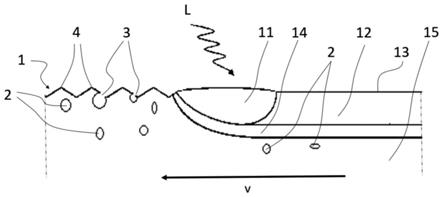
1.本发明涉及一种用于钟表的钟表部件以及一种用于这种部件的制造方法。本发明还涉及一种在这种部件的制造方法中使用的表面处理方法。本发明也涉及一种包括这种钟表部件的钟表。
背景技术:2.在钟表制造工业中,部件(特别是用于钟表装饰功能)的制造需要遵守许多限制条件。首先,由于其预期的功能性,部件必须遵守特定的机械限制条件。此外,部件必须实现无可挑剔的美学外观。最后,通常期望提供一种特定的通常复杂的形状的钟表部件,以实现新的整体美学效果和/或有效地满足特定的功能性。此外,总是优选提出一种解决方案,其允许以与大规模生产和销售兼容的方式制造这种钟表部件,包括通过使用常规铸造技术难以获得的合金成分。最后,特别是对于高密度的贵金属而言,获得较轻部件通常也是有利的。
3.最后,现有解决方案试图在上述所有要求之间达成折衷。它们通常基于金属材料或金属合金的使用,特别是基于使用传统冶金的贵金属的使用;或者基于陶瓷的使用。然而,需要改进现有解决方案以更好地满足上述各种要求。
4.因此,本发明的总体目的是提出一种用于制造钟表部件的解决方案,其在上述所有要求之间达成改进的折衷。
5.更准确地,本发明的第一目的是提出一种用于制造钟表部件的灵活解决方案,其能够形成复杂的形状,同时保持与最多不同材料的使用相兼容。
6.本发明的第二目的是提出一种用于制造具有无可挑剔的美学外观的钟表部件的解决方案。
7.本发明的第三目的是提出一种用于制造与大规模生产相兼容的钟表部件的解决方案。
8.本发明的第四目的是提出一种用于制造轻钟表部件的解决方案。
技术实现要素:9.为此,本发明基于一种表面处理方法,用于由包含通过粉末冶金或增材制造技术获得的诸如孔和/或析出物和/或条纹之类的不规则结构的部件制造金属基和/或金属陶瓷基钟表部件,其中,表面处理方法包括通过在部件的表面区上进行表面重熔来改善部件的表面光洁度的步骤。然后,所述表面处理方法包括对所述部件的表面区的表面进行精加工的步骤,该精加工的步骤在通过表面重熔来改善部件的表面光洁度的步骤之后执行。
10.本发明还涉及一种用于钟表的金属基和/或金属陶瓷基钟表部件,其包括具有诸如孔和/或析出物之类的不规则结构的芯部,其中,所述金属基和/或金属陶瓷基钟表部件由于涉及表面重熔的表面处理而包括具有与所述芯部相比更少的不规则结构的表面区。所述表面区可以包括与所述芯部相比更低的孔隙率。本发明还涉及钟表,特别是手表。
11.本发明由权利要求更精确地限定。
附图说明
12.参考附图,以下以非限制性方式提供的具体实施方式的描述将详细阐明发明的这些目的、特征和优点,在附图中:
13.图1示意性地示出了根据本发明的实施方式的通过lsm(激光表面熔化)方法来改善部件的表面的步骤的实施。
14.图2和图3示出了材料的吸收率和反射率相对于特定波长变化的若干实例。
15.图4示出了经过不同表面处理的三个白金样品的反射率。
16.图5示意性地示出了根据本发明的实施方式的变型通过lsm方法来改善表面光洁度的步骤的实施。
17.图6示出了以示例的方式在白金中部上实施的本发明。
18.图7示出了以示例的方式在316l型钢基板上实施的本发明。
19.图8通过图7的316l型钢基板的厚度的放大图示出了本发明。
20.图9示出了在5级钛基板上实施本发明的实例。
21.图10a示出了根据本发明的实施方式处理的图9的5级钛基板的表面区。
22.图10b示出了与图10a类似但未根据本发明的实施方式进行处理的5级钛基板的表面区。
具体实施方式
