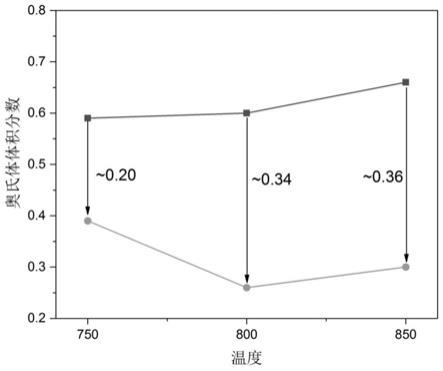
[0001]
本发明涉及汽车用钢领域,尤其涉及一种高强塑积中锰钢及其制备方法。
背景技术:[0002]
现如今发展以来,由于汽车用钢朝向轻量化和高安全性的标准发展,汽车所用的中锰钢板材已经革新到第三代先进汽车用钢,具有高强塑积(强塑积 30gpa
·
%)的第三代汽车用钢。
[0003]
从宏观力学性能方面,传统的第三代汽车先进用钢的强塑积在30gpa
·
%,如何获得更高的强塑积性能的中锰钢板材成为如今的研究趋势。同时从微观组织来说,由于中锰钢中冷轧过程中出现奥氏体由于形变产生马氏体组织,导致中锰钢的在冷轧过程中变形抗力较大,同时,由于单道次冷轧及逆相变退火工艺得到的中锰钢组织不均匀,进而导致中锰钢力学性能不好,强塑积较低。如何提高中锰钢的强塑积是目前亟待解决的技术难题。
[0004]
奥氏体逆相变工艺原理:将马氏体组织加热至奥氏体转变开始温度以上时间,组织将发生奥氏体组织转变,在进一步通过c、mn元素配分,稳定奥氏体相,使得室温下保留较高含量的奥氏体组织。亚稳奥氏体相在形变过程中能够发生trip效应,从而产生持续的加工硬化率,从而实现高强度与高塑性的良好组合。
技术实现要素:[0005]
本发明的目的在于提供一种高强塑积中锰钢及其制备方法,其通过循环温轧+临界退火工艺制备出具有粗晶奥氏体与细晶奥氏体组织的超细晶中锰钢组织,使得材料获得超高强塑积,有助于提高汽车用钢的强度和韧性。
[0006]
为了实现本发明的上述目的,特采用以下技术方案:
[0007]
一种高强塑积中锰钢的制备方法,所述中锰钢的化学成分按重量百分比计包括:c:0.1~0.3%、mn:4~12%、余量为fe;
[0008]
所述制备方法包括:
[0009]
按重量百分比,取所述中锰钢的化学成分冶炼钢水,浇铸成为铸锭,再将所述铸锭锻造成为板坯,空冷至室温,切割得到板材;
[0010]
对所述板材进行多道次温轧处理,温轧温度为300~400℃,温轧压下率为 50~60%,得到温轧板;其中相邻两个道次之间进行临界区退火处理,退火温度为780~810℃,退火时间为5~15min,之后空冷至300~400℃进行下一道次的温轧;
[0011]
再将所述温轧板在临界区780~810℃下退火保温20~40min,空冷至室温。
[0012]
进一步地,在本发明较佳的实施例中,所述中锰钢的化学成分还包括一种或多种下述按重量百分比计的元素:al:0~4%;si:0~2%;cr:0.2~3.0%; ni:0.1~3.0%;v:0~2.0%;mo:0~0.7%;nb:0~0.3%;cu:0.5~2.0%。
[0013]
进一步地,在本发明较佳的实施例中,对所述铸锭进行锻造的步骤包括将所述铸锭加热至1100~1300℃,保温1.5~2.5h。
[0014]
进一步地,在本发明较佳的实施例中,锻造后所述板材的厚度为2~4mm;所述温轧板的厚度为1~2mm。
[0015]
进一步地,在本发明较佳的实施例中,所述多道次温轧处理的温轧次数为 3次,临界区退火处理的次数为2次。
[0016]
进一步地,在本发明较佳的实施例中,所述中锰钢的化学成分按重量百分比计包括:c:0.26%,mn:10.02%,al:2.86%,si:1.86%,余量为fe。
[0017]
一种高强塑积中锰钢,所述中锰钢的化学成分按重量百分比计包括:c: 0.1~0.3%、mn:4~12%、余量为fe;其通过上述制备方法制得。
