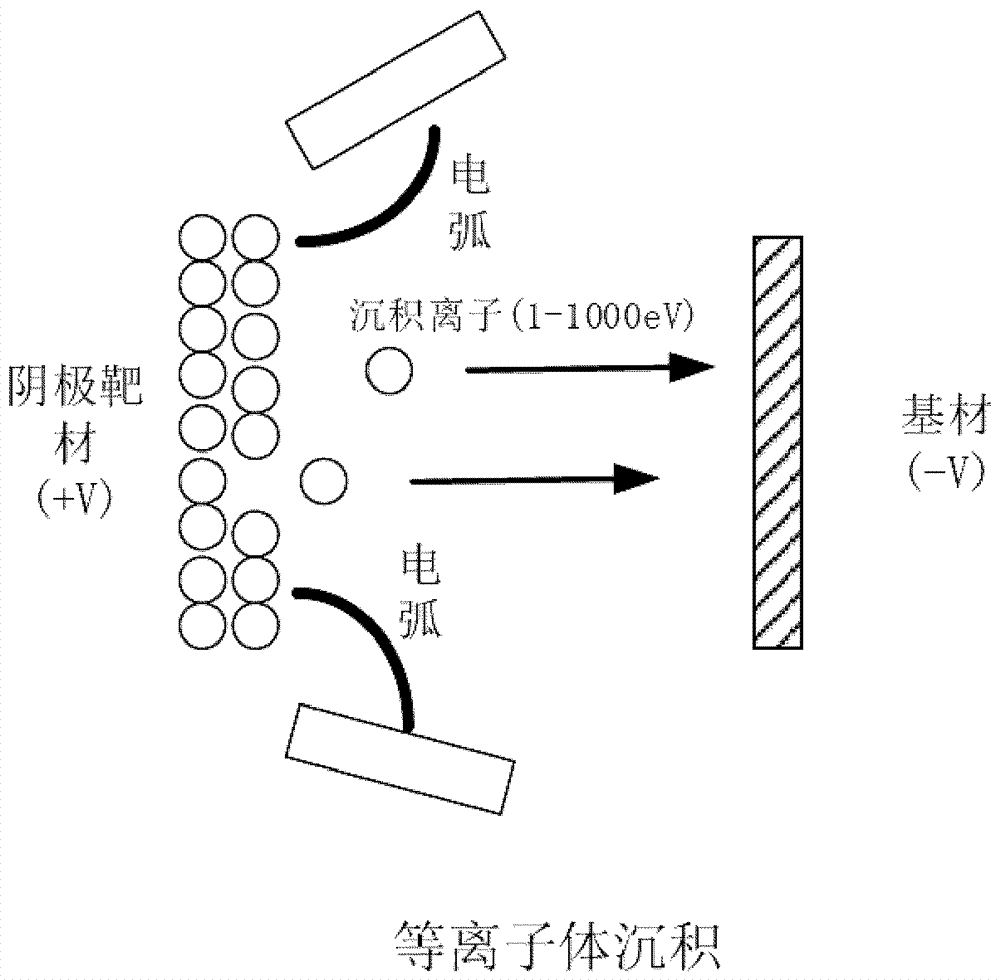
本发明涉及电路板的基板制造领域,并且具体地涉及覆铜板及其制造方法。
背景技术:
:作为基板的一例,覆铜板在电路板(pcb)等各种产品的工业生产中有着广泛的应用。按照所用基材的不同,覆铜板通常可分为不易弯折的刚性覆铜板(ccl)和可弯折的挠性覆铜板(fccl)。在现有技术中,制造刚性覆铜板的方法主要有压合法:在绝缘基材的单面或双面覆上铜箔,然后用压机将铜箔与绝缘基材压合在一起。此外,还可使用溅射法来制造刚性覆铜板:在真空环境下,用电离的氩离子高速轰击金属靶材的表面,使靶材上的金属原子被溅射出来并吸附沉积到基材的表面上而形成导电籽晶层,然后用电镀等方法在导电籽晶层上镀覆加厚导体层。另外,在制造挠性覆铜板时,除了压合法和溅射法外还可使用涂布法:在铜箔表面涂布多层树脂后,经高温处理再与铜箔压合,从而制得成品。在上述三种方法中,涂布法和压合法制得的覆铜板在铜箔与基材之间具有良好的结合力,但是制造工艺复杂,对设备要求高,而且均需要使用成品铜箔。这里,铜箔通常由压延法或电解法制成。受限于现有工艺水平,铜箔很难制成12μm以下的厚度,故难以蚀刻出精细度高、具有较细线宽线距的图案,因而在以hdi(高密度互连基板)和cof(柔性芯片)技术为基础的中高档精密电子产品中的应用受到限制。而且,由于在生产超薄铜箔覆铜板的过程中,需要对铜箔进行蚀刻减薄或者需要去除载体铜箔,因而存在铜利用率低、生产成本高等问题。与之相比,使用溅射法可以容易地以低成本制造出各种铜箔超薄的刚性覆铜板或两层型挠性覆铜板(2l-fccl)。其中,铜箔厚度例如能够薄至9微米,甚至达到7微米、乃至5微米等。但是,在溅射过程中,由于金属原子的能量约为1-10个电子伏特(ev),因而金属原子与基材表面的结合并不牢固或紧密,从而导致所制得的铜箔的剥离强度低,远低于涂布法和压合法。而且,采用溅射法所制得的铜箔存在针孔等问题,继而影响了它的推广应用。此外,通过溅射法制得的覆铜板在蚀刻后的耐离子迁移性能差,当在后段工序中制造成pcb或柔性电路板(fpc)后容易发生漏电现象。在下表中,列出了现有覆铜板生产技术的对比。表1现有覆铜板生产技术对比压合法涂布法溅射法领域fcclcclfcclfcclccl结合力高(可高于1.0n/mm)高(可高于1.0n/mm)低(低于0.5n/mm)铜箔厚度厚(大于12微米,12微米以下报废率高)厚(大于12微米,12微米以下报废率高)可做薄(3-12微米)针孔问题不易出现不易出现易出现来源:(effectofthermaltreatmentonadhesionstrengthofcu/ni–cr/polyimideflexiblecoppercladlaminatefabricatedbyroll-to-rollprocess,microelectronicengineering88(2011)718–723.,bo-innoh,jeong-wonyoon,jung-hyunchoi,seung-boojung)。因此,需要一种改进的覆铜板制造方法,其所制得的铜箔厚度超薄并且结合力很高。技术实现要素:针对现有技术的以上问题,本发明的目的之一在于提出一种新的覆铜板制造方法,并且通过该方法制备得到具有很高结合力并且铜箔厚度超薄的覆铜板。具体地,本发明公开了一种采用离子注入法制造覆铜板的方法。该方法包括提供由绝缘材料构成的基材并对其进行前处理;通过离子注入在基材上注入第一金属离子,以在基材的表面以内一定深度范围(例如,1-100纳米)形成离子注入层;对经过离子注入的基材进行等离子体沉积,以在离子注入层上沉积第二金属离子来形成第一等离子体沉积层;进行等离子体沉积以在第一等离子体沉积层上沉积第三金属离子来形成第二等离子体沉积层以制得覆铜板。其中,该方法还包括:通过控制沉积第三金属离子和第二金属离子的能量,在第一等离子体沉积层和第二等离子体沉积层的界面处形成厚度为5-50nm的合金层。在一个实施例中,通过控制沉积第三金属离子的能量达到200-800ev、优选为200-500ev来形成合金层。在一个实施例中,当基材为pi膜基材时,为使得pi膜基材获得最佳的耐离子迁移性能,该方法还包括控制注入剂量为1.0×1014-5.0×1016ions/cm2和注入深度为20-200纳米。在另一实施例中,当基材为fr-4基材时,为使得fr-4基材获得最佳的耐离子迁移性能,该方法还包括控制注入剂量为5.0×1014-8.0×1016ions/cm2和注入深度为10-80纳米。本发明还公开了一种采用离子注入法制得的覆铜板。