23.本发明基于第一选择,在于使用粉末冶金或增材制造技术作为钟表部件的制造方法中的第一步骤。这种选择具有第一优点,允许形成复杂多样的形状,包括例如传统冶金方法无法实现的形状。另一方面,该第一选择还具有第二优点,允许使用多种材料,甚至是通过另一种传统方法无法获得的合金或元素的组合,例如某些与传统冶金学不相兼容的金属合金。因此,根据本发明的该第一选择使得能够部分地响应于本发明的目的。
24.然而,这些所选技术具有形成具有可见表面缺陷(如可见或可感知的诸如孔和/或析出物和/或条纹之类的不规则结构)的多孔且通常异质的部件的特定特征。因此,这些所选技术很难与钟表制造要求相一致。此外,很明显的是,通过使用诸如磨削、抛光、电化学抛光之类的常规精加工技术,即使不是不可能,也很难消除具有复杂形状的部件上的这些缺陷。因此,本发明包括一种表面处理,其实施改进通过所述粉末冶金或增材制造技术所获得的部件的步骤,以便最终将改进的制造方法限定为与所有钟表制造要求相兼容。
25.现在将详细说明根据本发明的实施方式的钟表部件的制造方法。
26.根据本发明的实施方式,在第一步骤中,根据已知的增材制造或粉末冶金方法来制备部件的坯件。该坯件的形状非常接近最终部件的最终形状。然而,在如下详细描述的表面改进步骤之前或之后,该坯件可以可选地经历诸如螺纹加工和/或重新加工之类的附加操作。因此,我们会错误地按部件指定将要经历如下所述的表面改进处理的任何部件或任何坯件(无论经过重新加工与否)。该部件能够由诸如不锈钢、铝合金、钛、金或银之类的金属制成。可替代地,该部件能够由金属陶瓷制成。在上面所考虑的那些之中,整个部件可以是相同的材料。可替代地,该部件能够包括不同材料的组合。“由某种材料制成的部件”是指包含至少50重量%的所述材料,实际上至少80重量%的所述材料的部件。
27.在粉末冶金中,粉末能够例如通过喷雾、磨削或这些技术的组合来获得。它们然后
能够例如通过冷压、热压、等静压和/或烧结而被压实。已知的粉末冶金方法包括金属注射成型(mim)法和放电等离子体烧结(sps)法。
28.已知的增材制造技术的实例包括:选择性激光熔化(slm)、直接金属激光烧结(dmls)、电子束熔化(ebm)、纳米颗粒喷射(npj)、金属粘合剂喷射、激光工程化净成形(lens)和电子束增材制造(ebam)。
29.如上所述,应用于金属或金属陶瓷的粉末冶金和增材技术能够获得具有各种几何形状的部件。粉末冶金和增材技术还提供了以下优点,其允许在相同部件内使用合金成分或元素的组合,或甚至不同材料的组合,这是常规技术无法合成的。例如,它们能够使用白金合金,其包含按重量计至少75%的元素au、13%~17%的元素cr、5%~10%的元素pd以及1%~5%的元素fe,因此该合金根据cie 1976l*a*b*模型的比色参数b*为小于10。
30.粉末冶金和增材技术还能够使用按重量计包含90%~98%的wc和2%~10%的镍的组合物或者18ct金与2~25%的tin的组合物。它们还能够制造由铝合金的芯部和316l不锈钢的外层组成的部件,或者其成分根据例如中部、角(horns)、壳带(case band)、表圈等的表面上的位置而变化的外层可以由不同的合金和/或金属陶瓷制成。这使得例如获得不同颜色的颜色梯度或并置或不同机械阻力成为可能。
31.然而,由这些技术所获得的部件由于它们是多孔的而均具有与相同材料的固体部件的密度相比更低的密度。结果,它们通常不具有令人满意的表面光洁度,以使其不能用于钟表制造的领域。实际上,它是由于这些技术的本质,例如孔、凸点、凹陷、析出物和/或条纹等形式的不规则结构在部件的表面上是可见的或至少可察觉的。孔隙率的分数以及缺陷的数量取决于所使用的材料和制造技术。然而,当前的技术都不允许生产完全无缺陷的部件。
