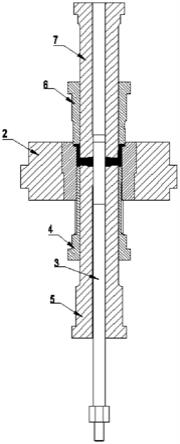
1.本实用新型涉及改善粉末冶金成型技术领域,具体涉及一种皮带轮的粉末冶金模具。
背景技术:2.皮带轮坯体如果采用机械加工的生产模式进行生产,不仅加工的工艺复杂,而且材料的浪费级为严重,并且因为所设齿型本体与法兰档片中属于段差式的一体结构设计,因而在机械加工时尺寸精度较难有效的精准掌控,容易造成产品的质量不良与报废品的产生。
技术实现要素:3.针对现有技术中存在的不足,本实用新型提供一种皮带轮的粉末冶金模具,大幅度降低加工复杂程度,节省了加工工时,避免了材料量费与产品精度的稳定。本实用新型采用的技术方案是:
4.一种皮带轮的粉末冶金模具,其中:包括成形阴模、成形芯棒、成形下一冲、成形下二冲、成形上一冲和成形上二冲,所述成形芯棒上套设成形下二冲,所述成形下二冲上套设成形下一冲,所述成形下一冲上套设成形阴模,所述成形阴模内设置齿形形腔和法兰形腔,所述法兰形腔设置在齿形形腔外周并和齿形形腔同心,所述成形芯棒顶端套设成形上二冲,所述成形上二冲下端套设成形上一冲,所述成形下二冲和成形下一冲套设后进入齿形形腔,所述成形上一冲和成形上二冲套设后进入法兰形腔。
5.优选的是,所述的皮带轮的粉末冶金模具,其中:所述成形阴模上端面设置法兰形腔,所述法兰形腔设置在齿形形腔外周并和齿形形腔同心,所述齿形形腔和法兰形腔(之间形成段差式形腔,所述段差式形腔的段差面上反向凸出设置形腔段差填料斜面,所述齿形形腔上端面设置第一外圆角。
6.优选的是,所述的皮带轮的粉末冶金模具,其中:所述成形芯棒包括成形芯棒逃料段和设置在成形芯棒逃料段顶端的成形芯棒有效段,所述成形芯棒逃料段直径比成形芯棒有效段直径小0.1~0.5mm,所述成形芯棒逃料段底部设置成形芯棒板手位和成形芯棒组配螺牙段,所述成形芯棒有效段长度为75~100mm。
7.优选的是,所述的皮带轮的粉末冶金模具,其中:所述成形下一冲包括成形下一底座、设置在成形下一底座上的成形下一冲头和成形下一贯穿孔,所述成形下一底座和成形下一冲头连接处设置第二外圆角,所述成形下一冲头外周为齿形,所述成形下一冲头的齿形轮廓与齿形形腔轮廓相同,所述成形下一冲头包括成形下一逃料段和设置在成形下一逃料段上的成形下一有效段,所述成形下一贯穿孔包括成形下一内孔有效段和成形下一内孔逃料段,所述成形下一内孔有效段设置在成形下一有效段内,所述成形下一内孔逃料段设置在成形下一逃料段内。
8.优选的是,所述的皮带轮的粉末冶金模具,其中:所述第二外圆角的半径值为2.5~
5mm,所述成形下一有效段4
‑2‑
1长度为10~25mm,所述成形下一内孔有效段4
‑4‑
1长度为10~25mm,所述成形下一内孔逃料段4
‑4‑
2直径比所述成形下一内孔有效段4
‑4‑
1大0.1~0.5mm。
9.优选的是,所述的皮带轮的粉末冶金模具,其中:所述成形下二冲5包括成形下二底座5
‑
1、设置在成形下二底座5
‑
1上的成形下二冲头5
‑
2和成形下二贯穿孔5
‑
4,所述成形下二底座5
‑
1和成形下二冲头5
‑
2交接处设置第三外圆角5
‑
3,所述成形下二冲头5
‑
2包括成形下二逃料段5
‑2‑
2和设置在成形下二逃料段5
‑2‑
2上的成形下二有效段5
‑2‑
1,所述成形下二贯穿孔5
‑
4包括成形下二内孔有效段5
‑4‑
1和成形下二内孔逃料段5
‑4‑
2,所述成形下二内孔有效段5
‑4‑
1设置在成形下二有效段5
‑2‑
1内,所述成形下二内孔逃料段5
‑4‑
2设置在成形下二逃料段5
