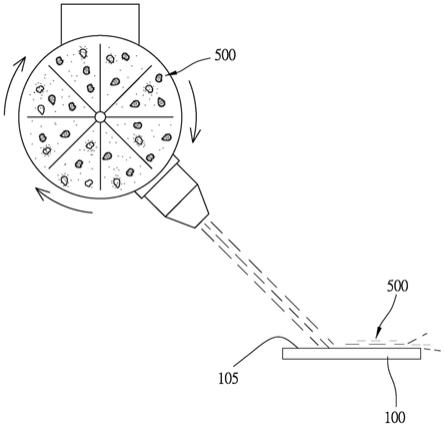
1.本发明涉及一种半导体基板的表面处理技术,具体而言涉及一种半导体晶圆的物理干式表面处理方法及其表面处理用组成物,藉以能提升半导体基板表面的去除、抛光或减薄的效率,不仅快速安全且不易破片,同时在作业时不需使用化学液体或水、减少环境破坏,也可提升人员在操作时的安全。
背景技术:2.由于半导体装置上的集成电路〔integrated circuit〕技术发展快速且成熟,使得半导体产业成为蓬勃发展的产业之一。而半导体晶圆片是藉由对硅晶圆等基板进行成膜、曝光、蚀刻、研磨、洗净等多数步骤来制造。一般晶圆厂在大量生产时,需要使用多达三成、甚至以上数量的监控与测试晶圆〔monitor wafer、dummy wafer〕,若生产特殊应用集成电路时,甚至需要使用超过四成的监控与测试晶圆。早期测试晶圆在使用过后都是与淘汰的晶圆一起丢弃,产生了很多有毒工业废弃物;后来随着产业快速发展,晶圆材料尺寸变大,而且成本也越来越高,而逐渐发展出再生晶圆〔reclaimed wafer〕产业,其是将使用过的测试晶圆及淘汰晶圆上面的镀膜〔如绝缘薄膜或金属薄膜〕等线路物经过研磨、抛光等程序后,可不断重复再生利用。
3.而现有半导体晶圆的再生晶圆方法,主要是用湿式蚀刻〔wet etching〕技术去除晶圆表面的镀膜,如sio2、si3n4等绝缘镀膜,或是al、cu、ti等金属镀膜,并在将半导体晶圆表面予以磨光(lapping)及/或研磨(grinding)之后,进行化学机械研磨〔chemical mechanical polish,cmp〕,或直接进行化学机械研磨,而予平坦化,最后再使晶圆表面达到原始的状态后,让半导体晶圆片在预定厚度的以内,还可重复再生使用。
4.然针对不同镀膜的组成成份,必须使用不同的腐蚀性液体〔如氢氟酸〕对再生晶圆进行蚀刻,因此增加了蚀刻制程的复杂性,且过程中也会产生有毒气体,而造成制程上安全性的问题。另外,腐蚀性液体对于不同的镀膜组成所产生的腐蚀效率亦不相同,而导致再生晶圆表面厚度不均的问题,且经过湿式蚀刻的再生晶圆表面,容易因腐蚀液所溶解的金属离子或杂质附着而将污染物残留在再生晶圆表面,如此一来必须先将残留的污染物去除后才可进行后续的制程,对制造成本亦是一笔不小的负担。除此之外化学机械研磨也会产生废研磨液、研磨污泥等废弃物的产生,这些化学废弃物会危害我们的环境,而为了生态环境不受有毒的化学废液的破坏,于蚀刻或化学机械研磨过程中所产生的化学废液不可任意排放,因此制造厂商需要负担化学废液回收处理工作、设备及人力费用的成本再支出。
5.虽然曾有业者提出如中国台湾专利公告第m320168号、第m324847号及公告第200524031号等专利申请使用干式喷砂方式来去除晶圆表面的镀膜,来减少蚀刻或研磨去除镀膜所造成的问题,但如图1所示,其喷砂是使用如天然钻石、人造钻石、碳化钨、碳化硼等硬质材来做为研磨材料,其粒径约为1um~10um,然因喷砂材料(20)的冲击速度快,且冲击晶圆(10)的表面(15)时为短暂的点击状态,而于晶圆(10)内形成内应力,其不仅会对晶圆(10)产生损伤,导致良率下降,且如晶圆(10)较薄,则可能发生裂痕或破裂的状况,再者