32.然而,这些缺陷会对部件的外观,特别是对希望光滑的表面(例如镜面抛光的表面)产生负面影响。此外,在至少一个方向上维度大于或等于1μm(或甚至0.5μm)的孔、析出物和/或条纹特别令人讨厌,因为诸如喷丸处理、机械抛光和/或化学抛光或电化学抛光之类的表面精加工方法(surface finishing process)不能消除它们。实际上,直径高达500μm的孔和析出物会在抛光表面上露出,从而导致彗星尾巴、点蚀和其他美学缺陷。更一般而言,对于镜面抛光,已经可能会感觉到尺寸大于或等于0.5μm的诸如孔和/或析出物和/或条纹之类的不规则结构。结果是,通过上述技术获得的部件尽管具有优点但在其当前状态下仍不能令人满意地形成钟表部件,并且传统的精加工工艺不适合于可靠地去除其所有缺陷。
33.因此,本发明提出了消除根据上述第一步骤制造部件所产生的上述缺陷,并且实施包括改善部件表面光洁度的步骤(下文将对此进行详细说明)的表面处理方法。
34.根据一种实施方式,改善部件的表面光洁度的步骤涉及表面重熔,特别是通过激光,例如通过已知为激光表面熔化(lsm)的方法。可替代地,能量能够通过激光束、等离子束、电子或离子束或电弧而被提供给部件。例如,由ti
‑
6al
‑
4v材料制成的表面在10
‑1pa的氦气气氛中用电流为1~50ma、斑点尺寸为10~100μm且扫描速度为0.1~1m/s的60kv电子束进行处理。
35.通过表面重熔来改善部件的表面光洁度的步骤可以涉及使用其在激光束末端的截面具有基本上均匀的能量分布的激光。可替代地,它包括使用等离子束或电子束或离子束或电弧。
36.这些处理的共同特征是通过增加能量来诱导部件的表面重熔,从而消除部件的表面上的孔和/或析出物和/或条纹,同时对部件的整体密度影响很小。这些是仅作用于部件的表面区的处理。有利地,这些处理还能够同时减小零件的粗糙度。
37.更准确地说,使用lsm方法的激光处理基于电磁辐射与部件材料的相互作用。根据激光束的能量密度(即,每单位面积的能量)、其在部件表面上或附近的聚焦/散焦以及相互作用的持续时间,一部分能量被部件的表面区吸收。因此,加热该表面区中的部件材料直到材料熔化。
38.图1是通过lsm方法处理部件表面的示意图。部件1如上所述而形成,并且包括形成表面缺陷3的孔2和表面条纹4。激光l以一定的速度v(在图1中从右到左)在表面上移动,并且熔化表面区上的部件材料,从而形成液体浴11。因此,该方法有效地实现了部件1的表面区的表面重熔。孔和/或析出物在该浴11中被消除。结果是具有较高密度和较好质量的经处理的表面区12,其表面13具有少很多的缺陷(如果有的话)。该处理对部件的芯部15影响很小,因此在激光通过之后保留了初始的孔2。最后,在表面区12和芯部15之间的中间区14中,材料没有熔化,但是其结构在浴11的冷却和固化期间通过温度扩散而改变。
39.浴11的厚度基本上对应于表面区12的厚度,并且为10μm~1mm。优选地,该厚度大于或等于50μm,或甚至大于或等于100μm。再次优选地,该厚度小于或等于1000μm,或甚至小于或等于500μm,或甚至小于或等于200μm,或甚至小于或等于100μm。
40.在该lsm方法中,优化激光速度v,以获得具有预定尺寸的浴11并确保该材料的受控固化。因此,通过该表面重熔处理使部件的表面区12致密化。中间区14是受到表面重熔处理影响的区:材料的微观结构可能发生变化,即使材料尚未完全熔化。
41.激光的能量和波长优选地适合于待处理的部件的性质,特别适合于其组成材料的吸收率和电导率,并且适合于待处理的物体的几何形状。如果激光能量不足,则局部温度将不足以获得合适的液体浴,并且不会消除所有可察觉的缺陷。如果液体浴的尺寸和/或固化之前在液相中的持续时间不足,则孔不能适当地升至表面,和/或没有可察觉的孔的层的厚度不能令人满意。此外,如果吸收的能量太高,则经处理的部件的几何形状可能会改变,从而可能在液体浴与材料(小孔)的界面处产生较大的变形和/或生成更多的孔,这在随后的抛光期间可能会被发现。此外,一旦材料变成液体,吸收率就会大大提高,如果光束能量过高,则吸收率也会提高。