[0018]
进一步地,在本发明较佳的实施例中,所述中锰钢的化学成分按重量百分比计包括:c:0.26%,mn:10.02%,al:2.86%,si:1.86%,余量为fe。
[0019]
其通过如上所述的制备方法制得。
[0020]
本发明的效果如下:
[0021]
本发明制备方法的原理是:锻造后空冷处理,使中锰钢板材含有较高的奥氏体和铁素体双相组织,并释放残余应力,便于温轧处理。同时在300℃-400℃下温轧中锰钢板材,既能够保证中锰钢板材具有较低的轧制变形抗力,同时能够保证板材表面较好的平整度。在相邻的温轧工艺间进行临界区退火处理,使得温轧过程中形变产生的马氏体组织通过逆相变转化为细晶奥氏体组织,这与原锻后空冷保存下的粗晶奥氏体组织共存,使得中锰钢为粗晶奥氏体与细晶奥氏体与铁素体共存组织。通过临界区温度退火和保温时间的控制,使得中锰钢板材的粗晶奥氏体与细晶奥氏体组织保持适当的比例,以及奥氏体相与铁素体相保持合适的比例,使得中锰钢材料能够产生twip效应与trip效应共存机制,从而制备出超高强塑积的温轧中锰钢板材。
[0022]
与传统的冷轧工艺相比,本发明具有以下技术特点:
[0023]
1、此发明能够保证中锰钢的微观组织均匀分布,出现奥氏体相和铁素体双相组织,其中奥氏体出现较为粗大的奥氏体晶粒以及由于临界退火处理产生细小的奥氏体晶粒,铁素体相与奥氏体相均匀分布,这保证了在变形过程中,首先发生较为粗大的奥氏体发生马氏体相变产生增塑行为(即为trip效应),随着变形量的增大,细小的奥氏体开始发生相变,由此中锰钢的增塑行为表现为持续且稳定的trip效应与twip效应,进而提高中锰钢的强塑积。
[0024]
2、温轧是在回复温度以上,在结晶温度以下的温度范围内进行的轧制过程。温扎工艺能够减小钢材轧制过程中的变形抗力,保证钢材表面质量,变形阻力小,表面光滑,生产效率高,节能,同时具有塑型高,热变形时允许变形量大的特点。不存在热轧后出现的较厚的氧化皮与麻点凹坑等现象。同时温轧能够保证细化晶粒尺寸。
[0025]
3、本发明采用的温轧+临界区退火工艺方法,既能够保证轧制过程中中锰钢变形抗力的减少,同时保证临界退火后形变马氏体逆相变产生细晶奥氏体组织,保证中锰钢板材出现粗晶奥氏体与细晶奥氏体共存组织,从而制备超高强塑积中锰钢板材。
[0026]
4、本发明采用的退火温度是根据thermo-calc热力学计算软件模拟得出,通过计算得出铁素体全部转变为奥氏体的温度(ac3)约为800℃,由此温度设置温轧循环工艺中间退火温度为780~810℃,从而保证在变形过程中产生的马氏体能够充分的转变为奥氏体组织。
[0027]
5、本发明提供的中锰钢采用特殊比例的元素成分,有助于提高中锰钢的强塑积。其中,碳元素能够提高中锰钢中奥氏体的稳定性,通常,碳的质量分数增加1%,马氏体的转变温度ms降低423℃。但是碳含量过高,中锰钢的焊接性能变差,鉴于此本发明中c含量为0.1~0.3%。mn元素能够拓宽奥氏体相区,强化基体,提高奥氏体的稳定性,但是mn含量过高会产生偏析,使得扩散退火难以组织成分的均匀化,因此中锰钢的mn含量在4%~12%。si元素能够促进奥氏体的形成,增加室温下残余奥氏体的含量。al元素同si元素的作用类似,同时al元素能够显著的减轻中锰钢的密度,使得汽车用钢的质量减轻,奥氏体的形成主要依赖于层错能,al元素能够增加奥氏体的层错能,但是al元素含量过多会导致连铸过程中水口堵塞,影响生产,因此al含量不超过3%,si含量不超过2%。
