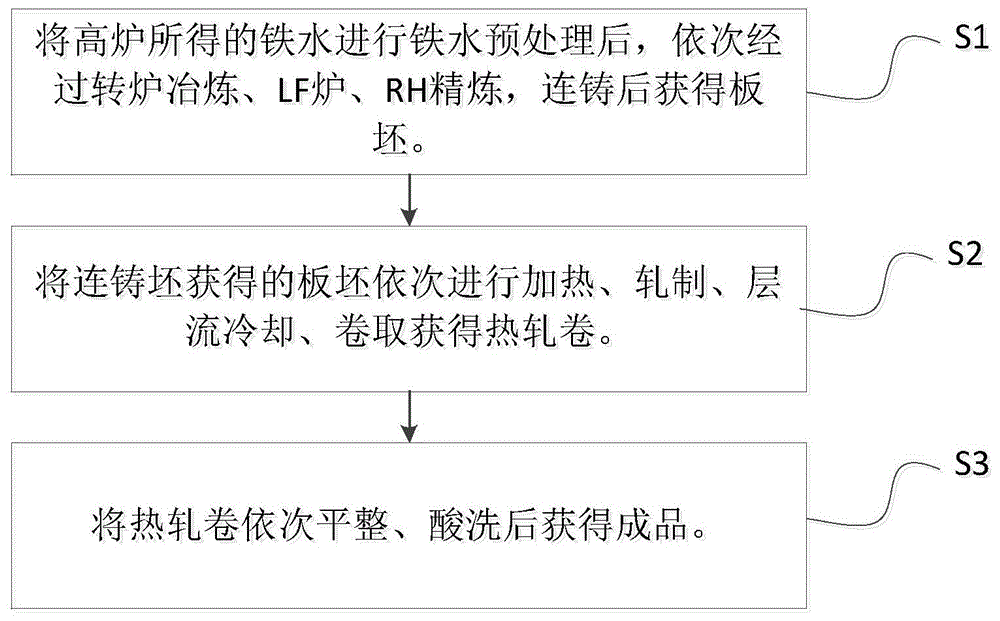
本发明属于钢铁冶炼
技术领域:
,特别涉及一种700mpa级汽车扭力梁用钢材及其制备方法。
背景技术:
:汽车在崎岖路面上行驶时,扭力梁同时承受车轮传递的纵向力以及垂直方向上的交变载荷,在横梁处应力高,易产生疲劳。因此必须要求扭力梁在具有高强度的同时,还需要高疲劳强度。在扭力梁的生产制造过程中,需要对焊接后的钢管进行较大程度的冷塑性变形,因此会在变形区域产生较大的残余应力,部分区域残余应力与外部载荷的叠加甚至可能使材料产生塑性变形而使其丧失承载能力。目前,为使扭力梁获得优异的疲劳性能,一般在生产工艺上会采取以下措施:1.扭力梁成形后经过热处理来实现消除残余应力和第二相补充析出强化。2.采用喷丸进行表面硬质化处理引入残余压应力。但是,引入热处理工艺会造成扭力梁表层脱碳,也可能使扭力梁发生形变,此时需额外增加矫正工序;采用喷丸处理对扭力梁表面进行硬质化处理使得扭力梁内壁难以得到有效硬化,内外壁之间存在的硬化差异会降低疲劳特性。技术实现要素:针对上述现有技术的不足,本发明提供了提供一种700mpa级汽车扭力梁用钢材及其制备方法,可以在不使用热处理或喷丸处理的工艺下同时获得优异疲劳性能的700mpa级汽车扭力梁用钢材。本发明通过以下技术方案来实现上述目的:本发明一方面公开了一种700mpa级汽车扭力梁用钢材,包含以下质量百分含量的成分:c:0.03~0.12%、si:0.05~0.18%、mn:0.8~2.0%、p≤0.02%、s≤0.009%、nb≤0.08%、ti≤0.1%、mo≤0.3%,al≤0.2%,其余是fe及不可避免杂质。进一步地,nb和ti的质量百分含量之和为0.1~0.15%。进一步地,(c+si/30+mn/20+mo/15)<0.18。更进一步地,所述汽车扭力梁用钢材的微观金相组织为贝氏体和珠光体。另一方面,本发明还公开了以上所述的一种700mpa级汽车扭力梁用钢材的制备方法,包括:s1,将高炉所得的铁水进行预处理后,依次经过转炉冶炼、lf炉、rh精炼,连铸后获得板坯;s2,将连铸获得的板坯依次进行加热、轧制、层流冷却、卷取获得热轧带钢;s3,将热轧带钢依次平整、酸洗后获得成品。进一步地,在步骤s2中,所述加热工序的加热温度控制为1200~1250℃,加热时间控制为150~200分钟。更进一步地,在步骤s2中,所述轧制工序包括粗轧和精轧,所述粗轧终止温度控制为1020~1080℃,所述精轧的终止温度控制为840~900℃。进一步地,在步骤s2中,所述卷取温度控制为450~550℃。进一步地,在步骤s3中,所述平整工序热轧带钢的延伸率控制为1~3%。进一步地,在步骤s3中,所述酸洗过程酸洗速度控制为60~100m/min,所述酸洗过程最后一个酸洗槽的酸洗温度控制为80~90℃,所述酸洗过程最后一个酸洗槽的铁离子浓度控制为30~40g/l。本发明的有益效果至少包括:本发明的公开的一种700mpa级汽车扭力梁用钢材及其制备方法,所述700mpa级汽车扭力梁用钢材包含以下质量百分含量的成分:c:0.03~0.12%、si:0.05~0.18%、mn:0.8~2.0%、p≤0.02%、s≤0.009%、nb≤0.08%、ti≤0.1%、mo≤0.3%,al≤0.2%,其余是fe及不可避免杂质。