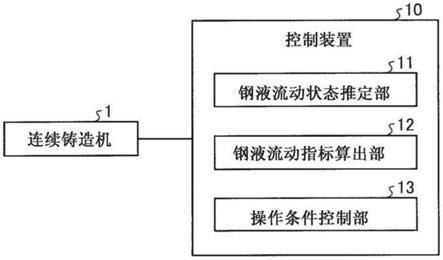
1.本发明涉及连续铸造机的控制方法、连续铸造机的控制装置及铸片的制造方法。
背景技术:2.近年来,对于在连续铸造机中制造的板坯等铸片的高品质化的要求日益升高。因此,开发出对连续铸造机的铸模内的钢液的状况进行控制的技术。例如专利文献1记载了向铸模内的钢液施加磁场的方法。通过向铸模内的钢液施加磁场来控制钢液流动,由此能够使铸片的品质稳定化。然而,即使向钢液施加磁场,由于未预期的操作变动,想完全地控制钢液流动也是困难的。因此,提出了并用由埋设于铸模铜板的测温元件产生的钢液的测温结果来控制操作的技术。例如专利文献2记载了通过基于铸模内铜板温度数据来校正铸模内的钢液流动,由此高精度地推定钢液流动的方法。
3.需要说明的是,作为铸片要求的品质之一,可列举由混入于铸片的表层附近的气泡、夹杂物等杂质造成的缺陷少的情况。在连续铸造机中,经由浸渍喷嘴向铸模内浇注的钢液从铸模壁面起开始凝固成壳状(以下,将凝固成壳状的钢称为凝固壳),随着铸造的进展而使凝固壳厚度增加。气泡、夹杂物悬浊于浇注到铸模内的钢液中,但是如果这些气泡、夹杂物被捕捉于凝固壳而在该状态下进行凝固,则成为上述的缺陷。
4.已知凝固界面的钢液流速越快,则悬浊在钢液中的气泡、夹杂物越不易被捕捉于凝固壳,从该观点出发,也进行了适当地控制铸模内的钢液流动的技术开发。例如专利文献3公开了一种技术,用于抑制在铸造速度为1.6m/min左右比较慢时等凝固界面处的钢液流速不足而产生缺陷。具体而言,该技术在以使制动力作用于从浸渍喷嘴喷出的钢液的喷出流的方式施加移动磁场而进行连续铸造时,将相对于移动磁场施加位置的浸渍喷嘴的喷出口的位置及喷出角度设为适当的范围。
5.现有技术文献
6.专利文献
7.专利文献1:日本特开平10
‑
305353号公报
8.专利文献2:日本特开2016
‑
16414号公报
9.专利文献3:日本特开2005
‑
152996号公报
技术实现要素:10.发明要解决的课题
11.专利文献2记载了高精度地推定铸模内的钢液流动的方法,但是并未公开或教导推定成为在铸模内杂质向铸片混入的要因的钢液流动指标并将钢液流动指标控制在适当范围内的内容。为了制造高品质的铸片,需要推定成为在铸模内杂质向铸片混入的要因的钢液流动指标,并将钢液流动指标控制在适当范围内。因此,仅通过专利文献2记载的方法,制造高品质的铸片是困难的。
12.另一方面,专利文献3记载了将凝固界面处的钢液流速控制为适当范围的方法,但是该适当范围只不过是仅由设备的几何学的关系规定的范围。然而,在实际的连续铸造中存在夹杂物附着于浸渍喷嘴的喷嘴孔而产生偏流等钢液流速的变动主要原因,在产生了这样的变动的情况下,需要根据其变动状况将凝固界面处的钢液流速控制在适当范围内。即,通过使用连续铸造机的操作条件及铸模内的钢液的温度数据,将在成为铸模内气泡、夹杂物等杂质向铸片混入的要因的凝固界面的钢液流速的下降推定作为钢液流动指标,并基于其推定结果而将钢液流动指标控制在适当范围内,能够制造更高品质的铸片。
13.本发明鉴于上述课题而作出,其目的在于提供能够制造高品质的铸片的连续铸造机的控制方法、连续铸造机的控制装置及铸片的制造方法。
14.用于解决课题的方案