其因不具研磨效果,故其去除镀膜后的晶圆(10)的表面(15)较不平整〔如图2所示〕,且可能有残留金属镀膜(a),故仍需于后续以化学机械研磨进行平坦化。
6.再者,随着内存和功率装置等应用朝着更小尺寸、更高性能的方向发展,且更薄的晶圆能够带来众多好处,包括超薄的封装,以及由此带来更小的尺寸外形,还包括改善的电气性能和更好的散热性能。因此对晶圆减薄的薄化制程需求也日益增长。而晶圆的薄化制程方法与前述再生晶圆的方法相似,大都会使用到化学机械研磨技术来进行减薄,因此其面临的成本及废液处理问题也就相当。
7.换言之,现行的半体导晶圆在进行去除、抛光或减薄等表面处理时技术上并无法完全满足需求,分别存在有制程复杂,且去除、抛光或减薄速度太慢,以及制程设备成本太高,以及破损率高良率低的问题,同时更会延伸出大量废液处理的困扰,而如何解决前述的问题是本领域迫切需要的,亦为本发明所欲解决的技术课题。
8.于是,本发明人针对现有再生晶圆所面临的问题深入探讨,并藉由近年来技术发展的需求,经不断努力的改良与试作,终于成功开发出一种半导体晶圆的物理干式表面处理方法及其表面处理用组成物,藉以克服现有因使用蚀刻或研磨来去除镀膜,节省制程工序及时间所造成的缺点与不便。
技术实现要素:9.因此,本发明的主要目的在于提供一种半导体晶圆的物理干式表面处理方法,藉以能简化再生晶圆的表面处理制程,并可提高表面加工精度,以及改善表面粗糙度,且提升表面处理的速度。
10.又,本发明的次一主要目的在于提供一种半导体晶圆的物理干式表面处理方法,其能并减少化学药品的污染,不仅可节省废液处理的程序与设备,从而使再生晶圆制程可以更为环保及安全。
11.再者,本发明的另一主要目的在于提供一种半导体晶圆的表面处理用组成物,其能提供研磨时较佳的缓压作用,可以减少再生晶圆于去除表面时的变质层,从而减少晶圆裂损,进一步可以提高整体制程的良率。
12.基于此,本发明主要是通过下列的技术手段,来具体实现前述的目的及功效:
13.本发明的一种半导体晶圆的表面处理用组成物,该表面处理用组成物包含有系列软质弹性载体及系列硬质微粒子,其中所述软质弹性载体是选自具沾黏性的弹性材料所制成,且所述软质弹性载体的粒径为10um~150um,又其中所述硬质微粒子的粒径为国际筛网规格〔mesh〕的目数1500~30000;
14.使得所述硬质微粒子在高速旋转离心力及喷出时可沾黏附着于所述软质弹性载体的表面,供通过一喷射设备喷击去除一半导体晶圆的一待处理表面。
15.其中,优选的,所述软质弹性载体选自塑料、橡胶、硅胶为基材的原料所制成的软质弹性复合物。
16.其中,优选的,所述硬质微粒子选自天然钻石、人造钻石或其混合物。
17.其中,优选的,所述硬质微粒子选自氮化硼、碳化硼或其混合物。
18.其中,优选的,所述硬质微粒子选自碳化钨或其混合物。
19.一种半导体晶圆的物理干式表面处理方法,包含一以特定喷射角度将该表面处理
用组合物喷击去除一半导体晶圆的待处理表面的步骤来进行,其中该表面处理用组成物为以上任一项所述者;
20.使得该表面处理用组成物与半导体晶圆的待处理表面高速接触时,其中软质弹性载体会产生变形且于待处理表面形成高速磨擦滑动,而由于软质弹性载体表面沾黏吸附有硬质微粒子可相对该待处理表面产生研磨效果,进而生成去除或抛光该半导体晶圆待处理表面的效果。