覆铜板包括:由绝缘材料构成的基材;在基材的表面下方由第一金属离子形成的离子注入层;在离子注入层上由第二金属离子形成的第一等离子体沉积层;在第一等离子体沉积层上由第三金属离子形成的第二等离子体沉积层。其中,覆铜板还包括:在第一等离子体沉积层和第二等离子体沉积层的界面处形成厚度为5-50nm的合金层。在根据本发明的一个实施例中,还公开了一种采用pi膜基材通过束线式离子注入制作挠性覆铜板的方法。该包括:提供pi膜基材并对其进行前处理;采用镍靶材利用金属蒸汽真空电弧离子源对pi膜基材进行束线式离子注入以得到镍离子注入层;采用镍靶材利用真空阴极弧磁过滤离子源对pi膜基材进行等离子体沉积以在镍离子注入层上沉积镍等离子体沉积层;采用铜靶材进行真空阴极弧磁过滤等离子体沉积来在镍等离子体沉积层上沉积铜等离子体沉积层以制得挠性覆铜板。其中,该方法还包括:通过控制沉积镍金属离子和铜金属离子的能量,在铜等离子体沉积层和镍等离子体沉积层的界面处形成厚度为5-50nm的铜-镍合金层。在一个实施例中,控制沉积铜金属离子的能量达到200-800ev、优选为200-500ev来形成铜-镍合金层。优选地,为使得注入与沉积过程的温度保持在注入温度为50-90摄氏度、沉积温度为60-100摄氏度的最佳温度,该方法还包括控制注入剂量为1.0×1014-5.0×1016ions/cm2。在另一实施例中,为使得pi膜基材的表面温度保持在50-90摄氏度的最佳注入温度,该方法还包括控制注入能量为5-60kev,注入剂量为8.0×1014-5.0×1015ions/cm2。本发明还公开了一种采用pi膜基材通过束线式离子注入制得的挠性覆铜板。挠性覆铜板包括:pi膜基材;在pi膜基材的表面下方由镍金属离子形成的镍离子注入层;在镍离子注入层上由镍金属离子形成的镍等离子体沉积层;在镍等离子体沉积层上由铜金属离子形成的铜等离子体沉积层。其中,挠性覆铜板还包括:在铜等离子体沉积层和镍等离子体沉积层的界面处形成厚度为5-50nm的铜-镍合金层。在根据本发明的一个实施例中,还公开了一种采用fr-4基材通过等离子体浸泡式离子注入制作刚性覆铜板的方法。该方法包括:提供fr-4基材并对其进行前处理;采用镍靶材作为金属等离子体源对fr-4基材进行等离子体浸泡式离子注入以得到镍离子注入层,其中,调节对fr-4基材施加偏压的脉冲宽度,使其大于或等于金属等离子体源的主弧脉冲宽度;继续使用镍靶材、但不对fr-4基材施加偏压来在镍离子注入层上沉积镍等离子体沉积层;更换铜靶材并且同样不对fr-4基材施加偏压来进行等离子体沉积来在镍等离子体沉积层上沉积铜等离子体沉积层以制得刚性覆铜板。其中,该方法还包括:通过控制注入和沉积的能量,在铜等离子体沉积层和镍等离子体沉积层的界面处形成厚度为5-50nm、优选为10-20nm的铜-镍合金层。优选地,控制沉积铜金属离子的能量达到200-800ev来形成铜-镍合金层。优选地,为使得fr-4基材的表面保持在100-150摄氏度的最佳注入温度,该方法还包括注入剂量为1.0×1014-5.0×1016ions/cm2和沉积厚度为30-100纳米。在另一实施例中,该方法还包括调节对fr-4基材施加偏压的脉冲宽度小于金属等离子体源的主弧脉冲宽度来进行等离子体沉积以在镍等离子体沉积层上同时地注入与沉积铜等离子体沉积层。在另一实施例中,该方法还包括:将在注入和沉积过程中的镍靶材更换为ni-cr合金靶材以提高刚性覆铜板的抗侧蚀能力,其中,cr的质量分数为5%-20%。本发明还公开了一种采用fr-4基材通过等离子体浸泡式离子注入制得的刚性覆铜板。刚性覆铜板包括:fr-4基材;在fr-4基材的表面下方由镍金属离子形成的镍离子注入层;在镍离子注入层上由镍金属离子形成的镍等离子体沉积层;在镍等离子体沉积层上由铜金属离子形成的铜等离子体沉积层。其中,刚性覆铜板还包括:在铜等离子体沉积层和镍等离子体沉积层的界面处形成厚度为5-50nm的铜-镍合金层。对于上述方法的实施例的变型和改进在本发明的范围和精神内,且可在本文中进一步描述。附图说明下面通过参考附图并结合实例具体地描述本发明,本发明的优点和实现方式将会更加明显,其中附图所示内容仅用于对本发明的解释说明,而不构成对本发明的任何意义上的限制,附图仅是示意性的,并非严格地按比例绘制。