‑2‑
2内;所述第三外圆角5
‑
3半径值为2.5~5mm,所述成形下二有效段5
‑2‑
1外径与成形下一内孔有效段4
‑4‑
1相同且长度为15~30mm,所述成形下二有效段5
‑2‑
1外径比成形下二逃料段5
‑2‑
2大0.1~0.5mm,所述成形下二内孔有效段5
‑4‑
1长度为15~30mm,且内孔直径尺寸和成形芯棒有效段(3
‑
1)外径相同,所述成形下二内孔逃料段5
‑4‑
2直径比所述成形下二内孔有效段5
‑4‑
1大0.1~0.5mm。
10.优选的是,所述的皮带轮的粉末冶金模具,其中:所述成形上一冲6包括成形上一底座6
‑
1和成形上一冲头6
‑
2,所述成形上一底座6
‑
1和成形上一冲头6
‑
2交接处设置第四外圆角6
‑
3,所述成形上一冲头6
‑
2包括成形上一逃料段6
‑2‑
2和设置于成形上一逃料段6
‑2‑
2上端的成形上一有效段6
‑2‑
1,所述成形上一冲6中间设置成形上一贯穿孔6
‑
4,所述成形上一贯穿孔6
‑
4包括成形上一内孔有效段6
‑4‑
1和成形上一内孔逃料段6
‑4‑
2。
11.优选的是,所述的皮带轮的粉末冶金模具,其中:所述第四外圆角6
‑
3半径值为2.5~5mm,所述成形上一内孔有效段6
‑4‑
1长度为15~30mm,所述成形上一内孔逃料段6
‑4‑
2直径比所述成形上一内孔有效段6
‑4‑
1大0.1~0.5mm,所述成形上一有效段6
‑2‑
1外径与法兰形腔2
‑1‑
2直径相同,成形上一有效段6
‑2‑
1长度为15~30mm,所述成形上一有效段6
‑2‑
1比成形上一逃料段6
‑2‑
2直径大0.1~0.5mm。
12.优选的是,所述的皮带轮的粉末冶金模具,其中:所述成形上二冲7包括成形上二底座7
‑
1和设置在成形上二底座7
‑
1上的成形上二冲头7
‑
2,所述成形上二底座7
‑
1和成形上二冲头7
‑
2交接处设置第五外圆角7
‑
3,所述成形上二冲头7
‑
2包括成形上二逃料段7
‑2‑
2和设置在成形上二逃料段7
‑2‑
2上的成形上二有效段7
‑2‑
1,所述成形上二有效段7
‑2‑
1外端设置上二冲拔模斜度面7
‑2‑
3,所述成形上二冲7中间设置成形上二贯穿孔7
‑
4,所述成形上二贯穿孔7
‑
4包括成形上二内孔有效段7
‑4‑
1和成形上二内孔逃料段7
‑4‑
2,所述成形上二内孔有效段(7
‑4‑
1)设置在成形上二有效段7
‑2‑
1内,所述成形上二内孔逃料段7
‑4‑
2设置在成形上二逃料段7
‑2‑
2内。
13.优选的是,所述的皮带轮的粉末冶金模具,其中:所述第五外圆角7
‑
3半径值为2.5~5mm,所述成形上二有效段7
‑2‑
1和成形上一内孔有效段6
‑4‑
1外径相同,所述成形上二逃料段7
‑2‑
2外径比成形上二有效段7
‑2‑
1小0.1~0.5mm,所述成形上二内孔有效段7
‑4‑
1长度为15~30mm,所述成形上二内孔逃料段7
‑4‑
2圆径比所述成形上二内孔有效段7
‑4‑
1大0.1~0.5mm。
14.发明的优点:本实用新型的皮带轮的粉末冶金模具生产的皮带轮坯体省去了繁琐的机械加工工艺流程,皮带轮坯体属于模具压制成形,各段差面的所需的产品密度与产品尺寸皆可依据实际的生产情况进行调整,提供了皮带轮坯体的稳定、可靠、并且快速的生产
方式,降低了生产成本,提高了生产时效,提升了整体市场的竞争力。
附图说明
15.图1为本实用新型皮带轮坯体的剖面图。
16.图2为本实用新型皮带轮坯体的仰视图。
17.图3为本实用新型成形阴模的俯视图。
