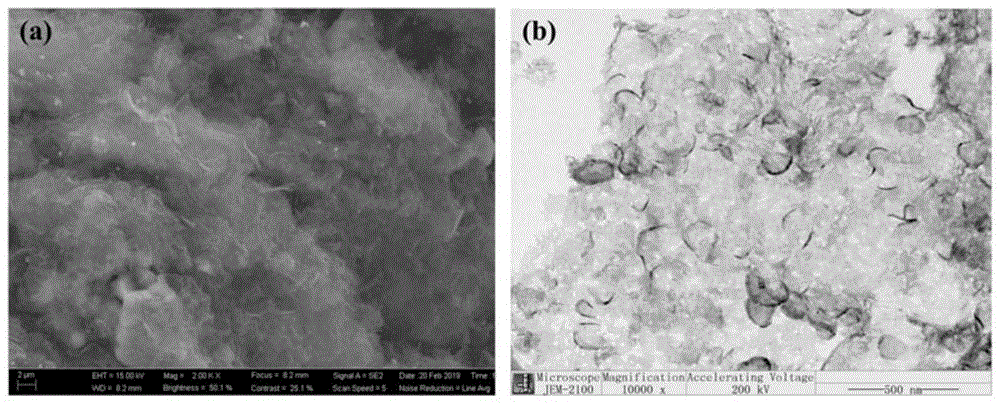
本发明涉及镁基复合材料制备
技术领域:
,具体涉及一种石墨烯增强镁基复合材料及其制备方法。
背景技术:
:镁是最轻量的金属结构材料,其密度比铝轻35%,比钛轻65%。但是镁合金的低刚度、低强度、高热膨胀系数等缺点极大地限制了它的应用范围。镁基复合材料通过在基体镁合金中添加合适的增强体,克服了或显著减轻镁合金的上述缺点,具有低密度、高比强度、高比刚度、耐高温性能好、兼具良好的阻尼性能和电磁屏蔽性,轻量化效果十分显著,是目前国防和航天等尖端领域的理想材料之一。石墨烯(graphene)是人类在自然界发现的第一种二维材料,具有优异的力学、热学、电学等方面的奇特性能,被认为是金属,陶瓷,树脂等材料的理想增强体。同时,石墨烯与镁在高温下不发生化学反应,具备较好的化学相容性。因此将镁和石墨烯进行复合可以制备出轻质高性能的镁基复合材料。然而,由于石墨烯和镁合金的润湿性差,且其纳米级的尺寸也使得石墨烯之间产生强大的范德华力而极易团聚,这都使得复合材料中石墨烯的增强效果不能完全的发挥。本团队前期的中国专利申请cn109207787a提出了利用co2与镁基体的原位反应制备出了原位自生石墨烯增强镁基复合材料,该石墨烯增强镁基复合材料中石墨烯获得了较好的分散性,其力学性能得到了明显的提升,但是该专利申请在原位反应过程中生成的较高含量的氧化镁严重的抑制了石墨烯在镁基体中的含量。为了进一步提升复合材料的机械性能必须进一步增加石墨烯的含量,同时减少氧化镁的含量(石墨烯的增强/韧效率远高于氧化镁)。另外,由于石墨烯与镁的润湿角较大(120°),石墨烯与镁的界面结合也决定着制备的复合材料的质量;因此也必须进一步优化石墨烯增强镁基复合材料的界面结合能力,以提高镁基复合材料的力学性能。综上,非常有必要提供一种新的石墨烯增强镁基复合材料及其制备方法。技术实现要素:为了解决现有技术中存在石墨烯在镁基体中容易产生团聚,镁基体中石墨烯的含量难以获得高体积分数,同时界面结合较差的技术问题,本发明提供了一种石墨烯增强镁基复合材料及其制备方法。本发明方法成本低廉可行,操作简单,操作安全系数高,本发明制备的石墨烯增强镁基复合材料是一种石墨烯高分散、氧化镁含量低,石墨烯含量高、界面结合强度高、力学性能优异的轻质高性能镁基复合材料。本发明在第一方面提供了一种石墨烯增强镁基复合材料的制备方法,所述方法包括如下步骤:(1)将镁基体在坩埚中加热熔化,得到镁基体熔体;在所述坩埚的顶部引入空气或由氧气与稀有气体混合而成的混合气体,使所述坩埚的顶部与流动的空气或流动的所述混合气体直接接触,所述混合气体中氧气的体积百分含量为10~30%;所述镁基体为镁锌合金、镁钙合金、镁铜合金、镁锌钙合金、镁锌锆合金中的一种或多种;(2)将一氧化碳气体持续通入所述镁基体熔体中进行气液原位反应,得到石墨烯增强合金熔体;在所述一氧化碳气体与所述镁基体熔体发生气液原位反应的同时,保证所述坩埚的顶部的温度为300℃以上,并在所述坩埚的顶部引燃逸出的未参与反应的一氧化碳气体;(3)将所述石墨烯增强合金熔体凝固,得到石墨烯增强镁基复合材料。优选地,在进行步骤(3)之前,还包括往步骤(2)得到的石墨烯增强合金熔体中通入高能超声波进行超声的步骤。优选地,所述高能超声波的超声功率为500~1000w,频率为20hz,往所述石墨烯增强合金熔体中通入高能超声波进行超声的时间为5~60min。优选地,在进行步骤(3)之后,还包括将得到的石墨烯增强镁基复合材料进行热变形以得到变形态的石墨烯增强镁基复合材料的步骤。优选地,所述热变形采用挤压热变形工艺、等通道径角挤压热变形工艺或轧制热变形工艺进行。