在附图中:图1为根据本发明的离子注入和等离子体沉积的设备原理示意图;图2a为根据本发明的离子注入的工作原理示意图;图2b为根据本发明的等离子体沉积的工作原理示意图;图3为根据本发明的一个示例性实施例的利用离子注入法制造覆铜板的方法的流程图;图4为根据图3的方法所制得的覆铜板;图5为采用聚酰亚胺(pi)膜基材通过束线式离子注入制作挠性覆铜板(fccl)的方法的流程图;图6描绘了根据本发明采用束线式离子注入所制得的覆铜板的成分结构图;以及图7为采用fr-4基材通过等离子体浸泡式离子注入(pⅲ)制作刚性覆铜板(ccl)的方法的流程图。具体实施方式现将详细地参照本发明的实施例,其中的一个或多个实例在附图中示出。各实例均是以阐述本发明的方式提供的,而并不限制本发明。实际上,本领域的技术人员很清楚,在不脱离本发明的范围或精神的情况下,可在本发明中作出各种修改和变型。例如,示为或描述为一个实施例的一部分的特征可结合另一实施例来使用,以产生又一个实施例。因此,期望的是,本发明包含归入所附权利要求及其等同方案范围内的这些修改和变型。图1为根据本发明的离子注入和等离子体沉积的设备原理示意图。如图所示,用于执行离子注入的设备主要由等离子体形成区(触发系统)和离子束形成区(引出系统)这两部分组成。等离子体形成区包括阴极、阳极和触发电极,而离子束形成区一般由一组多孔三电极构成。在触发电压的作用下,阴极和阳极之间形成高密度的等离子体并向引出系统扩散。在引出电场的加速作用下,等离子体中的带电离子被引出并加速形成离子束,该离子束的种类和纯度由阴极靶材料决定。典型地,阴极、触发电极和阳极为同轴结构。阴极为圆柱形并由所需离子的导电材料制成。阳极为圆柱筒形且套在阴极外面,中心开孔为等离子体通道。采用脉冲高压触发方式,例如将触发电极套在阴极外,之间用氮化硼绝缘,触发电压为10kv左右,触发脉宽为10ms左右。当触发电压施加在阴极和触发电极上时,由火花放电产生的等离子体使阴极和阳极电路接通而形成真空弧放电,在阴极表面形成只有微米级大小但电流密度高达106a/cm2的阴极斑,致使阴极靶材料蒸发并高度电离成等离子体。等离子体以大约104m/s的速度喷射,一部分通过阳极中心孔扩散到引出电极。然后,等离子体在引出电场的作用下被引出,形成高速的离子束。施加在阴极、阳极之间的弧电压越高,弧电流就越大,所产生的等离子体密度也就越高,从而有可能引出更大的束流。引出束流大小还与离子源的工作参数、引出电压、引出结构和阴极材料等有关。例如,离子束形成区(引出系统)的引出电压越高,则带电粒子的离子束就被加速到越高的速度,从而可以注入到基材的内部越深的部位。另外,真空弧放电在产生等离子体的同时也会产生很多尺寸在0.1-10μm的不带电微粒。这些微粒的存在对所沉积薄膜的性能有极大的影响,造成薄膜表面粗糙,致密性差,光泽度和与基材的结合力下降等。为了去掉或减少阴极真空弧产生的大颗粒,可以采用磁过滤器,即,建立一个弯曲的磁场,过滤掉不带电的大颗粒,仅将需要的带电等离子体沿着弯曲的磁场导向到基材的表面,由此得到的等离子体装置可称为真空阴极弧磁过滤离子源(fcva)。一般而言,可以使用各种金属、合金、导电氧化物、导电碳化物、导电有机物等作为离子注入用的靶材,但是并不限于此。优选地,使用与基材分子结合力强的金属或合金来进行离子注入,包括ti、cr、ni、cu、ag、au、v、zr、mo、nb中的一种或多种以及它们之间的合金中的一种或多种,例如有nicr、ticr、vcr、cucr、mov、nicrv、tinicrnb等。而且,离子注入层可以包括一层或多层。等离子体沉积可在离子注入设备中采用与上文所述的离子注入类似的方式来进行,只是施加较低的电压而使金属离子具有较低的能量。为简洁起见,文中不再单独详细描述等离子体沉积设备。图2a是根据本发明的离子注入的工作原理示意图。如图2a所示,在离子注入过程中,高压电场在金属阴极靶材的表面进行弧光放电,从而形成电弧斑。在电弧斑处的靶材表面的金属粒子通过离子化,并且脱离靶材表面。于是,离子化的金属粒子受到电压为1-1000kv的加速电场的作用,获得范围在1-1000kev的能量,成为高速粒子。这些被电场加速的高速粒子继而注入到基材内部的一定深度处,形成离子注入层。图2b是根据本发明的等离子体沉积的工作原理示意图。如图2b所示,在等离子体沉积过程中,高压电场类似地在金属靶材的表面进行弧光放电,从而形成电弧斑。在电弧斑处的靶材表面的金属粒子通过离子化,并且脱离靶材表面。于是,离子化的金属粒子受到电压为1-1000v的加速电场的作用,获得范围在1-1000ev的能量。这些被电场加速的粒子继而沉积在离子注入层上或直接沉积在基材上,形成等离子体沉积层。图3是根据本发明的一个示例性实施例的利用离子注入法制造覆铜板的方法的流程图。首先,在步骤s11中,提供由绝缘材料构成的基材。