[0028]
6、本发明的超高强塑积温轧中锰钢性能优越,耐磨性能好,变形承受能力强,材料密度低,适用范围广,满足汽车不同零部件性能指标和满足汽车轻量化和高安全性的要求。
附图说明
[0029]
图1为本发明微拉伸试样图纸尺寸;
[0030]
图2是本发明实施例1中的750℃~850℃不同退火温度工艺曲线;
[0031]
图3是本发明实施例2中于750℃不同退火时间工艺曲线;
[0032]
图4是本发明实施例1中温轧退火后中锰钢奥氏体ebsd分析;
[0033]
图5是本发明实施例1中温轧退火后中锰钢奥氏体的晶粒尺寸分析;
[0034]
图6是本发明实施例1中温轧退火后试样拉伸前后奥氏体体积份数的变化;
[0035]
图7是本发明实施例1中不同退火温度下工程应力-应变曲线;
[0036]
图8是本发明实施例2中750℃不同时间长度下工程应力-应变曲线;
[0037]
图9是本发明thermo-calc热力学计算软件模拟相图;
[0038]
图10是本发明实施例1中不同退火温度(750℃、800℃、850℃)的(sem) 微观组织图;
[0039]
图11为本发明对比例1中单道次温轧中锰钢800℃-30min工程应力-应变曲线。
具体实施方式
[0040]
下面将结合实施例对本发明的实施方案进行详细描述,但是本领域技术人员将会理解,下列实施例仅用于说明本发明,而不应视为限制本发明的范围。实施例中未注明具体条件者,按照常规条件或制造商建议的条件进行。所用试剂或仪器未注明生产厂商者,均为可以通过市售购买获得的常规产品。
[0041]
本发明实施例中进行室温拉伸实验的设备是来自燕山大学锻压实验室的 instron 8801液压伺服疲劳试验机上面进行的。
[0042]
本发明实施例中微观表征技术的设备为zeiss sigma500扫描电子显微镜,装备电子背散射衍射分析系统(ebsd)。
[0043]
本发明实施例中残余奥氏体体积分数的测定设备为d/max-2500/pcx射线衍射仪。
[0044]
本发明实施例中采用热处理炉是高温炉。
[0045]
本发明实施例中,将温轧超高强塑积中锰钢加工成为尺寸如图1所示的拉伸试样,采用1000粒度的砂纸进行打磨光亮,随后进行拉伸实验,变形速率为3mm/min直至拉断。
[0046]
本发明实施例中,将实验热镶嵌为30mm直径的圆饼,用砂纸磨光,在机械抛光。随后采用氯化铜腐蚀液进行腐蚀,腐蚀时间1min,腐蚀完成后用酒精清洗,完成后作为xrd、om、sem观测。
[0047]
实施例1
[0048]
本实施例提供一种高强塑积中锰钢,其制备方法包括:
[0049]
1.按照设定的成分冶炼钢水,然后浇铸成为20kg铸锭;钢水的质量百分比为:c:0.26%,mn:10.02%,al:2.86%,si:1.86%,余量为fe及不可避免的杂质。
[0050]
2.将铸锭加热至1200℃,保温2小时锻造成为板坯,空冷至室温;采用线切割技术对板坯进行线切割处理,切取板材厚度为3mm钢板。
[0051]
3.将钢板加热到400℃进行保温1h,然后进行三道次温轧,从3mm轧制1.5mm,温轧压下率为50%,制作成温轧板空冷至室温;其中相邻两个道次的温轧工艺之间进行中间退火,退火温度为800℃,时间为10min,随后冷却至 400℃再次进行下道次温轧工艺。
[0052]
4.随后将相同的温轧板分别在750℃、800℃和850℃保温30min,热处理工艺如图2所示,然后空冷至室温下,制作成为三组温轧中锰钢板材。
