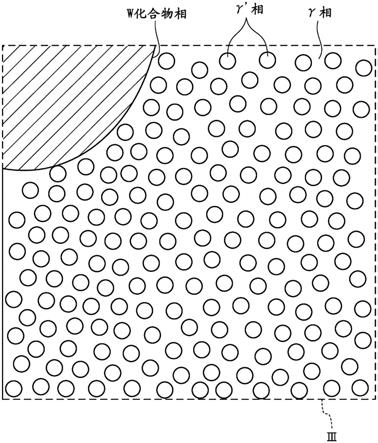
co基合金结构体及其制造方法
技术领域
1.本发明涉及co基合金结构体及其制造方法。
背景技术:2.钴(co)基合金与镍(ni)基合金一起是代表性的耐热合金材料,也被称为超合金,广泛用于例如涡轮(燃气轮机、蒸汽轮机等)的高温构件。另外,co基合金与ni基合金相比,材料成本高,但耐腐蚀性和耐磨耗性优异,具有容易固溶强化的特性。因此,co基合金一直以来应用于涡轮静叶片、燃烧器构件、摩擦搅拌接合用工具等。
3.关于这样的co基合金,例如已知有专利文献1的co基合金。具体而言,专利文献1中公开了一种co基合金,其具有:具有fcc结构的以co为主体的基体相(γ相)和由具有以原子比计co3(al,w)的l12结构的fcc结构的金属间化合物构成且在基体相的晶粒内析出的析出相(γ
′
相)。
4.现有技术文献
5.专利文献
6.专利文献1:日本特许第4996468号公报
技术实现要素:7.发明所要解决的课题
8.在专利文献1的co基合金中,析出相(γ
′
相)的粒径为50nm~1μm,且γ
′
相的析出量设定为40~85体积%。而且,在该文献的各图(特别是图2、图3)中,可看到粒径为1μm以下的具有立方体形状的γ
′
相的粒子在基体相(γ相)中析出。另外,在该文献中还记载了在时效处理中析出的析出相(γ
′
相)的平均粒径为150nm以下(参照该文献的段落0006)。
9.然而,即使参照专利文献1的各图,也可掌握粒径小于50nm的γ
′
相几乎未析出。进而,存在γ
′
相的粒子彼此的距离大于100nm的部位。即,在上述co基合金中,微细化至极限的γ
′
相相对于基体相(γ相)大量析出而未分散(均匀地配置)。因此,在上述co基合金材料中,难以得到基于以粒径小于50nm的方式微细化至极限的γ
′
相的析出强化的作用,作为其结果是,基于该作用的机械特性(特别是拉伸强度和屈服强度)变得不充分。
10.本公开是鉴于这一点而完成的,其目的在于提高co基合金结构体的机械特性。
11.用于解决课题的方法
12.为了达成上述目的,第一公开为一种co基合金结构体,具有以质量比计al:0.1~10%、w:3.0~45%且两者的合计小于50%且余量除了不可避免的杂质为co的组成。co基合金结构体具有具备fcc结构的以co为主体的基体相(γ相)以及由具有以原子比计co3(al,w)或〔(co,x)3(al,w,z)〕的l12结构的fcc结构的金属间化合物构成且在基体相中以分散的状态析出的析出相(γ
′
相)。而且,析出相(γ
′
相)以如下方式构成:粒径为10nm~1μm,析出相(γ
′
相)的粒子均匀地配置而析出,且析出量为40~85体积%。
13.在该第一公开中,以如下方式构成:在基体相(γ相)中以分散的状态析出的析出
相(γ
′
相)的粒径为10nm~1μm,且γ
′
相的析出量为40~85体积%。在该构成中,包含微细化至极限的粒径的γ
′
相相对于基体相(γ相)大量析出,成为分散的状态。其结果是,在co基合金结构体的组织内,基体相(γ相)与多个γ
′
相的界面的总表面积相对增加且γ
′
相的粒子彼此的距离相对缩小。即,在基体相(γ相)中,包含微细化至极限的粒子的γ
′
相成为均匀地析出强化的状态。而且,通过该析出强化,尤其提高高温下的机械特性。因此,在第一公开中,能够提高co基合金结构体的机械特性。
14.第二公开是在第一公开中析出相(γ
′
相)的粒径为10nm以上且小于50nm的范围。
15.在该第二公开中,微细化的γ
′
相相对于基体相(γ相)大量析出,成为分散的状态,由此,由γ
′
相带来的析出强化的作用被强化,能够进一步提高co基合金结构体的机械特性。
16.第三公开是在第一或第二公开中co基合金结构体作为由粉末构成的层叠造型体而构成。
