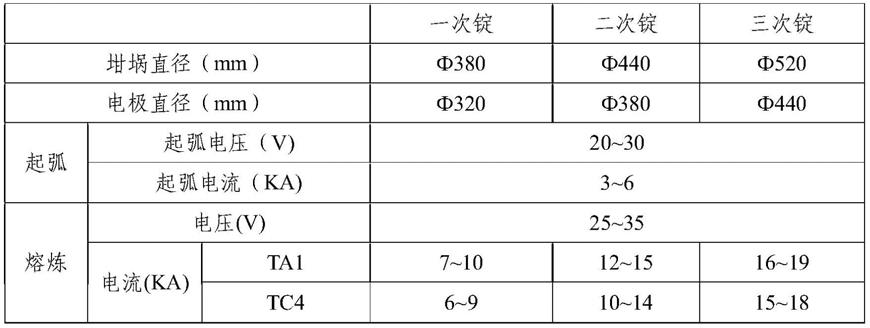
[0001]
本发明属于金属冶炼技术领域,具体涉及一种用真空自耗电弧炉回收重熔钛或钛合金残料的方法。
背景技术:[0002]
钛及钛合金具有比强度高、耐腐蚀等优异性能,被广泛应用于航空、航天、舰船、兵器、化工、医疗等领域。由于钛材的特殊性,其零件的成材率仅为50~60%,产生大量钛及钛合金残料,因此对于钛及钛合金残料回收利用方法的研究具有较大的社会和经济效益。
[0003]
真空自耗电弧炉(var)生产钛及钛合金铸锭是目前工业化应用范围最广且规模最大的一种生产方法。该炉有一个结晶器,结晶器装入水冷的外套里,并与熔炼电源的正极相接。电源的负极与活塞即“拉杆”连接,该拉杆通过滑动的真空密封进入炉内。待熔炼的电极夹紧在控制活塞的机座上,并且在炉膛抽空以后,下降电极与在结晶器底部的同样材料的金属垫料触发电弧。当电极由于输人功率而熔化时,就可通过液压控制系统下降活塞,以便保持电极同由此而形成的熔池之间的距离不变。当熔炼继续进行时,在结晶器里就逐渐地形成了一支新的锭料。此种熔炼方法可以有效的去除可挥发性杂质和气体,可经2~3次熔炼获得成分均匀且纯净度高的钛及钛合金铸锭。
[0004]
钛及钛合金残料主要来自铸锭锯切的冒口、半成品坯料的头、尾部、切边,及各工序中产生的不合格品,残料的大小不一,形状不同。以往捆绑式制作电极的方法在熔炼过程中存在掉块等不安全因素,残料和海绵钛混合经模具压制电极的方法生产工序长,模具制造成本较高且不能满足规模化生产的需要。
技术实现要素:[0005]
针对现有技术在回收重熔钛合金中存在的问题,本发明提供一种用真空自耗电弧炉回收重熔钛或钛合金残料的方法,包括如下步骤:
[0006]
1)将钛或钛合金残料进行回收;
[0007]
2)对所述钛或钛合金残料进行表面清洁,得可重熔残料;
[0008]
3)利用氩气保护的等离子弧焊接方式,将所述可重熔残料焊接成自耗电极,焊接的过程中,使用设有焊点保护区的焊接保护罩进行焊接,保证焊点为银白色或浅黄色;
[0009]
4)将所述自耗电极装入真空自耗电弧炉中进行熔炼;
[0010]
所述设有焊点保护区的焊接保护罩的结构为,所述焊接保护罩上设有焊点保护区、氩气入口和氩气出口,所述焊点保护区为设于所述保护罩表面的凹槽,所述氩气出口设于所述凹槽内。
[0011]
对钛或钛合金进行回收重熔过程中的主要技术问题是回收的重利用的钛残料的大小不一,形状不同,现有技术中以捆绑式或残料与海绵钛混合经模具压制电极的过程存在各种弊端,本申请提出利用氩气保护的等离子弧焊接方式将所述可重熔残料制备成自耗电极,但是在焊接的过程中焊点处易氧化,这会导致后续重新熔炼后无法得到组成均一理
想的材料,本申请针对上述问题,采用改良的焊接保护罩对其进行焊接,可防止钛或钛合金在焊接过程中被氧化,有利于重新熔炼得到性能良好的钛合金。
[0012]
优选的,在所述真空自耗电弧炉中进行熔炼的过程中,熔炼的次数不少于2次,每次熔炼的真空度均应保持在6.7pa以下,漏气率小于1.8pa/min。此真空度和漏气率参数能够保证炉内良好的真空度,保证所熔炼铸锭成分的符合国标要求。
[0013]
优选的,在所述真空自耗电弧炉中进行熔炼的过程中,控制起弧电压为20~30v,起弧电流为3~6ka;熔炼的过程中控制电压为25~35v。此参数可保证起弧阶段熔池内部的稳定性,减少因激冷产生的底部缺陷,最大限度的保证操作安全。
[0014]
优选的,针对于ta1,一次锭熔炼时电极直径为310~330mm,熔炼的电流为7~10ka;二次锭熔炼时电极直径为370~390mm,电流为12~15ka,三次锭熔炼时电极直径为430~450mm,电流为16~19ka;
[0015]