采用本发明的制备方法生产上述的700mpa级汽车扭力梁用钢材,所得的微观组织主要为贝氏体,并含有少量珠光体,其组织比常规的经过热处理、喷丸处理的扭力梁钢材组织更均匀,在扭力梁台架试验过程中,不会产生应力集中而萌生裂纹,从而保证扭力梁具备优良的疲劳性能;附图说明为了更清楚地说明本发明实施例中的技术方案,下面将对实施例描述中所需要使用的附图作简单地介绍,显而易见地,下面描述中的附图仅仅是本发明的一些实施例,对于本领域普通技术人员来讲,在不付出创造性劳动的前提下,还可以根据这些附图获得其他的附图。图1为本发明实施例的一种700mpa级汽车扭力梁用钢材的制备方法的工艺步骤图;图2为本发明实施例6制备的汽车扭力梁用钢材的微观金相组织示意图;图3为本发明实施例制备的汽车扭力梁用钢材的析出相;图4为热处理型汽车扭力梁用钢材的金相组织;图5为喷丸处理扭力梁用钢材的金相组织;图6为喷丸处理扭力梁用钢材的析出相。具体实施方式下面将结合本发明实施例中的附图,对本发明实施例中的技术方案进行清楚、完整地描述,显然,所描述的实施例仅仅是本发明一部分实施例,而不是全部的实施例。基于本发明中的实施例,本领域普通技术人员在没有做出创造性劳动前提下所获得的所有其他实施例,都属于本发明保护的范围。本发明公开了一种700mpa级汽车扭力梁用钢材,包含以下质量百分含量的成分:c:0.03~0.12%、si:0.05~0.18%、mn:0.8~2.0%、p≤0.02%、s≤0.009%、nb≤0.08%、ti≤0.1%、mo≤0.3%,al≤0.2%,其余是fe及不可避免杂质。碳与合金元素nb、ti、mo等会形成微合金碳化物而起到析出强化的作用;但是碳含量过高对钢材的焊接性存在不利影响,同时,从晶界析出的碳化物也会促使钢材裂纹的萌生与扩展,因而本发明中选择低碳体系,c含量设计为0.03~0.12%。本发明的si含量设计是考虑到:第一,硅含量过高会影响带钢的焊接性能与产品表面质量;第二,si含量过高会在钢材基体中生成硅氧化物夹杂,破坏基体组织的连续性,降低钢材韧性与成形后扭力梁的疲劳性能;第三,高硅带钢表面容易产生红锈缺陷,降低产品表面质量。因此,si含量控制为0.05~0.18%。在钢中添加mn元素可以提高钢材基体强度,但是mn元素添加过高会影响材料焊接性,并产生大量mns夹杂,并且mn元素的偏析会造成其它相组织如残余奥氏体的产生,降低组织的均匀性。因此,本发明控制mn含量在0.8~2.0%。p元素是钢中的有害元素,会增加钢材的冷脆性,s元素通常情况下也是钢种的有害元素,会使钢材产生热脆性,因此应尽可能的严格控制钢中p与s含量。al在本发明中作为脱氧剂与强化元素使用;同时非碳化物形成元素al可抑制c元素在贝氏体组织中脱溶,防止基体组织中大颗粒碳化物的产生,提高钢材韧性;而且al与n元素在轧制过程中会析出可细化组织晶粒,发挥细晶强化作用而提升疲劳性能。但al含量过高会造成连铸板坯表面裂纹与氧化铝夹杂,因此本发明中al含量控制为为≤0.2%。钢中加入少量的nb元素即可以充分发挥细晶强化与析出强化效果,但是nb属于贵金属,本发明设计nb含量不超过0.08%。本发明中适量添加ti元素,这是因为,其一,ti元素可以固定钢中n元素,细化晶粒并防止nbn与aln造成的连铸板坯裂纹。其二,降低沿轧向分布的条状mns造成的板材横纵向力学性能的差异。但是ti含量过高时会产生大颗粒的ti夹杂。因此,本发明设计钢中ti含量不超过0.1%。