作为示例,绝缘基材可以使用刚性基材(亦称为硬板),例如有机高分子刚性板、陶瓷板(如二氧化硅板)、玻璃板等中的一种或多种。有机高分子刚性板又可包括lcp、ptfe、ctfe、fep、ppe、合成橡胶板、玻纤布/陶瓷填料增强板中的一种或多种。其中,玻纤布/陶瓷填料增强板是以有机高分子材料如环氧树脂、改性环氧树脂、ptfe、ppo、ce、bt等作为基础材料、以玻纤布/陶瓷填料作为增强相的板材。另外,绝缘基材还可以使用挠性板(亦称为软板),例如有机高分子薄膜,其包括pi、pto、pc、psu、pes、pps、ps、pe、pp、pei、ptfe、peek、pa、pet、pen、lcp或ppa中的一种或多种。优选地,基材通常需要进行前处理。作为前处理的方法,可以包括表面清洁处理,例如,用浸渍过酒精的纱布擦拭基材的表面以除去上面附着的脏污,或者将基材放入清洁液中并采用超声波进行清洗,等等。此外,前处理还可包括表面沉积处理和/或表面脱水处理。表面沉积处理就是在基材的表面覆上一层沉积物,以填平基材表面上的孔或者改善基材表面的物理性质以便于后续沉积、电镀等工艺的进行。表面脱水处理就是去除基材表面分子中的水分,以便有利于后续沉积、电镀等工艺的进行。随后,在步骤s12中,通过离子注入在基材上注入第一金属离子,以在基材的表面以内一定深度范围形成离子注入层。任选地,可在基材的上表面、下表面或者二者的下方进行离子注入以形成各自的离子注入层。在一个实施例中,离子注入可通过以下方法来实现。选择导电材料作为靶材,利用金属蒸汽真空电弧离子源(mevva)在真空环境下通过电弧作用使靶材电离而产生金属离子。然后,使该离子在高电压的电场下加速而获得很高的能量(例如5-1000kev,如10kev、50kev、100kev、200kev、500kev等)。接着,高能的金属离子以很高的速度直接撞击基材上的绝缘表面,并且注入到绝缘表面下方一定的深度范围内(例如1-100nm,如5nm、10nm、20nm、50nm等)。在所注入的金属离子与绝缘基材的材料分子之间形成了化学键或填隙结构,从而组成掺杂结构。由此得到的离子注入层的外表面(或称为上表面)与基材绝缘表层的外表面相齐平,而其内表面(或称为下表面)则深入到基材绝缘表层的内部。例如,离子注入层位于基材表面下方1-100nm(例如5-50nm)的深度处。此时,基材的绝缘表层的外侧部分由于形成有离子注入层而构成为扩散阻挡层的一部分。在离子注入期间,靶材的离子以很高的速度强行地注入到基材的内部,与基材之间形成掺杂结构,相当于在基材的表面下方形成了数量众多的基桩。由于基桩的存在,且后续制得的导体层(等离子体沉积层或加厚导体层)与基桩相连,因此,最终制得的基板的导体层与基材之间的结合力较高,远高于现有技术中的磁控溅射制得的金属层与导体之间的结合力。而且,用于离子注入的金属离子的尺寸通常为纳米级别,在离子注入期间分布较均匀,并且相对于基材表面的入射角度差别不大。因此,能够确保离子注入层的表面具有良好的均匀度和致密性,不容易出现针孔现象。可以使用各种金属、合金、导电氧化物、导电碳化物、导电有机物等导电材料作为离子注入用的靶材,但是并不限于此。优选地,使用与基材分子结合力强的金属或合金来进行离子注入,包括ti、cr、ni、cu、ag、au、v、zr、mo、nb以及它们之间的合金中的一种或多种,该合金例如为nicr、ticr、vcr、cucr、mov、nicrv、tinicrnb等。而且,离子注入层可以包括一层或多层。在离子注入之前,可以对开设有孔的基材进行去污、表面清洁、封孔剂处理、真空环境下的霍尔源处理、表面沉积处理等前处理。另外,在离子注入过程中,通过控制各种相关参数,例如注入电流、注入电压、注入剂量等,可以调整离子注入层进入到绝缘表层内部的深度,也即,离子注入层的内表面在基材表面下方所处的深度。在一个优选的实施方案中,注入离子的能量为5-1000kev,注入剂量为1.0×1012-1.0×1018ions/cm2(优选地,注入剂量为1.0×1015-5.0×1016ions/cm2),从而使离子注入层的内表面位于基材表面下方5-50nm的深度处。回到图3,在步骤s12之后执行步骤s13,也即对经过离子注入的基材进行等离子体沉积,以在离子注入层上沉积第二金属离子来形成第一等离子体沉积层。这里,第二金属和第一金属可以是同一材料或者不同材料。在一个具体实施例中,采用镍作为第二金属以在离子注入层上形成镍等离子体沉积层。接着,在步骤s14中,进行等离子体沉积以在第一等离子体沉积层例如镍等离子体沉积层上沉积第三金属离子来形成第二等离子体沉积层以制得覆铜板。这里,第三金属和第二金属分属于不同材料。