15.本发明的连续铸造机的控制方法包括:钢液流动状态推定步骤,使用连续铸造机的操作条件及铸模内的钢液的温度数据在线地推定铸模内的钢液的流动状态;钢液流动指标算出步骤,基于在所述钢液流动状态推定步骤中推定出的钢液的流动状态在线地算出钢液流动指标,该钢液流动指标为在铸模内杂质向铸片混入的要因;及操作条件控制步骤,以使在所述钢液流动指标算出步骤中算出的钢液流动指标处于适当范围内的方式控制所述连续铸造机的操作条件。
16.可以是,所述钢液流动指标包含在通过电磁搅拌磁场产生的搅拌流之中流速为规定值以下的区域的面积。
17.可以是,所述钢液流动指标包含钢液表面的速度或流动状态。
18.可以是,所述钢液流动指标包含凝固界面流速为规定值以下的面积。
19.可以是,所述钢液流动指标包含钢液表面流速的最大值。
20.可以是,所述钢液流动指标包含钢液表面紊流能量的最大值。
21.可以是,所述铸模内的钢液的温度数据是包含设置于铸模的温度传感器的测定值的温度数据。
22.可以是,所述连续铸造机的操作条件包括铸造速度、电磁搅拌磁场的磁通密度及喷嘴浸渍深度中的至少一个。
23.所述操作条件控制步骤可以包括通过针对每个控制周期而推定使铸造速度、电磁搅拌磁场的磁通密度及喷嘴浸渍深度中的至少一个微小地变化的情况下的钢液的流动状态,来算出钢液的流动状态相对于操作条件的变更的灵敏度的步骤。
24.可以是,所述操作条件控制步骤包括显式地算出铸造速度、电磁搅拌磁场的磁通密度及喷嘴浸渍深度之间的相互干涉并进行控制的步骤。
25.本发明的连续铸造机的控制装置具备:钢液流动状态推定部,使用连续铸造机的操作条件及铸模内的钢液的温度数据在线地推定铸模内的钢液的流动状态;钢液流动指标算出部,基于由所述钢液流动状态推定部推定出的钢液的流动状态在线地算出钢液流动指标,该钢液流动指标为在铸模内杂质向铸片混入的要因;操作条件控制部,以使由所述钢液流动指标算出部算出的钢液流动指标处于适当范围内的方式控制所述连续铸造机的操作条件。
26.本发明的铸片的制造方法包括一边使用本发明的连续铸造机的控制方法来控制连续铸造机,一边制造铸片的步骤。
27.发明效果
28.根据本发明的连续铸造机的控制方法、连续铸造机的控制装置及铸片的制造方法,能够制造高品质的铸片。
附图说明
29.图1是表示应用本发明的连续铸造机的一构成例的示意图。
30.图2是表示本发明的一实施方式的连续铸造机的控制装置的结构的框图。
31.图3是表示浸渍喷嘴的一构成例的示意图。
32.图4是表示电磁搅拌磁场的磁通密度不同的两个条件下的电磁搅拌磁场的磁通密度的变更量与钢液表面最大流速的变化量的关系的图。
33.图5是表示基于本发明的一实施方式的连续铸造机的控制装置的操作条件控制处理的流程的流程图。
34.图6是表示与电磁搅拌磁场的磁通密度的变化相伴的低流速面积的变化的一例的图。
35.图7是表示与电磁搅拌磁场的磁通密度的变化相伴的钢液表面最大流速的变化的一例的图。
36.图8是表示与电磁搅拌磁场的磁通密度及喷嘴浸渍深度的变化相伴的钢液表面最大流速的变化的一例的图。
37.图9是表示与操作条件的控制的有无相伴的板坯的缺陷混入率的变化的一例的图。
38.图10是表示操作条件控制处理的实施例的时间图。
具体实施方式
39.以下,参照附图,说明本发明的一实施方式的连续铸造机的控制装置的结构及其动作。
40.〔连续铸造机的结构〕
41.首先,参照图1,说明应用本发明的连续铸造机的一构成例。
