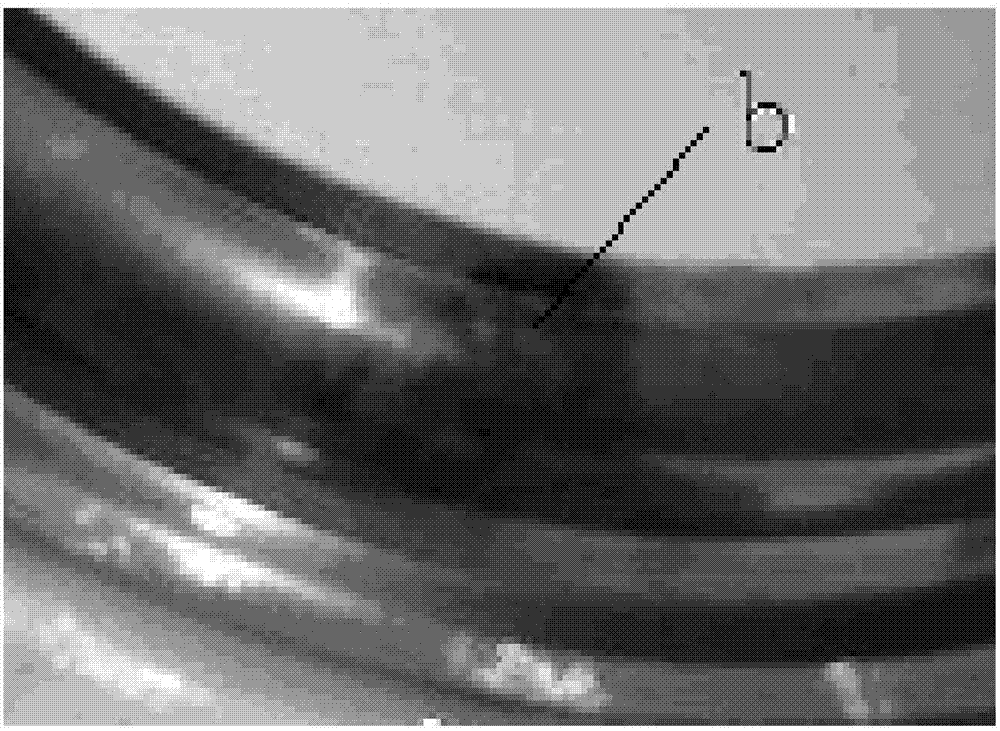
本发明涉及一种磨削烧伤检测的酸洗腐蚀方法。
背景技术:
现有技术中,材质为cr4mo4v、8cr4mo4v、s8cr4mo4v、m50、w9cr4v2mo、g13cr4mo4ni4v或sg13cr4mo4ni4v等的轴承零件在磨削加工过程中容易因为一些原因如磨削加工参数违反工艺要求、设备故障、应用了不适合的磨料、冷却液性能不良等,会产生磨削烧伤,如果带有磨削烧伤缺陷的轴承产品被应用了,这样的轴承经运转受力会产生疲劳剥落或碎裂,直接影响到整套轴承的使用寿命和安全;烧伤有两种状态,一种为回火烧伤,一种为淬火烧伤或再硬化烧伤,回火烧伤为工件部分区域变暗且随酸洗加深变黑,相对于周围区域由浅棕至黑,边缘明显清晰且沿着加工方向;淬火烧伤或再硬化烧伤为工件区域因酸洗从浅灰到白,周边呈浅棕色或黑色。
目前的实际生产应用中,酸洗腐蚀过程包括盐酸酸洗、硝酸酸洗和盐酸明化,盐酸酸洗、硝酸酸洗或盐酸明化的时间较长,均为1.5min~2.5min;酸洗检查工序由原有的套圈沟道细磨之后调整为套圈沟道终磨之后,这样酸洗检查后序机械加工留量变小,进而造成酸洗检查后的光饰和精研工序无法将腐蚀层去除完全而造成零件表面缺陷;
对于轴承零件酸洗检查磨削烧伤的方法来说,要有效控制酸洗过程及检查产品磨削烧伤,不仅要选择合适的酸洗溶液成份与配比,确定合理的酸洗工艺流程和工艺参数,还要确定有效的磨削烧伤检查标准,并做好过程控制。
技术实现要素:
本发明为了解决现有的轴承零件的酸洗检查工序从套圈沟道细磨工序后进行调整至终磨工序后进行,进而造成后序机械加工留量变小,酸洗检查后的光饰和精研工序无法将腐蚀变质层去除完全,进而造成零件表面缺陷的问题,提供一种用于轴承零件表面磨削烧伤检测的酸洗腐蚀方法。
本发明用于轴承零件表面磨削烧伤检测的酸洗腐蚀方法,该方法按以下步骤依次进行;
一、将轴承零件浸入75~95℃的脱脂液中,抖动轴承零件5~10min;
二、然后将轴承零件浸入75~85℃的热水中,抖动轴承零件1~2min;
三、然后将轴承零件转移至盛有室温的流动水的容器中,并将轴承零件浸入室温的流动水中,抖动轴承零件1~2min;
四、然后将轴承零件从室温的流动水中取出,目视检查零件表面水膜,如水膜在30秒内不断裂,则进行步骤五,如水膜在30秒内断裂则重复步骤一至四;
五、然后将轴承零件浸入室温的盐酸液中,抖动轴承零件15~45s;
六、然后将轴承零件转移至盛有室温的流动水的容器中,并将轴承零件浸入室温的流动水中,抖动轴承零件1~2min;
七、然后将轴承零件浸入室温的硝酸液中,抖动轴承零件15~45s;
八、然后将轴承零件转移至盛有室温的流动水的容器中,并将轴承零件浸入室温的流动水中,抖动轴承零件1~2min;
九、然后将轴承零件浸入室温的盐酸液中,抖动轴承零件15~45s;
十、然后将轴承零件转移至盛有室温的流动水的容器中,并将轴承零件浸入室温的流动水中,抖动轴承零件3~5min;
