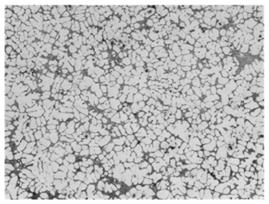
1.本发明属于铝合金制备技术领域,具体涉及一种利用废铝制备高强耐磨铸造铝硅合金的方法。
背景技术:2.铸造铝硅合金具有优良的铸造流动性、机械加工性能和耐磨性能,广泛应用于汽车、摩托车、农机具、电动工具等领域铸造形状结构复杂的零部件,如发动机缸体、缸套、活塞、刹车块、带轮、齿轮泵轴承等。随着汽车、摩托车、农机具、电动工具等向轻量化发展,零部件也不断向薄壁化、轻量化发展,这要求铸造铝硅合金具有更高的强度、塑性和耐磨性,使现有铸造铝硅合金强度偏低、塑形较差、耐磨性不足的问题日益突出。
3.现有铸造铝硅合金强度偏低、塑性较差、耐磨性不足的原因包括如下:首先是铸造铝硅合金由于si含量较高,si在铸造铝硅合金中是以针状共晶si和粗大块状初生si形式共同存在,针状共晶si和粗大块状初生si属于硬脆相,同样会严重割裂铝基体,降低铸造铝硅合金的强度、塑性和耐磨性能。其次是铸造铝硅合金的含fe量较高,fe在铝硅合金中通常是以粗大的针状al
‑
fe
‑
si系富fe相形式存在铸造铝硅合金基体中,这种粗大的针状富fe相本身属于硬而脆的金属间化合物相,会严重割裂铝基体,成为铸造铝硅合金受力断裂的裂纹源和裂纹扩展方向。
4.另外,现有铸造铝硅合金主要以纯铝为主要原材料,在熔炼铸造过程中再加入硅、镁、铜等合金元素来制备得到。众所周知,纯铝是由氧化铝电解得到,而氧化铝的电解属于高能耗行业,需要消耗大量的电力资源,再加上铝矿资源的开采、氧化铝的生产以及硅、镁、铜等合金元素的生产,导致现有方法生产铸造铝硅合金,需要消耗大量的煤炭电力资源,同时还会排放大量的二氧化碳、粉尘和固体废弃物,不仅增加了铸造铝硅合金的生产成本,还会造成严重的环境污染。
5.我国是铝合金生产和消费大国,每年需要消耗大量的铝合金,同时每年又会源源不断地产生大量铝合金废料,如建筑、汽车、摩托车、船舶、飞机、电子电器等领域报废后回收的铝合金零部件、型材、管材、板材等,以及生产过程中产生的大量铝合金边角料、切屑料等。利用铝合金废料来制备铸造铝硅合金,不仅可以降低铸造铝硅合金的生产成本,还可减少大量煤炭电力资源的消耗以及二氧化碳、粉尘和固体废弃物的排放。因此,利用铝合金废料来制备铸造铝硅合金,对于实现铸造铝行业的节能减排、环境保护、提高铝合金废料的使用价值和降低铸造铝硅合金的生产成本都具有十分重要的意义。因此,现有铸造铝硅合金的制备方法仍有待改进和发展。
技术实现要素:6.本发明的目的在于克服现有技术存在的不足,提供一种利用废铝制备高强耐磨铸造铝硅合金的方法,以铝合金废料为主要原材料,通过优化设计铝合金废料的组成和细化变质处理,制备高强耐磨的铸造铝硅合金,降低铸造铝硅合金的生产成本。
7.为达到上述目的,本发明是通过如下手段得以实现的:本发明第一方面提供了一种利用废铝制备高强耐磨铸造铝硅合金的方法,包括如下步骤:(1)选择铝硅合金废料作为原材料,加热熔化成铝硅合金液;(2)在铝硅合金液中加入铝镍碳合金、铝钡合金和铝硼合金进行细化变质处理;(3)使用惰性气体和铝合金精炼剂对铝硅合金液喷吹精炼进行除气除杂处理,扒渣后再静置;(4)将除气除杂处理后的铝硅合金液用金属模铸造成铝硅合金;(5)将铸造铝硅合金加热后淬水进行固溶处理;(6)将固溶处理后的铸造铝硅合金加热1
‑
2小时,然后降温后继续加热2
‑
3小时进行时效处理,随炉冷却后得到高强耐磨铸造铝硅合金。
8.作为优选地,所述铝硅合金废料由以下质量百分比的成分组成:si 16.0
‑
18.0%,cu 0.2
‑
0.8%,fe 0.2
‑
0.5%,余量为al和不可避免的杂质,杂质单个含量≤0.05%,杂质总量≤0.15%。铝硅合金废料是以元素硅为主要合金元素的铝合金废料,这类铝硅合金废料来源广泛,如各种报废回收的汽车、摩托的发动机缸体、活塞等。
9.作为优选地,步骤(1)所述原材料中还包含选自铝铜合金废料、铝镁合金废料、铝钛合金废料、铝铁合金废料中的一种或多种。
10.更优选地,所述铝铜合金废料由以下质量百分比的成分组成:cu 8.0
‑
10.0%,fe 0.4
‑
1.0%,cr 0.1
‑
0.3%,余量为al和不可避免的杂质,杂质单个含量≤0.05%,杂质总量≤0.15%。
11.更优选地,所述铝镁合金废料由以下质量百分比的成分组成:mg 7.0
‑
9.0%,cu 0.8
‑
2.0%,fe 0.4
‑
1.0%,si 0.4
‑
1.6%,余量为al和不可避免的杂质,杂质单个含量≤0.05%,杂质总量≤0.15%。
12.更优选地,所述铝钛合金废料由以下质量百分比的成分组成:ti 11.0
‑
13.0%,cu 4.0
‑
6.0%,mg 4.0
‑
6.0%,余量为al和不可避免的杂质,杂质单个含量≤0.05%,杂质总量≤0.15%。
13.更优选地,所述铝铁合金废料由以下质量百分比的成分组成:fe 1.0
‑
1.5%,cu 0.1
‑
0.4%,余量为al和不可避免的杂质,杂质单个含量≤0.05%,杂质总量≤0.15%。
14.其中铝铜合金废料是以元素铜为主要合金元素的铝合金废料,这类铝铜合金废料来源广泛,如飞机报废后产生的各种板材、型材、锻件、棒材等。
15.铝镁合金废料是以元素镁为主要合金元素的铝合金废料,这类铝镁合金废料来源广泛,如报废回收的船板、压力容器、冷藏集装箱、电视塔等。
16.铝钛合金废料是以元素钛为主要合金元素的铝合金废料,这类铝钛合金废料来源广泛,如飞机、潜艇、武器装备领域报废回收的各种铝钛合金零部件等。
