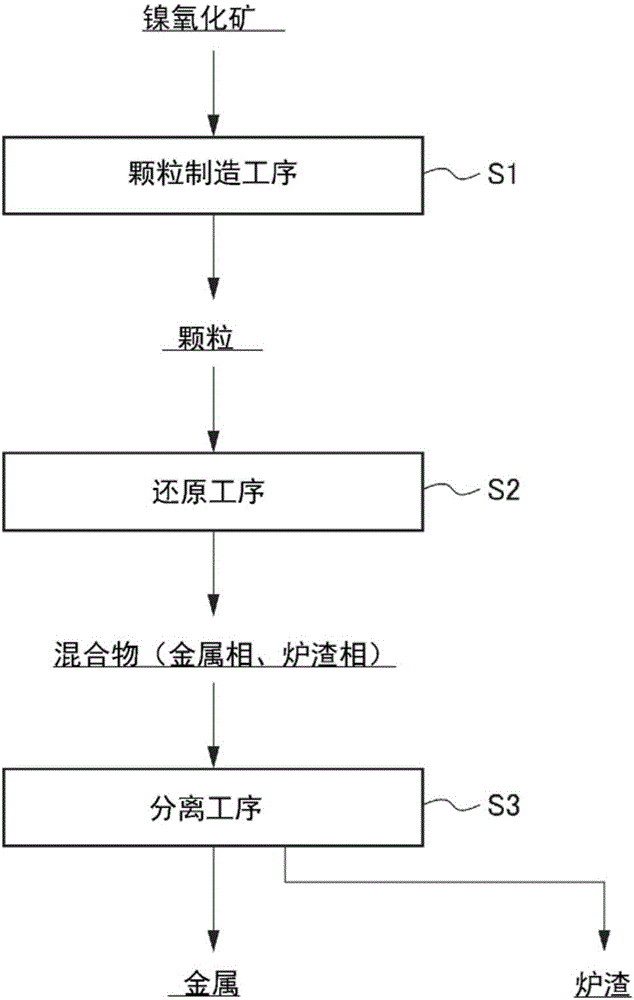
本发明涉及镍氧化矿的冶炼方法、颗粒的装入方法,更详细地,涉及由作为原料矿石的镍氧化矿形成颗粒,在冶炼炉中将所述颗粒还原加热,从而进行冶炼的镍氧化矿的冶炼方法以及将颗粒装入所述冶炼炉的方法。
背景技术:
:作为被称为褐铁矿或腐泥土的镍氧化矿的冶炼方法,已知使用熔炼炉制造镍锍的干式冶炼方法、使用回转窑或移动炉床炉制造镍铁的干式冶炼方法、使用高压釜制造混合硫化物的湿式冶炼方法等。将镍氧化矿装入冶炼工序时,进行用于将上述原料矿石颗粒化、浆料化等的前处理。具体而言,将镍氧化矿颗粒化,即,制造颗粒时,与除上述镍氧化矿以外的成分例如粘合剂、还原剂混合,进一步进行水分调节等后,装入块状物制造机,例如,通常制成10~30mm左右的块状物(指颗粒、团块等。以下,仅称为“颗粒”)。例如,为了实现保持通气性、防止原料成分的不均匀等作用,即使将上述颗粒装入冶炼炉,开始还原加热等冶炼操作,维持其形状也是重要的。例如,在专利文献1中,公开了一种作为利用移动炉床炉制造镍铁时的前处理方法的技术,所述技术在将含有氧化镍和氧化铁的原料与碳质还原剂混合形成混合物的混合工序中调节混合物中的剩余碳含量,制造颗粒,将所述颗粒装入炉内进行还原工序。然而,碳质还原剂与其他原料的“融合性”差,与不加碳质还原剂的情况相比,制造的颗粒强度弱。将颗粒装入冶炼炉时,在颗粒强度不足以至于由装入时承受的力导致崩解的情况下,如上述专利文献1(例如,参照段落[0061])所记载,存在必须采取添加粘合剂等用于得到所需强度的某些手段的问题。现有技术文献专利文献专利文献1:日本特开2004-156140号公报。技术实现要素:发明所要解决的问题本发明是基于上述实际情况而提出的,其目的在于,在通过由镍氧化矿形成颗粒,在冶炼炉中将所述颗粒还原加热,从而进行冶炼的方法中,提供能够在维持颗粒强度的同时使冶炼工序(还原工序)中的冶炼反应有效地进行的镍氧化矿的冶炼方法、将颗粒装入所述冶炼炉的方法。解决问题的技术方案本发明人为了解决上述问题而进行了悉心研究。其结果是,发现了通过制造不含有碳质还原剂的颗粒,将所述颗粒装入冶炼炉,从而成为被碳质还原剂覆盖的状态,实施还原加热处理,从而能够在维持颗粒强度的同时使冶炼反应有效地进行,完成了本发明。即,本发明提供以下内容。(1)本发明的第一发明是一种镍氧化矿的冶炼方法,通过由镍氧化矿形成颗粒,将所述颗粒还原加热,从而进行冶炼,所述镍氧化矿的冶炼方法的特征在于,具有:由所述镍氧化矿制造颗粒的颗粒制造工序,以及,在冶炼炉中以规定的还原温度将得到的颗粒还原加热的还原工序;在所述颗粒制造工序中,不混合碳质还原剂,而将含有所述镍氧化矿的原料混合作为混合物,将该混合物块状化,形成颗粒,在所述还原工序中,将得到的颗粒装入所述冶炼炉时,预先在该冶炼炉的炉床上铺满碳质还原剂,将所述颗粒载置在该碳质还原剂上,进一步在所述颗粒被碳质还原剂覆盖的状态下对所述颗粒进行还原加热。