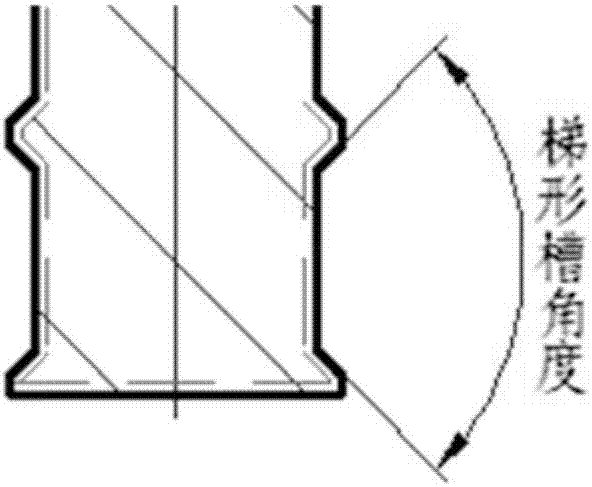
本发明涉及在保证低成本的同时切削能力强、加工精度高、适用玻璃范围广、并且所得玻璃的边部质量高的玻璃面板的加工方法。进一步,涉及包含利用该方法加工得到的玻璃面板的光伏/光热器件。
背景技术:
:随着世界范围内能源供应紧张状况日益加剧,能源将成为制约各国经济的主要因素。太阳能作为清洁的可再生能源,越来越受到人们的重视,应用领域也越来越广泛。作为同样都是利用太阳能进行发电的可再生能源技术,太阳能光热(集热)发电是将光能转变为热能、然后再通过传统的热力循环做功发电的技术。而光伏发电是由光子使电子跃迁,形成电位差,从而将光能直接转变为电能的技术。光热发电与光伏发电都是人类对太阳能的有效利用方式,是解决当前乃至未来人类能源、资源、环境等问题的有效途径和方法。伴随光伏/光热产业的发展,玻璃面板的应用领域越来越广泛,对于光伏/光热玻璃面板的需求也越来越大,前期种类以钠钙玻璃居多,而随着玻璃技术的发展,高铝玻璃的性能远远优于钠钙玻璃,以高铝玻璃为主导的光伏/光热组件由于在经过各工序加工后性能优异,因而已成为主流趋势。市场上的光伏/光热玻璃面板的厚度一般为1mm以上,迄今为止,对厚度为1mm以上的玻璃面板的外形加工大多是通过仿形磨边机而实现的。需要说明的是,传统的仿形磨边机通常依靠固定式、旋转的砂轮,通过移动玻璃面板边部与砂轮接触而实现对玻璃面板边部的加工。但是,这样的传统仿形磨边机由于工作机理是移动玻璃而固定用于磨削的砂轮,因此加工稳定性较差,进而,这样得到的玻璃板的边部质量缺陷较多,很容易发生崩边、烧边、欠磨等,尤其是边部崩边尺寸经常可达100~200um、甚至有时大于200um,严重影响了后续工序良率。并且,这样得到的玻璃板的外形尺寸精度不高,尺寸误差通常在±1mm左右,而这样的尺寸误差很可能影响到后续模组装配。另外,很多特异的异形形状是利用传统的仿形磨边机所无法实现的。技术实现要素:发明要解决的问题鉴于上述情况,本发明的目的在于解决如上所述的传统仿形磨边机中存在的问题,提供在保证低成本的同时切削能力强、加工精度高、适用玻璃范围广、并且所得玻璃的边部质量高的玻璃面板的加工方法。进一步,本发明的目的还在于提供包含利用该方法加工得到的玻璃面板的光伏/光热器件。解决问题的方法本发明人等为了达成上述目的而进行了深入研究,结果发现,通过利用特定的磨削组合刀具代替传统的仿形磨边机、并采取包含特定的分段磨削加工工序的加工方法对玻璃面板进行边部加工,可以在保证高切削强度的同时实现尺寸误差在±0.03mm以内的高加工精度,并且可以大幅减少崩边、烧边、欠磨等边部质量缺陷,获得理想的边部质量,同时,能够广泛地对应各种尺寸及形状的玻璃,另外,由于所使用的磨削组合刀具更换方便、使用寿命长,因而可大幅降低成本。具体而言,本发明提供一种玻璃面板的加工方法,其包括开料工序:利用开料机将待加工玻璃面板切割成比成品尺寸大0.6mm以上、优选大0.6~2.0mm,以及,边部加工工序:利用磨削组合刀具对在开料工序中得到的玻璃面板进行边部加工。其中,所述边部加工工序包括粗磨工序及多段精磨倒边工序,所述磨削组合刀具包含磨削机构、驱动机构及控制机构。在本发明的如上所述的玻璃面板的加工方法中,所述磨削机构优选包含安装柄、粗磨磨削区及精磨倒边区,在所述粗磨磨削区和所述精磨倒边区之间任选具有分界槽,所述精磨倒边区优选至少包含第一精磨倒边区及第二精磨倒边区,所述驱动机构优选为精雕机,所述控制机构优选为计算机辅助系统。