42.图1是表示应用本发明的连续铸造机的一构成例的示意图。如图1所示,在该连续铸造机1中,在装满钢液2的中间包3的铅垂方向下方设置铸模4,在中间包3的底部设置成为钢液2向铸模4的供给口的浸渍喷嘴5。钢液2从中间包3连续地向铸模4注入,由在内部设有冷却水的水路的铸模4冷却,从铸模4的下部拉拔而成为板坯。此时,为了使向铸模4注入的钢液2的重量和拉拔的板坯的重量一致,根据拉拔速度通过设置在浸渍喷嘴5的正上方的未图示的滑门喷嘴等来调整浸渍喷嘴5的开度。在铸模4中,在成为铸造的板坯的厚度方向的两端的f面及b面设置有多个温度传感器。各温度传感器测定各设置位置处的钢液2的温度。而且,在铸模4设置未图示的线圈,产生在铸模4内的钢液2中引起搅拌流的电磁搅拌磁场。
43.〔控制装置的结构〕
44.接下来,参照图2,说明本发明的一实施方式的连续铸造机的控制装置的结构。
45.图2是表示本发明的一实施方式的连续铸造机的控制装置的结构的框图。如图2所示,本发明的一实施方式的连续铸造机的控制装置10由计算机等信息处理装置构成,通过
cpu(central processing unit:中央处理单元)等的内部的运算处理装置执行计算机程序而作为钢液流动状态推定部11、钢液流动指标算出部12及操作条件控制部13发挥功能。
46.钢液流动状态推定部11利用专利文献2记载的钢液的流动状态推定方法等的周知的技术,在线地推定铸模4内的钢液2的流动状态。具体而言,钢液流动状态推定部11使用考虑了紊流模型的数值流体力学等的物理模型,在线地根据连续铸造机1的操作条件及设置于铸模4的温度传感器的测定值来推定铸模4内的钢液2的流动状态。作为连续铸造机1的操作条件,可以例示铸造宽度、铸造速度、电磁搅拌磁场的磁通密度、浸渍喷嘴5的浸渍深度(喷嘴浸渍深度)等。
47.钢液流动指标算出部12使用通过钢液流动状态推定部11推定出的钢液2的流动状态的数据,在线地推定成为在铸模4内杂质向板坯(铸片)混入的要因的钢液流动指标。在此,作为向板坯混入的杂质,存在以铸模粉末为起源的夹杂物。铸模粉末是被始终供给到向铸模4内注入的钢液的上表面,防止铸模4与板坯的烧结的润滑剂,也具有钢液2的保温效果等。在铸模4内的钢液2的最上部,铸模粉末以熔融状态与钢液2接触,钢液2以一定流速流动。在此,在本发明中,将与铸模粉末接触的接触位置处的钢液2的流速称为钢液2的表面流速。因此,如果钢液2的表面流速变得过大,则存在熔融粉末被卷入钢液2的内部而成为夹杂物缺陷的可能性。而且,氧化铝等夹杂物与从浸渍喷嘴5供给的ar气体等气泡一起随着钢液流动而上升,被熔融粉末层吸收而进行钢液2的清洁化。然而,在凝固界面流速慢的情况下,夹杂物、气泡陷入于凝固壳侧,在制品时可能会成为表面缺陷的原因。在此,凝固界面流速是指铸模内的凝固壳的附近区域处的钢液的流速。
48.因此,作为表示在铸模4内杂质向板坯混入的要因的钢液流动指标,可以例示铸模4内的钢液表面流速的最大值(钢液表面最大流速)、凝固界面流速为规定值以下的面积(低流速面积)、钢液表面紊流能量的最大值。具体而言,钢液流动指标算出部12根据钢液2的流动状态的数据,算出铸模4的最上段部(弯液面:钢液液面的高度位置)的钢液流动状态计算网格(宽度方向及厚度方向的整个区域)的钢液流速的最大值作为钢液表面最大流速。而且,钢液流动指标算出部12根据钢液2的流动状态的数据,算出在处于铸模4的高度方向(铸造方向)及厚度方向的规定位置的钢液流动状态计算网格(在宽度方向中整个区域)中的钢液流速为规定值以下的钢液流动状态计算网格的面积。例如钢液流动指标算出部12在宽度方向的整个区域且沿铸模高度方向至少从弯液面位置至下方200mm的范围内,将钢液流速为规定值以下的钢液流动状态计算网格的面积针对铸模长边的每个单面进行合计,将其值分别设为低流速面积。而且,钢液流动指标算出部12根据钢液2的流动状态的数据,算出铸模4的最上段部的钢液流动状态计算网格(宽度方向、厚度方向的整个区域)中的紊流能量的最大值作为钢液表面紊流能量的最大值。