42.因此,通过藉由激光器的功率分布和/或扫描和/或筛选速度来控制液体浴的温度梯度及其冷却速度,可以获得期望的结果并且消除经处理的表面区12中的重熔层的孔和可能的一些夹杂物。
43.根据该实施方式,扫描速度被选择成低于lsm方法通常使用的扫描速度,例如比通常使用的扫描速度低至少10倍,其为500~2000mm/s,从而允许孔迁移到表面。最后,功率、时空功率分布、激光扫描速度和筛选相对于材料和激光波长的变化能被优化,以限定液体浴的几何形状,从而限定经处理的表面区的厚度,而对部件的几何形状影响最小。
44.举例来说,使用了2kw功率的型激光器,其具有光学器件和带有ilt喷嘴的3
×
3方形斑点。也可以使用其他类似设备,尤其是红色或红外激光器,例如co2激光器。可替代地,也可以使用蓝色、绿色、uv等激光器。
45.光束聚焦和均匀化有利地根据特别有利的“顶帽”型空间功率分布进行调节。“顶
帽”型光束是其截面末端具有以下特定特征的光束:所述截面的任何点具有相同的能量。换句话说,在激光束末端的截面具有基本均匀的能量分布。另外,根据获得所需尺寸的液体浴并控制液体浴的冷却速度所需的能量来设定激光的速度和筛选。最后,选择激光器的功率以获得深度等于或稍大于由期望的致密化的表面区12形成的层的厚度的液体浴。方法的这种优化,特别是激光的起始点、扫描图案、扫描速度、通过次数等的优化能够消除材料中存在的缺陷并且限制或甚至完全防止激光产生新的缺陷,例如,变形、扭曲、飞溅等。
46.有利地,这种优化考虑了待处理部件的材料和形状。再次有利地,激光器参数也适合于部件的几何形状和/或表面光洁度和/或组成。能够调节速度和/或功率和/或通过次数和/或筛选,以考虑部件的特定几何形状或组成。可替代地,能够选择具有适合于待处理材料的特定反射率的波长的激光器,例如对于金或银,分别用于波长小于或等于500nm或者小于或等于350nm的激光器。
47.有利地,可以例如通过温度受控的支架在表面上或整体上对部件进行回火或冷却,以便控制固化方向。有利地,条件被选择成促进与经处理部件的外表面基本上垂直的晶粒取向。
48.在一变型中,在激光穿过期间或之后或在整个方法过程中,通过使用流体或气体(例如,适应预定温度的流体流)来冷却部件。冷却能够在激光处理后直接进行,也可以延迟进行。
49.下表列出了如上详述的在注入保护气体下实施表面处理的ipg激光器的参数的一些实例。
[0050] p
激光器
[w]v[mm/min]气体焦距[mm]316l型钢1500w1000ar或n20白金1500w500ar05级钛1500w1000ar0
[0051]
在另一变型中,激光器参数被伺服控制以例如通过使用光学高温测定传感器或任何其他合适的传感器来测量部件的经处理表面的温度。
[0052]
最后,表面处理方法有利地包括对部件进行受控冷却的步骤,其包括:
[0053]
‑
使用液体或气体,或者
[0054]
‑
控制整个部件的温度,尤其是通过温度控制的支架,或
[0055]
‑
伺服控制对部件的处理表面的温度的测量。
[0056]
如上所述,激光与材料的相互作用是一个复杂的现象。正如所见,激光辐射与待处理部件的相互作用不仅受激光的性质和激光工艺参数所影响,而且还受部件的构成材料的特性(特别是其反射率、电导率和吸收率)所影响。材料在激光波长下的吸收率是最重要的参数之一。吸收率越低,“吸收”的激光能量越少,从而使材料熔化变得更加困难。
[0057]
本发明观察到,待处理材料的吸收率直接影响液体浴的尺寸以及所供应的必需能量。
[0058]
然而,在某些情况下,观察到了材料的吸收率不足以实现表面重熔的最佳实施。
[0059]
