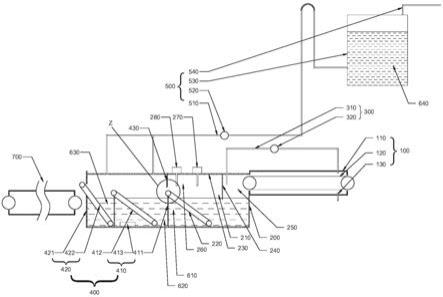
[0001]
本发明涉及使用淬火油进行淬火处理的设备技术领域,具体涉及一种淬火油气再燃烧式水净化的热处理设备。
背景技术:[0002]
热处理设备通常用到加热炉,通过使用天然气等能源产生高温,以加热各种零件。其一个使用场景是轴承滚子的淬火,先使用电热炉对轴承滚子加热,然后(通过加热炉内安装的传送链条等输送机构)再将轴承滚子输送至油槽,轴承滚子落入油槽中的淬火油中,从而快速降温,完成对轴承滚子的淬火,以使得轴承的金相组织全部或部分转变为马氏体,从而提高其硬度,最终保证其耐磨性能。
[0003]
高温的轴承滚子落入淬火油中时,淬火油急剧升温而汽化,同时携裹空气中的水分、粉尘等杂质,如果直接排放到空气中,势必造成环境的严重污染,如果使用现有的成套设备进行处理,成本高、结构复杂。
[0004]
因此,需要一种淬火油气再燃烧式水净化的热处理设备,以克服上述问题。
技术实现要素:[0005]
为了解决上述问题,即为了解决的问题,本发明实施例提供了一种淬火油气再燃烧式水净化的热处理设备,其包括沿工件的流转方向依次布置的加热炉、淬火油槽、清洗装置和回火炉,所述淬火油气再燃烧式水净化的热处理设备还包括淬火油烟回流装置,其中:
[0006]
所述加热炉包括炉体以及设置于所述炉体内的第一工件输送机构、燃烧机构,所述第一工件输送机构用于承载所述工件并且将工件从所述炉体的入口输送至所述炉体的出口,所述燃烧机构布置在所述第一工件输送机构周侧;
[0007]
所述淬火油槽设置于所述炉体的出口下方,用于接收从所述炉体的出口落下的工件,所述淬火油槽内盛装有淬火油,所述淬火油槽内设置有第二工件输送机构,所述第二工件输送机构的工件载入端位于所述炉体的出口下方并且没入淬火油,所述淬火油槽的上方盖合有油槽盖;
[0008]
所述淬火油烟回流装置包括回流管道和回流风机,所述回流管道的第一端穿过所述油槽盖延伸至所述淬火油槽内并且位于淬火油的上方,所述回流风机安装于所述回流管道并且用于产生淬火油槽内的淬火油气流入回流管道的负压,所述回流管道的第二端连通至所述燃烧机构的炉膛内。
[0009]
进一步的,所述清洗装置包括超声波清洗机构,超声波清洗机构包括超声波清洗容器、第三工件输送机构和超声波发生器,所述第二工件输送机构的工件输送端位于所述超声波清洗容器上方或内部,所述超声波发生器固定于所述超声波清洗容器内,所述第三工件输送机构位于所述超声波清洗容器内。
[0010]
进一步的,所述清洗装置还包括位于所述超声波清洗机构与所述回火炉之间的冷水清洗机构,所述冷水清洗机构包括冷水清洗容器和第四工件输送机构,所述冷水清洗容
器内盛装有4℃-8℃的冷水,所述第四工件输送机构用于将所述冷水清洗容器中的水输送至所述回火炉。
[0011]
进一步的,还包括水洗装置,所述水洗装置包括水洗管、水洗风机、水箱和出气管,所述水洗管的第一端连通至所述超声波清洗容器、所述冷水清洗容器中的至少一者的内部,所述水洗管的第二端没入所述水箱中的水中,所述水洗风机安装于所述水洗管,所述出气管的第一端连通至所述水箱内并且位于水面以上,所述出气管的第二端沿背离所述水箱的方向延伸。
[0012]
进一步的,还包括位于所述冷水清洗机构与所述回火炉之间的喷淋装置。
[0013]
进一步的,还包括冷凝百叶,所述冷凝百叶竖直设置并且位于所述淬火油槽与所述超声波清洗容器之间,所述冷凝百叶的每个叶片的高度沿从所述淬火油槽向所述超声波清洗容器的方向逐渐减小。
[0014]