17.铝铁合金废料是以元素铁为主要合金元素的铝合金废料,这类铝铁合金废料来源广泛,如各种报废回收的铝铁合金导线、铝铁合金板料等。
18.上述步骤(1)中,为了降低加热熔化的能耗和降低生产成本,应当选用节能环保的熔铝炉,加热熔化的温度不能太低,否则熔化速度慢,生产效率低,温度也不宜太高,否则容易引起铝的氧化耗损。另外,为了提高铝合金液成分的均匀性,防止合金元素产生偏析,需
要对铝合金液进行充分搅拌,如选用炉底带有永磁搅拌的熔铝炉进行加热熔炼,这是铝合金熔铸领域技术人员公知的常识。
19.作为优选地,以原材料总质量计,所述原材料包含以下质量百分比的各成分:75
‑
80%的铝硅合金废料、12
‑
15.1%的铝铜合金废料、3
‑
5%的铝镁合金废料、2
‑
4%的铝钛合金废料和1
‑
3%的铝铁合金废料。
20.作为优选地,步骤(1)中所述加热温度为760
‑
780℃。
21.作为优选地,以原材料总质量计,步骤(2)中所述铝镍碳合金、铝钡合金和铝硼合金的质量百分比分别为0.2
‑
0.4%、0.1
‑
0.2%和0.1
‑
0.2%。
22.更优选地,所述铝镍碳合金由以下质量百分比的成分组成:ni 4.8
‑
5.2%,c 0.8
‑
1.2%,余量为al和不可避免的杂质,杂质单个含量≤0.05%,杂质总量≤0.15%。
23.更优选地,所述铝钡合金由以下质量百分比的成分组成:ba 24.5
‑
25.5%,余量为al和不可避免的杂质,杂质单个含量≤0.05%,杂质总量≤0.15%。
24.更优选地,所述铝硼合金由以下质量百分比的成分组成:b 9.5
‑
10.5%,余量为al和不可避免的杂质,杂质单个含量≤0.05%,杂质总量≤0.15%。
25.上述步骤(2)中,加入铝镍碳合金的目的是细化α
‑
a晶粒,改善铸造流动性和组织均匀性,提高强度和塑性;加入铝钡合金的目的是细化变质粗大的针片状共晶si相,消除其对塑性和韧性的危害,提高铸造铝硅合金的强度、塑性和耐磨性能;加入铝硼合金的目的是细化变质粗大的针状富铁相,提高铸造铝硅合金的强度、塑性和耐磨性能。
26.作为优选地,步骤(3)中所述惰性气体选自氮气或氩气中的一种或多种,更优选为纯度为99.9%的氩气;所述铝合金精炼剂加入量为原材料总质量的0.3
‑
0.5%。
27.作为优选地,步骤(3)中所述铝合金精炼剂包括c2cl6,k3alf6,caco3,k2so4,mgso4,kf,naf,cacl2;更优选地,所述铝合金精炼剂由以下质量百分比的各成分组成:c2cl
6 45.3%,k3alf
6 14.1%,caco
3 9.5%,k2so
4 15.9%,mgso
4 4.1%,kf 2.3%,naf 5.6%,cacl
2 3.2%;最优选地,所述铝合金精炼剂用量为铝合金液质量的0.3
‑
0.5%。
28.作为优选地,步骤(3)中所述喷吹精炼时间为20
‑
30分钟,所述静置时间为10
‑
20分钟。
29.所述喷吹精炼是以惰性气体为载流介质,通过喷粉机,将颗粒状的铝合金精炼剂喷入铝硅合金液中,使精炼剂与铝硅合金液充分接触反应,再将铝硅合金液中的气体和夹杂物吸附带走,达到除气除杂净化的目的。惰性气体可以是氮气或者氩气,由于氮气在高温铝硅合金液中会与铝反应生成氮化铝而影响铝硅合金液的质量,因此,优选地,惰性气体选用纯度≥99.9%的氩气。
30.由于废旧铝合金料往往夹杂大量水、油脂、油漆、有机涂层等,使得铝硅合金液的气含量和夹杂物含量都更高,导致铝硅合金液的精炼除气除杂处理变得更加困难。针对铝硅合金液气杂含量高、除气除杂困难的问题,发明人通过对铝合金精炼剂的研究发现,精炼剂的成分组成对精炼除气除杂的效果有重要影响,目前市场上出售的铝合金精炼剂主要成分组成是c2cl6、kf、naf和cacl2,并且c2cl6的含量较低,不含氟铝酸盐、碳酸盐和硫酸盐,或者含量很少,这种精炼剂的除气除杂效果较差,难以获得高洁净度的铝合金液。发明人通过大量的实验研究后发现,对现有铝合金精炼剂的成分组成进行调整,去掉部分氯盐和氟盐,增加六氯乙烷的含量,并添加氟铝酸钾、碳酸钙、硫酸钾和硫酸镁,从而提高铸造铝硅合金
的性能,原因是六氯乙烷、氟铝酸钾、碳酸钙、硫酸钾和硫酸镁能够与高温铝硅合金液反应释放更多的气泡,从而能够吸附带着更多氢离子和夹杂物,起到更好的精炼除气除杂效果。
31.发明人的研究还发现,精炼剂的使用量也不能太少,精炼时间也不能太短,否则达不到理想的精炼除气除杂效果,精炼剂的使用量也不宜太多,否则会增加生产成本,而精炼时间也不能太长,否者会引起铝硅合金液过渡氧化。本发明通过严格控制精炼剂的使用量及喷吹精炼时间,可以较为彻底除气除杂,获得纯净的铝硅合金液,消除气孔和夹杂缺陷对铸造铝硅合金性能的影响,提高铸造铝硅合金的强度和塑性。
32.作为优选地,步骤(4)中将除气除杂处理后的铝硅合金液在690
‑
710℃条件下用金属模铸造成铝硅合金。该步骤中铸造温度不宜太低,否者铝硅合金液的流动性变差,容易导致铸造不畅或者成型不完整。
33.作为优选地,步骤(5)中加热温度为495
‑
505℃,加热时间为1
‑
2小时。
34.作为优选地,步骤(5)中淬水进行固溶处理过程中,铸造铝硅合金的转移时间小于或等于5秒钟,淬水的水温为20
‑
40℃。