例如,当部件以钟表制造中典型的金属或合金(例如吸收率低的基于金、铜、银、铂、钯或铝的金属)制成时,可能会遇到困难。实际上,这些材料在高于700nm的波长下的吸收率使得它通常不允许与例如波长为1064nm的激光进行最佳交互作用。
[0060]
应注意,如上所述,提高激光器功率或相互作用时间来补偿材料的低吸收率可能导致表面的几何变形,例如由于部件的整体加热而导致的部件变形。这种效果对于形成钟表部件而言是不可接受的,因此并非总是能够提高激光器功率或更改任何其他激光器参数。
[0061]
图2和图3中的曲线图示出了材料的吸收率和反射率相对于特定波长变化的一些实例。
[0062]
图2和图3示出了,例如,对于波长为1064nm的yag激光器,铜(cu)的平均吸收为10%,而镍(ni)的平均吸收为28%。对于波长≈10μm的co2激光器,铜的平均吸收率为1%,而镍的平均吸收率为4%。
[0063]
根据本发明,考虑到了材料的给定波长的吸收率是极端表面现象,其本质上涉及第一原子层并且取决于第一原子层的性质和/或材料的表面光洁度。因此,表面光洁度的变化,例如,一定粗糙度和/或孔隙的存在,或部件的表面组成的变化,都可能影响方法。
[0064]
从上述观察得出的结论是,如果材料的吸收率低并且供应的能量可能无法使材料充分熔化(其例如显示为材料的不完全熔化或液体浴的尺寸不足),则可能无法充分去除部件表面上可察觉的孔和/或析出物和/或条纹。
[0065]
例如,对于白金合金(75.2w%au、13.9w%pd、3w%ag和7.w%cu,其反射率为约75%),已经观察到,对于用具有光学元件和带有ilt喷嘴的3
×
3方形斑点并且扫描速度为500mm/分钟的、2kw功率的型的1500w激光束处理而言,液体浴的尺寸并不是最佳的。
[0066]
为了响应于这些特定情况,该实施方式提出实施改变所述部件的表面区的吸收率的预备步骤。该预备步骤实现了部件表面的准备,以便降低反射率部分,从而受益于此后待处理部件的表面区的能量吸收。因此,该表面准备具有例如在将来的lsm处理期间改变该表面相对于激光束的性能的效果。可选地,能够预先执行表面吸收率映射,以关联激光器参数。可选地,将表面准备定位在表面处理方法的初始斑点,以便随后利用液体浴相对于固体表面的吸收率的变化。
[0067]
根据第一变型实施方式,表面准备的预备步骤包括以涂层形式沉积化学元素的步骤。相对于表面区的整体组成,这种沉积有利地提供小于或等于5at%的化学元素含量。表面涂层能够改变所述表面的化学性质和/或颜色。可替代地或同时地,表面涂层能够改变表面的拓扑结构。表面涂层能够例如通过pvd、cvd、ald、电镀、溶胶
‑
凝胶或sam进行沉积。该表面涂层的厚度能够大于或等于0.1nm,或甚至大于或等于0.5nm,或甚至大于或等于1nm;并且小于或等于10μm,或甚至小于或等于1μm。
[0068]
下表示出了根据该第一变型制成的一些实例(对于yag激光器,波长为1064nm)。
[0069][0070]
表面涂层能够通过物理气相沉积(pvd)法、化学气相沉积(cvd)法、原子层沉积(ald)法、电沉积,或溶胶
‑
凝胶方法,或自组装单层(sam)进行沉积。
[0071]
这种表面处理能够暂时或永久地改变表面的颜色。
[0072]
有利地,沉积涂层的厚度大于或等于0.1nm,或甚至大于或等于0.5nm,或甚至大于或等于1nm。另外,该厚度优选小于或等于10μm,或甚至小于或等于1μm。
[0073]
在所有情况下,涂层都会改变部件材料的初始吸收率,并且促进改善表面光洁度的未来步骤。应注意,这种涂层对部件材料的性能的影响仍可按比例忽略不计,并且特别是所添加的材料不会显著改变经处理的表面区的组成并且不会改变材料的机械性能。
[0074]