49.在此,紊流能量是表示流动的紊乱的强度的值,基于在某空间位置时间性地变动的流速的相对于时间平均值的偏离的大小来赋予。具体而言,紊流能量由以下所示的数学式来赋予。
50.k=(1/2)
·
u
i2
51.u=u
ave
+u
i
52.k表示紊流能量,u表示某空间位置处的流体的流速的瞬时值,u
ave
表示某空间位置处的流体的流速的时间平均值,u
i
表示某空间位置处的流体的流速的相对于时间平均值的
偏离。
53.低流速面积在板坯的凝固界面处的钢液流动快的情况下具有能够减少由于由钢液2补充于凝固壳的杂质(气泡、夹杂物)的效果,因此成为有效的指标。在此,应判定为低流速的流速只要根据钢种成分、要求的品质水平及铸模尺寸等而单独确定即可,并非应确定为恒定值。需要说明的是,根据本发明者们的研究,作为判定为低流速的标准,可以采用小于0.05m/s。而且,针对低流速面积,例如在将钢液流动状态计算网格的单位面积设为1cm2(0.0001m2)的情况下,在针对铸模长边的单面而判定为低流速的单位网格存在100网格时,低流速面积为0.01m2。而且,关于低流速面积的适当值,也只要根据钢种成分、要求的品质水平及铸模尺寸等而单独确定即可,并非应确定为恒定值。需要说明的是,根据本发明者们的研究,在要求的品质水平严格的情况下,可以采用0.01m2以下作为标准,在要求的品质水平不那么严格的情况下,可以采用0.02m2以下作为标准。钢液表面最大流速在钢液表面的钢液流动慢的情况下具有能够减少铸模粉末的向钢液2内的卷入的效果,因此成为有效的指标。而且,钢液表面紊流能量的最大值出于与钢液表面最大流速同样的理由而成为有效的指标。
54.操作条件控制部13为了将由钢液流动指标算出部12算出的钢液流动指标控制在适当范围内,根据钢液流动指标来控制铸造速度、电磁搅拌磁场的磁通密度及喷嘴浸渍深度等操作条件。例如,在凝固界面流速为规定值以下的面积超过了预先确定的值的情况下,以增大电磁搅拌磁场的磁通密度而加强电磁搅拌力的方式控制操作条件。这是因为,如果通过电磁搅拌力向铸模内的钢液进一步赋予流速,则即使在凝固界面流速为规定值以下的位置也能以钢液流速增加的方式发挥作用。而且,即使增大电磁搅拌磁场的磁通密度,在凝固界面流速为规定值以下的面积超过预先确定的值而且凝固界面流速为规定值以下的位置接近钢液表面的情况下,依然可以以使浸渍喷嘴的深度变浅的方式控制操作条件。这是因为,如果使浸渍喷嘴的深度变浅,则从浸渍喷嘴喷出的钢液的喷出流的影响会进一步出现于钢液表面侧,并以使钢液表面的钢液流速增加的方式发挥作用。另一方面,通过增大电磁搅拌磁场的磁通密度,虽然凝固界面流速成为规定值以下的面积小于预先确定的值,但是在钢液表面流速及/或钢液表面紊流能量超过规定值的情况下,可以在增大了电磁搅拌磁场的磁通密度的状态下,以加深浸渍喷嘴的深度的方式控制操作条件。这是因为,如果加深浸渍喷嘴的深度,则从浸渍喷嘴喷出的钢液的喷出流的影响不易出现在钢液表面侧,以使钢液表面流速及/或钢液表面紊流能量减少的方式发挥作用。
