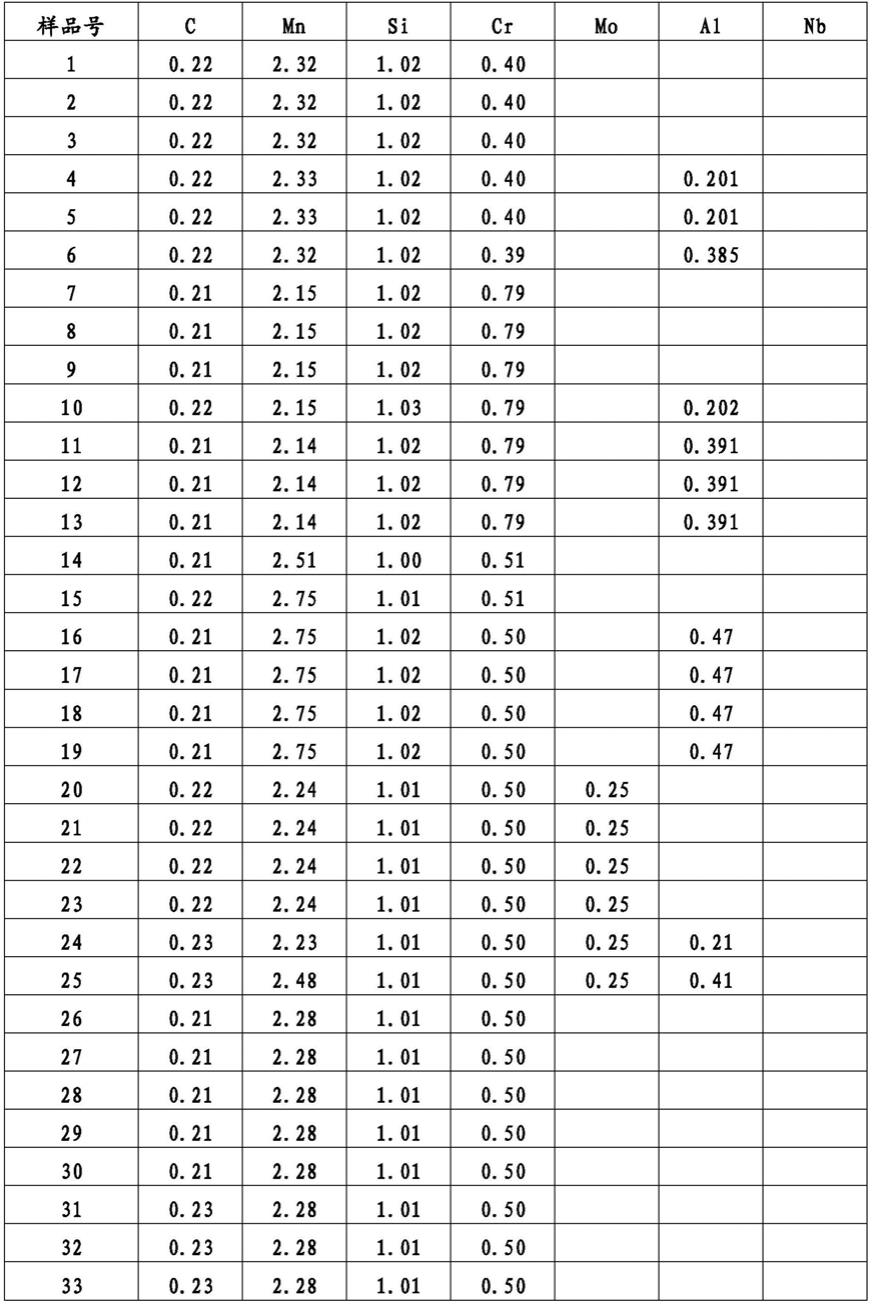
高延展性涂锌钢片材产品
1.相关申请的交叉引用
2.本技术要求2019年8月7日提交的美国临时专利申请no.62/883,704的益处,其通过引用并入本文。
技术领域
3.本发明涉及高延展性的涂锌钢片材产品,更具涉及具有受控量的si、cr、mo和al合金化添加剂的钢片材产品,所述钢片材产品经受淬火和配分(partition)过程以产生所需的机械性能,包括高的极限拉伸强度、高延展性和高扩孔率。
背景技术:4.淬火和配分的钢通常具有高硅含量,使得可以抑制碳化物析出,并且残留奥氏体用于高的强度和延展性的组合。至少1.5重量%的硅添加是典型的。然而,这种硅添加导致热轧钢中的晶界氧化层,这在酸洗期间难以去除。硅添加也与涂锌钢的焊接中的液态金属脆化有关,导致低强度焊缝。
技术实现要素:5.本发明提供了具有受控组成的高延展性钢片材产品,所述组成与受控热循环组合,产生所需的显微组织和有利的机械性能,包括至少1180mpa的极限拉伸强度、高的延展性、扩孔率、可弯曲性和成型性。钢组成包括受控量的碳、锰、硅和铬。可以以受控的量包含钼和铝。使轧制片材经受热循环,其包括加热阶段,然后淬火至低于马氏体开始温度和时效。
6.本发明的一个方面是提供一种淬火和配分的钢片材产品,其包含0.12-0.5重量%的c,1-3重量%的mn,0.4-1.1重量%si,0.2-0.9重量%cr,至多0.5重量%的mo,至多1重量%的al,其中钢片材产品包含马氏体、铁素体和残留奥氏体,并且具有至少1180mpa的极限拉伸强度、至少13%的总伸长率和至少25%的扩孔率。
7.本发明的另一方面是通过如下方式提供一种制造上述淬火和配分钢片材的方法:将钢片材产品加热到至少720℃的均热温度,将加热的钢片材产品淬火至低于马氏体开始温度的淬火温度,并在淬火温度或大于淬火温度的温度下将淬火钢片材产品进行时效,从而产生淬火和配分的钢片材产品。
8.本发明的另一方面是提供一种制造淬火和配分的钢片材产品的方法,该钢片材产品包含0.12-0.5重量%的c,1-3重量%mn,0.4-1.1重量%si,0.2至0.9重量%的cr,至多0.5重量%的mo,至多1重量%的al。该方法包括使钢片材产品经受至少720℃的均热温度,将加热的钢片材产品淬火至低于马氏体开始温度的温度,并在淬火温度或大于淬火温度的时效温度下将淬火的钢片材产品进行时效以由此产生淬火和配分的钢片材产品。钢片材产品包括马氏体、铁素体和残留奥氏体,并且具有至少1180mpa的极限拉伸强度,至少13%的总伸长率,和至少25%的扩孔率。
9.从以下描述中,本发明的这些和其他方面将更加明显。
10.附图的简要说明
11.图1是根据本发明的实施方案的温度与时间的曲线图,说明了任选的第一退火过程,然后是根据本发明的实施方案的淬火和配分热循环,包括淬火和时效。
12.图2是经受图1的淬火和配分过程的钢片材产品的显微照片。
13.本发明的高延展性钢片材产品具有受控的组成,其与受控的热循环组合,产生所需的显微组织和有利的机械性能,包括至少1180mpa的极限拉伸强度,高的延展性、扩孔率、弯曲性和成型性。钢组成包括受控量的碳、锰、硅、铬和钼,并且还可以包括铝,以及本领域技术人员已知的其他合金化添加剂。