根据预备表面准备步骤的第二变型实施方式,能够对部件表面执行化学或电解蚀刻。例如,在金合金上进行硝基盐酸(王水)蚀刻会降低表面的反射率。通过该制备方法改性的层有利地具有0.1nm~10μm,或甚至0.5nm~1μm的厚度。
[0075]
根据预备表面制备步骤的第三变型实施方式,例如通过喷砂、喷珠、磨削、激光处理或任何其他合适的技术来执行表面的微纹理化,以降低表面的反射率。
[0076]
根据预备表面制备步骤的第四变型实施方式,可以通过执行氧化、氮化、硼化、氯化、氟化或硫化来改变部件材料的表面的初始固态吸收率。这样的制备可以例如提高表面的粗糙度或改变其颜色。对于该第四变型,改性层的厚度与上述涂层的厚度具有相同数量级。另外,化学元素的贡献仍然很低。实际上,化学元素的这种贡献保持小于或等于5at%的表面层(即,待处理的表面区)的总组成。
[0077]
举例来说,金合金基部件的表面能被氧化。例如,白金部件(75.0w%au、7.0w%pd、15.0w%cr和3.0w%fe)能够预先例如通过将其在空气炉中于700℃下加热15分钟来进行表面氧化。获得了约100nm的氧化层。
[0078]
对三个18克拉白金样品进行了测试,然后按照常规技术在砂纸p320(磨削表面)上对其进行抛光,然后在砂纸p4000(镜面抛光)上对其进行抛光。然后在空气中将镜面抛光的样品之一于700℃下氧化15分钟。然后,使用紫外可见红外分光光度计来测量三个样品的反射率。下表和图4详细列出了所获得的结果:
[0079]
波长表面光洁度估计的反射率1064nm镜面抛光的p4000≈75%1064nm磨削的r320≈70%1064nm镜面抛光的p4000+氧化≈25%
[0080]
这些测试表明,通过产生厚度为100nm的氧化层,氧化能够降低金属的反射率,从非氧化态的70%或75%反射率降低到小于30%的反射率。
[0081]
此外,似乎在白金合金物体(75.2w%au、13.9w%pd、3w%ag和7.9w%cu)的先前氧化表面上,1500w激光器以500mm/min消除了可察觉的孔而不影响该物体的几何形状,然而相同的处理对存在于非氧化材料上的孔产生不足的影响。有利地,在气体或气体的混合物,例如还原性气体或还原性气体的混合物(甚至弱还原性)的存在下执行处理,以便从贵合金的表面层中消除氧气。这能够不改变部件的最终组成。
[0082]
作为最终的变型,上述不同的制备变型能够彼此组合。
[0083]
该表面准备的预备步骤尽管是可选的,但是在任何情况下都为随后的改善部件的表面光洁度的步骤带来了非常有利的效果。实际上,吸收率的提高促进了从初始固态开始的表面重熔的初始化。此外,已经观察到,通过提高部件材料表面的初始吸收率,对于给定的激光器(例如1064nm激光器),可以获得与相同部件的未准备表面相比更深的熔化浴。因此,制备步骤提高了表面改进步骤的效率,并且将表面缺陷消除到适当的深度,而不会带来可能影响部件的几何形状的过多能量。
[0084]
图5示意性地示出了在通过涂覆或氧化进行的表面准备步骤的实施之后通过lsm方法来改善表面光洁度的步骤的实施。部件1包括表面涂层或氧化层16,其叠加到用于待处理的表面区12,该表面区12自身叠加到所述表面区12与部件的芯部15之间的中间区域14。在用激光器l进行处理期间,涂层或氧化层16和表面区12将同时熔化,被涂层或氧化层16促进,并且中间区14将受到热影响但不会熔化。应注意,在表面改善处理之后,涂层或氧化层16将消失,从而与表面区12融合。
[0085]
这种表面准备对于基于金、铜、银、铂、钯、铝或其合金的部件而言特别引人注目。
[0086]
自然地,在一变型的实施方式中,预备步骤能够仅施加在部件的表面的一部分上,尤其是在方法初始区上。
[0087]
如上所述,改善部件表面的步骤最终提供了以下两个有益效果:
[0088]
