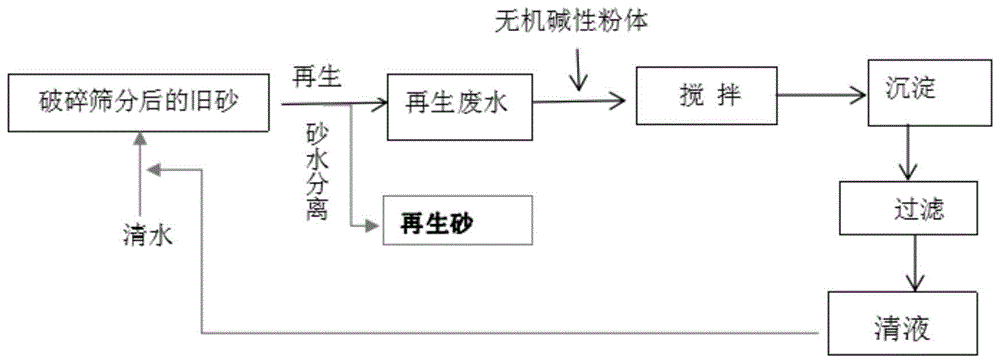
本发明属于铸造行业资源回收利用领域,具体涉及一种无废水排放的水玻璃旧砂湿法再生方法。
背景技术:
:绿色清洁生产是铸造生产的发展趋势,为了实现绿色清洁生产,旧砂的全部再生回用是关键。水玻璃砂被公认为是最有可能实现绿色铸造的型砂。它以其无色、无味、无毒,在混砂、造型浇注和落砂过程中没有刺激性气体和有毒气体产生对人体没有危害,最大的不足就是很难再生,造成较大污染,所以能实现循环利用问题,水玻璃砂将率先进入绿色铸造行列。水玻璃旧砂湿法再生是利用水的溶解、擦洗作用及机械搅拌作用,去除旧砂粒表面的残留粘结剂、盐、酯等水溶性物质。湿法再生水玻璃旧砂具有残留粘结剂去除率高、再生砂质量好等优点,现有的水玻璃砂湿法再生后产生大量碱性废水,需经处理后才能实现循环利用或向外排放,而废水处理问题一直没得到很好的解决。水玻璃砂污水的特点:水玻璃砂污水中一般含有较多的碳酸钠、naoh以及硅酸胶体和粘土胶体。这两种胶体颗粒均带负电荷,由于静电斥力的作用,阻止胶粒与胶粒之间碰撞而聚集成较大颗粒,它们稳定地呈悬浮状态存在于水中,因而这种污水不可能通过自然沉淀达到澄清的目的。因此必须投加能使胶体发生电荷中和而脱稳凝聚的凝聚剂,以及促使失去稳定的颗粒形成较大絮体的絮凝剂。何富强等人采用加酸中和后,再加聚合氯化铝(pac)和聚丙烯酰胺(pam)絮凝剂复合使用来处理污水,处理后污水中大部分胶体已被除去,处理后的水浊度降低到25度,已经接近纯净水的浊度1度,人的肉眼已不能区分,采用此种方法虽可以较为有效的处理污水,但是消耗的化学试剂的量大,成本高,且处理过程中加酸处理易腐蚀设备,处理后带入了氯离子、铝离子及聚丙烯酰胺等有机成分。龙威等人通过加酸将污水的ph值降低到7、再加入有机膨润土和聚合氯化铝对污水进一步处理,获得了满意的处理效果。但有机膨润土成本较高,处理周期较长。cn201510528118.6发明公开了一种co2硬化水玻璃砂湿法再生废水的处理方法,采用分次ph调节、混凝、助凝、沉淀、污泥脱水的方法处理铸造行业水玻璃砂湿法再生废水,并将浓缩后的沉淀泥渣用板框压滤机处理后外运,铸造水玻璃砂湿法再生原水经过ph粗调池和ph微调池,在泵前、后分别加入混凝剂pac和助凝剂pam,通过序批式絮凝沉淀浓缩池,停止进水处理2~3h后将上清液排出,再用泵将池底的浓缩污泥抽至板框压滤机。但是上述再生废水处理方法存在工艺操作繁琐,处理周期长,处理成本高等缺陷。基于上述理由,特提出本申请。技术实现要素:针对现有技术存在的问题或缺陷,本发明的目的在于提供一种无废水排放的水玻璃旧砂湿法再生方法。采用加化学试剂处理水玻璃旧砂湿法再生的污水,实现旧砂再生和滤液的循环利用是本发明的创新之处,且再生砂的性能优于传统湿法再生砂的性能。为了实现本发明的上述目的,本发明采用的技术方案如下:一种无废水排放的水玻璃旧砂湿法再生方法,所述方法具体包括如下步骤:(1)将收集的水玻璃旧砂破碎、筛分后与清水混合,直接静置10-36h;或机械搅拌3-10min;然后将砂水分离,获得湿砂和再生废水,将所述湿砂烘干,得到再生砂;(2)向步骤(1)获得的再生废水中加入碱性无机粉体,混合搅拌、静置沉淀、过滤,即可获得清液,再将所述清液用于下一批水玻璃旧砂的湿法再生用水,重复步骤(1)。进一步地,上述技术方案,还包括步骤(3):当步骤(1)获得的再生砂中的总碱量超标时,用清水淋洗再生砂,然后将淋洗获得的淋洗液用于补充旧砂再生用水。进一步地,上述技术方案,步骤(1)所述水玻璃旧砂筛分优选采用高频振筛机,所述振筛机是将颗粒大小不一的水玻璃旧砂多次通过均匀布孔的单层或多层筛面,最终实现粗砂、细砂粒的分离。