17.在该第三公开中,在由粉末构成的层叠造型体的粒界和/或粒内,w化合物等析出物在基体相(γ相)中以微细的状态析出且成为均匀地分散的状态。进而,在基体相(γ相)中,成为在上述析出物的周围分散有多个微细的γ
′
相的状态。这样,在作为由粉末构成的层叠造型体而构成的co基合金结构体中,产生由上述析出物和多个微细的γ
′
相双方的析出强化带来的作用。其结果是,在第三公开中,能够进一步提高co基合金结构体的机械特性。
18.第四公开是在第一或第二公开中co基合金结构体作为由粉末构成的粉末hip锻造体而构成。
19.在该第四公开中,能够提高co基合金结构体的机械特性。
20.第五公开是在第三或第四公开中粉末具有以质量比计al:2~5%、w:17~25%、c:0.05~0.15%、ni:20~35%、cr:6~10%、ta:3~8%且余量除了不可避免的杂质为co的组成。
21.在该第五公开中,如果是由具有上述组成的粉末构成的层叠造型体,则能够使析出相(γ
′
相)的粒径微细化。其结果是,能够进一步提高co基合金结构体的机械特性。
22.第六公开是在第一或第二公开中co基合金结构体作为锻造体而构成。
23.在该第六公开中,能够提高co基合金结构体的机械特性。
24.第七公开是第一或第二公开的co基合金结构体的制造方法,具有对co基合金结构体的前体实施固溶处理的固溶处理工序以及对实施了固溶处理的co基合金结构体的前体实施时效处理的时效处理工序。时效处理工序包括第一时效处理工序和在第一时效处理工序之后实施的第二时效处理工序。而且,第二时效处理工序的时效温度设定为比第一时效处理工序的时效温度高。
25.在该第七公开中,时效处理工序中,在第一时效处理工序之后实施的第二时效处理工序的时效温度设定为比第一时效处理工序的时效温度高。通过该设定,能够在co基合金结构体的组织内将γ
′
相的粒径微细化至极限。进而,在co基合金结构体的组织内难以产生微观偏析,在基体相(γ相)中γ
′
相均匀地分散。其结果是,由γ
′
相带来的析出强化的作用被强化,能够进一步提高co基合金结构体的机械特性。
26.第八公开是在第七公开的co基合金结构体的制造方法中,固溶处理的温度为1100
℃以上,第一时效处理工序的时效温度为500~700℃,第二时效处理工序的时效温度为600~800℃。
27.在该第八公开中,能够得到与上述第七公开同样的作用效果。
28.第九公开是在第七或第八公开的co基合金结构体的制造方法中,co基合金结构体的前体通过层叠造型法来制造。
29.在第九公开中,能够进一步提高co基合金结构体的机械特性。
30.第十公开是在第七或第八公开的co基合金结构体的制造方法中,co基合金结构体的前体通过锻造法制造。
31.在该第十公开中,能够提高co基合金结构体的机械特性。
32.第十一公开是在第七或第八公开的co基合金结构体的制造方法中,co基合金结构体的前体通过粉末hip锻造法来制造。
33.在该第十一公开中,能够提高co基合金结构体的机械特性。
34.发明效果
35.根据本公开,能够提高co基合金结构体的机械特性。
附图说明
36.[图1]图1是示出由层叠造型体构成的co基合金结构体的制造方法的工序例的流程图。
[0037]
[图2]图2是概略地示出由层叠造型体构成的co基合金结构体的组织状态的概略图。
[0038]
[图3]图3是将图2的iii部放大示出的局部放大图。
[0039]
[图4]图4是示出实施方式的变形例1的co基合金结构体的制造方法的工序例的流程图。
[0040]
[图5]图5是示出实施方式的变形例1的co基合金结构体的制造方法的工序例的流程图。
[0041]
[图6]图6是示出样品a的组织状态的电子显微镜照片。
[0042]
[图7]图7是示出样品b的组织状态的电子显微镜照片。
[0043]
[图8]图8是示出样品a和样品b的温度(℃)与拉伸强度(mpa)和0.2%屈服强度(mpa)的关系的图。
具体实施方式