并且,优选所述磨削机构安装在所述驱动机构的主轴上,并利用所述控制机构对所述驱动机构进行控制。在本发明的如上所述的玻璃面板的加工方法中,所述玻璃面板厚度优选为0.55mm以上、更优选为0.55~5mm。所述磨削组合刀具的磨削机构优选是在基体上形成金刚石颗粒层而成的。其中,所述基体的材质优选为硬质合金、更优选为镍铬合金。所述磨削机构的总长优选为40~60mm,其中的安装柄直径优选为6mm以上,粗磨磨削区的直径优选为6mm以上,精磨倒边区的直径优选为6mm以上。在本发明的如上所述的玻璃面板的加工方法中,在所述粗磨磨削区形成的金刚石颗粒层为金刚石粗颗粒层,所述金刚石粗颗粒的目数优选为200~600目、更优选为300~500目、最优选为400目,在所述精磨倒边区形成的金刚石颗粒层为金刚石细颗粒层,在所述第一精磨倒边区形成的金刚石细颗粒的目数优选为800~1100目、更优选为1000目,在所述第二精磨倒边区形成的金刚石细颗粒的目数优选为1000~1500目、更优选为1200目。在本发明的如上所述的玻璃面板的加工方法中,在所述精磨倒边区优选设置有倒边形状槽,该倒边形状槽优选为梯形槽、v型槽、u型槽、圆弧形槽,其中更优选为梯形槽。其中,为梯形槽时,所述梯形槽的梯形槽角度优选为50°~120°、更优选为60°~100°、进一步优选为90±1°,所述梯形槽的倒角大小优选为玻璃厚度的15%~45%、更优选为20%~40%、进一步优选为25%~35%、最优选为30%。在本发明的如上所述的玻璃面板的加工方法中,在所述边部加工工序中,所述驱动机构的主轴转速优选为40000~60000转/min,所述磨削机构的所述安装柄、粗磨磨削区及精磨倒边区的同轴度优选为0.01~0.05mm、更优选为0.02mm、进一步优选为0.01mm以下,所述主轴径向跳动优选小于0.05mm、更优选为0.03mm。在本发明的如上所述的玻璃面板的加工方法中,在所述边部加工工序中,在所述玻璃面板的厚度为0.55~1.0mm时,所述主轴转速优选为40000~60000转/min、更优选为45000mm/min,磨削量优选为0.10~0.25mm、更优选为0.20mm,粗磨工序的进给倍率优选为400~800mm/min、更优选为600mm/min,精磨工序的进给倍率优选为500~900mm/min、更优选为700mm/min;在所述玻璃面板的厚度为1.0~2.0mm时,所述主轴转速优选为30000~50000转/min、更优选为40000mm/min,磨削量优选为0.10~0.30mm、更优选为0.20mm,粗磨工序的进给倍率优选为300~600mm/min、更优选为400mm/min,精磨工序的进给倍率优选为700~900mm/min;在所述玻璃面板的厚度为2.0~5.0mm时,所述主轴转速优选为30000~40000转/min、更优选为38000mm/min,磨削量优选为0.10~0.30mm、更优选为0.20mm,粗磨工序的进给倍率优选为200~500mm/min、更优选为300mm/min,精磨工序的进给倍率优选为700~900mm/min。进一步,本发明提供一种光伏/光热器件,其包含利用上述任一玻璃面板的加工方法加工得到的玻璃面板。发明的效果根据本发明的玻璃面板的加工方法,通过利用特定的磨削组合刀具代替传统的仿形磨边机、并采取包含特定的分段磨削加工工序的加工方法对玻璃面板进行边部加工,可以在利用在刀具上形成的金刚石颗粒来保证高切削强度的同时实现尺寸误差在±0.03mm以内的高加工精度,并且,通过分多段进行不同程度的磨削,并严格管理磨削机构中各部分间的同轴度,可以大幅减少崩边、烧边、欠磨等边部质量缺陷,获得理想的边部质量,另外,通过将精磨倒边区的倒边形状槽灵活地设置为梯形槽、v型槽、u型槽、圆弧形槽,并灵活地设置倒边形状槽的角度,能够广泛地对应各种尺寸及形状的玻璃。