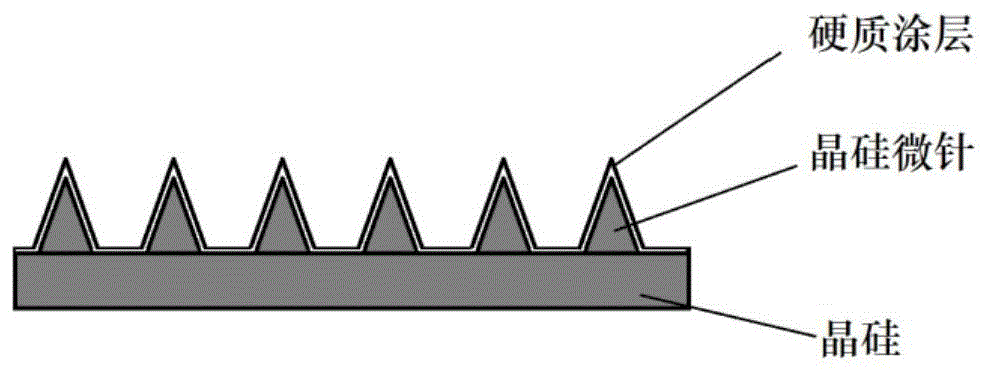
本发明涉及医学装置领域,尤其涉及一种具有硬质涂层保护的晶硅微针及其制备方法。
背景技术:
:纳米微针晶片正广泛应用于生活美容和医学美容等透皮器械
技术领域:
。纳米微针的制作是基于半导体工艺技术,即在单晶硅衬底上通过光刻和湿法腐蚀技术加工微米结构的金字塔结构而形成,高度根据光刻的尺度而定,从50um到500um不等。现有技术的微针制作方法如下:单晶硅片经过热氧化后获得覆盖有0.8-1.5微米厚度的氧化硅的硅晶圆,并在光刻区进行正性或负性光刻胶涂布,光刻胶厚度1.0微米。在掩膜版的辅助下,对涂有光刻胶晶硅片进行紫外曝光。曝光过后,将晶硅片转移到显影液中对光刻胶进行充分显影,在晶硅表面露出所需的光刻胶图案。然后将带有光刻胶图案的晶片在氢氟酸中腐蚀,将光刻胶图案转移到氧化硅表面上。将带有氧化硅图案的晶硅片投入到60-90度的温度和10-70%浓度的氢氧化钾碱液中腐蚀,腐蚀完毕后,对晶硅进行清洗,所需的晶硅微针也就定制完成。由于人体的角质层厚度在80um左右,所以在生活美容领域,高度在100um左右的微针已经足够,这类微针不容易断针,还保有一定的强度。而在医学美容行业,微针的高度往往超过了300um,由于微针的高宽比非常大,微针的结构强度也大为减弱,微针容易受到剪切外力而出现断针行为,断针留在皮肤里会引起人体的不适感。通常的办法是通过改变湿法腐蚀工艺改变微针的结构形态以提高微针的强度,然而改变的空间有限。技术实现要素:为解决上述技术问题,本发明的目的是提供一种具有硬质涂层保护的晶硅微针,通过在微针表面涂覆。本发明的第一个目的是提供了一种具有硬质涂层保护的晶硅微针,所述的晶硅微针包括微针本体和设置在微针本体表面的硬质涂层。进一步地,所述的硬质涂层为金刚石薄膜、类金刚石碳膜、氮化钛薄膜、碳化铬薄膜或氧化钛薄膜。本发明的第二个目的是提供所述的具有硬质涂层保护的晶硅微针得制备方法,包括如下步骤:s1、将微针本体置于超声溶液中进行超声处理;s2、将超声处理后的微针本体采用热丝化学气相沉积方法、化学气相沉积方法、磁控溅射法或电弧蒸发法进行硬质涂层制备。进一步地,所述的热丝化学气相沉积方法制备金刚石薄膜,包括如下步骤:在超声处理过程中,在溶液中添加纳米级金刚石粉;超声处理后的微针本体置于化学气相沉积装置中,金刚石薄膜的生长气体为甲烷和氢气,气压控制在100pa~5000pa之间,热丝的温度超过2700℃,微针衬底的温度控制在650℃~900℃的之间。进一步地,所述的甲烷的流量占比为1%~10%。进一步地,化学气相沉积装置真空度小于1*10-3pa。进一步地,所述的化学气相沉积方法制备氮化钛薄膜,包括如下步骤:将超声处理后的微针本体置于化学气相沉积装置中,氮化钛薄膜的生长气体为氨气和四氯化钛前驱体,气压控制在100pa~5000pa之间,加热温度在500~900℃之间。进一步地,所述的氨气的流量占比为50%~80%,四氯化钛的流量占比为20%~50%。进一步地,化学气相沉积装置真空度小于1*10-3pa。