[0044]
以下,基于附图对本公开的实施方式进行详细说明。以下的实施方式的说明本质上仅为例示,并不意图限制本公开、其应用物或其用途。
[0045]
[co基合金结构体的基本性质]
[0046]
co基合金与一般利用的ni基合金相比,熔点高50~100℃左右,置换型元素的扩散系数比ni基小。因此,在co基合金中,在高温下的使用中产生的组织变化少。另外,co基合金与ni基合金相比富有延展性。因此,co基合金容易进行锻造、轧制、冲压等塑性加工。因此,期待co基合金比ni基合金更广泛的用途的展开。
[0047]
一直以来用于强化相的co3ti或co3ta的γ
′
相的晶格常数相对于基体相(γ相)的
失配为1%以上,从抗蠕变性方面考虑不利。与此相对,在本公开的实施方式中用于强化相的金属间化合物〔co3(al,w)〕即使与基体相(γ相)的失配大也为0.5%左右,呈现出超过通过γ
′
相进行了析出强化的ni基合金的组织稳定性。
[0048]
进而,co基合金与ni基合金的200gpa相比,显示出220~230gpa的大1成以上的弹性模量。因此,也能够用于发条、弹簧、线、带、线缆引导件等需要高强度、高弹性的用途。另外,co基合金为硬质且耐磨损性、耐腐蚀性优异,因此也能够作为堆焊材料使用。
[0049]
[co基合金结构体的基本组成]
[0050]
在本公开的实施方式的co基合金结构体中,为了使l12型金属间化合物〔co3(al,w)〕或〔(co,x)3(al,w,z)〕适量分散,确定了成分及组成。co基合金结构体的基本组成具有以质量比计al:0.1~10%、w:3.0~45%且余量除了不可避免的杂质为钴(co)的组成。
[0051]
铝(al)是γ
′
相的主要构成元素。al也有助于耐氧化性的提高。al的含量低于0.1%时,γ
′
相不析出,或者即使析出也无助于高温强度。但是,若过剩地添加al,则脆弱且助长硬质的相的生成。因此,al的含量设定为0.1~10%的范围。al含量的优选下限为0.5%。al含量的优选的上限为5.0%。
[0052]
钨(w)是γ
′
相的主要构成元素。w具有使基体固溶强化的作用。w的含量低于3.0%时,γ
′
相不析出,或者即使析出也无助于高温强度。另一方面,若w的含量超过45%,则助长有害相的生成。因此,w的含量设定为3.0~45%的范围。w含量的优选的上限为30%。w含量的优选下限为4.5%。
[0053]
[组(i)和组(ii)]
[0054]
在co
‑
w
‑
al的基本成分体系中,根据需要添加选自组(i)和组(ii)中的至少任一者中的一种或两种以上的合金成分(选择元素)。在添加选自组(i)中的多种合金成分的情况下,在0.001~2.0%的范围内选择添加量的合计。另外,在添加选自组(ii)中的多种合金成分的情况下,在0.1~50%的范围内选定添加量的合计。
[0055]
组(i)是由b、c、y、la、混合稀土金属构成的组。
[0056]
硼(b)是在结晶粒界偏析而强化粒界的合金成分。b有助于高温强度的提高。b的添加效果在0.001%以上时变得显著。但是,若过剩地添加b,则加工性受损。因此,b的添加量的上限设定为1.0%。b添加量的优选上限为0.5%。
[0057]
碳(c)与b同样,对粒界强化有效。另外,c成为碳化物而析出,使高温强度提高。这样的效果在c的添加量为0.001%以上时得到。但是,若过剩地添加c,则加工性和/或韧性受损。因此,c的添加量的上限设定为2.0%。c添加量的优选上限为1.0%。
[0058]
钇(y)、镧(la)和混合稀土金属均是对提高耐氧化性有效的成分。特别是y、la和混合稀土金属均在添加量为0.01%以上时发挥耐氧化性。但是,若分别过剩地添加y、la及混合稀土金属,则会对组织稳定性造成不良影响。因此,y、la和混合稀土金属各自的添加量的上限设定为1.0%。y、la和混合稀土金属各自的添加量的优选上限为0.5%。