此外,根据本发明,还能够提供包含利用如上所述的玻璃面板的加工方法加工得到的玻璃面板的光伏/光热器件。附图说明[图1]示出了本发明的一个实施方式的磨削组合刀具的磨削机构的构成的示意图。[图2]示意性地示出了梯形槽角度的概念图。[图3]示意性地示出了倒角大小的概念图。[图4]示出了本发明的另一实施方式的磨削组合刀具的磨削机构的构成的示意图。符号说明1第一精磨倒边区2第二精磨倒边区3分界槽4粗磨磨削区5安装柄具体实施方式本发明涉及的玻璃面板的加工方法,其包括利用开料机将待加工玻璃面板切割成比成品尺寸大0.6mm以上、优选大0.6~2.0mm的开料工序、和利用磨削组合刀具对在开料工序中得到的玻璃面板进行边部加工的边部加工工序。其中,所述边部加工工序包括粗磨工序及多段精磨倒边工序,并且,所述磨削组合刀具包含磨削机构、驱动机构及控制机构。在利用开料机进行的开料工序中,所述开料机例如可以使用全自动玻璃切割机,其中,切割刀轮优选选用高渗透钻石刀轮,刀轮切割角度优选设为155°以下,切割速度优选设为30000~50000mm/min,切割压力优选设为4000hp以下(英制马力单位,1hp=746w)。其中,可配合适当浓度的切削液或类似于保护刀头的液体,从而确保切割后的光伏光热玻璃边部效果更佳,更有利于后序的边部加工。关于待加工玻璃,可以选用厚度为0.55mm以上、优选为0.55~5mm的玻璃面板。该玻璃面板的透光率优选为91.5%以上,由此,可谋求加工得到的玻璃面板兼具高透光性、和耐化性及抗冲击性等机械性能。在选用0.55~5mm的玻璃面板时,可以进一步根据玻璃面板的厚度的差异而选择不同的开料条件。例如,在所述玻璃面板的厚度为0.55~1.0mm时,所述刀轮切割角度优选为125°以下,切割速度优选为30000~50000mm/min,切割压力优选为3000hp以下。由此,玻璃切割后的切线细腻、断面平滑,无明显侧裂纹和凹凸感,切割良品率高,便于后续的边部加工。在所述光伏光热玻璃面板厚度为1~2mm时,所述刀轮切割角度优选为125~135°,切割速度优选为30000~40000mm/min,切割压力优选3000~4000hp。由此,玻璃切割后的切线细腻、断面平滑,无明显侧裂纹和凹凸感,切割良品率高,便于后续的边部加工。在所述光伏光热玻璃面板厚度为2~3mm时,所述刀轮切割角度优选为135°~145°,切割速度优选为30000~40000mm/min,切割压力优选为2000~3000hp,其特征在于玻璃切割后切线细腻、断面平滑,无明显侧裂纹和凹凸感,切割良品率高,便于后续的边部加工。在所述光伏光热玻璃面板厚度3mm~5mm时,所述刀轮切割角度优选为145°~155°,切割速度优选为30000mm/min以下,切割压力优选为3000~4000hp。由此,玻璃切割后切线细腻、断面平滑,无明显侧裂纹和凹凸感,切割良品率高,便于后续的边部加工。接着,将在上述开料工序中切割得到的玻璃面板依靠真空吸附机构吸附在专用治具上,利用本发明的磨削组合刀具对该玻璃面板进行边部加工。以图1所示的本发明的一个实施方式的磨削组合刀具的磨削机构为例,所述磨削组合刀具包含磨削机构、驱动机构及控制机构。所述磨削机构包含安装柄5、粗磨磨削区4及精磨倒边区,该精磨倒边区至少包含第一精磨倒边区1及第二精磨倒边区2。