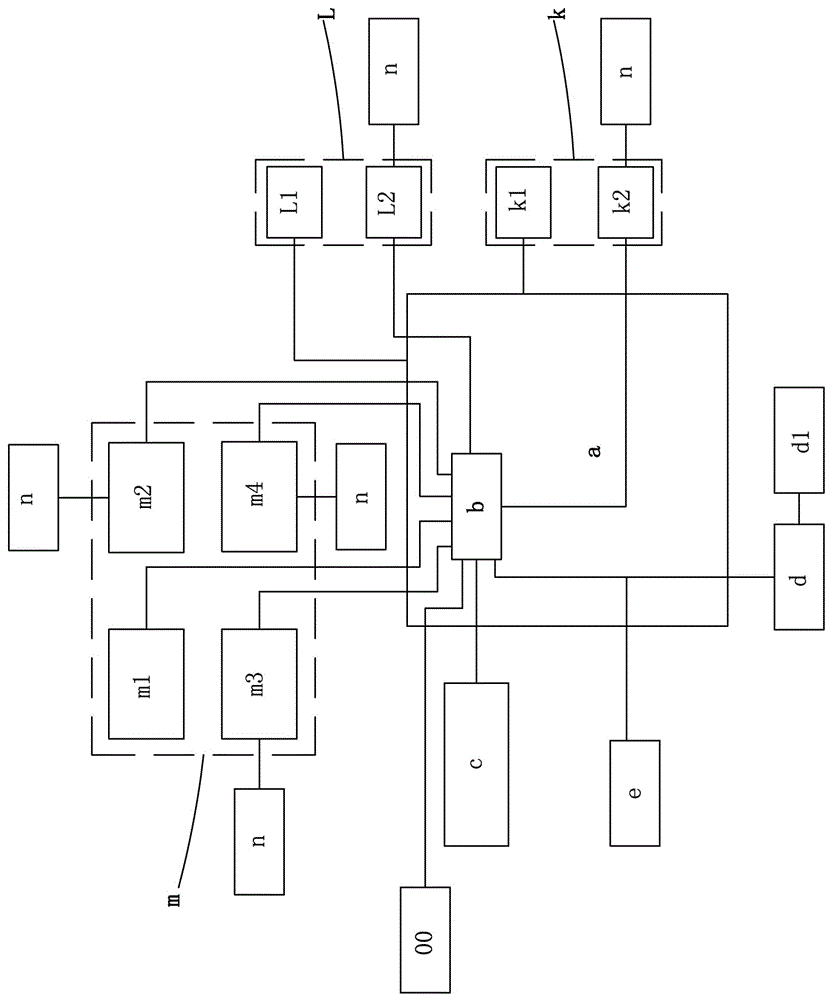
本发明涉及玻璃加工机械领域,具体地,涉及一种自动化程度高、使用门槛低的玻璃磨边机的自动控制系统。
背景技术:
:玻璃磨边机是目前常用的玻璃加工机械,其被广泛应用于玻璃片材的加工。申请号为cn201811070814.7的中国专利文献公开了一种立式双边玻璃磨边机,该玻璃磨边机包括机架;工件输送装置,包括至少一对夹持于待加工玻璃板两个面上的皮带输送单元,并按照预定方向输送玻璃板;皮带输送单元安装在第一活动支架上,第一活动支架通过第一滑移装置安装在机架上,第一活动支架在第一滑移装置作用下沿玻璃板的垂直方向移动;磨削装置,包括两个第二活动支架,玻璃板位于两第二活动支架之间,每个第二活动支架通过第二滑移装置安装在机架上,第二活动支架在第二滑移装置作用下沿皮带输送单元长度方向的垂直方向移动,每个第二活动支架上装有多个用于磨削玻璃板与输送方向平行的两条边的磨轮电机。解决现有技术中单边磨削,加工效率低的问题,实现双边磨削,提高磨削效率。申请号为cn201510254598.1的中国专利文献公开了一种玻璃磨边机,该玻璃磨边机包括机身和电控装置,机身上设有由前、后梁之间构成的夹紧输送通道,夹紧输送通道上分别设有进、出料口,所述进料口的前梁上安装有玻璃厚度感应保护装置,玻璃厚度感应保护装置由支臂、复位弹簧、感应滑轮以及触点开关组成,支臂呈弯接状并通过轴承可摆动式安装在前梁上,支臂一末端的左侧钩接有复位弹簧,复位弹簧另一端与固定立柱钩设,支臂一末端的右侧与触点开关的触点相抵,支臂另一端安装有感应滑轮,感应滑轮外侧圆弧端面与夹紧输送通道一侧处于同一水平面,触点开关与电控装置电性连接;通过在夹紧输送通道的进料口设置玻璃厚度感应保护装置,当玻璃厚度大于夹紧输送通道的宽度时,玻璃在进入夹紧输送通道的进料口时,玻璃前端便触碰到感应滑轮,支臂一末端绕轴承往触点开关摆动并压紧触点开关的触点,由于触点开关与电控装置电性连接,此时输送导轨断电停止输送,阻止玻璃继续前进,并提示操作工人应调节前、后梁之间的夹紧输送通道的宽度,再进行下一步操作,复位弹簧使支臂在调节好夹紧输送通道的宽度后自动复位,其结构简单、合理,防止玻璃爆碎,有效降低玻璃废品率,提高安全性及机器耐用性。然而,由于玻璃本身存在硬度高、脆性大的缺点,所以在玻璃机械加工过程中,现有的磨边机通常需要人手对磨边机的加工参数进行实时调整,以避免因加工参数产生变化而导致玻璃工件受力过大产生爆裂的情况。除了占用大量的人手资源外,其对设备的操作熟练程度还有较高的要求。因此,现有玻璃磨边机的自动化程度较低,不能实现其在大范围内的推广,且其使用门槛较高。技术实现要素:本发明的目的在于提供一种玻璃磨边机的自动控制系统,其用于解决上述技术问题。一种玻璃磨边机的自动控制系统,其特征在于,包括中央控制模块以及分别与中央控制模块电信号连接的输入组件、测量模块、输送模块、感应电眼、上倒棱控制模块k、下倒棱控制模块、侧边加工控制模块,其中:输入组件,用于把设备运行参数输入中央控制模块a;中央控制模块,用于接收输入组件、测量模块、输送模块、感应电眼、边缘检测模块的数据,并在运算后输出至输送模块、上倒棱控制模块、下倒棱控制模块、侧边加工控制模块,以使其正常工作;测量模块,通过测量或扫码的方式,对工件的长、宽、高尺寸进行测量,并输入至中央控制模块内;输送模块,用于接收和执行中央控制模块输出的移动、停止、减速或加速的指令,以使工件向前输送;上倒棱控制模块,用于在所述中央控制模块的指令下,对输送至其处的工件进行上倒棱;下倒棱控制模块,用于在所述中央控制模块的指令下,对输送至其处的工件进行下倒棱;侧边加工控制模块,用于在所述中央控制模块的指令下,对输送至其处的工件的侧边加工。