在一个具体实施例中,采用铜作为第三金属以在第一等离子体沉积层例如镍等离子体沉积层上形成第二等离子体沉积层,也即铜等离子体沉积层。类似于上文所述的离子注入方法,等离子体沉积同样可在离子注入设备中来进行,只是施加较低的引出电压而使导电材料或靶材的离子具有低得多的能量。也即,使用导电材料作为靶材,在真空环境下,通过电弧作用使靶材电离而产生离子,然后在高电压的电场下使离子加速而获得一定的能量,例如1-1000ev。加速后的金属离子飞向基材表面且沉积到事先形成于该基材表面下方的离子注入层上,构成厚度为1-10000nm的等离子体沉积层。作为示例,金属离子可在等离子体沉积期间获得50ev、100ev、200ev、300ev、400ev、500ev、600ev、700ev、800ev、900ev的能量,并且形成厚度为100nm、200nm、500nm、700nm、1μm、2μm、5μm、7μm或10μm的等离子体沉积层。在等离子体沉积中,可以使用与离子注入相同或不同的导电材料作为靶材。例如,可使用各种金属、合金、导电氧化物、导电碳化物、导电有机物等,但是不限于此。举例而言,可在离子注入与沉积时将镍靶材更换为镍-铬合金靶材。这样,可以得到耐化性较佳的覆铜板。此外,可根据所选用的基材、离子注入层的组成成分和厚度等来选择用于等离子体沉积的靶材。优选地,使用与离子注入层结合良好的金属或合金来进行等离子体沉积,例如可使用ti、cr、ni、cu、ag、au、v、zr、mo、nb以及它们之间的合金中的一种或多种,该合金例如为nicr、ticr、vcr、cucr、mov、nicrv、tinicrnb等。而且,等离子体沉积层可以包括一层或多层。例如,在一个优选实施例中,等离子体沉积层包括从内到外依次排列的ni层和cu层。等离子体沉积层的厚度可根据需要来设定,例如可以设定为使得形成有等离子体沉积层的基板的表面方阻小于200ω/□、100ω/□、80ω/□、50ω/□,等等。在等离子体沉积期间,因金属离子以较高的速度飞向基材表面且沉积到预先形成于该基材表面下方的离子注入层上,与离子注入层上的材料之间形成较大的结合力,因而不容易从基材的表面脱落。此外,用于等离子体沉积的金属离子的尺寸通常为纳米级别,在等离子体沉积期间分布较均匀,而且相对于基材表面的入射角度差别不大,因而可确保所得等离子体沉积层的表面具有良好的均匀度和致密性,不容易出现针孔现象。优选地,在一个实施例中,还包括在通过步骤s14所形成的第二等离子体沉积层上镀覆加厚铜层以改善导电性。优选地,采用电镀法来形成加厚铜层。相比于化学镀、真空蒸发镀、溅射等方法,电镀法速度快、成本低、而且可电镀的材料范围非常广泛,可用于cu、ni、sn、ag以及它们的合金等。如图4中所示,覆铜板10包括由绝缘材料构成的基材11。在基材的表面12下方,形成有离子注入层13,例如镍离子注入层。在离子注入层13上,形成有第一等离子体沉积层14,例如镍等离子体沉积层。进一步地,在第一等离子体沉积层14上还形成有第二等离子体沉积层24,例如铜等离子体沉积层。备选地,在第二等离子体沉积层24上还镀覆有加厚铜层以改善导电性。在一个具体实施例中,通过控制沉积能量,主要是沉积第三金属离子的能量,使沉积的第三金属离子的能量达到约200-800ev,优选为200-500ev,可使后沉积的第三金属离子和先沉积的第二金属离子在第一等离子体沉积层14和第二等离子体沉积层24的界面处形成一层厚度为5-50nm、优选为10-20nm的合金层,例如参见图6中的ni/cu层。研究证明,该厚度的合金层可使铜箔和基材之间的结合力大大提高约0.25-0.3n/mm。结果,根据本发明所形成的铜箔与基材之间的结合力良好,能够达到0.9n/mm以上。而且,在沉积过程中形成的、此种合金层厚度可以抗蚀刻药水侧蚀,从而大大提高制得的覆铜板的蚀刻因子。据发明人研究,通过调整后沉积的金属离子的能量,使其能量下降为50ev以下,这样形成的合金层的厚度极薄,可忽略不计。将该条件下制得的覆铜板作为对照组,相比该对照组,在根据本发明的优选实施方式中所形成的覆铜板的抗侧蚀能力提高了2倍以上。作为优选实施例的另一实施方式,在注入和沉积过程中的ni靶材可更换为ni-cr合金靶材。通过加入一定质量分数(例如,5%-20%)的cr之后,最终制得的覆铜板的抗侧蚀能力相比于纯ni靶材进一步提高,可用于下游对抗侧蚀能力要求很高的覆铜板。但是cr的加入也可能引入导致蚀刻不彻底的问题,因此,对于抗侧蚀要求不是特别高的覆铜板,一般采用纯ni靶材。据研究,覆铜板经蚀刻后的耐离子迁移性能和离子注入时的注入剂量、注入温度、注入深度直接相关。