(2)另外,本发明的第二发明是如上述第一发明所述的镍氧化矿的冶炼方法,其特征在于,在所述还原工序中,用碳质还原剂进一步覆盖载置在所述碳质还原剂上的颗粒时,使从被覆盖的颗粒的上端至所述碳质还原剂层的表面为止的厚度为所述颗粒的高度方向大小的至少5%以上。(3)另外,本发明的第三发明是如上述第一或第二发明所述的镍氧化矿的冶炼方法,其特征在于,将所述颗粒装入所述冶炼炉时的温度设定为600℃以下。(4)本发明的第四发明是一种颗粒的装入方法,其是用于通过由镍氧化矿形成颗粒,在冶炼炉中将该颗粒还原加热,从而进行冶炼的颗粒的装入方法,所述颗粒的装入方法的特征在于,具有:由所述镍氧化矿制造颗粒的颗粒制造工序,以及,将得到的颗粒装入用于还原加热的冶炼炉的颗粒装入工序;在所述颗粒制造工序中,不混合碳质还原剂,而将含有所述镍氧化矿的原料混合作为混合物,将该混合物块状化,形成颗粒,在所述颗粒装入工序中,预先在所述冶炼炉的炉床上铺满碳质还原剂,将该颗粒载置在该碳质还原剂上,用碳质还原剂进一步覆盖该颗粒使其处于被覆盖的状态。发明效果根据本发明,能够在维持颗粒强度的同时使将颗粒还原加热的还原工序中的冶炼反应有效地进行。附图说明图1是表示镍氧化矿的冶炼方法的流程的工序图。图2是表示在镍氧化矿的冶炼方法中的颗粒制造工序中的处理的流程的处理流程图。图3是示意性地表示将颗粒装入冶炼炉内的状态的图。具体实施方式下面,参照附图详细地说明本发明的具体实施方式(以下,称为“本实施方式”)。需要说明的是,本发明并不限定于以下实施方式,在不改变本发明要旨的范围内可进行各种改变。《1.镍氧化矿的冶炼方法》首先,对作为原料矿石的镍氧化矿的冶炼方法进行说明。下面,举例说明冶炼方法,所述冶炼方法通过将作为原料矿石的镍氧化矿颗粒化,对该颗粒进行还原处理,从而生成金属(铁-镍合金(以下,也将铁-镍合金称为“镍铁”))和炉渣,分离该金属和炉渣,从而制造镍铁。本实施方式的镍氧化矿的冶炼方法是通过使用镍氧化矿颗粒,将所述颗粒装入冶炼炉(还原炉)中,进行还原加热,从而进行冶炼的方法。具体而言,如图1的工序图所示,上述镍氧化矿的冶炼方法具备:由镍氧化矿制造颗粒的颗粒制造工序S1;在还原炉中以规定的还原温度将得到的颗粒还原加热的还原工序S2;以及,分离在还原工序S2中生成的金属和炉渣,回收金属的分离工序S3。<1-1.颗粒制造工序>在颗粒制造工序S1中,由作为原料矿石的镍氧化矿制造颗粒。图2是表示在颗粒制造工序S1中的处理的流程的处理流程图。如图2所示,颗粒制造工序S1具备:混合含有镍氧化矿的原料的混合处理工序S11;将得到的混合物形成为块状物(造粒)的块状化处理工序S12;以及,干燥得到的块状物的干燥处理工序S13。(1)混合处理工序混合处理工序S11是混合含有镍氧化矿的原料粉末,得到混合物的工序。