具体而言,所述磨削组合刀具的磨削机构是在基体上形成、例如电镀金刚石颗粒层而成的,其总长优选为40~60mm。在安装柄前端设置有包含第一精磨倒边区及第二精磨倒边区的精磨倒边区,安装柄的直径优选为6mm以上,优选优选选用表面光滑的材质,例如,安装柄的材质优选为硬质合金、更优选为镍铬合金。精磨倒边区的直径优选为6mm以上。连接精磨倒边区和安装柄之间的是粗磨磨削区,粗磨磨削区的直径优选为6mm以上。通过这样地设置磨削机构各部分的尺寸,可使加工的尺寸精准、使用方便、加工效率高、稳定性优良。另外,在所述粗磨磨削区形成的金刚石颗粒层为金刚石粗颗粒层,所述金刚石粗颗粒的目数优选为200~600目、更优选为300~500目、最优选为400目。通过这样地设置金刚石粗颗粒层的金刚石颗粒的目数,可以进一步提高加工效率,获得更佳的切削能力。需要说明的是,通常使在所述粗磨磨削区形成的金刚石颗粒层的长度大于待加工玻璃面板的厚度,以便灵活调整粗磨,提高刀具的使用寿命。在所述精磨倒边区形成的金刚石颗粒层为金刚石细颗粒层,在所述第一精磨倒边区和所述第二精磨倒边区上电镀有不同粒度的金刚石细颗粒层。例如,在所述第一精磨倒边区形成的金刚石细颗粒的目数优选为800~1100目、更优选为1000目,在所述第二精磨倒边区形成的金刚石细颗粒的目数优选为1000~1500目、更优选为1200目。通过这样地设置金刚石细颗粒层的金刚石颗粒的目数,可以达到更理想的边部磨削效果,使经过多段精磨倒边工序后的玻璃面板的边部达到更理想的光亮、光滑程度。另外,在所述粗磨磨削区和所述精磨倒边区之间任选具有分界槽3,优选设置有环型分界槽。在所述精磨倒边区(至少包括第一精磨倒边区及第二精磨倒边区)设置有倒边形状槽,该倒边形状槽优选为梯形槽、v型槽、u型槽、圆弧形槽,更优选为梯形槽。通过这样地设置倒边形状槽并根据实际需要而选择该倒边形状槽的形状,可以实现对不同形状及种类的玻璃面板的加工,并且可以进一步提高加工稳定性。需要说明的是,在本发明中优选的梯形槽,不仅包括梯形的上底及下底长度不等的形状,也包括梯形上底和下底长度相等的情形。即,就图2所示的梯形槽角度而言,包括该角度为90°的情况。在选择梯形槽作为倒边形状槽的情况下,其梯形槽角度优选为50°~120°、更优选为60°~100°、进一步优选为90°,需要说明的是,这里的90°包括存在少许误差的情况,例如,可以包含90±1°的情况。通过这样地设置梯形槽角度,可以减少玻璃面板被磨削时与刀具之间的震动,进一步达到更理想的加工效果。另外,所述梯形槽的倒角大小优选为玻璃厚度的15%~45%、更优选为20%~40%、进一步优选为25%~35%、最优选为30%。这里,所述倒角大小即倒边尺寸大小,如图3所示,指的是相对于玻璃厚度而言的斜边的边长尺寸大小,即图3中的倒角大小c。例如:玻璃厚度为0.55mm,倒角大小为厚度的30%,即,0.55×0.30=0.165mm,玻璃经研磨后,端面形状为梯形状,倒角大小为0.165mm为斜边边长尺寸大小。通过这样地设置梯形槽的倒角大小,可以减少玻璃面板磨削时与刀具之间的震动,进一步达到更理想的加工效果。在本发明的磨削组合刀具中,所述驱动机构优选为精雕机,通过将所述磨削机构安装在所述驱动机构、例如精雕机的主轴上,并利用所述控制机构对所述驱动机构进行控制,可以达到更理想的边部磨削效果,使经过边部磨削后的崩边尺寸最小。另外,所述驱动机构、例如精雕机的主轴转速优选为40000~60000转/min,所述主轴径向跳动,也称主轴径向跳动幅度,即磨头在旋转过程中的径向摆动。