优选地,所述热变形采用挤压热变形工艺进行;所述挤压热变形工艺的挤压温度为300~400℃,挤压比不小于10:1。优选地,在步骤(1)中,所述镁基体熔体的体积占所述坩埚的体积的0.25~0.75;和/或在步骤(1)中,所述加热的温度高于所述镁基体的熔点40~100℃。优选地,在步骤(2)中,通入所述一氧化碳气体的流量为0.1~2l/min;和/或在步骤(2)中,所述气液原位反应的温度为580~750℃,所述气液原位反应的时间为5~100min,所述气液原位反应的搅拌速度为100~3000r/min。优选地,在步骤(3)中,采用水冷的方式使所述石墨烯增强合金熔体凝固;或在50~100mpa压力下使所述石墨烯增强合金熔体凝固。本发明在第二方面提供了由本发明在第一方面所述的制备方法制得的石墨烯增强镁基复合材料。本发明与现有技术相比至少具有如下有益效果:(1)本发明通过采用一氧化碳作为碳源气体原位自生产生的石墨烯作为增强体,能够获得高强度高刚度同时保持较高的塑形的镁基结构材料,在军事,航天等轻量化领域有较高的价值。由于原位反应的石墨烯是一片一片的生成的,同时在原位反应过程中伴随着机械搅拌,因此石墨烯可以很好地分散在镁基体合金中;利用co作为碳源气体与镁基体反应,相较于co2碳源,一个明显的优势就是,co分子比co2分子少一个氧原子,在制备出的石墨烯增强镁基复合材料中生成的氧化镁摩尔分数理论上将减少50%,即相较于co2气体,co气体与镁气液原位反应过程中氧化镁的生成量减半,在保证界面强结合的的同时,能够进一步的提升石墨烯的含量。在本发明中,由于一氧化碳是一种有毒气体,过量吸入后会因缺氧而窒息死亡,因此将co气体作为原位反应的碳源时技术要求更高。由于在气液反应过程中co气体不能完全彻底反应会存在逸出的问题,本发明在所述坩埚的顶部引入流动的空气或由氧气与稀有气体混合而成的混合气体并在所述坩埚的顶部引燃在镁基体熔体表面逸出的未反应的co气体,如此不但避免了一氧化碳泄露而导致实验危险发生的问题,有效保证了实验安全之外,而且在镁基体熔体表面燃烧一氧化碳还进一步阻止了镁基体熔体表面被外界氧化,实现了镁基复合材料制备过程中避免氧化的自保护机制,进一步减少了所述石墨烯增强镁基复合材料中氧化镁的含量,氧化镁的含量减少,相应的石墨烯增强镁基复合材料中石墨烯的相对含量就将进一步增加,在镁基复合材料的制备过程中,石墨烯的增强/韧效率远高于氧化镁;因此本发明通过合理的调控气液反应的制备工艺,能够获得高体积分数石墨烯高分散性、界面结合强度高的轻质高性能的石墨烯增强镁基复合材料。(2)本发明能够解决现有技术中石墨烯在镁基体中容易产生团聚,镁基体中石墨烯的含量难以获得高体积分数,同时界面结合较差的问题;本发明方法成本低廉可行,操作简单,操作安全系数高,本发明制备的石墨烯增强镁基复合材料是一种石墨烯高分散、氧化镁含量低,石墨烯含量高、界面结合强度高、力学性能优异的轻质高性能镁基复合材料。附图说明图1是本发明实施例1制备的铸态石墨烯增强镁基复合材料在利用稀硫酸萃取出石墨烯增强镁基复合材料中的石墨烯粉后对石墨烯粉拍摄的扫描电子显微镜照片(sem图)和透射电子显微镜照片(tem图)。图中(a)为sem图,(b)为tem图。图2是本发明实施例1制备的铸态石墨烯增强镁基复合材料利用稀硫酸萃取出石墨烯增强镁基复合材料中的石墨烯粉的xrd图和拉曼光谱图。图中(a)为xrd图,(b)为拉曼光谱图。图3是本发明实施例2制备的铸态石墨烯增强镁基复合材料的底部沉降区sem图。图4是本发明实施例3中制备的铸态石墨烯增强镁基复合材料和挤压态石墨烯增强镁基复合材料的sem图。图中(a)为铸态石墨烯增强镁基复合材料的sem图(未腐蚀的原始形貌图,(b)为挤压态石墨烯增强镁基复合材料的sem图(未腐蚀的原始形貌图)。