14.该钢组成通常可包括0.12-0.5重量%的c,1-3重量%mn,0.4-1.1重量%的si,0.2-0.9重量%的cr,至多0.5重量%的mo。例如,钢组成可包括0.15至0.4重量%的c,2-2.8重量%的mn,0.5-1.0重量%的si,0.15-0.8重量%的cr,0.1或0.15-0.4重量%mo。在某些实施方案中,钢组成可包括0.2-0.25重量%的c,2.1-2.5重量%的mn,0.6-0.9重量%的si,0.3-0.7重量%的cr,0.2-0.3重量%的mo。铝可以以至多1重量%的量添加到钢组成,例如0.1%至0.7重量%,或0.2-0.5重量%。
15.已经发现,mn、si、cr、mo和al的受控组合导致高延展性1180片材钢产品中的优异性能,该片材钢产品具有小于1.1重量%,或小于1.0重量%,或小于0.95重量%,或小于0.90重量%,或小于0.85重量%,或小于0.80重量%的相对低的si含量。低si在涂锌片材的焊接过程中提供加工的便利和对液态金属脆化的良好耐受性。
16.在本发明的钢片材产品中,c提供了增加的强度并促进残留奥氏体的形成。mn提供硬化并用作固溶体增强剂。si在热处理过程中抑制碳化铁析出,并增加奥氏体保留。cr与mo组合提供了回火耐受性,并且可以抑制碳化物析出,特别是当与si或者si和al组合使用时。al抑制热处理过程中的碳化铁析出,并增加奥氏体保留。可以任选地添加ti和nb作为增大强度的晶粒细化剂。
17.除了上面列出的c、mn、si、cr、mo和a1的量之外,钢组成还可包括次要或杂质量的其他元素,例如至多0.05ti,至多0.05nb,至多0.015s,最多0.03p,最多0.2cu,最多0.2ni,最多0.1sn,最多0.015n,最多0.1v和最多0.004b。当提到钢片材产品的组成时,如本文所用的术语“基本上不含”意味着不有意地将特定元素或材料添加到组成中,并且仅作为杂质或痕量存在。
18.将具有如上所述的组成的钢片材产品进行淬火和配分加热过程,如下面更全面的描述的那样。已经发现,所得片材产品具有良好的机械性能,包括高伸长率、期望的极限拉伸和屈服强度、高弯曲性和高扩孔率。
19.如使用标准astm-l测试通过总伸长率(te)测量,钢片材产品可以具有高延展性,通常为至少12%,例如至少13%,或至少14%,或至少15%。例如,钢片材产品可具有13或14%至19%或更高的总伸长率。
20.钢片材产物的极限拉伸强度(uts)通常为至少1180mpa,例如1180至1370mpa。在某些实施方案中,uts可以小于1370mpa,或小于1350mpa,或小于1320mpa。钢片材产物的屈服强度(ys)通常为至少700mpa,例如700至1,100mpa。
21.钢片材产品可实现大于15,000mpa%的强度伸长率平衡(uts
·
te),例如大于17,
000mpa%,或大于18,000mpa%,或大于20,000mpa%。
22.钢片材产品具有高的扩孔率(he),例如至少25%,或至少30%,或至少32%,或至少34%。
23.用于钢片材产品的uts
·
te
·
he(mpa%2)的组合可以大于37.5
×
104,例如大于42.5
×
104,或大于50
×
104,或大于54
×
104,或大于64
×
104,或大于68
×
104。