35.上述步骤(5)中,所述固溶处理是指将铸造铝硅合金加热到某一高温区域恒温保温,使铸造铝硅合金中硅、镁、铜等金属元素和过剩相充分溶解进入铝基体,然后通过淬水等方式快速冷却,以得到过饱和固溶体的热处理工艺。所述淬水是将加热保温后的铸造铝硅合金转移放入水中冷却的过程。本发明人通过大量实验研究后发现,将铸造铝硅合金在495
‑
505℃加热1
‑
2小时后淬水,可使金属元素和过剩相充分溶解进入铝基体,得到过饱和固溶体,有利于时效后获得理想的组织性能。为了保证淬水效果,铸造铝硅合金的转移时间最佳地小于或等于5秒钟,淬水的水温为20
‑
40℃。
36.作为优选地,步骤(6)中现将将固溶处理后的铸造铝硅合金后在160
‑
170℃加热处理,随后降温至140
‑
150℃继续加热进行时效处理。
37.上述步骤(6)中,所述时效处理是将铸造铝硅合金加热到某一温度区域恒温保温的热处理工艺,是提高铸造铝硅合金力学性能和改善理化性能的重要手段。本发明人通过大量实验研究后发现,采用双级时效工艺,即将铸造铝硅合金在160
‑
170℃加热1
‑
2小时,然后降温至140
‑
150℃继续加热2
‑
3小时,然后随炉冷却,可以得到本发明上述的高强耐磨铸造铝硅合金。
38.本发明第二方面提供了根据上述利用废铝制备高强耐磨铸造铝硅合金的方法制备得到的高强耐磨铸造铝硅合金,所述高强耐磨铸造铝硅合金由以下成分组成:si,cu,mg,ti,fe,cr,ba,ni,c,b, al和不可避免的杂质。
39.作为优选地,所述高强耐磨铸造铝硅合金由以下质量百分比的成分组成:si 12.02%
‑
14.48%,cu 1.22%
‑
2.44%,mg 0.30%
‑
0.66%,ti 0.22%
‑
0.52%,fe 0.22%
‑
0.65%,cr 0.012%
‑
0.045%,ba 0.025%
‑
0.051%,ni 0.01%
‑
0.021%,c 0.002%
‑
0.005%,b 0.01%
‑
0.021%,余量为al和不可避免的杂质,杂质单个含量≤0.05%,杂质总量≤0.15%。
40.更优选地,所述高强耐磨铸造铝硅合金由以下质量百分比的成分组成:si 12.54%
‑
14.48%,cu 1.42%
‑
2.44%,mg 0.30%
‑
0.66%,ti 0.22%
‑
0.52%,fe 0.36%
‑
0.59%,cr 0.012%
‑
0.045%,ba 0.025%
‑
0.051%,ni 0.01%
‑
0.021%,c 0.002%
‑
0.005%,b 0.01%
‑
0.021%,余量为al和不可避免的杂质,杂质单个含量≤0.05%,杂质总量≤0.15%。
41.高强耐磨铸造铝硅合金中各元素的作用说明如下:
si是铸造铝硅合金的主要合金元素,首先是si与al可形成al+si共晶液相,提高铝硅合金的铸造流动性。其次si还能与mg可形成mg2si强化相,增强铸造铝硅合金的强度。最后是,当si相呈细小均匀的颗粒状或短纤维状弥散分布在α
‑
al基体上,能大幅提高铸造铝硅合金的耐磨性能和机械加工性能。
42.cu在铸造铝硅合金中既有固溶强化作用,还能与al形成al2cu强化相,进一步增强铸造铝硅合金的强度。cu含量越高,铝硅合金的强度也越高,但cu含量太高也会引起塑性下降。
43.mg在铸造铝硅合金中既有固溶强化作用,还能与si形成mg2si强化相,增强铝硅合金的强度。
44.ti在铸造铝硅合金中主要形成tial3弥散质点相并弥散分布在铝基体上,能够阻碍再结晶晶粒的长大,细化再结晶晶粒,提高铸造铝硅合金的再结晶温度和高温力学性能的稳定性。
45.fe在铸造铝硅合金中主要作用是起到脱模作用,有利于铝合金从金属模具中分离。另外,当含fe的富铁相呈细小均匀的颗粒状α
‑
fe富铁相并弥散分布在铝基体内部,消还能起到提高铸造铝硅合金强度和耐磨性能的作用。
46.cr属于过渡族元素,cr首先可以直接固溶进铝基体,增大铝原子间的结合力,减慢铝原子的扩散过程和固溶体的分解速度,提高铸造铝硅合金的热稳定性。其次,cr还能与al形成cral3弥散强化相并分布在铝基体和晶界上,阻碍晶界、亚晶界的迁移和位错运动,增大铝基体内位错运动的阻力,阻碍高温下晶界的流变,提高铸造铝硅合金的高温稳定性。
47.ba的作用是细化变质共晶si相。si除了形成mg2si强化相外,大部分的si是以共晶si形式存在铸造铝硅合金中,当这些共晶si呈通常呈粗大针片状,会严重割裂铝基体,降低铸造铝硅合金的强度,特别是塑性和韧性。通过加入铝钡合金引入元素ba,对共晶si相具有显著的细化变质作用,可使粗大针片状共晶si转变为细小均匀的颗粒状或短纤维状并弥散分布在铝基体上,可以消除其对塑性和韧性的危害,提高铸造铝硅合金的强度、耐磨性和机械加工性能。
48.ni和c是以铝镍碳合金的形式加入到铸造铝硅合金液中,主要作用是细化晶粒,改善铸造流动性和组织均匀性,提高强度和塑性。传统的altic中间合金虽然是铝晶粒非常有效的晶粒细化剂,但在含有si、cr的铸造铝硅合金中,其晶粒细化效果会被si、cr
ꢀ“
毒化”而失去晶粒细化效果。本发明人通过大量的实验研究后发现,铝镍碳合金晶粒细化剂对si、cr的“毒化”有免疫作用,可明显细化铸造铝硅合金的晶粒组织,改善铸造流动性和组织均匀性,提高强度和塑性。
49.b的作用主要是细化变质粗大针状富铁相。由于fe在铸造铝硅合金中通常以粗大针状feal3、fesial3等粗大针状β
‑
fe富铁相形式存在于铝硅合金中,这些粗大针状β
‑