图5是本发明实施例3中制备的挤压态石墨烯增强镁基复合材料经过腐蚀后显示的晶粒尺寸图像。图6是本发明实施例3中制备的挤压态石墨烯增强镁基复合材料的界面结构示意图。图7是本发明实施例4制备的变形态石墨烯增强镁基复合材料的sem图。图8本发明实施例5制备的挤压态石墨烯增强镁基复合材料与采用的镁基体的拉伸试验的力学性能对比图。图中,横坐标strain为延伸率,单位%;纵坐标stress为屈服强度,单位mpa。具体实施方式为使本发明的目的、技术方案和优点更加清楚,下面将结合本发明实施例,对本发明的技术方案进行清楚、完整地描述。显然,所描述的实施例是本发明的一部分实施例,而不是全部的实施例。基于本发明中的实施例,本领域普通技术人员在没有做出创造性劳动的前提下所获得的所有其他实施例,都属于本发明保护的范围。本发明在第一方面提供了一种石墨烯增强镁基复合材料的制备方法,所述方法包括如下步骤:(1)将镁基体在坩埚中加热熔化,得到镁基体熔体;在所述坩埚的顶部引入空气或由氧气与稀有气体混合而成的混合气体,在本发明中,例如利用曝气器在将一定流量的空气或由氧气与稀有气体(例如氩气)混合而成的混合气体引入所述坩埚的顶部,使得所述坩埚的顶部与流动的空气或流动的所述混合气体直接接触,所述混合气体中氧气的体积百分含量为10~30%(例如10%、15%、20%、25%或30%),所述混合气体例如由氧气和氩气混合而成,氧气与氩气的体积比为1:4;所述镁基体为镁锌合金、镁钙合金、镁铜合金、镁锌钙合金、镁锌锆合金中的一种或多种;在本发明中,所述镁锌合金例如为锌的质量百分含量为6wt.%、镁的质量百分含量为94wt.%的镁锌合金mg-6zn;所述镁锌钙合金例如为锌的质量百分含量为4wt.%、钙的质量百分含量为0.5wt.%、镁的质量百分含量为95.5wt.%的镁锌钙合金mg-4zn-0.5ca;所述镁锌锆合金例如为锌的质量百分含量为4wt.%、锆的质量百分含量为0.5wt.%、镁的质量百分含量为95.5wt.%的镁锌锆合金mg-4zn-0.5zr,如zk60镁合金。(2)将一氧化碳(co)气体持续通入所述镁基体熔体中进行气液原位反应,得到石墨烯增强合金熔体;在所述一氧化碳气体与所述镁基体熔体发生气液原位反应的同时,保证所述坩埚的顶部的温度为300℃以上;具体地,在本发明中,保证利用加热坩埚的温度通过热传导和热辐射而促使坩埚顶部的温度在300℃以上(此温度达到了一氧化碳的燃点);在本发明中,优选的是,在步骤(1)中,所述镁基体熔体的体积占所述坩埚的体积的0.25~0.75,由于坩埚中并未完全充满镁熔体,同时坩埚上方引入的空气或由氧气与稀有气体(例如氩气)混合而成的混合气体将抑制一氧化碳泄漏到操作环境中的可能,在坩埚中剩余的体积能够积聚一氧化碳,当一氧化碳浓度达到一定时将会被坩埚顶部残留的300℃以上的余温引燃,如此可以有效避免镁基体熔体被表面的氧气氧化,同时阻止有毒气体co的泄漏;在本发明中,利用所述坩埚顶部的300℃以上的余温即可将逸出的未参与反应的一氧化碳气体引燃;在本发明中,具体地,例如调整镁基体熔体的温度为580~750℃,将流速为0.1~2l/min的co气体持续通入镁熔体中并伴随着机械搅拌,搅拌速度为100~3000r/min;保证所述坩埚顶部的温度在300℃以上,在co气体和镁基体熔体发生反应的同时,将镁基体熔体表面逸出的co气体与坩埚顶部的氧气引燃,生成蓝色的可持续燃烧的火焰;避免镁基体熔体被表面的氧气氧化,同时阻止有毒气体泄漏。(3)将所述石墨烯增强合金熔体凝固,得到石墨烯增强镁基复合材料(也记作一氧化碳原位自生石墨烯增强镁基复合材料)。