通过控制离子注入过程中的注入能量、注入剂量,可以实现控制注入温度和注入深度。作为实例,离子注入包括束线式离子注入和等离子体浸泡式离子注入。图5示出了采用聚酰亚胺(pi)膜基材通过束线式离子注入制作挠性覆铜板(fccl)的方法的流程图。在步骤s21中,提供pi膜基材。优选地,在离子注入之前,可以对基材进行去污、表面清洁、封孔剂处理、真空环境下的霍尔源处理、表面沉积处理等前处理。随后,在步骤s22中,采用ni作为靶材在离子注入与沉积设备中利用金属蒸汽真空电弧离子源(mevva)对pi膜基材进行束线式离子注入(ιbⅱ)以得到镍离子注入层。在此过程中,以氩气为起弧气体,在真空室中抽真空度为2×10-3-5×10-5帕,该真空度可确保电弧放电能有效进行;通过电弧放电作用使阴极靶材电离而产生离子蒸汽,然后在高电压的电场下使该离子加速而获得15-30kev的能量,其中离子注入电压为5-50kv,优选为20-35kv,离子注入剂量为1.0×1014-5.0×1016ions/cm2,优选为8.0×1014-5.0×1015ions/cm2;高能的金属离子接着以很高的速度直接撞击基材表面,并且注入到基材表面下方一定的深度,例如20-200nm,形成离子注入层。由此,在所注入的金属离子与组成基材的材料分子之间形成稳定的化学键(例如离子键或共价键),二者共同构成了掺杂结构,如同半导体中的掺杂结构那样。这样就相当于在基材薄膜中打下了数量众多的“基桩”。之后,在步骤s23中,采用ni作为靶材在同一离子注入与沉积设备中利用真空阴极弧磁过滤离子源(fcva)对pi膜基材进行等离子体沉积(也即,真空阴极弧磁过滤等离子体沉积)以在镍离子注入层上沉积镍等离子体沉积层。接着,在步骤s24中,更换铜(cu)作为靶材在同一离子注入与沉积设备中进行真空阴极弧磁过滤等离子体沉积以在镍等离子体沉积层上沉积铜等离子体沉积层来制得挠性覆铜板。由此,在“基桩”的表面上沉积有一薄层金属镍层,之后在金属镍层上再沉积一层金属铜层。通过控制沉积能量,使沉积的金属铜层和镍层之间形成一层铜-镍合金层。结果,在基材薄膜表面沉积的镍-镍铜合金-铜层与这些嵌入基材薄膜内部的镍“基桩”结合,从而使得沉积的金属薄膜层与基材薄膜表面的结合力(剥离强度)得到极大地提高。根据实验研究,沉积过程中形成的铜-镍合金层对最终制得的铜箔的结合力有重要意义。在一个具体实施例中,通过控制沉积能量,主要是沉积铜(cu)的能量,使cu离子的能量达到200-800ev、优选为200-500ev,可使后沉积的cu和先沉积的镍(ni)在镍等离子体沉积层和铜等离子体沉积层的界面处会形成一层厚度为5-50nm的铜-镍合金层。研究证明,该厚度的铜-镍合金层可使铜箔和基材之间的结合力大大提高约0.25-0.3n/mm。结果,根据本发明所形成的铜箔与基材之间的结合力良好,能够达到0.9n/mm以上。优选地,在一个实施例中,还包括在基材的铜等离子体沉积层上镀覆加厚铜层以改善导电性,由此得到铜箔厚度为1-12微米的挠性覆铜板。对于所制得的挠性覆铜板,检测表明,在等离子体沉积过程中形成的镍等离子体沉积层的厚度约为10-50纳米,铜等离子体沉积层厚度为100-200纳米,铜-镍合金层的厚度为5-50纳米、优选为10-20纳米。进一步地试验证明,此种覆铜板中的覆铜层与薄膜基层之间的结合力较高。在离子注入过程中,若pi膜的注入温度过高,则会产生膜碳化现象,从而导致产生后续电镀后形成的覆铜板结合力低,或蚀刻性能不佳等现象。若pi膜的注入温度过低,则会导致注入深度不够,并且产生膜表面的分子生成化学键(例如离子键或共价键)的数量偏少,与注入粒子结合不紧密。这同样会导致产生后续电镀后形成的覆铜板结合力低,或蚀刻性能不佳等现象。理论上,高的束流密度会导致高的注入与沉积温度。实际上,发明人通过研究pi膜的束线式离子注入剂量、注入束流密度、真空阴极弧磁过滤等离子体沉积剂量与表面的温度之间的关系,发现可通过控制pi膜的注入剂量来实现精确控制pi膜表面的温度。例如,在根据本发明的一个具体实施例中,通过控制注入剂量为1.0×1014-5.0×1016ions/cm2,优选为8.0×1014-5.0×1015ions/cm2,可使注入与沉积过程的温度保持在最佳温度:注入温度为50-90摄氏度,沉积温度为60-100摄氏度。注意的是,当采用束线式离子注入时,进行注入和/或沉积的离子的束流密度(也即,单位时间内的注入剂量)可精确控制,因此注入温度、沉积温度也可精确控制。例如,pi膜的最佳注入温度为50-90摄氏度,以及fr-4的最佳注入温度为100-150摄氏度。