‑
它使多孔部件的表面与传统的精加工方法相兼容,从而进一步改善了表面光洁度的外观;
[0089]
‑
它使部件的表面相对于芯部而言致密化,从而提供了与由固体材料获得的部件相比,减轻部件的重量的可能性。
[0090]
优选地,根据本发明的实施方式的表面处理方法可以包括随后的精加工步骤。该步骤对于表面光洁度要求很高的装饰性钟表部件的制造而言特别引人注目。
[0091]
特别地,该精加工步骤包括:磨削、机加工或抛光该部件的所述表面区的表面的步骤。优选地,该精加工步骤包括抛光。
[0092]
应注意,不仅在制造期间,而且在维护操作之后,可能都需要多次抛光步骤以去除划痕。如果要最终达到镜面效果,则抛光也非常需要,这可能根据划痕的深度而需要去除最多约50μm甚至更大的厚度的材料。因此,部件的经处理表面区具有足够的厚度,以允许这样的后续精加工步骤。因此,可以根据期望的最终表面光洁度并且以与正常维护操作相兼容的方式来预限定该厚度。有利地,经处理的表面区的厚度可以大于或等于100μm,或甚至大于或等于200μm,或甚至大于或等于500μm,或甚至大于或等于1000μm。
[0093]
在所有情况下,如上所述的表面处理方法能够用于处理部件的整个表面,或仅处
理该表面的一部分。
[0094]
本发明已被描述在用于制造钟表部件的方法的上下文中,该方法包括:在实施通过第一步骤所获得的所述部件的表面处理的方法之前,通过粉末冶金制造法或增材制造法来制造金属基或金属陶瓷基部件的第一步骤。本发明也涉及这种表面处理方法。
[0095]
因此,如上所述的制造方法能够获得如上所述的有利钟表部件。这样的部件能够特别轻,能够采取复杂的形状,和/或能够基于元素或材料的原始组合。例如,该制造方法能够减轻钟表部件的重量(该钟表部件也可以通过现有的传统方法制造),同时保持相同外观的致密表层。因此,根据合金和/或部件的几何形状,能够获得明显的重量增加,例如增加了20%,或甚至30%,或甚至更多。
[0096]
因此,本发明涉及一种钟表部件。这种用于钟表的钟表部件是基于金属和/或金属陶瓷,并且包括:芯部,其包括通过粉末冶金制造法或增材制造法制造的诸如孔和/或析出物之类的不规则结构;并且包括表面区,其具有与所述芯部相比更少的不规则结构,由于它经历了涉及表面重熔的表面处理。
[0097]
根据本发明的实施方式,钟表部件的芯部和表面区具有大致相同的化学组成。
[0098]
因此,表面区可以具有与芯部相比更低的孔隙率。该表面区还可以含有与芯部析出物相比密度更低和/或尺寸更小的析出物。
[0099]
钟表部件的芯部可以是多孔的,其密度小于或等于99.5%,并且表面区可以具有与芯部相比严格更高的孔隙率和/或大于或等于99.9%的密度。密度代表相同固体材料的密度的百分比。
[0100]
该表面区可以具有小于或等于0.1%的尺寸大于0.5μm的孔隙率。
[0101]
该表面区可以延伸到大于或等于20μm,或甚至大于或等于50μm,或甚至大于或等于100μm的深度。因此,该深度对应于由表面区形成的层的厚度。它可被理解为最小值或平均值。
[0102]
该表面区可以延伸到小于或等于1000μm,或甚至小于或等于500μm,或甚至小于或等于200μm,或甚至小于或等于100μm的深度。
[0103]
部件的表面区可以仅在钟表部件的一部分表面上延伸或者在整个表面上延伸。
[0104]
钟表部件能够基于奥氏体不锈钢,或者基于钛合金,或者基于贵金属合金,或者基于铜合金。
[0105]
钟表部件能够基于具有低吸收率的小于或等于30%和/或高热导率的金属(如au、al、cu、pt、pd中的金属),及其合金。
[0106]
钟表部件可以是中部(middle)、后盘(back plate)、表圈、表冠、表链、表扣、表针或嵌花(applique)。