所述自动控制系统还包括分别与中央控制模块电信号连接的靠边导向定位模块、上压组件控制模块、边缘检测模块、前置下倒棱控制模块、削边控制模块,其中:靠边导向定位模块,用于在所述感应电眼感应到工件进入其所在位置处时,接收所述中央控制模块的指令,以使工件进行靠边、导向、并定位;上压组件控制模块,通过感应电眼触发时间延迟,并根据测量模块输入到中央控制模块内的工件尺寸,使靠边导向定位模块导向定位后的工件被固定,并使工件输送时始终被夹持;边缘检测模块,用于监控输送至其处的工件的毛边余量,并把数据反馈至所述中央控制模块,使中央控制模块根据毛边余量大小实时调整所述输送模块对工件的输送速度;前置下倒棱控制模块,用于在所述中央控制模块的指令下,对输送至其处的工件进行下倒棱;削边控制模块,用于在所述中央控制模块的指令下,对输送至其处的工件进行削边。所述中央控制模块内设有数据寄存器,数据寄存器用于存储输入组件向中央控制模块输入的系统参数,并用于储存感应电眼和输送模块的数据,以实现中央控制模块对上倒棱控制模块、下倒棱控制模块、侧边加工控制模块、输送模块的实时控制。所述边缘检测模块电信号连接有脉冲检测组件,所述边缘检测模块利用所述脉冲检测组件产生的脉冲监控工件的毛边余量,并反馈至所述中央控制模块。所述削边控制模块包括粗削模块和细削模块,在所述中央控制模块的指令下,所述粗削模块对输送至其处的工件进行粗削,之后所述中央控制模块恢复所述输送模块对工件的设定输送速度,所述细削模块对工件进行细削。所述削边控制模块还包括二次粗削模块,二次粗削模块的动作设于粗削模块和细削模块之间,所述二次粗削模块与所述中央控制模块电信号连接,在所述中央控制模块的指令下,所述二次粗削模块对粗削模块粗削后的工件进行二次粗削。所述上倒棱控制模块包括上倒棱开粗模块和上倒棱抛光模块,上倒棱开粗模块用于在所述中央控制模块的指令下,对输送至其处的工件进行开粗,上倒棱抛光模块与中央控制模块电信号连接,用于在所述中央控制模块的指令下,对上倒棱开粗模块加工后的工件进行抛光。所述下倒棱控制模块包括下倒棱开粗模块和下倒棱抛光模块,所述下倒棱开粗模块用于在所述中央控制模块的指令下,对输送至其处的工件进行开粗,所述下倒棱抛光模块与中央控制模块电信号连接,用于在所述中央控制模块的指令下,对输送至其处的工件进行抛光。所述侧边加工控制模块包括细磨控制模块和侧边抛光控制模块,细磨控制模块用于在所述中央控制模块的指令下,对输送至其处的工件的侧边进行细磨,侧边抛光控制模块与中央控制模块电信号连接,用于在所述中央控制模块的指令下,对输送至其处的工件的侧边进行抛光。所述侧边抛光控制模块包括粗抛控制模块、精抛控制模块和亮抛控制模块,所述粗抛控制模块、精抛控制模块和亮抛控制模块均与中央控制模块电信号连接,分别用于在所述中央控制模块的指令下,依次对输送至其处的工件的侧边进行粗抛、精抛和亮抛。