通过控制注入剂量为1.0×1014-5.0×1016ions/cm2,优选为8.0×1014-5.0×1015ions/cm2,沉积层厚度为10-50纳米,可使注入与沉积过程的温度保持在最佳温度。在根据本发明的另一具体实施例中,通过控制注入能量为5-60kev,注入剂量8.0×1014-5.0×1015ions/cm2,可使pi膜表面温度保持在最佳注入温度50-90摄氏度。在步骤s23和步骤s24中,通过控制沉积剂量和沉积能量,可使后沉积的铜(cu)和先沉积的镍(ni)在铜等离子体沉积层和镍等离子体沉积层的界面处形成一层厚度为5-50nm、优选为10-20nm的铜-镍合金层。研究证明,此种厚度的铜-镍合金层的存在可使铜箔和基材之间的结合力大大提高。据发明人研究,此种铜-镍合金层的厚度每增加1纳米,则对应的铜箔的剥离强度近似会增加0.03n/mm左右。此外,在束线式离子注入时,基材表面的等离子体温度较低,不会对基材表面产生损伤,因此可获得较高结合力。图6描绘了根据本发明采用束线式离子注入所制得的覆铜板的成分结构图。通过对最终形成的产品进行测试,证明形成了一层厚度约为5-10纳米的铜-镍合金层。如上文所述,覆铜板经蚀刻后的耐离子迁移性能和离子注入时的注入剂量、注入温度、注入深度直接相关。通过控制离子注入过程中的注入能量、注入剂量,可以实现控制注入温度和注入深度。研究表明,在对pi膜基材的注入剂量为1.0×1014-5.0×1016ions/cm2,优选为8.0×1014-5.0×1015ions/cm2,注入温度达到60-90摄氏度,注入深度为20-200纳米时,可以使得基材获得最佳的耐离子迁移性能。在根据本发明的一个具体实施例中,在对pi膜基材的注入剂量为1×1014-5×1016ions/cm2,优选为8×1014-5.0×1015ions/cm2,注入深度为20-200纳米时,可以使得基材获得最佳的耐离子迁移性能。在另一种优选的实施方式中,采用等离子体浸泡式离子注入(pⅲ)。进一步地,还可使用等离子体浸泡式离子注入与沉积技术(pⅲd),其中pⅲd可同时地进行离子注入与等离子体沉积。在pⅲd过程中,当被处理基材上所加脉冲偏压的宽度大于或等于金属等离子体源的主弧脉冲宽度时,处理过程是纯金属离子注入。当不对基材施加偏压而仅存在金属等离子体源,即仅存在金属等离子体时,仅有金属薄膜沉积在基材表面而不存在离子注入过程。当所加偏压脉冲宽度小于金属等离子体源的主弧脉冲宽度时,在基材表面上既进行离子注入又同时进行等离子体沉积。图7示出了采用fr-4基材通过等离子体浸泡式离子注入(pⅲ)制作刚性覆铜板(ccl)的方法的流程图。鉴于同样作为离子注入,下文着重描述等离子体浸泡式离子注入与束线式离子注入的不同,其它相同部分不作过多详细描述。在步骤s31中,提供fr-4基材。优选地,在离子注入之前,可以对基材进行去污、表面清洁、封孔剂处理、真空环境下的霍尔源处理、表面沉积处理等前处理。随后,在步骤s32中,采用ni作为靶材在离子注入与沉积设备中作为金属等离子体源对fr-4基材进行等离子体浸泡式离子注入(pⅲ)以得到镍离子注入层。在本发明的一个具体实施例中,首先调节待处理fr-4基材上所加脉冲偏压的宽度,使其大于或等于金属等离子体源的主弧脉冲宽度,进行ni金属离子注入以得到镍离子注入层。接着,在步骤s33中,继续使用同一ni靶材、但不对fr-4基材施加偏压来在镍离子注入层上沉积ni等离子体沉积层。此时,仅存在金属等离子体源的主弧脉冲,也即在仅存在ni等离子体时,在同一离子注入与沉积设备中对基材进行等离子体沉积ni,以在镍离子注入层上沉积镍等离子体沉积层。备选地,在本发明的另一实施例中,在离子注入时,采用ni作为靶材,对待处理的fr-4基材施加偏压但所加偏压脉冲宽度小于金属等离子体源的主弧脉冲宽度,使得fr-4基材表面既进行离子注入ni,又同时进行等离子体沉积ni。然后,在步骤s34中,更换铜(cu)作为靶材并且同样不对fr-4基材施加偏压来进行等离子体沉积以在镍等离子体沉积层上沉积铜等离子体沉积层来制得刚性覆铜板。备选地,更换铜靶材并且调节对fr-4基材所施加的偏压而使其脉冲宽度小于金属等离子体源的主弧脉冲宽度来进行等离子体沉积。由此,在ni等离子体层的表面上同时地注入与沉积cu等离子体层。