18.图4为本实用新型成形阴模的剖视图。
19.图5为本实用新型成形芯棒的正视图。
20.图6为本实用新型成形下一冲的剖视图。
21.图7为本实用新型成形下二冲的剖视图。
22.图8为本实用新型成形上一冲的剖视图。
23.图9为本实用新型图8的b部位详图。
24.图10为本实用新型成形上二冲的剖视图。
25.图11为本实用新型成形模具装配图。
26.图12为本实用新型皮带轮坯体成形工艺的分段示意图。
具体实施方式
27.下面结合具体附图和实施例对本实用新型作进一步说明。
28.实施例1
29.皮带轮坯体1为一圆柱体在本体上设有一处皮带轮齿型本体(1
‑
1),并在齿形面上设有一齿型轮廓1
‑1‑
1,在齿型端面上设有一法兰档片1
‑
2,该法兰档片1
‑
2与皮带轮齿形本体1
‑
1为一体式结构,且于所设皮带轮齿形本体1
‑
1中齿型轮廓与法兰档片1
‑
2交接处设有半径为0.3~0.7的内圆角1
‑
3,并于法兰档片1
‑
2的外径圆1
‑2‑
1底面到齿形轮廓1
‑1‑
1中的齿顶径1
‑1‑
2中有一处角度为12度到18度的除料斜面1
‑
4,在皮带轮坯体1上端面中设一处具体深度为17~19mm并含有1.5~3
∘
拔模斜度1
‑5‑
1的段差凹台1
‑
5,其段差凹台1
‑
5的2段具体段差为0.5~1.5mm 1
‑5‑
2,并于段差凹台1
‑
5底部端面上设有半径值0.7~1.3mmm的圆角1
‑5‑
3、1
‑5‑
4,在皮带轮坯体1下底面中设一处具体深度1.7~2.3mm的凹槽1
‑
6,该凹槽1
‑
6具有拔模斜度12~18
∘1‑6‑
1且于凹槽1
‑
6底端设有半径值为0.7~1.3mm的圆角1
‑6‑
2,皮带轮坯体1中间部位设有一处贯穿的传动轴装配孔1
‑
7,在皮带轮坯体1上端面与法兰档面1
‑
2中所设外圆径1
‑2‑
1及段差凹台1
‑
5交接处及皮带轮坯体1下底面与所设传动轴装配孔1
‑
7交接处中均设有深度为0.3~0.7mm,角度为25~45
∘
,且含有一个0.1~0.5平面的倒角1
‑2‑
2、1
‑5‑
5、1
‑
8,由上述皮带轮坯体1中的各项特征中可以看出,该皮带轮坯体1如果采用机械加工的生产模式进行生产,不仅加工的工艺复杂,而且材料的浪费级为严重,并且因为所设齿型本体1
‑
1与法兰档片1
‑
2中属于段差式的一体结构设计,因而在机械加工时尺寸精度较难有效的精准掌控,容易造成产品的质量不良与报废品的产生。
30.粉末冶金工艺中,可以藉由各模具的相互交错与搭配的模式,一次成形出与所述皮带轮坯体1最终形状级为相符的产品。进而很大幅度的降低加工复杂程度与节省了加工工时的情况下还避免了材料量费与产品精度的稳定。
31.如图1~12所示,本实施例提供一种皮带轮的粉末冶金模具,其中:包括成形阴模
2、成形芯棒3、成形下一冲4、成形下二冲5、成形上一冲6和成形上二冲7,所述成形芯棒3上套设成形下二冲5,所述成形下二冲5上套设成形下一冲4,所述成形下一冲4上套设成形阴模2,所述成形阴模2内设置齿形形腔 2
‑1‑
1和法兰形腔2
‑1‑
,所述法兰形腔2
‑1‑
2设置在齿形形腔 2
‑1‑
1外周并和齿形形腔2
‑1‑
1同心,所述成形芯棒3顶端套设成形上二冲7,所述成形上二冲7下端套设成形上一冲6,所述成形下二冲5和成形下一冲4套设后进入齿形形腔 2
‑1‑
1,所述成形上一冲6和成形上二冲7套设后进入法兰形腔2
‑1‑
2。
32.其中:所述成形阴模2上端面设置法兰形腔2
‑1‑