所述上倒棱控制模块、下倒棱控制模块、侧边加工控制模块电信号连接有加工部件的归零定位模组,归零定位模组包括分别与上述模块电信号连接的伺服电机、位于与磨头位置相对应的定位块,伺服电机与中央控制模块电信号连接。所述上倒棱控制模块、下倒棱控制模块、侧边加工控制模块电信号连接有抛光补偿模组,抛光补偿模组包括并联连接并分别与上倒棱控制模块、下倒棱控制模块、侧边加工控制模块电信号连接的磨头电机和伺服电机,磨头电机上设有电流检测器,电流检测器与中央控制模块电信号连接,电流检测器实时检测上倒棱控制模块、下倒棱控制模块、侧边加工控制模块与工件接触的负载电流,并把数据反馈至所述中央控制模块,以使中央控制模块通过把负载电流控制在一个稳定的设定区间,实现上倒棱控制模块、下倒棱控制模块、侧边加工控制模块对应的刀具抛光的实时补偿。与现有技术相比,本发明的玻璃磨边机的自动控制系统具有以下优点:1、本发明的玻璃磨边机的自动控制系统,在整个加工过程中,操作人员只需要在加工开始前把预设的加工参数通过输入组件输进中央控制模块。整个加工过程均由中央控制模块自动控制,完全无需人手对加工参数进行干预和调整,真正实现了玻璃磨边机傻瓜式操作,除了大幅提升玻璃磨边机的自动化程度外,还大大降低玻璃磨边机的操作门槛。2、本发明的玻璃磨边机的自动控制系统,利用感应电眼、输送模块、边缘检测模块等监控,并把数据输入至中央控制模块,通过中央控制模块发出指令,控制刀具进行自动定位、磨头抛光量进行实时调整,以及输送模块对工件的输送速度进行实时调整,确保工件在整个加工过程中都处于十分稳定的加工状态,有效保障了工件加工的完整性,大大提升了玻璃磨边机的加工速度。附图说明图1为本发明玻璃磨边机的自动控制系统的示意图;图2为本发明玻璃磨边机的自动控制系统的另一示意图;图3为本发明玻璃磨边机的自动控制系统的流程示意图;图4为本发明玻璃磨边机的自动控制系统的另一流程示意图;图5为本发明玻璃磨边机的自动控制系统的工件流转示意图;图6为本发明的归零定位模组的连接示意图;图7为本发明的归零定位模组的另一连接示意图;图8为本发明的抛光补偿模组的连接示意图;图9为本发明的抛光补偿模组的另一连接示意图;图10为本发明的玻璃磨边机的示意图;图11为本发明的玻璃磨边机的结构示意图;图12为图11另一方向的结构示意图;图13为图11中前置下倒棱组件的结构示意图。图中:a.中央控制模块、b.数据寄存器、c.测量模块、d.输送模块、d1.圈数计数器、e.感应电眼、e1.计时器、f.靠边导向定位模块、g.上压组件控制模块、h.边缘检测模块、h1.脉冲检测组件、i.前置下倒棱控制模块、j.削边控制模块、j1.粗削模块、j2.细削模块、j3.二次粗削模块、k.上倒棱控制模块、k1.上倒棱开粗模块、k2.上倒棱抛光模块、l.下倒棱控制模块、l1.下倒棱开粗模块、l2.下倒棱抛光模块、m.侧边加工控制模块、m1.细磨控制模块、m2.粗抛控制模块、m3.精抛控制模块、m4.亮抛控制模块、n.电流检测器、00.输入组件、0.测量组件、1.输送组件、11.上传送带组、12.下传送带组、13.上传动带驱动组、14.下传送带驱动组、2.靠边导向定位组件、21.固定导向组、22.移动导向组、3.上压组件、31.压轮驱动件、32.压轮、4.边缘检测组件、5.前置下倒棱组件、51.磨头电机、52.磨头、53.磨头电机活动架、54.伺服电机、55.定位块、6.削边组件、61.粗削组件、62.