fe富铁相为硬脆相,会严重割裂铝基体,成为铸造铝硅合金断裂的裂纹源和裂纹扩展方向,危害铸造铝硅合金的强度和塑性。本发明人对这个问题进行大量实验探索研究后发现,添加元素b,在合金凝固过程中可吸附在feal3、fesial3等富铁相的生长前沿,抑制β
‑
fe富铁相的按针状生长,最终可使粗大针状β
‑
fe富铁相转变为细小均匀的颗粒状α
‑
fe富铁相,并弥散分布在铝基体内部,不仅可以消除粗大针状β
‑
fe富铁相对铸造铝硅合金强度和塑性的危害,还能提高铸造铝硅合金的耐磨性能和机械加工性。
50.本发明相对于现有技术具有如下有益效果:(1)本发明以铝合金废料为主要原材料,通过优化设计铝合金废料的组成,添加少量铝镍碳合金、铝钡合金和铝硼合金进行细化变质处理,直接再生高强耐磨的铸造铝硅合金,既没有使用纯铝,也没有额外添加硅、镁、铜等金属元素,既提高了铝合金废料的使用价值,又降低了铸造铝硅合金的生产成本,比现有技术的生产成本至少可以降低20%以上,同时还促进了铸造铝行业的节能减排和环境保护。
51.(2)本发明充分利用铝合金废料中含有的硅、镁、铜等大属元素,通过科学优化设计铝合金废料的组成,再添加少量的铝镍碳合金、铝钡合金和铝硼合金进行细化变质处理,使元素之间相互配合产生固溶强化、析出强化和弥散相强化,消除粗大针片状共晶硅相和富铁相对铸造铝硅金强度和塑性的危害,显著提高了铸造铝硅合金强度、塑性和耐磨性能。
52.(3)本发明铸造铝硅合金的室温抗拉强度大于510mpa,伸长率大于12%,磨损率小于0.17
×
10
‑6g/m,具有强度高、塑性好和耐磨性能优良的优点,可应用于铸造形状结构复杂的零部件,满足汽车、摩托车、农机具、电动工具等轻量化的发展要求。
附图说明
53.图1为实施例1铸造铝硅合金放大100倍的显微组织。
54.图2为实施例1铸造铝硅合金放大500倍的显微组织。
55.图3为对比例1铸造铝硅合金放大100倍的显微组织。
56.图4为对比例1铸造铝硅合金放大500倍的显微组织。
57.图5为对比例2铸造铝硅合金放大100倍的显微组织。
58.图6为对比例2铸造铝硅合金放大500倍的显微组织。
具体实施方式
59.为使本发明的目的、技术方案及效果更加清楚、明确,以下参照实施例对本发明作进一步详细说明。应当理解,此处所描述的具体实施例仅用以解释本发明,并不用于限定本发明。
60.实施例1一种利用废铝制备高强耐磨铸造铝硅合金的方法,包括如下步骤:(1)选择占原材料总重量75%的铝硅合金废料,15.1%的铝铜合金废料,4.3%的铝镁合金废料,2.6%的铝钛合金废料、2.5%的铝铁合金废料在770℃加热熔化成铝硅合金液,各原材料的化学成分及质量百分比如下:铝硅合金废料的化学成分及质量百分比为:si 17.02%,cu 0.52%,fe 0.37%,余量为al和不可避免的杂质,杂质单个含量≤0.05%,总量≤0.15%;铝铜合金废料的化学成分及质量百分比为:cu 9.08%,fe 0.59%,cr 0.28%,余量为al和不可避免的杂质,杂质单个含量≤0.05%,总量≤0.15%;铝镁合金废料的化学成分及质量百分比为:mg 7.02%,cu 1.76%,fe 0.53%,si 0.64%,余量为al和不可避免的杂质,杂质单个含量≤0.05%,总量≤0.15%;铝钛合金废料的化学成分及质量百分比为:ti 12.90%,cu 5.68%,mg 4.50%,余量为al和不可避免的杂质,杂质单个含量≤0.05%,总量≤0.15%;铝铁合金废料的化学成分及质量百分比为:fe 1.32%,cu 0.3%,余量为al和不可避免的杂质,杂质单个含量≤0.05%,总量≤0.15%;
(2)在铝硅合金液中加入占原材料总重量0.2%的铝镍碳合金、0.1%的铝钡合金和0.2%的铝硼合金进行细化变质处理;其中铝镍碳合金的化学成分及质量百分比为:ni 4.99%,c 1.02%,余量为al和不可避免的杂质,杂质单个含量≤0.05%,总量≤0.15%;铝钡合金的化学成分及质量百分比为:ba 24.98%,余量为al和不可避免的杂质,杂质单个含量≤0.05%,总量≤0.15%;铝硼合金的化学成分及质量百分比为:b 10.12%,余量为al和不可避免的杂质,杂质单个含量≤0.05%,总量≤0.15%;(3)用纯度99.9%的氩气和占原材料总重量0.3%%的铝合金精炼剂对铝硅合金液喷吹精炼30分钟进行除气除杂处理,扒渣后再静置10分钟,所述铝合金精炼剂由以下质量百分比成分组成:c2cl
6 45.3%,k3alf
6 14.1%,caco
3 9.5%,k2so
4 15.9%,mgso
4 4.1%,kf 2.3%,naf 5.6%,cacl
2 3.2%;(4)将除气除杂处理后的铝硅合金液在温度为690℃的条件下用金属模铸造成铝硅合金;(5)将铸造铝硅合金在500℃加热2小时后淬水进行固溶处理,铸造铝硅合金的转移时间为5秒钟,淬水的水温为30℃;(6)将固溶处理后的铸造铝硅合金后在165℃加热1.5小时,然后降温至145℃继续加热3小时进行时效处理,随炉冷却后得到高强耐磨铸造铝硅合金。