本发明设计mo含量低于0.30%,这是因为mo是促进贝氏体组织形成的最有效元素,其可以降低nb元素奥氏体轧制过程中的析出量,使更多的nb元素在铁素体温度区间与mo形成细小弥散的析出相,充分发挥弥散强化的作用。进一步地,nb和ti的质量百分含量之和为0.1~0.15%,当ti含量为0.1%时,奥氏体晶粒粗化温度为1100℃,继续提高ti含量对于提高奥氏体晶粒粗化温度影响较小,而提高奥氏体晶粒粗化温度,有助于我们粗轧过程细化奥氏体晶粒,而带钢内部的形态具有遗传性,最终所得的成品晶粒也会更细小,有利于提高成品的塑性、韧性和强度;当nb含量为0.05%时,奥氏体再结晶停止温度达到峰值1000℃,并且会继续提高奥氏体晶粒粗化温度;鉴于以上所述,同时考虑成本因素,限制nb与ti含量在0.1~0.15%。进一步地,(c+si/30+mn/20+mo/15)<0.18。pcm=(c+si/30+mn/20+mo/15),这是焊接敏感系数,这个系数越大,表示钢材的焊接性能越差,此系数越小,表示钢材的焊接性能越好。将焊接敏感系数设计为<0.18,是钢材的强度和焊接性能之间的一个平衡点。更进一步地,所述汽车扭力梁用钢材的微观金相组织为贝氏体和珠光体。其中贝氏体的体积分数为90%,珠光体的体积分数为10%。贝氏体组织均匀,具有良好的成形性,台架试验过程中,因为组织均匀的特点不易在钢材中产生应力集中而萌生裂纹,从而可以保证其具有良好的疲劳性能。本发明公开的一种700mpa级汽车扭力梁用钢材,采用c-si-mn-al-nb-mo-ti成分体系的合理设计,使产品的强度、延伸率等性能指标符合客户和标准要求。本发明采用nb和ti元素在起到析出强化作用的同时,还能细化组织晶粒,发挥细晶强化的作用。mo元素的加入,可有效的促进钢材形成贝氏体组织,而均匀的贝氏体组织在台架试验过程中不易产生应力集中而萌生裂纹,保证了汽车扭力梁用钢的良好疲劳性能。另一方面,本发明公开了以上所述的700mpa级汽车扭力梁用钢材的制备方法,图1为一种700mpa级汽车扭力梁用钢材的制备方法的工艺步骤图,结合图1,本制备方法,包括:s1,将高炉所得的铁水进行预处理后,依次经过转炉冶炼、lf炉、rh精炼,连铸后获得板坯;高炉冶炼所得的钢水碳含量高,杂质元素多,经过以上所述的转炉冶炼、lf炉、rh精炼处理后得到成分符合本发明要求的钢水,钢水经过连铸机浇注出板坯,为热轧提供成分合格的原料。s2,将连铸获得的板坯依次进行加热、轧制、层流冷却、卷取获得热轧带钢;所述加热工序的加热温度控制为1200~1250℃,加热时间控制为150~200分钟。对连铸获得的板坯进行加热,是为了确保板坯成分均匀化,微合金析出相充分溶解,并获得均匀的奥氏体组织。控制加热温度和加热时间既可以保证板坯受热均匀也不会使板坯产生过热等缺陷。所述轧制工序包括5道次粗轧、7道次精轧,所述粗轧终止温度控制为1020~1080℃,所述精轧终止温度控制为840~900℃。经过5道次粗轧,将板坯内粗大的奥氏体晶粒细化,为获得均匀细化组织的成品提供条件。精轧终止温度控制在ar3温度点以上的奥氏体未再结晶区温度范围,这种低温终轧,可以使奥氏体充分形变,引入大量变形带,从而为形核析出提供大量的晶界,可进一步均匀、细化奥氏体晶粒。所述卷取温度控制为450~550℃。