二次粗削组件、63.细削组件、7.上倒棱组件、71.上倒棱开粗组件、72.上倒棱抛光组件、8.下倒棱组件、81.下倒棱开粗组件、82.下倒棱抛光组件、9.侧边加工组件、91.侧边加工细磨组件、92.侧边加工粗抛组件、93.侧边加工精抛组件、94.侧边加工亮抛组件。具体实施方式本发明功能的实现及优点将结合实施例,参照附图做进一步说明。根据图1-13所示,玻璃磨边机的自动控制系统包括中央控制模块a以及分别与中央控制模块a电信号连接的输入组件00、测量模块c、输送模块d、感应电眼e、靠边导向定位模块f、上压组件控制模块g、边缘检测模块h、前置下倒棱控制模块i、削边控制模块j、上倒棱控制模块k、下倒棱控制模块l、侧边加工控制模块m,中央控制模块a内设有数据寄存器b。本发明的输入组件00用于把设备运行参数输入中央控制模块a,其可采用带输入按键和显示器的输入器,用于将系统参数输入中央控制模块a,并储存至数据寄存器b内。本发明的测量模块c,通过测量或扫码的方式,对工件的长、宽、高尺寸进行测量,并输入至中央控制模块a内。测量模块c可采用磁栅尺搭配计数模组实现工件长、宽、高的尺寸测量,其可采用市售的sony公司的gb-205er、gb-220er等型号的磁栅尺,并搭配汇川公司的h2u-4hc计数模组。而扫码则是通过扫描头对工件上的二维码或条形码进行扫描,以识别工件的具体尺寸。事实上,测量模块c为本发明自动控制系统的前置工序,工件的尺寸数据可直接输入至中央控制模块a内。本发明的中央控制模块a用于接收输入组件00、测量模块c、输送模块d、感应电眼e、边缘检测模块h的数据,并在运算后输出至输送模块d、靠边导向定位模块f、上压组件控制模块g、前置下倒棱控制模块i、削边控制模块j、上倒棱控制模块k、下倒棱控制模块l、侧边加工控制模块m,以使其正常工作。中央控制模块a可采用市售的中央处理模组,如三星公司的s3c2440、s3c2416等。数据寄存器b用于存储输入组件00向中央控制模块a输入的系统参数,并用于储存感应电眼e和输送模块d的数据,以实现中央控制模块a对削边控制模块j、上倒棱控制模块k、下倒棱控制模块l、侧边加工控制模块m、输送模块d的实时控制。数据寄存器b可采用中央控制模块a内的ram模组,也可以采用外置的单独扩展ram模组,如microcchip公司的23lc模组系列。数据寄存器b中还可以内置工件的加工余量模式,并与测量模块c输入至中央控制模块a内的工件高度进行匹配,从而通过中央控制模块a自动调整玻璃磨边机的加工参数,以实现玻璃磨边机的全自动运作。当然,为了使系统的运作灵活性更强,工件的双边加工余量也可以通过输入组件00直接输入至中央控制模块a内。加工余量模式和工件高度的对应请参考表一:模式1模式2模式3模式4模式5模式6模式7模式8工件厚度(mm)小于55-88-1010-1212-1515-1919-25大于25双边余量(mm)1-22-33-44-55-66-86-1010-12本发明的输送模块d用于接收和执行中央控制模块a输出的移动、停止、减速或加速的指令,以控制输送组件1对工件进行输送。输送模块d上还设置有圈数计数器d1,其以工件通过感应电眼e后触发,对输送组件1的电机圈数进行计算,得出工件的移动距离,从而得出工件到达前置下倒棱控制模块i、削边控制模块j、上倒棱控制模块k、下倒棱控制模块l、侧边加工控制模块m的时间。