十一、然后将轴承零件浸入室温的中和液中,抖动轴承零件5~30min;
十二、然后将轴承零件转移至盛有室温的流动水的容器中,并将轴承零件浸入室温的流动水中,抖动轴承零件1~2min;
十三、然后将轴承零件浸入室温的防锈液中,抖动轴承零件1~2min,即完成;
进一步的,所述脱脂液由无水碳酸钠、磷酸三钠、氢氧化钠和去离子水组成;脱脂液中,无水碳酸钠的质量分数为2.5~3.5%,磷酸三钠的质量分数为2.5~3.5%,氢氧化钠的质量分数为1~2%;
进一步的,所述无水碳酸钠的纯度规格为基准试剂、优级纯试剂、分析纯试剂或化学纯试剂;所述磷酸三钠的纯度规格为基准试剂、优级纯试剂、分析纯试剂或化学纯试剂;所述氢氧化钠的纯度规格为基准试剂、优级纯试剂、分析纯试剂或化学纯试剂;
进一步的,步骤五所述盐酸液由质量分数为36~38%的盐酸和去离子水组成,盐酸和去离子水的体积比为(4~6):100;所述盐酸的纯度规格为优级纯试剂;
进一步的,所述硝酸液由质量分数为65~68%的硝酸和去离子水组成,硝酸和去离子水的体积比为(3~5):100;所述硝酸的纯度规格为优级纯试剂;
进一步的,步骤九所述盐酸液由质量分数为36~38%的盐酸和去离子水组成,盐酸和去离子水的体积比为(4~6):100;所述盐酸的纯度规格为优级纯试剂;
进一步的,所述中和液由无水碳酸钠和去离子水组成,中和液中无水碳酸钠的质量分数为3~5%;所述无水碳酸钠的纯度规格为基准试剂、优级纯试剂、分析纯试剂或化学纯试剂;
进一步的,所述防锈液由亚硝酸钠、无水碳酸钠和去离子水组成,防锈液中亚硝酸钠的质量分数为8~10%,防锈液中无水碳酸钠的质量分数为1~2%;所述亚硝酸钠的纯度规格为基准试剂、优级纯试剂、分析纯试剂或化学纯试剂;所述无水碳酸钠的纯度规格为基准试剂、优级纯试剂、分析纯试剂或化学纯试剂;
进一步的,所述去离子水的电导率小于20μs/cm;
进一步的,所述零件的材质为cr4mo4v、8cr4mo4v、s8cr4mo4v、m50、w9cr4v2mo、g13cr4mo4ni4v或sg13cr4mo4ni4v;
进一步的,所述抖动轴承零件时抖动频率是120~140次/分钟,抖动幅度为3~6cm。
本发明具备以下有益效果:
1、本发明经过长期的生产实践应用,对于轴承零件使用该酸洗方法,可以有效保证检出零件磨削烧伤,保证有效检出磨削烧伤的同时提高产品外观质量,酸洗检查后的光饰和精研工序能够将腐蚀变质层去除完全,避免了零件表面缺陷产生,提高产品表面外观质量,解决了前期存在的生产瓶颈问题;
2、本发明方法在保证有效检出磨削烧伤的前提下,不改变槽液成份及浓度,尽可能的缩短腐蚀时间以达到减小腐蚀量的目的;
3、本发明中轴承零件酸洗线上除加热槽之外的槽液温度随环境温度变化而变化,经监测槽液温度范围在10~25℃之间,试验验证时实测酸槽液温度13℃,处于10~25℃的下限附近,此时采用本发明方法可以有效检出烧伤,随酸槽液温度升高腐蚀会逐渐加深,烧伤会更明显被检出,采用本发明方法不会发生因腐蚀程度不够而导致缺陷漏检情况,同时也说明本发明方法不需要高温实现;