需要说明的是,摆动会使磨头对玻璃边部的切削力不均,易产生崩边及微裂纹,且形态为连续性。主轴径向跳动优选小于0.05mm、更优选为0.03mm。这是由于,驱动机构的主轴高速旋转时的转速越高,刀具切削力越大,但主轴径向跳动越大,边部质量越差,反之,转速越低则刀具切削力越小,但主轴径向跳动越小,边部质量越好,因此,需要使主轴转速与刀具粒度、刀具加工质量、磨削量等参数相匹配。其中,通过将主轴转速设定为如上所述的范围,可以进一步提高磨削边部的加工质量。通过将主轴径向跳动设定在上述范围,可以进一步提高磨削边部的加工稳定性。另外,所述磨削机构的所述安装柄、粗磨磨削区及精磨倒边区的同轴度优选为0.01~0.05mm、更优选为0.02mm、进一步优选为0.01mm以下。这里,所述同轴度是指插芯内径距离整个圆心的偏移程度,理想状态是0,就是不偏移。但是在实际中无法达到理想状态,会产生一定的偏移。该同轴度的测定方法包括摆差测定仪测量法、手动影像测量仪法、圆度测量仪法、三坐标测量机法、全自动影像测量仪法等,本发明中采用的是摆差测定仪测量法。通过将同轴度设定在上述范围,可以进一步减少加工得到的玻璃面板的边部崩边等缺陷。在边部加工工序中,选用0.55~5.0mm的玻璃面板时,可以进一步根据玻璃面板的厚度的差异而选择不同的边部加工条件。例如,在所述玻璃面板的厚度为0.55~1.0mm时,所述主轴转速优选为40000~60000转/min、更优选为45000mm/min,由此,可以进一步提高磨削边部的加工质量,磨削量优选为0.10~0.25mm、更优选为0.20mm,粗磨工序的进给倍率优选为400~800mm/min、更优选为600mm/min,精磨工序的进给倍率优选为500~900mm/min、更优选为700mm/min,由此,可以保证加工质量并提高加工效率;在所述玻璃面板的厚度为1.0~2.0mm时,所述主轴转速优选为30000~50000转/min、更优选为40000mm/min,由此,可以进一步提高磨削边部的加工质量,磨削量优选为0.10~0.30mm、更优选为0.20mm,粗磨工序的进给倍率优选为300~600mm/min、更优选为400mm/min,精磨工序的进给倍率优选为700~900mm/min,由此,可以保证加工质量并提高加工效率;在所述玻璃面板的厚度为2.0~5.0mm时,所述主轴转速优选为30000~40000转/min、更优选为38000mm/min,由此,可以进一步提高磨削边部的加工质量,磨削量优选为0.10~0.30mm、更优选为0.20mm,粗磨工序的进给倍率优选为200~500mm/min、更优选为300mm/min,精磨工序的进给倍率优选为700~900mm/min,由此,可以保证加工质量并提高加工效率。需要说明的是,上述中的磨削量指的是待加工玻璃面板的表面到实际加工表面的垂直距离。所述进给倍率指的是刀具加工时的行进的速度。例如,相对于十分钟可加工完成的情况而言,如果调大进给倍率,即可缩短加工时间缩短,如果减小进给倍率,即可时加工时间波长。另外,在粗磨工序及多段精磨倒边工序中,刀数为1以上即可,所述刀数也称下刀数,指的是加工的次数。本发明中,通过将粗磨工序及多段精磨倒边工序设置为1以上,可保证加工质量和提高加工效率。另外,本发明的磨削组合刀具中的控制机构用于对驱动机构进行控制。具体而言,例如可以将作为驱动机构的精雕机与作为计算机辅助系统的cad/cam软件结合使用。