圈数计数器d1可采用市售的圈数感应器或计数器,如欧姆龙公司的e3x-na11。本发明的输送组件1包括两组上传送带组11、两组下传送带组12、两组上传动带驱动组13和两组下传送带驱动组14,每一组传送带组11、下传送带组12、上传动带驱动组13和下传送带驱动组14为一个组合,两个组合相对设置,工件的两侧分别位于一个组合的上传送带组11和下传送带组12之间,上传动带驱动组13用于驱动同一个组合内的上传送带组11下降,使上传送带组11作用到工件上表面,下传送带驱动组14用于驱动下传送带组12的传动带滚动,使工件在上传送带组11和下传送带组12的摩擦力下被输送到不同工序。本发明的靠边导向定位模块f用于在所述感应电眼e感应到工件进入其所在位置处时,接收所述中央控制模块a的指令,以控制靠边导向定位组件2将工件进行靠边导向定位。靠边导向定位模块f的作用是使工件在进入输送组件1时始终保持相同的朝向,解决了工件因歪斜、错位而导致后续加工工序不能顺利进行的问题,提升了工件加工的稳定性。靠边导向定位组件2包括固定导向组21和移动导向组22,固定导向组21和移动导向组22之间设置有工件进给通道,移动导向组22上设置有定位气缸以驱动移动导向组22和工件向固定导向组21运动,使得工件沿固定导向组21的导向方向运动。在工件进入固定导向组21和移动导向组22之间的工件进给通道处时,在中央控制模块a的指令下,靠边导向定位模块f控制移动导向组22启动,移动导向组22的定位气缸将工件向固定导向组21推动,进而将工件进行靠边导向定位。本发明的上压组件控制模块g通过感应电眼e外接的计时器e1触发时间延迟,并根据测量模块c输入到中央控制模块a内的工件高度,控制上压组件3对靠边导向定位模块f导向定位后的工件进行固定,并使上压组件3夹住工件进入输送组件1。计时器e1可采用市售的工业电子计时器,如明佳公司的sy系列、赛普公司的sp-sys系列等。上压组件控制模块g的设置可对工件在输送组件1中起良好的固定作用,避免工件因加工受力产生移位而导致其不能顺利加工的问题,有效提升了工件输送的稳定性及可靠性。上压组件3包括压轮驱动件31和压轮32,在工件被靠边导向定位组件2靠边导向定位后,上压组件控制模块g通过感应电眼e触发时间延迟,并根据输入组件00输入到中央控制模块a内的工件尺寸,控制上压组件3的压轮驱动件31启动,带动压轮32下降,并从工件上方作用到工件上,将靠边导向定位组件2导向定位后的工件固定,然后上压组件3夹住工件进入输送组件1。本发明的边缘检测模块h用于控制边缘检测组件监控所述输送组件输送至其处的工件的毛边余量,并把数据反馈至所述中央控制模块a,使中央控制模块a根据毛边余量大小实时调整所述输送模块d对工件的输送速度;边缘检测模块h电信号连接有脉冲检测组件h1,脉冲检测组件h1可采用市售的编码器,如中国台湾阳明公司的fotekmes-2000系列。所述边缘检测模块h利用所述脉冲检测组件h1产生的脉冲监控工件的毛边余量,并反馈至所述中央控制模块a。在工件被输送到边缘检测组件4处时,边缘检测模块h控制边缘检测组件4监控输送模块c输送至其处的工件的毛边余量,并把数据反馈至中央控制模块a,中央控制模块a向输送模块d发送指令,使输送模块d实时调整输送组件1对工件的输送速度,当工件宽度落差过大,或宽度超限超出磨量范围时,输送模块d控制输送组件1进行自动降速。