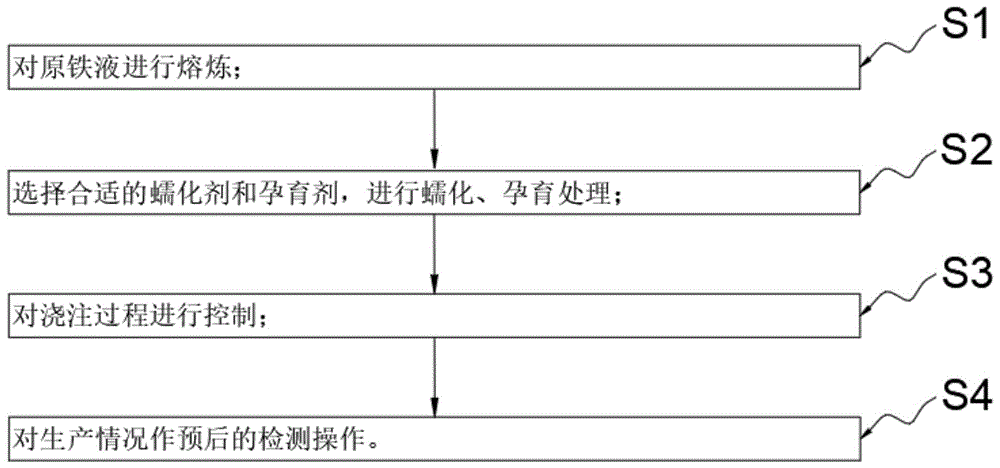
本发明涉及炼铁
技术领域:
,具体地说,涉及一种高性能蠕墨铸铁材料铸件的制备工艺。
背景技术:
:蠕墨铸铁是指铸铁液经蠕化处理,使其石墨呈蠕虫状与少量球团状的铸铁,其石墨形状介于灰铁的片状石墨与球铁的球状石墨之间。球墨铸铁时结构件的优良材料,蠕墨铸铁的抗拉强度高于灰铸铁、略低于球墨铸铁,蠕墨铸铁中球团石墨数增加,蠕化率降低,其强度与伸长率提高、热导率和收缩率将变差。蠕墨铸铁制备过程中,控制石墨的形态及不同形态的石墨量,使控制蠕墨铸铁的性能的关键。但是,目前却没有较好的可以提高蠕墨铸铁性能的制备工艺。技术实现要素:本发明的目的在于提供了一种高性能蠕墨铸铁材料铸件的制备工艺,以解决上述
背景技术:
中提出的问题。为实现上述技术问题的解决,本发明提供了一种高性能蠕墨铸铁材料铸件的制备工艺,包括如下步骤:s1、对原铁液进行熔炼;s2、选择合适的蠕化剂和孕育剂,进行蠕化、孕育处理;s3、对浇注过程进行控制;s4、对生产情况作预后的检测操作。作为本技术方案的进一步改进,所述s1中,对原铁液进行熔炼的方法包括如下步骤:s1.1、遵循高效、低耗的原则,选择开炉灵活、加热速度快、铁水中气体含量少、铁水温度成分均匀、铁水成分易于控制的中频感应电炉;s1.2、加入75%的珠光体为基体原料,置于中频炉中进行熔炼,入炉料必须用电子秤称量,计量准确、记录清楚,以保证出炉铁水量准确;s1.3、控制炉料原铁液中的化学成分为:c为3.2~3.9%,si为1.2~2.2%,mn为0.2~0.6%,s为≤0.06%,p为≤0.03%,cu为0.5~1.2%,sn为0.05~0.12%;s1.4、确保原铁液中的化学成分符合高碳、高硅、低磷、低硫和一定的含锰量后,将原铁液加热到1350~1380℃,获取化学成分稳定的原铁水。作为本技术方案的进一步改进,所述s2中,蠕化、孕育处理的方法包括如下步骤:s2.1、选取高度与直径比为2:1的球化包来处理原铁液;s2.2、按照原铁液重量1.1%的比例值,以5~15mm的小块加入稀土镁硅铁合金fesimgre17作为蠕化剂;s2.3、按照蠕化剂重量15%的比例值,加入fesimgre7的球化剂作为起爆剂;s2.4、按照原铁液重量1%的比例值,以5~15mm的小块加入fesi75作为孕育剂;s2.5、采用平底包冲入法对原铁液进行蠕化孕育处理;s2.6、继续加热熔炼,在炉前采用插入式热电偶进行测温,将出铁温度控制在1420~1450℃;s2.7、在炉前采用三角试样的方法检验孕育、蠕化效果的好坏。作为本技术方案的进一步改进,所述s2.5中,平底包冲入法的方法包括如下步骤:s2.5.1、先在包底按比例加入蠕化剂;s2.5.2、再在蠕化剂上面按比例加入孕育剂;s2.5.3、而后在蠕化剂、孕育剂上部覆盖干燥、干净的铁屑,以延缓蠕化反应,提高蠕化和孕育的效果;s2.5.4、最后在铁屑上面加结壳性好、吸渣性强的草木灰做作覆盖剂,以防止铁水与大气接触和镁蒸汽的逸出。作为本技术方案的进一步改进,所述s2.7中,三角试样的方法为:浇注三角试样,试样冷却至暗红色时进行淬火冷却;砸断后观察试样断口,若断口呈银白色、尖端白口、中心有缩松、两侧凹陷,同时砸断时有电石气味,敲击声与钢件相似,则蠕化良好,否则蠕化不良。