将卷曲温度控制为450~550℃,是因为在实际生产中,这个温度范围是粒状贝氏体的温度转变区间,在此温度范围可以将精轧所获得的的均匀细小的奥氏体组织相变获得均匀的贝氏体金相组织,卷取后大量细小的微合金析出相可以达到强化基体的目的。所述热轧带钢的厚度控制为1.8~5mm。本发明采用了控制轧制和控制冷却技术,即tmcp技术,实现了奥氏体晶粒细化和细晶强化的效果,经过一系列的粗轧、精轧、卷曲的工艺参数控制,所得的热轧带钢具有大量的均匀细小的贝氏体组织,少量的珠光体组织和第二相析出,提高了热轧带钢的塑性、韧性和强度,其均匀的贝氏体组织使其在台架试验中,不会产生应力集中,从而避免裂纹的产生,可获得优良的疲劳性能。s3,将热轧带钢依次平整、酸洗后获得成品。所述平整工序热轧带钢的延伸率控制为1~3%。所述酸洗过程酸洗速度控制为60~100m/min,所述酸洗过程最后一个酸洗槽的酸洗温度控制为80~90℃,所述酸洗过程最后一个酸洗槽的铁离子浓度控制为30~40g/l。控制酸洗速度、酸洗温度和铁离子浓度,是为了获得表面质量良好的成品,避免出现过酸洗或欠酸洗缺陷。本发明公开的700mpa级汽车扭力梁用钢材采用上述的制备方法,经铁水预处理、转炉炼钢、精炼以及连铸获得成分复合设计要求的板坯,在经过控制轧制、层流冷却,并配合一定的平整、酸洗工艺,获得抗拉强度700mpa级、成形性能优异且具备高焊接性能的成品,成品带钢微观金相组织为主要为贝氏体,含有少量的珠光体组织,该带钢屈服强度≥590mpa,抗拉强度≥700mpa,断后延伸率a80≥18%,具备优异的表面质量及焊接性,在贝氏体基体组织中析出的细小第二相充分发挥析出强化作用,由于其贝氏体金相组织比常规的热处理、喷丸处理的扭力梁钢金相组织均匀,因此在台架试验中,不会产生应力集中而萌生裂纹,而具有优良的疲劳性能。下面将列举8个实施例,来说明本发明公开的一种700mpa级汽车扭力梁用钢材极其制备方法。将高炉冶炼所得铁水进行铁水预处理后,进行转炉冶炼、lf精炼、rh精炼获得钢水后连铸获得成分合格的板坯,各元素化学成分见表1。表1将上述8个实施例所得的板坯放在加热炉中进行加热,板坯的出炉温度为1230~1245℃,经过粗轧、精轧获得热轧板,所述热轧板厚度规格变化范围控制在2~3.5mm,所述粗轧终止温度控制为1030~1055℃,所述精轧终止温度控制为845~875℃,将所述热轧板层流冷却后在450~500℃卷取温度下卷取获得热轧带钢,各实施例加热、轧制、卷曲的工艺参数具体见表2所示。表2编号出炉温度,℃粗轧终止温度,℃精轧终止温度,℃卷取温度,℃热轧板厚度,mm实施例1124010458554702实施例2123610408504502.5实施例3124510558654553实施例4123310508704752实施例5123010358455002.5实施例6123210308604653.5实施例7123510408654753实施例8123810308754803.5将所得的热轧带钢经平整、酸洗后获得成品。平整延伸率控制为1~3%;经过平整后,热轧带钢的酸洗运行速度控制为60~100m/min,最末酸洗槽酸洗温度控制为80~90℃、铁离子浓度控制为30~40g/l。各实施例工艺参数如表3所示。