2,所述法兰形腔2
‑1‑
2设置在齿形形腔 2
‑1‑
1外周并和齿形形腔2
‑1‑
1同心,所述齿形形腔2
‑1‑
1和法兰形腔2
‑1‑
2之间形成段差式形腔2
‑
1,所述段差式形腔2
‑
1的段差面上反向凸出设置形腔段差填料斜面2
‑1‑
4,所述齿形形腔2
‑1‑
1上端面设置第一外圆角2
‑1‑
5。
33.其中:所述成形芯棒3包括成形芯棒逃料段3
‑
2和设置在成形芯棒逃料段3
‑
2顶端的成形芯棒有效段3
‑
1,所述成形芯棒逃料段3
‑
2直径比成形芯棒有效段3
‑
1直径小0.1~0.5mm,所述成形芯棒逃料段3
‑
2底部设置成形芯棒板手位3
‑
3和成形芯棒组配螺牙段3
‑
4,所述成形芯棒有效段3
‑
1长度为75~100mm。
34.其中:所述成形下一冲4包括成形下一底座4
‑
1、设置在成形下一底座4
‑
1上的成形下一冲头4
‑
2和成形下一贯穿孔4
‑
4,所述成形下一底座4
‑
1和成形下一冲头4
‑
2连接处设置第二外圆角4
‑
3,所述成形下一冲头4
‑
2外周为齿形,所述成形下一冲头4
‑
2的齿形轮廓与齿形形腔 2
‑1‑
1轮廓相同,所述成形下一冲头4
‑
2包括成形下一逃料段4
‑2‑
2和设置在成形下一逃料段4
‑2‑
2上的成形下一有效段4
‑2‑
1,所述成形下一贯穿孔4
‑
4包括成形下一内孔有效段4
‑4‑
1和成形下一内孔逃料段4
‑4‑
2,所述成形下一内孔有效段4
‑4‑
1设置在成形下一有效段4
‑2‑
1内,所述成形下一内孔逃料段4
‑4‑
2设置在成形下一逃料段4
‑2‑
2内。
35.其中:所述第二外圆角4
‑
3的半径值为2.5~5mm,所述成形下一有效段4
‑2‑
1长度为10~25mm,所述成形下一内孔有效段4
‑4‑
1长度为10~25mm,所述成形下一内孔逃料段4
‑4‑
2直径比所述成形下一内孔有效段4
‑4‑
1大0.1~0.5mm。
36.其中:所述成形下二冲5包括成形下二底座5
‑
1、设置在成形下二底座5
‑
1上的成形下二冲头5
‑
2和成形下二贯穿孔5
‑
4,所述成形下二底座5
‑
1和成形下二冲头5
‑
2交接处设置第三外圆角5
‑
3,所述成形下二冲头5
‑
2包括成形下二逃料段5
‑2‑
2和设置在成形下二逃料段5
‑2‑
2上的成形下二有效段5
‑2‑
1,所述成形下二贯穿孔5
‑
4包括成形下二内孔有效段5
‑4‑
1和成形下二内孔逃料段5
‑4‑
2,所述成形下二内孔有效段5
‑4‑
1设置在成形下二有效段5
‑2‑
1内,所述成形下二内孔逃料段5
‑4‑
2设置在成形下二逃料段5
‑2‑
2内;所述第三外圆角5
‑
3半径值为2.5~5mm,所述成形下二有效段5
‑2‑
1外径与成形下一内孔有效段4
‑4‑
1相同且长度为15~30mm,所述成形下二有效段5
‑2‑
1外径比成形下二逃料段5
‑2‑
2大0.1~0.5mm,所述成形下二内孔有效段5
‑4‑
1长度为15~30mm,且内孔直径尺寸和成形芯棒有效段3
‑
1外径相同,所述成形下二内孔逃料段5
‑4‑
2直径比所述成形下二内孔有效段5
‑4‑
1大0.1~0.5mm。
37.其中:所述成形上一冲6包括成形上一底座6
‑
1和成形上一冲头6
‑
2,所述成形上一底座6
‑
1和成形上一冲头6
‑
2交接处设置第四外圆角6
‑
3,所述成形上一冲头6
‑
2包括成形上一逃料段6
‑2‑
2和设置于成形上一逃料段6
‑2‑
2上端的成形上一有效段6
‑2‑
1,所述成形上一冲6中间设置成形上一贯穿孔6