作为本技术方案的进一步改进,所述s3中,浇注控制的方法包括如下步骤:s3.1、对原铁水进行取样,检测原铁水中mg元素和re元素的残余量,当残留mg的含量降至0.013~0.022%、残留re的含量降至0.021~0.045%时;s3.2、将出铁温度控制在1420~1450℃;s3.3、将浇注温度控制在1380~1410℃,避免浇注过程中铸件出现气孔及浇不满等情况;s3.4、以400kg原铁水为一个包次,每个包次的铁液在10min内完成浇注;s3.5、每炉次的最后一个包次铁液浇注试样,做力学性能和金相检验,其中,产品与试样批次需一一对应,并且跟踪处理工序。作为本技术方案的进一步改进,所述s4中,预后检测操作的方法包括如下步骤:s4.1、浇注完成后,检查浇注产品,确定打箱后的铸件是否表面光洁无粘砂、夹渣和夹砂缺陷,确定加工后铸件内部是否无缩孔;s4.2、对随机连续3~5炉次的产品进行取样化验,确定铸件化学成分是否稳定;s4.3、用金相显微镜检测铸件组织,确定铸件组织的石墨蠕化率和基本组织,基本组织包括珠光体、铁素体、碳化物、共晶碳化物等;s4.4、对浇注铸件的机械性能进行检测试样,加工成规格为的试样作抗拉或屈服强度、塑性、导热率、硬度等机械性能检测,确保其机械性能达到或超过预设的期望标准。作为本技术方案的进一步改进,所述s4.4中,对试样强度的检测计算表达式为:拉伸强度:σb=p/(b×d);式中,σb为抗拉强度(mpa),p为最大负荷(n),b为试样铸件材料的宽度(mm),d为试样铸件材料的厚度(mm);屈服强度:σs=f/s;式中,σs为屈服强度(mpa),f为材料屈服时所受的最小的力(n),s为材料受力的横截面积(m2)。作为本技术方案的进一步改进,所述s4.4中,对试样塑性的检测步骤、计算公式及精度设定为:首先,使用高精度仪器化压入仪和面角为120°四棱锥压头对试样铸件材料实施压入深度>3μm的压入测试,并将所获得的结果进行及时记录,之后将该数据代入到特征应力公式:其中,(hn/eci)为压入比功、eci为试样铸件材料弹性模量、j为常量参数,取值标注范围可依据高精度仪器化压入仪说明书中内容进行选取;在得到特征应力之后,需要将压入比功(hn/eci)代入到特征应变公式中以求得该试样铸件材料在面角为120°四棱锥压头下的特征应变,其公式如下:其中k为常数参量,选取同j;此步骤结束后得到了面角为120°四棱锥压头的δr1和εr1;之后将面角为120°四棱锥压头替换为面角为175°四棱锥压头,重复上述操作步骤,得到该试样铸件材料的力学性能δr2和εr2;在获得了相应指标后,采用hollomon幂硬化函数来对两组测试结果(δr1,εr1)和(δr2,εr2)进行拟合实验,同时结合金属材料弹性模量eci,以此来确定该试样铸件材料自身具有的屈服强度系数;其次,为了降低由于试样铸件材料在生产批次、加工技术、保存运输等环节存在差异容易对仪器化压入识别方法精度产生的不利影响,则针对仪器化压入识别方法精度精度问题作出如下规定:试样铸件材料自身为标准幂硬化材料,则压入比功(hn/eci)处于0.02~0.5之间;此时,仪器化压入识别方法精度公式为:δyerr=(δyt-δy)/δy;其中δyt为该试样逐渐材料屈服强度识别结果、δy为真实误差值;通过计算可知,试样铸件材料塑性参数识别误差分布在-10%~20%之间,且试样铸件材料弹性模量eci越大,其误差识别范围也随之增大;但是在应用了压入比功(hn/eci)后,此种正相关性扭转为负相关性,即:试样铸件材料弹性模量eci越大,误差识别范围逐渐缩小,最终接近于一个常量值,也就是该试样铸件材料塑性参数的真实数值。