进一步地,上述技术方案,步骤(1)所述水玻璃旧砂与清水的质量比为1:2-10,较优选为1:3。进一步地,上述技术方案,步骤(1)所述静置时间优选为24h。进一步地,上述技术方案,步骤(2)所述碱性无机粉体为氢氧化镁、氢氧化钙、氧化钙中的任一种。优选地,上述技术方案,步骤(2)所述碱性无机粉体优选为氧化钙。进一步地,上述技术方案,步骤(2)所述再生废水中碳酸钠与碱性无机粉体摩尔比为1:1-6。优选地,上述技术方案,步骤(2)所述再生废水中碳酸钠与碱性无机粉体的摩尔比为1:6。进一步地,上述技术方案,步骤(2)所述混合搅拌时间可不作具体限定,只要达到均匀混合、反应充分的目的即可。所述混合搅拌时间较优选为1-10min,更优选为3min。进一步地,上述技术方案,步骤(2)所述静置时间不超过36h,较优选为24h。为了清除再生废水中的碳酸盐等物质,减少有害成分累积对旧砂的再生性能造成不利的影响,必须采取措施去除再生废水主要中的碳酸盐、硅酸盐等成分,而且不会引入新的有害成分。本发明采用的三种不同无机碱性粉体cao、ca(oh)2、mg(oh)2处理再生废水的反应方程式如下式一所示,通过上述反应可以将再生废水中的co32-和sio32-沉淀过滤后除去,得到稀的碱溶液。cao+co32-+h2o=caco3↓+2oh-+h2ocao+sio32-+h2o=casio3↓+2oh-+h2oca(oh)2+co32-+h2o=caco3↓+2oh-+h2oca(oh)2+sio32-+h2o=casio3↓+2oh-+h2omg(oh)2+co32-+h2o=mgco3↓+2oh-+h2omg(oh)2+sio32-+h2o=mgsio3↓+2oh-+h2o式一。与现有技术相比,本发明涉及的一种无废水排放的水玻璃旧砂湿法再生方法具有如下有益效果:本发明使用加氢氧化镁、氢氧化钙、氧化钙三种不同无机碱性粉体去除湿法再生废水中的有害成分,经处理过滤后的废水循环用于水玻璃旧砂的再生,再生砂的性能与新砂性能相近,完全能够达到工艺要求。经过实验对比分析发现,氧化钙处理再生废水的效果最好,且将氧化钙处理过滤后的废水再次用于湿法再生水玻璃砂,获得的再生砂中碳酸钠含量显著降低,其含量对再生砂性能没有影响。附图说明图1为本发明的一种无废水排放的水玻璃旧砂湿法再生方法的工艺流程示意图。图2为用酸滴本发明实施例1-3获得的清液所生成的二氧化碳气体体积对比图。图3为用酸滴本实施例4-11获得的清液所生成的二氧化碳气体体积对比图。图4为本发明实施例7、实施例12分别获得的再生砂以及市场上购买的新砂、旧砂的初始强度测试结果对比图:其中,纵坐标为初始强度,单位为mpa。图5为本发明实施例7、实施例12分别获得的再生砂以及市场上购买的新砂、旧砂的终强度测试结果对比图;其中,纵坐标为终强度,单位为mpa。图6为本发明实施例7、实施例12分别获得的再生砂以及市场上购买的新砂、旧砂的溃散性测试结果对比图;其中,纵坐标为残留强度,单位为mpa。图7为本发明实施例13获得的再生砂以及市场上购买的新砂、旧砂的初强度、终强度及溃散性测试结果对比图;其中,纵坐标为强度,单位为mpa。图8为用酸滴本实施例13的新砂、旧砂及获得的再生砂所生成的二氧化碳气体体积对比图;其中,纵坐标为体积,单位为ml。具体实施方式下面通过实施案例对本发明作进一步详细说明。本实施案例在以本发明技术为前提下进行实施,现给出详细的实施方式和具体的操作过程来说明本发明具有创造性,但本发明的保护范围不限于以下的实施案例。