本发明在所述石墨烯增强镁基复合材料的制备过程中利用co作为碳源气体与镁基体反应生成石墨烯增强镁基复合材料,相较co2碳源,一个明显的优势就是,co分子比co2分子少一个氧原子,在制备出的石墨烯增强镁基复合材料中生成的氧化镁摩尔分数理论上将减少50%,解决了现有技术中利用co2气体作为碳源时原位反应过程中因生成氧化镁含量过高导致石墨烯体积分数受限,同时镁基体熔体表面容易氧化的问题。然而现有技术中却未见有采用co气体作为碳源与镁基体进行气液原位反应,以有效控制原位反应中氧化镁的含量的相关报道。这可能的原因是,由于co是一种有毒气体,过量吸入后会因缺氧而窒息死亡,特别是当工业化生产石墨烯增强镁基复合材料时,co的用量极大,未参与反应的co极易泄露,存在很大的操作安全隐患,因此将co气体作为原位反应的碳源时对技术要求很高;而恰恰是,co的毒性以及其存在的巨大操作安全隐患,引导人们不去考虑这方面的可能性。而本发明通过合理的气液反应的制备工艺,即在所述坩埚的顶部引入空气或由氧气与稀有气体混合而成的混合气体并在所述坩埚的顶部引燃在镁基体熔体表面逸出的未反应的co气体,如此不但避免了一氧化碳泄露而导致实验危险发生的问题,有效保证了实验安全之外,而且在镁基体熔体表面燃烧一氧化碳还进一步阻止了镁基体熔体表面被外界氧化,进一步减少了所述石墨烯增强镁基复合材料中氧化镁的含量,实现了镁基复合材料制备过程中避免氧化的自保护机制,进一步减少了所述石墨烯增强镁基复合材料中氧化镁的含量,氧化镁的含量减少,相应的石墨烯增强镁基复合材料中石墨烯的相对含量就将进一步增加,在镁基复合材料的制备过程中,石墨烯的增强/韧效率远高于氧化镁;因此本发明通过合理的气液反应的制备工艺,能够获得高体积分数石墨烯高分散性、界面结合强度高的轻质高性能的石墨烯增强镁基复合材料。本发明能够解决现有技术中石墨烯在镁基体中容易产生团聚,镁基体中石墨烯的含量难以获得高体积分数,同时界面结合较差的问题;本发明方法成本低廉可行,操作简单,操作安全系数高,本发明制备的石墨烯增强镁基复合材料是一种石墨烯高分散、氧化镁含量低,石墨烯含量高、界面结合强度高、力学性能优异的轻质高性能镁基复合材料。根据一些优选的实施方式,在进行步骤(3)之前,还包括往步骤(2)得到的石墨烯增强合金熔体中通入高能超声波进行超声的步骤;在本发明中,优选为在co与镁基体反应完毕后,向所述石墨烯增强合金熔体中通入高能超声波以消除所述石墨烯增强合金熔体中的残余的极少量稀有或空气中的氮气等气体,同时将一些团絮状夹杂沉淀消除,并起到促进石墨烯分散的作用。根据一些优选的实施方式,所述高能超声波的超声功率为500~1000w(例如500、600、700、800、900或1000w),频率为20hz,往所述石墨烯增强合金熔体中通入高能超声波进行超声的时间为5~60min(例如5、10、15、20、25、30、35、40、45、50、55或60min);在本发明中,在通入高能超声波进行超声时,优选为控制所述石墨烯增强合金熔体的温度为700~750℃。根据一些优选的实施方式,在进行步骤(3)之后,还包括将得到的石墨烯增强镁基复合材料进行热变形以得到变形态的石墨烯增强镁基复合材料的步骤;在本发明中,优选为将步骤(3)制备的石墨烯增强镁基复合材料进行热变形进一步消除孔洞及改善界面结合,制备出变形态的石墨烯增强镁基复合材料。根据一些优选的实施方式,所述热变形采用挤压热变形工艺、等通道径角挤压热变形工艺(例如16道次等通道径角挤压热变形工艺)或轧制热变形工艺进行。根据一些优选的实施方式,所述热变形采用挤压热变形工艺进行,得到挤压态石墨烯增强镁基复合材料;所述挤压热变形工艺的挤压温度为300~400℃(例如300℃、350℃或400℃),挤压比不小于10:1例如10:1、15:1、20:1、25:1、30:1等优选为挤压比不小于20:1。