作为本技术方案的进一步改进,所述s4.4中,对试样导热率的检测计算表达式为:热传导方程表达式:引入比例系数λ,则得上式称为傅里叶定律,其中,单位时间内物体以热传导方式传递的热量q与传热面积a呈正比,与壁面两侧的温度差(t1-t2)成正比,而与壁面厚度δ成反比;将上式改写为:式中,δt=t1-t2为导热过程的推动力,为单层平壁的导热热阻;导热率:单位为w/(m·k)或w/(m·℃)。与现有技术相比,本发明的有益效果:该高性能蠕墨铸铁材料铸件的制备工艺中,通过选择合适的熔化设备,选择合适的蠕化处理包及方法,同时通过选取合适的蠕化剂、孕育剂并调整添加比例,并严格控制出铁温度、控制出铁时原铁液中的石墨形态及不同形态石墨的量,另外通过控制浇注包次的原铁液量及浇注时间,提高石墨蠕化率,从而提高铸件成品的强度、塑性及导热率等性能。附图说明图1为本发明的整体工艺流程图;图2为本发明的局部工艺流程图之一;图3为本发明的局部工艺流程图之二;图4为本发明的局部工艺流程图之三;图5为本发明的局部工艺流程图之四;图6为本发明的局部工艺流程图之五。具体实施方式下面将结合本发明实施例中的附图,对本发明实施例中的技术方案进行清楚、完整地描述,显然,所描述的实施例仅仅是本发明一部分实施例,而不是全部的实施例。基于本发明中的实施例,本领域普通技术人员在没有做出创造性劳动前提下所获得的所有其他实施例,都属于本发明保护的范围。实施例1如图1-图6所示,本实施例提供了一种高性能蠕墨铸铁材料铸件的制备工艺,包括如下步骤:s1、对原铁液进行熔炼;s2、选择合适的蠕化剂和孕育剂,进行蠕化、孕育处理;s3、对浇注过程进行控制;s4、对生产情况作预后的检测操作。本实施例中,s1中,对原铁液进行熔炼的方法包括如下步骤:s1.1、遵循高效、低耗的原则,选择开炉灵活、加热速度快、铁水中气体含量少、铁水温度成分均匀、铁水成分易于控制的中频感应电炉;s1.2、加入75%的珠光体为基体原料,置于中频炉中进行熔炼,入炉料必须用电子秤称量,计量准确、记录清楚,以保证出炉铁水量准确;s1.3、控制炉料原铁液中的化学成分为:c为3.2~3.9%,si为1.2~2.2%,mn为0.2~0.6%,s为≤0.06%,p为≤0.03%,cu为0.5~1.2%,sn为0.05~0.12%;s1.4、确保原铁液中的化学成分符合高碳、高硅、低磷、低硫和一定的含锰量后,将原铁液加热到1350~1380℃,获取化学成分稳定的原铁水。本实施例中,s2中,蠕化、孕育处理的方法包括如下步骤:s2.1、选取高度与直径比为2:1的球化包来处理原铁液;s2.2、按照原铁液重量1.1%的比例值,以5~15mm的小块加入稀土镁硅铁合金fesimgre17作为蠕化剂;s2.3、按照蠕化剂重量15%的比例值,加入fesimgre7的球化剂作为起爆剂;s2.4、按照原铁液重量1%的比例值,以5~15mm的小块加入fesi75作为孕育剂;s2.5、采用平底包冲入法对原铁液进行蠕化孕育处理;s2.6、继续加热熔炼,在炉前采用插入式热电偶进行测温,将出铁温度控制在1420~1450℃;s2.7、在炉前采用三角试样的方法检验孕育、蠕化效果的好坏。