[0059]
组(ii)是由ni、cr、ti、fe、v、nb、ta、mo、zr、hf、ir、re、ru构成的组。
[0060]
组(ii)的合金成分越是分配系数大的元素,对γ
′
相的稳定化越有效。分配系数k
xγ
′
/γ
表示为k
xγ
′
/γ
=c
xγ
′
/cx
γ
〔其中,c
xγ
′
:γ
′
相的x元素浓度(原子%),c
xγ
:基体(γ)相的x元素浓度(原子%)〕。该式(k
xγ
′
/γ
=c
xγ
′
/cx
γ
)表示γ
′
相所含的预定元素相对于基体相(γ相)所含的预定元素的浓度比。分配系数≥1则为γ
′
相的稳定化元素。分配系数<1,则为基
体相(γ相)的稳定化元素。钛(ti)、钒(v)、铌(nb)、钽(ta)、钼(mo)是用于使γ
′
相稳定化的元素。特别是对于ta,用于使γ
′
相稳定化的效果比其他元素更容易显现。
[0061]
镍(ni)是与l12型金属间化合物的co置换并改善耐热性和/或耐腐蚀性的成分。若ni的添加量为1.0%以上,则可观察到由添加带来的效果(耐热性和/或耐腐蚀性)。但是,若过剩地添加ni,则生成有害的化合物相。因此,ni的添加量的上限设定为50%。ni添加量的优选上限为40%。另外,ni与al和w分别置换,使γ
′
相的稳定度提高。其结果是,能够使γ
′
相稳定地存在至更高的温度。
[0062]
铱(ir)是与l12型金属间化合物的co置换并改善耐热性和/或耐腐蚀性的成分。如果ir的添加量为1.0%以上,则可观察到添加带来的效果。但是,若过剩地添加ir,则生成有害的化合物相。因此,ir的添加量的上限设定为50%。ir添加量的优选上限为40%。
[0063]
铁(fe)与co置换,具有改善加工性的作用。该作用在fe的添加量为1.0%以上时变得显著。但是,例如若如fe的添加量超过10%的情况那样过剩地添加fe,则成为导致高温区域中的组织的不稳定化的原因。因此,fe的添加量的上限设定为10%。fe添加量的优选的上限为5.0%。
[0064]
铬(cr)是在co基合金结构体的表面生成致密的氧化皮膜并提高耐氧化性的合金成分。另外,cr有助于高温强度和/或耐腐蚀性的改善。这样的效果在cr的添加量为1.0%以上时变得显著。但是,若过剩地添加cr,则成为加工性劣化的原因。因此,cr的添加量的上限设定为20%。cr添加量的优选上限为15%。
[0065]
钼(mo)是对γ
′
相的稳定化和基体的固溶强化有效的合金成分。特别是在mo的含量为1.0%以上时,可见mo的添加效果。但是,若过剩地添加mo,则成为加工性劣化的原因。因此,mo的含量的上限设定为15%。mo含量的优选的上限为10%。
[0066]
铼(re)和钌(ru)是对提高耐氧化性有效的合金成分。re和ru均为0.5%以上时,添加效果显著。但是,若分别过剩地添加re、ru,则诱发有害相的生成。因此,re、ru的添加量的上限均设定为10%。re添加量和ru添加量的优选上限均为5.0%。
[0067]
钛(ti)、铌(nb)、锆(zr)、钒(v)、钽(ta)、铪(hf)均是对γ
′
相的稳定化和/或高温强度的提高有效的合金成分。特别是在ti:0.5%以上、nb:1.0%以上、zr:1.0%以上、v:0.5%以上、ta:1.0%以上、hf:1.0%以上时,可得到添加效果。但是,若ti、nb、zr、v、ta、hf各自过剩地添加,则成为有害相的生成和/或熔点下降的原因。因此,ti、nb、zr、v、ta、hf各自的添加量的上限设定为ti:10%、nb:20%、zr:10%、v:10%、ta:20%、hf:10%。
[0068]
[γ
′
相的粒径]
[0069]
l12型的金属间化合物〔co3(al,w)〕或〔(co,x)3(al,w,z)〕以析出相(γ
′
相)的粒径为10nm~1μm(1000nm)的粒子的方式构成。在超过1μm的粒径时,强度、硬度等机械特性劣化。γ