61.实施例2一种利用废铝制备高强耐磨铸造铝硅合金的方法,包括如下步骤:(1)选择占原材料总重量78%的铝硅合金废料,15%的铝铜合金废料,3%的铝镁合金废料,2%的铝钛合金废料、1.3%的铝铁合金废料在760℃加热熔化成铝硅合金液,各原材料的化学成分及质量百分比如下:铝硅合金废料的化学成分及质量百分比为:si 16.02%,cu 0.78%,fe 0.24%,余量为al和不可避免的杂质,杂质单个含量≤0.05%,总量≤0.15%;铝铜合金废料的化学成分及质量百分比为:cu 4.02%,fe 1.9%,cr 0.30%,余量为al和不可避免的杂质,杂质单个含量≤0.05%,总量≤0.15%;铝镁合金废料的化学成分及质量百分比为:mg 7.0%,cu 1.60%,fe 0.55%,si 1.26%,余量为al和不可避免的杂质,杂质单个含量≤0.05%,总量≤0.15%;铝钛合金废料的化学成分及质量百分比为:ti 11.0%,cu 5.22%,mg 4.52%,余量为al和不可避免的杂质,杂质单个含量≤0.05%,总量≤0.15%;铝铁合金废料的化学成分及质量百分比为:fe 1.35%,cu 0.32%,余量为al和不可避免的杂质,杂质单个含量≤0.05%,总量≤0.15%;(2)在铝硅合金液中加入占原材料总重量0.4%的铝镍碳合金、0.2%的铝钡合金和0.1%的铝硼合金进行细化变质处理;其中铝镍碳合金的化学成分及质量百分比为:ni 5.2%,c 1.2%,余量为al和不可避免的杂质,杂质单个含量≤0.05%,总量≤0.15%;铝钡合金的化学成分及质量百分比为:ba 25.5%,余量为al和不可避免的杂质,杂质单个含量≤0.05%,总量≤0.15%;铝硼合金的化学成分及质量百分比为:b 9.5%,余量为al和不可避免的杂质,杂质单个含量≤0.05%,总量≤0.15%;(3)用纯度99.9%的氩气和占原材料总重量0.4%的铝合金精炼剂对铝硅合金液喷吹精炼25分钟进行除气除杂处理,扒渣后再静置20分钟,所述铝合金精炼剂由以下质量百分比成分组成:c2cl
6 45.3%,k3alf
6 14.1%,caco
3 9.5%,k2so
4 15.9%,mgso
4 4.1%,kf 2.3%,naf 5.6%,cacl
2 3.2%;
(4)将除气除杂处理后的铝硅合金液在温度为700℃的条件下用金属模铸造成铝硅合金;(5)将铸造铝硅合金在505℃加热1小时后淬水进行固溶处理,铸造铝硅合金的转移时间为3秒钟,淬水的水温为20℃;(6)将固溶处理后的铸造铝硅合金后在170℃加热1小时,然后降温至150℃继续加热2.5小时进行时效处理,随炉冷却后得到高强耐磨铸造铝硅合金。
62.实施例3一种利用废铝制备高强耐磨铸造铝硅合金的方法,包括如下步骤:(1)选择占原材料总重量80%的铝硅合金废料,12%的铝铜合金废料,4%的铝镁合金废料,2%的铝钛合金废料、1.3%的铝铁合金废料在780℃加热熔化成铝硅合金液,各原材料的化学成分及质量百分比如下:铝硅合金废料的化学成分及质量百分比为:si 17.8%,cu 0.4%,fe 0.5%,余量为al和不可避免的杂质,杂质单个含量≤0.05%,总量≤0.15%;铝铜合金废料的化学成分及质量百分比为:cu 9.0%,fe 0.9%,cr 0.2%,余量为al和不可避免的杂质,杂质单个含量≤0.05%,总量≤0.15%;铝镁合金废料的化学成分及质量百分比为:mg 7.0%,cu 2.0%,fe 0.5%,si 1.4%,余量为al和不可避免的杂质,杂质单个含量≤0.05%,总量≤0.15%;铝钛合金废料的化学成分及质量百分比为:ti 13.0%,cu 6.0%,mg 4.2%,余量为al和不可避免的杂质,杂质单个含量≤0.05%,总量≤0.15%;铝铁合金废料的化学成分及质量百分比为:fe 1.5%,cu 0.1%,余量为al和不可避免的杂质,杂质单个含量≤0.05%,总量≤0.15%;(2)在铝硅合金液中加入占原材料总重量0.4%的铝镍碳合金、0.2%的铝钡合金和0.1%的铝硼合金进行细化变质处理;其中铝镍碳合金的化学成分及质量百分比为:ni 4.8%,c 1.2%,余量为al和不可避免的杂质,杂质单个含量≤0.05%,总量≤0.15%;铝钡合金的化学成分及质量百分比为:ba 24.5%,余量为al和不可避免的杂质,杂质单个含量≤0.05%,总量≤0.15%;铝硼合金的化学成分及质量百分比为:b 9.9%,余量为al和不可避免的杂质,杂质单个含量≤0.05%,总量≤0.15%;(3)用纯度99.9%的氩气和占原材料总重量0.5%的铝合金精炼剂对铝硅合金液喷吹精炼20分钟进行除气除杂处理,扒渣后再静置15分钟,所述铝合金精炼剂由以下质量百分比成分组成:c2cl
6 45.3%,k3alf
6 14.1%,caco
3 9.5%,k2so
4 15.9%,mgso
4 4.1%,kf 2.3%,naf 5.6%,cacl
2 3.2%;(4)将除气除杂处理后的铝硅合金液在温度为710℃的条件下用金属模铸造成铝硅合金;(5)将铸造铝硅合金在495℃加热1.5小时后淬水进行固溶处理,铸造铝硅合金的转移时间为4秒钟,淬水的水温为40℃;(6)将固溶处理后的铸造铝硅合金后在160℃加热2小时,然后降温至140℃继续加热2小时进行时效处理,随炉冷却后得到高强耐磨铸造铝硅合金。
63.实施例4一种利用废铝制备高强耐磨铸造铝硅合金的方法,包括如下步骤:(1)选择占原材料总重量77%的铝硅合金废料,13%的铝铜合金废料,4%的铝镁合金废料,3%的铝钛合金废料、2.4%的铝铁合金废料在770℃加热熔化成铝硅合金液,各原材料