进一步地,s2.5中,平底包冲入法的方法包括如下步骤:s2.5.1、先在包底按比例加入蠕化剂;s2.5.2、再在蠕化剂上面按比例加入孕育剂;s2.5.3、而后在蠕化剂、孕育剂上部覆盖干燥、干净的铁屑,以延缓蠕化反应,提高蠕化和孕育的效果;s2.5.4、最后在铁屑上面加结壳性好、吸渣性强的草木灰做作覆盖剂,以防止铁水与大气接触和镁蒸汽的逸出。具体地,s2.7中,三角试样的方法为:浇注三角试样,试样冷却至暗红色时进行淬火冷却;砸断后观察试样断口,若断口呈银白色、尖端白口、中心有缩松、两侧凹陷,同时砸断时有电石气味,敲击声与钢件相似,则蠕化良好,否则蠕化不良。本实施例中,s3中,浇注控制的方法包括如下步骤:s3.1、对原铁水进行取样,检测原铁水中mg元素和re元素的残余量,当残留mg的含量降至0.013~0.022%、残留re的含量降至0.021~0.045%时;s3.2、将出铁温度控制在1420~1450℃;s3.3、将浇注温度控制在1380~1410℃,避免浇注过程中铸件出现气孔及浇不满等情况;s3.4、以400kg原铁水为一个包次,每个包次的铁液在10min内完成浇注;s3.5、每炉次的最后一个包次铁液浇注试样,做力学性能和金相检验,其中,产品与试样批次需一一对应,并且跟踪处理工序。本实施例中,s4中,预后检测操作的方法包括如下步骤:s4.1、浇注完成后,检查浇注产品,确定打箱后的铸件是否表面光洁无粘砂、夹渣和夹砂缺陷,确定加工后铸件内部是否无缩孔;s4.2、对随机连续3~5炉次的产品进行取样化验,确定铸件化学成分是否稳定;s4.3、用金相显微镜检测铸件组织,确定铸件组织的石墨蠕化率和基本组织,基本组织包括珠光体、铁素体、碳化物、共晶碳化物等;s4.4、对浇注铸件的机械性能进行检测试样,加工成规格为的试样作抗拉或屈服强度、塑性、导热率、硬度等机械性能检测,确保其机械性能达到或超过预设的期望标准。其中,s4.3中,石墨蠕化率>62%,基本组织为珠光体+铁素体+碳化物,珠光体占85%,共晶碳化物占5%。具体地,s4.4中,对试样强度的检测计算表达式为:拉伸强度:σb=p/(b×d);式中,σb为抗拉强度(mpa),p为最大负荷(n),b为试样铸件材料的宽度(mm),d为试样铸件材料的厚度(mm);屈服强度:σs=f/s;式中,σs为屈服强度(mpa),f为材料屈服时所受的最小的力(n),s为材料受力的横截面积(m2)。具体地,s4.4中,对试样塑性的检测步骤、计算公式及精度设定为:首先,使用高精度仪器化压入仪和面角为120°四棱锥压头对试样铸件材料实施压入深度>3μm的压入测试,并将所获得的结果进行及时记录,之后将该数据代入到特征应力公式:其中,(hn/eci)为压入比功、eci为试样铸件材料弹性模量、j为常量参数,取值标注范围可依据高精度仪器化压入仪说明书中内容进行选取;在得到特征应力之后,需要将压入比功(hn/eci)代入到特征应变公式中以求得该试样铸件材料在面角为120°四棱锥