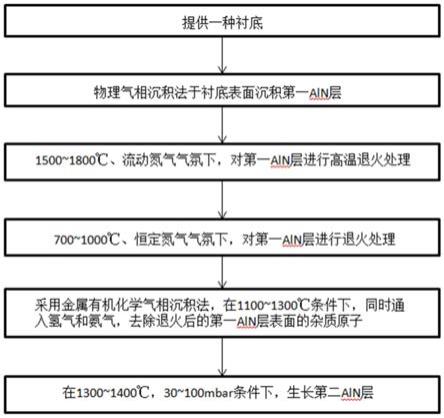
一种aln薄膜的制备方法
技术领域
1.本发明涉及半导体技术领域,具体涉及一种低位错密度、原子级别平整表面特点的aln薄膜制备方法。
背景技术:2.深紫外led作为典型的第三代宽禁带半导体产物,其具有体积小、寿命长、无毒等优点,能够非常有效地杀灭细菌,对炭疽孢子,大肠杆菌,流感,疟疾等病毒具有高速高效灭杀的功能,被广泛用于表面、空气、水杀菌等。而algan作为深紫外led的典型材料,其禁带宽度随着al组分由0到1变化在3.4ev到6.2ev之间连续可调,相应波段覆盖了200
‑‑
365nm,涵盖了大部分紫外波段,是制备紫外发光与探测器件的理想材料。
3.从生长应变和光透过率的角度考虑,要想制备高质量的algan材料及相关器件,采用aln同质衬底和aln/蓝宝石模版衬底是较为理想的选择。由于传统技术缺少低成本、高质量、大尺寸的aln单晶衬底,相比于aln同质衬底来说,在廉价且工艺较成熟的蓝宝石衬底上生长aln薄膜将是该领域的主流技术发展路线。
4.因此,为了保证algan基高性能深紫外光器件的独特优势,关键基础之一是制备出高质量的aln外延薄膜。但由于aln外延层与异质衬底之间较大的晶格失配和热失配,导致这种aln薄膜中不但应力严重,而且有很高的贯穿位错密度,特别是这些贯穿位错一般会延伸到器件有源区内。这些缺陷可作为非辐射复合点或泄漏电流通路,对器件的性能(如效率、可靠性和寿命)造成不利影响。因而如何在衬底上制备相对较低位错密度的aln薄膜对于保证algan基高性能深紫外光器件的独特优势具有极为重要的意义。
5.为改善aln薄膜的质量,研究者们提出了多种生长方式,包括利用缓冲层、插入层法、超晶格法、外延侧向过生长法等等。这些方法虽然在一定程度上提升了aln薄膜的晶体质量,但离期待水平依然存在差距。
技术实现要素:6.本发明采用多次退火技术,同时配合后续外延生长aln薄膜的制备方法,能够提高异质衬底上aln外延层结晶质量,获得无裂纹、原子级平整且位错密度低的aln薄膜,为后续algan外延生长提供高质量的aln模板。
7.本发明的技术方案具体如下:
8.一种aln薄膜的制备方法,包括如下步骤:
9.(1).采用物理气相沉积法于衬底表面沉积第一aln层;
10.优选的,所述第一aln层的厚度为10~500nm;此处厚度过厚会导致后续的高温退火非常难融合成质量很高的aln单晶层,而厚度过薄,高温退火过程会损耗aln层,不会形成连续的膜;
11.优选的,所述衬底为蓝宝石、碳化硅或图形化衬底中的一种;
12.优选的,所述物理气相沉积方法为磁控溅射、射频溅射或电子束蒸发中的一种;
13.(2).在1500~1800℃、流动氮气气氛下,对第一aln层进行高温退火处理;因为al的迁移率非常低,步骤(1)中生长的第一aln层质量会较差,甚至有可能是多晶状态,此温度下退火处理能够使多晶状态下的aln薄膜变成高质量的单晶aln薄膜;
14.所述流动氮气流量为20~1000sccm;
15.所述高温退火时间为60~200min;
16.优选的,退火温度为1650~1800℃;
17.优选的,退火时间为120~180min;
18.该步骤中上述参数的范围选择,既能保证aln单晶的形成,也使aln不会损耗,最终aln晶体质量较好,时间太长或者温度过高,会导致aln损耗较多;