具体而言,在所述混合处理工序S11中,混合作为原料矿石的镍氧化矿以及铁矿石、助熔剂成分、粘合剂等粒径为例如0.2mm~0.8mm左右的原料粉末,得到混合物。在此,在本实施方式中,制造颗粒时,不混合碳质还原剂而得到混合物,由不包含上述碳质还原剂的混合物形成颗粒。如此地,作为原料粉末,不混合碳质还原剂而制造颗粒,从而能够抑制得到的颗粒的强度的降低。作为镍氧化矿,无特别限定,可以使用褐铁矿、腐泥土矿等。作为铁矿石,无特别限定,例如,可以使用铁品位为50%左右以上的铁矿石、通过镍氧化矿的湿式冶炼得到的赤铁矿等。另外,作为粘合剂,例如,可举例膨润土、多糖类、树脂、水玻璃、脱水泥饼等。另外,作为助熔剂成分,例如,可举例氧化钙、氢氧化钙、碳酸钙、二氧化硅等。在下述表1中示出原料粉末的部分组成(重量%)的一个实例。需要说明的是,作为原料粉末的组成,并不限定于此。[表1]原料粉末[重量%]NiFe2O3C镍氧化矿1~250~60-铁矿石-80~95-(2)块状化处理工序块状化处理工序S12是将混合处理工序S11中得到的原料粉末混合物形成为块状物(造粒)的工序。具体而言,在混合处理工序S11中得到的混合物中添加块状化所需的水分,例如,使用块状物制造装置(滚动造粒机、压缩成型机、挤出成型机等)等或通过人手形成颗粒状的块。作为颗粒的形状,无特别限定,例如,可以为球状。另外,作为形成颗粒状的块状物的大小,无特别限定,例如,通过后述的干燥处理、预热处理,使被装入还原工序中的冶炼炉等的颗粒的大小(在球状颗粒的情况下为直径)为10mm~30mm左右。(3)干燥处理工序干燥处理工序S13是对在块状化处理工序S12中得到的块状物进行干燥处理的工序。通过块状化处理成为颗粒状的块的块状物含有过量例如50重量%左右的水分,成为发粘的状态。为了使上述颗粒状的块状物的处理变得容易,在干燥处理工序S13中,实施干燥处理,例如使块状物的固体成分为70质量%左右,水分为30质量%左右。更具体地,作为干燥处理工序S13中对块状物的干燥处理,无特别限定,例如,对块状物吹300℃~400℃的热风,进行干燥。需要说明的是,该干燥处理时的块状物的温度小于100℃。在下述表2中示出干燥处理后的颗粒状的块状物中的固体成分组成(重量份)的一个实例。需要说明的是,作为干燥处理后块状物的组成,并不限定于此。表2在颗粒制造工序S1中,如上所述地混合含有作为原料矿石的镍氧化矿的原料粉末,将得到的混合物造粒(块状化)成颗粒状,使其干燥,从而制造颗粒。此时,在混合原料粉末时不混合碳质还原剂,制造不包含碳质还原剂的颗粒。得到的颗粒的大小为10mm~30mm左右,制造具有可维持形状的强度的颗粒,例如,所述强度是,即使在从高度1m下落的情况下,崩解的颗粒的比例也为1%以下左右的强度。这种颗粒能够承受装入下一步的还原工序S2时的下落等冲击,能够维持该颗粒的形状,而且,由于颗粒与颗粒之间形成适当的空隙,所以使冶炼工序中的冶炼反应适当地进行。