所述cad/cam指的是计算机辅助设计(computeraideddesign)和计算机辅助制造(computeraidedmaking),其核心是利用计算机进行设计和数值控制,从而实现按照工程人员的指令对驱动设备的设计、驱动及控制。除了本发明提供的光伏光热玻璃面板磨削组合刀具,利用精雕机结合,针对加工1mm以上的光伏光热玻璃面板,从而能加工出不同形状高精度、高质量的光伏光热玻璃面板,使用金刚石得到最大程度的利用,通过调整光伏光热玻璃面板与刀具之间的坐标高度,可以不用更换刀具,一次性完成外形粗磨、外形精磨及倒边等步骤,简化了工序,节约了成本,提高了生产效率。这样一来。根据本发明的实施方式之一的玻璃面板的加工方法,通过将磨削机构、驱动机构及控制机构相结合而构成磨削组合刀具,并利用这样的磨削组合刀具对经开料工序得到的玻璃面板进行边部加工,能够加工出不同形状高精度、高质量的光伏光热玻璃面板,使金刚石得到最大程度的利用。另外,通过调整玻璃面板与刀具之间的坐标高度,可以不用更换刀具,一次性完成外形粗磨、外形精磨及倒边等步骤,可简化工序、节约成本、提高生产效率。如上所述,示出了如图1所示的本发明的一个实施方式的磨削组合刀具的磨削机构的构成。在图1所示的构成中,与安装柄5的直径相比,粗磨磨削区4、精磨倒边区(第一精磨倒边区1及第二精磨倒边区2)的直径较大。由于在这样的情况下,在主轴转速一定的情况下,磨削直径越大则圆周速度越大,因此该实施方式的磨削组合刀具适合于厚度为2mm以上的较厚玻璃面板的加工,方便刀具更换,加工效率相对较高。与此相对,在本发明的另一实施方式的磨削组合刀具的磨削机构中,也可以如图4所示那样,使安装柄5的直径与粗磨磨削区4、精磨倒边区(第一精磨倒边区1及第二精磨倒边区2)的直径相同。在该情况下,在主轴转速一定的情况下,在磨削直径较大时圆周速度较小,因此该实施方式的磨削组合刀具更适合于厚度小于2mm的较薄玻璃面板的加工。实施例以下,结合实施例对本发明的技术方案作进一步的说明,但本发明并不限定于此。需要说明的是,凡是对本发明技术方案进行修改或者等同替换、而不脱离本发明技术方案的精神和范围的技术方案,均应涵盖在本发明的保护范围中。在本发明的实施例中,利用包括下述工序的玻璃面板的加工方法制造了玻璃面板。(1)开料工序利用开料机(全自动玻璃切割机;型号:yxt-cnc05;制造商:东莞维迪光电器材有限公司)将下述表1所示的各厚度的待加工玻璃面板(以下,如无特殊说明,本发明的实施例中使用的待加工玻璃面板均为四川旭虹光电科技有限公司制造的玻璃面板)、基于表1中示出的各参数切割成了比目标的成品尺寸大0.6~2.0mm的玻璃面板。[表1](2)粗磨工序将例如图1或图4所示的作为磨削机构的组合式金刚石刀具安装在精雕机(型号:da-650t;制造商:东莞迪奥数控)的机床主轴上,将开好料的玻璃面板依靠真空系统吸附在专用治具上。其中,上述组合式金刚石刀具包含第一精磨倒边区1、第二精磨倒边区2、粗磨磨削区4及安装柄5。具体而言,在安装柄5前端设置的包含第一精磨倒边区1及第二精磨倒边区2的精磨倒边区电镀有1000目/1200目(砂号)的金刚石细颗粒层,并使作为梯形槽的倒边形状槽的倒边角度为90°。在精磨倒边区电镀有400目(砂号)的金刚石粗颗粒层。另外,在第二精磨倒边区2与粗磨磨削区4之间设置有环形分界槽3。其中,使电镀在粗磨磨削区4的400目的金刚石粗颗粒层长度大于加工玻璃面板的厚度,以便灵活调整粗磨,提高刀具的使用寿命。精雕机通过软件mastercam9.1(美国cncsoftwareinc.