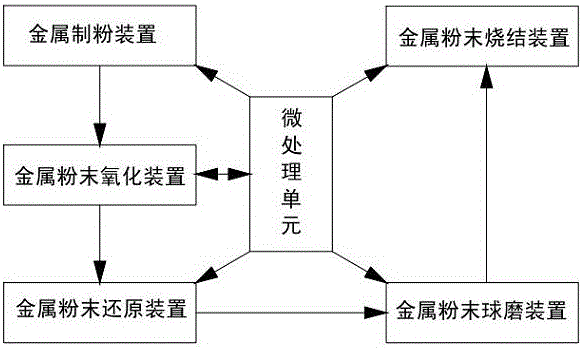
一种弥散强化铜自动加工系统,属于粉末冶金技术领域。
背景技术:
弥散强化铜是以弥散分布的纳米金属颗粒为强化相的复合材料,细小坚硬的金属颗粒通过钉扎和阻碍位错的运动,提高了铜基体的强度和硬度,特别是高温下的强度和硬度。由于具有高强度、高硬度、高软化温度、高导热性和高导电性等优异的综合性能,弥散强化铜已在焊接、电子、电器、冶金等领域得到了广泛的应用,如弥散强化铜制备的电阻焊电极、缝焊滚轮、焊炬喷嘴在焊接时不易变形、不粘结、不发生元素扩散、焊接质量好;此外,弥散强化铜是制作集成电路引线框架、电器工程开关触桥、电子真空器件、连铸机结晶器内衬、发电机集电环、电枢、转子、电车及电力火车架空导线等的优良材料。
现有技术中弥散强化铜的加工系统复杂、各加工工序相对独立、自动化程度低,从而导致弥散强化铜生产过程中的质量控制不够稳定,次品率偏高;目前国内大部分的弥散强化铜还需依赖进口,进而造成使用其作为原材料的产品成本居高不下。
技术实现要素:
本实用新型要解决的技术问题是:克服现有技术的不足,提供一种控制结构简单、自动化程度高、出产成品合格率高的弥散强化铜自动加工系统。
本实用新型解决其技术问题所采用的技术方案是:该弥散强化铜自动加工系统,包括金属制粉装置、金属粉末氧化装置、金属粉末还原装置、金属粉末球磨装置和金属粉末烧结装置,所述金属制粉装置、金属粉末氧化装置、金属粉末还原装置、金属粉末球磨装置和金属粉末烧结装置依次通过输送机构连接,所述金属制粉装置为高压水雾化制粉装置,包括漏包、金属液导管、高压水室、高压喷嘴、金属粉末收集箱和保温层;所述保温层设置在金属液导管的外部并紧密结合,金属液导管的两侧对称设置高压水室,每个高压水室底部设置高压喷嘴,高压喷嘴的下方设置金属粉末收集箱。
优选的,所述金属粉末氧化装置包括内氧化气源、氧化真空泵、氧化三通电磁阀、气体通道、冷却机构、内氧化炉、内氧化滚筒、内氧化炉座、动力机构和温度传感器;所述内氧化气源、氧化真空泵、内氧化炉和动力机构均设置在内氧化炉座上,气体通道通过氧化三通电磁阀分别与内氧化气源和氧化真空泵相连,气体通道可旋转地设置在内氧化滚筒的一端,内氧化滚筒的另一端的内部设置有温度传感器。
优选的,所述内氧化滚筒的两端均设置有冷却机构,内氧化滚筒的中心筒体设置在内氧化炉内部。
优选的,所述温度传感器为电热偶管。
优选的,所述金属粉末还原装置包括氢气管路、还原真空泵、真空管路、真空管路截止阀、主气体管路截止阀、还原三通电磁阀、氮气管路、氮气罐、真空管式炉、氢还原炉管、氢还原台、泄压管路、泄压管路截止阀、主气体管路和氢气罐;所述氢气罐和氮气罐分别设置在真空管式炉的两侧,氢气罐经氢气管路、还原三通电磁阀和主气体管路截止阀连接到主气体管路,氮气罐经氮气管路、还原三通电磁阀和主气体管路截止阀连接到主气体管路,主气体管路与真空管式炉相连,还原真空泵通过真空管路和真空管路截止阀与主气体管路相连,氢还原炉管内部设置有氢还原台,氢还原炉管设置在真空管式炉的内部中心位置,泄压管路通过泄压管路截止阀与真空管式炉相连。
优选的,所述真空管路截止阀、主气体管路截止阀和泄压管路截止阀均为截止式电磁阀。
优选的,所述氢气管路与还原三通电磁阀之间设置有氢气管路压力传感器,输送氮气管路与还原三通电磁阀之间设置有氮气管路压力传感器,主气体管路与真空管式炉的底部之间设置有主气体管路压力传感器,泄压管路与真空管式炉之间设置有泄压管路压力传感器。
优选的,所述氢气管路压力传感器、氮气管路压力传感器、泄压管路压力传感器和主气体管路压力传感器均为扩散硅压力变送器。
优选的,该弥散强化铜自动加工系统还包括微处理单元,微处理单元通过信号线分别与金属制粉装置、金属粉末氧化装置、金属粉末还原装置、金属粉末球磨装置和金属粉末烧结装置互联。