优选的,针对于tc4,一次锭熔炼时电极直径为310~330mm,熔炼的电流为6~9ka;二次锭熔炼时电极直径为370~390mm,电流为10~14ka,三次锭熔炼时电极直径为430~450mm,电流为15~18ka。使用如上参数进行铸锭熔炼得到的铸锭成分均一性良好,纯净性程度较高。
[0016]
上述两种金属的具体熔炼的工艺参数见表1:
[0017]
表1熔炼工艺参数
[0018][0019]
优选的,在所述真空自耗电弧炉中进行熔炼的过程中的补缩操作为:直径440mm铸锭及直径520mm铸锭参考剩余电极重量为100~150kg时进入补缩;每次降低0.5~1ka,在10~30分钟内将电流降至6~8ka,之后每次降低电流时都要增加熔化时间;直径440mm铸锭补缩过程应在1.5~2.0小时内完成,直径520mm铸锭补缩过程应在2~2.5小时内完成。成品熔炼末期使用如上参数进行补缩操作可降低铸锭的缩孔深度,提高铸锭成材率。
[0020]
优选的,利用氩气保护的等离子弧焊接方式焊接的过程中,控制焊机的电压35~40v,电流300~350a,氩气流量4~15l/min。使用如上参数进行电极焊接能够保证焊接过程中焊点呈现白色和浅黄色,降低因焊点氧化带入铸锭中氧化物夹杂风险。
[0021]
优选的,所述保护罩为中空的壳体,所述氩气入口设于所述壳体的外壁。
[0022]
优选的,所述凹槽为长方体,所述氩气出口分布于所述凹槽的侧壁和底面。上述结构有利于对焊点提供全面的氩气保护。
[0023]
优选的,对钛或钛合金残料进行回收的具体操作为:根据残料的牌号、炉号、来源不同进行分类回收。
[0024]
优选的,对所述钛或钛合金残料进行表面清洁的具体操作为,将所述待重熔的残料置于酸性或碱性溶液中浸泡,去除残料表面的氧化皮,再经打磨、喷砂、抛丸去除残料表面残留的氧化物;然后将氧化物处理完毕的残料置于清水或含有一定浓度的清洗剂溶液中进行清洗,除去表面油污或其他异物;最后将清理干净的残料放置于烘干机中进行烘干或自然晾干。
[0025]
本发明具有如下有益效果:
[0026]
1)本发明可将钛及钛合金残料进行100%回收利用,通过var生产出成分均一性良好,洁净度高的合格铸锭。实现钛及钛合金残料的循环再利用,减少资源浪费并提高经济效益。
[0027]
2)本发明的方法操作简单,成本低,有利于进行大规模地工业化推广和应用。
附图说明
[0028]
图1为采用氩气保护的等离子弧焊接方式将处理完毕且合格的残料制备成的自耗电极;
[0029]
图2经本发明方法熔炼得到表面质量良好的成品铸锭;
[0030]
图3为本发明所述焊接罩的结构示意图;
[0031]
图4为不使用改良保护罩焊接电极生产铸锭锻坯金相图;
[0032]
图5为使用改良保护罩焊接电极生产铸锭锻坯金相图。
具体实施方式
[0033]
以下实施例用于说明本发明,但不用来限制本发明的范围。
[0034]
下述两种牌号的铸锭具体熔炼工艺参数见表1:
[0035]
表1熔炼工艺参数
[0036][0037]
实施例1
[0038]
本实施例涉及ta1残料重熔制备ф440mm-1080kg铸锭的方法:
[0039]
将同一牌号的合金铸锭冒口、坯料料头及不合格棒材等进行酸碱洗、喷砂、抛丸、清洗后获得洁净的残料,将洁净的残料码放在固定工装中,利用氩气保护的等离子弧焊接方式将残料焊接成ф320mm左右的自耗电极,根据表1中的工艺参数经var两次熔炼得到ф440mm-1080kg铸锭,其参数具体为起弧电压为25v,起弧电流为4.5ka,熔炼过程中电压为28~29v,一次熔炼的电流为8ka。二次熔炼的电流为13ka。
[0040]
补缩的具体操作为二次熔炼末期电极剩余110kg时进行补缩,每次降低0.6ka,在20分钟内将电流降至6~8ka,之后每次降低电流时都要增加10min熔化时间;补缩操作完成时间为105分钟。