4、采用本发明方法进行了4年左右的大量产品酸洗应用和后序跟踪,本发明方法可以有效检出磨削烧伤的同时提高产品外观质量,避免精研后产品零件表面缺陷产生,并且本发明方法已经正式确定为生产工艺,应用该方法后未发现产品缺陷漏检情况。
附图说明:
图1为实施例1中酸洗腐蚀后的cr4mo4v钢轴承零件,其中a为检出的磨削烧伤;
图2为实施例2中酸洗腐蚀后的w9cr4v2mo钢钢轴承零件,其中b为检出的磨削烧伤;
图3为实施例3中酸洗腐蚀后的g13cr4mo4ni4v钢轴承零件,其中c为检出的磨削烧伤。
具体实施方式:
本发明技术方案不局限于以下所列举具体实施方式,还包括各具体实施方式间的任意合理组合。
具体实施方式一:本实施方式一种用于轴承零件表面磨削烧伤检测的酸洗腐蚀方法,该方法按以下步骤依次进行;
一、将轴承零件浸入75~95℃的脱脂液中,抖动轴承零件5~10min;
二、然后将轴承零件浸入75~85℃的热水中,抖动轴承零件1~2min;
三、然后将轴承零件转移至盛有室温的流动水的容器中,并将轴承零件浸入室温的流动水中,抖动轴承零件1~2min;
四、然后将轴承零件从室温的流动水中取出,目视检查零件表面水膜,如水膜在30秒内不断裂,则进行步骤五,如水膜在30秒内断裂则重复步骤一至四;
五、然后将轴承零件浸入室温的盐酸液中,抖动轴承零件15~45s;
六、然后将轴承零件转移至盛有室温的流动水的容器中,并将轴承零件浸入室温的流动水中,抖动轴承零件1~2min;
七、然后将轴承零件浸入室温的硝酸液中,抖动轴承零件15~45s;
八、然后将轴承零件转移至盛有室温的流动水的容器中,并将轴承零件浸入室温的流动水中,抖动轴承零件1~2min;
九、然后将轴承零件浸入室温的盐酸液中,抖动轴承零件15~45s;
十、然后将轴承零件转移至盛有室温的流动水的容器中,并将轴承零件浸入室温的流动水中,抖动轴承零件3~5min;
十一、然后将轴承零件浸入室温的中和液中,抖动轴承零件5~30min;
十二、然后将轴承零件转移至盛有室温的流动水的容器中,并将轴承零件浸入室温的流动水中,抖动轴承零件1~2min;
十三、然后将轴承零件浸入室温的防锈液中,抖动轴承零件1~2min,即完成。
本实施方式具备以下有益效果:
1、本实施方式经过长期的生产实践应用,对于轴承零件使用该酸洗方法,可以有效保证检出零件磨削烧伤,保证有效检出磨削烧伤的同时提高产品外观质量,酸洗检查后的光饰和精研工序能够将腐蚀变质层去除完全,避免了零件表面缺陷产生,提高产品表面外观质量,解决了前期存在的生产瓶颈问题;
2、本实施方式方法在保证有效检出磨削烧伤的前提下,不改变槽液成份及浓度,尽可能的缩短腐蚀时间以达到减小腐蚀量的目的;
3、本实施方式中轴承零件酸洗线上除加热槽之外的槽液温度随环境温度变化而变化,经监测槽液温度范围在10~25℃之间,试验验证时实测酸槽液温度13℃,处于10~25℃的下限附近,此时采用本发明方法可以有效检出烧伤,随酸槽液温度升高腐蚀会逐渐加深,烧伤会更明显被检出,采用本发明方法不会发生因腐蚀程度不够而导致缺陷漏检情况,同时也说明本发明方法不需要高温实现;