′
相的优选粒径为10nm以上且小于50nm的范围。
[0070]
[γ
′
相的析出量]
[0071]
l12型的金属间化合物〔co3(al,w)〕或〔(co,x)3(al,w,z)〕以析出相(γ
′
相)的析出量为40~85体积%的方式构成。该析出量低于40%时,析出强化的作用变得不充分。另一方面,若该析出量超过85%,则有可能在co基合金结构体中产生延展性劣化。
[0072]
[层叠造型体]
[0073]
co基合金结构体例如作为由粉末构成的层叠造型体来构成。层叠造型体通过层叠
造型法(additive manufacturing,am法)形成。层叠造型法是使用以激光等为热源的3d打印机,将通过气体雾化法等制作的粉末选择性地熔融及凝固,由此成形层叠造型体的方法。
[0074]
作为层叠造型体的原材料,优选使用具有以质量比计al:2~5%、w:17~25%、c:0.05~0.15%、ni:20~35%、cr:6~10%、ta:3~8%且余量除了不可避免的杂质为co的组成的粉末(以下称为“原料粉末”)。通过使用该原料粉末实施后述的制造方法,可得到具有与上述原料粉末同样的组成的层叠造型体。
[0075]
[由层叠造型体构成的co基合金结构体的制造方法]
[0076]
接着,将由层叠造型体构成的co基合金结构体的制造方法的一例示于图1。作为主要工序,该制造方法具有粉末制作工序s1、选择性激光熔融工序s2、固溶处理工序s3和时效处理工序s4。以下,对各工序进行说明。
[0077]
[粉末制作工序]
[0078]
粉末制作工序s1是制作成为co基合金结构体的原材料的粉末的工序。该粉末具有例如上述原料粉末那样的预定的化学组成。
[0079]
作为制作该粉末的方法,例如使用气体雾化法。具体而言,使用气体雾化装置进行高频感应加热,由此在真空排气后的非活性气体气氛中或大气中进行试样的溶解。然后,通过对该试样吹送高压的气体(氦、氩、氮等气体),由此制作数十μm左右的球状的粉末。
[0080]
从下一工序的选择性激光熔融工序(s2)中的操作性、合金粉末床的填充性的观点出发,粉末的粒径优选为5μm以上且100μm以下。若粉末的粒径小于5μm,则在下一工序s2中合金粉末的流动性降低(合金粉末床的形成性降低),成为层叠造型体的形状精度降低的主要原因。另一方面,若粉末的粒径超过100μm,则在下一工序s2中难以控制合金粉末床的局部熔融和急冷凝固,粉末的熔融变得不充分,或者成为层叠造型体的表面粗糙度增加的主要原因。而且,粉末的粒径更优选为10μm以上且70μm以下,进一步优选为10μm以上且50μm以下。
[0081]
[选择性激光熔融工序]
[0082]
选择性激光熔融工序s2是使用通过粉末制作工序s1制作的粉末利用选择性激光熔融(slm)法形成所希望形状的层叠造型体的工序。
[0083]
如图1所示,工序s2包括铺满通过粉末制作工序s1制作的粉末而准备预定厚度的合金粉末床的合金粉末床准备工序(s21)以及对合金粉末床的预定的区域照射激光而使该区域的粉末局部熔融和急冷凝固的激光熔融凝固工序(s22)。通过反复实施合金粉末床准备工序(s21)和激光熔融凝固工序(s22),从而形成层叠造型体(即,co基合金结构体的前体)。
[0084]
在选择性激光熔融工序s2中,为了得到作为最终的层叠造型体优选的微细组织,控制层叠造型体的微细组织。即,为了控制层叠造型体的微细组织,控制粉末床的局部熔融和急冷凝固。
[0085]
[固溶处理工序]
[0086]
固溶处理工序s3是对通过选择性激光熔融工序s2得到的层叠造型体(co基合金结构体的前体)实施固溶处理的工序。作为固溶处理的温度条件,设定为1100℃以上且1200℃以下的范围。固溶处理的优选温度为1160℃。另外,固溶处理的保持时间优选设定为0.5小时以上且10小时以下。需要说明的是,作为热处理后的冷却方法,没有特别限定,例如实施