压头下的特征应变,其公式如下:其中k为常数参量,选取同j;此步骤结束后得到了面角为120°四棱锥压头的δr1和εr1;之后将面角为120°四棱锥压头替换为面角为175°四棱锥压头,重复上述操作步骤,得到该试样铸件材料的力学性能δr2和εr2;在获得了相应指标后,采用hollomon幂硬化函数来对两组测试结果(δr1,εr1)和(δr2,εr2)进行拟合实验,同时结合金属材料弹性模量eci,以此来确定该试样铸件材料自身具有的屈服强度系数;其次,为了降低由于试样铸件材料在生产批次、加工技术、保存运输等环节存在差异容易对仪器化压入识别方法精度产生的不利影响,则针对仪器化压入识别方法精度精度问题作出如下规定:试样铸件材料自身为标准幂硬化材料,则压入比功(hn/eci)处于0.02~0.5之间;此时,仪器化压入识别方法精度公式为:δyerr=(δyt-δy)/δy;其中δyt为该试样逐渐材料屈服强度识别结果、δy为真实误差值;通过计算可知,试样铸件材料塑性参数识别误差分布在-10%~20%之间,且试样铸件材料弹性模量eci越大,其误差识别范围也随之增大;但是在应用了压入比功(hn/eci)后,此种正相关性扭转为负相关性,即:试样铸件材料弹性模量eci越大,误差识别范围逐渐缩小,最终接近于一个常量值,也就是该试样铸件材料塑性参数的真实数值。具体地,s4.4中,对试样导热率的检测计算表达式为:热传导方程表达式:引入比例系数λ,则得上式称为傅里叶定律,其中,单位时间内物体以热传导方式传递的热量q与传热面积a呈正比,与壁面两侧的温度差(t1-t2)成正比,而与壁面厚度δ成反比;将上式改写为:式中,δt=t1-t2为导热过程的推动力,为单层平壁的导热热阻;导热率:单位为w/(m·k)或w/(m·℃)。其中,导热率λ值越大,则试样铸件材料的导热能力越强。实施例2本实施例中对原铁液出铁时mg元素和re元素的残余量作出以下三组对比实验:实验1当残留mg的含量降至0.013~0.022%、残留re的含量降至0.021~0.045%时出铁浇注。实验2当残留mg的含量降至<0.013、残留re的含量降至<0.021时出铁浇注。实验3当残留mg的含量降至>0.022%、残留re的含量降至>0.045%时出铁浇注。将上述三组实验在石墨形态、成品、强度、硬度进行对比,具体如下表所示:石墨形态成品强度(mpa)硬度(hbs)实验1蠕虫状石墨>50%,余为团球状蠕墨铸铁≥480mpa180~240实验2团球状石墨>50%,余为蠕虫状球墨铸铁≥480mpa>240实验3基本为片状石墨灰铸铁<480mpa100~220由上表可以看出,本实施例的高性能蠕墨铸铁材料铸件的制备工艺,通过选取合适的蠕化剂、孕育剂并调整添加比例,并严格控制出铁温度、控制出铁时原铁液中的石墨形态,提高石墨蠕化率,从而提高铸件成品的强度、塑性及导热率等性能。以上显示和描述了本发明的基本原理、主要特征和本发明的优点。本行业的技术人员应该了解,本发明不受上述实施例的限制,上述实施例和说明书中描述的仅为本发明的优选例,并不用来限制本发明,在不脱离本发明精神和范围的前提下,本发明还会有各种变化和改进,这些变化和改进都落入要求保护的本发明范围内。本发明要求保护范围由所附的权利要求书及其等效物界定。当前第1页12