55.通常,铸模4内的钢液2的流动状态根据连续铸造机1的操作状态的差异而变化。例如图3所示,使用左右的两个部位存在喷出口5a的浸渍喷嘴5的情况下,由于在单侧的喷出口5a附着有氧化铝等夹杂物,有时在铸模4内的钢液2的喷出流产生左右差(偏流)。该偏流即使铸造宽度、铸造速度、电磁搅拌磁场的磁通密度这样的操作条件相同也会产生,因此通过使用设置于铸模4的温度传感器的测定值高精度地再现包含偏流的钢液的流动状态来更高精度地在线推定钢液流动指标。
56.即,以对应于在铸模4设置的温度传感器的测定值的方式,修正钢液流动指标算出部12的计算条件,并将计算值逐次更新,由此在线且更高精度地推定钢液流动指标。需要说明的是,温度传感器的设置数量、间距及测定值的采样间隔只要根据实施本发明的环境等在可能的范围内确定即可。根据本发明者们的研究,如果将温度传感器沿铸造方向及宽度
方向分别以50mm间距以下及100mm间距以下配置,以1秒间隔以下选取测定值,则钢液流动指标算出部12的计算精度进一步提高。通过在线推定钢液流动指标,能够掌握是否能够在缺陷发生风险少的适当范围内进行操作,通过变更操作条件能够将钢液流动指标控制在适当范围内。结果是,能够制造高品质的板坯。
57.需要说明的是,在本实施方式中,将低流速面积作为凝固界面流速成为规定值以下的面积进行了研讨,但是作为钢液流动指标,并不局限于凝固界面其本身的流速。如果在通过电磁搅拌磁场等产生的钢液流动(搅拌流)之中存在成为低流速的区域,则这样的区域对于气泡、夹杂物向凝固界面的补充会造成不良影响,因此可以将其作为钢液流动指标。这样,低流速面积并不局限于凝固界面流速,可以是各种定义的方法。同样,钢液表面流速的最大值及钢液表面紊流能量的最大值表示钢液的表面状态,如上所述与铸模粉末的卷入相关联。因此,作为钢液流动指标,并不局限于上述最大值,能够通过适当规定钢液表面的速度或流动状态而设为钢液流动指标。
58.另外,在钢液流动指标的控制中,优选立足于以下的两点进行。第一点是钢液流动现象为非线性的点。即,如果原本的操作条件不同,则即使使操作条件的变更量相同,钢液流动指标的变化量也不同。图4(a)、(b)是表示电磁搅拌磁场的磁通密度不同的两个条件下的电磁搅拌磁场的磁通密度的变更量与钢液表面最大流速的变化量的关系的图。在图4(a)所示的条件下,即使变更电磁搅拌磁场的磁通密度,钢液表面最大流速也几乎不会变化。相对于此,在图4(b)所示的条件中,当使电磁搅拌磁场的磁通密度上升时,钢液表面最大流速也增加。此外,如上所述,无论操作条件如何,都会在钢液的喷出流产生偏流。因此,相对于操作条件的变更量的钢液流动指标变化的灵敏度可能会时时刻刻地变化,如果预先设置既定的灵敏度,则有时难以将钢液流动指标控制在适当范围内。
59.第二点是在操作条件与钢液流动指标之间存在相互干涉。例如,如果使铸造速度增加,则低流速面积减少而钢液表面最大流速增加。而且,通过变更浸渍喷嘴的浸渍深度而能够使钢液表面最大流速及钢液表面紊流能量的最大值变化。为了将全部的钢液流动指标控制在适当范围内,需要进行将若干的操作条件组合并考虑了干涉的控制。然而,如果通过收敛计算而隐式地求出操作条件的变更量,则计算时间变长,难以动态地控制。因此,希望考虑干涉并显式地算出操作条件的变更量,并反映到下一控制周期中的操作条件中。
60.图5是表示基于作为本发明的一实施方式的连续铸造机的控制装置的操作条件控制处理的流程的流程图。图5所示的流程图每当由钢液流动指标算出部12算出钢液流动指标时开始,操作条件控制处理进入步骤s1的处理。需要说明的是,以下,说明为了将低流速面积s、钢液表面最大流速v及钢液表面紊流能量的最大值e作为钢液流动指标来控制而变更操作条件a、b、c的情况。