水冷、油冷、空冷、炉冷中的任一种方法即可。
[0087]
通过固溶处理工序s3,在通过选择性激光熔融工序s2得到的层叠造型体(co基合金结构体的前体)的内部,产生母相晶粒的再结晶,在急冷凝固时产生的层叠造型体的内部应变得到缓和。另外,优选通过再结晶,将母相晶粒的平均结晶粒径粗大化控制在20μm以上145μm以下的范围。若该平均结晶粒径小于20μm或超过145μm,则作为最终的co基合金结构体无法得到充分的蠕变特性。
[0088]
[时效处理工序]
[0089]
时效处理工序s4是对通过固溶处理工序s3实施了固溶处理的层叠造型体(co基合金结构体的前体)实施时效处理的工序。具体而言,时效处理工序s4包括第一时效处理工序s41和第二时效处理工序s42。
[0090]
第一时效处理工序s41在经过固溶处理工序s3后实施。作为第一时效处理工序s41中的时效温度的条件,优选设定为500℃以上且700℃以下的范围。第一时效处理工序s41的保持时间优选设定为0.5小时以上30小时以下。
[0091]
第二时效处理工序s42在经过第一时效处理工序s41后实施。第二时效处理工序s42的时效温度设定为比第一时效处理工序s41的时效温度高。具体而言,作为第二时效处理工序s42中的时效温度的条件,优选设定为600℃以上且800℃以下的范围。第二时效处理工序s42的保持时间优选设定为0.5小时以上且20小时以下。
[0092]
作为第一及第二时效处理工序s41、s42的冷却方法,没有特别限定,例如实施水冷、油冷、空冷、炉冷中的任一种方法即可。
[0093]
需要说明的是,虽然未图示,但也可以根据需要对通过固溶处理工序s3或时效处理工序s4得到的层叠造形体形成耐腐蚀性被覆层。或者,也可以对通过固溶处理工序s3或时效处理工序s4得到的层叠造形体实施表面精加工。
[0094]
[实施方式的作用效果]
[0095]
如上所述,co基合金结构体如下构成:在基体相(γ相)中以分散的状态析出的析出相(γ
′
相)的粒径为10nm~1μm,且析出相(γ
′
相)的析出量为40~85体积%。在该构成中,包含微细化至极限的粒径的γ
′
相相对于基体相(γ相)大量析出,成为分散的状态。其结果是,在co基合金结构体的组织内,基体相(γ相)与多个γ
′
相的界面的总表面积相对增加且γ
′
相的粒子彼此的距离相对缩小(小于100nm)。即,在基体相(γ相)中,包含微细化至极限的粒子的γ
′
相成为均匀地析出强化的状态。而且,通过该析出强化,特别是高温下的机械特性(特别是拉伸强度及屈服强度(0.2%屈服强度))提高。因此,在本公开的实施方式的co基合金结构体中,能够提高由上述析出强化的作用带来的机械特性。需要说明的是,在本公开的实施方式中,“分散的状态”是指多个γ
′
相在基体相(γ相)内均匀地配置的状态。
[0096]
另外,γ
′
相的粒径优选为10nm以上且小于50nm的范围。如果这样微细化的γ
′
相相对于基体相(γ相)大量析出且为分散的状态,则由γ
′
相带来的析出强化的作用被强化,能够进一步提高co基合金结构体的机械特性。
[0097]
另外,co基合金结构体作为由粉末构成的层叠造型体而构成。在层叠造型法中,特别是在使用以激光为热源的金属3d打印机的情况下,在层叠造型体的造型时成为原材料的粉末的凝固速度与以往的铸造等相比变得非常快。其结果是,在层叠造型体中形成微细的凝固组织。并且,如图2和图3所示,通过对造型后的层叠造型体实施热处理(固溶处理和时
效处理),在层叠造型体的粒界和/或粒内,w化合物成为在基体相(γ相)中以微细的状态析出且均匀地分散的状态。进而,在基体相(γ相)中,成为在w化合物的周围分散有多个微细的析出相(γ
′
相)的状态。这样,在作为由粉末构成的层叠造型体而构成的co基合金结构体中,能够得到w化合物和多个微细的析出相(γ