表3编号平整延伸率,%酸洗运行速度,m/min最末酸洗温度,℃最末酸洗铁离子浓度,g/l实施例12.0808534实施例21.5758335实施例32.0708237实施例41.5758636实施例52.2708437实施例62.1758336实施例72.0708637实施例81.9658834以上所述的8个实施例生产的汽车扭力梁用钢成品的力学性能如表4所示。表4编号屈服强度,mpa抗拉强度,mpa延伸率,a80%实施例160471520.5实施例261270322.5实施例359771820.5实施例460371221实施例561470821.5实施例661170822实施例760971621.5实施例862472320.5根据表4中的数据可知,采用本发明制备的汽车扭力梁用钢材的抗拉强度达到了700mpa级。为了说明实施例中所得汽车扭力梁用钢成品的强度,将实施例所得的钢材取样并在扫描电镜下观察析出相,并将其与喷丸处理所得汽车扭力梁用钢进行对比。图3是本发明实施例制备的汽车扭力梁用钢的析出相,图6是喷丸处理扭力梁用钢材的析出相,对比图3和图6,两者均是在50nm的视野下所拍的细小析出相,本发明实施例制备的汽车扭力梁用钢的细小析出相数量明显超过了喷丸处理扭力梁用钢的析出相,而析出相可以有效地提升钢材的强度,由此可知,采用本发明制备的汽车扭力梁用钢具备更高的强度。为了说明实施例中所得汽车扭力梁用钢成品的疲劳性能,将实施例所得的钢材取样并观察微观金相组织,并将其与热处理、喷丸处理所得汽车扭力梁用钢进行对比。图2是采用本法明制备所得的汽车扭力梁用钢的微观金相组织,图4是热处理型汽车扭力梁用钢材的金相组织,图5是喷丸处理汽车扭力梁用钢材的金相组织,三张图皆为1000倍拍摄。观察图2、图4和图5可知:采用本发明制得的汽车扭力梁用钢微观金相组织为贝氏体和珠光体,贝氏体占比90%以上,且贝氏体组织均匀,可以保证产品具有良好的折弯性能,在扭力梁台架试验过程中,不会产生应力集中而萌生裂纹,从而保证扭力梁具备优良的疲劳性能;热处理型汽车扭力梁用钢材的微观金相组织为铁素体和珠光体,见图4,软质相铁素体与硬质相珠光体组织分布不均匀,珠光体成条带状分布,冲压成形时存在开裂风险,且扭力梁在台架试验过程中,铁素体-珠光体的软硬相之间容易产生应力集中,并萌生裂纹,不利于扭力梁疲劳寿命的提高;喷丸处理主要是通过在材料表面引入发生塑性变形的组织层(加工硬化层)来提升产品的疲劳性能,但受喷丸工艺所限,汽车扭力梁各处的加工硬化层组织不均匀,参见图5,局部喷丸过强会导致加工硬化层脱落,经喷丸处理后,汽车扭力梁的表面凹凸不平,粗糙度增大,在台架试验过程中,汽车扭力梁的表面会出现应力集中,引发裂纹,降低疲劳强度。由以上分析可知,本发明制备的汽车扭力梁用钢材的疲劳性能绝对可以超过热处理、和喷丸处理型扭力梁钢。需要说明的是,因实际生产中无法测量钢材的疲劳强度,一般认为,组织的均匀性、应力集中和钢中的大颗粒夹杂是影响疲劳强度的几个重要因素。汽车扭力梁用钢属于是高品质特殊用途钢材,其产品设计、性能要求和生产工艺要求都非常严格,所以在本类型的钢材中几乎不存在大颗粒夹杂,因此本专利申请中仅采用组织均匀性和应力集中两个方面来衡量汽车扭力梁用钢材的疲劳性能。以上所举实施例为本发明的较佳实施方式,仅用来方便说明本发明,并非对本发明作任何形式下的限制,任何所述
技术领域:
中具有通常知识者,若在不脱离本发明所提技术特征的范围内,利用本发明所揭示技术内容所作出局部更动或修饰的等效实施例,并且未脱离本发明的技术特征内容,均仍属于本发明技术特征的范围内。当前第1页12