的化学成分及质量百分比如下:铝硅合金废料的化学成分及质量百分比为:si 17.2%,cu 0.6%,fe 0.4%,余量为al和不可避免的杂质,杂质单个含量≤0.05%,总量≤0.15%;铝铜合金废料的化学成分及质量百分比为:cu 8.8%,fe 0.8%,cr 0.2%,余量为al和不可避免的杂质,杂质单个含量≤0.05%,总量≤0.15%;铝镁合金废料的化学成分及质量百分比为:mg 7.6%,cu 1.2%,fe 0.8%,si 1.0%,余量为al和不可避免的杂质,杂质单个含量≤0.05%,总量≤0.15%;铝钛合金废料的化学成分及质量百分比为:ti 12.2%,cu 5.0%,mg 4.6%,余量为al和不可避免的杂质,杂质单个含量≤0.05%,总量≤0.15%;铝铁合金废料的化学成分及质量百分比为:fe 1.3%,cu 0.2%,余量为al和不可避免的杂质,杂质单个含量≤0.05%,总量≤0.15%;;(2)在铝硅合金液中加入占原材料总重量0.3%的铝镍碳合金、0.15%的铝钡合金和0.15%的铝硼合金进行细化变质处理;其中铝镍碳合金的化学成分及质量百分比为:ni 5%,c1%,余量为al和不可避免的杂质,杂质单个含量≤0.05%,总量≤0.15%;铝钡合金的化学成分及质量百分比为:ba 25%,余量为al和不可避免的杂质,杂质单个含量≤0.05%,总量≤0.15%;铝硼合金的化学成分及质量百分比为:b 10%,余量为al和不可避免的杂质,杂质单个含量≤0.05%,总量≤0.15%;(3)用纯度99.9%的氩气和占原材料总重量0.4%的铝合金精炼剂对铝硅合金液喷吹精炼25分钟进行除气除杂处理,扒渣后再静置15分钟,所述铝合金精炼剂由以下质量百分比成分组成:c2cl
6 45.3%,k3alf
6 14.1%,caco
3 9.5%,k2so
4 15.9%,mgso
4 4.1%,kf 2.3%,naf 5.6%,cacl
2 3.2%;(4)将除气除杂处理后的铝硅合金液在温度为710℃的条件下用金属模铸造成铝硅合金;(5)将铸造铝硅合金在500℃加热1小时后淬水进行固溶处理,铸造铝硅合金的转移时间为5秒钟,淬水的水温为30℃;(6)将固溶处理后的铸造铝硅合金后在165℃加热1.5小时,然后降温至145℃继续加热2.5小时进行时效处理,随炉冷却后得到高强耐磨铸造铝硅合金。
64.实施例5一种利用废铝制备高强耐磨铸造铝硅合金的方法,包括如下步骤:(1)选择占原材料总重量80%的铝硅合金废料,12%的铝铜合金废料,4.5%的铝镁合金废料,2%的铝钛合金废料、1%的铝铁合金废料在780℃加热熔化成铝硅合金液,各原材料的化学成分及质量百分比如下:铝硅合金废料的化学成分及质量百分比为:si 18.0%,cu 0.8%,fe 0.5%,余量为al和不可避免的杂质,杂质单个含量≤0.05%,总量≤0.15%;铝铜合金废料的化学成分及质量百分比为:cu 10.0%,fe 1.0%,cr 0.10%,余量为al和不可避免的杂质,杂质单个含量≤0.05%,总量≤0.15%;铝镁合金废料的化学成分及质量百分比为:mg 7.0%,cu 2.0%,fe 1.0%,si 1.6%,余量为al和不可避免的杂质,杂质单个含量≤0.05%,总量≤0.15%;铝钛合金废料的化学成分及质量百分比为:ti 13.0%,cu 6.0%,mg 4.0%,余量为al和不可避免的杂质,杂质单个含量≤0.05%,总量≤0.15%;铝铁合金废料的化学成分及质量百分比为:fe 1.5%,cu 0.4%,余量为al和不可避免的杂质,杂质单个含量≤0.05%,总量≤0.15%;(2)在铝硅合金液中加入占原材料总重量0.2%的铝镍碳合金、0.1%的铝钡合金和
0.2%的铝硼合金进行细化变质处理;其中铝镍碳合金的化学成分及质量百分比为:ni 4.8%,c 0.8%,余量为al和不可避免的杂质,杂质单个含量≤0.05%,总量≤0.15%;铝钡合金的化学成分及质量百分比为:ba 24.5%,余量为al和不可避免的杂质,杂质单个含量≤0.05%,总量≤0.15%;铝硼合金的化学成分及质量百分比为:b 10.5%,余量为al和不可避免的杂质,杂质单个含量≤0.05%,总量≤0.15%(3)用纯度99.9%的氩气和占原材料总重量0.3%%的铝合金精炼剂对铝硅合金液喷吹精炼30分钟进行除气除杂处理,扒渣后再静置20分钟,所述铝合金精炼剂由以下质量百分比成分组成:c2cl
6 45.3%,k3alf
6 14.1%,caco
3 9.5%,k2so
4 15.9%,mgso
4 4.1%,kf 2.3%,naf 5.6%,cacl
2 3.2%;(4)将除气除杂处理后的铝硅合金液在温度为690℃的条件下用金属模铸造成铝硅合金;(5)将铸造铝硅合金在505℃加热2小时后淬水进行固溶处理,铸造铝硅合金的转移时间为4秒钟,淬水的水温为20℃;(6)将固溶处理后的铸造铝硅合金后在170℃加热1小时,然后降温至140℃继续加热2小时进行时效处理,随炉冷却后得到高强耐磨铸造铝硅合金。