′
相)双方的析出强化的作用。其结果是,在本公开的实施方式的co基合金结构体中,能够进一步提高机械特性。
[0098]
需要说明的是,在图2和图3中,示出了w化合物析出时的组织状态,但也存在不是该w化合物而是碳化物相在层叠造型体的粒界和/或粒内析出的情况。或者,也有w化合物和碳化物相这两者在层叠造型体的粒界和/或粒内析出的情况。
[0099]
另外,成为层叠结构体的原材料的粉末具有以质量比计al:2~5%、w:17~25%、c:0.05~0.15%、ni:20~35%、cr:6~10%、ta:3~8%且余量除了不可避免的杂质为co的组成。如果是由具有这样的组成的粉末构成的层叠造型体,则能够使析出相(γ
′
相)的粒径微细化。其结果是,能够进一步提高co基合金结构体的机械特性。
[0100]
另外,在co基合金结构体的制造方法中,在时效处理工序中,在第一时效处理工序之后实施的第二时效处理工序的时效温度设定为高于第一时效处理工序的时效温度。具体而言,固溶处理的温度设定为1100℃以上,第一时效处理工序的时效温度设定为500~700℃,第二时效处理工序的时效温度设定为600~800℃。由此,能够在co基合金结构体的组织内将析出相(γ
′
相)的粒径微细化至极限。进而,在co基合金结构体的组织内难以产生微观偏析,在基体相(γ相)中γ
′
相均匀地分散。其结果是,由γ
′
相带来的析出强化的作用被强化,能够进一步提高co基合金结构体的机械特性。
[0101]
[实施方式的变形例1]
[0102]
在上述实施方式中,对作为由粉末构成的层叠造型体而构成的co基合金结构体进行了说明,但不限于该方式。作为具体例,co基合金结构体的前体也可以作为通过锻造法制造的锻造体来构成从而代替通过层叠造型法制造的层叠造型体。即,作为co基合金结构体的制造方法,也可以采用将图1所示的粉末制作工序(s1)和选择性激光熔融工序(s2)置换为基于锻造法的锻造工序(s5)的方式(参照图4)。
[0103]
在锻造法中,在刚铸造后的组织中形成比较粗大的凝固组织,但通过作为后工序的热锻,该组织被均质化并且晶粒通过再结晶而被微细化。进而,通过经过图1所示的固溶处理工序s3和时效处理工序s4,在co基合金结构体的组织内析出相(γ
′
相)的粒子被进一步微细化且难以产生微观偏析。因此,即使是由锻造体构成的co基合金结构体,也能够与上述实施方式同样地提高机械特性。
[0104]
[实施方式的变形例2]
[0105]
另外,co基合金结构体的前体也可以作为通过粉末hip锻造法制造的粉末hip锻造体来构成,从而代替通过层叠造型法制造的层叠造型体。即,作为co基合金结构体的制造方法,也可以采用将图1所示的选择性激光熔融工序(s2)置换为基于粉末hip锻造法的hip处理工序(s6)的方式(参照图5)。
[0106]
hip处理工序(s6)是将粉末制作工序(s1)中制作的粉末装填到罐中,通过高温和静水压化来进行烧结的工序。粉末制作工序(s1)中制作的粉末的组织例如通过气体雾化法被急冷凝固。由此,w化合物和/或碳化物相等在粒界和/或粒内成为微细化且分散的状态。而且,通过经过固溶处理工序(s3)和时效处理工序(s4),在co基合金结构体的组织内γ
′
相
的粒子被进一步微细化且难以产生微观偏析。因此,即使是由粉末hip锻造体构成的co基合金结构体,也能够与上述实施方式同样地提高机械特性。
[0107]
[其他实施方式]
[0108]
在图1和图5所示的粉末制作工序(s1)中,制作作为co基合金的原材料的粉末的方法和技法没有特别限定。即,在粉末制作工序(s1)中,可以利用以往的方法和技法。例如,也可以进行以成为所希望的化学组成的方式将原料混合、熔炼、铸造而制作母合金块(母锭)的母合金块制作工序和由该母合金块形成合金粉末的雾化工序。另外,雾化方法也没有特别的限定,可以利用以往的方法和技法。例如,也可以采用离心力雾化法来代替上述气体雾化法。