根据一些优选的实施方式,在进行所述热变形之前,还包括将步骤(3)得到的石墨烯增强镁基复合材料进行固溶处理的步骤,以调整所述石墨烯增强镁基复合材料的组织的均匀性;在本发明中,固溶处理是将凝固过程中产生的第二相,在一定温度一定时间下将第二相通过热扩散的方式回溶到镁基体中;这能够有效的调控挤压过程中的析出行为;所述固溶处理的温度为350~400℃(例如350℃或400℃),固溶处理的时间为12~48h(例如12、16、20、24、28、32、36、40、44或48h)。根据一些优选的实施方式,在步骤(1)中,所述镁基体熔体的体积占所述坩埚的体积的0.25~0.75(例如1/4、1/3、1/2或3/4);在本发明中,为了避免未参与反应的co气体直接泄漏,保证操作的安全性,将镁基体熔体在坩埚中加热熔化,控制镁基体熔体熔化后的体积占坩埚的体积的1/4-3/4范围内,是本发明重要的工艺手段之一,如此使得所述坩埚的顶部预留有一定的空间能够积聚气液原位反应过程中从镁基体熔体表面逸出的co气体,有效避免co在来不及燃烧之前直接泄露的问题。根据一些优选的实施方式,在步骤(1)中,所述加热的温度高于所述镁基体的熔点40~100℃(例如40℃、50℃、60℃、70℃、80℃、90℃或100℃);在本发明中,具体地,所述加热的温度例如可以为660~800℃(例如660℃、680℃、700℃、720℃、750℃、780℃或800℃)。根据一些优选的实施方式,在步骤(2)中,通入所述一氧化碳气体的流量为0.1~2l/min(例如0.1、0.5、0.8、1、1.2、1.5、1.8或2l/min);和/或在步骤(2)中,所述气液原位反应的温度为580~750℃(例如580℃、600℃、620℃、650℃、680℃、700℃、720℃或750℃),所述气液原位反应的时间为5~100min(例如5、10、15、20、25、30、35、40、45、50、55、60、65、70、75、80、85、90、95或100min),所述气液原位反应的搅拌速度为100~3000r/min(例如100、500、800、1000、1500、2000、2500或3000r/min)优选为500~1500r/min(500、600、700、800、900、1000、1100、1200、1300、1400或1500r/min);在本发明中,通过控制反应时间可以调整石墨烯增强合金熔体中石墨烯的质量百分含量。根据一些优选的实施方式,在步骤(3)中,采用水冷的方式使所述石墨烯增强合金熔体凝固,在本发明中,所述水冷的方式例如为将含有石墨烯增强合金熔体的坩埚以10~400mm/min的速度放入水中进行水冷凝固;或在50~100mpa压力下使所述石墨烯增强合金熔体凝固。根据一些具体的实施方式,所述石墨烯增强镁基复合材料的制备包括如下步骤:一、将镁基体在720℃坩埚中加热熔化,得镁基体熔体;其中,镁基体熔体熔化后的体积占坩埚体积的1/2,使得所述坩埚的顶部能够积聚后续气液原位反应从镁基体熔体表面逸出的co气体,坩埚顶部与流动的空气直接接触(在空气环境下暴露);二、调整镁基体熔体的温度至680℃,将co气体以流速为0.5l/min通入到镁基体熔体中进行气液原位反应,并伴随着机械搅拌,搅拌速度为800r/min,得到石墨烯增强合金熔体,最后控制石墨烯的生成量为所述石墨烯增强合金熔体的质量分数为1%;在co气体和镁基体熔体发生气液原位反应的同时,保证坩埚顶部的温度在300℃以上,将镁基体熔体表面逸出的co气体与坩埚顶部的流动空气中含有的氧气接触引燃,生成蓝色燃烧的火焰;三、向步骤二反应得到的石墨烯增强合金熔体中通入高能超声波进行超声;四、将高能超声波超声后的石墨烯增强合金熔体在压力下凝固,得到铸态石墨烯增强镁基复合材料;五、对步骤四得到的铸态石墨烯增强镁基复合材料进行固溶处理后进行挤压热变形(热挤压),挤压温度为300℃,挤压比不小于10:1,制得挤压态石墨烯增强镁基复合材料。