另外,在该颗粒制造工序S1中,也可以设置预热处理工序,所述预热处理工序是在规定温度下对上述在干燥处理工序S13中实施干燥处理的块状物的颗粒进行预热处理的工序。如此地,对干燥处理后的块状物实施预热处理,制造颗粒,即使在将还原工序S2中的颗粒在例如1400℃左右的高温下还原加热时,也能够更有效地抑制由热冲击导致的颗粒破碎(破坏、崩解)。例如,能够使装入冶炼炉的全部颗粒中崩解的颗粒的比例为很小的比例,能够更有效地维持颗粒的形状。具体而言,在预热处理中,在350℃~600℃的温度下对干燥处理后的颗粒进行预热处理。另外,优选在400℃~550℃的温度下进行预热处理。如此地,通过在350℃~600℃、优选400℃~550℃的温度下预热处理,能够减少构成颗粒的镍氧化矿中含有的结晶水,即使在装入约1400℃的冶炼炉,温度急剧升高的情况下,也能够抑制由该结晶水脱离导致的颗粒的崩解。另外,通过实施这种预热处理,使构成颗粒的镍氧化矿、氧化铁、粘合剂和助熔剂成分等粒子的热膨胀分两个阶段缓慢地进行,由此,能够抑制由粒子的膨胀差导致的颗粒的崩解。另外,作为预热处理的处理时间,无特定限定,根据含有镍氧化矿的块状物的大小适当地调整即可,如果得到的颗粒是大小为10mm~30mm的通常大小的块状物,则能够将处理时间设为10分钟~60分钟左右。<1-2.还原工序>在还原工序S2中,将颗粒制造工序S1中得到的颗粒在指定的还原温度下还原加热。通过在该还原工序S2中对颗粒进行还原加热处理,从而进行冶炼反应,生成金属和炉渣。具体而言,还原工序S2中的还原加热处理是使用冶炼炉(还原炉)等进行的,通过将含有镍氧化矿的颗粒装入加热至例如1400℃左右的温度的冶炼炉中进行还原加热。在本实施方式中,将上述得到的颗粒装入冶炼炉时,预先在上述冶炼炉的炉床上铺满碳质还原剂,将颗粒载置在上述铺盖的碳质还原剂上。接着,用碳质还原剂进一步覆盖载置在碳质还原剂上的颗粒使其处于被覆盖的状态。即,本实施方式的特征在于,将含有镍氧化矿的颗粒还原加热时,使颗粒处于被碳质还原剂覆盖的状态。在下文进行更详细地说明。在该还原工序S2的还原加热处理中,首先,仅用例如一分钟左右的时间在容易进行还原反应的颗粒表面附近将颗粒中的镍氧化物和铁氧化物还原,金属化,成为铁-镍合金(镍铁),形成壳(shell)。另一方面,在壳中,随着上述壳的形成,颗粒中的炉渣成分逐渐熔融,生成液相炉渣。由此,在一个颗粒中,分别生成镍铁金属(以下,仅称为“金属”)和镍铁炉渣(以下,仅称为“炉渣”)。然后,通过将还原工序S2中的还原加热处理的处理时间进一步延长至10分钟左右,从而使铺盖于冶炼炉的炉床的、为了进一步覆盖颗粒而包围的碳质还原剂中不参与还原反应的剩余碳质还原剂的碳成分进入铁-镍合金中,使熔点降低。其结果是,铁-镍合金溶解成为液相。如上所述,虽然颗粒中的炉渣熔融成为液相,但是,已经分离生成的金属和炉渣不会混杂在一起,通过随后的冷却,成为金属固相与炉渣固作为单独的相混合的混合物。