‑
4,所述成形上一贯穿孔6
‑
4包括成形上一内孔有效段6
‑4‑
1和成形上一内孔逃料段6
‑4‑
2。
38.其中:所述第四外圆角6
‑
3半径值为2.5~5mm,所述成形上一内孔有效段6
‑4‑
1长度为15~30mm,所述成形上一内孔逃料段6
‑4‑
2直径比所述成形上一内孔有效段6
‑4‑
1大0.1~0.5mm,所述成形上一有效段6
‑2‑
1外径与法兰形腔2
‑1‑
2直径相同,成形上一有效段6
‑2‑
1长度为15~30mm,所述成形上一有效段6
‑2‑
1比成形上一逃料段6
‑2‑
2直径大0.1~0.5mm。
39.其中:所述成形上二冲7包括成形上二底座7
‑
1和设置在成形上二底座7
‑
1上的成形上二冲头7
‑
2,所述成形上二底座7
‑
1和成形上二冲头7
‑
2交接处设置第五外圆角7
‑
3,所述成形上二冲头7
‑
2包括成形上二逃料段7
‑2‑
2和设置在成形上二逃料段7
‑2‑
2上的成形上二有效段7
‑2‑
1,所述成形上二有效段7
‑2‑
1外端设置上二冲拔模斜度面7
‑2‑
3,所述成形上二冲7中间设置成形上二贯穿孔7
‑
4,所述成形上二贯穿孔7
‑
4包括成形上二内孔有效段7
‑4‑
1和成形上二内孔逃料段7
‑4‑
2,所述成形上二内孔有效段7
‑4‑
1设置在成形上二有效段7
‑2‑
1内,所述成形上二内孔逃料段7
‑4‑
2设置在成形上二逃料段7
‑2‑
2内。
40.其中:所述第五外圆角7
‑
3半径值为2.5~5mm,所述成形上二有效段7
‑2‑
1和成形上一内孔有效段6
‑4‑
1外径相同,所述成形上二逃料段7
‑2‑
2外径比成形上二有效段7
‑2‑
1小0.1~0.5mm,所述成形上二内孔有效段7
‑4‑
1长度为15~30mm,所述成形上二内孔逃料段7
‑4‑
2圆径比所述成形上二内孔有效段7
‑4‑
1大0.1~0.5mm。
41.成形阴模2中间设有一处与皮带轮坯体1所述齿形轮廓1
‑1‑
1相同且贯穿的齿形形腔 2
‑1‑
1,并在成形阴模2上端面设一处与皮带轮坯体1的法兰档片1
‑
2中所设外圆径1
‑2‑
1尺寸相同且具体深度为4~8mm的法兰形腔2
‑1‑
2,该法兰形腔2
‑1‑
2与齿形型腔为同心圆,此时齿形形腔2
‑1‑
1与法兰形腔2
‑1‑
2会形成一个段差式形腔2
‑
1,在其段差式形腔2
‑
1的段差面上设一处起点为齿形形腔齿顶径2
‑1‑
3终点为法兰形腔2
‑1‑
2且角度与皮带轮坯体1中所设除料斜面1
‑
4角度相符但反向凸出的形腔段差填料斜面2
‑1‑
4,并且于齿形上端面上设有与皮带轮坯体1中所设圆角1
‑
3尺寸相同的第一外圆角2
‑1‑
5。
42.成形芯棒有效段3
‑
1为外径尺寸比皮带轮坯体1中所设传动轴装配孔1
‑
7圆径相同且具体长度为75~100mm圆柱体。
43.成形下一冲头4
‑
2为齿形本体,其分为齿形轮廓与成形阴模2中所设的齿形形腔 2
‑1‑
1轮廓相同且具体长度为10~25mm的成形下一有效段4
‑2‑
1,与齿形轮廓比成形下一有效段4
‑2‑
1的齿形轮廓小0.1~0.5mm的成形下一逃料段4
‑2‑
2。
44.成形下二有效段5
‑2‑
1顶端设有与皮带轮坯体1中所设凹槽1
‑
6形状相符,但为凸出的下二面取成形段5
‑2‑
3,并且在成形下二冲5中间部位设一处包含有成形下二内孔有效段5
‑4‑
1与成形下二内孔逃料段5
‑4‑
2的成形下二贯穿孔5
‑
4,成形下二内孔有效段5
‑4‑