本发明在第二方面提供了由本发明在第一方面所述的制备方法制得的石墨烯增强镁基复合材料。下文将通过举例的方式对本发明进行进一步的说明,但是本发明的保护范围不限于这些实施例。实施例1本实施例的石墨烯增强镁基复合材料的制备方法如下:一、将700gmg-6zn合金(镁基体)在720℃坩埚中加热熔化,得镁基体熔体;其中,镁基体熔体熔化后的体积占坩埚体积的3/5,在坩埚的顶部引入空气,使坩埚顶部与流动的空气直接接触;二、调整镁基体熔体的温度至680℃,将co气体以流速为2l/min持续通入到镁基体熔体中40min进行气液原位反应,并伴随着机械搅拌,搅拌速度为600r/min,得到石墨烯含量占比为0.6wt.%的石墨烯增强合金熔体;在co气体和镁基体熔体发生气液原位反应的同时,保证坩埚顶部的温度在300℃以上,将镁基体熔体表面逸出的co气体与坩埚顶部的流动空气中含有的氧气接触引燃,生成蓝色燃烧的火焰;三、将步骤二得到的石墨烯增强合金熔体在50mpa压力下凝固,得到铸态石墨烯增强镁基复合材料;四、对步骤三得到的铸态石墨烯增强镁基复合材料进行固溶处理,固溶工艺为:固溶温度:340℃,固溶时间24h。固溶完成后在挤压温度为300℃,挤压比为20:1的条件下进行热挤压,制得挤压态石墨烯增强镁基复合材料。本实施例制备出的铸态石墨烯增强镁基复合材料利用稀硫酸萃取出石墨烯增强镁基复合材料中的石墨烯粉;石墨烯粉的扫描电子显微镜(sem)照片如图1(a)所示,由图1(a)可以得出石墨烯粉有明显的薄层结构;为了进一步观察石墨烯粉的形貌,对其进行了透射电子显微镜(tem)照片观察,如图1(b)所示,可以发现石墨烯展现出了明显的二维结构,在其表面存在着大量的褶皱和卷曲。本实施例制备的铸态石墨烯增强镁基复合材料利用稀硫酸萃取出石墨烯增强镁基复合材料中的石墨烯粉的xrd图和拉曼光谱图如图2所示;如图2(a)所示,通过xrd测试,得到的石墨烯粉能够观察出石墨烯002面产生的特征峰,图2(b)所示通过拉曼光谱分析,展现出明显的石墨烯d峰、g峰、2d峰,上述结果说明利用一氧化碳能够成功与镁基体气液原位反应,能够成功制备出石墨烯。实施例2本实施例的石墨烯增强镁基复合材料的制备方法如下:一、将700gmg-4zn-0.5ca合金在720℃坩埚中加热熔化,得镁基体熔体;其中,镁基体熔体熔化后的体积占坩埚体积的1/2,在坩埚的顶部引入空气,使坩埚顶部与流动的空气直接接触;二、调整镁基体熔体的温度至680℃,将co气体以流速为2l/min持续通入到镁基体熔体中40min进行气液原位反应,并伴随着机械搅拌,搅拌速度为600r/min,得到石墨烯含量占比为0.6wt.%的石墨烯增强合金熔体;在co气体和镁基体熔体发生气液原位反应的同时,保证坩埚顶部的温度在300℃以上,将镁基体熔体表面逸出的co气体与坩埚顶部的流动空气中含有的氧气接触引燃,生成蓝色燃烧的火焰;三、将步骤二反应得到的石墨烯增强合金熔体的温度升至700℃,然后往其中通入高能超声波进行超声20min;高能超声波的通入功率为500w,频率为20hz;四、将高能超声波超声后的石墨烯增强合金熔体在50mpa压力下凝固,得到铸态石墨烯增强镁基复合材料;五、对步骤四得到的铸态石墨烯增强镁基复合材料在挤压温度为300℃,挤压比为20:1的条件下进行热挤压,制得挤压态石墨烯增强镁基复合材料。本实施例制备出的铸态石墨烯增强镁基复合材料由于进行超声处理,其夹杂和气孔明显减少,如图3所示;团絮状的氧化夹杂在超声的作用下已经沉入坩埚底部,这对复合材料的性能提升有显著作用。