与装入的颗粒相比,所述混合物的体积收缩为50%~60%左右的体积。在上述冶炼反应最理想地进行的情况下,对于装入的一个颗粒而言,得到一个金属固相与一个炉渣固相混合的一个混合物,成为“不倒翁状”形状的固体。在此,“不倒翁状”是指金属固相与炉渣固相接合的形状。混合物具有这种“不倒翁状”的形状时,由于上述混合物粒子的尺寸达到最大,因此,从冶炼炉回收时,回收的劳力和时间少,能够抑制金属回收率的降低。在本实施方式的镍氧化矿的冶炼方法中,如上所述,在颗粒制造工序S1中,为了制造不包含碳质还原剂的颗粒,将上述颗粒装入在炉床上铺满碳质还原剂的冶炼炉,用碳质还原剂进一步包围颗粒以进行覆盖,在这种状态下实施还原加热处理。如此地,通过实施还原加热处理,在维持颗粒强度,抑制还原加热处理中的崩解的同时,能够使冶炼反应有效地进行。<1-3.分离工序>在分离工序S3中,分离在还原工序S2中生成的金属和炉渣,回收金属。具体而言,从通过对颗粒进行还原加热处理而得到的、包含金属相(金属固相)和炉渣相(包含碳质还原剂的炉渣固相)的混合物中分离回收金属相。作为从得到的金属相和炉渣相的固体混合物中分离金属相和炉渣相的方法,例如,不仅可以通过筛分除去不需要的物质,还可以利用比重分离、磁力分离等方法。另外,由于得到的金属相和炉渣相润湿性差,因此,能够容易地分离,对于上述“不倒翁状”的混合物而言,例如,通过实施设置规定的落差使所述混合物下落、或者通过在筛分时给予规定的振动等冲击,能够容易地从上述“不倒翁状”的混合物中分离金属相和炉渣相。如此地,通过分离金属相和炉渣相,从而回收金属相。《2.颗粒的装入方法》然后,在上述镍氧化矿的冶炼方法中,对用于由原料矿石的镍氧化矿形成颗粒,在冶炼炉中将所述颗粒还原加热,从而进行冶炼的将颗粒装入冶炼炉的方法,进行更详细的说明。本实施方式的特征在于,在上述颗粒制造工序S1中的混合处理工序S11中,不混合碳质还原剂,例如,将作为原料矿石的镍氧化矿与铁矿石(氧化铁)混合,成为混合物。接着,通过将得到的混合物块状化,制造不包含碳质还原剂的颗粒。如此地,由于得到的颗粒的强度高于混合了碳质还原剂的颗粒,因此,即使在下一步的还原工序S2中装入冶炼炉时承受冲击等的情况下,也能够抑制上述颗粒的崩解。本实施方式的特征在于,如此地,制造不包含碳质还原剂的颗粒后,将上述颗粒装入用于还原加热的冶炼炉时,如图3(A)的示意图所示,预先在冶炼炉1的炉床1a上铺满碳质还原剂10,将制造的颗粒20载置在上述铺盖的碳质还原剂10上。接着,如图3(B)所示,对载置的颗粒20,进一步添加碳质还原剂10,从而覆盖包围颗粒20,即,成为由碳质还原剂20完全覆盖颗粒20的状态。在本实施方式中,在如此地成为由碳质还原剂覆盖围绕颗粒周围的状态的基础上,实施还原加热处理。由此,在还原加热时,由于围绕颗粒周围的碳质还原剂不破坏颗粒的形状,因此,上述碳质还原剂发挥所谓壳的作用,使冶炼反应适当地进行,有效地形成金属与炉渣接合的“不倒翁状”的块状物(包含金属相和炉渣相的混合物)。