优选的,所述动力机构为智能伺服电机及其控制器总成。
优选的,所述金属粉末球磨装置为添加金属粉末专用酸洗液的高能球磨机。
优选的,所述金属粉末烧结装置为金属粉末专用自动烧结机。
与现有技术相比,该弥散强化铜自动加工系统的上述技术方案所具有的有益效果是:
1、设置的高压水雾化制粉装置,在金属液导管的两侧对称设置高压水室,每个高压水室底部设置高压喷嘴,高压喷嘴的下方设置金属粉末收集箱,解决了制粉过程中部分合金元素的微观偏聚问题,使金属粉体粒度更加细腻均匀,同时实现了金属粉末的自动收集。
2、该弥散强化铜自动加工系统包括微处理单元和与其互联的金属制粉装置、金属粉末氧化装置、金属粉末还原装置、金属粉末球磨装置和金属粉末烧结装置,在加工弥散强化铜的各工序中,由微处理单元根据与其互联的所述各装置的反馈信号进行自动控制,克服了现有技术中弥散强化铜的加工系统复杂、各加工工序相对独立、自动化程度低,从而导致的弥散强化铜生产过程中的质量控制不够稳定,次品率偏高的不足,该弥散强化铜自动加工系统简单、高效,实现了弥散强化铜加工的自动化,提高了产品合格率。
3、设置的金属粉末氧化装置的内氧化滚筒,接收来自高压水雾化制粉装置的金属粉末收集箱输送的金属粉末,预先调配好的内氧化气源的混合氧化气体,经氧化三通电磁阀和气体通道进入内氧化滚筒内,由微处理单元根据温度传感器的反馈信号,与冷却机构一起控制内氧化炉内的内氧化滚筒维持在合适的温度范围内,内氧化滚筒在由微处理单元控制的动力机构的带动下,实现对筒内金属粉末的选择性氧化。
4、设置的金属粉末还原装置的氢还原台,接收来自金属粉末氧化装置的内氧化滚筒输出的金属粉末,通过还原真空泵对氢还原炉管抽真空,微处理单元根据主气体管路的气压信号,关闭还原真空泵和真空管路截止阀,使还原三通电磁阀连接氢气管路的一路和连接主气体管路截止阀的一路保持开通状态,此时,氢气罐中的氢气通过主气体管路进入氢还原炉管,微处理单元根据泄压管路的压力信号和反复的抽真空动作,实现对氢还原炉内压力的自动控制;与此同时,微处理单元控制根据真空管式炉的温度传感信号,实现对真空管式炉内氢还原炉管的自动加热功能,当氢还原炉管被加热至预设最佳氢还原反应温度时,微处理单元根据主气体管路压力与泄压管路压力的差值信号,控制还原三通电磁阀与氮气管路连接的一路和与主气体管路连接的一路为开通状态,此时氮气罐内的氮气经主气体管路进入氢还原炉管内,实现了金属粉末的自动低氧化处理过程。
5、设置的金属粉末球磨装置的原料入口,接收来自金属粉末还原装置的氢还原台的金属粉末,并采用金属粉末专用酸洗液、由微处理单元控制高能球磨机进行该金属粉末的处理,可自动、有效地去除金属粉末表面氧化物的夹杂。
6、设置的金属粉末烧结装置采用金属粉末专用自动烧结机,由微处理单元控制自动烧结机完成对球磨装置输出的金属粉末的烧结操作,实现了对金属粉末进行烧结的自动控制。
附图说明
图1 弥散强化铜自动加工系统结构框图。
图2 高压水雾化制粉装置结构示意图。
图3 金属粉末氧化装置结构示意图。
图4 金属粉末还原装置结构示意图。
其中:1、漏包 2、金属液导管 3、高压水室 4、高压喷嘴 5、金属粉末收集箱 6、保温层 7、金属液 8、内氧化气源 9、氧化真空泵 10、氧化三通电磁阀 11、气体通道 12、冷却机构 13、内氧化炉 14、内氧化滚筒 15、内氧化炉座 16、动力机构 17、温度传感器 18、氢气管路 19、氢气管路压力传感器 20、还原真空泵 21、真空管路截止阀 22、主气体管路截止阀 23、还原三通电磁阀 24、氮气管路 25、氮气管路压力传感器 26、氮气罐 27、真空管式炉 28、信号输送单元 29、氢还原炉管 30、金属合金粉末 31、氢还原台 32、泄压管路 33、泄压管路压力传感器 34、泄压管路截止阀 35、主气体管路压力传感器 36、主气体管路 37、真空管路 38、氢气罐。