24.钢片材产品具有例如至少2r/t或至少2.5r/t的高弯曲性(r/t)。
25.根据本发明的某些实施方案,钢片材产品的最终显微组织可以主要包含马氏体,例如50至80体积%,以及较少量的铁素体,例如5至35体积%,和较少量的残留奥氏体,例如1至20体积%。残留奥氏体通常占大于5体积%,或大于8体积%。在某些实施方案中,残留奥氏体可占5至16体积%,或8至15体积%,或10至14体积%,或者11至12体积%。贝氏体也可以以少量存在,例如从零到5体积%或10体积%或15体积%。这些相的量可以通过标准ebsd技术确定。
26.先奥氏体可以具有1至20微米的平均晶粒尺寸,例如5至10微米。铁素体可以具有1至20微米的平均晶粒尺寸,例如3至5微米。残留奥氏体的平均晶粒尺寸可小于2微米,或小于1微米,或小于0.5微米。残留奥氏体晶粒可以基本上等轴,并且可以具有小于3:1,或小于2:1,或小于1.9:1的平均纵横比。
27.淬火和配分热循环
28.淬火和配分热循环涉及加热,然后淬火到低于马氏体开始温度并在初始淬火温度下或大于初始淬火温度下直接时效。通过适当的合金化抑制碳化物析出,并将来自过饱和马氏体相的碳配分到未转化的奥氏体相,从而在随后冷却至室温时增加残余奥氏体的稳定性。该处理可以称为淬火和配分(q&p)。
29.第一退火或均热阶段可以在相对高的退火温度下进行,在温度降低到低于马氏体开始时进行第二淬火或冷却阶段,在将片材产品再加热到相对低的保持温度并保持所需的时间段时进行第三时效或保持阶段。控制温度以促进最终产品中所需的显微组织和机械性能的形成。
30.在均热阶段中的部分或完全奥氏体化之后,将钢淬火至计算的温度(qt),以产生预先确定的马氏体和未转化的奥氏体的平衡分数。然后将钢升高到配分温度(pt),当碳逃逸到未转化的奥氏体中时,提高其化学稳定性,使得在配分后在随后冷却至环境温度后,奥氏体得到残留。随着在配分期间未转化的奥氏体富集碳,抑制了其有效的m
s-mf温度范围。为了化学稳定化,ms应降低到室温或以下。
31.在第一退火阶段中,可以使用a1和a3之间的均热区温度,例如可以使用至少720℃的退火温度。在某些实施方案中,均热区温度通常可以为720至890℃,例如760至825℃。在某些实施方案中,峰值退火温度通常可以保持至少15秒,例如20至300秒,或30至150秒。
32.均热区温度可以通过例如以0.5至50℃/秒,例如约2至20℃/秒的平均速率将钢从低于ms相对低温(例如室温)加热来实现。在某些实施方案中,温升(ramp-up)可需要25至800秒,例如100到500秒。第二循环的第一加热阶段可以通过任何合适的加热系统或方法来实现,例如使用辐射加热、感应加热、直接烧制的炉加热等。
33.在达到均热区温度并保持所需的时间段后,可以将钢冷却到高于室温的受控温度到保持区。钢可以通过水冷却,气体冷却等来冷却至低于马氏体起始以形成马氏体。可以使
用5至200℃/秒,例如20至100℃/秒或30至80℃/秒的典型整体淬火速率。淬火可以将钢片材产品的温度降低到150至350℃,例如220至300℃,或250至280℃的典型淬火温度。任何合适类型的冷却和淬火系统都可以适用于从均热温度冷却到保持温度,包括上述那些。