进一步的,所述油槽盖的下方固定有挡板,所述挡板的下端没入淬火油,所述挡板的两侧边分别固定于所述淬火油槽的两内侧壁,所述挡板朝向所述第一工件输送机构的一侧的空间形成油气富集区域,所述挡板背离所述第一工件输送机构的一侧的空间形成无淬火油气区域。
[0015]
进一步的,所述油槽盖上安装有压力风机,所述压力风机的出气口连通至所述无淬火油气区域。
[0016]
进一步的,所述第二工件输送机构为提升机,所述提升机的上方固定有淬火油滴落风机,所述淬火油滴落风机的出风口朝向所述提升机设置。
[0017]
进一步的,所述超声波清洗容器还包括浮油打捞机,所述浮油打捞机的进料口位于所述超声波清洗容器和所述冷水清洗容器中至少一者中的水位下方并且靠近水位线布置,所述浮油打捞机的出油口延伸至所述淬火油槽。
[0018]
本发明实施例的有益效果为:
[0019]
待淬火的工件(如轴承滚子)先经加热炉的加热后在第一工件输送机构的作用下进入淬火槽,经淬火油冷却后零件转变为马氏体,从而提高了硬度,满足了耐磨性;
[0020]
高温工件进入淬火油时,淬火油发生完全燃烧和不完全燃烧,不完全燃烧的产物经淬火油烟回流装置的引流返回至加热炉进行再次燃烧,有效利用了携裹在淬火油气中的油,节约了加热炉的能源消耗,从而避免不完全燃烧的产物排放至空气或者需要借助环保设备的处理,同时淬火油气中的部分有毒、有害物质(如二噁英等)在炉膛内进行燃烧分解(最终产物只有水和二氧化碳),进一步降低了对环境的污染;
[0021]
在水洗装置的作用下,从超声波清洗容器、冷水清洗容器逸出的清洗油气(夹带有油、水的空气)排放前经水过滤和降温,污染物被截留在水中,从而进一步降低对环境的污染,降温作用减轻了温室效应,从而可实现零排放。
附图说明
[0022]
图1为淬火油气再燃烧式水净化的热处理设备一实施例的结构示意图;
[0023]
图2为图1中区域z的局部放大图。
[0024]
图中:
[0025]
100、加热炉;110、炉体;120、第一工件输送机构;130、燃烧机构;
[0026]
200、淬火油槽;210、淬火油槽的上方;220、第二工件输送机构;230、油槽盖;240、挡板;250、淬火油气富集区域;260、无淬火油气区域;270、压力风机;280、淬火油滴落风机;
[0027]
300、淬火油烟回流装置;310、回流管道;320、回流风机;
[0028]
400、清洗装置;410、超声波清洗机构;411、超声波清洗容器;412、第三工件输送机构;413、超声波发生器;420、冷水清洗机构;421、冷水清洗容器;422、第四工件输送机构;430、冷凝百叶;
[0029]
500、水洗装置;510、水洗管;520、水洗风机;530、水箱;540、出气管;
[0030]
610、淬火油;620、超声波清洗用水;630、冷水;640、水洗用水;
[0031]
700、回火炉。
具体实施方式
[0032]
下面参照附图来描述本发明的优选实施方式。本领域技术人员应当理解的是,这些实施方式仅仅用于解释本发明的技术原理,并非旨在限制本发明的保护范围。
[0033]
参见图1和图2,本发明实施例公开了一种淬火油气再燃烧式水净化的热处理设备,其包括沿工件的流转方向依次布置的加热炉100、淬火油槽200、清洗装置400和回火炉700,所述淬火油气再燃烧式水净化的热处理设备还包括淬火油烟回流装置300,其中:
[0034]
所述加热炉包括炉体110以及设置于所述炉体内的第一工件输送机构 120、燃烧机构130(燃烧机构为可为电阻炉,将炉体内加热至850℃左右,在此高温下淬火油得以完全、彻底燃烧,无残留),所述第一工件输送机构用于承载所述工件并且将工件从所述炉体的入口输送至所述炉体的出口,所述燃烧机构布置在所述第一工件输送机构周侧;