根据本申请包含的信息,对于本领域技术人员来说可以轻而易举地对本发明的精确描述进行各种改变,而不会偏离所附权利要求的精神和范围。应该理解,本发明的范围不局限于所限定的过程、性质或组分,因为这些实施方案以及其他的描述仅仅是为了示意性说明本发明的特定方面。实际上,本领域或相关领域的技术人员明显能够对本发明实施方式作出的各种改变都涵盖在所附权利要求的范围内。为了更好地理解本发明而不是限制本发明的范围,在本申请中所用的表示用量、百分比的所有数字、以及其他数值,在所有情况下都应理解为以词语“大约”所修饰。因此,除非特别说明,否则在说明书和所附权利要求书中所列出的数字参数都是近似值,其可能会根据试图获得的理想性质的不同而加以改变。各个数字参数至少应被看作是根据所报告的有效数字和通过常规的四舍五入方法而获得的。本发明采用的三种碱性无机粉体原料物化性质如下:氢氧化镁,白色无定形粉末。别名苛性镁石,轻烧镁砂等,氢氧化镁在水中的悬浊液称为氢氧化镁乳剂,简称镁乳,氢氧化镁是无色六方柱晶体或白色粉末,难溶于水和醇,溶于稀酸和铵盐溶液,水溶液呈弱碱性。氧化钙化学式为cao,白色粉末,具有吸湿性,能够溶于蔗糖,酸类等,在生产中常用作填充剂原料等。由于氧化钙能够和空气中的二氧化碳反应,在存放时要保证密闭和干燥。氢氧化钙(calciumhydroxide),无机化合物,化学式ca(oh)2,俗称熟石灰或消石灰。是一种白色粉末状固体,加入水后,呈上下两层,上层水溶液称作澄清石灰水,下层悬浊液称作石灰乳或石灰浆。本发明下述实施例中涉及的旧砂筛分步骤如下:首先使用托盘装取适量破碎后的旧砂(未筛),以备进一步处理,采用20目和200目的筛子,从上到下依次叠放,用铁铲取适量的未筛旧砂放入20目的筛子里,再将这些筛子一起放到振筛机上,放好后打开振筛机选择10min挡位,待10min后振筛机自动停止完成一次振筛,将20目筛子上的旧砂舍弃,将200目的筛子里的砂装入袋子中作为本发明用砂,完成一次振筛后重复以上步骤继续进行三到四次(可根据所用砂量进行多次振筛),待得到足够砂样,备用。所采用的新砂及旧砂的粒度分布如下表1所示。表1原砂和旧砂的粒度分布(%)筛号(目)30405070100140200>200总量原砂6.045.7428.4936.7622.865.040.400.1099.30筛分后旧砂4.311.4826.0631.0417.374.551.393.7699.95以下实例所使用的水玻璃为武汉本地产,模数为3.1,密度为1.32,使用时加入一定量的naoh饱和溶液混合均匀,以调整水玻璃模数和密度,调整后水玻璃模数m=2.3,密度为1.41。加入量占原砂的6.0%;性能测试用砂样采用中空圆柱状样桶在锤击式制样机上制得,砂样直径30mm,高30mm。水玻璃硬化用二氧化碳气体:采用武汉某公司制造的瓶装工业co2气体,吹气流量15l/min,吹气时间15s~20s。实施例1本实施例的一种无废水排放的水玻璃旧砂湿法再生方法,所述方法具体包括如下步骤:(1)将500g收集的水玻璃旧砂破碎、筛分后与1500g清水混合,机械搅拌3min,搅拌结束后将砂水分离,获得湿砂和再生废水,将所述湿砂烘干,得到再生砂;(2)取100ml步骤(1)获得的再生废水,加入0.5g(过量)氧化钙,混合搅拌30s、静置沉淀24h、过滤,即可获得清液。实施例2本实施例的一种无废水排放的水玻璃旧砂湿法再生方法,所述方法与实施例1基本相同,区别仅在于:本实施例步骤(2)中加入的是0.5g(过量)氢氧化钙。