1具体长度为15~30mm,且内孔圆径尺寸与成形芯棒有效段3
‑
1为外径尺寸相符,而成形下二内孔逃料段5
‑4‑
2圆径则要比所设成形下二内孔有效段5
‑4‑
1要大0.1~0.5mm,成形下二冲头5
‑
2顶端与成形下二内孔有效段5
‑4‑
1所设圆径交接处设有与皮带轮坯体1中所设倒角1
‑
8形状相符,但为凸出的上一面取成形段5
‑4‑
3。
45.成形上一内孔有效段6
‑4‑
1内孔圆径尺寸与带轮坯体1中所设段差凹1
‑
5最大圆径相符,而成形上一内孔逃料段6
‑4‑
2圆径则要比所设成形上一内孔有效段6
‑4‑
1要大0.1~0.5mm,成形上一冲头6
‑
2顶端与成形上一冲有效段6
‑2‑
1及成形上一内孔有效段6
‑4‑
1所设圆径交接处均设有与皮带轮坯体1中所设倒角1
‑2‑
2、1
‑5‑
5形状相符,但为凸出的上一面取成形段6
‑2‑
3、6
‑2‑
4。
46.成形模具装配实施方式:成形芯棒3利用所设的成形芯棒组配螺牙段3
‑
4锁固于成形压机,将成形下二冲4经由所设的成形下二贯穿孔5
‑
4通过成形芯棒2由上往下套入到成形芯棒2中,并固定于成形压机上,此时成形下二冲4所设成形下二内孔有效段5
‑4‑
1圆径会与成形芯棒3所设成形芯棒有效段3
‑
1圆径相互贴合,再将成形下一冲4经由所设的成形下一贯穿孔4
‑
4通过成形下二冲5所设成形下二冲头5
‑
2由上往下套入到成形下二冲5中,并固定于成形压机上,此时成形下一冲3所设成形下一内孔有效段3
‑4‑
1圆径会与成形下二冲4所设成形下二有效段5
‑2‑
1圆径相互贴合,将成形阴模2所设齿形形腔 2
‑1‑
1与成形下一冲4成形下一有效段4
‑2‑
1的齿形轮廓相互配合后套入成形下一冲4所设成形下一冲头4
‑
2中,此时成形阴模2所设齿形形腔将与成形下一有效段4
‑2‑
1的齿形轮廓相互贴合,将成形上二冲7所设冲头7
‑
2朝向成形阴模2并利用成形上二贯穿孔7
‑
4中所设成形上二内孔有效段7
‑4‑
1对齐成形芯棒有效段3
‑
1圆径后装配于成形压机中,将成形上一冲6所设冲头6
‑
2朝向成形阴模2后利用所设成形上一贯穿孔6
‑
4对齐成形上二冲冲头7
‑
2后由下往上套入到成形上二冲中,并将成形上一冲冲头6
‑
2所设有效段外径6
‑2‑
1对齐成形阴模2所设法兰形腔2
‑1‑
2圆径后由上往下套入到成形阴模中并固定于成形压机上。
47.粉末冶金在成形工艺时依成形压机的作动方式可分为填料、成形、与出模等步骤,而经由上述成形模具的设计中,可把皮带轮坯体1分为法兰段差位1
‑
10、齿部段差位1
‑
11与中间段差位1
‑
12等3个段差位,在成形压机进入到填料与成形步骤时便可以依各段差部位所需填粉量与成形尺寸藉由成形压机对模具高度的调整,对皮带轮坯体1的成形密度与成形尺寸进行设定,进而生产出密度与尺寸皆符合要求且可靠性高的皮带轮坯体1。
48.本实用新型的皮带轮的粉末冶金模具生产的皮带轮坯体省去了繁琐的机械加工工艺流程,皮带轮坯体属于模具压制成形,各段差面的所需的产品密度与产品尺寸皆可依据实际的生产情况进行调整,提供了皮带轮坯体的稳定、可靠、并且快速的生产方式,降低了生产成本,提高了生产时效,提升了整体市场的竞争力。
49.最后所应说明的是,以上具体实施方式仅用以说明本实用新型的技术方案而非限制,尽管参照实例对本实用新型进行了详细说明,本领域的普通技术人员应当理解,可以对本实用新型的技术方案进行修改或者等同替换,而不脱离本实用新型技术方案的精神和范围,其均应涵盖在本实用新型的权利要求范围当中。