[0041]
重熔完成后,对铸锭头部、中部、尾部三处的化学成分进行检测,与国标中要求成分范围对比结果如表2所示,结果表明使用此发明方法得到的铸锭满足标准要求且成分较为均匀。
[0042]
表2新锭成分与国标范围对比
[0043][0044]
由上表可知,本发明得到的铸锭的成分可达到国标的要求,甚至要远远地优于国标,可直接进行再利用。
[0045]
实施例2
[0046]
tc4(ti-6al-4v)残料重熔制备ф520mm-1550kg铸锭的方法:将同一牌号的合金铸锭冒口、坯料料头及不合格棒材等进行酸碱洗、喷砂、抛丸、清洗后获得洁净的残料,将洁净的残料码放在固定工装中,利用氩气保护的等离子弧焊接方式将残料焊接成ф320mm左右的自耗电极,根据表1中的工艺参数通过var三次熔炼得到ф520mm-1550kg铸锭。起弧电压为25v,起弧电流为4.5ka,熔炼过程中电压为28~29v,一次熔炼的电流为7.5ka。二次熔炼的电流为12ka。三次熔炼电流为14ka。
[0047]
补缩的具体操作为三次熔炼末期电极剩余110kg时进行补缩,每次降低0.8ka,在25分钟内将电流降至6ka,之后每次降低电流时都要增加10分钟熔化时间;补缩操作完成时间为155分钟。
[0048]
铸锭头部、中部、尾部三处的化学成分与名义成分对比结果如表3所示,结果表明使用此发明方法得到的铸锭满足标准要求且成分较为均匀。
[0049]
表3新锭成分与国标范围对比
[0050][0051]
由上表可知,本发明得到的铸锭的成分可达到国标的要求,甚至要远远地优于国标,可直接进行再利用。
[0052]
对比例1
[0053]
与实施例相比,其区别在于,焊接的过程中不使用改良的保护罩,焊接点由于被氧
化发蓝,甚至焊点出现白色粉末状物质造成严重氧化,电极入炉熔炼后氧化物进入熔池,增加铸锭低密夹杂风险。如下图4和图5所示。图4为不使用改良保护罩焊接电极生产铸锭锻坯金相图,图5为使用改良保护罩焊接电极生产铸锭锻坯金相图。
[0054]
对比例2
[0055]
与实施例1相比,所述重熔过程中的工艺参数不同,具体为为起弧电压为25v,起弧电流为4.5ka,熔炼过程中电压为28~29v,一次熔炼的电流为6ka。二次熔炼的电流为11ka。
[0056]
补缩工艺参数不同,具体操作为二次熔炼末期电极剩余103kg时进行补缩,每次降低0.6ka,在20分钟内将电流降至6~8ka,之后每次降低电流时都要增加10min熔化时间;补缩操作完成时间为108分钟。
[0057]
铸锭头部、中部、尾部三处的化学成分与名义成分对比结果如表4所示,结果表明此工艺参数得到的铸锭成分虽满足标准要求但成分均一性较差。
[0058]
表4新锭成分与国标范围对比
[0059][0060]
对比例3
[0061]
与实施例1相比,所述重熔过程中的工艺参数不同,具体为所述重熔过程中的工艺参数为起弧电压为25v,起弧电流为4.5ka,熔炼过程中电压为28~29v,一次熔炼的电流为11ka。二次熔炼的电流为16ka。
[0062]
补缩工艺参数不同,二次熔炼末期电极剩余100kg时进行补缩,每次降低0.6ka,在20分钟内将电流降至6~8ka,之后每次降低电流时都要增加10min熔化时间;补缩操作完成时间为110分钟。铸锭头部、中部、尾部三处的化学成分与名义成分对比结果如表5所示,结果表明此工艺参数得到的铸锭成分虽满足标准要求但成分均一性较差。
[0063]
表5新锭成分与国标范围对比
[0064][0065]
虽然,上文中已经用一般性说明及具体实施方案对本发明作了详尽的描述,但在本发明基础上,可以对之作一些修改或改进,这对本领域技术人员而言是显而易见的。因此,在不偏离本发明精神的基础上所做的这些修改或改进,均属于本发明要求保护的范围。