4、采用本实施方式方法进行了4年左右的大量产品酸洗应用和后序跟踪,本发明方法可以有效检出磨削烧伤的同时提高产品外观质量,避免精研后产品零件表面缺陷产生,并且本发明方法已经正式确定为生产工艺,应用该方法后未发现产品缺陷漏检情况。
具体实施方式二:本实施方式与具体实施方式一不同的是:步骤一所述脱脂液由无水碳酸钠、磷酸三钠、氢氧化钠和去离子水组成;脱脂液中,无水碳酸钠的质量分数为2.5~3.5%,磷酸三钠的质量分数为2.5~3.5%,氢氧化钠的质量分数为1~2%。其他步骤和参数与具体实施方式一相同。
具体实施方式三:本实施方式与具体实施方式二不同的是:所述无水碳酸钠的纯度规格为基准试剂、优级纯试剂、分析纯试剂或化学纯试剂;所述磷酸三钠的纯度规格为基准试剂、优级纯试剂、分析纯试剂或化学纯试剂;所述氢氧化钠的纯度规格为基准试剂、优级纯试剂、分析纯试剂或化学纯试剂。其他步骤和参数与具体实施方式二相同。
具体实施方式四:本实施方式与具体实施方式一至三之一不同的是:步骤五所述盐酸液由质量分数为36~38%的盐酸和去离子水组成,盐酸和去离子水的体积比为(4~6):100;所述盐酸的纯度规格为优级纯试剂。其他步骤和参数与具体实施方式一至三之一相同。
具体实施方式五:本实施方式与具体实施方式一至四之一不同的是:步骤七所述硝酸液由质量分数为65~68%的硝酸和去离子水组成,硝酸和去离子水的体积比为(3~5):100;所述硝酸的纯度规格为优级纯试剂。其他步骤和参数与具体实施方式一至四之一相同。
具体实施方式六:本实施方式与具体实施方式一至五之一不同的是:步骤九所述盐酸液由质量分数为36~38%的盐酸和去离子水组成,盐酸和去离子水的体积比为(4~6):100;所述盐酸的纯度规格为优级纯试剂。其他步骤和参数与具体实施方式一至五之一相同。
具体实施方式七:本实施方式与具体实施方式一至六之一不同的是:步骤十一所述中和液由无水碳酸钠和去离子水组成,中和液中无水碳酸钠的质量分数为3~5%;所述无水碳酸钠的纯度规格为基准试剂、优级纯试剂、分析纯试剂或化学纯试剂。其他步骤和参数与具体实施方式一至六之一相同。
具体实施方式八:本实施方式与具体实施方式一至七之一不同的是:步骤十三所述防锈液由亚硝酸钠、无水碳酸钠和去离子水组成,防锈液中亚硝酸钠的质量分数为8~10%,防锈液中无水碳酸钠的质量分数为1~2%;所述亚硝酸钠的纯度规格为基准试剂、优级纯试剂、分析纯试剂或化学纯试剂;所述无水碳酸钠的纯度规格为基准试剂、优级纯试剂、分析纯试剂或化学纯试剂。其他步骤和参数与具体实施方式一至七之一相同。
具体实施方式九:本实施方式与具体实施方式一至八之一不同的是:所述轴承零件的材质为cr4mo4v、8cr4mo4v、s8cr4mo4v、m50、w9cr4v2mo、g13cr4mo4ni4v或sg13cr4mo4ni4v。其他步骤和参数与具体实施方式一至八之一相同。