进一步地,所述的磁控溅射法制备类金刚石碳膜,包括如下步骤:将超声处理后的微针本体置于磁控溅射的真空腔室内,通入氩气使得腔室内的气体压强在2.0pa-10.0pa之间,靶材为高纯石墨靶材,采用等离子体放电在石墨靶材表面鞘层产生200-1000v的负高压,靶材原子溅射沉积到微针本体表面,生长成类金刚石碳膜。进一步地,所述的电弧蒸发法制备氮化钛薄膜,包括如下步骤:将超声处理后的微针本体置于真空腔室内,电弧用的靶材为钛靶,放电气体为氩气和氮气,气体压强在1.0pa~10.0pa之间。进一步地,氮化钛薄膜与微针本体之间还包括10-50nm的钛薄膜。借由上述方案,本发明至少具有以下优点:本发明的加固晶硅微针的加工方法简单高效,不仅可以强化微针的强度防止微针的断裂,同时涂覆有硬质涂层的微针可以很轻松的实现皮肤的穿刺,促进药物的吸收。上述说明仅是本发明技术方案的概述,为了能够更清楚了解本发明的技术手段,并可依照说明书的内容予以实施,以下以本发明的较佳实施例并配合详细附图说明如后。附图说明图1为表面涂覆有硬质涂层的晶硅微针示意图。具体实施方式下面结合实施例,对本发明的具体实施方式作进一步详细描述。以下实施例用于说明本发明,但不用来限制本发明的范围。实施例1:热丝化学气相沉积法在硅基微针表面涂覆金刚石薄膜1、将定制好的微针放入超声溶液中进行超声处理,溶液中含有粒径为纳米级的金刚石粉,经过金刚石粉的超声处理后,微针的表面拥有了金刚石微颗粒籽晶,为接下来的金刚石薄膜的表面生长提供了合适的生长籽晶。2、将处理后的微针放入化学气相沉积装置中,生长金刚石方法为热丝化学气相沉积法,沉积装置是一个真空系统,真空获得由机械泵和分子泵联合组成,装置的本底真空小于1*10-3pa。金刚石薄膜的生长气体为甲烷和氢气,甲烷气体的流量占比1%-10%,其余为氢气,气压控制在100pa-5000pa之间,热丝的加热温度超过2700℃,微针衬底的温度控制在650℃-900℃的之间,在热丝温度的作用下,甲烷通常会被分解成能够促进金刚石相生长的生长因子·ch3,该生长因子密度越高,生成的金刚石相成分越纯;另外,氢气在热解作用下也会分解成原子h,其主要作用是将沉积在表面的碳膜中多余的h给刻蚀掉,从而促进碳原子沿着金刚石籽晶生长方向进行金刚石生长。生长厚度超过2微米的厚度。涂覆有金刚石相的微针通常的硬度和强度都有显著提高,但生长的金刚石速度很慢,且生产成本较高,不利于产品的推广和应用。实施例2:采用化学气相沉积方法生长硬质氮化钛薄膜1、将定制好的微针放入超声溶液中进行超声处理,实现去油去污的目的。2、将处理好的微针放入化学气相沉积装置中,沉积装置是一个真空系统,真空获得由机械泵和分子泵联合组成,装置的本底真空小于1*10-3pa。硬质氮化钛薄膜的生长气体为氨气和四氯化钛前驱体,氨气气体的流量占比50%-80%,四氯化钛是挥发性的,其流量占比在20%-50%,两种气体可以直接通过质量流量计通入真空加热系统中,气压控制在100pa-1000pa之间,炉内的加热温度在500-900℃。两种气体在高温下实现化合,并在微针表面形成致密的氮化钛薄膜。为解决硅片表面氮化钛薄膜的附着力,可以在涂覆氮化钛薄膜之前,先涂覆一层钛层作为缓冲层,前驱气体直接将氨气换成一定流量的氢气即可。