边缘检测组件4的具体结构,可参考中国专利文献cn111156952a,在此不再赘述。本发明的上倒棱控制模块k用于在所述中央控制模块a的指令下,控制上倒棱组件进行零点定位,并对输送至其处的工件进行上倒棱。上倒棱控制模块k包括上倒棱开粗模块k1和上倒棱抛光模块k2,当工件经输送组件1输送至上倒棱组件7时,上倒棱开粗模块k1在所述中央控制模块a的指令下,控制上倒棱开粗组件71对输送至其处的工件进行开粗,上倒棱抛光模块k2和中央控制模块a电信号连接,在所述中央控制模块a的指令下,控制上倒棱抛光组件72对上倒棱开粗组件71加工后的工件进行抛光。本实施例中,上倒棱开粗组件71和上倒棱抛光组件72包括磨头电机51、磨头52、磨头电机活动架53、伺服电机54及定位块55,磨头电机51设于磨头电机活动架53上,磨头52与磨头电机51的输出端连接,磨头电机活动架53与伺服电机54的驱动端连接,在工件被输送组件1输送到上倒棱开粗组件71和上倒棱抛光组件72处时,上倒棱开粗模块k1和上倒棱抛光模块k2在中央控制模块a的指令下,控制伺服电机54带动磨头电机活动架53移动,实现磨头电机51驱动磨头52对工件进行上倒棱开粗和上倒棱抛光。上倒棱的加工可把工件上表面上的直角加工成钝角,除了增大工件相邻面的受力角度,提高工件的碰撞强度外,还能避免工件的邻接角对人员产生划伤的现象。本发明的前置下倒棱控制模块i用于在所述中央控制模块a的指令下,控制前置下倒棱组件5对输送至其处的工件进行下倒棱。前置下倒棱的目的是增加工件在后续加工中与与磨轮之间接触的角度,即使其从直角变成钝角,避免工件的底边在后续过程中产生爆边的现象。同时,下倒棱可减少磨轮与工件之间的切削面积,提高工件加工的速度。前置下倒棱组件5的机构与上倒棱开粗组件71的机械机构相同。本发明的削边控制模块j用于在所述中央控制模块a的指令下,控制削边组件6对输送至其处的工件进行削边。削边控制模块j包括粗削模块j1、二次粗削模块j3、细削模块j2,在所述中央控制模块a的指令下,所述粗削模块j1控制粗削组件61对输送至其处的工件进行粗削。利用边缘检测模块h对工件的毛边余量的监测,以及感应电眼e和圈数计数器d1的移动距离计算,当工件宽度落差过大,或宽度超限超出磨量范围时,工件前端进入粗削组件61时,输送模块d控制输送组件1进行自动降速,而工件后端通过粗削组件61后,所述中央控制模块a恢复所述输送模块d控制输送组件1对工件在中央控制模块a内设定的输送速度。粗削组件61是对工件的边缘进行初始加工,通过输送模块d控制输送组件1进行自动降速,可最大程度上避免因磨削量过大或磨削量突变而导致工件出现爆裂、崩坏等情况,有效保障工件在加工过程中的完整性和稳定性。所述二次粗削模块j3控制二次粗削组件62对粗削模块j1粗削后的工件进行二次粗削,所述细削模块j2控制细削组件63对工件进行细削。粗削组件61、二次粗削组件62和细削组件63的结构与上倒棱开粗组件71的机械结构相同,区别点在于,粗削组件61、二次粗削组件62和细削组件63的磨头52上具有径向放射型分布的凹槽,上倒棱开粗组件71的磨头52则为平整磨头。本发明的下倒棱控制模块l用于在所述中央控制模块a的指令下,控制下倒棱组件对输送至其处的工件进行下倒棱。