19.(3).在700~1000℃、恒定氮气气氛下,对(2)中的第一aln层进行退火处理;700~1000℃温度下退火对应力的消除较好,同时对aln晶体也没有任何影响;
20.优选的,退火时间为20~120min;
21.优选的,退火温度为750~950℃;
22.优选的,退火时间为30~90min;
23.该步骤中上述参数的范围选择,得到的aln应力消除较好,且同时可以缩短时间,提高产能;此外,高温下退火时aln小晶粒融合长大,会产生较多的应力,使用中高温退火,能够消除这些应力,避免后续生长过程中开裂;
24.(4).将退火后的第一aln层移至金属有机物化学气相沉积设备中,在1100~1300℃条件下,同时通入氢气和氨气,去除退火后的第一aln层表面的杂质原子;此温度下,配合氢气和氨气的通入,可以有效去除杂质原子;
25.所述氢气和氨气流量比为5~50;
26.所述同时通入氢气和氨气的时间为1~10min;
27.优选的,所述同时通入氢气和氨气的时间为3~5min;
28.因为氢气和氨气具有腐蚀性,该步骤中上述参数的范围选择,使aln损耗极少,否则,可能会使aln损耗较多;
29.(5).在1300~1400℃,30~100mbar条件下,生长第二aln层;因为al原子的迁移率较低,使用高温能够增大al原子的迁移率,有利于aln单晶的形成;在较低的压力下,能够减少三甲基铝和氨气的预反应,避免原料消耗较多,同时减少杂质碳颗粒对aln的污染;
30.所述第二aln层生长厚度为1000~5000nm;随着aln厚度的增加,aln外延层中的应力会逐渐增大,会导致裂纹的产生,上述厚度范围,既可以保证aln晶体质量比较高,又不容易产生裂纹;
31.优选的,所述利用金属有机化合物气相沉积方法外延生长第二aln层时,所用的金属有机源为三甲基铝或三乙基铝,所用载气为氮气、氢气或者二者的混合气体,所使用氮源为氨气;
32.如上所述,本发明的一种高质量aln薄膜的制备方法,具有以下有益效果:
33.本发明包括在衬底上利用物理气相沉积法生长氮化铝薄膜,利用不同气体状态下的高温、低温退火结合的方式,第一aln层通过物理溅射形成,可能会有一些杂质,在高温下,aln晶体在融合时上述杂质可以释放出来,通过流动氮气能够带走这些杂质,同时,恒定氮气能够在应力消除退火中起保护作用,在使用中高温退火时,aln晶体不像高温退火时一
样会多个小晶粒融合成大晶粒释放杂质;并且在金属有机物化学气相沉积设备中对退火后的第一aln层进行去除杂质原子的处理,然后生长第二aln层。所述生长的aln薄膜成本低,无污染,稳定。
34.此外,物理溅射得到的第一aln可能是非晶,也可能是多晶,高温退火能够使溅射的aln重新结晶形成单晶;而低温退火能够消除高温退火aln晶粒融合形成的应力,二者作用不同,配合使用,经过高温和低温的退火处理,有效的降低了由于异质结衬底与外延层因晶格失配产生的位错,同时改善了aln薄膜的应力状态,解决了aln薄膜外延过程中的开裂行为。在金属有机物化学气相沉积设备中通过同时通入氢气和氨气并控制流量比,对退火后的aln进行清洁处理,可以有效的去除表面氧、碳以及含铝的氧化物,改善aln薄膜的晶体质量,并提高了aln表面的平整度,为后续生长第二aln层并获得原子级表面平整的高质量aln外延薄膜做出了较大的作用,其中,某一种气体量如果过多,在去除杂质的时候对aln损耗较多,而较少的话效果又不理想,需要控制合适的流量比。该方法具有操作流程简单,工艺效果容易实现、aln晶体质量提高显著等优点,具有广阔的应用前景,对宽禁带三族氮化物半导体器件的制备与大规模应用有重要意义。