实施例1:本实施例一种用于轴承零件表面磨削烧伤检测的酸洗腐蚀方法,该方法按以下步骤依次进行;
一、将轴承零件浸83℃的脱脂液中,然后抖动轴承零件5min;
二、然后将轴承零件浸入80℃的热水中,抖动轴承零件1min;
三、然后将轴承零件转移至盛有室温的流动水的容器中,并将轴承零件浸入室温的流动水中,抖动轴承零件1min;
四、将轴承零件从室温的流动水中取出,目视检查零件表面水膜,如水膜在30秒内不断裂,则进行步骤五,如水膜在30秒内断裂则重复步骤一至四;
五、然后将轴承零件浸入室温的盐酸液中,抖动轴承零件30s;
六、然后将轴承零件转移至盛有室温的流动水的容器中,并将轴承零件浸入室温的流动水中,抖动轴承零件1min;
七、然后将轴承零件浸入室温的硝酸液中,抖动轴承零件15s;
八、然后将轴承零件转移至盛有室温的流动水的容器中,并将轴承零件浸入室温的流动水中,抖动轴承零件1min;
九、然后将轴承零件浸入室温的盐酸液中,抖动轴承零件30s;
十、然后将轴承零件转移至盛有室温的流动水的容器中,并将轴承零件浸入室温的流动水中,抖动轴承零件3min;
十一、然后将轴承零件浸入室温的中和液中,抖动轴承零件5min;
十二、然后将轴承零件转移至盛有室温的流动水的容器中,并将轴承零件浸入室温的流动水中,抖动轴承零件1min;
十三、然后将轴承零件浸入室温的防锈液中,抖动轴承零件1min,即完成;
进一步的,所述脱脂液由无水碳酸钠、磷酸三钠、氢氧化钠和去离子水组成;脱脂液中,无水碳酸钠的质量分数为3.5%,磷酸三钠的质量分数为3.5%,氢氧化钠的质量分数为2%;
进一步的,所述无水碳酸钠的纯度规格为化学纯试剂;所述磷酸三钠的纯度规格为化学纯试剂;所述氢氧化钠的纯度规格为化学纯试剂;
进一步的,步骤五所述盐酸液由质量分数为38%的盐酸和去离子水组成,盐酸和去离子水的体积比为4.37:100;所述盐酸的纯度规格为优级纯试剂;
进一步的,所述硝酸液由质量分数为68%的硝酸和去离子水组成,硝酸和去离子水的体积比为4.74:100;所述硝酸的纯度规格为优级纯试剂;
进一步的,步骤九所述盐酸液由质量分数为38%的盐酸和去离子水组成,盐酸和去离子水的体积比为4.45:100;所述盐酸的纯度规格为优级纯试剂;
进一步的,所述中和液由无水碳酸钠和去离子水组成,中和液中无水碳酸钠的质量分数为3%;所述无水碳酸钠的纯度规格为化学纯试剂;
进一步的,所述防锈液由亚硝酸钠、无水碳酸钠和去离子水组成,防锈液中亚硝酸钠的质量分数为9%,防锈液中无水碳酸钠的质量分数为1.5%;所述亚硝酸钠的纯度规格为化学纯试剂;所述无水碳酸钠的纯度规格为化学纯试剂;
进一步的,所述去离子水的电导率为7μs/cm;
进一步的,所述零件的材质为cr4mo4v;
进一步的,所述抖动轴承零件时抖动频率是125次/分钟,抖动幅度为4cm。
图1为实施例1中酸洗腐蚀后的cr4mo4v钢轴承零件照片,其中a为检出的磨削烧伤;从图1可以看出,本实施例可以有效检出烧伤,且烧伤较明显,易辨别。