65.实施例6一种利用废铝制备高强耐磨铸造铝硅合金的方法,包括如下步骤:(1)选择占原材料总重量75%的铝硅合金废料,15%的铝铜合金废料,4.6%的铝镁合金废料,4%的铝钛合金废料、1%的铝铁合金废料在760℃加热熔化成铝硅合金液,各原材料的化学成分及质量百分比如下:铝硅合金废料的化学成分及质量百分比为:si 18.0%,cu 0.8%,fe 0.5%,余量为al和不可避免的杂质,杂质单个含量≤0.05%,总量≤0.15%;铝铜合金废料的化学成分及质量百分比为:cu 10.0%,fe 1.0%,cr 0.3%,余量为al和不可避免的杂质,杂质单个含量≤0.05%,总量≤0.15%;铝镁合金废料的化学成分及质量百分比为:mg 9.0%,cu 2.0%,fe 1.0%,si 1.6%,余量为al和不可避免的杂质,杂质单个含量≤0.05%,总量≤0.15%;铝钛合金废料的化学成分及质量百分比为:ti 13.0%,cu 6.0%,mg 6.0%,余量为al和不可避免的杂质,杂质单个含量≤0.05%,总量≤0.15%;铝铁合金废料的化学成分及质量百分比为:fe 1.5%,cu 0.4%,余量为al和不可避免的杂质,杂质单个含量≤0.05%,总量≤0.15%;(2)在铝硅合金液中加入占原材料总重量0.2%的铝镍碳合金、0.1%的铝钡合金和0.1%的铝硼合金进行细化变质处理;其中铝镍碳合金的化学成分及质量百分比为:ni 5.02%,c 1.12%,余量为al和不可避免的杂质,杂质单个含量≤0.05%,总量≤0.15%;铝钡合金的化学成分及质量百分比为:ba 25.3%,余量为al和不可避免的杂质,杂质单个含量≤0.05%,总量≤0.15%;铝硼合金的化学成分及质量百分比为:b 10.1%,余量为al和不可避免的杂质,杂质单个含量≤0.05%,总量≤0.15%;(3)用纯度99.9%的氩气和占原材料总重量0.5%的铝合金精炼剂对铝硅合金液喷吹精炼20分钟进行除气除杂处理,扒渣后再静置10分钟,所述铝合金精炼剂由以下质量百分比成分组成:c2cl
6 45.3%,k3alf
6 14.1%,caco
3 9.5%,k2so
4 15.9%,mgso
4 4.1%,kf 2.3%,naf 5.6%,cacl
2 3.2%;(4)将除气除杂处理后的铝硅合金液在温度为700℃的条件下用金属模铸造成铝
0.78%,fe 0.24%,余量为al和不可避免的杂质,杂质单个含量≤0.05%,总量≤0.15%;铝铜合金废料的化学成分及质量百分比为:cu 4.02%,fe 1.9%,cr 0.30%,余量为al和不可避免的杂质,杂质单个含量≤0.05%,总量≤0.15%;铝镁合金废料的化学成分及质量百分比为:mg 7.0%,cu 1.60%,fe 0.55%,si 1.26%,余量为al和不可避免的杂质,杂质单个含量≤0.05%,总量≤0.15%;铝钛合金废料的化学成分及质量百分比为:ti 11.0%,cu 5.22%,mg 4.52%,余量为al和不可避免的杂质,杂质单个含量≤0.05%,总量≤0.15%;铝铁合金废料的化学成分及质量百分比为:fe 1.35%,cu 0.32%,余量为al和不可避免的杂质,杂质单个含量≤0.05%,总量≤0.15%;(2)在铝硅合金液中加入占原材料总重量0.4%的铝镍碳合金进行细化变质处理;其中铝镍碳合金的化学成分及质量百分比为:ni 5.2%,c 1.2%,余量为al和不可避免的杂质,杂质单个含量≤0.05%,总量≤0.15%;铝钡合金的化学成分及质量百分比为:ba 25.5%,余量为al和不可避免的杂质,杂质单个含量≤0.05%,总量≤0.15%;铝硼合金的化学成分及质量百分比为:b 9.5%,余量为al和不可避免的杂质,杂质单个含量≤0.05%,总量≤0.15%;(3)用纯度99.9%的氩气和占原材料总重量0.4%的铝合金精炼剂对铝硅合金液喷吹精炼25分钟进行除气除杂处理,扒渣后再静置20分钟,所述铝合金精炼剂由以下质量百分比成分组成:c2cl
6 45.3%,k3alf
6 14.1%,caco
3 9.5%,k2so
4 15.9%,mgso
4 4.1%,kf 2.3%,naf 5.6%,cacl
2 3.2%;(4)将除气除杂处理后的铝硅合金液在温度为700℃的条件下用金属模铸造成铝硅合金;(5)将铸造铝硅合金在505℃加热1小时后淬水进行固溶处理,铸造铝硅合金的转移时间为3秒钟,淬水的水温为20℃;(6)将固溶处理后的铸造铝硅合金后在170℃加热1小时,然后降温至150℃继续加热2.5小时进行时效处理,随炉冷却后得到铸造铝硅合金。
68.对比例3一种铸造铝硅合金的废铝再生方法,包括如下步骤:(1)选择占原材料总重量80%的铝硅合金废料,12%的铝铜合金废料,4%的铝镁合金废料,2%的铝钛合金废料、1.3%的铝铁合金废料在780℃加热熔化成铝硅合金液,各原材料的化学成分及质量百分比如下:铝硅合金废料的化学成分及质量百分比为:si 17.8%,cu 0.4%,fe 0.5%,余量为al和不可避免的杂质,杂质单个含量≤0.05%,总量≤0.15%;铝铜合金废料的化学成分及质量百分比为:cu 9.0%,fe 0.9%,cr 0.2%,余量为al和不可避免的杂质,杂质单个含量≤0.05%,总量≤0.15%;铝镁合金废料的化学成分及质量百分比为:mg 7.0%,cu 2.0%,fe 0.5%,si 1.4%,余量为al和不可避免的杂质,杂质单个含量≤0.05%,总量≤0.15%;铝钛合金废料的化学成分及质量百分比为:ti 13.0%,cu 6.0%,mg 4.2%,余量为al和不可避免的杂质,杂质单个含量≤0.05%,总量≤0.15%;铝铁合金废料的化学成分及质量百分比为:fe 1.5%,cu 0.1%,余量为al和不可避免的杂质,杂质单个含量≤0.05%,总量≤0.15%;(2)在铝硅合金液中加入占原材料总重量0.4%的铝镍碳合金、0.2%的铝钡合金和0.1%的铝硼合金进行细化变质处理;其中铝镍碳合金的化学成分及质量百分比为:ni 4.8%,c 1.2%,余量为al和不可避免的杂质,杂质单个含量≤0.05%,总量≤0.15%;铝钡合金