具体实施方式
下面结合附图1~4对本实用新型做进一步说明。
参照图1,弥散强化铜自动加工系统结构示意图,包括微处理单元、金属制粉装置、金属粉末氧化装置、金属粉末还原装置、金属粉末球磨装置和金属粉末烧结装置,所述金属制粉装置、金属粉末氧化装置、金属粉末还原装置、金属粉末球磨装置和金属粉末烧结装置依次通过输送机构连接,微处理单元通过信号线分别与金属制粉装置、金属粉末氧化装置、金属粉末还原装置、金属粉末球磨装置和金属粉末烧结装置互联。金属粉末球磨装置为添加金属粉末专用酸洗液的高能球磨机。金属粉末烧结装置为金属粉末专用自动烧结机。
参照图2,高压水雾化制粉装置结构示意图,包括漏包1、金属液导管2、高压水室3、高压喷嘴4、金属粉末收集箱5和保温层6;保温层6设置在金属液导管2的外部并紧密结合,金属液导管2的两侧对称设置高压水室3,每个高压水室3的底部设置高压喷嘴4,高压喷嘴4的下方设置金属粉末收集箱5。漏包1内设置金属冶炼专用耐高温液位传感器,该传感器与微处理单元通过信号线相连,用于检测漏包1内金属液7的液位高度,金属液导管2内底部设置截止式电磁阀,高压水室3内设置启动控制单元;当微处理单元根据耐高温液位传感器的反馈信号检测到漏包1内的金属液7的容量符合制粉要求时,漏包1内停止输送金属液7,微处理单元控制金属液导管2内底部的截止式电磁阀为开通状态,同时发送指令给高压水室3内的启动控制单元,金属液7在高压喷嘴4的喷射下形成符合目标粒度目数的金属合金粉末30,该粉末被金属粉末收集箱5收集,当微处理单元检测到漏包1内无金属液7时,5分钟后,微处理单元控制金属液导管2内底部的截止式电磁阀为关断状态,微处理单元发送指令控制传动机构将金属粉末收集箱5传送至金属粉末氧化工序,同时,高压水室3接收微处理单元发送的停止信号后,停止工作;微处理单元发送指令控制前端输送机构将另一空置的金属粉末收集箱5传送至金属液导管2的正下方,等待下一时刻的高压水雾化制粉工序启动。
参照图3,金属粉末氧化装置结构示意图,包括内氧化气源8、氧化真空泵9、氧化三通电磁阀10、气体通道11、冷却机构12、内氧化炉13、内氧化滚筒14、内氧化炉座15、动力机构16和温度传感器17;内氧化气源8、氧化真空泵9、内氧化炉13和动力机构16均设置在内氧化炉座15上,气体通道11通过氧化三通电磁阀10分别与内氧化气源8和氧化真空泵9相连,气体通道11可旋转地设置在内氧化滚筒14的一端,内氧化滚筒14的另一端的内部设置有温度传感器17,内氧化滚筒14的另一端的外部连接动力机构16,内氧化滚筒14的两端均设置有冷却机构12,内氧化滚筒14的中心筒体设置在内氧化炉13的内部。动力机构16为智能伺服电机及其控制器总成。温度传感器17为电热偶管。
金属粉末氧化装置在其输送机构的两侧还设置有由微处理单元控制的起吊机构和倾倒机构,内氧化滚筒14设置有智能滚筒盖和智能端盖,智能滚筒盖被设置在内氧化滚筒14的中心位置,智能端盖设置在内氧化滚筒14与气体通道11连接的一端,初始时智能滚筒盖和智能端盖均为关闭状态。当图2中的金属粉末收集箱5内的金属合金粉末30被输送至该金属粉末氧化工序时,微处理单元控制内氧化滚筒14的智能滚筒盖为打开状态,同时控制倾倒机构将金属合金粉末30倒入内氧化滚筒14内,金属粉末收集箱5为待岗状态;此后,微处理单元控制内氧化滚筒14的智能滚筒盖为关闭状态,同时微处理单元控制氧化真空泵9为启动状态,并控制氧化三通电磁阀10连接氧化真空泵9和气体通道11的一路处于导通状态,即对内氧化滚筒14开始进行抽真空操作,15分钟后,微处理单元发送控制信号关闭氧化真空泵9和氧化三通电磁阀10连接氧化真空泵9和气体通道11的一路,同时发送控制信号控制氧化三通电磁阀10连接内氧化气源8和气体通道11的一路处于开通状态,即对内氧化滚筒14开始充氧,微处理单元发送指令使内氧化炉13处于加热状态,微处理单元根据温度传感器17的反馈信号,与冷却机构12一起控制内氧化炉13内的内氧化滚筒14维持在合适的温度范围内,同一时刻,微处理单元控制智能伺服电机启动,与其连接的内氧化滚筒14也开始在加热的内氧化炉13中滚动,从而实现对筒内金属合金粉末30的选择性氧化。