附图说明
35.图1为本发明所述aln薄膜的制备方法的流程图。
具体实施方式
36.为使本发明实施例的目的、技术方案和优点更加清楚,下面将结合附图对本发明的各实施方式进行详细的阐述。然而,本领域的普通技术人员可以理解,在本发明各实施方式中,为了使读者更好地理解本申请而提出了许多技术细节。但是,即使没有这些技术细节和基于以下各实施方式的种种变化和修改,也可以实现本申请所要求保护的技术方案。以下各个实施例的划分是为了描述方便,不应对本发明的具体实现方式构成任何限定,各个实施例在不矛盾的前提下可以相互结合相互引用。
37.本发明通过在氮气氛围下,利用高温、低温热处理方法,使在异质衬底上外延的aln材料发生重结晶过程,使晶粒重新排列。在此过程中会使aln晶粒排列均一性更高,因此使由于晶粒倾斜(tilt)产生的螺位错以及由于晶粒相互扭转(twist)产生的刃位错密度大大降低,从而可以提升材料的结晶质量。其中,高温热处理使溅射后的多晶甚至是非晶的aln重新结晶形成小晶粒,而小晶粒又可以在高温下重新融合生长成大晶粒,从而降低位错密度,并有序排列形成单晶,同时在晶粒融合的过程中,会产生应力,降低温度退火能够消除这些应力。同时,在热处理的过程中,改善了aln薄膜的应力状态,使其从张应力状态转变为压应力状态,解决了aln薄膜外延过程中的开裂行为。在金属有机物化学气相沉积设备中通过同时通入氢气和氨气并控制流量比,对退火后的aln进行清洁处理,可以有效的去除表面氧、碳以及含铝的氧化物,改善aln薄膜的晶体质量,并提高了aln表面的平整度。
38.下面结合附图和特定的具体实例对本发明做以详细说明。
39.需要说明的是,本实施例中所采用的衬底为蓝宝石,金属有机源为三甲基铝,所使用氮源为氮气、氨气其中一种或多种。
40.实施例1
41.1.采用物理气相沉积设备,在蓝宝石衬底上生长第一aln层,其中,靶材为单质铝,沉积环境为氩气和氮气的混合气体,控制温度为600℃,沉积厚度为200nm;此处温度适合第一aln层的形成,温度太低或者太高,aln薄膜形成的可能不够致密或者存在缺陷。
42.2.将沉积第一aln层的衬底,转移到高温退火炉,在纯氮气气氛下,通入50sccm的流动氮气,在1750℃条件下退火150min;50sccm的流动氮气,既不会带走过多热量使温度降低从而使退火效果不好,又可以带走某些杂质。温度和时间的设置要和aln的厚度联系起来考虑,温度和时间合适,既能得到较好的单晶,又能使aln不受损耗。
43.3.将退火炉温度降低至800℃,关闭流动氮气,退火90min,然后随炉冷却;其中,关闭流动氮气是为第二次消除应力退火做准备,使退火炉中保持恒定氮气。
44.4.将退火后的第一aln层移至金属有机物化学气相沉积设备中,升温至1250℃,同时通入流量比为20:1的氢气和氨气,烘烤4min,去除第一aln层表面的杂质。
45.5.控制设备压力为50mbar,升温至1350℃,通入三甲基铝和氨气,生长3000nm第二aln层。
46.上述获得的aln薄膜光学显微镜检测下无裂纹;原子力显微镜检测下具有原子级平整表面;xrd测得(002)方向的半宽为130arcsec,(102)方向的半宽为300arcsec。其中,(002)和(102)表示晶体的两个不同晶面方向;两个半宽数值与位错密度相关,数值越大,代表位错越多,晶体质量越差,通常(002)半宽数值代表螺位错,而(102)半宽数值代表刃位错。