[0109]
以上,对关于本公开的实施方式进行了说明,但本公开并不仅限定于上述的实施方式,能够在本公开的范围内进行各种变更。
[0110]
[实施例]
[0111]
以下,通过经过下述工序制作的样品a(实施例)和样品b(比较例),对本发明进行更具体的说明。需要说明的是,本发明并不限定于这些实施例。
[0112]
在此,样品a是由经过图1所示的全部工序而制作的层叠造型体构成的co基合金结构体。样品a包含粒径小于50nm的析出相(γ
′
相)的粒子(参照图6)。另一方面,样品b是由经过图1所示的第二时效处理工序(s42)以外的全部工序而制作的层叠造型体构成的co基合金结构体。样品b包含粒径为约250nm的γ
′
相的粒子(参照图7)。
[0113]
首先,为了制作样品a和样品b,通过图1所示的粉末制作工序(s1)制作成为上述实施方式中说明的层叠造型体的原材料的粉末(原料粉末)。具体而言,将预定的原料混合后,进行通过真空高频感应熔炼法进行熔炼和铸造而制作母合金块的母合金块制作工序。接着,进行将该母合金块再熔炼,通过氩气气氛中的气体雾化法形成合金粉末的雾化工序。接着,对得到的粉末进行用于控制粒径的合金粉末分级工序。
[0114]
使用上述原料粉末,通过图1所示的选择性激光熔融工序(s2)制作层叠造型体(直径8mm
×
高度60mm)。选择性激光熔融(slm)的条件是将合金粉末床的厚度h设为100μm,将激光的输出p设为100w,通过对激光的扫描速度s(mm/s)进行各种变更来控制局部热输入量p/s(单位:w
·
s/mm=j/mm)。局部热输入量的控制相当于冷却速度的控制。
[0115]
对通过选择性激光熔融工序(s2)制作的层叠造型体(前体)实施图1所示的固溶处理工序(s3)。在本实验中,固溶处理的温度为1160℃。固溶处理的保持时间为4小时。
[0116]
接着,对实施了固溶处理的层叠造型体(前体)实施时效处理工序。具体而言,在样品a中,实施图1所示的第一时效处理工序(s41)及第二时效处理工序(s42)这两者。另一方面,在样品b中,仅实施图1所示的第一时效处理工序(s41)。即,在样品b中,未实施图1所示的第二时效处理工序(s42)。
[0117]
在本实验中,第一时效处理工序(s41)的温度为650℃。第一时效处理工序(s41)的保持时间为24小时。另外,第二时效处理工序(s42)的温度为760℃。第二时效处理工序的保持时间(s42)为16小时。
[0118]
参照图6和图7可知,在实施了第一和第二时效处理工序双方的样品a中,与仅实施了第一时效处理工序的样品b相比,微细化的多个析出相(γ
′
相)的粒子在基体相(γ相)中以均匀分散的状态析出。即,在样品a中,在基体相(γ相)中γ
′
相均匀地分散,结果在co基
合金结构体的组织内不产生微观偏析。
[0119]
在样品a及样品b中,将表示伴随温度(℃)的变化的拉伸强度及0.2%屈服强度(mpa)的关系的图表示于图8。
[0120]
根据图8,在样品a中,得到了拉伸强度及0.2%屈服强度双方的数值整体上高于样品b中的拉伸强度及0.2%屈服强度的数值的结果。具体而言,在约20℃~600℃的范围内,样品a的拉伸强度相对于样品b的拉伸强度提高100mpa左右。另外,在约20℃至600℃的范围内,样品a的0.2%屈服强度相对于样品b的0.2%屈服强度提高20mpa左右。
[0121]
如上所述可知,在本实验中,在具有通过经过第一时效处理工序(s41)及第二时效处理工序(s42)而微细化至极限的γ
′
相的粒子的实施例的样品a中,相对于仅进行第一时效处理工序(s41)的比较例的样品b,机械特性(拉伸强度及0.2%屈服强度)提高。
[0122]
产业上的可利用性
[0123]
本公开可以作为适合于要求高温强度、高强度、高弹性等的用途的co基合金结构体及其制造方法在产业上利用。