氧化后的金属合金粉末30,由微处理单元控制起吊机构将内氧化炉13吊起倾斜,并控制智能伺服电机保持工作状态,进而内氧化滚筒14也处于滚动状态,微处理单元发送信号控制内氧化滚筒14的端盖打开,氧化后的金属合金粉末30被倾倒在待岗的金属粉末收集箱5内,传送至下一工序。
参照图4,金属粉末还原装置结构示意图,包括氢气管路18、氢气管路压力传感器19、还原真空泵20、真空管路37、真空管路截止阀21、主气体管路截止阀22、还原三通电磁阀23、氮气管路24、氮气管路压力传感器25、氮气罐26、真空管式炉27、信号输送单元28、氢还原炉管29、氢还原台31、泄压管路32、泄压管路压力传感器33、泄压管路截止阀34、主气体管路压力传感器35、主气体管路36和氢气罐38;氢气罐38和氮气罐26分别设置在真空管式炉27的两侧,氢气罐38经氢气管路18、还原三通电磁阀23和主气体管路截止阀22连接到主气体管路36,氢气管路18与还原三通电磁阀23之间设置有氢气管路压力传感器19,氮气罐26经氮气管路24、还原三通电磁阀23和主气体管路截止阀22连接到主气体管路36,氮气管路24与还原三通电磁阀23之间设置有氮气管路压力传感器25,主气体管路36与真空管式炉27相连,主气体管路36与真空管式炉27的底部之间设置有主气体管路压力传感器35,还原真空泵20通过真空管路37和真空管路截止阀21与主气体管路36相连,氢还原炉管29内部设置有氢还原台31,氢还原炉管29设置在真空管式炉27的内部中心位置,泄压管路32通过泄压管路截止阀34与真空管式炉27相连,泄压管路32与真空管式炉27之间设置有泄压管路压力传感器33,信号输送单元28与微处理单元通过信号线相连。真空管路截止阀21、主气体管路截止阀22和泄压管路截止阀34均为截止式电磁阀。氢气管路压力传感器19、氮气管路压力传感器25、泄压管路压力传感器33和主气体管路压力传感器35均为扩散硅压力变送器。
金属粉末还原装置在其输送机构的一侧还设置有由微处理单元控制的倾倒机构,上一工序中金属粉末收集箱5内的氧化后的金属合金粉末30,在由微处理单元控制的输送机构和倾倒机构的作用下被输送至氢还原炉管29内的氢还原台31中,金属粉末收集箱5处于待岗状态;氢还原台31底部设置重量传感器,微处理单元接收到重量传感器感的预设重量信号后,微处理单元发送指令信号控制启动还原真空泵20,真空管路截止阀21处于开通状态,当微处理单元检测到主气体管路压力传感器35的压力信号符合预设真空度要求时,微处理单元发出控制指令关闭还原真空泵20,真空管路截止阀21处于关断状态,同时微处理单元发出指令控制还原三通电磁阀23连接氢气管路18与主气体管路截止阀22连通的一路为开通状态,同时根据氢气管路压力传感器19的传感信号测定氢还原炉管29内的氢气压力和氢气通入速率,30分钟后,微处理单元控制真空管式炉27加热4小时后停止,当微处理单元检测到氢还原炉管29内的氢气压力符合预设标准时,微处理单元发送控制指令,使还原三通电磁阀23连接氮气管路24和主气体管路截止阀22的一路为开通状态,此时氮气罐26的氮气经主气体管路36进入氢还原炉管29内,微处理单元根据氮气管路压力传感器25的压力传感信号测定氮气的压力和流速,1小时后,微处理单元发出控制信号关闭主气体管路截止阀22,氢还原台31的金属合金粉末30的低氧化处理完成。上述所有传感器信号均发送至信号输送单元28,并由其发送至微处理单元进行信号处理。
