4和图5所示,托块2的侧表面开设有通槽12,且通槽12的内部安装有顶杆13,枕块1的上表面连接有滑动的滑板14,滑板14朝向架设块5的上端一侧表面固定有顶块15,顶杆13和滑板14均设置有3个,且3个滑板14分别位于3个定位槽10的正下方,顶杆13与通槽12为螺纹连接,且顶杆13的一端与滑板14的侧表面相贴合,利用顶杆13转动相对托块2滑动的方式,使得顶杆13可以挤压滑板14,滑板14在滑动过程中对工件进行限位使得工件能够更加稳定,不会在焊接过程中发生松动。
29.工作原理:在使用该前叉模具工装时,首先将主叉上螺母放置在托块2上表面的定位槽10中,然后将活块3下表面的定位槽10对准主叉上螺母放在主叉上螺母的上表面,然后转动摇杆9使得摇杆9通过回转块8向活块3侧表面的2个压块7之间移动,直至摇杆9与活块3侧表面的2个压块7卡合,使得活块3和托块2的横向相对位置固定,此时相对回转块8转动摇杆9,摇杆9通过与回转块8的螺纹连接滑动,直至摇杆9通过与压块7的接触将活块3和主叉上螺母压紧在托块2的上表面;
30.然后将枢轴的一端放置在架设块5上面的中心槽11中,然后推动枢轴使其一端与主叉上螺母一端贴合,此时将卡块6通过中心槽11与枢轴卡合放置在架设块5上表面,然后通过回转块8翻转摇杆9并在摇杆9与压块7卡合后转动摇杆9,进而达到对卡块6和枢轴固定的目的,然后将上连板放置在滑板14与定位块4之间,然后转动顶杆13,利用顶杆13与通槽12的螺纹连接使得顶杆13顶动滑板14在枕块1上表面滑动,直至滑板14通过顶块15将上连板顶紧在定位块4的侧表面,此时通过对剩余部件的焊接完成对前叉的预焊接,增加了整体的实用性。
31.尽管已经示出和描述了本实用新型的实施例,对于本领域的普通技术人员而言,可以理解在不脱离本实用新型的原理和精神的情况下可以对这些实施例进行多种变化、修改、替换和变型,本实用新型的范围由所附权利要求及其等同物限定。