实施例2:
一种用于轴承零件表面磨削烧伤检测的酸洗腐蚀方法,该方法按以下步骤依次进行;
一、将轴承零件浸83℃的脱脂液中,然后抖动轴承零件5min;
二、然后将轴承零件浸入80℃的热水中,抖动轴承零件1min;
三、然后将轴承零件转移至盛有室温的流动水的容器中,并将轴承零件浸入室温的流动水中,抖动轴承零件1min;
四、将轴承零件从室温的流动水中取出,目视检查零件表面水膜,如水膜在30秒内不断裂,则进行步骤五,如水膜在30秒内断裂则重复步骤一至四;
五、然后将轴承零件浸入室温的盐酸液中,抖动轴承零件30s;
六、然后将轴承零件转移至盛有室温的流动水的容器中,并将轴承零件浸入室温的流动水中,抖动轴承零件1min;
七、然后将轴承零件浸入室温的硝酸液中,抖动轴承零件30s;
八、然后将轴承零件转移至盛有室温的流动水的容器中,并将轴承零件浸入室温的流动水中,抖动轴承零件1min;
九、然后将轴承零件浸入室温的盐酸液中,抖动轴承零件30s;
十、然后将轴承零件转移至盛有室温的流动水的容器中,并将轴承零件浸入室温的流动水中,抖动轴承零件3min;
十一、然后将轴承零件浸入室温的中和液中,抖动轴承零件5min;
十二、然后将轴承零件转移至盛有室温的流动水的容器中,并将轴承零件浸入室温的流动水中,抖动轴承零件1min;
十三、然后将轴承零件浸入室温的防锈液中,抖动轴承零件1min,即完成;
进一步的,所述脱脂液由无水碳酸钠、磷酸三钠、氢氧化钠和去离子水组成;脱脂液中,无水碳酸钠的质量分数为3.5%,磷酸三钠的质量分数为3.5%,氢氧化钠的质量分数为2%;
进一步的,所述无水碳酸钠的纯度规格为化学纯试剂;所述磷酸三钠的纯度规格为化学纯试剂;所述氢氧化钠的纯度规格为化学纯试剂;
进一步的,步骤五所述盐酸液由质量分数为38%的盐酸和去离子水组成,盐酸和去离子水的体积比为4.37:100;所述盐酸的纯度规格为优级纯试剂;
进一步的,所述硝酸液由质量分数为68%的硝酸和去离子水组成,硝酸和去离子水的体积比为4.74:100;所述硝酸的纯度规格为优级纯试剂;
进一步的,步骤九所述盐酸液由质量分数为38%的盐酸和去离子水组成,盐酸和去离子水的体积比为4.45:100;所述盐酸的纯度规格为优级纯试剂;
进一步的,所述中和液由无水碳酸钠和去离子水组成,中和液中无水碳酸钠的质量分数为3%;所述无水碳酸钠的纯度规格为化学纯试剂;
进一步的,所述防锈液由亚硝酸钠、无水碳酸钠和去离子水组成,防锈液中亚硝酸钠的质量分数为9%,防锈液中无水碳酸钠的质量分数为2%;所述亚硝酸钠的纯度规格为化学纯试剂;所述无水碳酸钠的纯度规格为化学纯试剂;
进一步的,所述去离子水的电导率为7μs/cm;
进一步的,所述零件的材质为w9cr4v2mo;
进一步的,所述抖动轴承零件时抖动频率是125次/分钟,抖动幅度为4cm。
图2为实施例2中酸洗腐蚀后的w9cr4v2mo钢轴承零件照片,其中b为检出的磨削烧伤;从图2可以看出,本实施例可以有效检出烧伤,且烧伤较明显,易辨别。