47.实施例2
48.1.采用物理气相沉积设备,在蓝宝石衬底上生长第一aln层,其中,靶材为单质铝,沉积环境为氩气和氮气的混合气体,控制温度为600℃,沉积厚度为300nm。
49.2.将沉积第一aln层的衬底,转移到高温退火炉,在纯氮气气氛下,通入50sccm的流动氮气,在1750℃条件下退火180min。
50.3.将退火炉温度降低至800℃,关闭流动氮气,退火90min,然后随炉冷却。
51.4.将退火后的第一aln层移至金属有机物化学气相沉积设备中,升温至1250℃,同时通入流量比为20:1的氢气和氨气,烘烤4min,去除第一aln层表面的杂质。
52.5.控制设备压力为50mbar,升温至1350℃,通入三甲基铝和氨气,生长3000nm第二aln层。
53.上述获得的aln薄膜光学显微镜检测下无裂纹;原子力显微镜检测下具有原子级平整表面;xrd测得(002)方向的半宽为110arcsec,(102)方向的半宽为270arcsec。
54.实施例3
55.1.采用物理气相沉积设备,在蓝宝石衬底上生长第一aln层,其中,靶材为单质铝,沉积环境为氩气和氮气的混合气体,控制温度为600℃,沉积厚度为400nm。
56.2.将沉积第一aln层的衬底,转移到高温退火炉,在纯氮气气氛下,通入50sccm的流动氮气,在1750℃条件下退火180min。
57.3.将退火炉温度降低至800℃,关闭流动氮气,退火90min,然后随炉冷却。
58.4.将退火后的第一aln层移至金属有机物化学气相沉积设备中,升温至1250℃,同时通入流量比为20:1的氢气和氨气,烘烤4min,去除第一aln层表面的杂质。
59.5.控制设备压力为50mbar,升温至1350℃,通入三甲基铝和氨气,生长4000nm第二
aln层。
60.上述获得的aln薄膜光学显微镜检测下无裂纹;原子力显微镜检测下具有原子级平整表面;xrd测得(002)方向的半宽为90arcsec,(102)方向的半宽为225arcsec。
61.实施例4
62.1.采用物理气相沉积设备,在蓝宝石衬底上生长第一aln层,其中,靶材为单质铝,沉积环境为氩气和氮气的混合气体,控制温度为600℃,沉积厚度为500nm。
63.2.将沉积第一aln层的衬底,转移到高温退火炉,在纯氮气气氛下,通入50sccm的流动氮气,在1800℃条件下退火150min。
64.3.将退火炉温度降低至800℃,关闭流动氮气,退火90min,然后随炉冷却。
65.4.将退火后的第一aln层移至金属有机物化学气相沉积设备中,升温至1250℃,同时通入流量比为20:1的氢气和氨气,烘烤4min,去除第一aln层表面的杂质。
66.5.控制设备压力为50mbar,升温至1350℃,通入三甲基铝和氨气,生长5000nm第二aln层。
67.上述获得的aln薄膜光学显微镜检测下无裂纹;原子力显微镜检测下具有原子级平整表面;xrd测得(002)方向的半宽为75arcsec,(102)方向的半宽为180arcsec。
68.显然,上述实施例仅是为清楚地说明所作的举例,而并非对实施方式的限定。对于所属领域的普通技术人员来说,在上述说明的基础上还可以做出其它不同形式的变化或变动。这里无需也无法对所有的实施方式予以穷举。而由此所引伸出的显而易见的变化或变动仍处于本发明创造的保护范围之中。