实施例3本实施例的一种无废水排放的水玻璃旧砂湿法再生方法,所述方法与实施例1基本相同,区别仅在于:本实施例步骤(2)中加入的是0.5g(过量)氢氧化镁。分别用气体法测量实施例1获得的再生废水、清液以及实施例2、实施例3获得的清液中的co32-的含量,其含量是以酸滴废水(或清液)所生成的二氧化碳气体体积为衡量。测量时,每次取10ml液体,每种液体测量三次后取气体体积平均值。其结果如图2所示,其中:图中原液表示实施例1获得的再生废水,cao表示实施例2获得的清液;ca(oh)2表示实施例2获得的清液;mg(oh)2表示实施例3获得的清液。由图2可以看出,在同样加入了过量的试剂处理后的污水中,用cao和ca(oh)2处理再生废水获得的清液产生的气体明显减少,即清液中碳酸根的量有明显的减小,且两者处理效果相当,而mg(oh)2的处理效果相较于前两种效果不显著,故本发明的无机碱性粉体优选采用氧化钙和氢氧化钙。实施例4本实施例的一种无废水排放的水玻璃旧砂湿法再生方法,所述方法具体包括如下步骤:(1)将500g收集的水玻璃旧砂破碎、筛分后与1500g清水混合,静置沉淀24h,然后将砂水分离,获得湿砂和再生废水,将所述湿砂烘干,得到再生砂;(2)取100ml步骤(1)获得的再生废水,加入氧化钙,混合搅拌30s、静置24h、过滤,即可获得清液,其中:所述再生废水中碳酸钠与氧化钙的摩尔比为1:1。实施例5本实施例的一种无废水排放的水玻璃旧砂湿法再生方法,所述方法与实施例4基本相同,区别仅在于:本实施例步骤(2)所述再生废水中碳酸钠与氧化钙的摩尔比为1:2。实施例6本实施例的一种无废水排放的水玻璃旧砂湿法再生方法,所述方法与实施例4基本相同,区别仅在于:本实施例步骤(2)所述再生废水中碳酸钠与氧化钙的摩尔比为1:4。实施例7本实施例的一种无废水排放的水玻璃旧砂湿法再生方法,所述方法与实施例4基本相同,区别仅在于:本实施例步骤(2)所述再生废水中碳酸钠与氧化钙的摩尔比为1:6。实施例8本实施例的一种无废水排放的水玻璃旧砂湿法再生方法,所述方法与实施例4基本相同,区别仅在于:本实施例步骤(2)中加入的无机碱性粉体为氢氧化钙,其用量与实施例4中氧化钙的用量相同。实施例9本实施例的一种无废水排放的水玻璃旧砂湿法再生方法,所述方法与实施例5基本相同,区别仅在于:本实施例步骤(2)中加入的无机碱性粉体为氢氧化钙,其用量与实施例5中氧化钙的用量相同。实施例10本实施例的一种无废水排放的水玻璃旧砂湿法再生方法,所述方法与实施例6基本相同,区别仅在于:本实施例步骤(2)中加入的无机碱性粉体为氢氧化钙,其用量与实施例6中氧化钙的用量相同。实施例11本实施例的一种无废水排放的水玻璃旧砂湿法再生方法,所述方法与实施例7基本相同,区别仅在于:本实施例步骤(2)中加入的无机碱性粉体为氢氧化钙,其用量与实施例7中氧化钙的用量相同。分别用气体法测量实施例4-11获得的清液中的co32-的含量,其含量是以酸滴废水(或清液)所生成的二氧化碳气体体积为衡量。测量时,每次取10ml液体,每种液体测量三次后取气体体积平均值。其结果如图3所示。由图3可以看出,ca(oh)2处理获得的清液生成的co2体积随着比例的增加相较于cao有着较快的下降,但是,cao处理的上限要比ca(oh)2高,即再生废水中碳酸钠与氧化钙或氢氧化钙的摩尔比为1:6时,cao的处理效果要比ca(oh)2好,为求达到完全去除或尽可能多的去除污水中na2co3的目的,本发明最优选用cao作为再生废水的处理试剂,并且用1:6的量来处理。为了测试本发明获得的清液再次用于水玻璃旧砂湿法再生处理的处理效果,设置如下实施例。