34.在某些实施方案中,可以使用多个淬火速率,例如第一相对慢的淬火速率,然后是第二相对快速的淬火速率。例如,第一淬火速率可以为每秒1至30℃以达到500至800℃的第一淬火温度,然后以每秒5至200℃的第二淬火速率达到上述最终淬火温度。在某些实施方案中,第一淬火速率可以为每秒5至20℃,以达到630至700℃的第一淬火温度,然后是每秒20至200℃的第二淬火速率到达最终淬火温度。
35.在淬火后,然后将钢加热至更高的保持温度用于回火和上述配分过程。在某些实施方案中,在均热和保持阶段之间将钢片材产品维持在高于300℃的温度。
36.根据本发明的实施方案,时效或保持区步骤在例如300至440℃的典型温度下进行,例如370至430℃。保持区可以保持至多800秒,例如30到600秒。例如,时效可以在350至450℃的pt下进行30至300秒,或在370至430℃下进行60至180秒。
37.保持区温度可以保持恒定,或者可以在所选的温度范围内稍微变化。在保持之后,可以例如通过感应或其他加热方法再加热钢至例如约470℃的温度从而在为良好的涂层结果而适当的温度下进入热浸涂布罐,如果要热浸涂钢。
38.在某些实施方案中,在维持时效或保持区温度所需的时间段之后,温度可以降至室温。这种降温通常可需要10至1000秒,例如约20至500秒。这种降温的速率通常可以为1至1,000℃/秒,例如2至20℃/秒。
39.在某些实施方案中,在保持区的末端将淬火和配分的钢片材进行热浸镀锌。镀锌温度通常可以在440至480℃,例如450至470℃的范围内。作为替代或补充,可以在480℃至530℃的典型温度下进行镀锌退火。
40.在某些实施方案中,可以作为在连续镀锌生产线(cgl)上的第二步退火过程的一部分进行镀锌步骤。该cal+cgl过程可用于生产锌基或锌合金基的热浸镀锌产品,或者在涂覆后再加热以生产铁-锌镀锌退火型的涂覆产品。可以在cal和cgl步骤之间进行任选的镍基涂覆步骤,以改善锌涂层性能。在第二步骤中使用连续镀锌生产线可以相对于使用cal+cal+eg途径增加生产涂覆产品的生产效率。还可以在特殊设计的cgl上制造镀锌产品或锌基合金热浸涂覆产品,其中两步退火可以在单一生产线中进行。在这种情况下镀锌退火也可以是个选择。此外,还可以专门设计和构建单个生产设施,以结合两个循环热过程以生产钢片材产品。
41.初始热循环
42.在本发明的某些实施方案中,使用两个热循环过程来生产具有有利机械性能的高的延展性和强度的钢产品,例如上述那些。在第一和第二热循环中的每个内,可以使用用于进行热处理的多种方法。第一热循环退火方法的实例描述于美国专利no.10,385,419中,其通过引用并入本文。连续退火线(cal)可用于第一循环,然后是连续镀锌线(cgl)用于第二循环。
43.可以使用初始退火过程,例如以实现马氏体显微组织。根据本发明的实施方案,在第一热循环的第一退火阶段,可以使用高于a3温度的退火温度,例如可以使用至少820℃的退火温度。在某些实施方案中,第一阶段退火温度通常可以为830至980℃,例如830至940