具体地在注入和/或沉积过程中,在真空室中抽真空度为2.0×10-1-5.0×10-2帕并且使用氩气来控制真空度,该真空度可确保脉冲阴极电弧放电能有效进行;通过施加高压脉冲电弧(约10kv)在阴极镍表面的放电作用使ni阴极靶材电离产生等离子体,其中离子注入剂量为1.0×1014-8.0×1017ions/cm2,优选为5.0×1016-5.0×1017ions/cm2;在进行注入的实施例中,高能的导电材料离子接着以很高的速度直接撞击基材表面,并且注入到基材表面下方一定的深度,例如20-500nm。在所注入的金属离子与组成基材的材料分子之间形成稳定的化学键(例如离子键或共价键),二者共同构成了掺杂结构,如同半导体中的掺杂结构那样。优选地,在一个实施例中,还包括在基材的铜等离子体沉积层上镀覆加厚铜层以改善导电性。发明人研究发现,对于所制得的刚性覆铜板,在ni等离子体沉积层的厚度为10-50纳米,铜等离子体沉积层厚度为100-200纳米,铜-镍合金层的厚度为5-50纳米、优选为10-50纳米时,获得的覆铜板中的加厚铜层与薄膜基材之间的结合力较高。最终,形成的箔材与基材薄膜之间的结合力很好,达到1.0n/mm以上。如上文所述,覆铜板经蚀刻后的耐离子迁移性能和离子注入时的注入剂量、注入温度、注入深度直接相关,而通过控制离子注入过程中的注入能量、注入剂量可以实现控制注入温度和注入深度。在根据本发明的一个实施例中,对于环氧树脂玻纤布基材例如fr-4基材,通过控制注入温度达到100-200摄氏度,注入深度为10-80纳米时,注入剂量为5.0×1014-8.0×1016ions/cm2,优选为1.0×1015-2.0×1016ions/cm2,使得该基材获得最佳的耐离子迁移性能。在根据本发明的另一具体实施例中,对于环氧树脂玻纤布基材例如fr-4基材而言,当注入剂量为5.0×1014-8.0×1016ions/cm2,优选为1.0×1015-2.0×1016ions/cm2,注入深度为10-80纳米时,可以使得基材获得最佳的耐离子迁移性能。在根据本发明的一个实施例中,通过控制注入和沉积能量,主要是沉积cu的能量,使沉积的cu离子的能量达到约200-800ev,可使后沉积的cu和先沉积的ni在界面处会形成一层厚度为5-50nm、优选为10-20nm的铜-镍合金层。试验证明,该厚度的铜-镍合金层可使箔材和基材之间的结合力大大提高约0.3-0.5n/mm。在离子注入过程中,若注入温度过高,则会使fr-4基材产生碳化现象,导致产生后续电镀后形成的覆铜板结合力低,或蚀刻性能不佳等现象。若注入温度过低,则会导致注入深度不够,且产生膜表面的分子产生化学键的数量偏少,与注入粒子结合不紧密,同样会导致产生后续电镀后形成的覆铜板结合力低,或蚀刻性能不佳等现象。理论上,高的束流密度会导致高的注入与沉积温度。实际上,发明人通过研究fr-4基材在等离子体浸泡式离子注入剂量、注入束流密度、真空阴极弧磁过滤等离子体沉积剂量与表面的温度之间的关系,探究通过控制注入剂量实现精确控制fr-4基材表面的温度的方法。在一个实施例中,通过控制注入剂量为1.0×1014-5.0×1016ions/cm2,优选为8.0×1014-5.0×1015ions/cm2,控制沉积厚度为30-100纳米,可使fr-4基材表面保持在最佳注入温度100-150摄氏度。根据本发明,在沉积过程中形成的铜-镍合金层厚度可以抗蚀刻药水侧蚀,大大提高制得的覆铜板的蚀刻因子。据发明人研究,调整后沉积的ni离子的能量,使ni离子的能量下降为50ev以下,这样形成的铜-镍合金层的厚度可忽略不计。将该条件下制得的覆铜板作为对照组,相比该对照组,在根据本发明的方法所形成的覆铜板的抗侧蚀能力提高了2倍以上。在根据本发明的另一实施例中,在注入和沉积过程中的ni靶材可更换为ni-cr合金靶材,并且加入一定质量分数(5%-20%)的cr之后,最终制得的覆铜板的抗侧蚀能力相比于纯ni靶材进一步提高,可用于下游对抗侧蚀能力要求很高的覆铜板。但是cr的加入也可能引入导致蚀刻不彻底的问题,因而对于抗侧蚀要求不是特别高的覆铜板,一般采用纯ni靶材。在根据本发明的另一实施例中,在注入和沉积过程中可以先使用ni靶材,后使用cr作为靶材,形成ni-cr合金层。通过控制ni以及cr靶材的注入与沉积速度及时间,使得ni-cr合金层中cr的质量分数为5%-20%。本书面说明使用了包括最佳模式的实例来公开本发明,且还使本领域的技术人员能够实施本发明,包括制作和使用任何装置或系统,以及执行任何相结合的方法。本发明可取得专利的范围由权利要求限定,并且可包括本领域技术人员所构思出的其它实例。如果这些其它的实例具有与权利要求的书面语言并无不同的结构元件,或者如果这些其它实例包括与权利要求的书面语言无实质差异的同等结构元件,则认为这些实例处在权利要求的范围之内。当前第1页12