[0053]
对所制得的三组中锰钢板材进行性能测试,结果如表1所示:
[0054]
表1.中锰钢板材的性能测试结果
[0055]
板材的保温温度抗拉强度断后伸长率强塑积屈服强度750℃1012.24mpa68.31%69.15gpa
·
%735.98mpa800℃1105.62mpa76.87%84.99gpa
·
%570.32mpa850℃1154.77mpa37.76%43.60gpa
·
%484.13mpa
[0056]
由表1可知,在进行多道次温扎+退火工艺后,将所得的温轧板在800℃保温30min,所得的中锰钢板材的断后伸长率和强塑积有了较为显著的增长,同时,又能保持较好的抗拉强度和屈服强度。
[0057]
ebsd观测结果如图4所示,晶粒尺寸分析如图5所示,微观组织分析显示,温轧中锰钢板材经过800℃退火30min的工艺后,红色铁素体组织均匀分布在蓝色奥氏体组织上,奥氏体晶粒存在细晶奥氏体在5um以下,同时存在粗晶奥氏体组织在10um以上。由此说明,温轧中锰钢板材良好的力学性能来自于粗晶奥氏体与细晶奥氏体的混晶组织,由于奥氏体的晶粒尺寸不同,根据公式ms=545-432c-30.4mn-60.5v
γ-1/3
,c、mn代表实验钢中的元素的体积的分数,v
γ
代表实验钢中的奥氏体晶粒尺寸,由公式可知,奥氏体的尺寸越小,ms (马氏体转变的开始温度)越低,奥氏体稳定性越高,由于混晶组织中奥氏体中含有粗晶奥氏体和细晶奥氏体组织,由此粗晶奥氏体的稳定性较差,首先发生马氏体相变,而细晶奥氏体稳定性较高,随着变形的增加再发生马氏体相变,进而产生持续的加工硬化行为,从而保证实验钢具有良好的力学性能。
[0058]
拉伸前后奥氏体体积分数变化曲线如图6所示,经过800℃保温处理所得板材,拉伸前奥氏体体积分数在60%,拉伸后奥氏体体积分数为26%,温轧中锰钢板微拉伸试样在拉伸变形过程中奥氏体的转变量为34%;而在750℃下保温处理所得板材的在拉伸变形过程中奥氏体的转变量为20%;在850℃下保温处理所得板材的在拉伸变形过程中奥氏体的转变量为36%。由此说明,实验钢中发生了明显的trip效应,存在大量的奥氏体转变为马氏体组织,在750℃下,奥氏体的转变量较少,进而导致试验钢工程应力-应变曲线,如图7上没
有产生明显的“拐点”,由此导致延伸率较低。而850℃下奥氏体转变量足够多,但试验钢工程应力-应变曲线,如图7所示,曲线上升太过明显,说明在 850℃奥氏体稳定性太低,在变形过程中发生trip效应过快,不能产生连续的加工硬化效果。而在800℃下,可以看到奥氏体转变量为34%,与850℃下奥氏体转变量36%相差不多,但是从试验钢工程应力-应变曲线,如图7所示可以看到力学性能优异,这与奥氏体稳定性适中,保证在变形过程中产生持续的trip效应有关。
[0059]
应力应变曲线如图7所示,图7为温轧中锰钢不同退火温度下工程应力
-ꢀ
应变曲线,实验钢在750℃下退火,屈服强度为735.98mpa,抗拉强度为 1012.24mpa,延伸率为68.31%,强塑积为69.15gpa
·
%。800℃下退火,屈服强度为570.32mpa,抗拉强度为1105.62mpa,延伸率为76.87%,强塑积为 84.99gpa
·
%。850℃下退火,屈服强度为484.13mpa,抗拉强度为1154.77mpa,延伸率为37.76%,强塑积为43.60gpa
·
%。由此可见,实验钢在800℃下退火力学性能最优,强塑积可达84.99gpa