通过冶炼反应得到的块状物是在由碳质还原剂覆盖的状态下而得到的,上述块状物的尺寸为约6mm~18mm左右的大小,另一方面,例如,对于碳质还原剂而言,例如,仅是次微米(Sub-Micron)粒子进行了微弱烧结。因此,将得到的块状物从冶炼炉中排出时,碳质还原剂被粉碎,通过筛分等手段能够容易地与块状物分离。另外,根据需要,通过使用振动筛等或利用比重差分级,能够更有效地分离。在本实施方式中,在进行还原加热处理的还原工序S2中,重要的是,围绕装入冶炼炉的颗粒周围的碳质还原剂不破坏颗粒的形状。在还原工序中的冶炼反应中,在上述还原加热初期形成的壳在确保还原环境中发挥了重要的作用,如上所述,在本实施方式中,覆盖颗粒的碳质还原剂所形成的空间(以下,仅称为“空间”)发挥了上述壳的作用,维持了还原环境。由此,不需要像现有技术那样使颗粒中含有碳质还原剂,基于所含有的碳质还原剂而形成壳,可以抑制颗粒强度的降低。另外,包围颗粒的碳质还原剂发挥了壳的作用,使冶炼反应有效地进行,因此,适当地形成“不倒翁状”的块状物。在此,作为碳质还原剂,无特别限定,例如,可举例煤粉、焦粉等。另外,作为碳质还原剂的粒度,无特别限定,优选能够有效地覆盖颗粒的大小。另外,进一步加入碳质还原剂覆盖在铺盖于炉床的碳质还原剂上载置的颗粒时,无特别限定,例如,如图3(B)的示意图所示,从被覆盖的颗粒20的上端至碳质还原剂10层的表面为止的厚度“X”优选为上述颗粒的高度方向(图3(B)中的箭头H)大小(在球状颗粒的情况下为直径)的至少5%以上。例如,考虑到颗粒尺寸通常为10~30mm左右的大小,则颗粒大小的5%为0.5mm~1.5mm左右。如此地,通过使图3(B)所示的厚度X为颗粒20的高度方向H的大小的5%以上,从而能够在可操作管理的范围内,并且成为用碳质还原剂完全覆盖颗粒的状态,上述碳质还原剂不破坏形状,随着冶炼反应的进行,更有效地发挥作为所谓的壳的作用。当厚度X小于颗粒尺寸的5%时,操作控制变得困难,由于操作上的偏差导致颗粒表面从碳质还原剂层露出至冶炼炉内的空间。在这种情况下,不能维持对于冶炼反应而言重要的壳内(空间内)还原环境,不能进行适当的冶炼反应。另一方面,若厚度X为颗粒尺寸的5%以上,虽然能够发挥上述效果,但是,即使厚度X过大,效果也不累积,使用的碳质还原剂的成本增加。另外,当厚度X过大时,由于颗粒中的热的传导变得困难,燃料成本增加。因此,作为上限值,厚度X优选为颗粒尺寸的10%以下左右。另外,作为将制造的颗粒装入冶炼炉内时的温度,即,作为从开始将颗粒装入冶炼炉内至用碳质还原剂完全覆盖颗粒为止的操作时的温度,优选为600℃以下。另外,从使碳质还原剂缓慢烧结的影响为最低限度的观点出发,更优选为550℃以下。装入颗粒时的温度大于600℃时,覆盖颗粒的碳质还原剂可能开始燃烧。