实施例3:
一种用于轴承零件表面磨削烧伤检测的酸洗腐蚀方法,该方法按以下步骤依次进行;
一、将轴承零件浸83℃的脱脂液中,然后抖动轴承零件5min;
二、然后将轴承零件浸入80℃的热水中,抖动轴承零件1min;
三、然后将轴承零件转移至盛有室温的流动水的容器中,并将轴承零件浸入室温的流动水中,抖动轴承零件1min;
四、将轴承零件从室温的流动水中取出,目视检查零件表面水膜,如水膜在30秒内不断裂,则进行步骤五,如水膜在30秒内断裂则重复步骤一至四;
五、然后将轴承零件浸入室温的盐酸液中,抖动轴承零件45s;
六、然后将轴承零件转移至盛有室温的流动水的容器中,并将轴承零件浸入室温的流动水中,抖动轴承零件1min;
七、然后将轴承零件浸入室温的硝酸液中,抖动轴承零件45s;
八、然后将轴承零件转移至盛有室温的流动水的容器中,并将轴承零件浸入室温的流动水中,抖动轴承零件1min;
九、然后将轴承零件浸入室温的盐酸液中,抖动轴承零件45s;
十、然后将轴承零件转移至盛有室温的流动水的容器中,并将轴承零件浸入室温的流动水中,抖动轴承零件3min;
十一、然后将轴承零件浸入室温的中和液中,抖动轴承零件5min;
十二、然后将轴承零件转移至盛有室温的流动水的容器中,并将轴承零件浸入室温的流动水中,抖动轴承零件1min;
十三、然后将轴承零件浸入室温的防锈液中,抖动轴承零件1min,即完成;
进一步的,所述脱脂液由无水碳酸钠、磷酸三钠、氢氧化钠和去离子水组成;脱脂液中,无水碳酸钠的质量分数为3.5%,磷酸三钠的质量分数为3.5%,氢氧化钠的质量分数为2%;
进一步的,所述无水碳酸钠的纯度规格为化学纯试剂;所述磷酸三钠的纯度规格为化学纯试剂;所述氢氧化钠的纯度规格为化学纯试剂;
进一步的,步骤五所述盐酸液由质量分数为38%的盐酸和去离子水组成,盐酸和去离子水的体积比为4.37:100;所述盐酸的纯度规格为优级纯试剂;
进一步的,所述硝酸液由质量分数为68%的硝酸和去离子水组成,硝酸和去离子水的体积比为4.74:100;所述硝酸的纯度规格为优级纯试剂;
进一步的,步骤九所述盐酸液由质量分数为38%的盐酸和去离子水组成,盐酸和去离子水的体积比为4.45:100;所述盐酸的纯度规格为优级纯试剂;
进一步的,所述中和液由无水碳酸钠和去离子水组成,中和液中无水碳酸钠的质量分数为5%;所述无水碳酸钠的纯度规格为化学纯试剂;
进一步的,所述防锈液由亚硝酸钠、无水碳酸钠和去离子水组成,防锈液中亚硝酸钠的质量分数为9%,防锈液中无水碳酸钠的质量分数为2%;所述亚硝酸钠的纯度规格为化学纯试剂;所述无水碳酸钠的纯度规格为化学纯试剂;
进一步的,所述去离子水的电导率为8μs/cm;
进一步的,所述零件的材质为g13cr4mo4ni4v;
进一步的,所述抖动轴承零件时抖动频率是125次/分钟,抖动幅度为4cm。
图3为实施例3中酸洗腐蚀后的g13cr4mo4ni4v钢轴承零件照片,其中c为检出的磨削烧伤;从图3可以看出,本实施例可以有效检出烧伤,且烧伤较明显,易辨别。