实施例3本实施例的石墨烯增强镁基复合材料的制备方法如下:一、将700gmg-4zn-0.5ca合金在720℃坩埚中加热熔化,得镁基体熔体;其中,镁基体熔体熔化后的体积占坩埚体积的1/2,在坩埚的顶部引入空气,使坩埚顶部与流动的空气直接接触;二、调整镁基体熔体的温度至680℃,将co气体以流速为2l/min持续通入到镁基体熔体中40min进行气液原位反应,并伴随着机械搅拌,搅拌速度为800r/min,得到石墨烯含量占比为0.6wt.%的石墨烯增强合金熔体;在co气体和镁基体熔体发生气液原位反应的同时,保证坩埚顶部的温度在300℃以上,将镁基体熔体表面逸出的co气体与坩埚顶部的流动空气中含有的氧气接触引燃,生成蓝色燃烧的火焰;三、将步骤二得到的石墨烯增强合金熔体在50mpa压力下凝固,得到铸态石墨烯增强镁基复合材料;四、对步骤四得到的铸态石墨烯增强镁基复合材料在挤压温度为400℃,挤压比为20:1的条件下进行热挤压,制得挤压态石墨烯增强镁基复合材料。本实施例制得的铸态石墨烯增镁基复合材料的石墨烯分布方式如图4(a)所示,可以看出高体积分数石墨烯在镁基体中实现了均匀分布,经过热挤压后石墨烯的呈现出条带状分布,材料表面无空洞等缺陷,但仍未出现团聚,如图4(b)所示。本实施例制得的挤压态石墨烯增强镁基复合材料晶粒尺寸图像如图5所示,石墨烯的存在使得石墨烯增强镁基复合材料出现了细小的等轴晶。本实施例制得的挤压态石墨烯增强镁基复合材料的界面结构如图6所示,石墨与镁的界面清晰无空洞的存在,在界面出能够看到氧化镁的存在;说明利用一氧化碳制备出的石墨烯增强复合材料实现了强的界面结合。实施例4本实施例的石墨烯增强镁基复合材料的制备方法如下:一、将700gzk60镁合金(mg-4zn-0.5zr)在720℃坩埚中加热熔化,得镁基体熔体;其中,镁基体熔体熔化后的体积占坩埚体积的1/2,在坩埚的顶部引入空气,使坩埚的顶部与流动的空气直接接触;二、调整镁基体熔体的温度至680℃,将co气体以流速为2l/min持续通入到镁基体熔体中80min进行气液原位反应,并伴随着机械搅拌,搅拌速度为600r/min,得到石墨烯含量为1.1wt.%的石墨烯增强合金熔体;在co气体和镁基体熔体发生气液原位反应的同时,保证坩埚顶部的温度在300℃以上,将镁基体熔体表面逸出的co气体与坩埚顶部的流动空气中含有的氧气接触引燃,生成蓝色燃烧的火焰;三、将步骤二反应得到的石墨烯增强合金熔体的温度升至700℃,然后往其中通入高能超声波进行超声20min;高能超声波的通入功率为500w,频率为20hz;四、将高能超声波超声后的石墨烯增强合金熔体在50mpa压力下凝固,得到铸态石墨烯增强镁基复合材料;五、对步骤四得到的铸态石墨烯增强镁基复合材料进行16道次等通道径角挤压变形,制得变形态石墨烯增强镁基复合材料。本实施例制得的变形态石墨烯增强镁基复合材料的石墨烯分布方式如图7所示,与实施例3制得的挤压态石墨烯增强镁基复合材料的条带分布相比有明显不同,可以看出高体积分数石墨烯在镁基体中实现了均匀分布。实施例5本实施例的石墨烯增强镁基复合材料的制备方法如下:一、将700gmg-6zn合金在720℃坩埚中加热熔化,得镁基体熔体;其中,镁基体熔体熔化后的体积占坩埚体积的1/2,在坩埚的顶部引入空气,使坩埚顶部与流动的空气直接接触;二、调整镁基体熔体的温度至680℃,将co气体以流速为2l/min持续通入到镁基体熔体中40min进行气液原位反应,并伴随着机械搅拌,搅拌速度为600r/min,得到石墨烯含量占比为0.6wt.