另一方面,在进行连续的冶炼处理的过程时,如果过于降低温度,则在升温成本方面是不利的,因此,作为下限值,无特别限定,优选为500℃以上。需要说明的是,即使不将装入颗粒时的温度控制在上述温度的情况下,若在不产生燃烧、烧结的影响的短时间内将颗粒装入冶炼炉中,也没有特别的问题。实施例下面,示出实施例和比较例,更具体地说明本发明,但是,本发明并不限定于以下实施例。[实施例1]将作为原料矿石的镍氧化矿、铁矿石、作为助熔剂成分的硅砂和石灰石、粘合剂混合,得到混合物。需要说明的是,不混合作为原料的碳质还原剂。然后,在得到的原料粉末混合物中添加适量水分,用手捏成球状的块状物。接着,为了使得到的块状物的固体成分为70重量%左右,水分为30重量%左右,对块状物吹300℃~400℃的热风,实施干燥处理。制造不包含碳质还原剂的球状颗粒(尺寸(直径):17mm)。另外,在下述表3中示出干燥处理后颗粒的固体成分组成。[表3]然后,在冶炼炉中,将作为碳质还原剂的煤炭粉(碳含量:55重量%,粒度:0.4mm)在炉床上铺满,在铺盖于上述炉床上的碳质还原剂上载置并装入制造的100个颗粒,用作为碳质还原剂的煤炭粉进一步覆盖载置的颗粒。此时,用煤炭粉覆盖颗粒以使从被覆盖颗粒的上端至碳质还原剂层的表面为止的厚度(图3中的X)为约1mm(颗粒的大小(直径)的约5%)。需要说明的是,将颗粒装入冶炼炉时,在600℃以下的温度条件下进行。接着,将还原温度设定为1400℃,在冶炼炉内进行还原加热处理。观察还原加热处理开始三分钟后(在颗粒表层形成金属壳后,金属壳不溶解,维持颗粒形状的时间范围)的状态,数出崩解颗粒的个数,作为颗粒崩解的比例,基于上述个数计算崩解个数/装入个数的百分率(%)。其结果,在实施例1中,崩解的颗粒的比例为0%,完全没有崩解的颗粒。然后,继续进行还原加热处理的结果是,颗粒不崩解且维持其形状,同时,冶炼反应有效地进行,得到金属与炉渣接合的“不倒翁”状的块状物。[比较例1]在颗粒的制造中,混合作为原料的碳质还原剂,制造颗粒,在仅将上述颗粒载置在铺盖在炉床上的碳质还原剂的状态下进行还原加热处理。另外,在冶炼炉内,没有用碳质还原剂覆盖颗粒。除此之外的条件与实施例1相同。其结果,在比较例1中,崩解颗粒的比例为15%,而且不能抑制颗粒的崩解。然后,继续进行还原加热处理的结果是,对于崩解的颗粒而言,由于颗粒崩解,因此,不能得到金属与炉渣接合的“不倒翁”状的块状物。[比较例2]在颗粒的制造中,不混合作为原料的碳质还原剂,而制造不含有碳质还原剂的颗粒,在仅将上述颗粒载置在铺盖在炉床上的碳质还原剂上的状态下进行还原加热处理。另外,在冶炼炉内,没有用碳质还原剂覆盖颗粒。除此之外的条件与实施例1相同。其结果,在比较例2中,崩解颗粒的比例为0%,完全没有崩解的颗粒。但是,接着,进行还原处理的结果是,由于颗粒表面处于未与碳质还原剂接触的状态,因此,冶炼反应不能有效地进行,不能得到金属与炉渣接合的“不倒翁”状的块状物。当前第1页1 2 3