[0035]
所述淬火油槽设置于所述炉体的出口下方,用于接收从所述炉体的出口落下的工件,所述淬火油槽内盛装有淬火油610,所述淬火油槽内设置有第二工件输送机构,所述第二工件输送机构220的工件载入端位于所述炉体的出口下方并且没入淬火油,所述淬火油槽的上方210盖合有油槽盖230;
[0036]
所述淬火油烟回流装置包括回流管道310和回流风机320,所述回流管道的第一端穿过所述油槽盖延伸至所述淬火油槽内并且位于淬火油的上方,所述回流风机安装于所述回流管道并且用于产生淬火油槽内的淬火油气流入回流管道的负压,所述回流管道的第二端连通至所述燃烧机构的炉膛内。
[0037]
待淬火的工件(如轴承滚子)先经加热炉的加热后在第一工件输送机构的作用下进入淬火槽,经淬火油冷却后零件转变为马氏体,从而提高了硬度,满足了耐磨性;
[0038]
高温工件进入淬火油时,淬火油发生完全燃烧和不完全燃烧,不完全燃烧的产物经淬火油烟回流装置的引流返回至加热炉进行再次燃烧,有效利用了携裹在淬火油气中的油,节约了加热炉的能源消耗,从而避免不完全燃烧的产物排放至空气或者需要借助环保设备的处理,同时淬火油气中的部分有毒、有害物质(如二噁英等)在炉膛内进行燃烧分解,进一步降低了对环境的污染;
[0039]
在水洗装置500的作用下,从超声波清洗容器(其内部盛装有超声波清洗用水620)、冷水清洗容器逸出的清洗油气(夹带有油、水的空气)排放前经水过滤和降温,污染物被截留在水中,从而进一步降低对环境的污染,降温作用减轻了温室效应,从而可实现零排放。
[0040]
另外,所述清洗装置包括超声波清洗机构410,超声波清洗机构包括超声波清洗容器411、第三工件输送机构412和超声波发生器413,所述第二工件输送机构的工件输送端位于所述超声波清洗容器上方或内部,所述超声波发生器固定于所述超声波清洗容器内,所述第三工件输送机构位于所述超声波清洗容器内。通过超声波清洗,保证对附着在工件表面的淬火油的清洗效果
[0041]
需要说明的是,所述清洗装置还包括位于所述超声波清洗机构与所述回火炉之间的冷水清洗机构420,所述冷水清洗机构包括冷水清洗容器421和第四工件输送机构422,所述冷水清洗容器内盛装有4℃-8℃的冷水630,所述第四工件输送机构用于将所述冷水清洗容器中的水输送至所述回火炉。冷水清洗的目的是用于降低参与奥氏体,保证滚子的韧性,适用于各种工况,避免表面裂纹和脱落。
[0042]
还需要说明的是,本发明实施例还可包括水洗装置,所述水洗装置包括水洗管510、水洗风机520、水箱530(内部盛装有水洗用水640)和出气管 540,所述水洗管的第一端连通至所述超声波清洗容器、所述冷水清洗容器中的至少一者的内部,所述水洗管的第二端没入所述水箱中的水中,所述水洗风机安装于所述水洗管,所述出气管的第一端连通至所述水箱内并且位于水面以上,所述出气管的第二端沿背离所述水箱的方向延伸。清洗后产生的油气通过其上安装有水洗风机的管道连通至水箱中的水中,经水的过滤和降温后排出,零污染、低温度排放。
[0043]
另外,本发明实施例还可包括位于所述冷水清洗机构与所述回火炉之间的喷淋装置。通过喷淋装置的喷淋,在工件回火前完成最终的清洗。此处的喷淋装置可选用能够喷水的喷头。
[0044]
本发明实施例还可包括冷凝百叶430,所述冷凝百叶竖直设置并且位于所述淬火油槽与所述超声波清洗容器之间,所述冷凝百叶的每个叶片的高度沿从所述淬火油槽向所述超声波清洗容器的方向逐渐减小。超声波清洗的水汽化后遇到百叶冷凝后回流至超声波清洗容器,继续参与超声波清洗,避免进入淬火油槽后影响淬火的正常进行。