61.在步骤s1的处理中,操作条件控制部13判别由钢液流动指标算出部12算出的钢液流动指标是否全部处于适当范围内。在判别的结果是钢液流动指标全部处于适当范围内的情况下(步骤s1:是),操作条件控制部13不进行操作条件的变更而结束一系列的操作条件控制处理。另一方面,在钢液流动指标的至少一个为适当范围外的情况下(步骤s1:否),操作条件控制部13使操作条件控制处理进入步骤s2的处理。
62.在步骤s2的处理中,操作条件控制部13针对操作的对象的操作条件而推定使其各自微小地变化的情况下的钢液流动状态而算出钢液流动指标。需要说明的是,操作条件的
变化量如果从原本的操作条件大幅变化,则钢液流动分布的推定精度可能会恶化,因此优选使其在原本的操作条件的10%以内变化。并且,操作条件控制部13将算出的钢液流动指标与由钢液流动指标算出部12算出的钢液流动指标的差量算出,并算出变更了各个操作条件时的钢液流动指标的灵敏度矢量,由此得到灵敏度矩阵x。得到了变更操作条件a时的钢液流动指标的灵敏度矢量变更了操作条件b时的钢液流动指标的灵敏度矢量及变更了操作条件c时的钢液流动指标的灵敏度矢量时的灵敏度矩阵x如以下的数学式(1)所示。由此,步骤s2的处理完成,操作条件控制处理进入步骤s3的处理。
63.[数学式1]
[0064][0065]
在步骤s3的处理中,操作条件控制部13对由钢液流动指标算出部12算出的钢液流动指标,算出各自的与适当范围的差量值,由此得到偏差矢量y。在低流速面积s、钢液表面最大流速v及钢液表面紊流能量的最大值e的偏差分别为δs、δv、δe的情况下,偏差矢量y如以下所示的数学式(2)表示。由此,步骤s3的处理完成,操作条件控制处理进入步骤s4的处理。
[0066]
[数学式2]
[0067][0068]
在步骤s4的处理中,操作条件控制部13使用通过步骤s2的处理而得到的灵敏度矩阵x及通过步骤s3的处理得到的偏差矢量y,通过最小二乘法而算出最优的操作条件的变更量矢量z=(δa、δb、δc)。以下的数学式(3)表示灵敏度矩阵x、偏差矢量y、操作条件的变更量矢量z及与误差矢量ε的关系。最小二乘法是将使数学式(3)中的误差矢量ε的平方和最小的变更量矢量z作为最优解而求出的方法,最优的操作条件的变更量矢量z能够通过以下所示的数学式(4)算出。这样,最优的操作条件的变更量矢量z基于作为已知量的原本的操作条件及由钢液流动指标算出部12算出的钢液流动指标而被显式地算出。由此,步骤s4的处理完成,操作条件控制处理进入步骤s5的处理。
[0069]
[数学式3]
[0070][0071]
[数学式4]
[0072][0073]
在步骤s5的处理中,操作条件控制部13将通过步骤s4的处理得到的最优的操作条件的变更量矢量z=(δa、δb、δc)反映到操作条件中,设为下一控制周期中的操作条件。具体而言,操作条件控制部13在下一控制周期中使用操作条件a+δa、b+δb、c+δc。由此,
步骤s5的处理完成,一系列的操作条件控制处理结束。
[0074]
实施例
[0075]