缓冲钛层的厚度约在10-30nm之间为宜。实施例3:采用磁控溅射在晶硅微针表面涂覆类金刚石碳膜1、将定制好的微针放入超声溶液中进行超声清洗处理,实现去油去污的目的。2、将处理后的微针硅片转移到磁控溅射的真空腔室内,磁控靶材使用石墨靶材。机械泵和分子泵的组合,使得腔室的真空度小于1*10-3pa的本底真空口后,通过质量流量计通入氩气使得放电室的气体压强在2.0pa-10.0pa之间,磁控溅射的电源可以采用射频放电或直流放电模式,靶材采用高纯石墨靶。利用等离子体放电在石墨靶材表面鞘层产生200-1000v的负高压,等离子体中的离子成分尤其氩离子成分在负偏压的作用下加速轰击靶材,使得靶材原子能够从表面溅射出来,然后沉积到晶硅微针的表面,实现类金刚石碳膜的生长。实施例4:采用电弧蒸发法生长硬质氮化钛薄膜1、将定制好的微针放入超声溶液中进行超声清洗处理,实现去油去污的目的。2、将处理后的微针硅片转移到真空腔室内,电弧用的靶材可以是高纯钛靶。通过机械泵和分子泵的组合,使得腔室的真空度小于1*10-3pa的本底真空口后,通过质量流量计将氩气和氮气按一定的比例通入放电室,放电的气体压强在1.0pa-10.0pa之间。启动电弧蒸发电源按钮,调节一定的弧电流,安置在高纯靶材后面的磁铁产生的磁场使得电弧被局域在靶材表面,并不断做旋转运动。电弧产生的高温等离子体不仅可以将靶材表面的原子蒸发出来,同时高温等离子体也将背景气体电离,当蒸发出来的钛粒子在衬底表面上与氮离子发生碰撞时就可以在晶硅微针表面形成硬质氮化钛薄膜。一般而言,由于硬质氮化钛薄膜与晶硅的热胀系数的差异,一般要在涂覆氮化钛薄膜之前需要在晶硅表面预涂覆10-50纳米的钛薄膜。为比较直观的了解具有涂层保护的晶硅微针的物理特性,我们采用了市面上购买到的猪肉皮作为一个测试对象。具体实验方案如下:将5mm*5mm的微针(该面积范围内具有36根微针,针高390微米,微针底宽约280微米)粘贴在导入仪末端,按下电源开关,旋转的直流电机驱动偏心轮机械结构,促使导入仪末端带着微针做上下震动运动,频率控制在50hz-150hz之间,将震动的微针自然垂放在猪皮表面,由于微针上下震动的缘故,微针将不断刺穿表皮。为避免在同一个地方做刺穿运动,每隔5秒平移到另一快猪皮表面,如此,连续针刺时间为1,3,5,10分钟。每个类型的微针针刺实验进行了5组。待针刺过程完成后,取下晶硅微针,并在显微镜下观察断针的个数,记录未断的针数。由于晶硅微针在运动过程中存在着横向移动和纵向运动,基本上可以确定晶硅微针在不同硬质涂层保护下的强度与穿刺能力。不同实验参数下的统计平均测试结果如下表所示:表11分钟3分钟5分钟10分钟未涂覆的晶硅微针30.625.422.816.6实施例133.831.628.422.4实施例232.232.828.825.6实施例330.826.823.417.4实施例431.230.425.624.6以上仅是本发明的优选实施方式,并不用于限制本发明,应当指出,对于本
技术领域:
的普通技术人员来说,在不脱离本发明技术原理的前提下,还可以做出若干改进和变型,这些改进和变型也应视为本发明的保护范围。当前第1页12