[0045]
进一步需要说明的是,所述油槽盖的下方固定有挡板240,所述挡板的下端没入淬火油,所述挡板的两侧边分别固定于所述淬火油槽的两内侧壁,所述挡板朝向所述第一工件输送机构的一侧的空间形成油气富集区域250,所述挡板背离所述第一工件输送机构的一侧的空间形成无淬火油气区域260。
[0046]
刚开始淬火时产生的大量油烟被约束在挡板内不能进入后边,限制在局部狭小的油气富集区域;由于加热炉温度高、压力大,因此也不会前窜至加热炉,进一步限制在该狭小的油气富集区;回流管道上安装回流风机,在回流风机产生的负压的作用下油气富集区域的油气返回至加热炉再次燃烧。
[0047]
另外,所述油槽盖上安装有压力风机270,所述压力风机的出气口连通至所述无淬火油气区域。淬火油槽上方安装压力风机,形成风幕,不过避免淬火油气压力过大影响淬火油槽与油槽盖之间的密封性。
[0048]
另外,所述第二工件输送机构的一种具体方式为提升机,所述提升机的上方固定有淬火油滴落风机280,所述淬火油滴落风机的出风口朝向所述提升机设置。从淬火油槽出来的提升机上方安装风机,促进淬火油滴落,减少进入超声波清洗前附着在零件表面的淬火油。
[0049]
还需要说明的是,所述超声波清洗容器还包括浮油打捞机,所述浮油打捞机的进料口位于所述超声波清洗容器和所述冷水清洗容器中至少一者中的水位下方并且靠近水位线布置。通过浮油打捞机实现超声波清洗用水、冷水中的油水分离,分离出来的淬火油、水可循环使用,节约能源。另外,浮油打捞机为目前市场所应用的成熟技术,如专利号为“201810886790.6”的发明专利申请,故不再就其具体采用的型号及相应结构做进一步说明。浮油打捞机的出油口延伸至所述淬火油槽,从而使得分离出来的淬火油返回至淬火油槽,循环再利用。
[0050]
最后需要说明的是,上述的第一工件输送机构可采用由传动辊驱动的金属网带,第二工件输送机构、第三工件输送机构和第四工件输送机构不仅要实现工件的水平转移还要实现工件的提升,可选用提升机,当然,本领域技术人员可知的是,还可采用其他的结构,不再一一列举。
[0051]
需要说明的是,在本发明的描述中,术语“中心”、“上”、“下”、“左”、“右”、“竖直”、“水平”、“内”、“外”等指示方向或位置关系的术语是基于附图所示的方向或位置关系,这仅仅是为了便于描述,而不是指示或暗示所述装置或元件必须具有特定的方位、以特定的方位构造和操作,因此不能理解为对本发明的限制。此外,术语“第一”、“第二”、“第三”仅用于描述目的,而不能理解为指示或暗示相对重要性。
[0052]
此外,还需要说明的是,在本发明的描述中,除非另有明确的规定和限定,术语“安装”、“相连”、“连接”应做广义理解,例如,可以是固定连接,也可以是可拆卸连接,或一体地连接;可以是机械连接,也可以是电连接;可以是直接相连,也可以通过中间媒介间接相连,可以是两个元件内部的连通。对于本领域技术人员而言,可根据具体情况理解上述术语在本发明中的具体含义。
[0053]
术语“包括”或者任何其它类似用语旨在涵盖非排他性的包含,从而使得包括一系列要素的过程、物品或者设备/装置不仅包括那些要素,而且还包括没有明确列出的其它要素,或者还包括这些过程、物品或者设备/装置所固有的要素。
[0054]
至此,已经结合附图所示的优选实施方式描述了本发明的技术方案,但是,本领域技术人员容易理解的是,本发明的保护范围显然不局限于这些具体实施方式。在不偏离本发明的原理的前提下,本领域技术人员可以对相关技术特征作出等同的更改或替换,这些更改或替换之后的技术方案都将落入本发明的保护范围之内。