21.其中,优选的,该特定夹角为2度至60度。
22.其中,优选的,该表面处理用组成物喷出的速度为50m/s~200m/s。
23.其中,优选的,该表面处理方法选择进行二道或二道以上,且每道喷击表面处理步骤的表面处理用组成物硬质微粒子的粒径不同,供依序进行粗去除、细去除及精抛光的处理步骤。
24.其中,优选的,该半导体晶圆是蓝宝石基板、玻璃基板或石英基板。
25.藉此,通过上述技术手段的具体实现,本发明不仅制程极为简单、且速度快,且可提高加工精度,同时可以不需使用腐蚀性液体,以避免过程中产生有毒气体,大幅提升制程的安全性,同时再者也不会有废研磨液、研磨污泥等废弃物的产生,减少对生态环境的破坏,进而减少化学废液回收处理及所需的设备人力的成本支出,可大幅降低其制程成本,以提高其附加价值,进一步可提高其经济效益。
26.为使本领域技术人员能进一步了解本发明的构成、特征及其他目的,以下乃举本发明的较佳实施例,并配合图式详细说明如后,同时让熟悉该项技术领域者能够具体实施。
附图说明
27.图1为传统以喷砂技术进行晶圆表面镀膜去除制程的动作示意图;
28.图2为传统以喷砂技术进行晶圆表面镀膜去除后的晶圆表面放大示意图,其中(a)为局部再放大示意图,说明其粗糙度;
29.图3为本发明半导体晶圆的表面处理用组成物的混成示意图,其中(a)为表面处理用组成物的混合示意图,而(b)为单颗表面处理用组成物的放大示意图;
30.图4为本发明半导体晶圆的物理干式表面处理方法的喷磨架构示意图;
31.图5为本发明半导体晶圆的物理干式表面处理方法的表面处理用组成物于晶圆表面喷磨的动作示意图,其中(a)为单颗表面处理用组成物与晶圆表面滑磨的状态;
32.图6为本发明半导体晶圆的表面处理用组成物于晶圆表面喷磨后的状态示意图。
33.符号说明:
34.10:晶圆
35.15:表面
36.20:喷砂
37.a:残留金属镀膜
38.100:半导体晶圆
39.105:待处理表面
40.500:表面处理用组成物
41.50:软质弹性载体
42.55:硬质微粒子
43.60:残屑
具体实施方式
44.本发明是一种半导体晶圆的物理干式表面处理方法及其表面处理用组成物,随附图例示本发明的具体实施例及其构件中,所有关于前与后、左与右、顶部与底部、上部与下部、以及水平与垂直的参考,仅用于方便进行描述,并非限制本发明,亦非将其构件限制于任何位置或空间方向。图示与说明书中所指定的尺寸,当可在不离开本发明的申请专利范围内,根据本发明的具体实施例的设计与需求而进行变化。
45.本发明半导体晶圆的物理干式表面处理方法及其表面处理用组成物,则是如图3的(a)、(b),该半导体晶圆的表面处理用组成物500是由系列软质弹性载体50及系列硬质微粒子55混合而成,其中所述软质弹性载体50选自具沾黏性的软质弹性材料所制成,如塑料、橡胶或硅胶为基材的原料所制成的软质弹性复合物,所述软质弹性载体50的粒径为10um~150um,而所述硬质微粒子55可以选自如钻石、氮化硼、碳化钨等硬质材料,且所述硬质微粒子55的粒径为国际筛网规格〔mesh〕的目数1500~30000,再者所述硬质微粒子55在高速旋转离心力及高速喷出时可沾黏附着于所述软质弹性载体50)的表面中〔如图3的(b)所示〕,供喷射设备高速喷出;