[0107]
本发明还涉及包括至少一种如上所述的钟表部件的钟表,特别是手表,如腕表。
[0108]
有利地,选择部件的初始孔隙率以获得预定密度的部件。根据本发明的方法能够仅致密化表面层(即,上述表面区),从而能够获得具有改善的美学的较轻部件。此外,由于表面层的材料与多孔芯部的材料相同,因此不会发生传统涂层(如镀层)可能遇到的界面问题。
[0109]
下面通过三个实施例来说明本发明,这些实施例允许制造钟表部件。
[0110]
根据第一实施例,白金中部(75.2w%au、13.9w%pd、3w%ag和7.9w%cu)通过使用
上述slm方法进行制造。在任何处理之前,经slm处理的中部的表面具有由大于0.5μm的孔组成且吸收率为约20%的0.5~2%的孔隙率。然后,将中部在空气中于700℃下氧化15分钟,从而生成大约100nm的氧化层。该步骤对应于上述根据本发明的处理方法的制备步骤。接下来,具有光学元件和带有ilt喷嘴的3
×
3方形斑点的2kw ipg激光器以1500w(顶帽)的功率在中部的表面上以500mm/min的平均扫描速度并且在氩气流通下进行扫描。调节激光器与待处理的表面之间的距离以使表面处于焦平面水平。最后的步骤对应于根据本发明的通过在部件的表面区上进行表面重熔来改善部件的表面光洁度的步骤。获得了没有可察觉的表面孔和/或析出物的中部。致密层的厚度为200μm并且具有由大于0.5μm的孔组成的小于0.1%的孔隙率。
[0111]
图6通过比较中部的未处理区与处理区示出了该实施例。未处理区的放大图示出了缺陷20,其在根据本发明的实施方式的表面处理方法的实施之后已经消失。
[0112]
在第二实施例中,通过选择性激光熔化(slm)制造的316l型钢板根据本发明进行处理。在处理之前,316l型钢板的表面具有由大于0.5μm的孔组成的0.5~2%的孔隙率。具有光学元件和带有ilt喷嘴的3
×
3方形斑点的2kw ipg激光器以1500w(顶帽)的功率在平板表面上以1000mm/min的平均扫描速度并且在氮气流下进行扫描。调节激光器与待处理表面之间的距离,以使该表面位于焦平面上。获得了在表面上没有可察觉的孔和/或析出物的板。致密层的厚度为约200μm并且具有由大于0.5μm的孔组成的小于0.1%的孔隙率。此实施例由图7和图8示出。
[0113]
图7示出了316l型钢基板的表面。该表面包括具有若干可见缺陷20的未处理区。它包括通过根据本发明的表面处理方法进行处理的表面13,其不再包括这些缺陷20。图8示出了根据本发明的316l型钢基板的厚度的放大图。该部件包括致密且无缺陷的表面区12和较不致密的包含孔2的芯部15。
[0114]
在第三实施例中,通过选择性激光熔化(slm)制造的5级钛板根据本发明进行处理。在处理之前,5级钛板的表面具有由大于0.5μm的孔组成的0.2~1%的孔隙率。具有光学器件和带有ilt喷嘴的3
×
3方形斑点的2kw ipg激光器以1500w(顶帽)的功率在平板的表面上以1000mm/min的平均扫描速度并且在氩气通量下进行扫描。调节激光器与待处理的表面之间的距离,以使该表面处于焦平面水平。获得了在表面上没有可察觉的孔和/或析出物的板。致密层的厚度为300μm并且具有由大于0.5μm的孔组成的小于0.1%的孔隙率。此实施例由图9和图10示出。
[0115]
图9示出了例如5级钛基板的表面。该表面包括具有若干可见缺陷20的未处理区。它包括通过根据本发明的表面处理方法进行处理的表面13,其不再包括这些缺陷20。图10a和图10b分别示出了根据本发明的经处理的和未处理的5级钛基板的表面区的放大图。图10a中可见的根据本发明处理的表面区12在其厚度中及其表面13上都没有缺陷。相反,图10b中可见的未处理区含有缺陷,如表面缺陷3和表面条纹4。