℃,或840至930℃,或860至925℃。在某些实施方案中,峰值退火温度通常可以保持至少20秒,例如20至500秒,或30至200秒。可以通过常规技术,例如非氧化或氧化直燃炉(dff)、富氧的dfi、感应、气体辐射管加热,电辐射加热等来实现加热。在美国专利no.5,798,007;7,368,689;8,425,225和8,845,324,美国专利申请no.2009/0158975,和转给fives stein的已公布pct申请号wo/2015083047中公开了可以适用于本发明方法的加热系统的实例。可以适用于本发明方法的加热系统的另外实例包括转给drever international的美国专利no.7,384,489,以及转给nippon steel和sumitomo metal corporation的美国专利no.9,096,918。任何其他合适的已知类型的加热系统和方法可以适用于第一和第二循环。
44.在第一阶段,在达到峰值退火温度并保持所需的时间段之后,将钢淬火至室温,或至高于室温的受控温度下,如下文所更详细地描述。淬火温度可能不一定是室温,但应低于马氏体开始温度(ms),优选低于马氏体结束温度(mf),以形成主要马氏体的显微组织。在某些实施方案中,在第一步骤过程和第二步骤过程之间,钢片材产品可以冷却至低于300℃的温度,例如低于200℃。
45.淬火可以通过诸如水淬、浸没式刀具/喷嘴水淬、气体冷却,使用冷、温或热水和气体的组合的快速冷却、水溶液冷却、其他液体或气体流体冷却、冷却辊淬火、水雾喷射、湿闪速冷却、非氧化湿闪速冷却等的常规技术来实现。通常可以使用30至2,000℃/秒的淬火速率。
46.本领域技术人员已知的各种类型的冷却和淬火系统和方法可以适用于本发明的方法。常规用于商业基础的合适的冷却/淬火系统和方法可包括水淬、水雾冷却、干燥闪速和湿式闪速、氧化和非氧化冷却、烷烃流体至气相变化冷却、热水淬火,包括两个步骤的水淬、辊淬火、高百分比氢或氦气体喷射冷却等。例如,可以使用干燥闪速和/或湿式闪速氧化和非氧化冷却/淬火,例如给fives stein的已公开pct申请号wo2015/083047中公开的。描述了可以适用于本发明方法的冷却/淬火系统和方法的其他fives stein专利文献包括美国专利no.6,464,808b2;6,547,898b2;和8,918,199b2和美国专利申请公开no.us2009/0158975a1;us2009/0315228a1;和us2011/0266725a1。可以适用于本发明方法的冷却/淬火系统和方法的其他实例包括美国专利no.8,359,894b2;8,844,462b2;和7,384,489b2,和美国专利申请公开号2002/0017747a1和2014/0083572a1中公开的那些。
47.在某些实施方案中,在达到第一阶段峰值退火温度并将钢淬火以形成马氏体之后,可以任选地回火马氏体以使钢稍微软化,以使进一步加工更加可行。通过将在室温范围内的钢的温度升高到约500℃并保持至多600秒来进行回火。如果利用回火,则回火温度可以保持恒定,或者可以在该优选范围内变化。
48.在回火后,温度可以降至室温。这种降温的速率通常可以在1至40℃/秒的范围内,例如2至20℃/秒。在单道次设施炉的情况下,可能不需要回火。
49.根据某些实施方案,可以在连续退火生产线(cal)上执行初始热循环和淬火与配分热循环过程中的一个或两个。经过cal+cal过程后,可以将钢进行电镀锌以产生锌基的涂覆产品,并且如果需要,也可以镀锌退火。
50.以下实施例旨在说明本发明的各个方面,并且不旨在限制本发明的范围。