作为本实施例,在极低碳素钢的连续铸造中应用了本发明。铸模尺寸为宽度1200mm、厚度260mm,稳态状态的铸造速度为1.6m/min。在本实施例中,将低流速面积的适当范围设定为0.02m2以下,将钢液表面最大流速的适当范围设定为0.05~0.30m/s而进行了操作。在操作过程中,为了使在连续铸造机1的操作中算出的低流速面积比适当范围大而将电磁搅拌磁场的磁通密度增大了5%。其结果是,如图6所示,铸模4内的钢液搅拌力增强,凝固界面流速上升,低流速面积减少。然而,通过该操作条件的变更而钢液搅拌力增强,由此如图7所示,钢液表面最大流速有时会超过适当范围。因此,将喷嘴浸渍深度加深了30mm。这是因为,浸渍喷嘴5的喷出流与铸模铜板碰撞、反转而流动与搅拌流重合,提高了钢液表面流速,因此通过加深浸渍喷嘴5的浸渍深度而反转流减小,能够抑制钢液表面流速。通过该操作条件变更,如图8所示,能够减小低流速面积,并将钢液表面最大流速控制在适当范围内。而且,通过在线地推定钢液流动指标(钢液表面最大流速、低流速面积及钢液表面紊流能量的最大值),能够控制用于使钢液流动指标处于适当范围的操作条件,结果是,如图9所示,能够降低作为板坯品质指标的板坯的缺陷混入率。这样,确认了根据本发明的连续铸造机的控制方法,能够制造优异的品质的板坯的情况。
[0076]
在图10(a)~(d)所示的实施例中,在模拟上,作成人工地使堵塞浸渍喷嘴那样的干扰产生的假想设备,确认了通过操作电磁搅拌磁场的磁通密度及铸造速度,是否能够利用作为本发明的一实施方式的连续铸造机的控制装置将根据假想设备算出的低流速面积及钢液表面最大流速控制在适当范围内。在图10(a)~(d)所示的时间t=t1的定时产生干扰时,在由钢液流动指标算出部12算出的低流速面积及钢液表面最大流速与假想设备的低流速面积及钢液表面最大流速之间产生了推定误差。接下来,在图10(a)~(d)所示的时间t=t2的定时开始钢液流动状态推定处理时,由钢液流动指标算出部12算出的低流速面积及钢液表面最大流速与假想设备的低流速面积及钢液表面最大流速的推定误差减少。此外,在图10(a)~(d)所示的时间t=t3的定时开始了操作条件控制处理时,电磁搅拌磁场的磁通密度上升,铸造速度下降,假想设备的低流速面积及钢液表面最大流速能够控制为适当范围的上限附近。根据该情况,确认了通过在线的推定钢液流动指标(钢液表面最大流速、低流速面积及钢液表面紊流能量的最大值),能够随时控制用于使钢液流动指标处于适当范围的操作条件,能够制造出高品质的板坯。需要说明的是,在图10(a)~(d)中,虚线l1表示假想设备的低流速面积,线l2表示通过钢液流动指标算出部12算出的低流速面积,虚线l3表示假想成套设备的钢液表面最大流速,线l4表示由钢液流动指标算出部12算出的钢液表面最大流速。
[0077]
以上,说明了应用了由本发明者们作出的发明的实施方式,但是本发明并非通过形成基于本实施方式作出的本发明的公开的一部分的记述及附图被限定。例如,在图10(a)~(d)所示的实施例中,进行了操作电磁搅拌磁场的磁通密度及铸造速度情况的验证,但是低流速面积、钢液表面流速、钢液表面紊流能量等流动指标也能够通过操作电磁搅拌磁场的磁通密度进行控制。这样,基于本实施方式而由本领域技术人员等作出的其他的实施方式、实施例及运用技术等全部包含于本发明的范畴。
[0078]
工业实用性
[0079]
根据本发明,能够提供一种能够制造高品质的铸片的连续铸造机的控制方法、连续铸造机的控制装置及铸片的制造方法。
[0080]
标号说明
[0081]
1 连续铸造机
[0082]
2 钢液
[0083]
3 中间包
[0084]
4 铸模
[0085]
5 浸渍喷嘴
[0086]
10 控制装置
[0087]
11 钢液流动状态推定部
[0088]
12 钢液流动指标算出部
[0089]
13 操作条件控制部