%的石墨烯增强合金熔体;在co气体和镁基体熔体发生气液原位反应的同时,保证坩埚顶部的温度在300℃以上,将镁基体熔体表面逸出的co气体与坩埚顶部的流动空气中含有的氧气接触引燃,生成蓝色燃烧的火焰;三、将步骤二反应得到的石墨烯增强合金熔体的温度升至700℃,然后往其中通入高能超声波进行超声20min;高能超声波的通入功率为500w,频率为20hz;四、将高能超声波超声后的石墨烯增强合金熔体在50mpa压力下凝固,得到铸态石墨烯增强镁基复合材料;五、对步骤四得到的铸态石墨烯增强镁基复合材料在挤压温度为400℃,挤压比为20:1的条件下进行热挤压,制得挤压态石墨烯增强镁基复合材料。本实施例制得的挤压态石墨烯增强镁基复合材料的力学性能如图8所示,可以看出挤压态石墨烯增强镁基复合材料的力学性能有明显的提升;根据图8的结果可以得出本实施例制得的挤压态石墨烯增强镁基复合材料的屈服强度得到明显提高,其屈服强度结果如表1所示。对比例1本对比例的一种原位自生石墨烯增强镁基复合材料的制备方法,它是按照以下步骤进行:一、将700g锌的重量百分比为6wt.%的镁锌合金(mg-6zn)在坩埚中熔化;二、将合金熔体冷却到625℃半固态温度区间,以600r/min的转速进行机械搅拌;同时将流速为2l/min的co2气体通入到合金熔体中持续40min;三、在半固态区间以600r/min的搅拌速度继续搅拌10min,促进石墨烯的宏观均匀分散;四、将石墨烯增强合金熔体升温至700℃,向石墨烯增强合金熔体中通入功率为500w,频率20hz的高能超声波;超声作用时间为20min,促进石墨烯的更均匀分散;五、将坩埚以20mm/min速度沉入水冷池中凝固,制备出复合材料;六、对复合材料在350℃下固溶24h,进行热挤压,得镁基复合材料;其中,挤压温度320℃,挤压比14:1。对比例2本对比例的石墨烯增强镁基复合材料的制备方法如下:一、将700gmg-6zn在720℃坩埚中加热熔化,得镁基体熔体;二、调整镁基体熔体的温度至680℃,将co2气体以流速为2l/min持续通入到镁基体熔体中40min进行气液原位反应,并伴随着机械搅拌,搅拌速度为600r/min;三、将步骤二反应得到的石墨烯增强合金熔体的温度升至700℃,然后往其中通入高能超声波进行超声20min;高能超声波的通入功率为500w,频率为20hz;四、将高能超声波超声后的石墨烯增强合金熔体在50mpa压力下凝固,得到铸态石墨烯增强镁基复合材料;五、对步骤四得到的铸态石墨烯增强镁基复合材料在挤压温度为400℃,挤压比为20:1的条件下进行热挤压,制得挤压态石墨烯增强镁基复合材料。本发明还对实施例1~5以及对比例1~2制得的石墨烯增强镁基复合材料及其采用的镁基体的力学性能进行了测试,得到屈服强度(stress)如表1所示。表1:实施例1~5以及对比例1~2的力学性能测试结果。屈服强度(mpa)mg-6zn150mg-4zn-0.5ca230zk60镁合金232实施例1235实施例2360实施例3320实施例4400实施例5255对比例1180对比例2200本发明根据上表1能够得到实施例1~5以及对比例1~2制得的石墨烯增强镁基复合材料相比其采用的镁基体的屈服强度增加量(stress增加量),其结果如表2所示。表2:实施例1~5以及对比例1~2的屈服强度增加量。屈服强度增加量实施例156.7%实施例256.5%实施例339.1%实施例472.4%实施例570%对比例120%对比例233.3%本发明未详细说明部分为本领域技术人员公知技术。最后应说明的是:以上实施例仅用以说明本发明的技术方案,而非对其限制;尽管参照前述实施例对本发明进行了详细的说明,本领域的普通技术人员应当理解:其依然可以对前述各实施例所记载的技术方案进行修改,或者对其中部分技术特征进行等同替换;而这些修改或者替换,并不使相应技术方案的本质脱离本发明各实施例技术方案的精神和范围。当前第1页12