下倒棱控制模块l包括下倒棱开粗模块l1和下倒棱抛光模块l2,当工件经输送组件1输送至下倒棱组件8时,所述下倒棱开粗模块l1在所述中央控制模块a的指令下,控制下倒棱开粗组件81输送至其处的工件进行开粗,所述下倒棱抛光模块l2和中央控制模块a电信号连接,在所述中央控制模块a的指令下,控制下倒棱抛光组件82对输送至其处的工件进行抛光。本实施例中,下倒棱开粗组件81和下倒棱抛光组件82与上倒棱开粗组件71的机械结构相同。下倒棱的加工可清除一次下倒棱完成后的工件余量,除了增大工件相邻面的受力角度,提高工件的碰撞强度外,还能避免工件的邻接角对人员产生划伤的现象。本发明的侧边加工控制模块m用于在所述中央控制模块a的指令下,控制侧边加工组件9对输送至其处的工件的侧边加工。侧边加工控制模块m包括细磨控制模块m1和侧边抛光控制模块,而侧边抛光控制模块则包括粗抛控制模块m2、精抛控制模块m3和亮抛控制模块m4。与侧边加工控制模块m的设置对应,侧边加工组件9包括侧边加工细磨组件91、侧边加工粗抛组件92、侧边加工精抛组件93和侧边加工亮抛组件94。侧边加工细磨组件91、侧边加工粗抛组件92、侧边加工精抛组件93和侧边加工亮抛组件94依工件输送方向顺序排列,即工件在输送组件1的带动下依次通过侧边加工细磨组件91、侧边加工粗抛组件92、侧边加工精抛组件93和侧边加工亮抛组件94。细磨控制模块m1在所述中央控制模块a的指令下,控制侧边加工细磨组件91对输送至其处的工件的侧边进行细磨,侧边抛光控制模块和中央控制模块a电信号连接,在所述中央控制模块a的指令下,控制侧边加工抛光组件对输送至其处的工件的侧边进行抛光。本发明中,粗抛控制模块m2、精抛控制模块m3和亮抛控制模块m4均和中央控制模块a电信号连接,分别用于在所述中央控制模块a的指令下,控制侧边加工粗抛组件92、侧边加工精抛组件93和侧边加工亮抛组件94对输送至其处的工件的侧边进行粗抛、精抛和亮抛。本实施例中,侧边加工细磨组件91、侧边加工粗抛组件92、侧边加工精抛组件93和侧边加工亮抛组件94与上倒棱开粗组件71的机械结构相同。工件侧边的细磨,可在保障抛光工序的加工余量的前提下,最大程度上减少工件侧边的加工余量,从而减少后续抛光组件的磨削压力,有效延长抛光组件的使用寿命。而三道抛光工序除了可在工件侧面形成光滑的抛光面外,还能降低抛光组件的损耗,以延长其使用寿命。在本发明中,前置下倒棱控制模块i、削边控制模块j、上倒棱控制模块k、下倒棱控制模块l、侧边加工控制模块m的加工量(即加工深度)由中央控制模块a自动分配,工件的双边余量则由数据寄存器b根据测量模块c得出的工件厚度自动分配,或由人工输入。当上述模块的加工深度达到预设值时,加工部件即停止进给并退回。此外,前置下倒棱控制模块i、削边控制模块j、上倒棱控制模块k、下倒棱控制模块l、侧边加工控制模块m还电信号连接有加工部件的归零定位模组。根据本实施例,电信号连接归零定位模组的模块有:前置下倒棱控制模块i、粗削模块j1、细削模块j2、二次粗削模块j3、上倒棱开粗模块k1、上倒棱抛光模块k2、下倒棱开粗模块l1、下倒棱抛光模块l2、细磨控制模块m1、粗抛控制模块m2、精抛控制模块m3和亮抛控制模块m4。该归零定位模组包括分别与上述模块电信号连接的伺服电机54、位于与磨头52位置相对应的定位块55,伺服电机54与中央控制模块a电信号连接。