实施例12将500g收集的水玻璃旧砂破碎、筛分后与1500g实施例7获得的清液混合,机械搅拌3min,搅拌结束后静置沉淀24h,然后将砂水分离,获得湿砂和再生废水,将所述湿砂烘干,得到再生砂。将实施例7、实施例12分别获得的再生砂以及市场上购买的新砂、旧砂的初始强度、终强度、溃散性进行测试。其中:初始强度、终强度测试方法如下:用电子天平称取1.0kg砂样放入搅拌锅中,再使用微量移液管取60g水玻璃,倒入搅拌锅内,将搅拌锅正确安放到水泥膠砂搅拌机上,打开开关选择低速挡,搅拌三分钟,待搅拌完成后,取下搅拌锅。使用锤击式制样机进行制样,每次利用电子天平称取33g混合砂样进行制样,并用15ml/min的co2吹气20秒,以起到硬化作用,吹完后取出制样,在连续制备相同的三个样本(样本1、样本2、样本3)后,使用液压万能强度试验机测量其及时(初始)强度。续采用以上步骤制样,将制样用托盘放置24小时。待24小时后用液压万能强度试验机测量其终强度。溃散性测试方法如下:事先打开高温箱式电阻炉,预热两小时左右,使炉内温度到达800℃。待温度达到要求,用铁片放置制样并用铁钳放入高温箱式电阻炉内,关闭炉门,保持炉内800℃加热20分钟。到达时间后,取出制样自然冷却,待制样回到常温使用液压万能强度试验机测量其强度,以得到溃散性。实施例7、实施例12分别获得的再生砂以及市场上购买的新砂、旧砂的初始强度的测试结果如图4所示。由图4可以看出,旧砂直接加水玻璃co2吹气硬化后的初始强度是最高的,实施例7获得的再生旧砂的初始强度相比于旧砂的强度要低一点,但是比新砂和实施例12获得的再生砂强度要高,而实施例12获得的再生砂的初始强度比新砂略高一些,接近新砂的性能。实施例7、实施例12分别获得的再生砂以及市场上购买的新砂、旧砂的终强度的测试结果如图5所示。得到图5。由图5可以看出,实施例7获得的再生旧砂加入水玻璃后co2吹气硬化后的终强度略低于旧砂的,而新砂和实施例12获得的再生旧砂都明显低于旧砂的终强度,且新砂的强度最低,实施例12获得的再生旧砂与新砂终强度相近。实施例7、实施例12分别获得的再生砂以及市场上购买的新砂、旧砂的溃散性测试结果如图6所示。由图6可以看出,旧砂的残留强度最高,实施例7获得的再生旧砂的残留强度最低,新砂的残留强度与实施例12获得的再生旧砂的残留强度接近。通过再生砂的性能测试结果可知,将本发明获得的再生砂,以及将氧化钙处理、过滤获得的清液再次用于水玻璃旧砂湿法再生得到的再生砂与新砂在初始强度、终止强度、残留强度三个性能指标上都比较接近,因为1:6加入氧化钙处理后的再生砂是满足性能要求的。在进行旧砂的再生时,再生砂中的总碱量的多少是衡量再生效果的一个标准。因此,本发明还将实施例7、实施例12分别获得的再生砂以及市场上购买的新砂、旧砂的砂样滤液进行相应的总碱量及碳酸钠含量进行测定。以购买的旧砂砂样中总碱量及碳酸钠含量测试方法如下:总碱量测试方法如下:取100g旧砂擦洗后,采用shb—iii循环水式多用真空泵抽滤,将得到的滤液进行7000r/min离心7分钟后放入容量瓶中定容,得最终提取液。取10ml(约为10g)提取液进行总碱量测定,滴入三至四滴溴甲酚绿-甲基红指示剂,摇匀,溶液呈蓝色。用酸式滴定管进行盐酸滴定,滴定前记下初始刻度,待溶液从蓝色变为红色停止滴定,记下终止刻度,由初始刻度和终止刻度即可算到所耗盐酸体积,即完成一次测定,依次采用上述步骤测量三次,所得起始刻度、终止刻度及用量测试结果如下表2所示。表2三次酸碱滴定测试结果表注:使用的盐酸浓度为0.064mol/l。