51.实施例1
52.使冷轧钢片材经受如图1中所示的双循环加热过程,该钢片材的组成为0.22重
量%c,2.3重量%mn,1.0重量%si,0.5重量%cr,0.25重量%mo和0.4重量%al。如图1所示,在第一循环中,将钢片材加热至890℃以奥氏体化钢,并迅速冷却。在第二淬火和配分循环中,达到823℃的峰值温度,然后将片材慢速喷嘴冷却至660℃,快速淬火至230℃,在400℃下过时效,并从约470℃涂覆锌。使用以下处理参数(℃):930rts1、660sjc1、30rjc1、800rts2、660sjc2、231rjc2、400oa1、400oa2和470gi。所得钢制产品包括12.7%的残留奥氏体(ra),并显示出以下的机械性能:41%he,1016mpa ys,1222mpa uts,12.3%ue,16.6%te和20285mpa
·
%uts
·
te。所得产品的显微组织如图2所示。显微组织主要由回火马氏体组成,兼具有细长的条间(interlath)和小的等轴残留奥氏体,量为12.7%。也可以存在少量等轴铁素体。也可有少量的无碳化物的贝氏体。
53.实施例2
54.将具有如表1中列出的组成的冷轧钢片材进行如表2列出的淬火和配分加热过程。所得钢片材产品表现出如表3所列出的机械性能。
55.表1
56.组成(重量%)
57.[0058][0059]
表2
[0060]
热循环(℃)
[0061]
[0062][0063]
表3
[0064]
机械性能
[0065]
[0066][0067]
根据本发明的实施方案,在添加相对低量的al时减小si的量。相比之下,用大量铝部分替代硅导致较低的强度和强度-延展性平衡的降低。具有0.24重量%的碳,2.4重量%的锰,0.6重量%的si和0.8重量%的比较性钢导致了1018mpa ys,1100mpa uts,8.6%ue和14.2%te的性能。在该样品中,使用以下处理参数(c
°
):930rts1、800sjc1、30rjc1、900rts2、730sjc2、270rjc2、360oa1、360oa2、470gi和510ga。发现这种退火参数没有导致达到1180mpa的所需极限拉伸强度。
[0068]
采用1重量%的si和相对较少量的al,并且添加0.4-0.8重量%cr,可以实现强度最小值(参见样品号4-6、10-13和38-39),虽然总伸长率为12-14%。铝合金添加稍微增加总伸长率,尽管在某些情况下也导致了强度的降低。表4比较了含al的样品号12和13与无al的样品号3和9。
[0069]
表4
[0070]
组成(重量%)
[0071]
样品号cmnsicrmoalheysutsuete30.222.321.020.40003180811968.412.690.212.151.020.79001980912007.611.3120.212.141.020.7900.3913996811999.714.1130.212.141.020.7900.3913195511969.713.7
[0072]
随着mn的增加(参见样品号14-19),增大了强度和伸长率,但强度相对较高(在约1300mpa),且扩孔率降低。铝添加降低强度和增加伸长率,但扩孔率保持低,如表5所示。
[0073]
表5组成(重量%)
[0074]