的化学成分及质量百分比为:ba 24.5%,余量为al和不可避免的杂质,杂质单个含量≤0.05%,总量≤0.15%;铝硼合金的化学成分及质量百分比为:b 9.9%,余量为al和不可避免的杂质,杂质单个含量≤0.05%,总量≤0.15%;(3)用纯度99.9%的氩气和占原材料总重量0.5%的市售铝合金精炼剂对铝硅合金液喷吹精炼20分钟进行除气除杂处理,扒渣后再静置15分钟;(4)将除气除杂处理后的铝硅合金液在温度为710℃的条件下用金属模铸造成铝硅合金;(5)将铸造铝硅合金在495℃加热1.5小时后淬水进行固溶处理,铸造铝硅合金的转移时间为4秒钟,淬水的水温为40℃;(6)将固溶处理后的铸造铝硅合金后在160℃加热2小时,然后降温至140℃继续加热2小时进行时效处理,随炉冷却后得到铸造铝硅合金。
69.验证例1在实施例1
‑
6和对比例1
‑
3制备的铸造铝硅合金上分别取样,并在arl
‑
4600型光电直读光谱仪上进行化学成分分析,分析结果如表1所示。
70.表1实施例和对比例铸造铝硅合金的化学成分组成(质量百分比,%) sicumgtifecrbanicb实施例112.802.000.420.340.420.0420.0250.0100.0020.020实施例212.541.980.300.220.360.0450.0510.0210.0050.010实施例314.301.420.360.260.550.0240.0490.0190.0050.010实施例413.281.800.440.360.480.0250.0480.0150.0030.015实施例514.482.060.400.260.580.0120.0380.0100.0020.021实施例613.582.440.660.520.590.0450.0250.0100.0020.010对比例112.802.000.420.340.420.0420.025
‑‑
0.020对比例212.541.980.300.220.360.045
‑
0.0210.005
‑
对比例314.301.420.360.260.550.0240.0490.0190.0050.010验证例2在实施例1、对比例1和对比例2的铸造铝硅合金上分别取样,试样经磨制、抛光和腐蚀后,在leik
‑
dmi3000m型光学显微镜上进行组织观察,图1和图2分别为实施例1铸造铝硅合金放大100倍和放大500倍的显微组织。图3和图4分别为对比例1铸造铝硅合金放大100倍和放大500倍的显微组织。图5和图6分别为对比例2铸造铝硅合金放大100倍和放大500倍的显微组织。
71.从图1和图2可看到,实施例1铸造铝硅合金由于添加了铝镍碳合金、铝钡合金和铝硼合金进行细化变质处理,铸造铝硅合金的显微组织未见有粗大的树枝状α
‑
al晶粒和粗大的针片状共晶si相和富铁相。从图3和图4可看到,对比例1铸造铝硅合金由于没有添加铝镍碳合金进行细化处理,铸造铝硅合金的α
‑
al晶粒仍然呈粗大的树枝状。从图5和图6可看到,对比例2铸造铝硅合金由于没有添加铝钡合金和铝硼合金进行细化变质处理,共晶si相和富铁相仍然呈粗大的针片状。通过比较可看到,本发明通过添加铝镍碳合金、铝钡合金和铝硼合金进行细化变质处理,可以消除粗大的树枝状α
‑
al晶粒和粗大的针片状共晶si相和富铁相。
72.验证例3按照标准gc/t 228
‑
1987,分别在实施例1
‑
6和对比例1
‑
3制备的铸造铝硅合金上分别取样并加工成标准拉伸试样,在hwg
‑
1000型电子拉伸试验机上进行室温拉伸,拉伸速率为2毫米/分钟,结果如表2所示。在dnm
‑
350型摩擦磨损试验机上检测铸造铝硅合金的磨损率,载荷为8.9n,结果如表2所示。
73.表2实施例和对比例铸造铝硅合金的拉伸力学性能和磨损率 抗拉强度/mpa伸长率/%磨损率/
×
10
‑6g/m实施例1519.513.40.155实施例2531.812.90.151实施例3542.212.40.147实施例4513.913.60.163实施例5524.112.50.161实施例6552.812.20.134对比例1461.88.60.204对比例2426.37.50.251对比例3472.610.40.214从表2可以看到,本发明实施例制备的铸造铝硅合金的室温抗拉强度大于510mpa,伸长率大于12%,磨损率小于0.17
×
10
‑6g/m,具有高强度、良好的塑性和优异的耐磨性能。对比例1的铸造铝硅合金由于没有添加铝镍碳合金进行细化处理,对比例2的铸造铝硅合金由于没有添加铝钡合金和铝硼合金进行变质处理,对比例3的铸造铝硅合金由于没有添加本发明所述铝合金精炼剂进行除气除杂处理,使得对比例1
‑
3铸造铝硅合金的强度和塑性都明显低于本发明实施例1
‑
6铸造铝硅合金的强度和塑性,而对比例1
‑
3铸造铝硅合金的磨损率则明显高于本发明实施例1
‑
6铸造铝硅合金的磨损率。通过比较可以看到,本发明通过添加铝镍碳合金、铝钡合金和铝硼合金进行细化变质处理和精炼除气除杂处理,可显著提高铸造铝硅合金的强度、塑性和耐磨性能。
74.以上具体实施方式部分对本发明所涉及的分析方法进行了具体的介绍。应当注意的是,上述介绍仅是为了帮助本领域技术人员更好地理解本发明的方法及思路,而不是对相关内容的限制。在不脱离本发明原理的情况下,本领域技术人员还可以对本发明进行适当的调整或修改,上述调整和修改也应当属于本发明的保护范围。