·
%。
[0060]
图9为用thermo-calc热力学计算软件模拟相图,由相图可以知,实验钢的ac3(铁素体全部转变为奥氏体温度)约为800℃,说明在800℃以上,铁素体将全部转变为奥氏体组织,即在800℃下,铁素体组织能够发生充分的相变反应,产生奥氏体组织。
[0061]
不同退火温度的微观组织图如图10所示,不同退火温度的金相组织图片显示,在750℃下,退火温度较低,铁素体转变细小的奥氏体组织。在800℃下,由于退火温度升高,奥氏体的转变量增加,同时奥氏体组织的尺寸开始增大。在850℃下,由于退火温度过高,导致奥氏体组织的尺寸过大,进而奥氏体稳定性下降。
[0062]
实施例2
[0063]
本实施例提供一种高强塑积中锰钢,其制备方法与实施例1基本一致,不同之处在于:
[0064]
将经过步骤3的三道次温扎+退火工艺后得到的温轧板分别在800℃保温, 15min、30min、60min,热处理工艺如图3所示,然后空冷至室温,制成三组高强塑积的中锰钢板材。
[0065]
对所制得的三组中锰钢板材进行性能测试,结果如表2所示:
[0066]
表2.中锰钢板材的性能测试结果
[0067]
板材的保温时间抗拉强度断后伸长率强塑积屈服强度15min1112.12mpa76.75%85.36gpa
·
%625.19mpa30min1105.62mpa76.87%84.99gpa
·
%570.32mpa60min1103.10mpa75.63%83.43gpa
·
%556.53mpa
[0068]
由表2可知,在进行多道次温扎+退火工艺后,将所得的温轧板在800℃保温15min、30min、60min,所得的中锰钢板材的力学性能都很优异,说明温轧中锰钢板材在800℃下退火,保温时间对其影响较小,同时表明在较短的时间内(例如15min),实验钢就能保证较为优异的力学性能,相比较传统的退火工艺,此材料能够更为快捷高效的完成退火过程,节省成本。
[0069]
工程应力应变曲线如图8所示,随着退火时间的延长,实验钢的屈服强度略有下降,从625.19mpa下降至556.53mpa。抗拉强度与延伸率变化并不明显,表明实验钢在15min~60min之间退火均能保持良好的力学性能。
[0070]
对比例
[0071]
本对比例提供一种中锰钢,其制备方法包括:
[0072]
1.按照设定的成分冶炼钢水,然后浇铸成为20kg铸锭;钢水的质量百分比为:c:0.26%,mn:10.02%,al:2.86%,si:1.86%,余量为fe及不可避免的杂质。
[0073]
2.将铸锭加热至1200℃,保温2小时锻造成为板坯,空冷至室温;采用线切割技术对板坯进行线切割处理,切去板材厚度为3mm钢板。
[0074]
3.将钢板加热到400℃保温1h,然后进行单道次温轧,温轧中间不采用800℃中间临界区退火工艺,温轧变形量为50%,空冷至室温。
[0075]
4.随后将所得温轧板在800℃保温30min,然后空冷至室温下,制作成组轧中锰钢板材。
[0076]
切取所得中锰钢板材的微拉伸试件,材料的工程应力-应变曲线如图11所示,抗拉强度为1177.17mpa,断后延伸率为54.38%,强塑积为64.01gpa%。
[0077]
以上所述的实施例仅是对本发明的优选实施方式进行描述,并非对本发明的范围进行限定,在不脱离本发明设计精神的前提下,本领域普通技术人员对本发明的技术方案做出的各种变形和改进,均应落入本发明权利要求书确定的保护范围内。