46.而本发明半导体晶圆的物理干式表面处理方法是如图3、4所示,本发明的特色为该表面处理包含一以特定喷射角度将该表面处理用组合物喷击去除一半导体晶圆100的待处理表面105的步骤来进行,其中该表面处理用组成物500)包含表面沾黏有硬质微粒子55的软质弹性载体50,而该特定夹角为2度至60度,且该表面处理用组成物500喷出的速度为50m/s~200m/s,使得该表面处理用组成物500与半导体晶圆100的待处理表面105高速接触时,则如图5所示,其中软质弹性载体50会产生变形且于待处理表面105形成高速磨擦滑动,而由于表面处理用组成物500的软质弹性载体50表面沾黏吸附有硬质微粒子55,使得其可相对该半导体晶圆100的待处理表面105产生研磨效果,进而生成去除该半导体晶圆100待处理表面105的镀膜或该待处理抛光表面105的作用;
47.而根据某些实施例,本发明可依据表面处理用组成物500选用不同材质〔如钻石、氮化硼、碳化钨或其混合物〕或不同粒径〔如目数5000、10000或15000〕的硬质微粒子55,而可用于去除半导体晶圆100的待处理表面105上不同材质的镀膜,且进一步可达到半导体晶圆100减薄的薄化作用〔如选用目数10000左右的硬质微粒子55〕,又或进行半导体晶圆100待处理表面105的平坦化或镜面抛光〔如选用目数20000的硬质微粒子55〕。
48.再者,另根据某些实施例,本发明进一步可依据该半导体晶圆100的待处理表面105的状态如半导体晶圆100无镀膜、有镀膜〔如绝缘镀膜或金属镀膜〕,而选择进行二道或二道以上的喷击表面处理步骤,且每道喷击表面处理步骤的表面处理用组成物500硬质微粒子55的粒径不同,又或依据厂商对半导体晶圆100的待处理表面105粗细要求不同,而依序进行粗去除、细去除及精抛光等多道处理步骤,以满足加工速度及加工精度的要求。当然本发明的方法也可依据半导体晶圆100的制程需求组合现有蚀刻、化学机械研磨或清洗等典型制程的前后搭配应用。
49.又,根据某些实施例,本发明的半导体晶圆100进一步可以是蓝宝石基板、玻璃基
板或石英基板,用于去除镀膜或抛光表面。
50.而由上述可知,本发明半导体晶圆的物理干式表面处理方法的特色在于,如图4、5以及6所示,其利用包含有软质弹性载体50与硬质微粒子55的表面处理用组成物对半导体晶圆100的待处理表面105进行喷击去除的动作,当表面处理用组成物500的软质弹性载体50与待处理表面105高速接触时,软质弹性载体50本身会产生形变且于工件表面产生磨擦滑动〔如图5所示〕,并利用该磨擦动使软质弹性载体50表面的硬质微粒子55进行去除或抛光的作用,使其表面残屑60被刮除〔如图5的(a)所示〕,如此相较于现有以蚀刻或化学机械研磨的技术而言,不仅制程极为简单、且速度快,同时可以不需使用腐蚀性液体〔如氢氟酸〕,以避免过程中产生有毒气体,大幅提升制程的安全性。再者也不会有废研磨液、研磨污泥等废弃物的产生,减少对生态环境的破坏,进而减少化学废液回收处理所需的设备及人力的成本支出,使得本发明具有能简化再生晶圆的表面处理制程,并可提高加工精细度,且提高表面处理的速度之效。
51.同时,其能并减少化学药品的污染,不仅可节省废液处理的程序与设备,从而使再生晶圆制程可以更为环保及安全。且能减少半导体晶圆100于再生时的变质层,从而提高整体制程的良率。