样品号cmnsicrmoalheysutsuete150.222.751.010.5100.002794512989.613.9170.212.751.020.5000.4724971125213.918.7
[0075]
采用0.25重量%的mo添加(参见样品号20-25和40-50),强度增加,具有相似伸长率,用于增加uts
·
te。强度增加到约1300mpa,几乎处于所需强度范围的最大值,如表6所示,样品号21。然而,与mo组合的al添加导致了与没有mo类似的强度,连同改善的总伸长率和扩孔率,如表6所示,样品号41。
[0076]
表6.组合物(重量百分比)
[0077]
样品号cmnsicrmoalheysutsuete210.222.241.010.500.250.0018968130410.815.4410.212.270.990.500.250.434989124512.316.6
[0078]
利用si、cr、al和mo合金化产生的性质的优化组合,鉴别到用于更好的酸洗和焊接行为的进一步si减少(参见样品号45和50)。发现良好的性质保持在0.6-0.7重量%的si,如表7所示。还进行了nb的添加,这增加了强度和延展性,但是扩孔率在所需范围以下(表7,样品号51)。
[0079]
表7.组合物(重量百分比)
[0080]
样品号cmnsicrmoalnbheysutsuete450.222.270.630.500.250.43 34979119910.214.8500.222.260.700.500.250.43 32918122210.815.3510.212.290.790.500.250.410.02818875124812.917.3
[0081]
如本文所用,在本技术的上下文中“包含”、“包含”和相似的术语理解为与“包含”同义,因此是开放式的,并且不排除额外的未描述或未提及的元素,材料,阶段或方法步骤。如本文所用,在本技术的上下文中的“由...组成”理解为排除任何未指定的元素,材料,阶段或方法步骤的存在。如本文所用,在本技术的上下文中的“基本由...组成”理解为包括所指定的元素,材料,阶段或方法步骤,在适用时还包括任何不实质影响本发明的基本或新颖特征的未指定的元素,材料,阶段或方法步骤。
[0082]
尽管阐述本发明的广泛范围的数值范围和参数是近似的,但是尽可能精确地报告特定实施例中列出的数值。然而,任何数值都固有地包含必然由它们各自的测试测量中的标准变化导致的某些误差。
[0083]
此外,应该理解,本文所述的任何数值范围旨在包括其中所述的所有子范围。例如,“1到10”的范围旨在包括所述最小值1和所述最大值10(并且包括)之间的所有子范围,即具有等于或大于1的最小值和等于或小于10的最大值。
[0084]
在本技术中,除非另外特别说明,否则单数的使用包括复数,且复数涵盖单数。另外,在本技术中,除非另外特别说明,否则使用“或”或意指“和/或”,即使可以在某些情况下明确地使用“和/或”。在本技术和所附权利要求中,除非明确且清楚地限于一个指代物,否则“一”、“一个”和“该”包括复数指代物。
[0085]
尽管上面已经描述了本发明的特定实施方案用于说明目的,但本领域技术人员将清楚,可以在不脱离所附权利要求定义的本发明的情况下进行本发明的细节的许多变化。