当玻璃磨边机启动前,前置下倒棱控制模块i、削边控制模块j、上倒棱控制模块k、下倒棱控制模块l、侧边加工控制模块m分别驱动伺服电机54前进,磨头52接触到定位块55时,伺服电机54受力而产生扭矩。当扭矩达到伺服电机54预设值时,即磨头52已达到归零状态,伺服电机54即把信号传输至中央控制模块a内,由中央控制模块a下达前置下倒棱控制模块i、削边控制模块j、上倒棱控制模块k、下倒棱控制模块l、侧边加工控制模块m的停止指令,至此完成加工部件的归零定位的过程。加工部件的归零定位可确保工件在进入加工状态时,上述模块始终能与工件充分接触,避免了因磨头52磨损而导致上述模块不能对工件进行充分加工的情况。同时,该归零定位可为上述模块的初始位置、状态为中央控制模块a提供完善的位置数据,从而确保中央控制模块a下达加工指令的准确性。另外,在磨头52首次安装时即进行归零定位,伺服电机54的位置数据及磨头52的工作厚度数据将通过输入组件00输入至中央控制模块a内。磨头52每次进行归零定位时,中央控制模块a都会对伺服电机54在归零定位时的位置与磨头52初始安装时伺服电机54的位置进行对比,当两者位置的距离小于磨头52的工作厚度时,即磨头52还处于正常工作的状态下,当两者位置的距离等于磨头52的工作厚度时,即磨头52达到磨损极限,中央控制模块a即发出更换磨头52的报警信号。本发明中,上倒棱控制模块k、下倒棱控制模块l、侧边加工控制模块m电信号连接有抛光补偿模组。根据本实施例,电信号连接抛光补偿模组的模块有:上倒棱抛光模块k2、下倒棱抛光模块l2、粗抛控制模块m2、精抛控制模块m3和亮抛控制模块m4。该抛光补偿模组包括并联连接并分别与上述模块电信号连接的磨头电机51和伺服电机54,磨头电机51上设有电流检测器n,电流检测器n与中央控制模块a电信号连接,中央控制模块a内设定了一个负载电流范围。当上倒棱抛光模块k2、下倒棱抛光模块l2、粗抛控制模块m2、精抛控制模块m3和亮抛控制模块m4正常工作时,磨头电机51驱动磨头52与工件接触,磨头电机51受力后产生负载电流,并经电流检测器n反馈至中央控制模块a中,当负载电流在中央控制模块a设定的范围内时,磨头52处于正常工作状态。当负载电流低于该设定范围时,由中央控制模块a下达进给指令,上倒棱抛光模块k2、下倒棱抛光模块l2、粗抛控制模块m2、精抛控制模块m3和亮抛控制模块m4即使伺服电机54向前进给;当负载电流高于该设定范围时,由中央控制模块a下达回退指令,上倒棱抛光模块k2、下倒棱抛光模块l2、粗抛控制模块m2、精抛控制模块m3和亮抛控制模块m4使伺服电机54向后回退。抛光补偿模组可最大程度的保障工件抛光的稳定性及可靠性,并根据磨头电机51的负载电流变化实时调整伺服电机54带动磨头电机51和磨头52进给或回退,有效保障了工件加工的完整性及抛光效果。事实上,与传统的静态抛光不同,本发明的工件由于在输送组件1持续移动,电流检测器n在磨头52与工件接触开始,到工件离开磨头52为止的移动过程中均处于检测状态,所以伺服电机54和电流检测器n的配合可实现整个工件抛光的连续动态自动检测和自动补偿,并避免因加工误差而导致抛光量过大的情况,使工件抛光后的光洁度更加均匀,并提升工件的整体抛光效果。以上仅为本发明的较佳实施例而已,并不用以限制本发明,凡在本发明的精神和原则之内所作的任何修改、等同替换或改进等,均应包含在本发明的保护范围之内。当前第1页12