即盐酸的平均用量为(21.1+21+20.9)/3=21ml,根据如下计算公式进行总碱量的计算:其中:c—所用盐酸的浓度(mol/l);v1—所用盐酸的体积(ml);m—所取试样的质量(g)。碳酸钠含量测定方法如下:取上述提取液10ml(约为10g),放入圆底烧瓶中,滴入2~3滴甲基红指示剂(黄色),放到恒温磁力搅拌器上(将磁石放入烧瓶),气体体积法测定装置安装正确后打开电源,先记下量气管的初始刻度,一边滴盐酸一边调整旁边u型量气管的开关,待圆底烧瓶中溶液变为红色,停止滴入盐酸,等u型管内两边液面相平时记下终止刻度。连续进行三次上述过程,所得数据如下表3所示。表3三次酸碱滴定测试结果表注:所用盐酸浓度为0.064mol/l则平均co2体积为:(13.5+13.2+13.6)/3=13.43ml,根据以下公式粗略计算碳酸钠含量:其中:v—生产二氧化碳体积(u型管液面下降体积)ml;m—所取试样质量(g)。采用上述旧砂砂样中总碱量测试相同的方法测试本发明实施例7、实施例12分别获得的再生砂总碱量及碳酸钠含量,测试结果如表4、表5所示。表4旧砂、实施例7、实施例12获得的再生砂总碱量测试结果表表5旧砂、实施例7、实施例12获得的再生砂中碳酸钠含量测试结果表由表4可知,实施例12获得的再生砂总碱量低于实施例7获得的再生旧砂的总碱量;由表5可知,实施例12获得的再生砂砂分中的碳酸钠含量低于实施例7获得的再生旧砂中的碳酸钠含量。通过上述性能测试对比,实施例12获得的再生砂在初始强度,终强度,可使用时间,溃散性等方面都满足要求。由以上有害成分的对比实验发现,实施例12获得的再生砂的碳酸钠含量是最少的,因此将本发明湿法再生获得的清液循环用于水玻璃砂湿法再生获得的再生砂性能满足工艺要求。实施例131)将88.25g氧化钙与170.19g水混合制成石灰浆料密闭备用;2)选用1500g旧砂,测得旧砂的碳酸钠含量为2.6%,加入3000ml自来水,搅拌5min进行湿法再生,过滤分离再生砂和再生废水,将再生砂用600ml清水淋洗后烘干,得淋洗液500ml;在再生砂中加入水玻璃混砂制样,测试再生砂的性能(直接再生砂);3)在2400g污水中加入步骤1)制备的石灰浆料混合,搅拌30s,静置1min,得污水处理液;4)选用1000g旧砂,取步骤3)所得污水处理液上清液2000ml处理液洗加入旧砂中,搅拌5min进行湿法再生,过滤分离再生砂和再生废水,将再生砂烘干后,加入水玻璃混砂制样,测试再生砂的性能(二次再生砂);5)选用1000g旧砂,取步骤4)所得污水处理液上清液1500ml处理液,搅拌5min进行湿法再生,过滤分离再生砂和再生废水,将再生砂烘干后,加入水玻璃混砂制样,测试再生砂的性能(三次再生砂);为了对比再生效果,采用同种原砂的新砂和旧砂,加入等量水玻璃和同样的制样吹气工艺,测得型砂的性能如表6所示:表6新砂、旧砂及再生砂性能比较表6、图7和图8显示的测试结果表明:再生过程中氧化钙加入量、水加入量和放置时间对再生效果有不同影响,在一定范围内,随水的加入量增加,终强度增强,溃散性变差;而氧化钙的加入量不宜过低或过高,且静置处理时间则以12h为优。经适当再生处理后再生砂性能接近新砂,终强度甚至超过了新砂,多次再生后砂中残留的碳酸钠含量显著降低,和直接再生砂相近,除去了旧砂中90%的碳酸钠,说明再生过程除去了激活了旧砂中残留的水玻璃,恢复了残留水玻璃的粘结性能,再生砂强度等性能超过了新砂,因此,可以减少再生砂生产时的水玻璃加入量,旧砂再生回用率可以达到85~95%;且当多次再生时,再生液会减少,如不补充洗砂用水,再生砂初强度低于新砂,而终强度和残留强度高于新砂,洗砂时需适当补充水分。当前第1页1 2 3