公司开发的基于pc平台的cad/cam软件)调整刀具与玻璃面板之间的位置高度,利用粗磨磨削区4沿玻璃面板周边走刀至少一周以上,从而进行粗磨工序。所述玻璃面板的厚度为0.55~5.0mm,粗磨磨削边部的磨削量与程序设置参见下述表2。[表2]需要说明的是,上述表2中示出的磨头直径,指的是粗磨磨削区的直径。(3)多段精磨倒边工序重新调整刀具和玻璃面板之间的位置,利用第一精磨倒边区的梯形槽上形成的1000目金刚石细颗粒层、第二精磨倒边区的梯形槽上形成的1200目金刚石细颗粒层沿玻璃面板周边走刀至少一周以上,完成精磨倒边工序。详细条件与程序设置参见下述表3的记载。需要说明的是,下述表3所针对的厚度在0.55~5.0mm内的纵400mm×横500mm的不同玻璃面板而进行的。[表3]根据上述表3中的崩边大小的结果可知,利用电镀在第一精磨倒边区3的1000目的金刚石细颗粒层、电镀在第二精磨倒边区4的1200目的金刚石细颗粒层,达到了更理想的边部磨削效果,并且,玻璃边部端面粗糙度ra均较低(均在0.18μm以内)。其中,为了证明梯形槽角度对边部加工质量的影响,对于同样的玻璃纵400mm×横500mm×厚2.0mm,在除了梯形槽角度不同以外,其它条件和程序与上述表3中厚度为1.0~2.0mm时采用的条件完全相同的情况下进行了玻璃面板的加工,并对加工得到的玻璃面板的崩边大小进行了评价。详情如下述表4所示。[表4]梯形槽角度(°)崩边大小(μm)5029.66025.39020.111028.812029.613027.6需要说明的是,上述梯形槽角度是利用奥林巴斯(olympus)株式会社制造的型号为bx51-p的偏光显微镜进行观察并测定的。上述崩边大小利用奥林巴斯(olympus)株式会社制造的型号为bx51-p的偏光显微镜进行了观察,需要说明的是,所示崩边大小采用的是针对6块以上玻璃面板进行测定而得到的平均值。根据上述表4的结果可以明确的是,在其它条件相同且均符合本发明的构成的情况下,在梯形槽角度为90°的情况下崩边大小明显更小、即取得了更为优异的边部加工质量。另外,为了证明在使用本发明的特定的磨削组合刀具时相对于传统的仿形磨边机(型号:fx-120、制造商:江西中航)所加工得到的玻璃的优异性能,对于相同规格的玻璃样品,分别采用仿形磨边机和精雕机进行加工,并针对加工得到的玻璃的尺寸精度、磨削量、崩边大小、端面粗糙度进行了评价和比较。详细结果参见下述表5。[表5]需要说明的是,上述尺度精度是采用日本三丰株式会社制造的精度为±0.05mm的0~600mm数显卡尺进行测定的。上述边部缺陷的评价是通过利用10倍率的放大镜对加工得到的玻璃面板的边部进行目测观察而进行的评价。上述崩边大小利用奥林巴斯(olympus)株式会社制造的型号为bx51-p的偏光显微镜进行了观察,需要说明的是,所示崩边大小采用的是针对6块以上玻璃面板进行测定而得到的平均值。上述端面粗糙度使用株式会社东京精密制造的型号为480a的粗糙度仪进行了测量。根据上述表5的结果可知,通过利用本发明特定的磨削组合刀具、并采取本发明特定的包含分段磨削加工工序的加工方法对玻璃面板进行边部加工,与传统的仿形磨边机,在尺寸精度、磨削量、崩边大小、端面粗糙度方面均获得了令人满意的技术效果。以上,结合实施例对本发明的技术方案及技术效果进行了详细说明,但上述实施例仅为本发明的优选实施例,并非对本发明保护范围的限制,但凡是采用本发明的设计原理,以及在此基础上对本发明技术方案进行修改或者等同替换、而不脱离本发明技术方案的精神和范围的技术方案,均涵盖在本发明的保护范围之内。当前第1页12