参照图1~图4,弥散强化铜自动加工系统的自动加工过程:
A、制粉工序,经金属液化工序后的金属液7被输送到漏包1中,当微处理单元检测到漏包1内的金属液7的容量符合制粉要求时,微处理单元控制金属液导管2内底部的截止式电磁阀为开通状态,同时发送指令给高压水室3内的启动控制单元,金属液7在高压喷嘴4的喷射下形成符合目标粒度目数的金属合金粉末30,该粉末被金属粉末收集箱5收集;
B、内氧化工序,微处理单元控制内氧化滚筒14的智能滚筒盖为打开状态,同时控制倾倒机构将金属粉末收集箱5内的金属合金粉末30倒入内氧化滚筒14内,金属粉末收集箱5为待岗状态;微处理单元控制内氧化滚筒14的智能滚筒盖为关闭状态,同时微处理单元控制氧化真空泵9为启动状态,对内氧化滚筒14开始进行抽真空操作,15分钟后,微处理单元发送控制信号对内氧化滚筒14开始充氧,微处理单元发送指令使内氧化炉13处于加热状态,微处理单元控制智能伺服电机启动,与其连接的内氧化滚筒14也开始在加热的内氧化炉13中滚动,从而实现对筒内金属合金粉末30的选择性氧化,氧化后的金属合金粉末30,由微处理单元控制起吊机构将内氧化炉13吊起倾斜,并控制智能伺服电机保持工作状态,进而内氧化滚筒14也处于滚动状态,微处理单元发送信号控制内氧化滚筒14的端盖打开,氧化后的金属合金粉末30被倾倒在待岗的金属粉末收集箱5内。
C、氢还原工序,金属粉末收集箱5内的氧化后的金属合金粉末30,在由微处理单元控制的输送机构和倾倒机构的作用下被输送至氢还原炉管29内的氢还原台31中,同时金属粉末收集箱5处于待岗状态;微处理单元发送指令信号控制启动还原真空泵20,真空管路截止阀21处于开通状态,当微处理单元检测到主气体管路压力传感器35的压力信号符合预设真空度要求时,微处理单元发出控制指令关闭还原真空泵20,真空管路截止阀21处于关断状态,同时微处理单元发出指令控制还原三通电磁阀23连接氢气管路18与主气体管路截止阀22连通的一路为开通状态,30分钟后,微处理单元控制真空管式炉27加热4小时后停止,当微处理单元检测到氢还原炉管29内的氢气压力符合预设标准时,微处理单元发送控制指令,使还原三通电磁阀23连接氮气管路24和主气体管路截止阀22的一路为开通状态,此时氮气罐26的氮气经主气体管路36进入氢还原炉管29内,1小时后,微处理单元发出控制信号关闭主气体管路截止阀22,氢还原台31的金属合金粉末30的低氧化处理完成。低氧化处理后的金属合金粉末30,被由微处理单元控制的倾倒机构倾倒至待岗的金属粉末收集箱5内。
D、球磨酸洗工序,微处理单元控制输送机构,将氢还原工序的金属粉末收集箱5内的金属合金粉末30,送入添加金属粉末专用酸洗液的高能球磨机的原料入口内,进行粉末表面氧化物的夹杂处理,同时微处理单元控制输送机构将金属粉末收集箱5输送至高能球磨机的物料出口处待岗,待处理完成后,微处理单元控制高能球磨机的物料出口为打开状态,球磨酸洗处理后的金属合金粉末30被倾倒至待岗的金属粉末收集箱5内。
E、烧结工序,微处理单元控制输送机构,将球磨酸洗工序的金属粉末收集箱5内的金属合金粉末30,送入金属粉末专用自动烧结机内进行烧结操作,同时微处理单元控制输送机构将金属粉末收集箱5输送至制粉工序工位待岗,烧结成型后的弥散强化铜烧结锭或棒材,被输送至后续代加工工序。后续代加工工序,根据具体制品的不同尺寸和形状可选择轧制、拉拔、冷冲、机加工等具体工艺,最终获得不同应用产品。
以上所述,仅是本实用新型的较佳实施例而已,并非是对本实用新型作其它形式的限制,任何熟悉本专业的技术人员可能利用上述揭示的技术内容加以变更或改型为等同变化的等效实施例。但是凡是未脱离本实用新型技术方案内容,依据本实用新型的技术实质对以上实施例所作的任何的简单修改、等同变化与改型,仍属于本实用新型技术方案的保护范围。